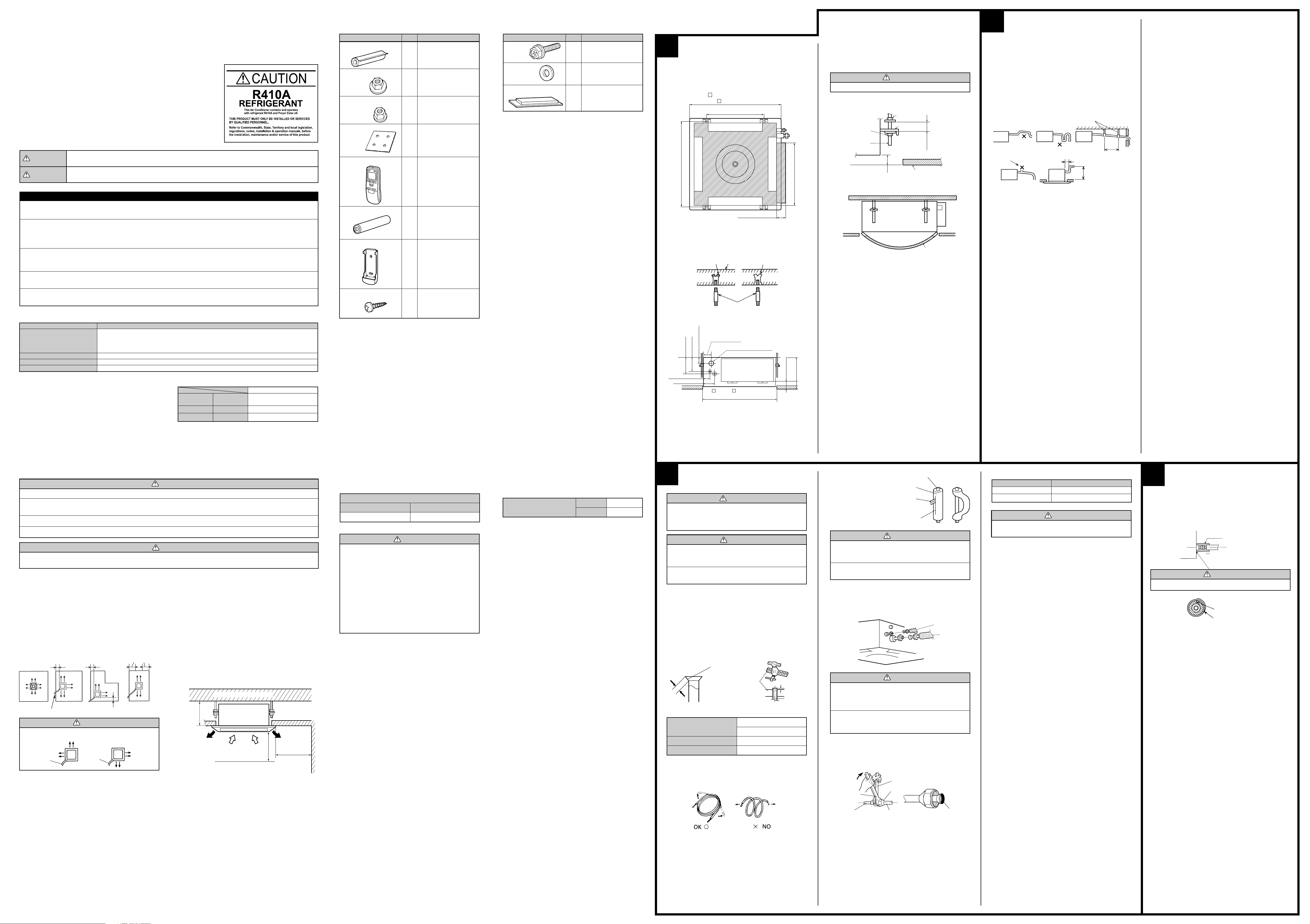
SPLIT TYPE AIR CONDITIONER
(5-5/32”)
131 mm
(4-3/8”)
111 mm
47 mm (1-27/32”)
60 mm (2-3/8”)
Drain pipe (I. D. ø32 mm)
600 mm ( 23-5/8”)
(Ceiling opening measurement)
46 mm (1-27/32”)
86 mm (3-3/8”)
250 mm (9-27/32”)
54 mm (2-1/8”)
INSTALLATION INSTRUCTION
SHEET
STANDARD PARTS
The following installation parts are furnished. Use them as required.
