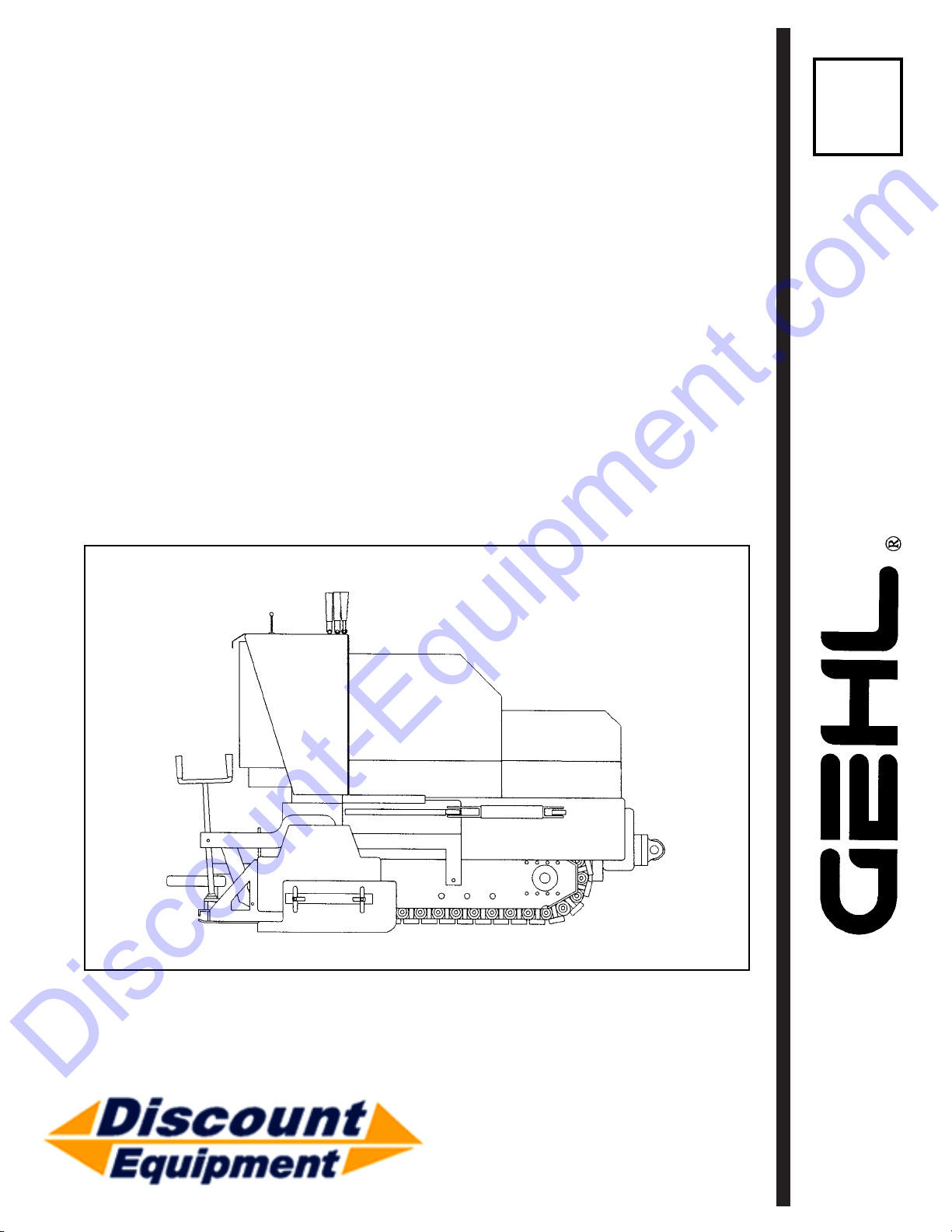
1639/1649
PowerBox
Self Propelled
Paver
OPERATOR’S MANUAL
www.discount-equipment.com
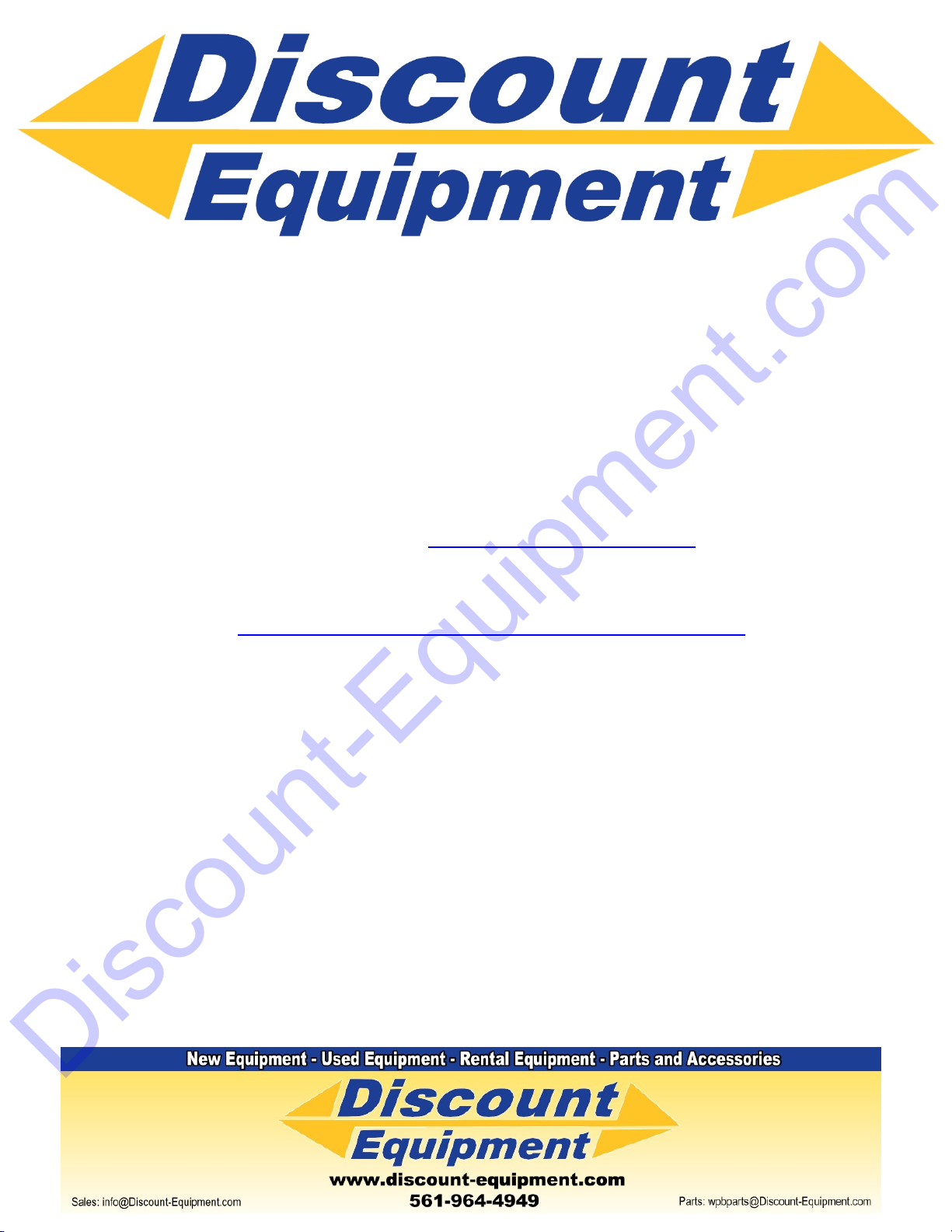
Discount-Equipment.com is your online resource for commercial and industrial
quality parts and equipment sales.
Locations:
Florida (West Palm Beach): 561-964-4949
Outside Florida TOLL FREE: 877-690-3101
Need parts? Check out our website at www.discount-equipment.com
Can’t find what you need?
Click on this link: http://www.discount-equipment.com/category/5443-parts/ and fill out
the request form.
Please have the machine model and serial number available in order to help us get
you the correct parts. One of our experienced staff members will get back to you with
a quote for the right part that your machine needs.
We sell worldwide for the br
Diamond
Chicago Pneumatic, Allmand Brothers, Essick, Miller Spreader, Skyjack, Lull, Skytrak,
Tsurumi, Husquvarna/Target, Whiteman-Concrete/Mortar, Stow-Concrete/Mortar, Baldor,
Wacker, Sakai, Snorkel, Upright, Mi-T-M, Sullair, Neal, Basic, Dynapac, MBW, Weber,
Bartell, Bennar Newman, Haulotte, Ditch Runner, Blaw-Knox, Himoinsa, Best, Buddy,
Crown, Edco, Wyco, Bomag, Laymor, Terremite, Barreto, EZ Trench, Takeuchi, Basic, Bil-
Jax, Curtis, Gehl, Heli, Honda, ICS/PowerGrit, Puckett, Waldon, ASV, IHI, Partner, Imer,
Clipper, MMD, Koshin, Rice, Gorman Rupp, CH&E, Cat Pumps, Comet, General Pump,
Giant,AMida, Coleman, NAC, Gradall, Square Shooter, Kent, Stanley, Tamco, Toku, Hatz,
Kohler, Robin, Wisconsin, Northrock, Oztec, Toker TK, Rol-Air, Small Line, Wanco, Yanmar
Products, Magnum, Airman, Mustang, Power Blanket, Nifty Lift, Atlas Copco,
ands: Genie, Terex, JLG, MultiQuip, Mayco, Toro/Stone,

Table of Contents
Chapter Description Page
Warranty . . . . . . . . . . . . . . . . . . . . . . . . . . . . . . . . . . . . .Inside Front Cover
1 Introduction . . . . . . . . . . . . . . . . . . . . . . . . . . . . . . . . . . . . . . . . . . . . . . . .1
2 Specifications . . . . . . . . . . . . . . . . . . . . . . . . . . . . . . . . . . . . . . . . . . . . . .4
3 Check Lists . . . . . . . . . . . . . . . . . . . . . . . . . . . . . . . . . . . . . . . . . . . . . . . .7
4 SAFETY . . . . . . . . . . . . . . . . . . . . . . . . . . . . . . . . . . . . . . . . . . . . . . . .10
5 Controls, Attachments & Accessories . . . . . . . . . . . . . . . . . . . . . . . . . . .16
6 Operation & Adjustments . . . . . . . . . . . . . . . . . . . . . . . . . . . . . . . . . . . .24
7 Lubrication . . . . . . . . . . . . . . . . . . . . . . . . . . . . . . . . . . . . . . . . . . . . . . .33
8 Trouble Shooting . . . . . . . . . . . . . . . . . . . . . . . . . . . . . . . . . . . . . . . . . .36
9 Service & Storage . . . . . . . . . . . . . . . . . . . . . . . . . . . . . . . . . . . . . . . . . .44
10 Decal Locations . . . . . . . . . . . . . . . . . . . . . . . . . . . . . . . . . . . . . . . . . . .58
11 Maintenance Log . . . . . . . . . . . . . . . . . . . . . . . . . . . . . . . . . . . . . . . . . .62
Index . . . . . . . . . . . . . . . . . . . . . . . . . . . . . . . . . . . . . . . . . . . . . . . . . . . .66
Standard Hardware Torque Data . . . . . . . . . . . . . . . . . . . . . . . . . . . . . . .68
International Symbols . . . . . . . . . . . . . . . . . . . . . . . . . . .Inside Back Cover
IDENTIFICATION INFORMATION
Write your Gehl PowerBox Model (1639, or 1649) and Serial Numbers in the space provided below.
