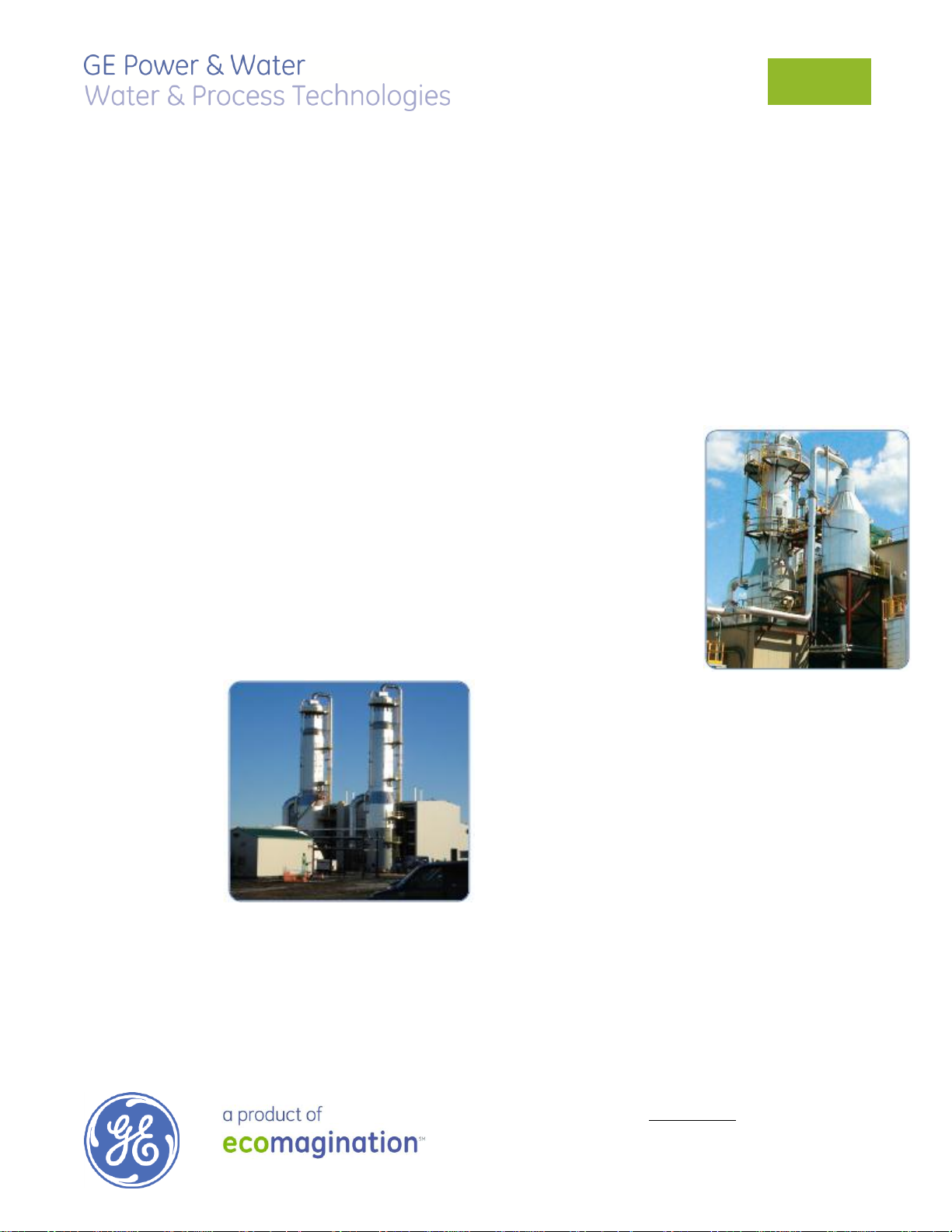
Find a contact near you by visiting www.gewater.com and clicking on “Contact Us”.
* Trademark of General Electric Company; may be registered in one or more countries.
©2013, General Electric Company. All rights reserved.
