
Installation & Operation Guide
Supporting Phase 1 Units
MDS 05-4819A01, Rev. 08
MAY 2010
MDS LCT 450
Tri-Mode Data Transceiver
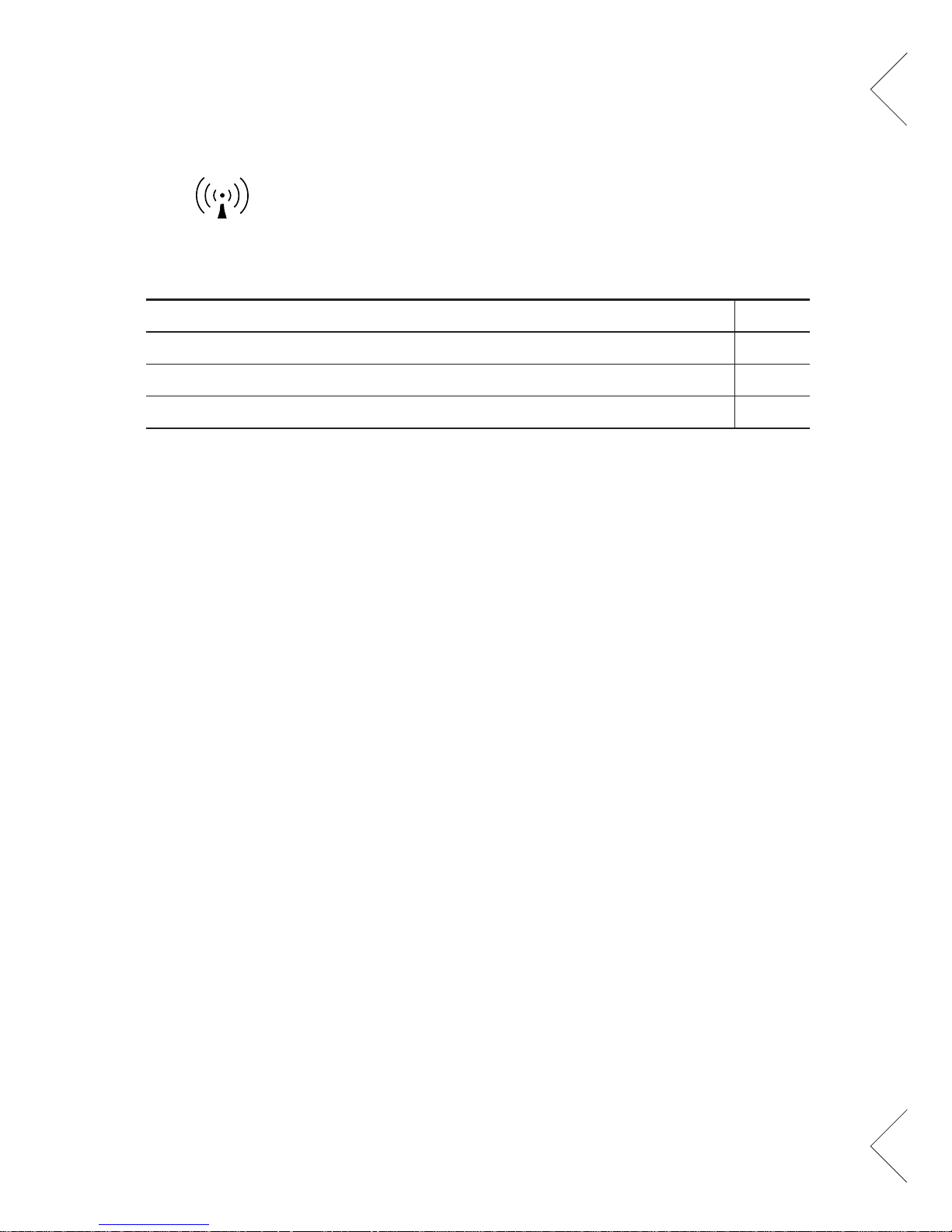
OPERATIONAL & SAFETY NOTICES
Concentrated energy from a directional antenna may pose a health
hazard to humans. Do not allow people to come closer to the antenna
than the distances listed in the table below when the transmitter is
operating. More information on RF exposure can be found online at
the following website:
www.fcc.gov/oet/info/documents/bulletins
Above data based on a 30-watt RF output level with a 100% duty cycle.
