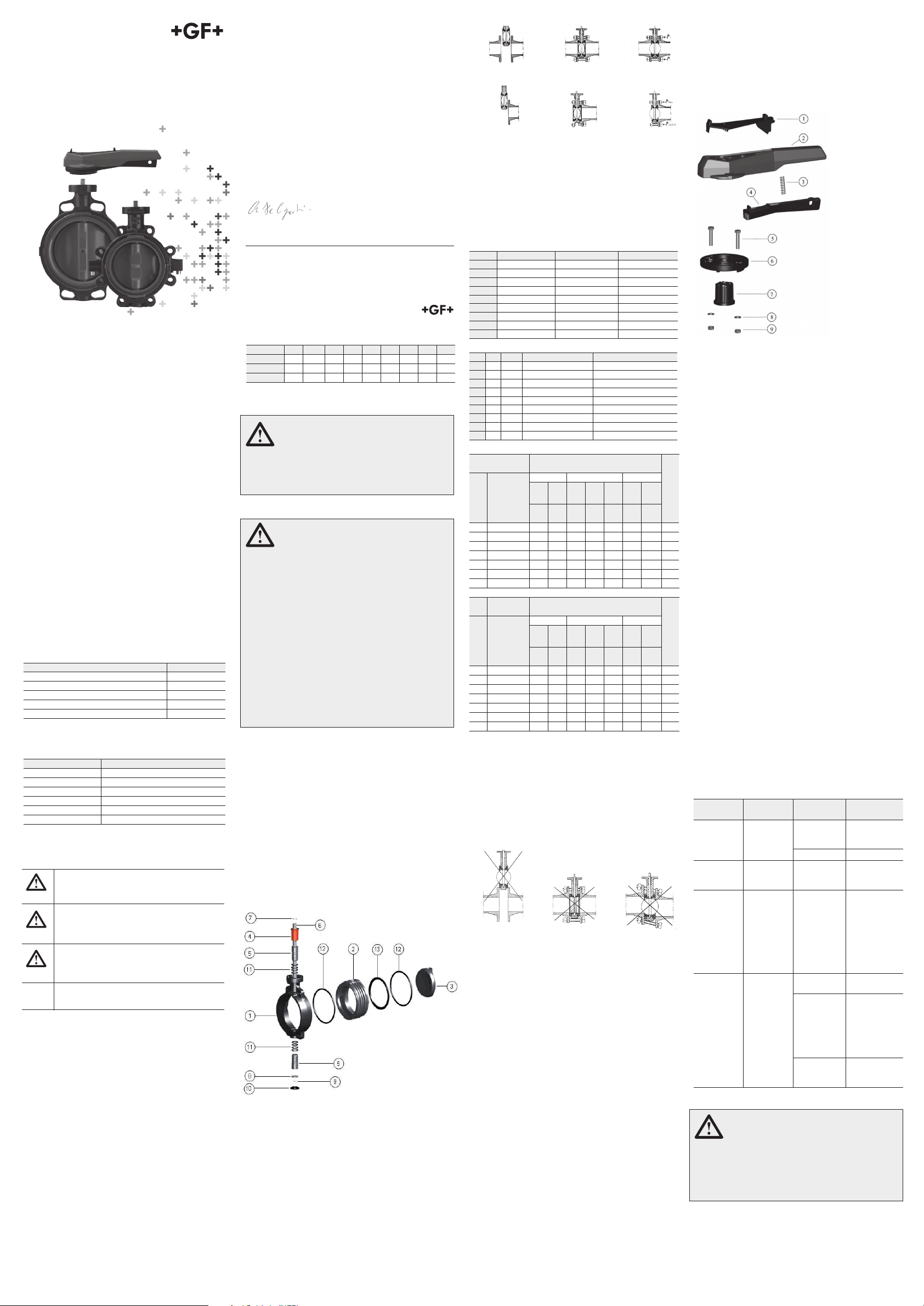
GF Piping Systems
Instruction manual
Butterfly valve Type 567/568
Observe instruction manual
The instruction manual is part of the product and an
important element within the safety concept.
• Read and observe instruction manual.
• Always keep instruction manual available close to the
product.
• Pass on instruction manual to all subsequent users of the
product.