GEA17906_SAGD_Brochure.doc Jun-13
Connacher Oil & Gas Great Divide Project,
Ft. McMurray, Alberta, Canada
Approx. 900 gpm feed, 2007
Petro Canada Mackay River,
Ft. McMurray, Alberta, Canada,
Approx. 165 gpm feed, 2002
Treatment of Heavy Oil Produced Water Using
Evaporation and Zero Discharge Technology
Proven Global Experience
GE Water & Process Technologies (GE) is the pioneer
and an industry leader in produced water evaporation
and crystallization systems, having developed its patented high pH evaporation technology in the late
1990s and optimized its evaporation and crystallization technologies over the past 10 years. With 20
evaporators, crystallizers, and dryers installed or under
construction at heavy–oil, in-situ thermal production
facilities in the Alberta Oil Sands alone, GE continues to
lead the way in the safe and reliable treatment of produced water and OTSG (once-through steam generator) blowdown for boiler feed water and/or Zero Liquid
Discharge (ZLD). High pH evaporation is the only commercially proven and the most cost-effective thermal
solution for the treatment of produced water in heavy
oil recovery processes.
Superior Distillate Quality Provides
Reliable Operation of Drum Boilers
GE evaporators
employ a proprietary Contaminant Reduction System
for the production of superior
distillate quality,
enabling efficient and reliable operation of
high-pressure
(>1,000 psig)
drum boilers.
When coupled
with GE’s high pH evaporator design, this internal system enables produced water evaporators to generate
distillate that is four to five times better than evaporators operating with external vapor washers. The Contaminant Reduction System is self-cleaning, protects
against foaming events, and produces no additional
waste compared to an external vapor washer. In the
Alberta Oil Sands, GE has supplied six produced water evaporators to provide distillate for drum boilers
on SAGD (Steam-Assisted Gravity Drainage) applications and four evaporators that provide distillate for
OTSGs.
Improving on a Proven Technology
With an advanced research and development
program and abundant
experience from several
commercially operating
produced water evaporator systems, GE continues to optimize and
improve upon its high pH
evaporation technology.
Some recent optimizations include:
• More than 50% re-
duction in caustic
consumption, resulting in low chemical and operating costs compared to other produced water evaporative technologies
• Elimination of scale inhibitor, further reducing
chemical costs and producing evaporator blowdown that is easily post treated prior to deep well
injection
• Cascade and split-sump evaporator designs
providing lower capital costs and improving energy efficiency
• An internal Contaminant Reduction System for
superior distillate quality and reliable operation of
high-pressure (>1,000 psig) drum boilers
• In-situ chemical cleaning to improve system
availability and maximize steam to field
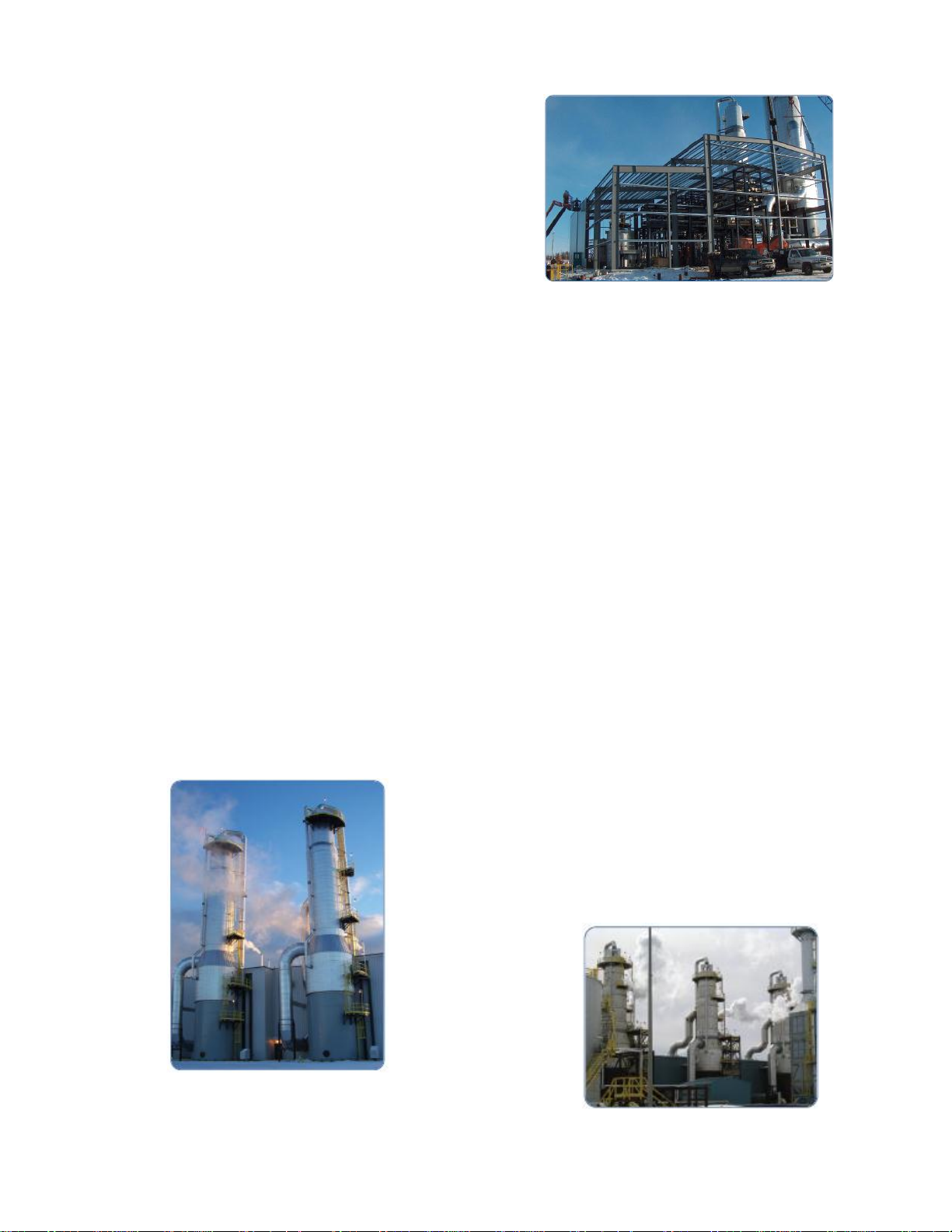
Total Canada Joslyn Phase 2,