FCC Part 15 Notice
The transceiver is approved under Part 15 of the FCC Rules. Operation is subject to the following two conditions: (1) this device may not cause harmful interference, and (2) this device
must accept any interference received, including interference that may cause undesired operation. Any unauthorized modification or changes to this device without the express approval of
Microwave Data Systems may void the user’s authority to operate this device. Furthermore,
this device is intended to be used only when installed in accordance with the instructions outlined in this manual. Failure to comply with these instructions may void the user’s authority to
operate this device.
Antenna Gain vs. Recommended Safety Distance
Device complies with Power Density requirements at 20 cm separation: No
Required separation distance for 5 dBi antenna (in meters): 1.6
Required separation distance for 10 dBi antenna (in meters): 2.8
Required separation distance for 16.5 dBi antenna (in meters): 6.0
RF Exposure

05-4819A01, Rev. 08 LCT 450 Installation/Operation Guide
1
INTRODUCTION
This guide presents installation and operating instructions for the
MDS LCT 450 Series wireless transceiver.
The transceiver (Figure 1) is designed to operate in Railroad Distributed Power applications. It is software-configurable to provide flexible operation in a variety of applications using one hardware
platform. It employs microprocessor control and Digital Signal Processing (DSP) technology to provide robust communications even
under adverse conditions.
Figure 1. Data Transceiver
NOTE:
Some features may not be available on all units, based on the
options purchased and the applicable regulatory constraints
for the region in which the radio will operate.
Front Panel Connectors
Figure 2 and Figure 3 show the interface connectors and indicators on
the transceiver’s front and rear panels. These items are referenced in
the installation steps given later in this guide.

2 LCT 450 Installation/Operation Guide 05-4819A01, Rev. 08
Invisible place holder
Figure 2. Antenna & DC Power Connectors
Invisible place holder