1. Intended use
After being installed into a piping system, butterfly valves
type 567/ 568 are exclusively meant to block or convey media
within the approved pressure and temperature limits, and to
regulate the flow.
The maximum time of operation is 25 years. The valve is
intended to be used within the chemical stability of the entire
valve and all its components.
Butterfly valves are not recommended for media with
solid matters. Cavitation has to be avoided during normal
operation.
In case of degreasing or jamming media, butterfly valves
can only be used after consulting a GF Piping Systems
representative.
• Use type 567 only as intermediate butterfly valves.
• Use type 568 as intermediate or ending butterfly valve.
See «Georg Fischer‘s planning criteria» for approved
pressure areas of all approved temperatures for all housing
materials. These documents also contain the „list of
chemical resistivity“ for the different valve materials.
2. Regarding this document
This document contains all necessary information for the
installation, operation and service of the product.
2.1 Related documents
• Georg Fischer planning fundamentals
• Instruction manual for expanding the BFV 567/ 568 for
further functions:
Instruction manual GMST number
Quick Guide Electrical actuator 5886/1, 4
Pneumatic actuator PA30- PA90 5377/1, 2, 4d
Integrated Electric Feedback 5939/1, 4
Intermediate Element for BUV 567/568 5918/1, 4
These documents can be obtained from the GF Piping Systems representative or under www.piping.georgfischer.com
2.2 Abbreviations
.
Abbreviation Meaning
BFV Butterfly Valve
Type 567/ 568 Butterfly Valve 567/ 568
DN Nominal diameter
PN Pressure rate
SFA Socket flange adaptor
BFA Butt fusion flange adaptor
3. Safety and warning instructions
This manual contains warning instructions that shall warn
against injuries or material losses. Always read and observe
those warning instructions.
• Imminent danger!
DANGER
WARNING
CAUTION
NOTICE
4. Safety and responsibility
In order to provide safety in the plant, the operator is
responsible for the following measures:
• Products may only be used for its intended purpose, see
• Never use a damaged or defective product.
• Make sure that the piping system has been installed
• Products and equipment shall only be installed by persons
• Regularly train personnel in all relevant questions
The personnel is responsible for the following measures:
• Know, understand and observe the instruction manual and
The same safety guidelines apply for butterfly valves as for
the piping system into which they are built.
To operate the butterfly valves, the torques as indicated in
table 1 are sufficient.
• At high flow veloctiy we recommend to use a gear operator
• A butterfly valve is not self-locking:
Non-observance may result in major injuries
or death.
• Possible danger!
Non-observance may result in major injuries.
• Dangerous situation!
Non-observance may result in minor injuries
• Dangerous situation!
Non-observance may result in material losses.
intended purpose
Immediately sort out damaged product.
professionally and serviced regularly.
who have the required training, knowledge or experience.
regarding locally applicable regulations regarding safety at
work, environmental protection especially for pressurised
pipes.
the advices therein.
instead of a hand lever.
The actuating device shall not be disassembled, as long as
the valve is flowed or pressurised.
EC declaration of conformity
The manufacturer Georg Fischer Rohrleitungssysteme AG, 8201 Schaffhausen (Switzerland) explains that the butterfly valves types 567/ 568
according to the harmonised construction type standards EN-593
1. are pressure-maintaining components in terms of the EG Pressure
Equipment Directive 97/23™/EG and comply with the requirements of
this directive that apply to valves,
2. comply with the applicable requirements of the Construction Products
Directive 89/106/EG for valves
The Œ sign on the valve proves this compliance (according to the
Pressure Equipment Directive, only valves with a ND larger than 25 shall
be indicated with Œ).
The operation of these butterfly valves is not allowed until the conformity of the entire system, in which the butterfly valves have been installed
has been explained with one of the mentioned EG Directives.
Changes to the butterfly valve that could effect the stated technical data
and the intended purpose, void this declaration of conformity. Additional
information can be found in „Georg Fischer‘s planning fundamentals“.