Refer to these numbers when inquiring about parts or service from your Gehl dealer.
The Model and Serial Numbers for this machine are on a Decal located on the Backwall.
Printed In U.S.A. 1 907389/AP297
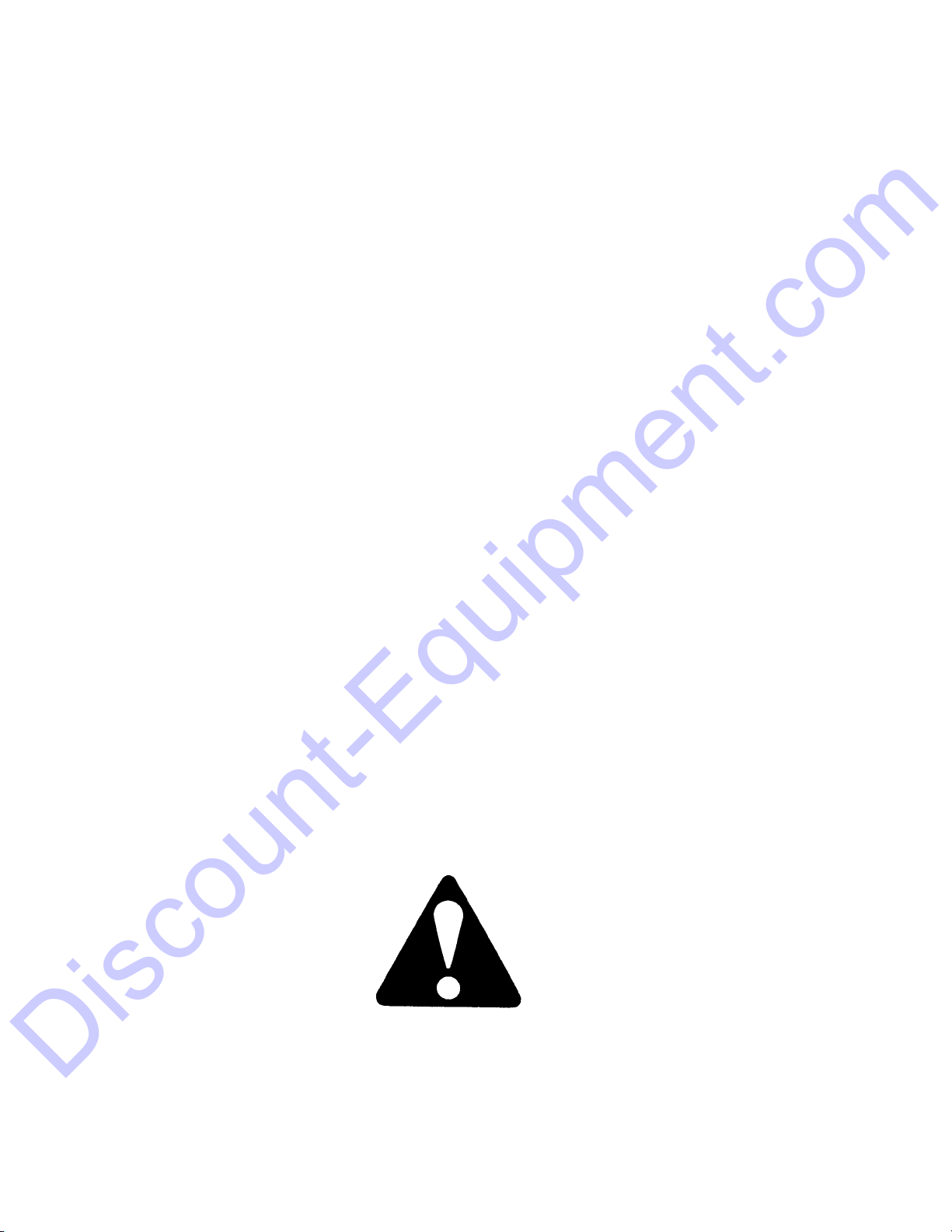
Chapter 1
INTRODUCTION
The information in this Operator’s Manual was written to give the owner/operator assistance in preparing, adjusting, maintaining and servicing of the Paver. More importantly, this manual provides an operating plan for safe and
proper use of the machine. Major points of safe operation are detailed in the SAFETY chapter of this manual. A
chart of standard hardware torques is located in the back of this manual.
The GEHL Company asks that you read and understand the contents of this manual COMPLETELY and
become familiar with your new machine, BEFORE attempting to operate it.
Throughout this manual, information is provided which is set in italic type and introduced by the word NOTE. Be
sure to read carefully and comply with the message or directive given. Following this information will improve
your operating or maintenance efficiency, help you to avoid breakdowns or damage and extend your machine’s
life.
A plastic container is provided on the unit for storing the Operator’s Manual. After using the Manual, please return
it to the container and keep it with the unit at all times! If this machine is resold, GEHL Company recommends
that this Manual be given to the new owner.
“Right” and “left” are determined from a position standing on the Screed Platform and facing forward.
Our wide Dealership network stands by to provide you with any assistance you may require, including genuine
GEHL service parts. All parts should be obtained from or ordered through your GEHL Dealer. Give complete
information about the part and include the model and serial numbers of your machine. Record the serial number
in the space provided on the previous page, as a handy record for quick reference.
GEHL Company reserves the right to make changes or improvements in the design or construction of any part
without incurring the obligation to install such changes on any unit previously delivered.
The GEHL Company, in cooperation with the
American Society of Agricultural Engineers and the
Society of Automotive Engineers, has adopted this
SAFETY ALERT SYMBOL
to pin point characteristics which, if NOT properly followed, can create a safety hazard. When you see
this symbol in this manual or on the machine itself,
you are reminded to BE ALERT! Your personal safey
is involved!
907389/AP297 2 Printed In U.S.A.
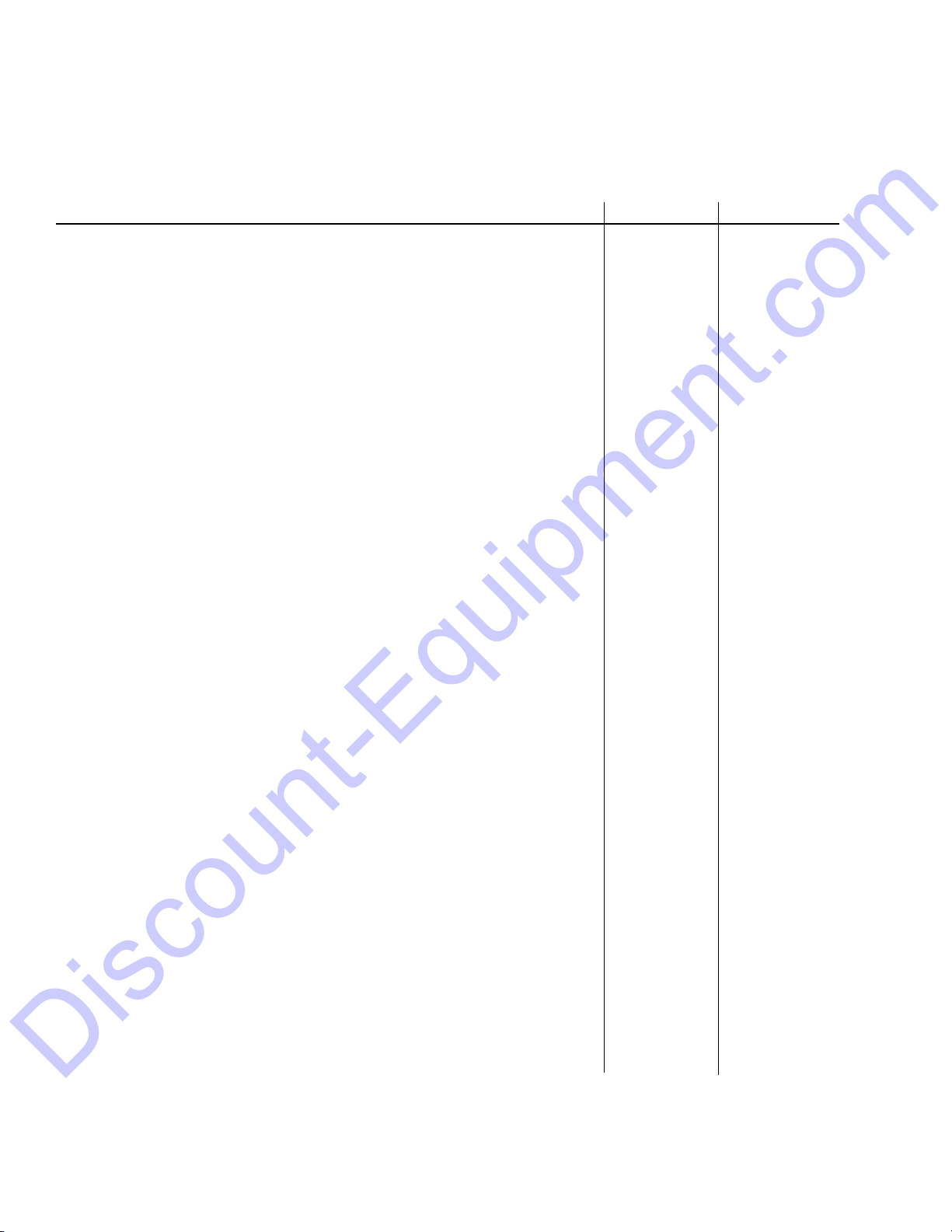
Chapter 2
SPECIFICATIONS
Gehl PowerBox Paver Models: 1639 1649
General Dimensions:
Length . . . . . . . . . . . . . . . . . . . . . . . . . . . . . . . . . . . . . . . . . . . . . . . . . . . . . . . . 8 ft. 8 ft.
(2438 mm) (2438 mm)
Minimum Width (Transport) . . . . . . . . . . . . . . . . . . . . . . . . . . . . . . . . . . . . . . . 9 ft. 10 in. 9 ft. 10 in.
(2997 mm) (2997 mm)
Maximum Width (Operating) . . . . . . . . . . . . . . . . . . . . . . . . . . . . . . . . . . . . . . 9 ft. 10 in. 9 ft. 10 in.
(2997 mm) 2997 mm)
Overall Height . . . . . . . . . . . . . . . . . . . . . . . . . . . . . . . . . . . . . . . . . . . . . . . . . . 5 ft. 5 in. 5 ft. 5 in.
(1651 mm) 1651 mm)
Weight . . . . . . . . . . . . . . . . . . . . . . . . . . . . . . . . . . . . . . . . . . . . . . . . . . . . . . . . 8,395 lb. 8,460 lb.
(3803 kg) (3803 kg)
Truck Clearance (Height from ground to asphalt hopper floor) . . . . . . . . . . . . . 21 in. 21 in.
(533 mm) (533 mm)
Screed:
Maximum Variable Crown/Invert. . . . . . . . . . . . . . . . . . . . . . . . . . . . . . . . . . . . 2 in. 2 in.
(51 mm) (51 mm)
Width. . . . . . . . . . . . . . . . . . . . . . . . . . . . . . . . . . . . . . . . . . . . . . . . . . . . . . . . . 12 in. 12 in.
