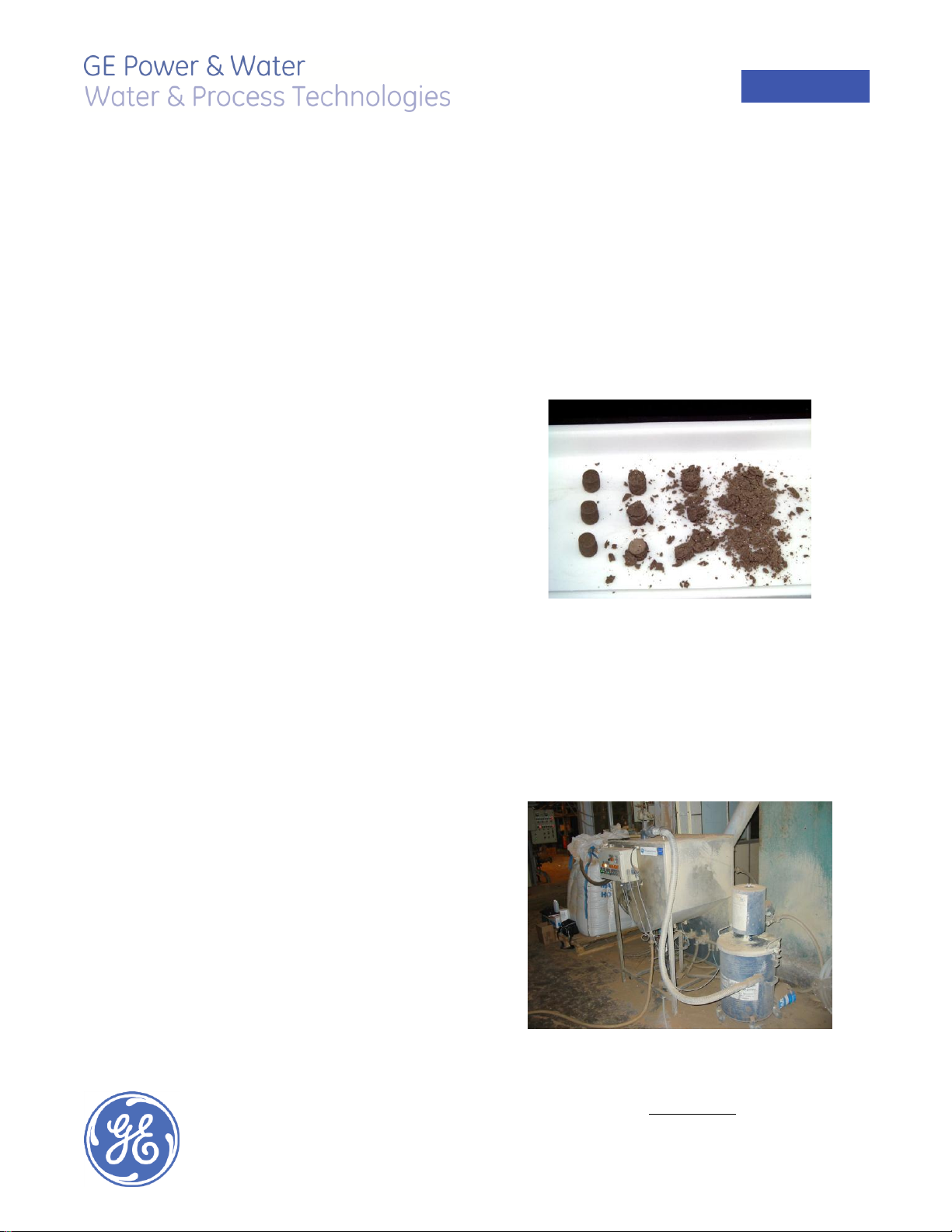
Find a contact near you by visiting www.gewater.com and clicking on “Contact Us”.
* Trademark of General Electric Company; may be registered in one or more countries.
©2013, General Electric Company. All rights reserved.
E-CHbFuelSolvFS3954_EN.doc 05
FuelSolv* FS3954: Controls Ash-Clogging
in an Incinerator Boiler
Setting up a FuelSolv FS3954 treatment program on a 7
ton/hour household waste incinerator that produces electricity
for EDF and heats horticultural greenhouses
Challenge
During its winter season, a household waste incinerator faces many shutdowns due to the accumula-
tion of deposits on the boiler’s exchange surfaces.
As a result of that reduction in heat exchange, the
limit temperature acceptable for the first superheater is reached quickly.
Several shutdowns are necessary during the season
(5 months) for a quick cleaning of the smoke pathways, i.e. one shutdown about every six weeks.
Those shutdowns cause operating losses:
Treatment of household waste at an outside
site (transfer cost)
EDF penalty for not supplying electricity
Outside servicing costs
Solution
GE Water & Process Technologies offers an expansive FuelSolv FS3954 treatment that limits boiler
clogging to reduce the number of shutdowns for
cleaning over the course of the season.