Figure 3. Data Interface Connectors & LED Status Panel
DC Power Input
13.6 Vdc +/-15%
Antenna Connector
(UHF)
Power Connector:
Tyco/AMP Electronics 172129-1
LED Indicator Panel
P1 Control Interface Connect
(DB-25)
PWR
DCD
TXD
RXD
P2 Programming & Diagnostic
(DB-9)

05-4819A01, Rev. 08 LCT 450 Installation/Operation Guide
3
INSTALLATION
There are three main requirements for installing the transceiver as follows:
• Adequate and stable primary power
• An efficient and properly installed antenna system
• Correct data connections between the transceiver and the data
equipment.
Figure 4 shows a typical station arrangement. This is followed by
step-by-step procedures for installing the transceiver and making front
and rear panel connections.
Figure 4. Typical Station Arrangement
INTEGRATED PROCESSING
MODULE (IPM)
ANTENNA
SYSTEM
LOW-LOSS
COAXIAL CABLE
(50 Ohm)
RADIO
TRANSCEIVER
PL-259 UHF
CONNECTOR
DB-25M
CONNECTOR
Antenna Connector
DC POWER CABLE
Negative Ground
13.6 Vdc +/-15%
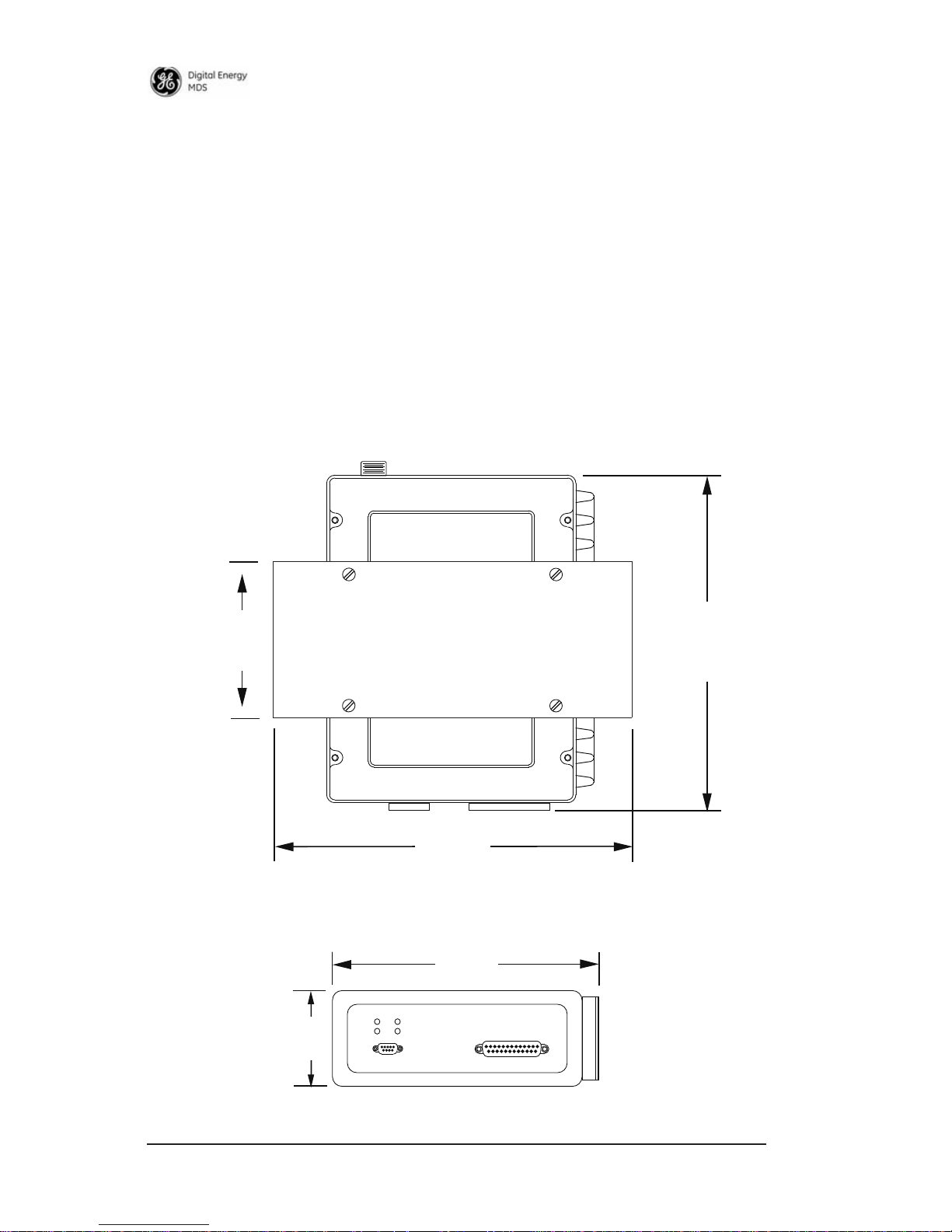
4 LCT 450 Installation/Operation Guide 05-4819A01, Rev. 08
Installation Steps
Below are the basic steps for installing the transceiver. Refer to
Figure 4 as necessary when making cable connections.
1.
Mount the transceiver to a stable surface using the U-shaped
bracket provided. Begin by attaching the radio’s mounting bracket
to the bottom of the transceiver case (if not already attached) using
the four 6-32 x 1/4 inch (6 mm) screws supplied. Figure 5 shows
the transceiver mounting dimensions with bracket attached.
NOTE:
To prevent moisture from entering the radio, do not mount the
case with the cable connectors pointing up. Also, dress all
cables to prevent moisture from running along the cables and
into the radio.
Invisible place holder
Figure 5. Transceiver Mounting Bracket Dimensions
6.86"
3.25"
83 mm
2.0"
51 mm
5.63"
143 mm
174.24 mm
177.80 mm
7.00"
U-Shaped Bracket
(Part No. 821753A14)

05-4819A01, Rev. 08 LCT 450 Installation/Operation Guide
5
Using screws longer than 1/4 inch (6 mm) to attach the
bracket to the radio may damage the internal PC board.
Use only the supplied screws.