INDOOR UNIT ACCESSORIES
Name and Shape
Coupler heat insulation
Special nut A (large flange)
Special nut B (small flange)
Template
Q’ty
For indoor side pipe joint
2
For installing indoor unit
4
For installing indoor unit
4
For ceiling hole cutting
Application
GRILLE ACCESSORIES
Name and Shape
Bolt
Washer
Blower cover insulation
Q’ty
For mounting grille
4
For mounting grille
4
For discharged air
2
Application
INSTALLATION PROCEDURE
Install the room air conditioner as follows:
1
INDOOR UNIT INSTALLATION
1. Position the ceiling hole and hanging bolts as
shown in Fig. 3.
Fig. 3
( 650 mm) (Grille measurement)
650 mm (25-15/32”)
(
(Hanging bolt position)
400 mm (15-3/4”)
3. Body installation
(1) Install special nut A, then special nut B onto the hanging bolt. (Fig. 6)
(2) Raise the body and mount its hooks onto the hanging bolt between
the special nuts. (Fig. 6)
(3) Turn special nut B to adjust the height of the body. (Fig. 6)
(4) Leveling
Using a level, or vinyl hose filled with water, fine adjust so that the
body is level.
WARNING
Perform final tightening by tightening the double nut firmly.
Fig. 6
Special nut A
After installing the
body, tighten the nuts.
Special nut B
Hook
2
Note: Install the drain pipe.
••
• Install the drain pipe with downward gradient (1/50 to 1/100) and so
••
there are no rises or traps in the pipe.
••
• Use general hard polyvinyl chloride pipe (VP25) [outside diameter 32
••
mm (1-1/4”)] and connect it with adhesive (polyvinyl chloride) so that
there is no leakage.
••
• When the pipe is long, install supporters.
••
••
• Do not perform air bleeding.
••
••
• Always heat insulate the indoor side of the drain pipe.
••
••
• When desiring a high drain pipe height, raise it up to 400 mm (15”) or
••
less from the ceiling within a range of 150 mm (6”) from the body. A
rise dimension over this range will cause leakage.
INSTALLING DRAIN PIPE
Fig. 8
Supporter
(PART NO. 9374318025)
WARNING
CAUTION
The basic installation work procedures are the same as conventional refrigerant models.
However, pay careful attention to the following points:
(1) Since the working pressure is 1.6 times higher than that of conventional refrigerant models, some of the piping and
installation and service tools are special. (See the table below.)
Especially, when replacing a conventional refrigerant model with a new refrigerant R410A model, always replace the conventional piping and flare nuts with the R410A piping and flare nuts.
(2) Models that use refrigerant R410A have a different charging port thread diameter to prevent erroneous charging with con-
ventional refrigerant and for safety. Therefore, check beforehand. [The charging port thread diameter for R410A is 1/2 UNF
20 threads per inch.]
(3) Be more careful that foreign matter (oil, water, etc.) does not enter the piping than with refrigerant models. Also, when
storing the piping, securely seal the openings by pinching, taping, etc.
(4) When charging the refrigerant, take into account the slight change in the composition of the gas and liquid phases, and
always charge from the liquid phase side whose composition is stable.
Special tools for R410A
Tool name
Gauge manifold
Charge hose
Vacuum pump
Gas leakage detector
This mark indicates procedures which, if improperly performed, might lead to the death or serious injury of
the user.
This mark indicates procedures which, if improperly performed, might possibly result in personal harm to
the user, or damage to property.
This air conditioner uses new refrigerant HFC (R410A).
Contents of change
Pressure is high and cannot be measured with a conventional gauge. To prevent erroneous mixing of other
refrigerants, the diameter of each port has been changed.
