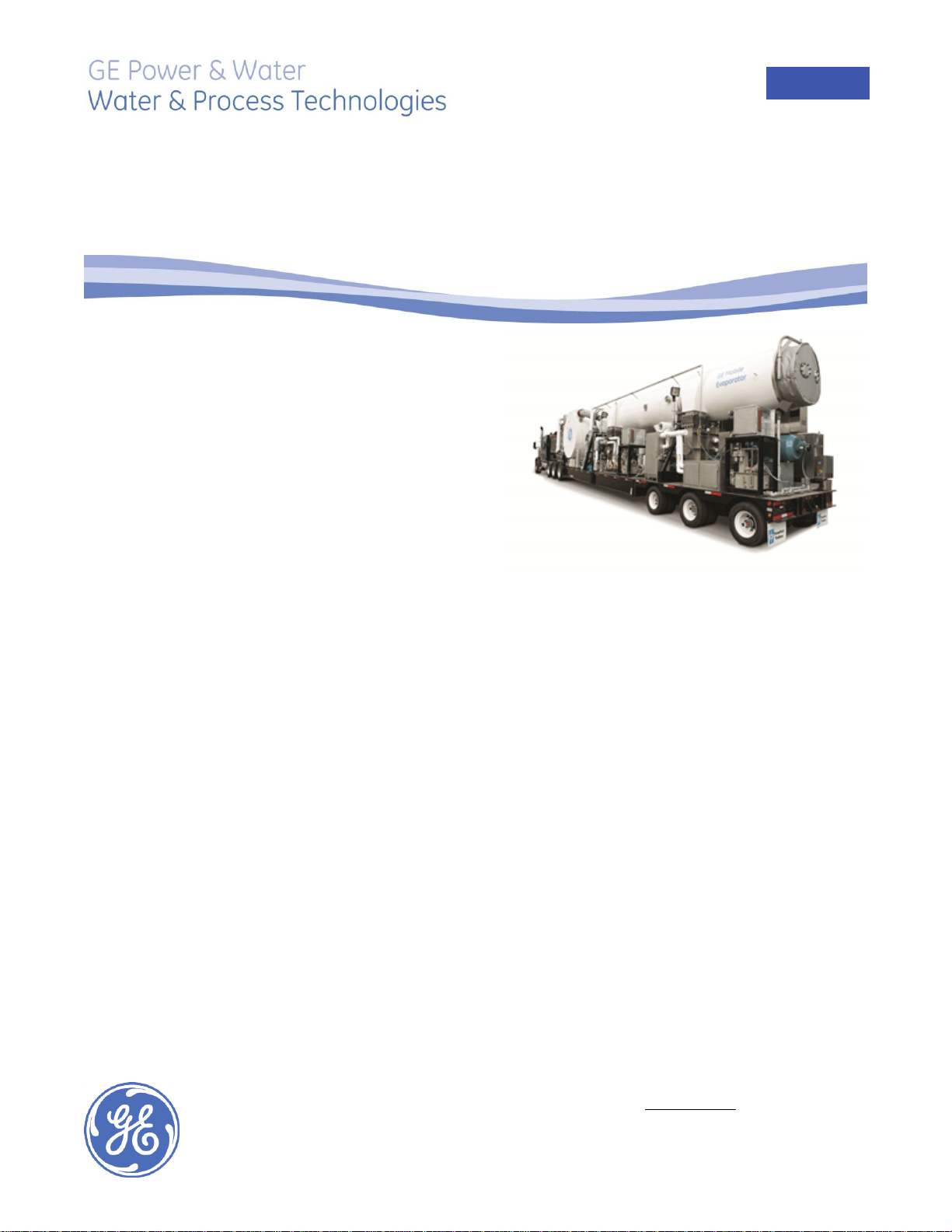
Find a contact near you by visiting www.ge.com/water and clicking on “Contact Us”.
* Trademark of General Electric Company; may be registered in one or more countries.
©2012, General Electric Company. All rights reserved.
AM-FSteMobileEvaporator_EN.doc Feb-12
Mobile Evaporator
Treat Shale Gas Flowback and Produced Water at the Well Site
Product Overview
GE’s new, completely mobilized evaporator is
designed to enable onsite flowback and produced
water recycling, reducing the volume of wastewater
and fresh water that needs to be hauled to and
from the site. The mobile evaporator will enable
natural gas producers to significantly decrease their
transportation and disposal costs. Additionally, the
communities will benefit from less truck traffic and
decreased wear and tear on local roads.
The mobile evaporator is a 50 gallon per minute
(gpm), truck-mounted, mechanical vapor
recompression (MVR) system. It features a wellproven and robust, horizontal shell and tube, forced
circulation evaporator.
Typical Applications
Through its robust design and compact footprint,
the mobile evaporator will be able to treat all types
of unconventional gas wastewater streams
throughout the world, including shale gas produced
water applications and coal bed/seam methane
applications.
Regions like the Marcellus Shale are unique in that
they produce very high TDS flowback and produced
water, have limited deep well capacity and
increasingly stringent discharge regulations.
