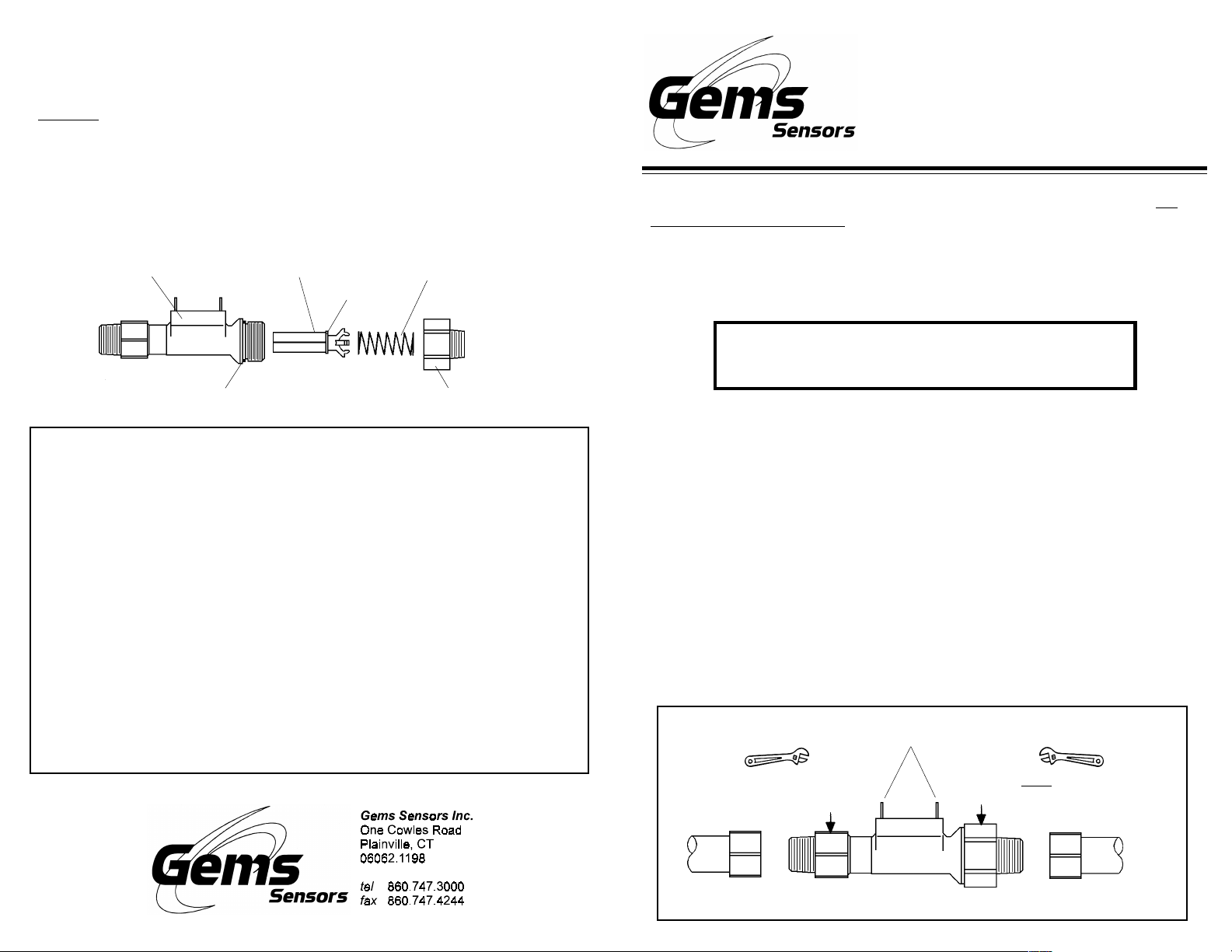
Maintenance . . .Maintenance . . .
Maintenance . . .
Maintenance . . .Maintenance . . .
Any foreign particle accumulation is easily cleared by removing the outlet
fitting and piston/spring assembly and then cleaning the bore.
CautionCaution
Caution
CautionCaution
dislodge the metering disc or damage the spring.dislodge the metering disc or damage the spring.
dislodge the metering disc or damage the spring.
dislodge the metering disc or damage the spring.dislodge the metering disc or damage the spring.
