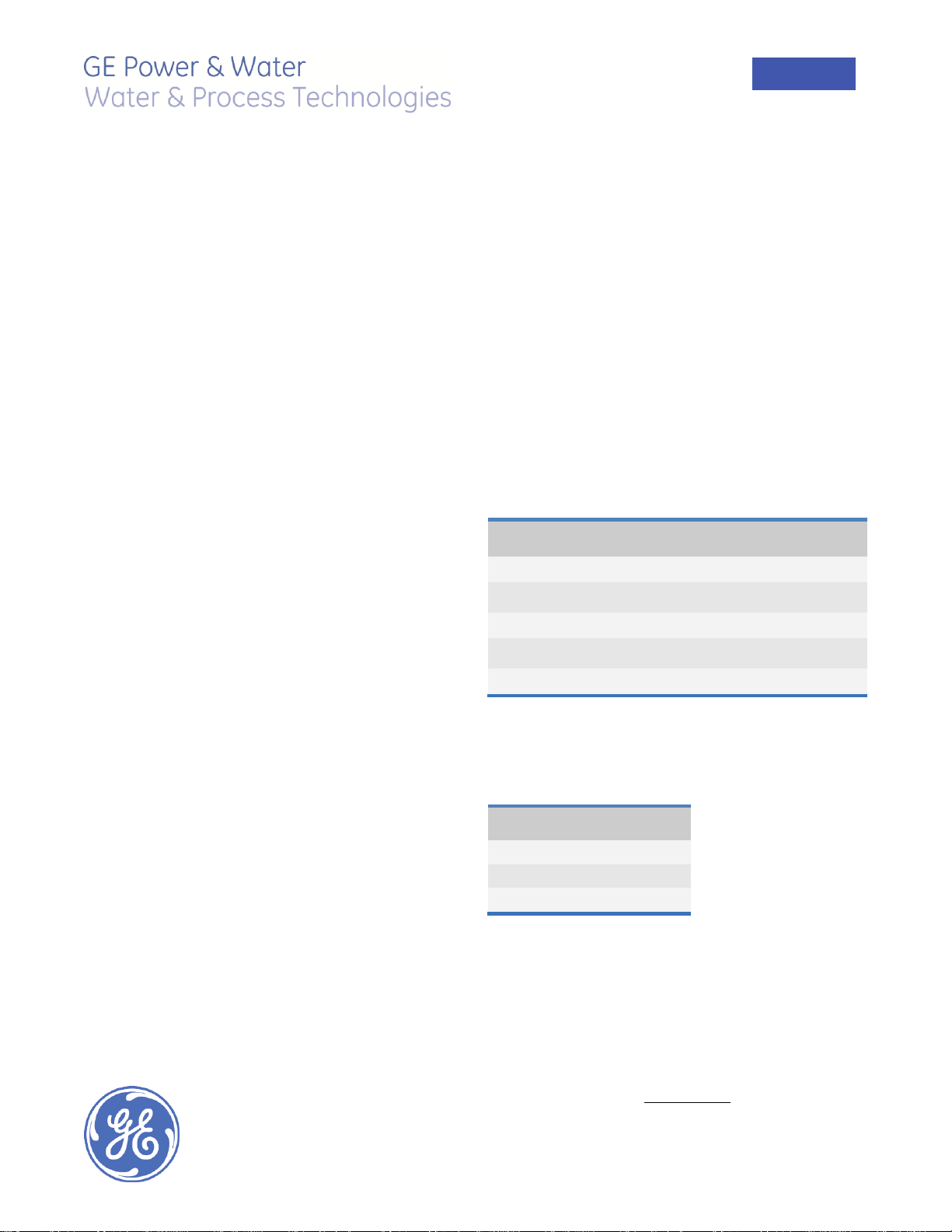
Find a contact near you by visiting www.gewater.com and clicking on “Contact Us”.
* Trademark of General Electric Company; may be registered in one or more countries.
©2013, General Electric Company. All rights reserved.
FSsmDuracid_EN.docx Sep-13
Duracid Series
Industrial Acid Stable Nanofiltration Elements
Description and Use
The Duracid NF membrane element is engineered
to operate continuously under extreme acid conditions where pH is at or below zero.
The family of Duracid proprietary thin-film nanofiltration membrane elements is characterized by an
approximate molecular weight cut-off of 150-200
Dalton for unchanged organic molecules. Divalent
and multivalent ions are preferentially rejected by
the membrane while monovalent ions and mineral
acids commonly have full transmission through the
membrane (transmission can vary depending upon
feed concentration and composition). Since mineral
acids and monovalent ions have high passage
through the membrane, these substances have a
minor contribution to the osmotic pressure.
Among other applications, Duracid NF Elements are
used for acid purification and metals concentration
in low pH streams.
They feature patented feed spacers, polysulfone
parts and a fiberglass outer wrap. All materials of
construction are low pH tolerant.
Markets
Metal Surface Treatment / Coating / Galvanic
Heap Leaching Process in Mining
Phosphate-based Chemical Production
Spent Acid Recovery
Application Data
Table 1: Membrane Metal Rejection
1
Based on flat sheet test conducted at 25°C (77°F) under 400 psig operating
pressure in a dead-end filtration mode. A single acid feed solution was dosed with
a mixture of all metals listed in Table 1 for each type.