Install the antenna and feedline for the station. The antenna
used with the transceiver must be designed to operate in the
radio’s frequency band, and be mounted in a location that provides a clear path to the other associated station(s). Use low loss
coaxial feedline and keep the cable as short as possible.
3.
Connect the data equipment to the
connector. Check P1 CONTROL INTERFACE on Page 24 for pin wiring
details.
NOTE:
port is used for entering configuration
commands and reprogramming the radio’s firmware.
4.
Connect primary power to the transceiver. Power applied must
be 13.6 Vdc (+/- 15%) and capable of providing at least 8
Amperes of continuous current. A power connector with is provided with each unit (see Figure 4).
The transceiver is designed for use with negative-ground systems only. The power supply should be
equipped with overload protection (NEC Class 2 rating),
to protect against a short circuit between its output terminals and the radio’s power connector.
This completes the installation of the transceiver.
SOFTWARE COMMANDS
Table 1 lists software commands commonly used during configuration
of the transceiver. In many cases, no changes or settings will be
required, as the radio is typically supplied ready for operation from the
factory. These commands are provided in the event future changes are
needed, or to facilitate troubleshooting of the unit.
These commands require a PC to be connected to the transceiver as
explained in the following steps:
1. Connect a PC to the transceiver’s
P2
connector as shown in
Figure 6. If desired, a connecting cable may be assembled using
the information shown on Page 26.
CAUTION
POSSIBLE
EQUIPMENT
DAMAGE
CAUTION
POSSIBLE
EQUIPMENT
DAMAGE
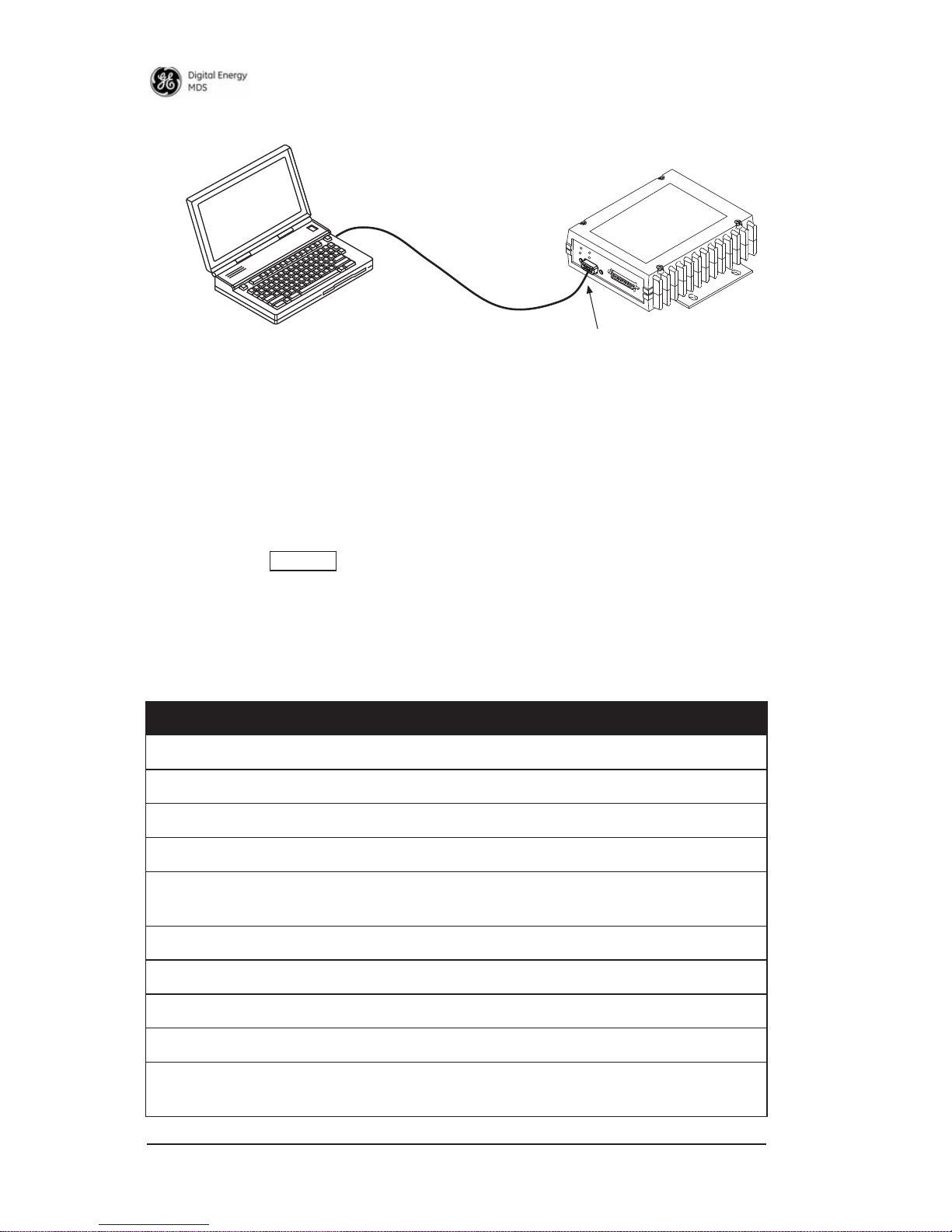
6 LCT 450 Installation/Operation Guide 05-4819A01, Rev. 08
Invisible place holder
Figure 6. PC Configuration Setup
2. Launch a terminal communications program, such as HyperTerminal (included with most Windows
systems). Data parameters
are 8 data bits, no parity, and 1 stop bit (8N1). Data rate is determined by autobaud, but 1115200 bps is the preferred speed.
3. Press the key a few times (at half-second intervals) to
obtain the ready “>” prompt on the screen. Commands may now
be entered from the keyboard.
Table 1. Command Summary
Command Name
Function
ALARM
Alarm Summary
AMASK
Alarm Mask
AUDIO
Audio Monitor/Orderwire Status
BOOT
Reboot Radio
CHAN
Channel commands (RX/TX frequency, RF
power, bandwidth)
CKEY
Key TX Continuously (Digital Only)
DATAKEY
Key on Data Activity
DUMP
Read Current Unit Profile
EMP
Modem TX Audio Pre-Emphasis
FSET
Receive or Transmit frequency mini/max
value
