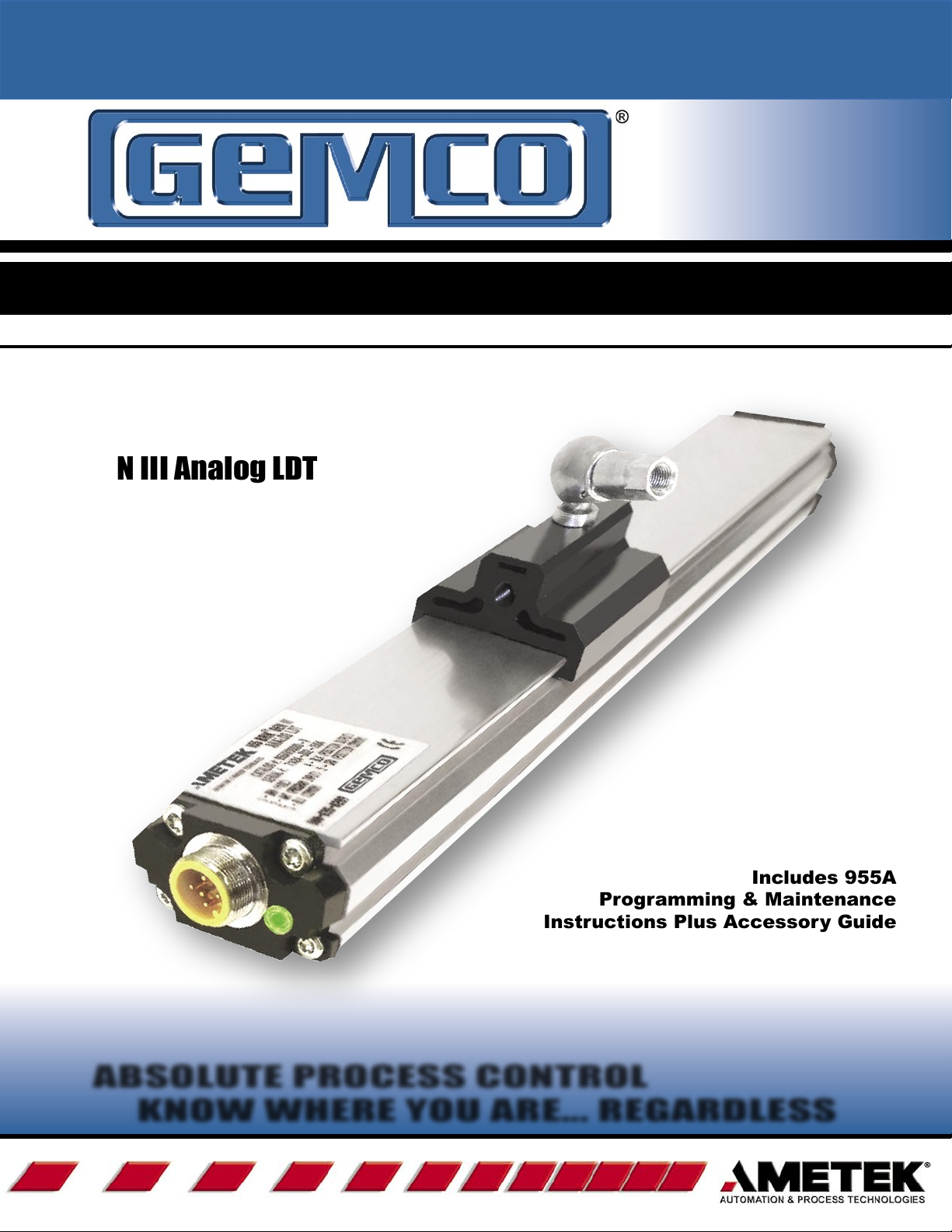
I
NSTALLATION
L
INEAR
D
ISPLACEMENT
MANUAL
T
RANSDUCERS
955A BRIK
GEN III Analog LDT
Series 956
955 Series
Includes 955A
Programming & Maintenance
Instructions Plus Accessory Guide
ABSOLUTE PROCESS CONTROL
KNOW WHERE YOU ARE... REGARDLESS
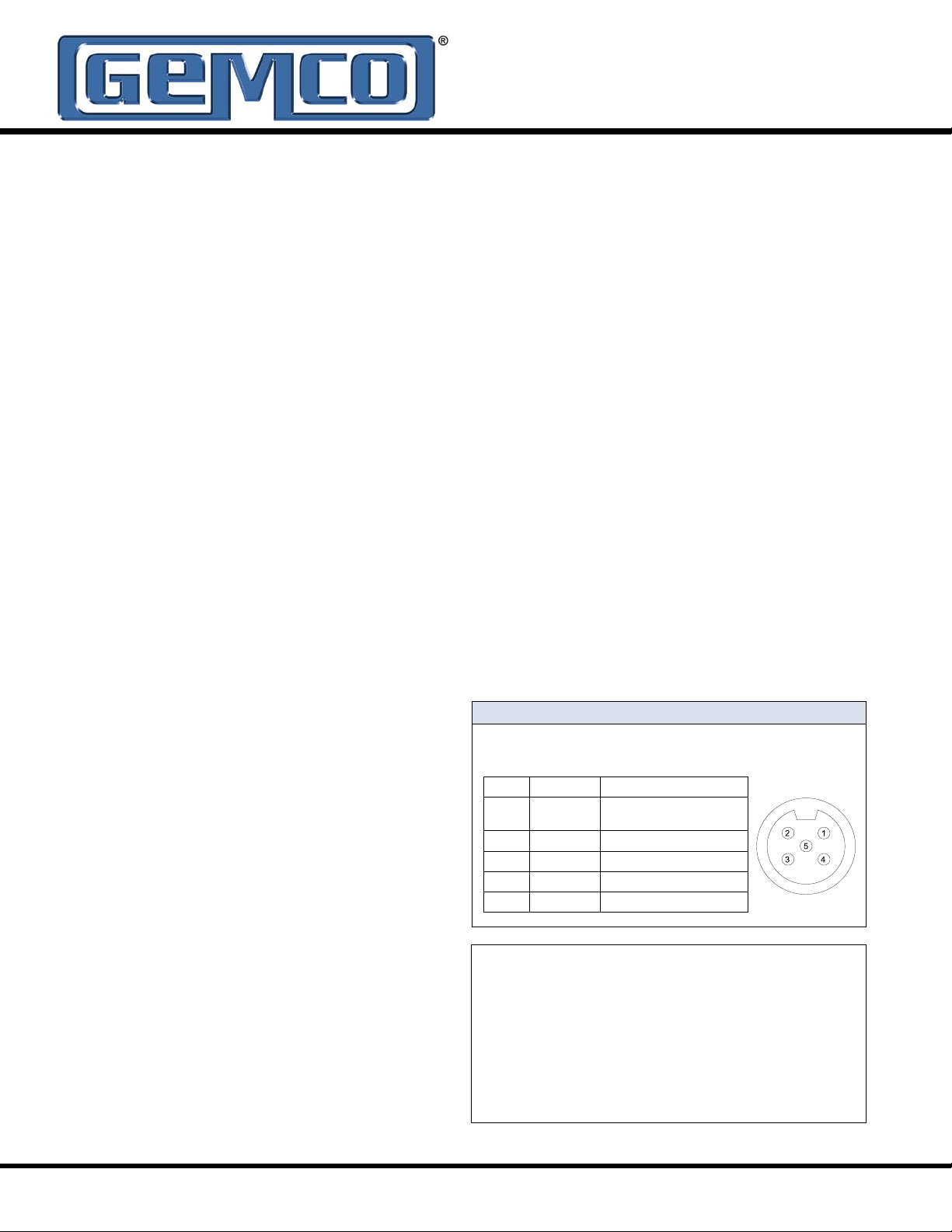
Introduction
The 955A BRIK Gen III is an accurate programmable, autotuning, non-contact, linear displacement transducer in an
economical, low profile package. The transducer utilizes our
field proven magnetostrictive technology to give absolute
position, repeatable to .006% of the programmable sensing
distance. The streamlined anodized aluminum extrusion houses
the sensing element and electronics. The magnet moves over
the sensing element that determines the position and converts
it to an analog output. It can be ordered with a 0 to 10 VDC or 4
to 20mA output.