A laboratory study of vitrification tests was done on
ashes from stages 2 and 3 of the boiler. Those tests
show the effect of FuelSolv FS3954 for a dosing
greater than 2% with respect to ash at a temperature of 750°C/1380°F).
White 1% 2% 4%
Due to the rate of ash generated by household
waste, we recommend a dosing of 500 g of FuelSolv
FS3954/ton of waste incinerated.
FuelSolv FS3954 comes in the form of nonhygroscopic particles that can be injected into the
boiler using a compressed-air doser.
View of Injection System
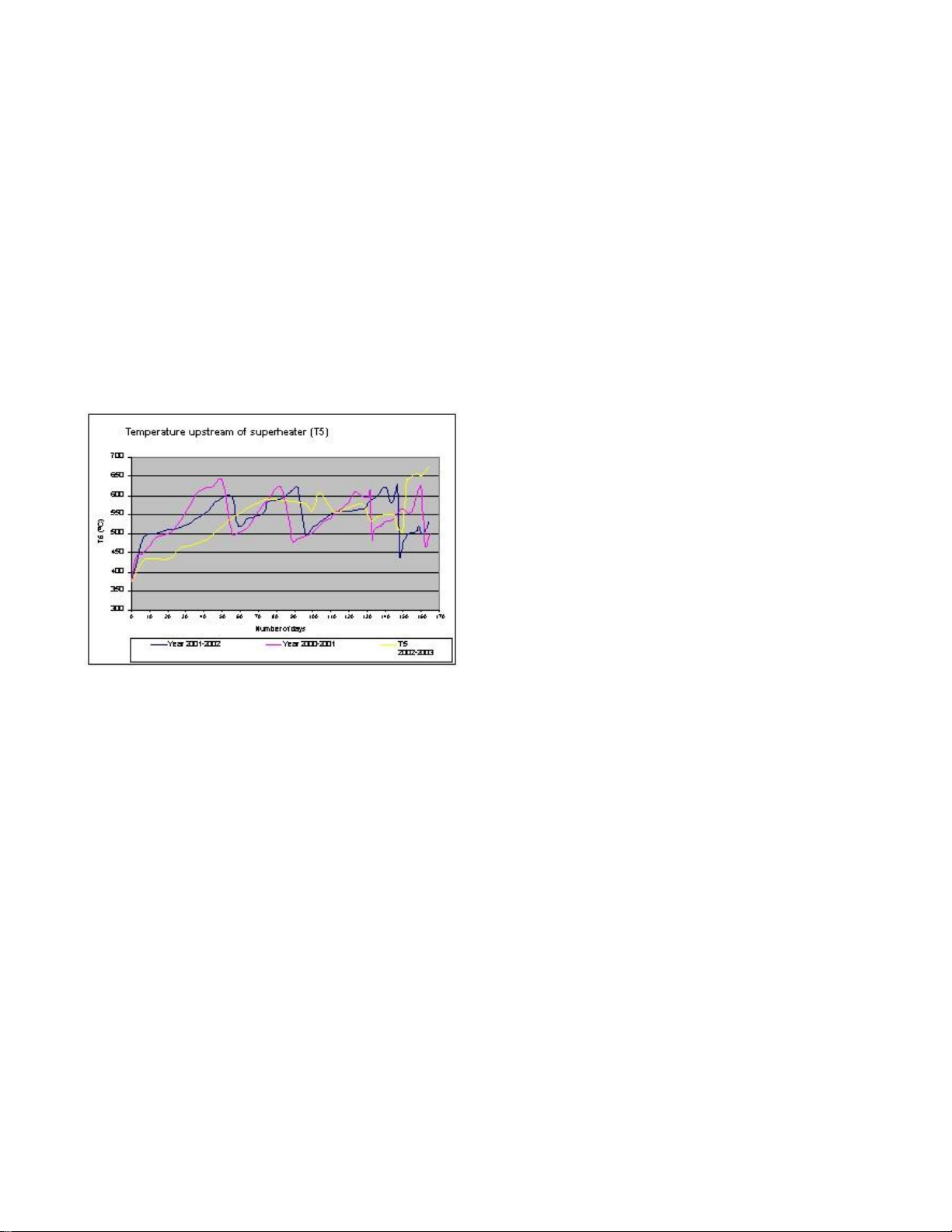
In the test, two injection points were placed at the
outlet of the furnace in the first riser stage of the
boiler (smoke temperature 850°C/1560°F, the minimum temperature for injection being 760°C/
1400°F).
The test was conducted from December 2002 to
May 2003.
Results
The critical parameter for validating the test is the
temperature of the smoke (T5) upstream of the
superheaters. That temperature enables the operator to determine the shutdown for cleaning of the
installation. (650°C/1200°F).
Thanks to our technology, the client achieved its
primary goal: no shutdown between the two scheduled annual technical maintenances.
Achieving that goal enabled the operator to make
significant gains:
Fulfill electricity-supply commitments with EDF
No additional cost from outside treatments of
household waste
Reduction in operating cost
Page 2 Case Study