Schaffhausen, 01 July 2013
Antonio De Agostini
R&D Manager
Georg Fischer Piping Systems
Georg Fischer Piping Systems Ltd. CH-8201 Schaffhausen (Switzerland)
Phone +41(0)52 631 30 26 / info.ps@georgfischer.com / www.gfps.com
161.484.584 / GMST 5906/1e, 4e (07.13)
© Georg Fischer Rohrleitungssysteme AG
CH-8201 Schaffhausen/Schweiz, 2013
Printed in Switzerland
Operating torque (everage value) for opening / closing the
BFV (standard valves in new condition)
DN
Inch
Nm 5bar
Nm 10 bar
50 65 80 100 125 150 200 250
2“ 2 1⁄2“ 3“ 4“ 5“ 6“ 8“ 10“
6 8 14 19 25 33 50 70
12 17 28 38.5 50 61 90 115
300
12“
90
145
Remark: Depending on the application the operating torque
can increase up to 4 times.
CAUTION
Damage to the butterfly valves through the use
of auxiliary equipment to increase the coupling
• Operate valve only with the intended actuating means
(lever, transmission, actuator).
moment.
• If an increased actuating torque occurs, check valve for
damage/wear and tear.
When dismantling the butterfly valve, the following risks can
emerge:
WARNING
When dismantling the butterfly valve, there is a
risk of injury through the uncontrolled leakage
of the medium and/or subsequent flow of the
medium from an open pipeline and/or the butterfly valve.
If the pressure has not been relieved completely and the
pipeline has not been emptied completely, the medium can
leak uncontrollably.
There is a risk of injury depending on the type of the medium.
• Completely relieve pressure from the pipeline before
dismantling.
• In case of harmful, inflammable or explosive media,
completely empty and flush pipeline. After dismantling
the butterfly valve, also let the valve run dry while putting
it in a vertical position.
Consider possible residues.
• Guarantee the safe catching of the medium (e.g. mounting
of a catchment tank) and avoid splashing through
appropriate measures.
• Make sure that opening and closing the pipe is not done
jerkily and that pressure surges in the piping system are
avoided. This has to be observed especially when operating
the pipe with a hand lever.
5. Transport and storage
• Transport and/or store product in unopened original
packaging.
• Protect product from dust, dirt, dampness as well as
thermal and UV radiation.
• Make sure that the product has not been damaged neither
by mechanical nor thermal influences.
• Store product in the same idle position as it has been
delivered.
• Check product for transport damages prior to the
installation.
Gaskets
• All gaskets/collars (material e.g. EPDM, FPM) are
organic materials and react to environmental conditions.
Therefore, store cool, dry and dark in its original
packaging.
• Check gaskets/collars for possible ageing damages such
as tearing or rigidification prior to the installation.
• Sort out defective gaskets/collars.
6. Design
1 Wafer housing
2 Inner body
3 Disc
4 End stop
5 Bearing bush
6 Shaft
7 Large retaining ring
8 Washer
9 Small retaining ring
10 Cap
11 O-ring
7. Installation
Installation into the pipeline
• Only use butterfly valves type 567 as intermediate butterfly
valves
• Use butterfly valves type 568 as intermediate or end
butterfly valves
As connecting part we recommend socket flange adaptor
(SFA) or butt fusion flange adaptor (BFA) with flat sealing
surface in connection with flanges of PVC-U, PP-V or PP/
steel. When SFA / BFA with serrated sealing surface are
used, in individuel cases a flat gasket needs to be added.
Prior to the installation
• Make sure that only butterfly valves are installed whose
pressure category, connection type, connection dimensions
and materials correspond to the operating conditions
• Carry out function test. To do so, close and reopen butterfly
valve.
• Only install butterfly valves without functional
disturbances.
12 Flange sealing
13 Profile sealing
AK 567: 1 2 3
AK 568: 1 2 3
• 1. Allow for sufficient spacing between the flange ends.
Note that the BFV opens counterclockwise.
During the installation
• 2: Put the valve disc at closed position.