The 955A BRIK Gen III has a few truly unique features. One
feature is the LDT’s auto-tuning capability, the ability to sense
a magnet other than the standard slide magnet and adjust its
signal strength accordingly. Another feature is that the analog
output is programmable over the entire active stroke length. The
active stroke area of the LDT lies between the Null and Dead
zones.
LED Colors
Green: Magnet is present and within the active programmed
range. Red: Fault, the LDT has lost its signal from the magnet
or the magnet has moved into the Null or Dead zone. Yellow:
The magnet is out of the programmed ZERO to SPAN range.
Note 1: ZERO or SPAN can be adjusted individually
without setting the other. Note 2: ZERO = 0V on 0 to 10 VDC
units and 4mA on 4 to 20mA units.
Setting Zero & Span Positions
The 955A is programmable over the entire active stroke length
of the LDT. Keep in mind that there is a 3” Null area at the
connector end of the LDT and a 2.0” Dead area at the other
end of the LDT that the magnet must stay out of at all times.
The diagnostic LED can aid you in the setup of the Zero and
Span. A green or yellow LED means that it is OK to program
the LDT in this area, a red LED means that the LDT cannot be
programmed in this area.
There is a diagnostic LED located at the connector end of the
probe that remains green while a good magnet signal is present
and when the magnet is in the programmed stroke area. The
LED turns yellow when the magnet is out of the programmed
active range, but still within the active stroke area. The LED
turns red and the output goes to 0 volts on voltage output units,
or 4mA on current output units when there is no magnet present
or when the magnet is out of the sensing area. The unit can
easily be changed in the field from a 0 - 10VDC to a 10 - 0VDC
or 4 - 20mA to a 20 - 4mA .
Mounting
The transducer can be mounted vertically or horizontally using
SD0522000 mounting brackets. The mounting brackets slide
in the grooves on the lower part of the extrusion and clamp
down when tightened. It is recommended to use one mounting
bracket on each end and every three feet between.
Ferro-magnetic material, which is material readily magnetized,
should be placed no closer than .25” from the sensing surface
of the LDT.
Floating Magnet Assembly
When using the Floating Magnet assembly SD0522100, the
magnet should be installed within 3/8” of the sensing surface.
The magnet assembly should also be installed in such a
manner that it remains an even distance from the aluminum
extrusion throughout the entire stroke. Improperly installed
magnets can result in output signal non-linearity.
To set the ZERO and SPAN position for the probe
follow these steps.
1. Power up the probe in normal operating mode (i.e. “PRGM”
pin floating),
2. Place magnet assembly where ZERO is to be located, but
within the active region of probe,
3. Momentarily short “PRGM” pin (pin 2) to ground (pin 3),
4. Place magnet assembly where SPAN is to be located, but
within the active region of the probe,
5. Momentarily short “PRGM” pin (pin 2) to V+ (pin 1).
Wiring Diagram 955A Only
Euro Connector (Micro 12 mm single keyway)
Note: Refer to your specific model number and application
manual for the correct wire diagram and pin location.