(305 mm) (305 mm)
Hydraulic Vibrator . . . . . . . . . . . . . . . . . . . . . . . . . . . . . . . . . . . . . . . . . . . . . . . Std. (83 Hz.) Std. 83 Hz.)
(5000 cy/min) (5000 cy/min)
Heat Medium (Exhaust). . . . . . . . . . . . . . . . . . . . . . . . . . . . . . . . . . . . . . . . . . . Standard Standard
Heat Medium (Propane). . . . . . . . . . . . . . . . . . . . . . . . . . . . . . . . . . . . . . . . . . . Optional Optional
Variable Hydraulic Strike Off Max. Extension Length . . . . . . . . . . . . . . . . . . . . 18 in. 18 in.
(457 mm) (457 mm)
Dual Span Operator Platform (Isolated) . . . . . . . . . . . . . . . . . . . . . . . . . . . . . . . Standard Standard
Service Capacities:
Engine Cooling System (Isuzu - 4LC1) . . . . . . . . . . . . . . . . . . . . . . . . . . . . . . . N/A 6.8 Qt.
(6.4 Liter)
Engine Oil w/Filter (Wisconsion - VH4D) . . . . . . . . . . . . . . . . . . . . . . . . . . . . . 4 Qt. N/A
(3.8 Liter)
Engine Oil w/Filter (Isuzu 4LC1). . . . . . . . . . . . . . . . . . . . . . . . . . . . . . . . . . . . N/A 6.9 qt.
(6.5 Liter)
907389/AP297 4 Printed In U.S.A.
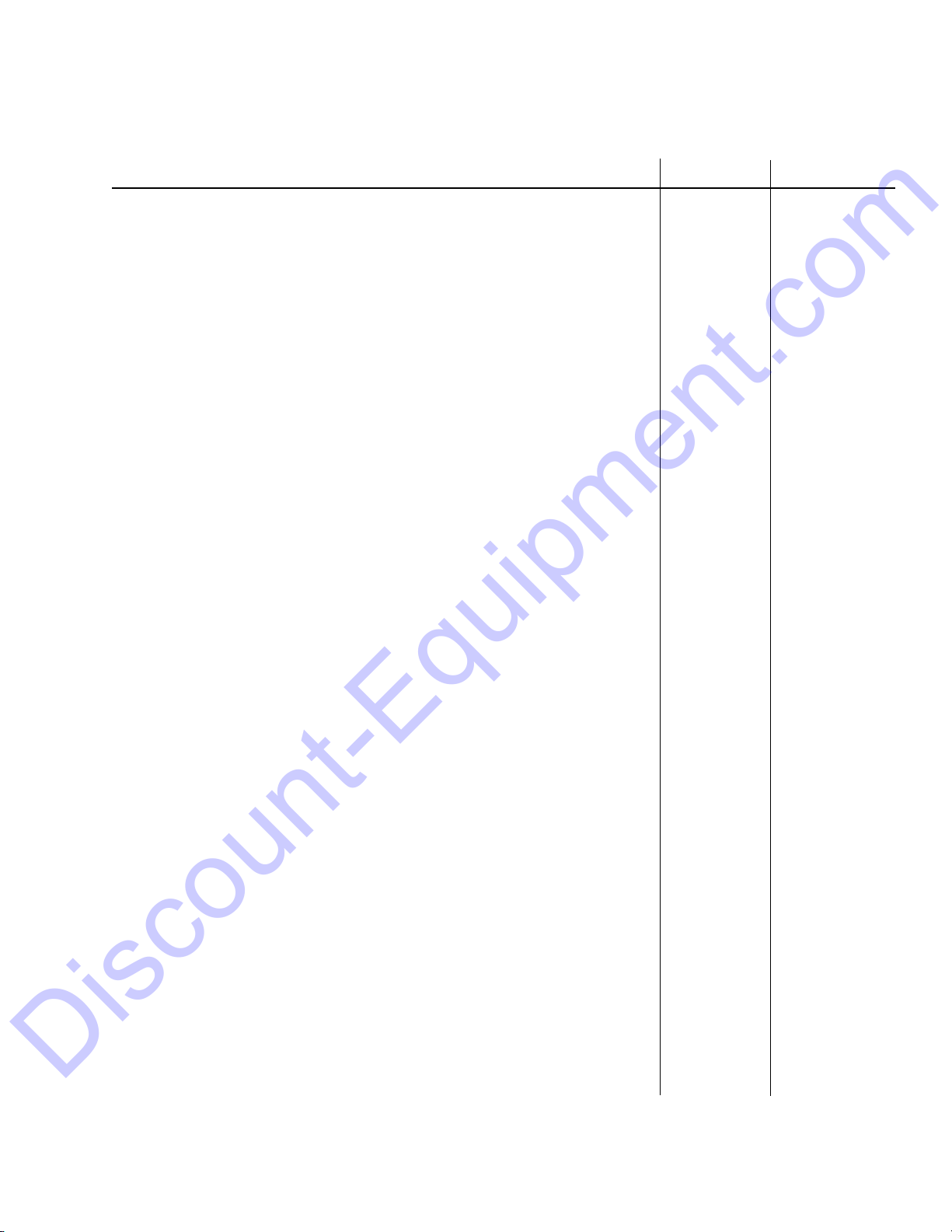
SPECIFICATIONS (Continued)
Gehl PowerBox Paver Models: 1639 1649
Service Capacities (Continued):
Hydraulic Reservoir. . . . . . . . . . . . . . . . . . . . . . . . . . . . . . . . . . . . . . . . . . . . . . 20 Gal. 20 Gal.
(75.7 Liter) 75.7 Liter
Fuel Reservoir . . . . . . . . . . . . . . . . . . . . . . . . . . . . . . . . . . . . . . . . . . . . . . . . . . 12 Gal. 12 Gal.
45.4 Liter) (45.4 Liter)
Wash Down Tank w/Electric Pump . . . . . . . . . . . . . . . . . . . . . . . . . . . . . . . . . . 4.5 Gallons) 4.5 Gallons)
(17 Liter) (17 Liter)
Engine:
Wisconsin - VH4D, 30 HP (22.4 Kw) Gas, Air-Cooled, 12 Volt Electric Start,
30 Amp Alternator, 575 CCA Battery. . . . . . . . . . . . . . . . . . . . . . . . . . . . . . . . . Standard N/A
Isuzu - 4LC1, 41 HP (30.6 Kw) Diesel, Water-Cooled, 12 Volt Electric Start,
35 Amp Alternator, 575 CCA Battery. . . . . . . . . . . . . . . . . . . . . . . . . . . . . . . . . N/A Standard
Drive System:
Hydrostatic Steel Track Type, Single-Speed, Positive/Self-Adjusting
Counter-Rotating, Fine Tune Steering Valve. . . . . . . . . . . . . . . . . . . . . . . . . . . . Std. Std.
Maximum Ground Speed . . . . . . . . . . . . . . . . . . . . . . . . . . . . . . . . . . . . . . . . . . 130 FPM 130 FPM
(39.7 mpm) (39.7 mpm)
Hydraulic System:
Variable Hydrostatic Drive Pump - Maximum Flow. . . . . . . . . . . . . . . . . . . . . . 27 GPM 27 GPM
(102 Ltrs/M) (102 Ltrs/M)
Variable Hydrostatic Drive Pump - Maximum Relief Pressure . . . . . . . . . . . . . . 3500 PSI 3500 PSI
(24.5 Bar) (24.5 Bar)
Hydraulic Auger Drive Pump - Maximum Flow. . . . . . . . . . . . . . . . . . . . . . . . . 12 GPM 12 GPM
(45.4 Ltrs/M) (45.4 Ltrs/M)
Hydraulic Auger Drive Pump - Maximum Relief Pressure. . . . . . . . . . . . . . . . . 2000 PSI 2000 PSI
(14 Bar) (14 Bar)
Hydraulic Cylinder Pump - Maximum Flow . . . . . . . . . . . . . . . . . . . . . . . . . . . 12 GPM 12 GPM
(45.4 Ltrs/M) (45.4 Ltrs/M)
Hydraulic Cylinder Pump - Maximum Relief Pressure. . . . . . . . . . . . . . . . . . . . 1800 PSI 1800 PSI
(126 Bar) (126 Bar)
Return Filter . . . . . . . . . . . . . . . . . . . . . . . . . . . . . . . . . . . . . . . . . . . . . . . . . . . 5 Micron 5 Micron
Suction Strainer . . . . . . . . . . . . . . . . . . . . . . . . . . . . . . . . . . . . . . . . . . . . . . . . . 100 Micron 100 Micron
Aux. Oil Cooler Capacity . . . . . . . . . . . . . . . . . . . . . . . . . . . . . . . . . . . . . . . . . 12 GPM 12 GPM
(45.4 Ltrs/M) (45.4 Ltrs/M)
Printed In U.S.A. 5 907389/AP297
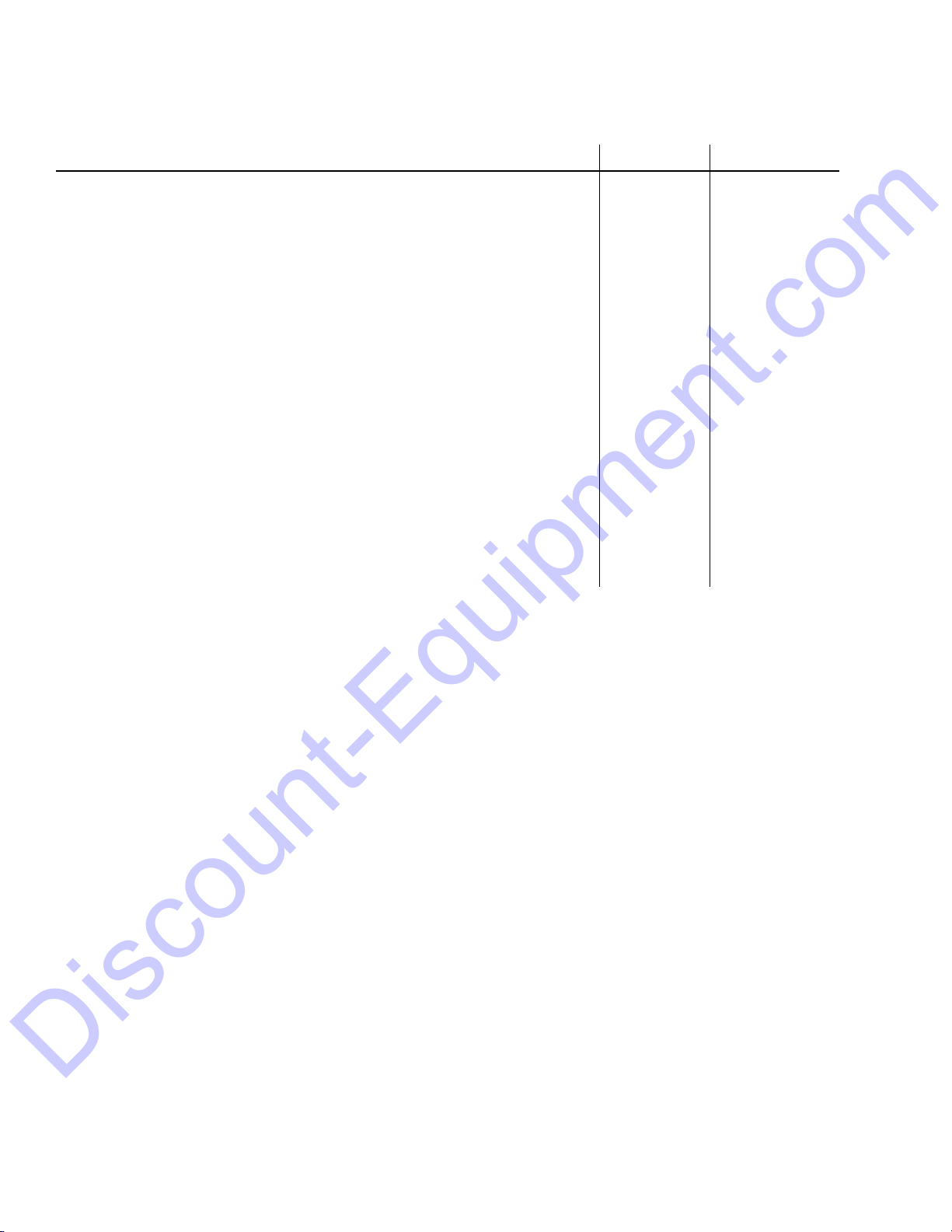
Gehl PowerBox Paver Models: 1639 1649
Paving Performance:
Minimum Variable Paving Width . . . . . . . . . . . . . . . . . . . . . . . . . . . . . . . . . . . . 4.5 ft. 4.5 ft.
