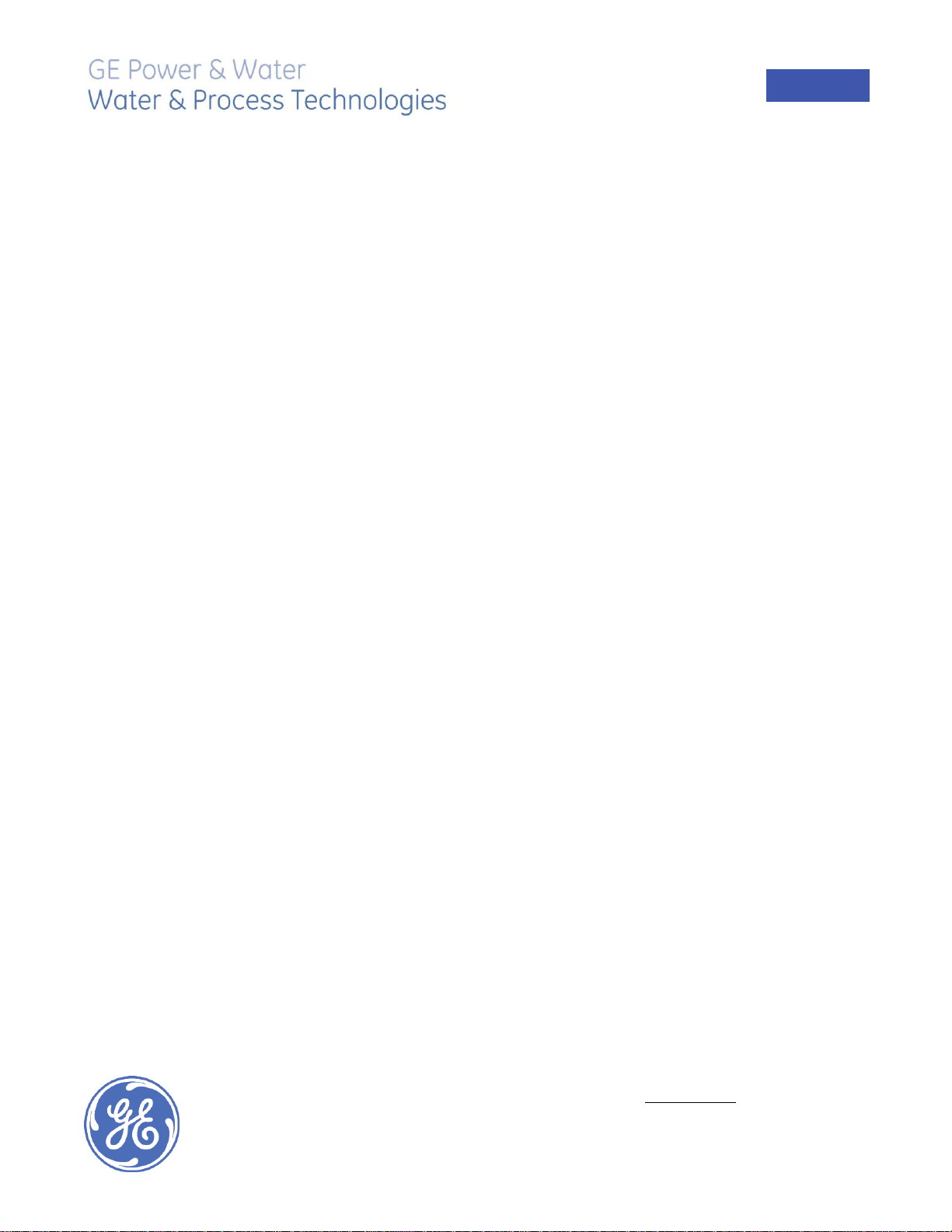
Find a contact near you by visiting www.ge.com/water and clicking on “Contact Us”.
* Trademark of General Electric Company; may be registered in one or more countries.
©2012, General Electric Company. All rights reserved.
pfg384.doc Feb-12
Kleen* MCT524
Membrane Cleaner - FDA/GRAS Approved and Kosher
Features
Highly effective cleaner for use with Thin Film
Composites (RO/NF) and hollow fiber membranes (MF/UF).