General Properties
The mobile evaporator provides greater reliability,
higher on-stream availability, lower power
consumption, and reduced fouling of heat exchange
surfaces as compared to systems currently in use
for gas well return water recycling.
The mobile evaporator is a truck-mounted design
that fits within one standard trailer - a truly mobile
system with straightforward setup and operation.
Key Properties Include:
Robust heat exchanger configuration
MVR (high efficiency) design can reduce energy
costs by approximately 35%
Reduced fouling rates
Easy access for cleaning and maintenance
Excellent on-stream availability
Mobile design fits within one standard trailer
No site support equipment (cranes, etc.)
required
Completely self-contained with all ancillary
equipment included within the trailer
Single drop trailer provides maximum
clearance for remote site access
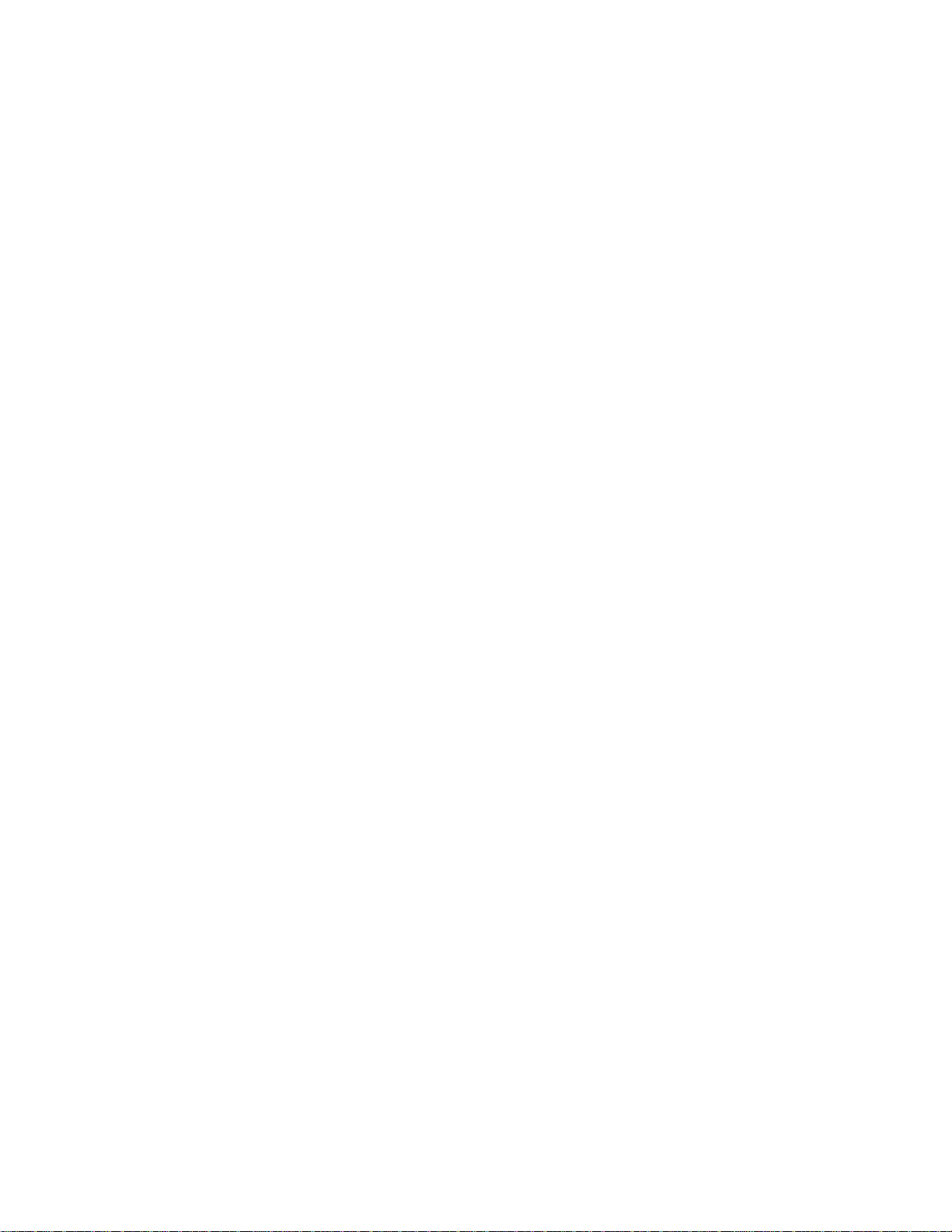
Operation
Cleaning
Mobilization-cold start
- Fully operational, producing distillate/
concentrate in 3.0–5.5 hrs
- Variation depends on feedwater temperature
(38°F–90°F design)
Minimal operator requirement
- Remote monitoring
- Allen Bradley PLC/17” HMI Control
- All critical parameters (amp, temp, pressures)
have alarm
CIP system on board
CIP solutions typically acid/caustic
30–60 minutes once a month
Data trending to predict cleaning requirements
and allow scheduling in advance
Page 2 Fact Sheet