(1372 mm) (1372 mm)
Maximum Variable Paving Width . . . . . . . . . . . . . . . . . . . . . . . . . . . . . . . . . . . 12 ft. 12 ft.
(3658 mm) (3658 mm)
Minimum Variable Paving Depth . . . . . . . . . . . . . . . . . . . . . . . . . . . . . . . . . . . . 0-1/2 in. 0-1/2 in.
(0-13 mm) (0-13 mm)
Maximum Variable Paving Depth . . . . . . . . . . . . . . . . . . . . . . . . . . . . . . . . . . . 6 in. 6 in.
(152.4 mm) (152.4 mm)
Gravity Feed Hopper Capacity. . . . . . . . . . . . . . . . . . . . . . . . . . . . . . . . . . . . . . 6 Ton 6 Ton
(5436 kg) (5436 kg)
Hydraulic Feed Augers . . . . . . . . . . . . . . . . . . . . . . . . . . . . . . . . . . . . . . . . . . . 2 2
Hydraulic Material Flow Gates . . . . . . . . . . . . . . . . . . . . . . . . . . . . . . . . . . . . . 2 2
Operating Speed . . . . . . . . . . . . . . . . . . . . . . . . . . . . . . . . . . . . . . . . . . . . . . . . 0-130 FPM 0-130 FPM
(0-40 mpm) (0-40 mpm)
Left and Right Side Operator Controls . . . . . . . . . . . . . . . . . . . . . . . . . . . . . . . . Standard Standard
SPECIFICATIONS (Continued)
907389/AP297 6 Printed In U.S.A.
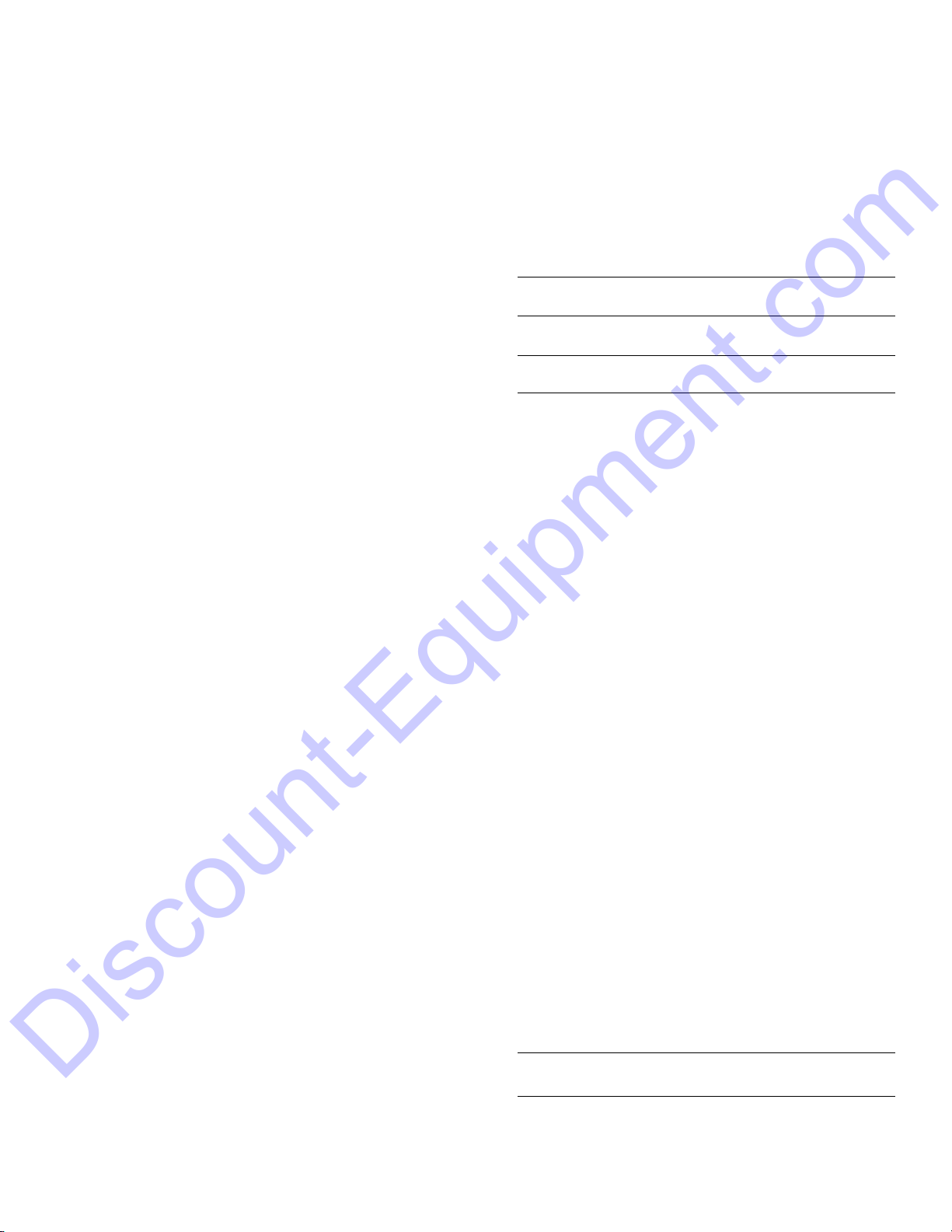
Chapter 3
CHECKLISTS
PRE-DELIVERY
The following Checklist is an important reminder of valuable information and inspections which MUST be made
before delivering the Paver to the Customer. Check off each
item after prescribed action is taken.
Check that:
NO parts of Paver have been damaged in shipment. Check
for such things as dents and loose or missing parts; correct
or replace components as required.
Battery is securely mounted and NOT cracked. Cable con-
nections are tight. Electrolyte at proper level.
Cylinders, hoses and fittings are NOT damaged, leaking or
loosely secured.
Oil, fuel and air filters are NOT damaged leaking or loose-
ly secured.
All grease fittings have been properly lubricated and NO
fittings are missing; see Lubrication chapter of this manual.
Hydraulic system reservoir, engine crankcase, and engine
coolant are filled to the proper operating levels.
All adjustments have been made to comply with the set-
tings given in this manual and in the separate Engine manual.
All Guards, Shields and Decals are in place and securely
attached.
Model and Serial Number for this unit is recorded in space
provided on this page and page 1.
Start the Paver and test-run the unit while checking
that proper operation is exhibited by all controls.
Check that:
All indicator lamps, meters, etc. function properly.
Proper operation of all Hopper and Screed Controls.
Dynamic braking in effect with Drive Motors in neutral.
No hydraulic system leaks when under pressure.
Listen for abnormal noises or vibrations; if detected, deter-
mine their cause and repair as necessary.
I acknowledge that pre-delivery procedures were performed
on this unit as outlined above.
Dealership’s Name
Dealer Representative’s Name
Date Checklist filled-out
Paver Model# Paver Serial # Engine Serial #
DELIVERY
Check that:
The following Checklist is an important reminder of valuable information that MUST be passed on to the Customer at
the time the unit is delivered. Check off each item as you
explain it to the Customer.
Review with the Customer the contents of this manual;
especially:
The INDEX at the back, for quickly locating topics;
The SAFETY, CONTROLS/ATTACHMENTS & ACCES-
SORIES, and OPERATION/ADJUSTMENTS Chapters
for information regarding safe use of the machine.
The LUBRICATION, SERVICE and TROUBLESHOOT-
ING Chapters, for information regarding proper maintenance of the machine. Explain that regular lubrication and
maintenance are required for continued safe operation and
long life.
Give this Operator’s Manual to the Customer and instruct
the Customer to be sure to read and completely understand
its contents BEFORE operating the unit.
Explain that the Customer MUST consult the Engine
Manual (provided) for related specifications, operating
adjustments and maintenance instructions.
Completely fill out the Owner’s Registration, including
Customer’s signature and, return it to the company.
Customer’s Signature
Date Delivered
Printed In U.S.A. 7 907389/AP297

Chapter 4
SAFETY
The above Safety Alert Symbol means ATTENTION!
ALLWAYS BE ALERT! YOUR SAFETY IS
INVOLVED! It stresses an attitude of “Heads Up for
Safety” and can be found throughout this Operator’s
Manual and the machine itself.
BEFORE YOU ATTEMPT TO OPERATE THIS
EQUIPMENT READ AND STUDY THE FOLLOWING SAFETY INFORMATION. IN ADDITION, MAKE SURE THAT EVERY INDIVIDUAL WHO OPERATES OR WORKS WITH THIS
EQUIPMENT, WHETHER FAMILY MEMBER
OR EMPLOYEE, IS FAMILIAR WITH THESE
SAFETY PRECAUTIONS.
The Gehl Company ALWAYS takes the operator’s
safety into consideration when designing its machinery
and guards exposed moving parts for his/her protection. However, some areas can NOT be guarded or
shielded in order to assure proper operation. In addition, this Operator’s Manual and Decals
, on the
machine, warn of further danger and should be read and
observed closely.
REMEMBER! It is the owner’s responsibility for
communicating information on the safe use and proper
maintenance of this machine! This includes providing
understandable interpretation of these instructions for
operators who are not fluent in reading English.
MANDATORY SAFETY SHUTDOWN
PROCEDURE
BEFORE cleaning, adjusting, lubricating or servicing the unit:
1. Bring machine to full parking stop on level sur-
face (NEVER park on a slope or hill side).
2. Lower the Hopper and Screed Assembly to the
“full down” position.
3. Place controls in Neutral.
4. Move the Throttle to low idle.
5. Shut off the Engine and remove the Key.
ONLY when you have taken these precautions can
you be sure it is safe to proceed. Failure to follow
the above procedure, could lead to death or serious
bodily injury.
ADDITIONAL SAFETY REMINDERS
z USER/OPERATOR SAFETY PRACTICES, as
estabished by Industry Standards, are included in
this Operator’s Manual and intended to promote
SAFE OPERATION of the Paver. These guidelines do NOT preclude the use of good judgment,
care and common sense as may be indicated by the
particular jobsite work conditions.
z It is essential that operators be physically and men-
tally free of mind altering drugs and chemicals and
thoroughly trained in the safe operation of the
Paver. Such training should be presented completely to all new operators and not condensed for
those claiming previous experience. Information
on operator training is available from several
sources including the manufacturer.