It is recommended the gauge with seals –0.1 to 5.3 MPa (–76 cmHg to 53 kgf/cm2) for high pressure.
–0.1 to 3.8 MPa (–76 cmHg to 38 kgf/cm2) for low pressure.
To increase pressure resistance, the hose material and base size were changed.
A conventional vacuum pump can be used by installing a vacuum pump adapter.
Special gas leakage detector for HFC refrigerant R410A.
Remote control unit
Battery (penlight)
Remote control unit holder
Tapping screw (ø3 × 12)
1
Use for air conditioner
operation
1
For remote control unit
2
For mounting the remote
control unit
1
For remote control unit
holder installation
2
606 mm (23-27/32”)
(Hanging bolt position)
440 mm (17-5/16”)
66 mm (2-19/32”)
2. Hanging preparations
Firmly fasten the hanging bolts as shown in Fig. 4 or by another method.
Fig. 4
Hole-in anchor
Hole-in plug
Fig. 5
Concrete
Hanging bolt
M10
Insert
Fig. 7
Hanging bolt
15 mm (19/32”)
30 mm
or more
Ceiling
Vinyl hose
Air bleeding
Rise
Trap
150 mm (6”) or less
1.5 to 2.0 m (5 to 6.5 ft)
Max. 400 mm (15”)
Copper pipes
It is necessary to use seamless copper pipes and it is desirable that the amount
of residual oil is less than 40 mg/10 m. Do not use copper pipes having a
collapsed, deformed or discolored portion (especially on the interior surface).
Otherwise, the expansion valve or capillary tube may become blocked with
contaminants.
As an air conditioner using R410A incurs pressure higher than when using
R22, it is necessary to choose adequate materials.
Thicknesses of copper pipes used with R410A are as shown in Table 1. Never
use copper pipes thinner than 0.8 mm (Nominal diameter is 1/4 in., 1/2 in.),
even when it is available on the market.
Table 1 Thicknesses of Annealed Copper Pipes
Thickness (mm)
Nominal
diameter (inch)
1/4
1/2
Outer diameter
(mm)
6.35
12.70
R410A
0.80
0.80
For authorized service personnel only.
WARNING
(1) For the air conditioner to operate satisfactorily, install it as outlined in this installation instruction sheet.
(2) Connect the indoor unit and outdoor unit with the air conditioner piping and cords available from our standards parts. This
installation instruction sheet describes the correct connections using the installation set available from our standard parts.
(3) Installation work must be performed in accordance with national wiring standards by authorized personnel only.
(4) Do not turn on the power until all installation work is complete.
CAUTION
This installation instruction sheet describes how to the indoor unit only.
To install the outdoor unit, refer to the installation instruction sheet included with the outdoor unit.
••
• Be careful not to scratch the air conditioner when handling it.
••
••
• After installation, explain correct operation to the customer, using the operating manual.
••
••
• Let the customer keep this installation instruction sheet because it is used when the air conditioner is serviced or moved.
••
SELECTING THE MOUNTING POSITION
Especially, the installation place is very important for the split type air conditioner because it is very difficult to move from place after the first installation.
Decide the mounting position together with the customer as follows:
The discharge direction can be selected as shown below.
Fig. 1
100 mm (4”) or more
(4 directions)
Piping position
(3 directions)
100 mm (4”) or more
(2
directions
)
100 mm (4”) or more
1,000 mm (39”) or more
(2
directions
)
CAUTION
Since 2-way outlet as shown below causes performance
problems, do not set it.
Pipe
Pipe
INDOOR UNIT
(1) Install the indoor unit on a place having a sufficient strength so that it
withstands against the weight of the indoor unit.
(2) The inlet and outlet ports should not be obstructed; the air should be
able to blow all over the room.
(3) Leave the space required to service the air conditioner. (Fig. 2)
(4) The ceiling rear height is 250 mm (9-3/8”) or more.
(5) A place from where the air can be distributed evenly throughout the
room by the unit.