PC Running Terminal Session
Transceiver
To DB-9
Management Port
ENTER
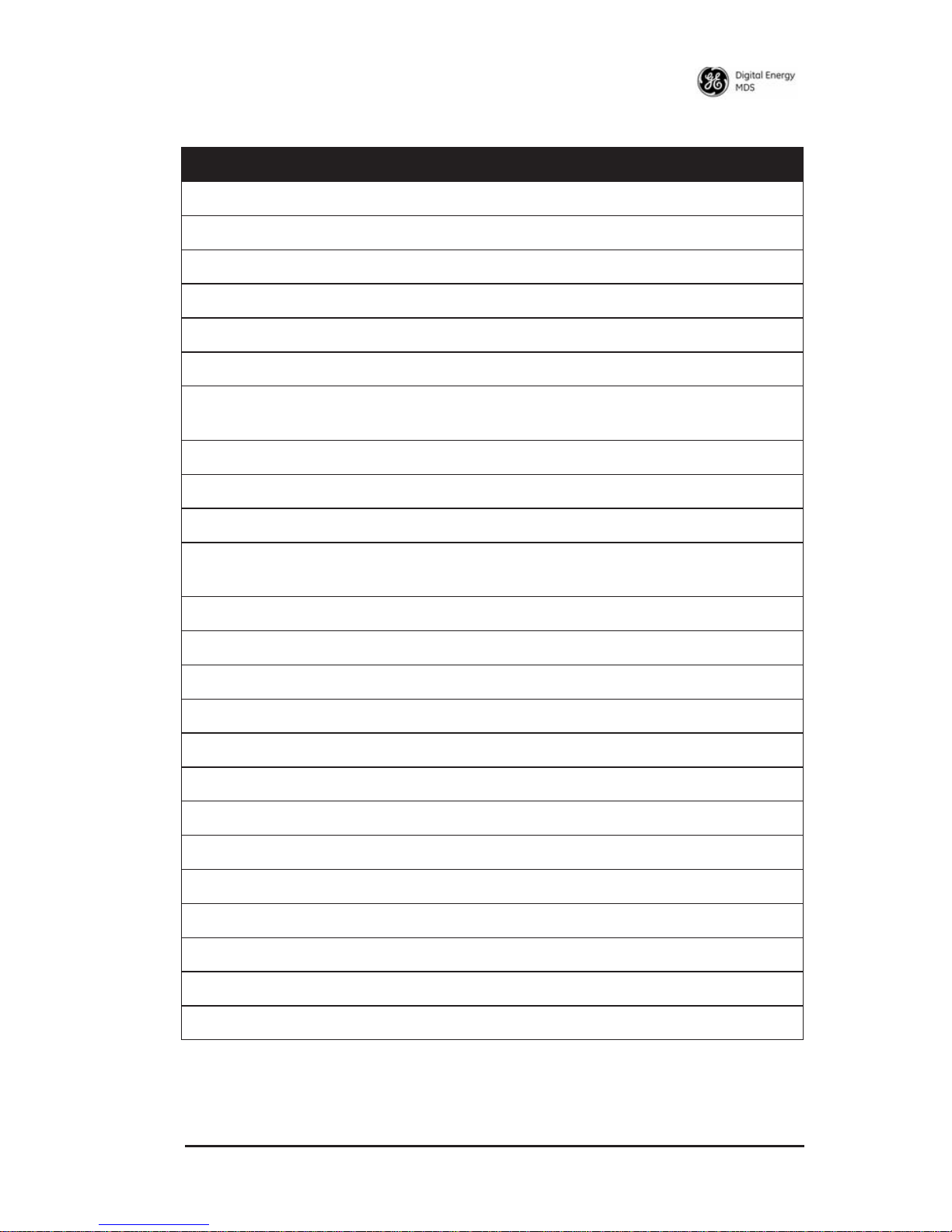
05-4819A01, Rev. 08 LCT 450 Installation/Operation Guide
7
HELP
User Help
HREV
Display Hardware Revision
INIT
Initialize EEPROM Defaults
MODE
Radio Mode
MODEL
Model Number Information
MTYPE
Modem Family Type
OPT, OPTION,
OPTIONS
Display Authorized Options
OWM
Owner’s Message
OWN
Owner’s Name
PROG
Program
PWRL, PWRM, PWRH,
PWRRXH
Power Lo (5W), Medium (20W), Hi (25),
Extra-High (30W)
PTT
Push-to-Talk Delay
REF
Reference Frequency
RSSI
Received Signal Strength Indicator
RXTOT
Loss of RX Data Alarm Time
SER
Radio’s Serial Number
SHOW
Show Power Settings
SPECTRUM
Internal Spectrum Analyzer
SQUELCH
Squelch Operation
SREV
Software/Firmware Revision Level
STAT
Alarm Status
TEMP
Internal Temperature
TOT
TX Timeout-Timer
VERSION
Firmware Version
Table 1. Command Summary
(Cont’d)
Command Name
Function
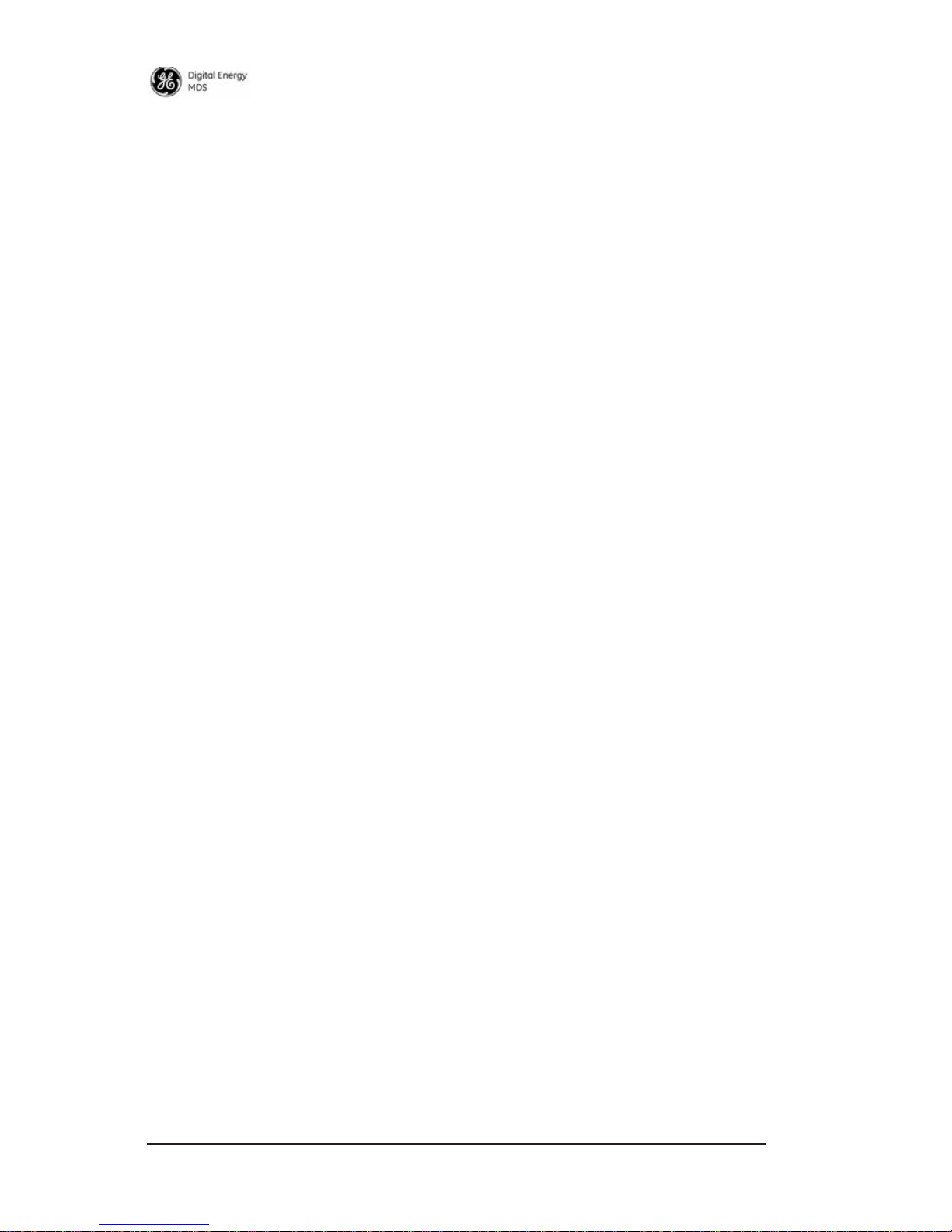
8 LCT 450 Installation/Operation Guide 05-4819A01, Rev. 08
DETAILED USER COMMANDS
The commands in this section may be used in two ways. First, you can
type only the command name to view the currently programmed data.
Secondly, you can set or change the existing data by typing the command, followed by a space, and then the desired entry. In the list
below, allowable programming variables, if any, are shown in brackets
following the command name.
ALARM
command displays a summary of the radio's current operating condition. An eight-digit code will be presented which can be
decoded as described in “Major Alarms vs. Minor Alarms”.
AMASK [0000 0000-FFFF FFFF]
command displays or sets which events cause an alarm
output signal to be active. Normally, the mask is
FFFF FFFF
, meaning
that any of the 32 possible events will activate the alarm output signal.
Entering the
AMASK
command alone displays the current setting of
alarm events in hexadecimal format. Entering the
AMASK
command
followed by an eight-digit hexadecimal number reprograms the specified events to trigger an alarm. The eight-digit hexadecimal number
used as the command parameter specifies 0 to 32 events that can
trigger the external alarm output. The hex value for the mask corresponds to the hex value for the
STAT
command. Each bit that is a '1'
identifies an alarm condition that can trigger the external output. For
more information on configuring the alarm response, contact GE
MDS.
ASENSE [HI/LO]
command sets or displays the sense of the alarm output
at Pin 6 of the COM2 port. Entering the
ASENSE
command alone
shows whether the alarm output is active high or low. Entering the
ASENSE
resets the alarm output to
active high or low.