DANGER
“DANGER” indicates an imminently hazardous situation which, if not avoided, will
result in death or serious injury.
WARNING
“WARNING” indicates a potentially hazardous
situation which, if not avoided, could result in
death or serious injury.
CAUTION
“CAUTION” indicates a potentially hazardous
situation which, if not avoided, may result in
minor or moderate injury. Also alerts to unsafe
practices.
907389/AP297 10 Printed In U.S.A.
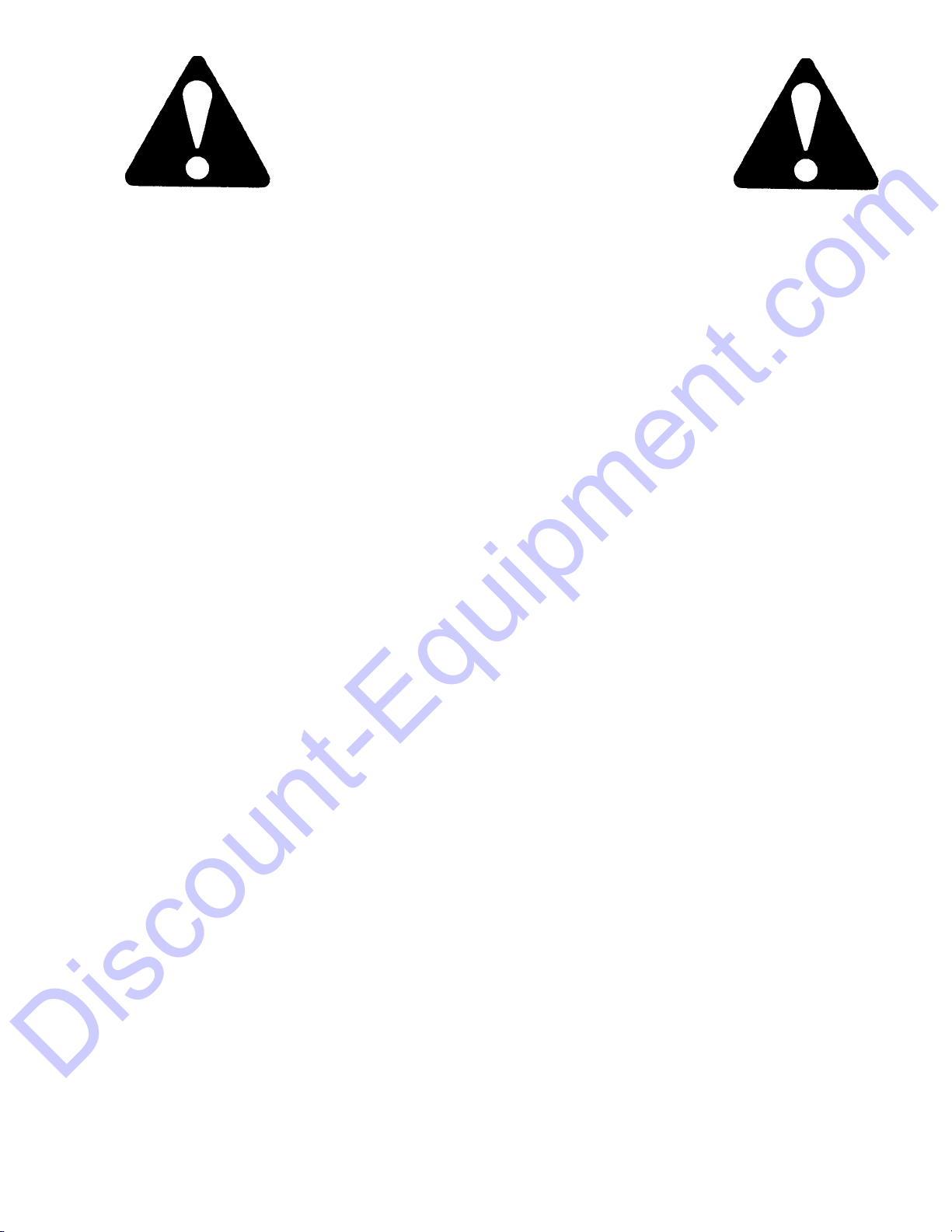
SAFETY
(Continued)
z Some illustrations, used in this manual, may show
Doors, Guards and Shields open or removed for
illustration purposes ONLY. Be SURE that all
Doors, Guards and Shields are in their proper operating positions BEFORE starting the Engine to
operate the Paver.
z ALWAYS wear appropriate personal safety gear
called by the job or working conditions. Do NOT
wear loose or baggy clothing while operating or
servicing the machine.
z ALWAYS maintain safe clearance from electrical
powerlines and avoid contact with any electrically
charged conductor. Contact can result in electrocution. Contact proper local authorities for utility line
location BEFORE starting a job.
z ALWAYS check the job site for obstructions and
bystanders!
z NEVER use your hands to search for hydraulic
fluid leaks. Use a piece of paper or cardboard.
Escaping fluid under pressure can be invisible and
can penetrate the skin causing serious injury. If any
fluid is injected into your skin, see a doctor at
once. Injected fluid MUST be surgically removed
by a doctor familiar with this type of injury or gangrene may result!
z Do NOT attempt to move HOT asphalt mix with
your hands or feet. Contact can cause serious skin
burns!
z Do NOT allow minors or any unqualified person-
nel to operate or be near the Paver unless properly
supervised!
z Do NOT operate the Paver in an enclosed area
without adequate ventilation! Internal combustion
engines deplete the oxygen supply within enclosed
spaces and may create a serious hazard unless the
oxygen is replaced!
z Do NOT leave the Paver unattended with the
Engine running. ALWAYS lower the Hopper to
“full down” position, shut off the Engine and place
all controls in neutral BEFORE leaving the
machine!
z ALWAYS position the Safety Props when leaving
the Hopper raised for inspection, cleaning or service!
z Do NOT attempt to refill the Fuel Reservoir when
the Engine is hot. Allow Engine to cool down
BEFORE refilling to prevent hot Engine from
igniting the fuel if it should spill or splash!
z Do NOT smoke while filling the Fuel Reservoir,
while working on the fuel or hydraulic systems, or
while working around the Battery!
z Do NOT attempt to loosen or disconnect ANY
Hydraulic Lines, Hoses or Fittings without first
relieving hydraulic circuit pressure. Also, be careful NOT to touch any hydraulic components that
have been in recent operation because they can be
extremely HOT and can burn you!.
z ALWAYS disconnect the Battery connection to
prevent unintentional starting while working on
this machine!
z Do NOT attempt to remove the Radiator Cap after
the Engine has reached operating temperature or if
it is overheated. At operating temperatures, the
Engine Coolant will be extremely HOT and under
pressure. ALWAYS wait for the Engine to cool
down before attempting to relieve pressure and
remove the Radiator Cap. Failure to heed this
warning could result in severe burns!
z ALWAYS observe the following Safety
Procedures when Propane Screed Heater is used:
Wrench tighten all fittings. NEVER use grease or
lubrication. Do NOT use oxygen with the Heater.
Keep cylinder upright at all times. Keep equipment
free from dirt and oil.
Use a regulator on supply cylinder.
Check equipment carefully each time before lighting. ALWAYS light with a striker, NEVER with
matches. Do NOT operate in an enclosed area or
Printed In U.S.A. 11 907389/AP297
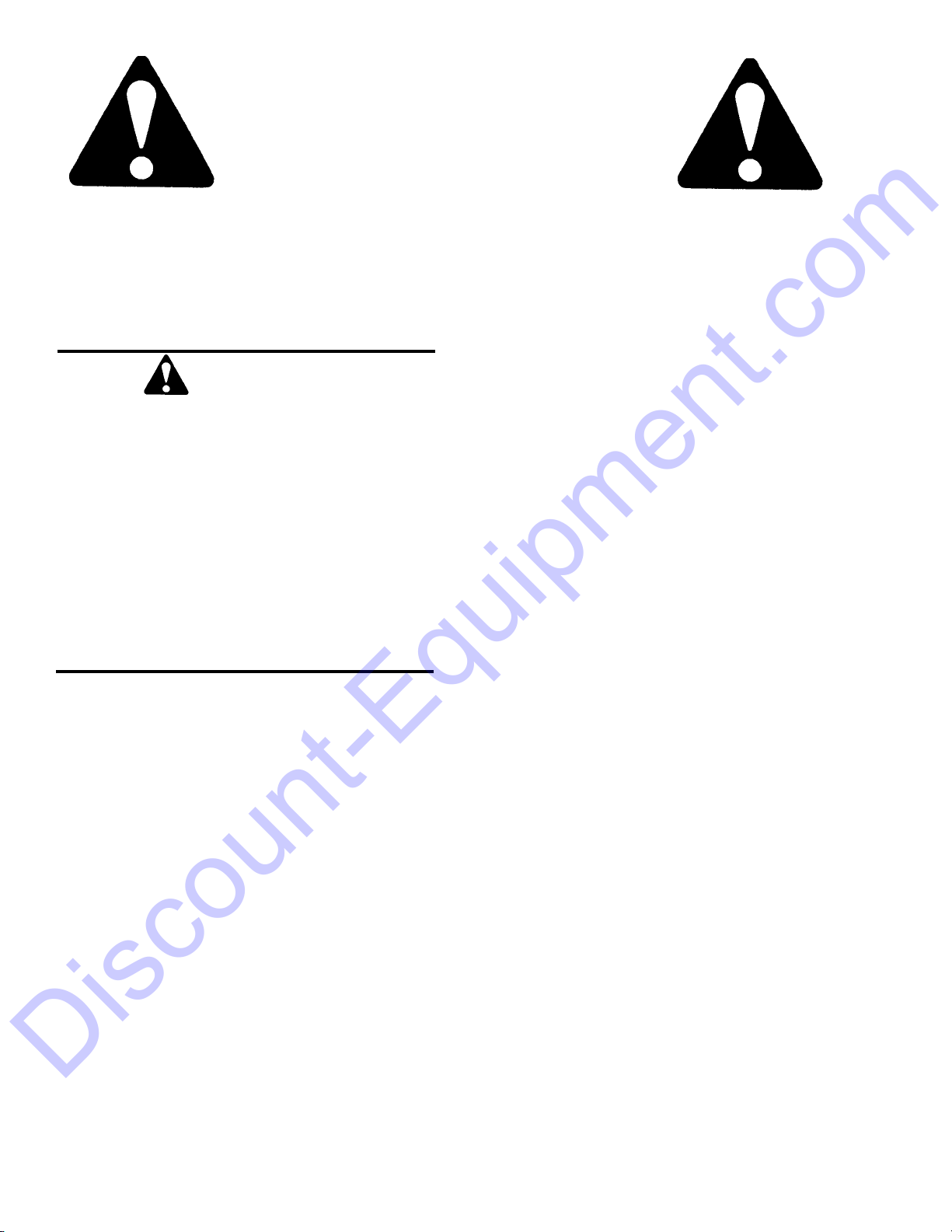
SAFETY
(Continued)
near flammable material. Close all valves when
not in use. Comply with all federal, state, and local
regulations when operating this equipment.