(6) A place from where drainage can be extracted outdoors easily.
Fig. 2
Strong and durable ceiling
250 mm
(9-3/8”)
or more
1,000 mm (39”)
or more
Obstruction
1,000 mm (39”)
or more
CONNECTION PIPE REQUIREMENT
Table 2
Diameter
Small
6.35 mm (1/4 in.)
••
• Use pipe with water-resistant heat insulation.
••
CAUTION
Install heat insulation around both the gas and liquid pipes.
Failure to do so may cause water leaks.
Use heat insulation with heat resistance above 120 °C. (Reverse cycle model only)
In addition, if the humidity level at the installation location
of the refrigerant piping is expected to exceed 70%, install
heat insulation around the refrigerant piping. If the expected humidity level is 70-80%, use heat insulation that
is 15 mm or thicker and if the expected humidity exceeds
80%, use heat insulation that is 20 mm or thicker.
If heat insulation is used that is not as thick as specified,
condensation may form on the surface of the insulation.
In addition, use heat insulation with heat conductivity of
0.045 W/(m·K) or less (at 20 °C).
Large
12.7 mm (1/2 in.)
ELECTRICAL REQUIREMENT
••
• Electric wire size:
••
Table 3
Connection cord (mm2)
••
• Always use H07RN-F or equivalent to the connection cord.
••
••
• Install the circuit breaker nearby the units. (Both indoor unit and out-
••
door unit)
MAX. 2.5
MIN. 1.5
3
CONNECTING THE PIPING
WARNING
Do not use the existing piping and flare nuts.
• If the existing materials are used, the pressure inside the
refrigerant cycle will rise and cause breakage, injury, etc.
(Use the special R410A materials.)
CAUTION
(1) Do not use mineral oil on flared part.
Prevent mineral oil from getting into the system as this
would reduce the lifetime of the units.
(2) While welding the pipes, be sure to blow dry nitrogen
gas through them.
1. FLARING
(1) Cut the connection pipe to the necessary length with a pipe cutter.
(2) Hold the pipe downward so that cuttings will not enter the pipe and
remove the burrs.
(3) Insert the flare nut (always use the flare nut attached to the indoor
and outdoor units respectively) onto the pipe and perform the flare
processing with a flare tool.
Use the special R410A flare tool, or the conventional flare tool.
When using the conventional flare tool, always use an allowance adjustment gauge and secure the A dimension shown in table 4.
Fig. 9
L
Check if [L] is flared uniformly
and is not cracked or scratched.
Die
A
Pipe
Table 4 Pipe outside diameter
Pipe outside diameter
Flare tool for R410A, clutch type
6.35 mm (1/4 in.)
12.7 mm (1/2 in.)
A (mm)
0 to 0.5
0 to 0.5
2. Bending pipes
The pipes are snapped by your hands. Be careful not to collapse them.
Fig. 10
When bending the pipe, do not
bend it as is. The pipe will be
collapsed. In this case, cut the
heat insulating pipe with a
sharp cutter as shown in Fig.
11, and bend it after exposing
the pipe. After bending the pipe
as you want, be sure to put the
heat insulating pipe back on the
pipe, and secure it with tape.
Fig. 11
Heat insulating
pipe
Cutter
Cut line
Pipe
CAUTION
(1) To prevent breaking of the pipe, avoid sharp bends.
Bend the pipe with a radius of curvature of 150 mm or
over.
(2) If the pipe is bent repeatedly at the same place, it will
break.
3. Connection pipes
••
• Indoor unit side
••
Fig. 12
(1) Be sure to apply the pipe against the port on the in-
door unit correctly. If the centering is improper, the flare
nut cannot be tightened smoothly. If the flare nut is
forced to turn, the threads will be damaged.
(2) Do not remove the flare nut from the indoor unit pipe
unit immediately before connecting the connection
pipe.
When the flare nut is tightened properly by your hand, hold the body side
coupling with a separate spanner, then tighten with a torque wrench. (Fig.
13)
Fig. 13
Torque wrench
Indoor unit
Small pipe
Large pipe
CAUTION
Tighten with two wrenches.