Excellent results are achieved when used to
remove organic foulants and biological slime
Liquid product, which allows shorter mixing
time
This formulation meets FDA requirements
(GRAS) for membrane process applications
Improved results are obtained when used in
conjunction with Kleen* MCT403 or Kleen
MCT503
Description
Kleen MCT524 is a high pH liquid formulation
designed to remove organics, silt, microbiological
accumulation; and other particulate deposits from
Reverse Osmosis (RO), Nanofiltration (NF), ultrafiltration (UF) and microfiltration (MF) membranes
used in food applications. It is also an excellent
cleaner in pure water applications. This highly effective product provides superior cleanings resulting in longer system running time.
ating pressure, or an excessive pressure drop in
the system, which may lead to irreversible membrane damage. Before these foulants accumulate
to a level where product water flow or quality declines or membrane damage occurs, they should
be removed through a clean-in-place (CIP) off-line
cleaning. Indications of the need for cleaning include a significant decrease in normalized permeate flow, a significant increase in pressure drop
across the system (or individual stage), or an increase in the normalized salt passage such that
product quality is unacceptable.
Your GE representative can assist you with monitoring your system and determining when cleaning is advised.
Kleen MCT524 contains a blend of solubilizing and
complexing agents designed to specifically
remove organic and particulate foulants from the
surfaces of the membrane. Used in tandem with
an acidic cleaner for scale removal, regular cleanings with Kleen MCT524 can help to preserve the
life of your membranes.
Depending on the nature of the fouling, a soak
period may be necessary for optimum results.
Consult your GE representative for details.
Typical Applications
During the operation of a membrane separation
system, organic materials and suspended solids in
the incoming stream can accumulate on the
membrane surface. The presence of organic materials also provides an environment conducive to
microbiological activity, which can result in microbiological fouling. Fouling from these species
impedes the flow through the membrane. This can
result in unacceptably low production, high oper-
Application
For improved results in food applications, Kleen
MCT524 should be used in combination with low
pH cleaners such as Kleen MCT403 or MCT503.
Feed Requirements
Feed System - This product should be applied
using the membrane cleaning equipment,
supplied by the manufacturer of the membrane
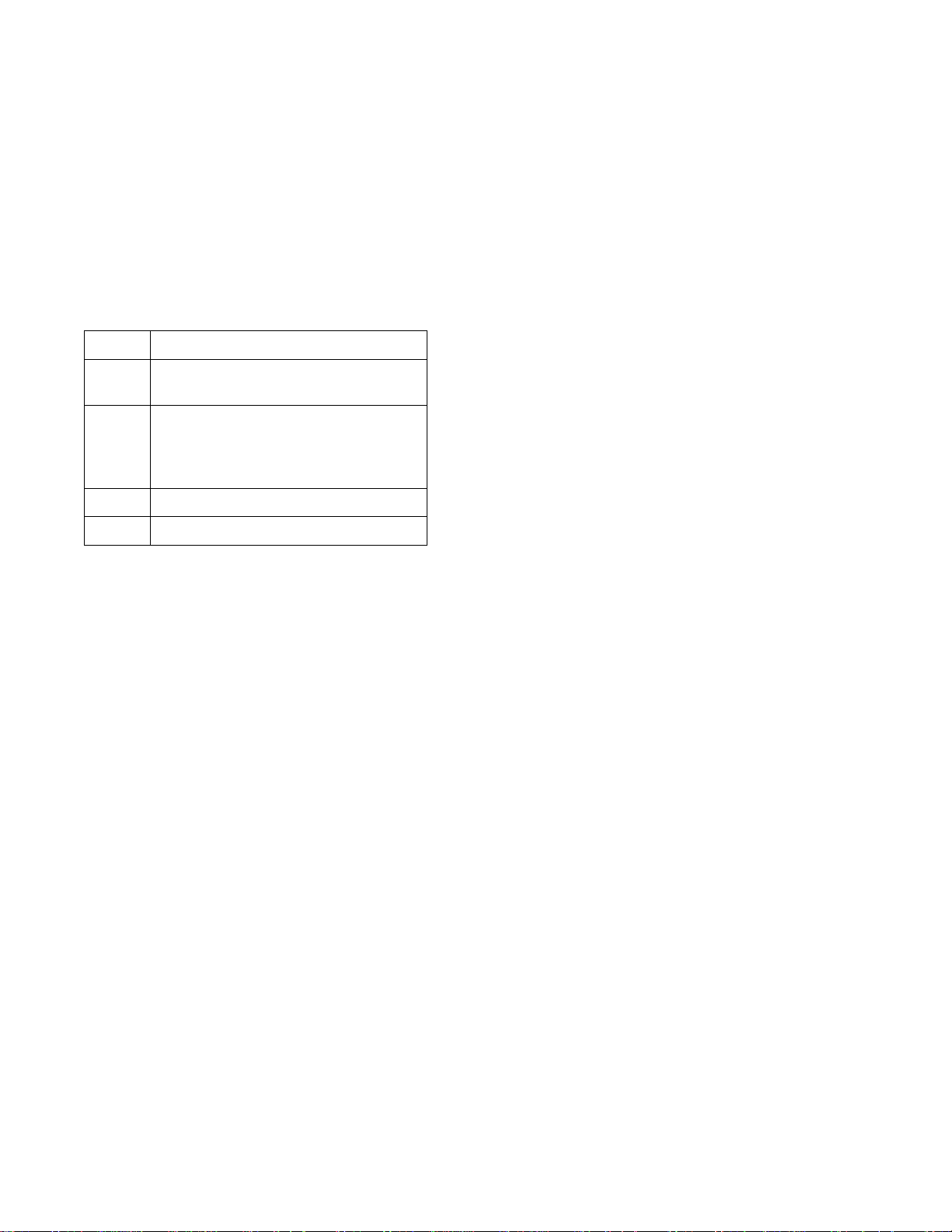
system. If such a system is not present, contact
LB, SS, Buna S, Hypalon, EPR, Natural
Rubber, Teflon
Butyl, Buna N, Neoprene, Viton
Lithurge, Polyethyl HD & LD, PVC, Kynar,
Polyethyl HDCL, Polypropylene, Polysulfone
LCS, Viton A, Tygon, Nylon
your GE representative for information on