Pin # Wire Color Function
1 Brown Customer Supplied Power
(+VDC)
2 White Program Input
3 Blue Power Supply Common
4 Black Position Output
5 Gray Analog Output Common
AMETEK Automation & Process Technologies has checked
the accuracy of this manual at the time it was approved
for printing. However, this manual may not provide all
possible ways of installing and maintaining the LDT. Any
errors found in this manual or additional possibilities to
the installation and maintenance of the LDT will be added
in subsequent editions. Any comments you have for the
improvement of this manual are welcomed. AMETEK
reserves the right to revise and redistribute the entire
contents or selected pages of this manual. All rights to the
contents of this manual are reserved by AMETEK.

Specifications
Input Voltage 13.5 to 30 VDC
Current Draw 2.5 Watts Maximum,
Output 0 to 10 VDC
Resolution
Internal
Analog Output
Non-Linearity +/- 0.05% of Stroke
Repeatbility +/- 0.006% of Full Stroke
Update
40” or less
41” to 100”
101” to 150”
151” to 180”
Operating Temperature -20° to 70° C
Span Length 5” to 180”
Null Zone 3.00”
Dead Zone 2.00”
LED Green = Power is applied and magnet is present.
Connector Standard 5 Pin Micro
Approvals CE
Enclosure IP67, Optional IP68
Specifications are subject to change without notice.
120 mA @ 15 VDC Typical
10 to 0 VDC
4 to 20 mA
20 to 4 mA
0.001”
16 Bit (1 part in 65,535)
1mS (Stroke Lengths 40” - 50”)
2mS (Stroke Lengths 41” - 100”)
3mS (Stroke Legnths 101” - 150”)
4mS (Stroke Lengths 151” - 180”)
Red = Fault, magnet is in the Dead Zone or lost
Yellow = Out of the active programmed range
12mm Euro Connector
Specifications are based on a typical 36” LDT.
Dimensions
Floating Magnet Assembly (SD0522100)
Sensing Surface
NOTE: The north pole of the magnet should be pointed towards the probe.
Mounting brackets (SD0522000) slide in the grooves on the side of the
extruded housing. When tightened down with fastening hardware the
mounting brackets clamp the unit into place. It is recommended to use
one mounting bracket on each end and every three feet between.
A standard female swivel mounting arm is provided with the slide magnet
assembly. For extensions and other options contact the factory.
S
N
Accessories
Item Part Number
Slide Magnet SD0521800
Float Magnet SD0522100
Mounting Foot SD0522000
6 Ft. Cable 949019L6
12 Ft. Cable 949019L12
6 Ft. Cable; Right Angle Connector 949020L6
12 Ft. Cable; Right Angle Connector 949020L12
Part Numbering
955A
955A BRIK
with Analog
Output
Output
V0 = 0 to 10 VDC
V1 = 10 to 0 VDC
C4 = 4 to 20mA
C2 = 20 to 4mA
XX
XXXX
Stroke Length
Insert stroke in inches
to 0.1 inch. Enter as
a four-place number.
Valid lengths are 0050
to 1800. Example:
12.0 inch probe stroke
is entered as 0120.
convert a metric stroke
in millimeters, multiply
millimeter value by
0.03937 to arrive at inch
value.
To
X
Options
X = None
A standard 12 mm 5 pin micro connector is used. Straight mating
cables can be ordered in a 6’ length (949019L6), or 12’ length
(949019L12). If space is a consideration a right angle connector is
also available, (949020L6 or 949020L12).
* WARNING: do not use cord sets with LED’s
Differential Input
Power +
Supply
_
Customer Supplied Power (Brown)
Power Supply Common (Blue)
Program Input (White)
955A
LDT
Single Ended Input
Power +
Supply
_
Customer Supplied Power (Brown)
Power Supply Common
Program Input
(White)
955A
LDT
Note: 955A-C is current sourcing, which allows the current to flow from the LDT into
the user’s equipment.
Position Output (Black)
Position Common (Gray)
Position Output (Black)
(Blue)
+ Input
- Input
+ Input
Common