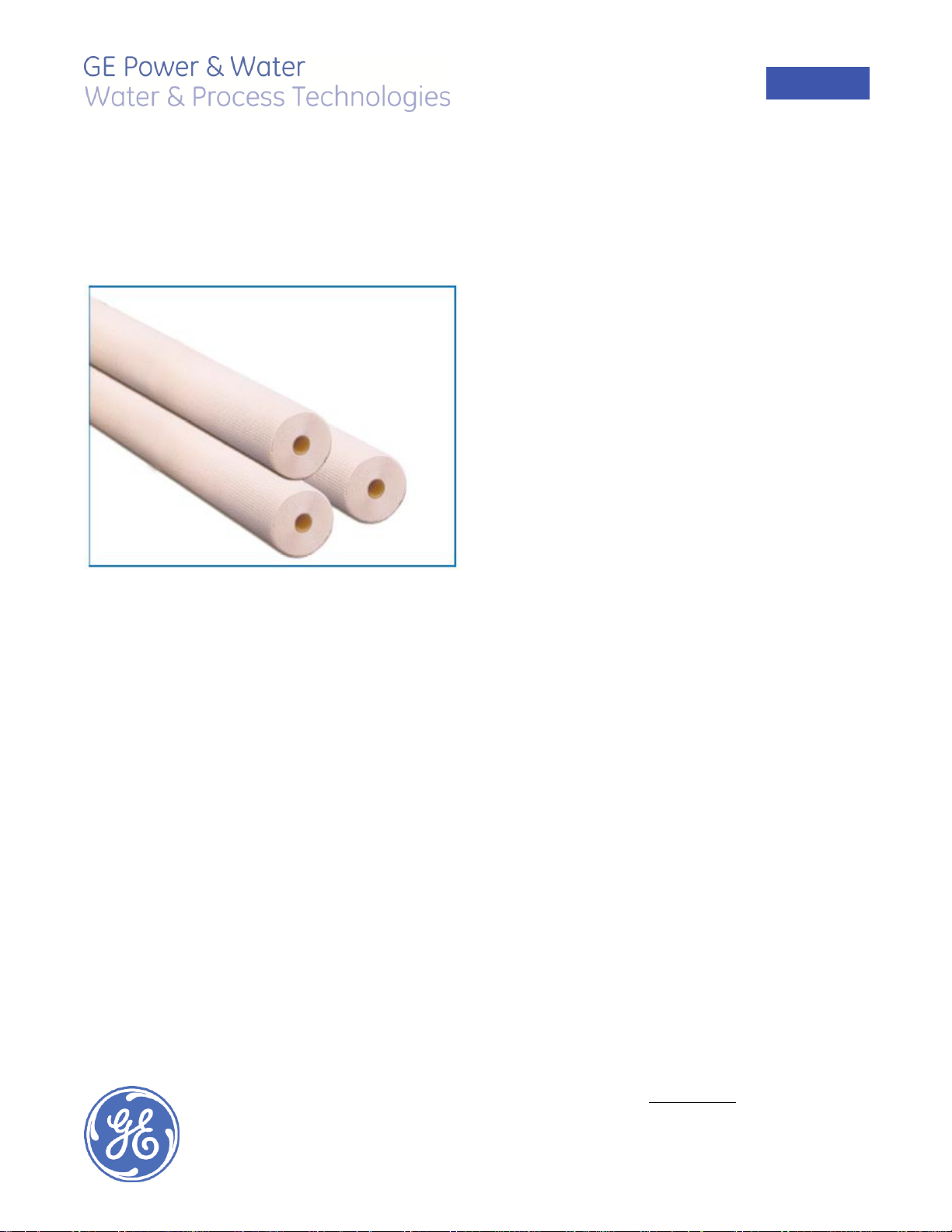
Find a contact near you by visiting www.gewater.com and clicking on “Contact Us”.
* Trademark of General Electric Company; may be registered in one or more countries.
©2013, General Electric Company. All rights reserved.