Table 2: Typical Process Streams
Features and Benefits
Extreme low pH stability
100% wet testing Quality Assurance
Durable construction
High temperature compatibility
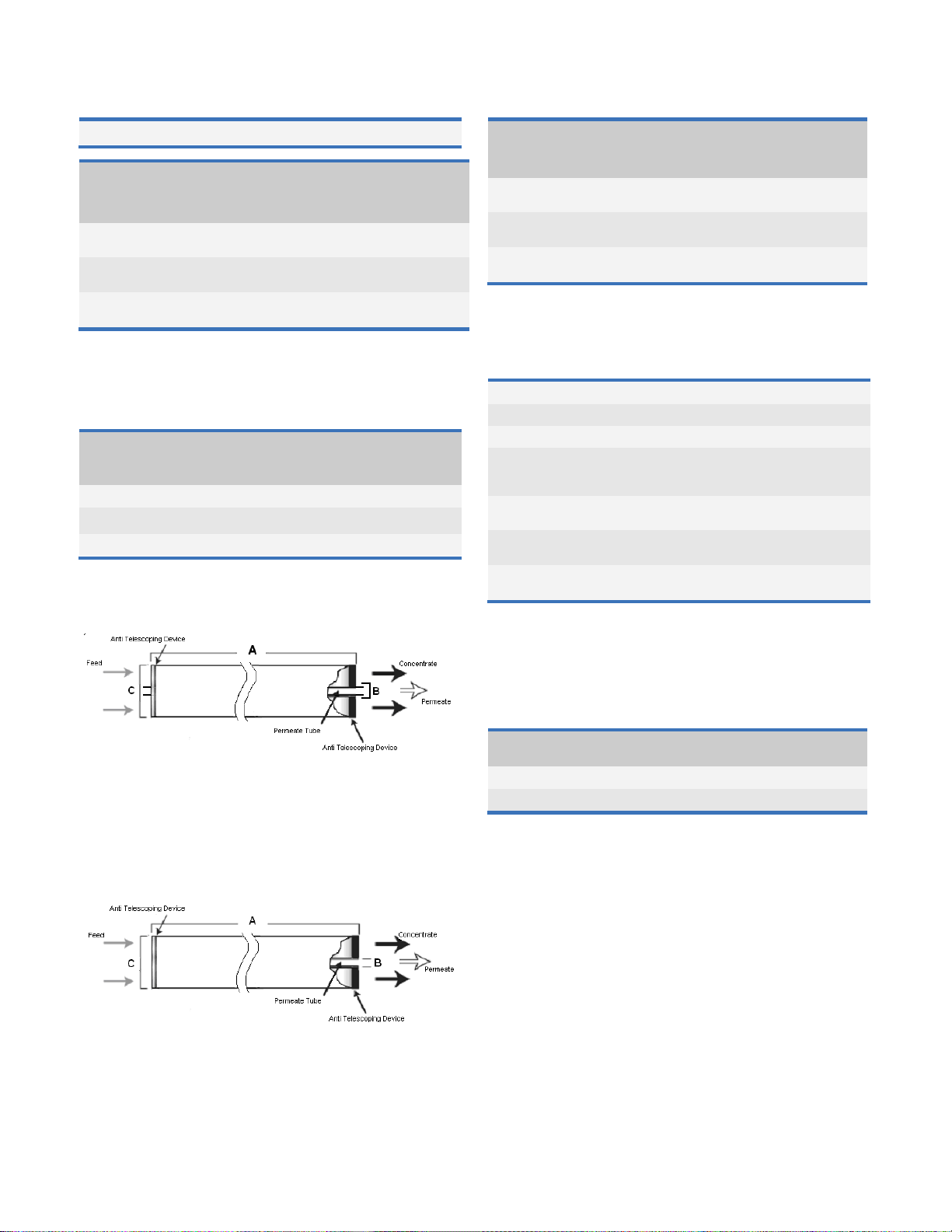
Duracid, Thin-film membrane (TFM*)
Average
permeate
flow, gpd
(m3/day)
1,2
Average
permeate
flow, gpd
(m3/day)
1,3
Maximum
crossflow gpm
(m3/hr)
Average
MgSO4
rejection
1,2
Typical Operating Pressure
400 – 800psi (2758 – 5516kPa)
10-19 GFD (17-32 LMH) @ 225psi (1551kPa)
Maximum Operating
Pressure
1200psi (8,273kPa)
800psi (5,515kPa)
600 psi (4,136kPa)
32 – 77°F (0 – 25°C)
78 – 122°F (26 – 50°C)
123 – 158°F (51 – 70°C)
Continuous operation: 158°F (70°C)
Clean-In-Place (CIP): 158°F (70°C)
Continuous operation: < 9
Clean-In-Place (CIP): < 9
500 ppm-hrs,
dechlorination recommended
Table 3: Element Specification
1
Average permeate flow and salt rejection measured on pre-conditioned ele-
ments after 24 hours operation. Individual flow rate may vary ±25%
2
Testing conditions: 2,000ppm MgSO4 solution at 110psi (760kPa) operating
pressure, 77 °F (25°C), 15 % recovery.
3
Testing conditions: 3% glucose solution at 440psi (3034kPa) operating pressure,
77⁰F (25⁰C), 15% recovery.
Table 4: Dimensions and Weight
1
These elements are dried then bagged before shipping.
2
Internal diameter unless specified OD (outside diameter).
Table 5: Operating and CIP parameters
Figure 1: Element Dimensions Diagram (Male) – 2540 &
4040
Figure 2: Element Dimensions Diagram (Female) – 8040
1
Clean water flux (CWF) is the rate of water permeability through the membrane
after cleaning (CIP) at reproducible temperature and pressure. It is important to
monitor CWF after each cleaning cycle to determine if the system is being
cleaned effectively. CWF can vary ±25%.
Table 6: Maximum Pressure Drops
Pre-conditioned Elements
To optimize flow and rejection performance of
Duracid membranes, a pre-conditioning step is required. Element pre-conditioning consists of a 5min
pure water flush at a minimum pressure of 500 psig
(3447kPa) at ambient temperature.
Page 2 Fact Sheet