fabricating or obtaining a cleaning system.
Dilution - The recommended dilution for this
product is from 1% - 2.5 % with permeate water.
Materials Compatibility - Corrosion-resistant
equipment should be used for the storage,
preparation, and use of this product per the
following compatibility chart:
Packaging Information
Kleen MCT524 is a liquid material, available in a
variety of containers and delivery methods.
Contact your GE representative for details.
General Cleaning Instructions
The following general cleaning procedure can be
followed. For the optimum cleaning procedure for
your system, contact your GE representative.
1. Inspect cleaning tank, hoses, and cartridge
filters. Clean tank and flush hoses if necessary.
Install new cartridge filters.
2. Fill cleaning tank with RO permeate or DI
water. Turn on agitator or tank recirculation
pump.
3. Slowly add Kleen MCT524 to cleaning tank
in order to prepare a solution of 1- 2,5 % concentration, based on the CIP total volume and
the product strength needed and allow to mix
thoroughly.
4. Check solution temperature. If solution tem-
perature is lower than recommended level,
adjust heating control to provide optimum
temperature. If manufacturer’s recommendation is not available, contact your GE representative.
5. Check solution pH. The solution pH should be
<12 or as recommended by the membrane
manufacturer. If pH is too low, adjust pH
upward with NaOH, or other chemical as recommended by the membrane manufacturer.
If pH is too high, adjust with hydrochloric acid.
6. Circulate solution through one stage at a time
in the direction of feed flow for 30 minutes.
Circulate at the flow rate recommended by
the membrane or system manufacturer. If
manufacturer’s recommendation is not available, contact your GE representative. Pressure
should be low enough so that minimal permeate is produced during cleaning, but always
less than 60 psig (4.2 kg/cm2).
7. In cases of heavy fouling, the first return flow
(up to 15% of the cleaning tank volume)
should be diverted to drain to prevent
redeposition of removed solids. For optimum
results, each stage must be cleaned separately in a multistage system.
8. If the first stage cleaning solution becomes
turbid or discolored, dump the tank and prepare a fresh cleaning solution before proceeding. If solution pH or temperature moves out of
the recommended range, a new solution
should be prepared. In any event, a new
cleaning solution should be prepared for each
stage.
9. Rinse with RO permeate before returning
system to service.
10. When returning unit to service, divert product
water to drain until any residual cleaning solution has been rinsed from system.
Depending on the nature of the fouling, a soak
period may be necessary for optimum results.
Consult your GE representative for details.
Safety Precautions
A Material Safety Data Sheet (MSDS) containing
detailed information about this product is available upon request.
Page 2 Fact Sheet