FSpsDairyHWS_EN.doc Sep-13
Dairy HWS
Dairy Industry
Dairy HWS elements utilize polysulfone parts and
unique element construction to meet the requirements for hot water sanitization. Comprised of high
quality materials that meet 3A standards and conform to guidelines set by the Code of Federal Regulations, Dairy HWS elements feature a patented
Durasan* Cage protective sleeve that enhances
element integrity by securing the spiral. In addition,
the sleeve improves sanitizing effectiveness by
maintaining a controlled by-pass between the element and pressure vessel wall without the use of
traditional brine seals.
Hot Water Sanitization
Meeting Stringent Requirements
Without question, the dairy industry is faced with
increasingly stringent sanitary regulations. To help
meet these requirements, GE Water & Process
Technologies introduces the Dairy HWS family. Ideal
for applications with biologically active feeds, Dairy
HWS elements are designed for hot water sanitization (pasteurization) by periodic exposure to temperatures up to 90°C (194°F). An innovative breakthrough, you can now sanitize the permeate side of
a membrane element without risking membrane
damage. Additional benefits of Dairy HWS elements
include sanitization without the use of ineffective or
harmful chemicals, as well as protection against
detrimental bacterial growth on the membrane surface – thus limiting replacement costs.
Membrane Technology
A Valuable Solution
The use of spiral membrane technology in dairy applications allows plants to recover valuables, create
saleable products, recycle water and reduce plant
effluent. By utilizing Dairy HWS elements, spiral
membrane systems can strategically concentrate:
Sweet Whey
Lactose
Whole Milk
Skim Milk
A Market Leader
GE’s Commitment to You
After over 30-years of innovation in membrane
technology, GE has become a market leader in developing new ways to solve even the most difficult
industrial and commercial challenges. For sanitization specifications and protocols based on your
unique dairy process, please consult a GE representative.
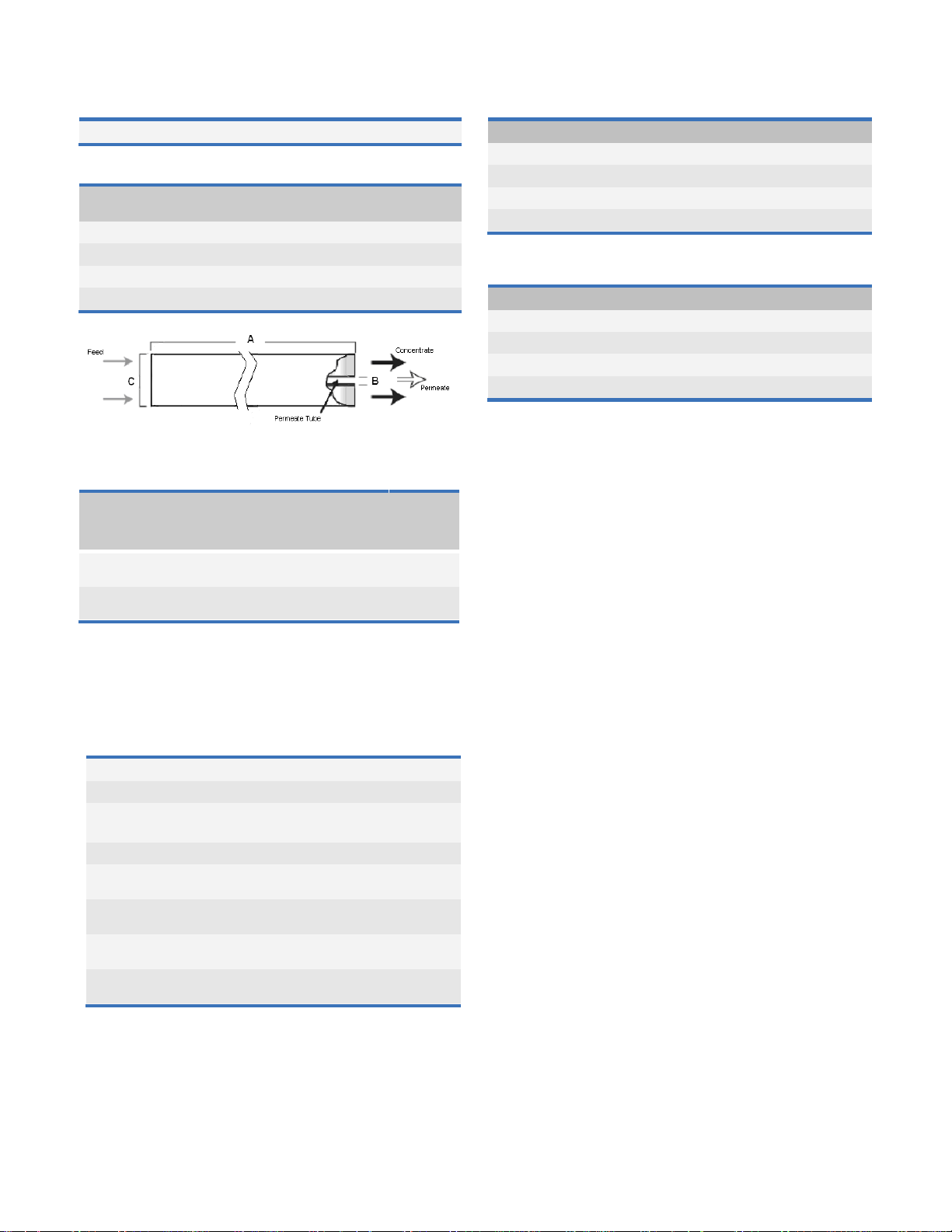
Thin-film membrane (TFM*)
Typical Operating Pressure
200-500 psi (1,379-3,447 kPa)
RO : 14 GFD (24 LMH)@ 225 psi
NF : 14 GFD (24 LMH) @ 110 psi
Maximum Operating Pressure
600 psi (4,137 kPa): 41 – 122°F (26 – 50°C)
Continuous operation: 122°F (50°C)
Hot Water Sanitization: 194°F (90°C)
RO elements: 3.0 – 10.0
NF elements: 3.0 – 9.0
500+ ppm hours,