• Move the butterfly valve with the seals (O-rings or flat
gaskets) between both flange ends
• 3: Realign the pipeline. Make sure that the disc can be fully
opened
• Fasten the butterfly valve with flange screws (see table 1)
Maximum closing torques for installing the BFV Type 567
DN Inch Nm Inch-lbs
50 2“ 30 256
65 2 ½“ 35 310
80 3“ 40 352
100 4“ 45 398
125 5“ 50 442
150 6“ 60 531
200 8“ 75 664
250 10“ 75 664
300 12“ 80 708
Indexes for fastening the BFV type 567 with flange screws
d DN Inch Schrauben gesamt Max. Drehmoment/ Nm
63 50 2 4 x M16 x 140mm 25
75 65 2 1/2 4 x M16 x 140mm 25
90 80 3 8 x M16 x 150mm 25
110 100 4 8 x M16 x 180mm 30
140 125 5 8 x M16 x 200mm 35
160 150 6 8 x M20 x 220mm 40
225 200 8 8 x M20 x 240mm 50
280 250 10 8 x M20 x 300mm 80
315 300 12 12 x M20 x 300mm 80
Indexes for fastening the BFV type 568 with flange screws
ISO BB - VSB with the various flanges
DN
Quantity of
screws
50 8xM16 55 55 50 55 50 55 50 20
65 8xM16 60 60 50 60 50 60 50 25
80 16xM16 60 65 55 60 55 65 55 15
100 16xM16 65 70 60 70 60 70 60 20
125 16xM16 70 80 70 70 70 80 70 25
150 16xM20 80 80 80 80 70 80 80 35
200 16xM20 90 90 90 90 90 90 80 45
ANSI
Quantity of
screws
2 8xUNC 5/8 55 55 50 55 50 55 50 25
2 1⁄2 8xUNC 5/8 55 60 50 60 50 60 50 25
3 8xUNC 5/8 60 65 55 60 55 65 55 25
4 16xUNC 5/8 65 70 60 60 60 70 60 30
5 16xUNC 3/4 70 80 70 70 70 80 70 35
6 16xUNC 3/4 80 80 80 80 70 80 70 40
8 16xUNC 3/4 90 90 90 90 90 90 80 50
PP PVC-U PVDF
PP-V
PP/
steel
PVC-UPP-V
L
MINLMINLMINLMINLMINLMINLMIN
BB - VSB with the various flanges
PP PVC-U PVDF
PP-V
PP/
steel
PVC-UPP-V
L
MINLMINLMINLMIN
PP/
steel
PP-V
PP/
steel
PP-V
L
MINLMINLMIN
steel
steel
in Nm
PP/
in Nm
PP/
After installing
• Do another function test also after installing.
Chamfering of the SFA / BFA
If SFA/BFA of Georg Fischer are used, chamfering is not
necessary, because the disc doesn’t touch the SFA/BFA or
the BFA already have a chamfer.
If you install a SFA/BFA of another manufacturer, please
observe that the inside diameter (Int-) of the SFA/BFA are larger than the disc outlet diameter (Q1). If necessary you may
chamfer the SFA/BFA as shown in this table below.
Possible consequences of a faulty installation:
A B C
Prior to installation
A: Not enough space between the two flanged pipe sides or
disc is open
B: The butterfly valve gets stuck in the pipeline
C: Pipeline is not well aligned or not at all
8. Disassembly/ Assembly
• Note that there are arrows ∆ on various parts of the
butterfly valves, which enable a quick and correct
assembly. Pictures according the steps, see„Quick Guide“.
8.1 Disassembly BFV 567/ 568
1. Turn disc to ca. 45°
2. Remove cap.
3. Remove the small retaining ring and take out the washer.
4. Remove the large retaining ring and take out the washer
and end stop.
5. Pull the shaft of the butterfly valve up to the upper
bearing bush.
6. Hold the shaft and turn disk to ca. 30°. Pull out shaft
completely.
7. Insert shaft from above at a 15°-position and push out
the upper bearing bush.
8. Pull the shaft of the butterfly valve up to the lower
bearing bush.
9. Hold shaft and turn disc to ca. 30°. Pull out shaft com-
pletely.
10. Insert shaft from above at a 45°-position and push out
the lower bearing bush.
11. Pull out shaft completely and remove the disc.
12. Press out the inner body from the notchless side.
8.2 Assembly BFV 567/ 568
1. Mount large safety ring, mechanical end stop and upper
bearing bush on shaft.
2. Insert inner body into the wafer housing (observe position
of arrow and cam) and move it to the limit stop
3. Insert disc in the open position of 90° (observe position
of arrow).