Wrench (fixed)
Flare nut
Table 5 Flare nut tightening torque
Flare nut
Small pipe (6.35 mm dia.)
Large pipe (12.7 mm dia.)
Tightening torque
14 to 18 N·m (140 to 180 kgf·cm)
50 to 62 N·m (500 to 620 kgf·cm)
CAUTION
Be sure to connect the large pipe after connecting the small
pipe completely.
4
INSTALLING THE COUPLER
HEAT INSULATION
After checking for gas leaks, insulate by wrapping insulation around the
two parts (large and small) of the indoor unit coupling, using the coupler
heat insulation.
Fig. 14
Coupler heat insulation
Body
Be sure to overlap the
insulation
CAUTION
Must fit tightly against body without any gap.
No gap
Coupler heat insulation
Indoor unit
pipe
Extend the pipe
by unwinding it.
Do not bend the pipes in an angle more than 90°.
When pipes are repeatedly bent or stretched, the material will harden,
making it difficult to bend or stretch them any more. Do not bend or stretch
the pipes more than three times.
Connection pipe
To prevent gas leakage,
coat the flare surface with
alkylbenzene oil (HAB).
Do not use mineral oil.
- Continued on back -
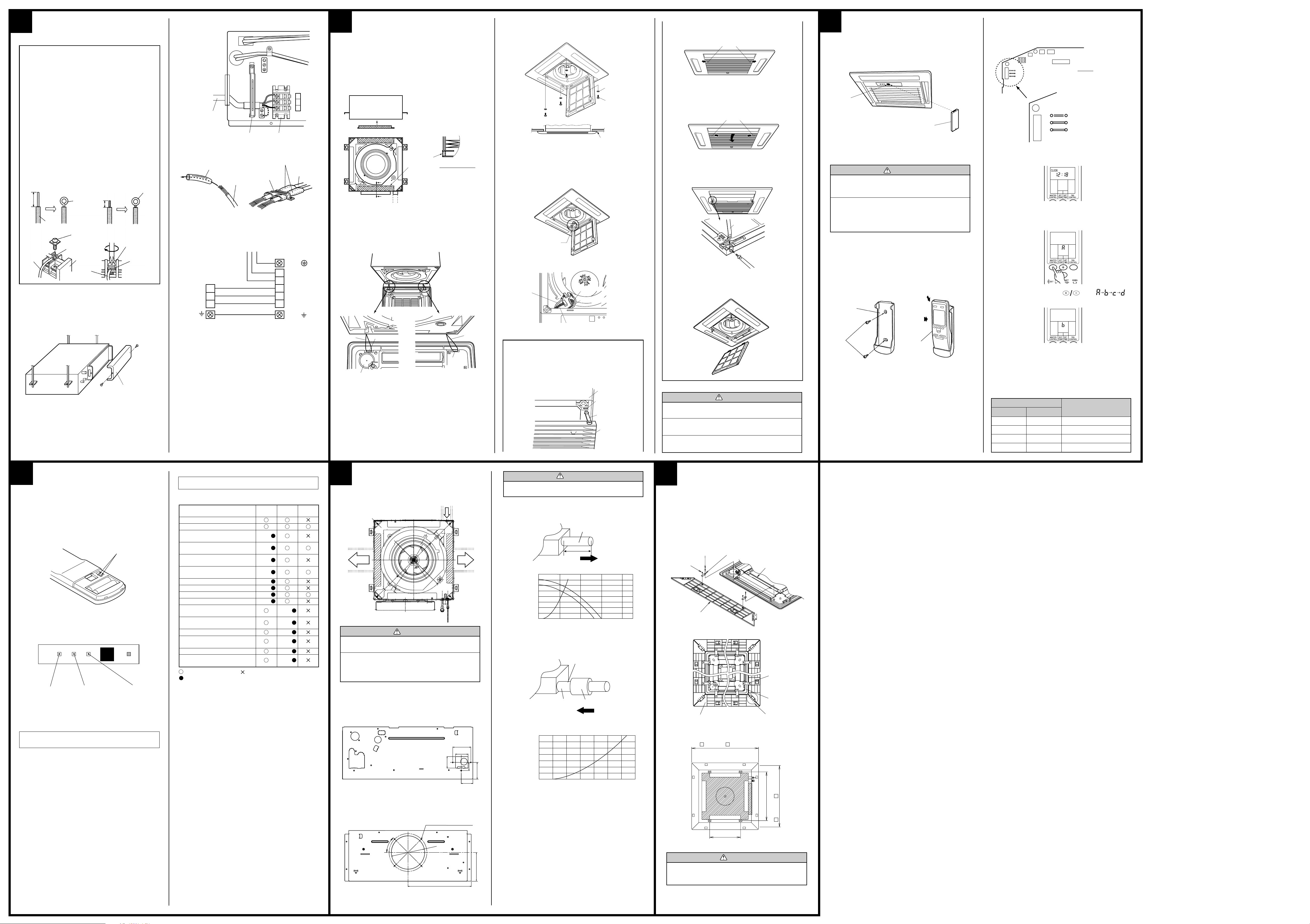
5
Blower cover
insulation
A-A Section view
A
A
Display PCB wire harness
Wire (Louver)
SWING TIMER OPERATION
MANUAL
AUTO
6-ø3.3 Self tapping
screw holes (for 4mm)
P.D 170
130
284
45˚
ø150
(m3/min)
80
70
60
50
40
30
20
10
0
0
2468
AU18
AU12,14
L=5m
DUCT
STATIC
PRESSURE
(Pa)
(m3/min)
70
60
50
40
30
20
10
0
0 0.1 0.2 0.3
(Pa)
DUCT
STATIC
PRESSURE
400mm (15-3/4”)
606mm(23-27/32”)
720mm( 28-11/32”)
770mm ( 30-5/16”)
(Hanging bolt position)
(Ceiling opening measurement)
(Grille measurement)
(Hanging bolt position)
Green/Yellow
1
2(N)
3
L
N
1
2(N)
3
EARTH
EARTH
ELECTRICAL WIRING
HOW TO CONNECT WIRING TO THE TERMINALS