Screed Propane Heater - General Safety
1. This equipment is designed to be used only with
propane gas.
2. Wrench tighten all fittings.
3. NEVER use oil or grease for lubrication.
4. Do NOT use oxygen with this equipment.
S. Keep cylinder upright at all times.
6. Keep equipment free from dirt and oil.
7. Use a regulator on supply cylinder.
8. Check equipment carefully each time before lighting.
9. Always light with a striker, never with matches.
10. Do NOT operate in an enclosed area or near
flammable material.
11. Close all valves when not in use.
12. Comply with all federal, state and local regulations when operating this equipment.
z To ensure continued safe operation, replace dam-
aged or worn-out parts with genuine GEHL service
parts, BEFORE attempting to operate this equipment.
Modifications, Nameplates, Markings
And Capacities
z Modifications and additions, which affect capacity
or safe operation, shall NOT be performed without
the manufacturer’s prior written approval. Where
such authorization is granted, tags or decals shall
be changed accordingly.
Protective Guards And Warning
Devices
z The Paver is fitted with protective Covers over the
Engine area in accordance with Industry
Standards. They are intended to offer protection to
the operator from physical injury. A Horn is provided which can be activated from either side of
the Paver.
Replacement Parts
z To ensure continued safe operation, replace dam-
aged or worn-out parts with genuine GEHL service
parts, BEFORE attempting to operate this equipment.
CAUTION
Do NOT smoke in the area around the Power
Box Paver when equipped with Propane
Burners.
ALWAYS make sure a suitable fire extinguisher is readily available.
ALWAYS light burner with a striker, NEVER
use a match.
Burner flame may be invisible in sunlight. Do
NOT place burner near your skin or clothing.
Servere burns will result.
907389/AP297 12 Printed In U.S.A.
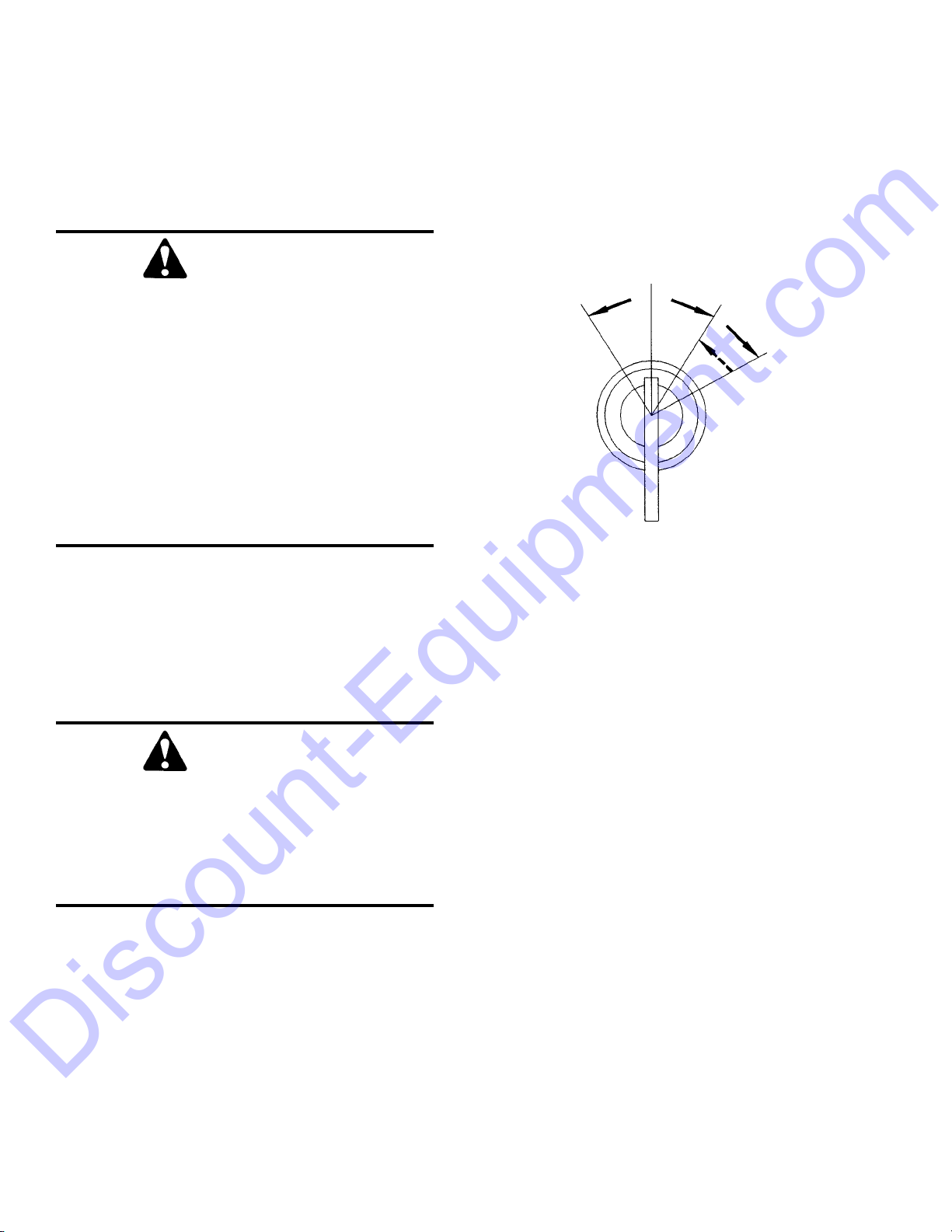
GUARDS AND SHIELDS
Whenever possible and without affecting Paver operation, Guards and Shields are used to protect potentially hazardous areas. In many places, Decals are also
provided to warn of potential dangers and/or to display
special operating procedures.
CONTROL INDICATORS & SWITCHES
(Figs. 1-5)
The Control Panel on the Backwall Console area contains the following Indicators and Switches:
Starter Keyswitch
Off Position: When the Key is vertical in the Key
switch, power from the Battery is disconnected to the
Fig. 1
Control and Instrument Panel electrical circuits. Also,
this is the only position in which the Key can be inserted or removed from the Key switch.
RUN Position: When the Key is turned one position
clockwise from the vertical (OFF) position, power
from the Battery is supplied to all Control and
Instrument Panel electrical circuits.
Start Position: Turn the Keyswitch clockwise two
positions from the vertical (OFF) position to activate
the Engine Starter. The Keyswitch will return to the
RUN position automatically as soon as the Engine
Starts.
NOTE: The Key MUST always be returned to
the OFF position between starting attempts. The
Battery Charge and Engine Oil Pressure (Model
1649) Indicators should activate when the key is
turned to the RUN position.
Pre-Heat Glow Plug Indicator (1649): As an Engine
starting aid, pre-heating is required in a cold Engine
starting condition. This pre-heating uses Glow Plugs
which are activated by rotating the Keyswitch counterclockwise to the Pre-Heat position.
WARNING
Read and thoroughly understand ALL Safety
Decals on the Paver BEFORE attempting to
operate it. Do NOT attempt to operate the
machine unless ALL factory installed Guards
and Shields are properly secured in place.
CAUTION
Become familiar with and know how to use
ALL safety devices and controls on the Paver
BEFORE attempting to operate it. Know how
to stop the machine operation BEFORE
attempting to operate it. This GEHL Power
Box Paver is designed and intended to be
used ONLY with GEHL Company accessories
or a GEHL Company approved or referral
accessory. The GEHL Company can NOT be
responsible for operator safety if the Paver is
used with an unapproved accessory or attachment.
Chapter 5
CONTROLS, ATTACHMENTS
AND ACCESSORIES
PREHEAT
(1649 ONLY)
OFF
RUN
START
AUTO
RETURN
907389/AP297 16 Printed In U.S.A.
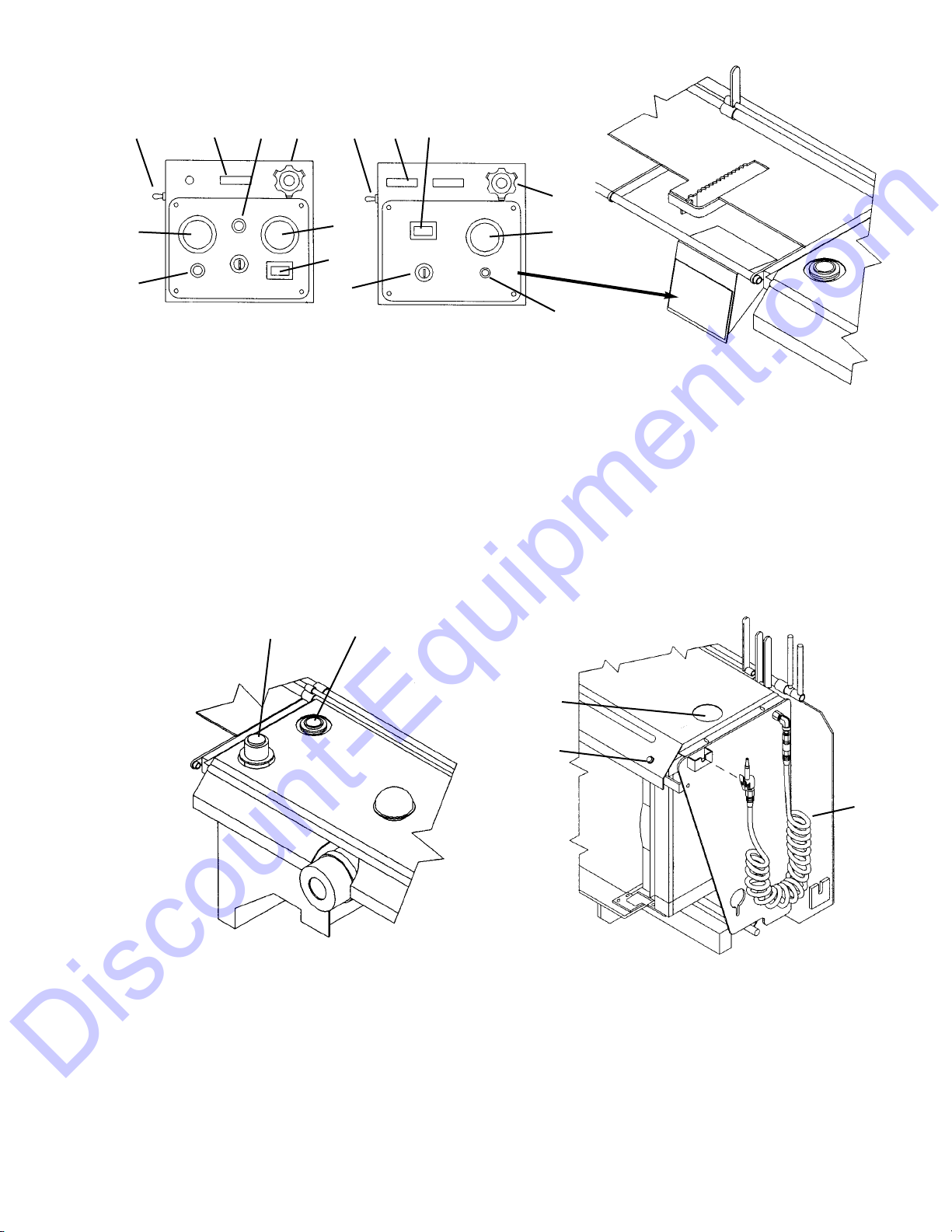
Fig. 3
1. Fuel Gauge 3. Radiator Fill (1649)
2. Fuel Fill Cap 4. Horn Push Button (Ea. Side)
5.