Ft. McMurray, Alberta, Canada,
Approx. 900 gpm feed, 2005
Suncor Firebag Stage 2,
Ft. McMurray, Alberta, Canada,
Approx. 3,000 gpm feed, 2005
Installation of a modular system at Connacher
Oil & Gas Great Divide Project
Fourth Generation Module Design
Maximizes Project Certainty and
Minimizes Total Installed Cost
Understanding that cost and schedule certainty are of
the utmost importance for heavy oil producers, GE offers completely modularized evaporator and crystallizer systems.
The fourth Generation Module Design leverages experience and optimizations from the design and supply
of 14 modularized evaporators and crystallizers on
seven Oil Sands projects. GE scope includes everything
from the anchor bolts up with tight-spooled piping and
easy-to-install bolt connections. Equipment modules
are pre-assembled to the fullest extent possible and
pre-fitted prior to shipment, thereby reducing fieldwork
and maximizing project certainty. The owners of the
two most recently installed projects reported total installed cost factors of 2.0 and 1.8, indicating $0.80 to
$1.00 in installation costs for every $1.00 in equipment
costs. These total installed cost factors are among the
lowest in the industry and include all applicable cost
components, such as:
• Complete installation of the evaporator/crystallizer
system, including civils, site grading, gravel, foundations, piles, mechanical, electrical, I&C, etc.
• A proportional fraction of indirect costs such as
camps, accommodations, subsistence, shop inspections, field inspections, programming, freight,
cranes, start-up assistance, fencing, start-up
equipment, communications hardware, offices,
buildings, warehouse, and back-up generators
• A proportional fraction of engineering, manage-
ment, and drafting.
Produced Water Evaporator
Blowdown Solutions
There are two common methods to treat or dispose
of produced water evaporator blowdown:
1. Deep well injection — The recent optimizations
to the high pH produced water evaporation process result in a safe and straightforward posttreatment process prior to disposal.
2. Zero Liquid Discharge — Crystallization of high
pH evaporator blowdown results in waste slurry
of mixed salts, silica, and organics. This waste
slurry is unique to produced water applications.
GE has five crystallizers operating or under construction in the Alberta Oil Sands and is highly
experienced in handling this unique waste
stream. A drying or solidification/stabilization
process treats the waste slurry for final disposal
in a landfill.
a. Drying—A proven method of waste slurry
treatment that results in a dry, free-flowing
solid residual for disposal in a lined landfill.
b. Solidification / Stabilization—An alternate to
drying, S/S is a simple and environmentally
friendly way to treat crystallizer waste as it
produces a stable, non-leachable solid for disposal in standard landfills, which addresses
the concerns associated with long-term liability of residuals disposal.
Page 2 Capability Profile