A. For solid core wiring (or F-cable)
(1) Cut the wire end with a wire cutter or wire-cutting pliers, then strip
the insulation to about 25 mm (15/16”) of expose the solid wire.
(2) Using a screwdriver, remove the terminal screw(s) on the terminal
board.
(3) Using pliers, bend the solid wire to form a loop suitable for the
terminal screw.
(4) Shape the loop wire properly, place it on the terminal board and
tighten securely with the terminal screw using a screwdriver.
B. For strand wiring
(1) Cut the wire end with a wire cutter or wire-cutting pliers, then strip
the insulation to about 10 mm (3/8”) of expose the strand wiring.
(2) Using a screwdriver, remove the terminal screw(s) on the terminal
board.
(3) Using a round terminal fastener or pliers, securely clamp a round
terminal to each stripped wire end.
(4) Position the round terminal wire, and replace and tighten the ter-
minal screw using a screwdriver.
Fig. 15
A. Solid wire
Insulation
Strip 25 mm (15/16”)
Wire
B. Strand wire
Loop
Strip 10 mm (3/8”)
Screw with
special washer
Round terminal
Terminal
board
Wire
Round
terminal
Screw with
special washer
Round
terminal
1. Indoor unit side
(1) Remove the control box cover and install the connection cord.
(Figs. 16 and 17)
Fig. 16
Control box cover
Fig. 17
Connection cord
Insulation tube
After passing the connection
cord through the insulation
tube, fasten it with the cord
clamp.
Fig. 18
Indoor unit
side terminal
Connection cord
Power supply
Terminal boardCord clamp
Insulation tube (Use VW-1,
0.5 to 1.0 mm thick, PVC
tube as the insulation tube)
Cord clamp
Outdoor unit
side terminal
Connection cord
6
GRILLE INSTALLATION
1. Blower cover insulation
Install the blower cover insulation only when the outlet direction is not
specified.