Spray Down Hose (Ea. Side)
Fig. 2
1.
Choke (1639) 4. Circuit Breaker (1639) 8. Engine Oil Pressure (1649)
2. Throttle 5. Keyswitch 9. Spray Down Pump Switch
3. Battery Gauge 6. Glow Plug Indicator (1649) 10. Hourmeter
7.
Water Temperature Gauge (1649)
11. Exhaust Diverter
1649 MODELS
1649 SHOWN
1649 SHOWN
1639 MODELS
TOP CONSOLE
2
3
4
3
10
5
7
6
21
3
4
5
9 11 8 2 9 1 10
Printed In U.S.A. 17 907389/AP297
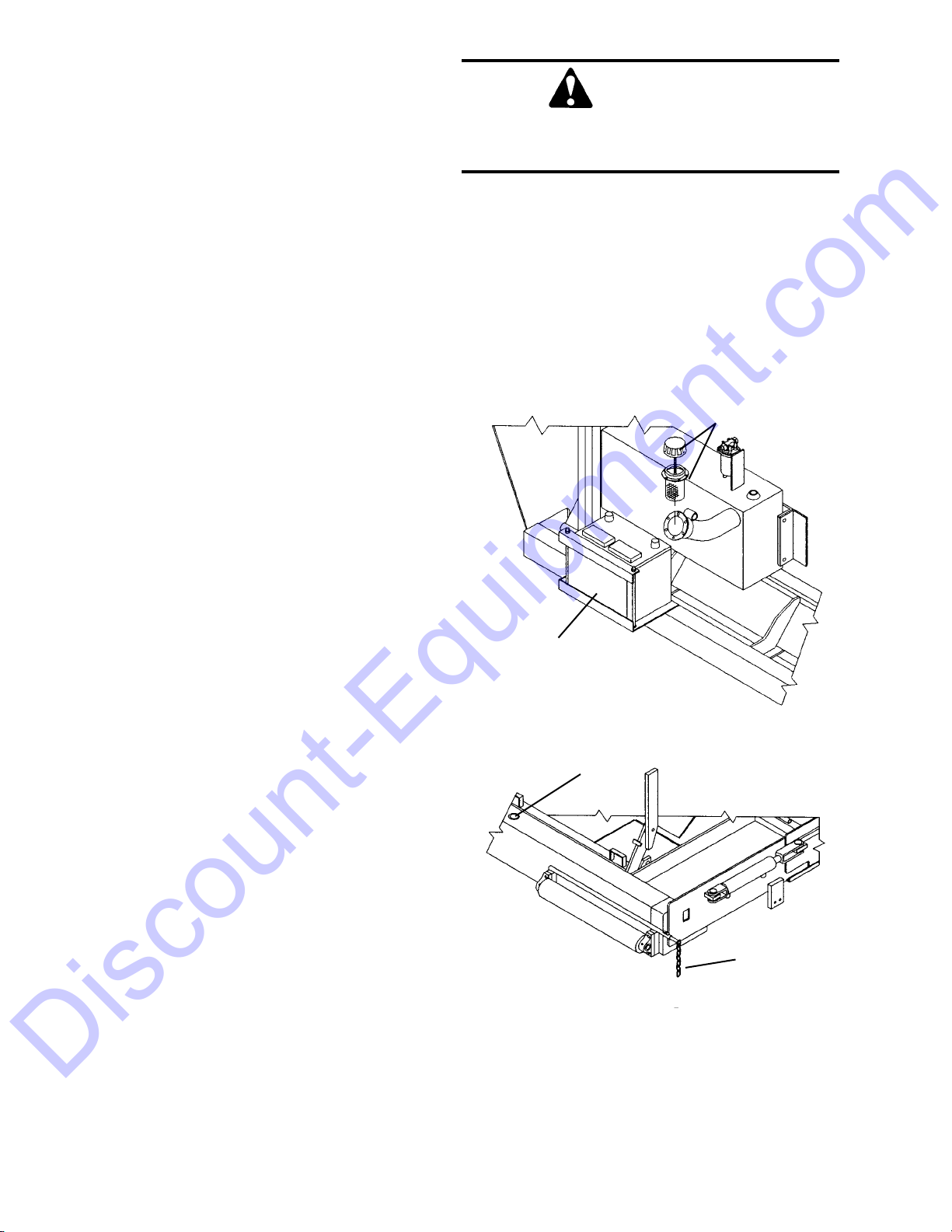
Fig. 4
1. Spray Tank Fill Cap
2. Battery
3.
Hydraulic Reservoir Fill Dipstick
4. Alignment Guide (Ea. Side)
Engine Throttle: This controls the Engine speed. Idle
position is with the Cable fully in. Operating position
is with the cable 1 to 1-1/2 inches out. Release the
Lock Ring, depress the red button on the Knob and pull
the Knob out to set speed. Rotate the Knob left or right
to fine adjust the speed during operation.
Horn Buttons: The Horn may be activated from a
Pushbutton on the left side or right side of the Console.
Fuel Level Gauge: Indicates the amount of fuel
remaining in the Fuel Reservoir.
Battery Charge gauge: Indicates the condition of the
charging system. During normal operation, this
Indicator should show minimum registeration.
Coolant Temperature Gauge: Indicates Engine
coolant temperature. Under normal operating condi-
tions, this Gauge should indicate approximately 185
o
F
(85
o
C).
Engine Oil Pressure (1649): This Lamp indicates
whether sufficient Engine lubricating oil pressure is
present or not. During normal operation, with the
Engine running, this Lamp should be OFF. During
starting and when the Engine is NOT running, this
Lamp will be ON
NOTE: If this lamp comes ON during normal
operation with the Engine running, STOP the
Engine immediately. After allowing the oil to drain
down for a few minutes, check the Engine oil
level. Maintain oil level at the FULL mark on the
dipstick
Circuit Breaker (1639): The 15 Amp Breaker protects
electrical circuits. If it is not in the “depressed position”, the Gauges and Indicators on the Control Panel
will not work and the Engine will shut off.
Hourmeter: Indicates the operating time of the
machine and should be used for keeping up the
Maintenance Log chapter of this manual.
Washdown Sprayer System: Sprayer is used periodically each day to wash down parts of the Paver which
contact asphalt. An asphalt releasing agent is used for
this.
Exhaust Diverter: Pull this Cable Handle OUT to
divert the Engine exhaust down through the Screed.
This heats up the Screed bottom surface when paving.
Push Handle IN to divert exhaust out through the
Muffler.
Fuel Level Gauge: The Gauge needle pointer indicates the amount of fuel remaining in the Reservoir.
CAUTION
Do NOT spray releasing agent on a HOT
Engine.
1
2
3
4
907389/AP297 18 Printed In U.S.A.
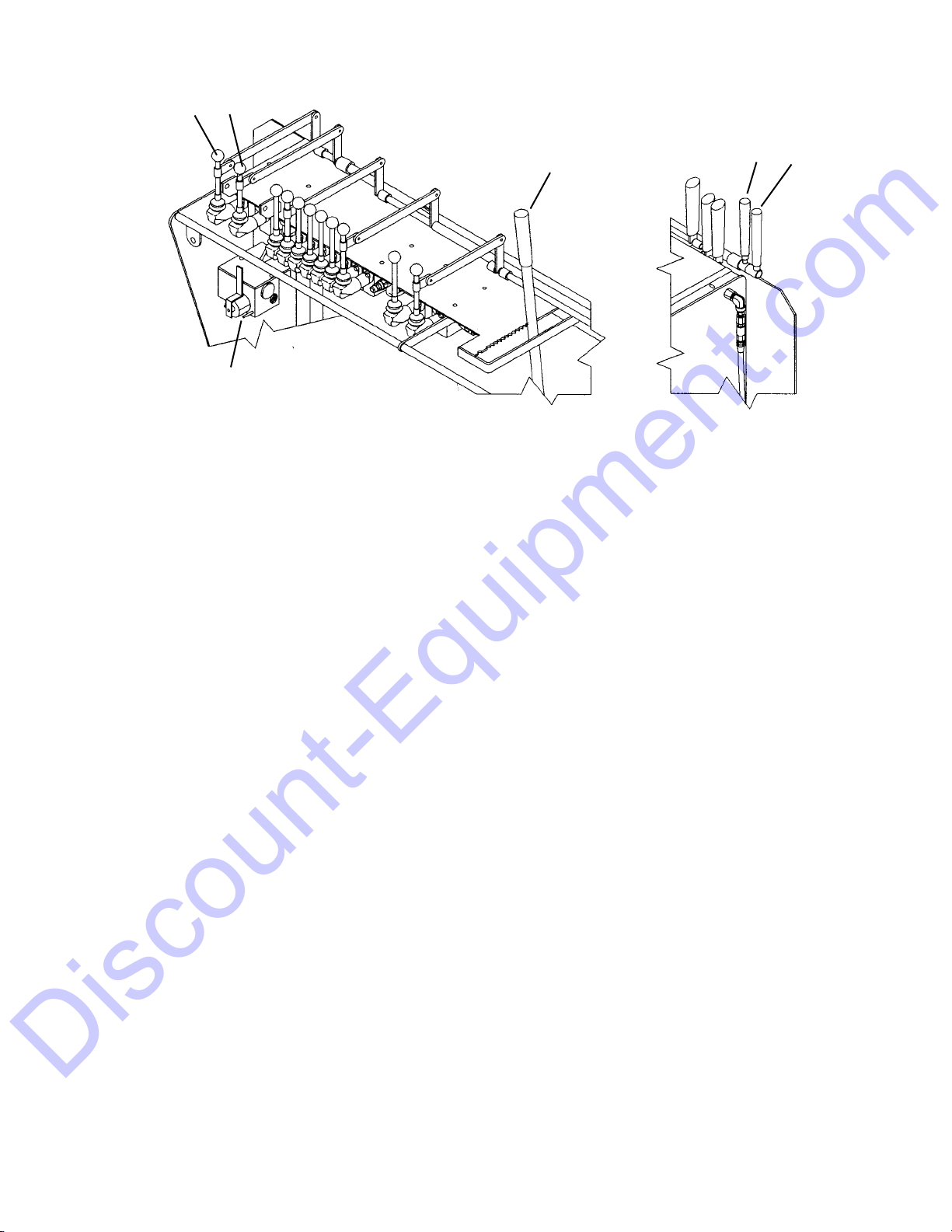
Fig. 5 - Travel Controls
1. Left Track Travel 3. Pump Speed
2.
Right Track Travel
4. Modular Steering
Hydraulic Fluid Reservoir: The Access/Fill Plug on
top may be removed to check fluid level..
NOTE: Before removing the Access/Fill Plug,
allow the fluid to cool for 10-15 minutes. Take a
wrench and slowly loosen the Hydraulic Breather
Cap on the Backwall Top Console to release system pressure.
Paving Alignment Guide: This is adjustable so the
Chain will align with a curb or the edge of a previously laid mat of asphalt..
TRAVEL CONTROLS (Figs. 5-6)
These controls are used to manuver the Paver around
on the jobsite or for road travel. Decals on the
Backwall Top Console area provide graphic representation of the various control actions.