::
During this cleaning operation, take care not to During this cleaning operation, take care not to
:
During this cleaning operation, take care not to
::
During this cleaning operation, take care not to During this cleaning operation, take care not to
During reassembly, remember to clean the O-Ring of any debris that may
have accumulated. Reinstall piston first, then spring, then outlet port
(hand-tight,
onlyonly
only). 150 Micron filtration is suggested.
onlyonly
FS-150
O-Ring
Piston
Metering
Disc
Spring
Outlet Fitting
In-Line Flow SwitchesIn-Line Flow Switches
In-Line Flow Switches
In-Line Flow SwitchesIn-Line Flow Switches
FS-150 SeriesFS-150 Series
FS-150 Series
FS-150 SeriesFS-150 Series
Instruction Bulletin No. 133690Instruction Bulletin No. 133690
Instruction Bulletin No. 133690
Instruction Bulletin No. 133690Instruction Bulletin No. 133690
FS-150 Series Flow Switches operate reliably in any mounted attitude
which they are calibratedwhich they are calibrated
which they are calibrated
which they are calibratedwhich they are calibrated
settings.settings.
settings.
settings.settings.
Unless otherwise specifiedUnless otherwise specified
Unless otherwise specified, units are calibrated in the horizon-
Unless otherwise specifiedUnless otherwise specified
. .
Other attitudes will slightly alter actuationOther attitudes will slightly alter actuation
.
Other attitudes will slightly alter actuation
. .
Other attitudes will slightly alter actuationOther attitudes will slightly alter actuation
tal position.
- Installation -- Installation -
- Installation -
- Installation -- Installation -
- WARNING -- WARNING -
- WARNING -
- WARNING -- WARNING -
The FS-150 is a plastic, NPT-threaded instrument.The FS-150 is a plastic, NPT-threaded instrument.
The FS-150 is a plastic, NPT-threaded instrument.
The FS-150 is a plastic, NPT-threaded instrument.The FS-150 is a plastic, NPT-threaded instrument.
Over-tightening will result in port breakage!Over-tightening will result in port breakage!
Over-tightening will result in port breakage!
Over-tightening will result in port breakage!Over-tightening will result in port breakage!
forfor
for
forfor
Important Points!Important Points!
Important Points!
Important Points!Important Points!
Product must be maintained and
installed in strict accordance with the
National Electrical Code and GEMS product catalog and instruction bulletin. Failure to observe this warning could result in
serious injuries or damages.
An appropriate explosion-proof enclosure or intrinsically safe interface device
must be used for hazardous area applications involving such things as
ited to)
ignitable mixtures, combustible dust
and flammable materials.
Pressure and temperature limitations
shown on individual catalog pages and
drawings for the specified flow switches
must not be exceeded. These pressures
and temperatures take into consideration
possible system surge pressures/temperatures and their frequencies.
Selection of materials for compatibility
with the media is critical to the life and
(but not lim-
operation of GEMS flow switches. Take care
in the proper selection of materials of construction; particularly wetted materials.
Life expectancy of switch contacts varies with
applications. Contact GEMS if life cycle testing is required.
Ambient temperature changes do affect
switch set points, since the specific gravity of
a liquid can vary with temperature.
Flow switches have been designed to resist
shock and vibration; however, shock and vibration should be minimized.
Liquid media containing particulate and/or
debris should be filtered to ensure proper operation of GEMS products.
Electrical entries and mounting points may
require liquid/vapor sealing if located in an enclosed tank.
Flow switches must not be field repaired.
Physical damage sustained by the product
may render it unserviceable.
All plastic NPT threads should be installed using a suitable thread sealant.
(Teflon tape or Permatex
unit during installation.
adjacent to the port being connected during installation, to insureadjacent to the port being connected during installation, to insure
adjacent to the port being connected during installation, to insure
adjacent to the port being connected during installation, to insureadjacent to the port being connected during installation, to insure
sealing of NPT and prevent port breakage. (See Diagram Below)sealing of NPT and prevent port breakage. (See Diagram Below)
sealing of NPT and prevent port breakage. (See Diagram Below)
sealing of NPT and prevent port breakage. (See Diagram Below)sealing of NPT and prevent port breakage. (See Diagram Below)
"No More Leaks")
Always hold the FS-150 by the wrench flatsAlways hold the FS-150 by the wrench flats
Always hold the FS-150 by the wrench flats
Always hold the FS-150 by the wrench flatsAlways hold the FS-150 by the wrench flats
. Sealant must be kept out of
The outlet port on the FS-150 is threaded hand-tight to the body and sealed
via an O-Ring.
ing of the union and cracking.ing of the union and cracking.
ing of the union and cracking. Install fittings or adapters onto flow switch
ing of the union and cracking.ing of the union and cracking.