Two blower cover insulations are packed with the grille assembly. Install
the blower cover insulation at the diffuser position shown in Fig. 19. At the
time, use the piping position as the criteria.
Fig. 19
2 direction example
Fit the blower cover insulation.
(Piping direction)
2. Installing grille assembly to body
Hang the grille assembly on the wires attached to the indoor unit as shown
in Fig. 20.
Fig. 20
Wire Wire hook
Wire hook
Motor cover assembly
Wire
Bolting the grille assembly to the body
Install the grille assembly to the body with the four bolts, spring washers,
and washers.
Fig. 21
Washer
Bolt
No gap between ceiling and
grille around entire periphery.
Wireless unit connection wire wiring
Connect the connector in accordance part A detail view.
Then clamp the lead wire with clamp so that it does not touch the rotating
parts.
Fig. 22
Fig. 23 Part A detail view
Display PCB
wire harness
Joint wire (Louver)
INSTALLING/REMOVING THE INTAKE GRILLE
1. Installing the intake grille
(1) Fully insert the intake grille hooks into the rectangular holes in the
panel.
Fig. 24
Panel
Rectangular hole
Grille hook
Intake grille
(2) Close the intake grille, then slide the two grille stoppers outward.
Fig. 25
Grille stopper
2. Removing the intake grille
(1) Slide the two grille stoppers inward, then open the intake grille.
Fig. 26
Grille stopper
(2) Remove the grille hook screws, then open the intake grille.
Fig. 27
(3) Open the intake grille so that it is at an angle of 20° to 40°, then
remove the grille.
Fig. 28
CAUTION
(1) The louver angle cannot be changed if the power is not
on, (If moved by hand, it may be damaged.)
(2) The grille assembly is directional relative to the air con-
ditioner body.
(3) Install so that there is no gap between the grille as-
sembly and the air conditioner body.
7
REMOTE CONTROL UNIT
INSTALLATION
••
• Install the remote control unit so that the front is facing the photocell.
••
(Fig. 29)
Fig. 29
Photocell
Remote control unit
••
• Install the remote control unit with a distance of 5 m between the re-
••
mote control unit and the grille photocell as the criteria.
However, when installing the remote control unit, check that it operates
positively.
CAUTION
(1) Check that the indoor unit correctly receives the sig-
nal from the remote control unit, then install the remote
control unit holder.
(2) Select the remote control unit holder selection site by
paying careful attention to the following:
Avoid places in direct sunlight.
Select a place that will not be affected by the heat from
a stove, etc.
1. REMOTE CONTROL UNIT HOLDER
INSTALLATION
• Install the remote control unit holder to a wall, pillar, etc. with the tap-
ping screws.
Fig. 30
Remote Control
Unit mounting
Remote control
unit holder
Tapping
screws
(small)
Remote Control Unit
holder fixing
1 Set
2 Push
Remote
control unit
2. SWITCHING REMOTE CONTROL UNIT SIGNAL
CODES
• Air conditioner settings
Fig. 31
Indoor unit
Printed circuit board
• Remote control unit settings
(1) Press the START/STOP button and display only the clock.
Fig. 32
(2) Press the MASTER CONTROL button continuously for more than five
seconds to display the current signal code.
Fig. 33
(3) Change the signal code with the button ( ).
Fig. 34
(4) Press the MASTER CONTROL button again to return to the clock
display and change the signal code.
Confirm the setting of the remote control unit signal code and the printed
circuit board setting.
If these are not confirmed, the remote control unit cannot be used to operate for the air conditioner.
Table 6
Jumper wire
JM2
Connect
Connect
Disconnect
Disconnect
JM3
Connect
Disconnect
Connect
Disconnect
Remote control unit
signal code
A (Primary setting)
B
C
D
8
• Perform test operation and check items (1) to (5) below.
• For the operation method, refer to the operating manual.
• The outdoor unit may not run, depending on the room temperature.
In this case, the ‘TEST RUN’ signal is received during air conditioner
operation (use a metallic object to short the two metal contacts under
the battery compartment lid and send the ‘TEST RUN’ signal from the
remote control unit).