Hydraulic Pump Variable Speed: This Lever
increases or decreases power to the Drive Motors. Push
the Lever FORWARD to increase speed, pull BACK to
decrease speed. Place the Lever in neutral when not
operating.
Track Travel: These two Levers control the Track
Drive Motors for forward and rearward movement and
also turning of the Paver. Both Levers are mechanically linked to Levers on the right side for control from
either side.
NOTE: “Right” and “left” are determined from a
position standing behind the unit and facing the
direction of forward travel. Pivot the machine at
slow speeds only.
Movement of the Travel Levers and the expected
results are as follows (See Fig. 6):
Move both Levers FORWARD to go forward. Move
both Levers REARWARD to go backwards. Move the
LEFT Track Lever FORWARD to pivot turn right.
Move the LEFT Track Lever REARWARD to pivot
turn left.
Move the RIGHT Track Lever FORWARD to pivot
turn LEFT. Move the RIGHT Track Lever REARWARD to pivot turn right.
Move both Levers in opposite directions to spin the
machine about its center position. Returning both
Levers to “neutral” position stops the Drive Tracks.
4
3
RT. SIDE CONTROL
1 2
1 2
Printed In U.S.A. 19 907389/AP297
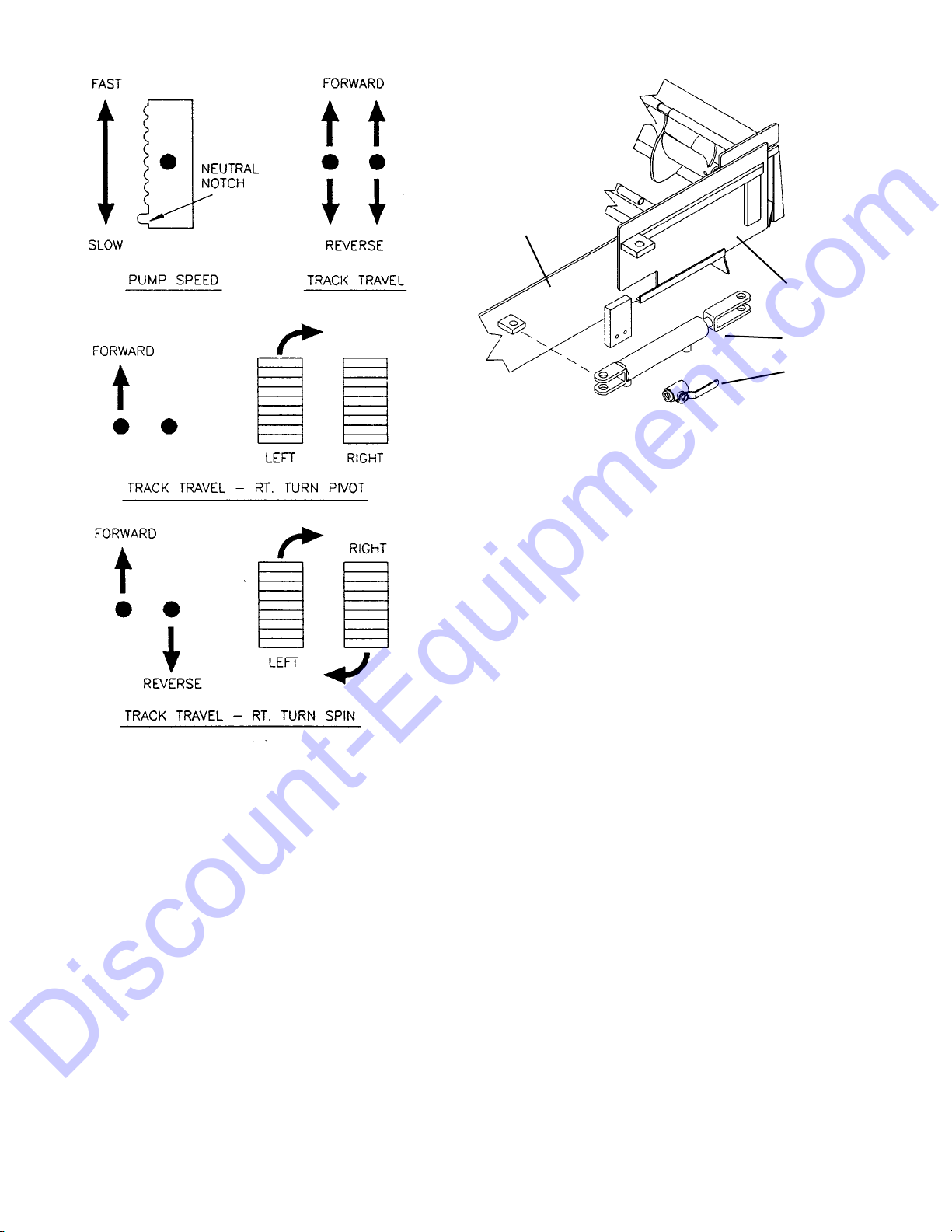
Modular Steering: This control is used for dividing
the hydraulic oil to each Drive Motor. It will be necessary to adjust this valve as paving conditions vary.
With the Track Travel Levers both either forward or
rearword, set the Pump Speed Lever to “travel” or
“pave”. Position the Modular Control Lever LEFT to
move left and RIGHT to move right. Place the Lever
in the CENTER position to move straight ahead.
HOPPER CONTROLS (Figs. 7-8)
Hopper Floor: Move Lever BACK to raise Hopper.
Move Lever FORWARD to lower Hopper. This Lever
is mechanically linked to a dual control Lever on the
right side.
Right & Left Flow Gates: These control flow of
asphalt out of the Hopper. One Lever controls each
Gate. Move Lever BACK to open Gate. Move Lever
FORWARD to close Gate.
Side Gates: When paving only 9 ft. wide, the Side
Gates should be closed. This is achieved by closing the
Shut Off Gates with the Side Gate Valve ON, then turning the Side Gate Valve to the OFF position before reopening the Shut Off Gate.
Right & Left Feed Augers: These are used intermittently only with Extensions “out”. One Lever controls
each Auger. Move Lever BACK to turn on Auger.
Return Lever to “neutral” to turn off Auger. The right
Auger Lever is mechanically linked to a dual control
Lever on the right side.
SCREED PLATFORM CONTROLS
(Figs. 9-10)
Up & Down Position: Move the Lever BACK to
lower Screed so that it floats over asphalt feed forming
the finished mat surface. Move the Lever FORWARD
to raise Screed off mat.
Vibrator: This is used to agitate the mat of asphalt
passing under the Screed. Move the Lever BACK to
Fig. 6 - Track Travel Action
Fig. 7 - Side Gates (Left Side Shown)
1. Shut Off Valve
2.
Side Gate Cylinder
3. Side Gate
LOWER
FRAME
3
2
1
907389/AP297 20 Printed In U.S.A.
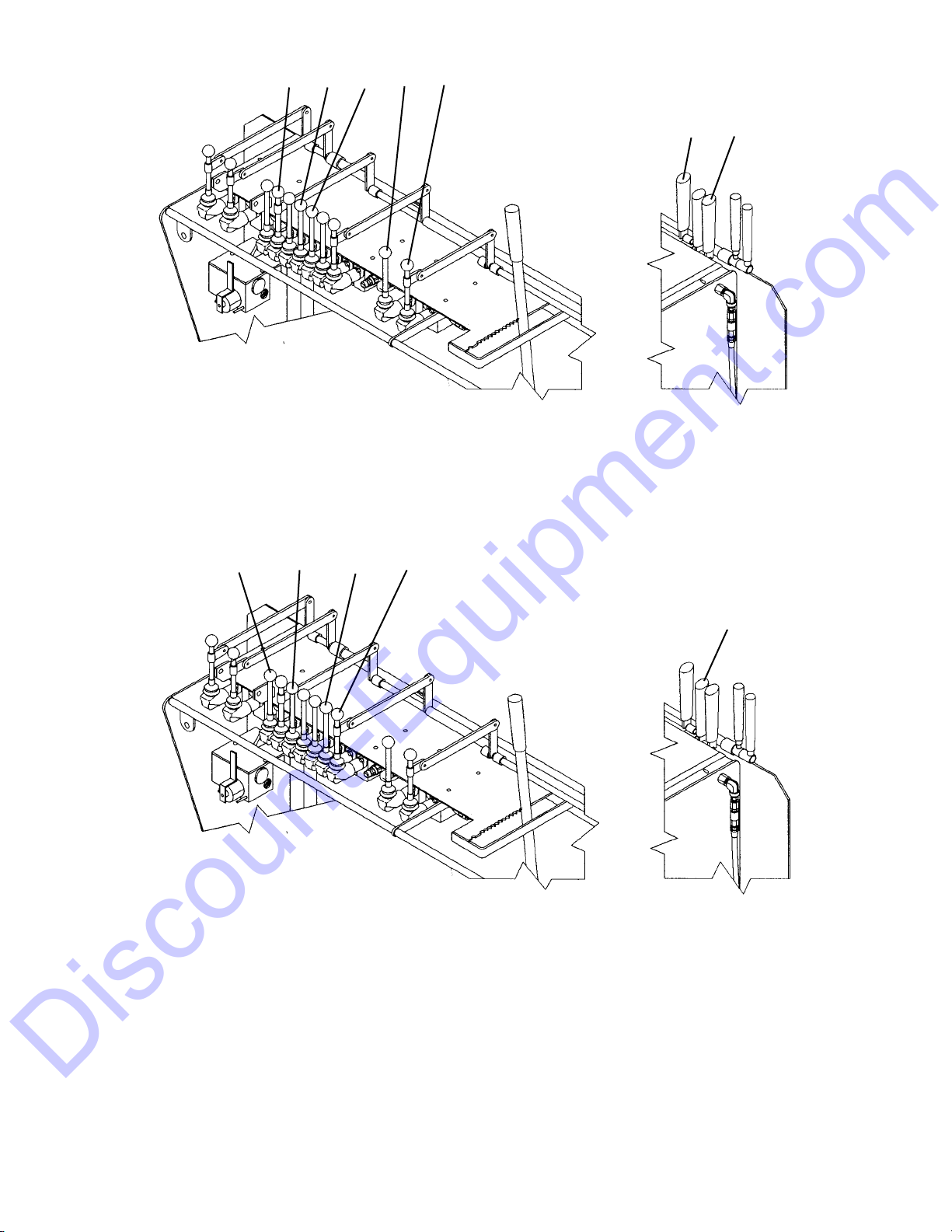
Fig. 8 - Hopper Controls On Backwall Console
1. Hopper Floor 4. Left Auger
2. Left Gate 5. Right Auger
3. Right Gate
Fig. 9 - Screed Controls On Backwall Console
1. Vibrator 3. Left Extension
2. Screed Lift 4. Right Extension
turn the Vibrator on. Allow the Lever to return to “neutral” to turn off the Vibrator.
Left & Right Extensions: These allow adjusting and
paving width beyond 9 feet. One Lever controls each
Extension. Move the Lever FORWARD to shift the
Extension inword. Move the lever BACK to shift the
Extension outward. The Right Extension Lever is
mechanically linked to Dual Control Levers on both
sides of the machine.
Depth Adjustment: The Screed has manually operated Adjustment Screws on each end that are used to set
the thickness of the asphalt mat. Turn the Screws
RT. SIDE CONTROL
51
1 2 3 4 5
RT. SIDE CONTROL
4
1234
Printed In U.S.A. 21 907389/AP297