4. Insert shaft and move it to the limit stop. Watch at the
shape of the shaft when inserting it:
• The notch on the upper side of the shaft indicates the
position of the disc.
• In addition two chamfers at the haft are larger, which
avoids a faulty assembly
5. Insert lower bearing bush and push it into the limit stop.
6. Insert washer and secure it with the small retaining ring.
7. Mount cap and flange sealings (o-rings).
8.3 Assembly hand lever
1 Lever clip
2 Lever
3 Spring
4 Lever catch
5 Screws
6 Index plate
7 End stop
8 Washers
9 Nuts
1. Hand lever assembled by closed disc. By the indexation of the shaft and the end stop a clear assembly is
ensured.
2. With view of the moulded GF logo disc at the wafer housing, the hand lever stands in closed position of the disc
to the right direction.
Closing torque for hand lever connection 15 Nm
8.4 Turn of the hand lever
To turn the hand lever at 180 degrees take the following
steps:
1. Butterfly valve is in closed position. Washer at the hand
Max. closing torque
lever solve easily. Do not remove it completely.
2. Open the lever clip with a screwdriver. Additionally by
the dimensions DN200-300 unscrew the boltes between
handlever and end stop.
3. Bring the screwdriver between raster element and
hand lever. Afterwards move the screwdriver upwards to
unlock the end stop.
4. Take nut and washer complete from the hand lever.
5. Turn hand lever and raster element at 180 degrees. End
stop remains on the shaft.
6. Reassemble hand lever and raster element at the butterfly valve.
7. Assemble the hand lever in closed position of the disc.
Lock the hand lever clip.
8. Finish the assembly of the hand lever with nut and
washer.
9. Maintenance
Max. closing torque
During normal operation, butterfly valves do not need
servicing. But it is recommended to maintain the butterfly
valves latest after 5000 cycles. The following provisions must
be taken:
• Periodic inspection to make sure that there is no leakage
of media to the outside. If media is exiting at the flanged
connectors, they have to be tightened according to Table 2.
In case of leaks or other disturbances, Chapters 1 to 5 must
be observed.
• It is recommended to once or twice a year operate butterfly
valves that are always in the same position in order to test
their functionality.
• Depending on the operating conditions, the collars should
be periodically lubricated with grease (silicone-based).
• It is recommended that the o-rings of the bearing bushes
are checked and if necessary exchanged after each
disassembly.
10. Troubleshooting List
In case of leakage, dismount butterfly valves and replace
damaged gaskets/collars. Order spare parts for butterfly
valves with complete specifications, e.g. all details regarding
the type plates. Only use original parts of GF Piping Systems.
Problem Conse-
Cause Solution
quence
BFV does
not fit
between the
flanges
Disc cannot
be opened
Installation
not possible
Flow rate
too low
Flanges are
too close to
each other
Disc is open • Close disc
Disc touches
SFA/BFA
completely
BFV can
hardly be
opened/
closed or
cannot be
opened/
closed at all
actuating
torque too
high
Operating
conditions
such as
media,
temperature
and pressure
are possible
outside of the
specifications
Leaky BFV /
connecting
elements
Medium is
exiting
Gasket is
damaged
irregular
tightening
of the flange
screws
SFA/BFA with
fluted sealing
face
Selection of lubricants
CAUTION
Material damage due to inappropriate lubricants
that corrode the materials that butterfly valves
and/or gaskets are made of.
• Make sure that no lubricants are used that are based on
mineral oil or Vaseline (petrolatum).
• Observe special manufacturer’s notice for
paint-compatible butterfly valves.
• Lubricate all gaskets with grease based on silicone
or polycol. Other lubricants are not permissible.
10. Spare parts
Spare parts are available at your local Georg Fischer
sales company or on the Internet
at www.piping.georgfischer.com/de
The technical data are not binding. They neither
constitute expressly warranted characteristics nor
guaranteed properties nor a guaranteed durability.
They are subject to modification. Our General Terms
of Sale apply.
• Push flange
apart with
spreading tool
• Bevel SFA/
BFA according
to Table
• Replace
valve
Contact
manufacturer
• Replace
gasket
• Evenly
tighten flange
screws
criss-cross
according to
Table Screw
fixation
• Use SFA/BFA
with even
sealing face