TEST RUNNING
Fig. 35
Short the two metal contacts under
the battery compartment lid.
• To end test operation, press the remote control unit START/STOP button.
(When the air conditioner is run by pressing the remote control unit
TEST RUN button, the OPERATION and TIMER lamps will simultaneously flash slowly.)
SWING LAMP
(Orange)
Operation can be checked by lighting and flashing of the grille display
section OPERATION and TIMER lamps.
Perform judgment in accordance with the following.
• Test running
When the air conditioner is run by pressing the remote control unit test
run button, the OPERATION and TIMER lamps flash slowly at the same
time.
TIMER LAMP
(Green)
OPERATION
LAMP (Red)
• Error
The OPERATION, TIMER and SWING lamps operate as follows
(Table 7) according to the error contents.
Table 7
Error contents
Indoor EEPROM abnormal
Outdoor EEPROM abnormal
Indoor room temperature sensor
open
Indoor room temperature sensor
shortcircuited
Indoor heat exchanger temperature
sensor open
Indoor heat exchanger temperature
sensor shortcircuited
Float switch operated
Indoor signal abnormal
Outdoor signal abnormal
Indoor fan abnormal
Outdoor power source connection
abnormal
Outdoor heat exchanger
temperature sensor error
Outdoor temperature sensor error
Outdoor discharge pipe
temperature sensor error
Outdoor high pressure abnormal
Outdoor discharge pipe
temperature abnormal
: 0.1s ON/0.1s OFF (flash) : OFF
: 0.5s ON/0.5s OFF (flash)
OPERATION
lamp (RED)
(2 times)
(2 times)
(3 times)
(3 times)
(4 times)
(5 times)
(5 times)
(6 times)
TIMER lamp
(GREEN)
(2 times)
(3 times)
(4 times)
(5 times)
(6 times)
(7 times)
SWING lamp
(ORANGE)
CHECK ITEMS
INDOOR UNIT
(1) Is operation of each button on the remote control unit normal?
(2) Does each lamp light normally?
(3) Do not air flow direction louvers operate normally?
(4) Is the drain normal?
(5) Is there any abnormal noise and vibration during operation?
9
OPENING THE DUCT
CONNECTION HOLE
Fig. 36
Distribution
duct
CAUTION
(1) When performing hole opening work, be careful not to
damage the drain pan.
(2) When connecting the distribution duct, to make the air
flow easily, block the outlet port with the blower cover
insulation as shown by the hatched lines in fig. 36. For
the blocking direction, refer to Fig. 19.
1. DIMENSION
(1) Fresh air duct connection hole and screw positions.
Fig. 37
Fresh air
Distribution
duct
Unit: mm
CAUTION
The air conditioner cannot take in fresh air by itself.
When connecting a fresh air duct, always use a duct fan.
OUTLET AIR
Fig. 39
Duct (inside dia. 150 mm)
FRESH AIR
Fig. 40
Duct
Duct Fan
Static pressure required to
take in fresh air
10
INSTALLING THE OPTION
PARTS (ADDITIONAL GRILLE)
THE ADDITIONAL GRILLE
• Mount the assembled additional grille to the indoor unit (grille) that has
been removed from the main unit.
• Make sure all areas are properly installed the reinforcement plate.
• Mount 4 additional grilles. (Fig. 42)
• After confirming proper meshing of the additional grilles, secure them
in place using the 8 screws provided.
Fig. 41
Screw (short)
Additional grille
Fig. 42 Illustration of completed mounting
POSITION THE CEILING HOLE AND HANGING BOLTS
Fig. 43
Screw (long)
Additional grille
Reinforcement plate
Indoor unit (grille)
Reinforcement
plate
Indoor unit (grille)
• Do not operate the air conditioner in the running state for a long time.
(2) Distribution duct connection hole and screw positions.
Fig. 38
Unit: mm
CAUTION
When installing the additional grille, please refer to the installation instruction sheet supplied with the additional
grille.
PART NO. 9374318025