dechlorination recommended
Over an element: 15 psi (103 kPa)
Per housing: 60 psi (414 kPa)
Table 1: Element Specification
Figure 1: Element Dimensions Diagram - Female
Table 2: Dimensions and Weight
1
These elements are dried and bagged before shipping.
2
Internal diameter.
Table 3: Operating parameters
Do not exceed 20 GFD (33 LMH) or 2,000 Wagner
units under any circumstance.
Table 4: CIP limits for RO elements
Table 5: CIP limits for NF elements
Hot Water Sanitization
Recommendations
For optimal performance, Dairy HWS elements
should always be cleaned using approved CIP
procedures and flushed with fouling free water
before the sanitization process. Feed pressure
during sanitization should not exceed 40psi
(275kPa) and the crossflow should not incur a
pressure drop greater than 2psi (14kPa) per
element. Heating rate to sanitizing temperature and
cool down should not be faster than 5°C (41°F) per
minute. Maximum sanitization temperature is 90°C
(194°F).
Loss of Permeate Flow after Repeated
90°C Sanitization Cycles
1
Clean water flux (CWF) is the rate of water permeability through the membrane
after cleaning (CIP) at reproducible temperature and pressure. It is important to
monitor CWF after each cleaning cycle to determine if the system is being
cleaned effectively. CWF can vary ±25%.
Page 2 Fact Sheet
It is almost impossible to exactly predict the percentage of permeate flow rate lost from the high
temperature sanitations, which among other factors depends on:
1) Rate of temperature increase and decrease.
2) Presence of other species like organics, ionic
and metallic compounds that could locally decrease or increase the temperature at the surface of the membrane.
3) Feed flow rate and specifically the heat transfer
rate to the membrane surface.
4) The thickness and geometry of the feed spacer
used.

At optimum conditions measured in controlled environment with deionized water, between 30% and
50% of the original permeate flow rate was lost before the element performance had stabilized after
repeated heat treatments (over 90% of this flow
reduction occurred during the first heat treatment).
With the loss of permeate flow rate, the salt rejection increases. The rate of cooling and heating was
not more than 5C (41°F) per minute, and the differential pressure drop per element did not exceed 2
psi.
Pilot testing based on the criteria noted above will
give the best operating parameters for any specific
application.
Fact Sheet Page 3