Improper installation to a process can result in torqu- Improper installation to a process can result in torqu-
Improper installation to a process can result in torqu-
Improper installation to a process can result in torqu- Improper installation to a process can result in torqu-
using strap wrenches. One to two turns past hand-tight is adequate. After
installing unit, electrical connection is made to 1/4" quick-connect terminals
with crimp-type receptacle, supplied by customer.
Quick-Connect
Terminals
Hold Here
When Installing
Inlet Fitting
Hold Here
When Installing
Outlet Fitting
P/N 133690
Rev. K
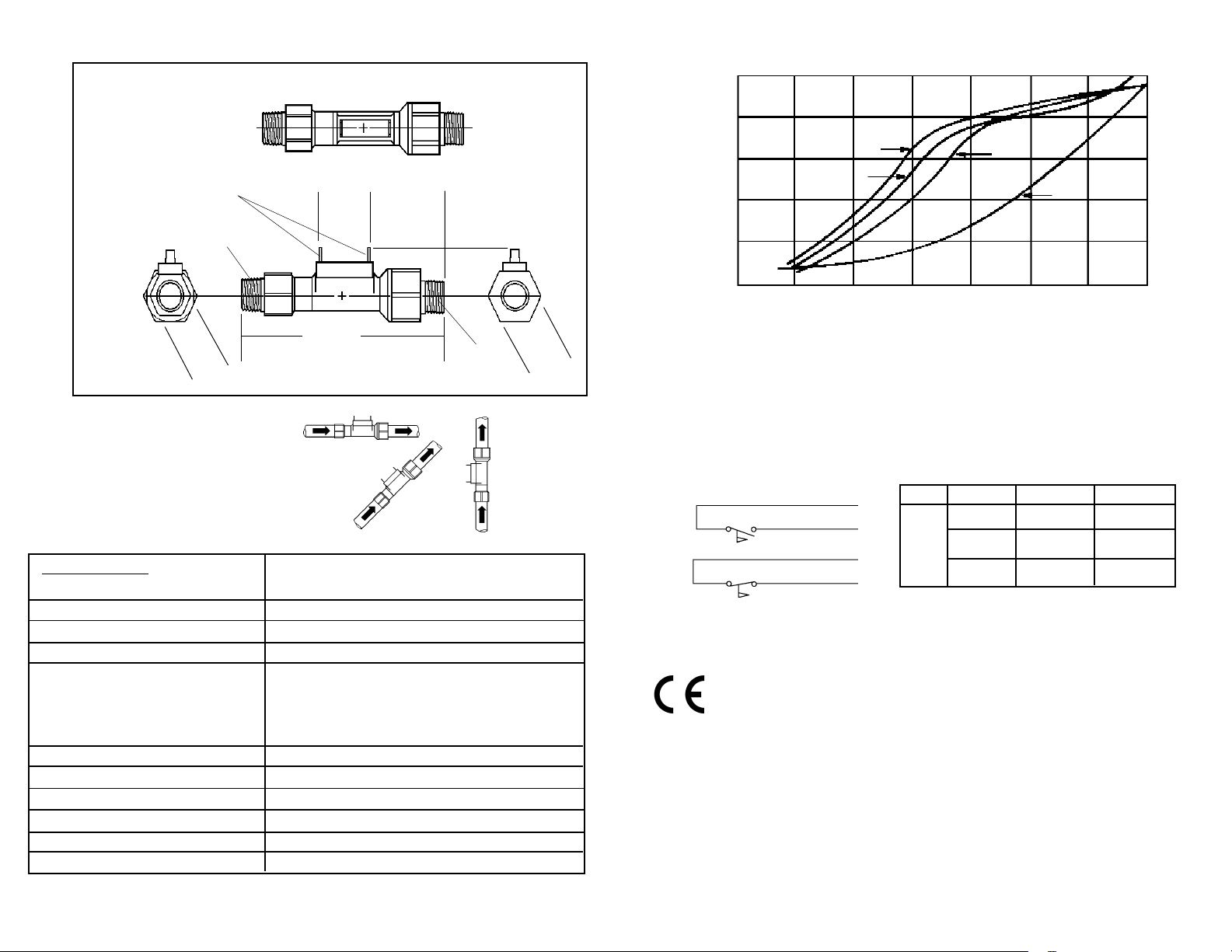
Dimensional Data . . .Dimensional Data . . .
Dimensional Data . . .
Dimensional Data . . .Dimensional Data . . .
7/8"
Dia.
ââ
â
ââ
áá
á
áá
1/4" Quick
Connect Terminals
1/2" NPT
1-1/16"
HEX
Mounting Attitudes . . .Mounting Attitudes . . .
Mounting Attitudes . . .
Mounting Attitudes . . .Mounting Attitudes . . .
Specifications . . .Specifications . . .
Specifications . . .
Specifications . . .Specifications . . .
Wetted Materials
Housing
Piston
O-Ring
Spring
Operating Pressure, Max.
Operating Temperature
Set Point Accuracy
Set Point Differential
Switch, See "Switch Ratings"
Inlet/Outlet Ports
Electrical Termination
**
* Hydrolytically stable, glass-reinforced, polypropylene is UL-recognized to UL746B at a
**
relative temperature index of 65°C
ßß
ß
ßß
VariousVarious
Various
VariousVarious
Polypropylene, Hydrolytically Stable
Ryton® - R4, 316 Stainless Steel
Viton
316 Stainless Steel
200 PSIG @ +70oF to 150oF
(+21.1°C to 65.5°C)
150 PSIG @ +150oF to 212oF
(+65.5°C to +100°C)
0oF to 212oF (-17.8°C to +100°C)
±15%
20%, Maximum
SPST, 20 VA
1/2" NPT Male
1/4" Male Quick Connect Terminals (2)
1-3/8"
ßß
ß
ßß
Ref.
5-29/32"
Ref.
®
àà
à
àà
ßß
ß
ßß
2"- 5/32"
Ref.
àà
à
àà
àà
à
àà
ââ
â
ââ
1-13/64"
Ref.
áá
á
áá
1/2"
NPT
Typical Pressure Drop Typical Pressure Drop
Typical Pressure Drop
Typical Pressure Drop Typical Pressure Drop
5
4
129663129663
129663
3
2
1
Pressure Drop - PSIDPressure Drop - PSID
Pressure Drop - PSIDPressure Drop - PSID
Pressure Drop - PSID
0
01
1-5/16"
HEX
Wiring Diagrams . . .Wiring Diagrams . . .
Wiring Diagrams . . .
Wiring Diagrams . . .Wiring Diagrams . . .
Normally Open
Normally Closed
**
*
**
Tests Conducted with Units in a Horizontal Position
This product is suitable for Class I and Class II applications only, per the
requirements of standard EN60730 and any additional specific requirements for
a particular application or medium being sensed. Class I compliance of metal
bodied units requires a ground connection between the metal body and the
earthing system of the installation. Class I compliance of plastic bodied units in
contact with a conductive medium requires that the medium be effectively
earthed so as to provide an earthed barrier between the unit and accessible
areas. For Class III compliance, a supply at safety extra-low voltage (SELV)
must be provided. Please consult the Factory for compliance information on
specific part numbers.
129663129663
129664129664
129664
129664129664
2
Flow Rate - GPMFlow Rate - GPM
Flow Rate - GPM
Flow Rate - GPMFlow Rate - GPM
(Terminals Up) with water at +70oF)
Switch Ratings - Max. Resistive LoadSwitch Ratings - Max. Resistive Load
Switch Ratings - Max. Resistive Load
Switch Ratings - Max. Resistive LoadSwitch Ratings - Max. Resistive Load
3
VAVA
VA
VAVA
20
. . .. . .
. . .
. . .. . .
VoltsVolts
Volts
VoltsVolts
4
0-30
120
240
129665129665
129665
129665129665
5
Amps ACAmps AC
Amps AC
Amps ACAmps AC
129660129660
129660
129660129660
129661129661
129661
129661129661
129662129662
129662
129662129662
.4
.17
.08
6
Amps DCAmps DC
Amps DC
Amps DCAmps DC
7
.3
.13
.06