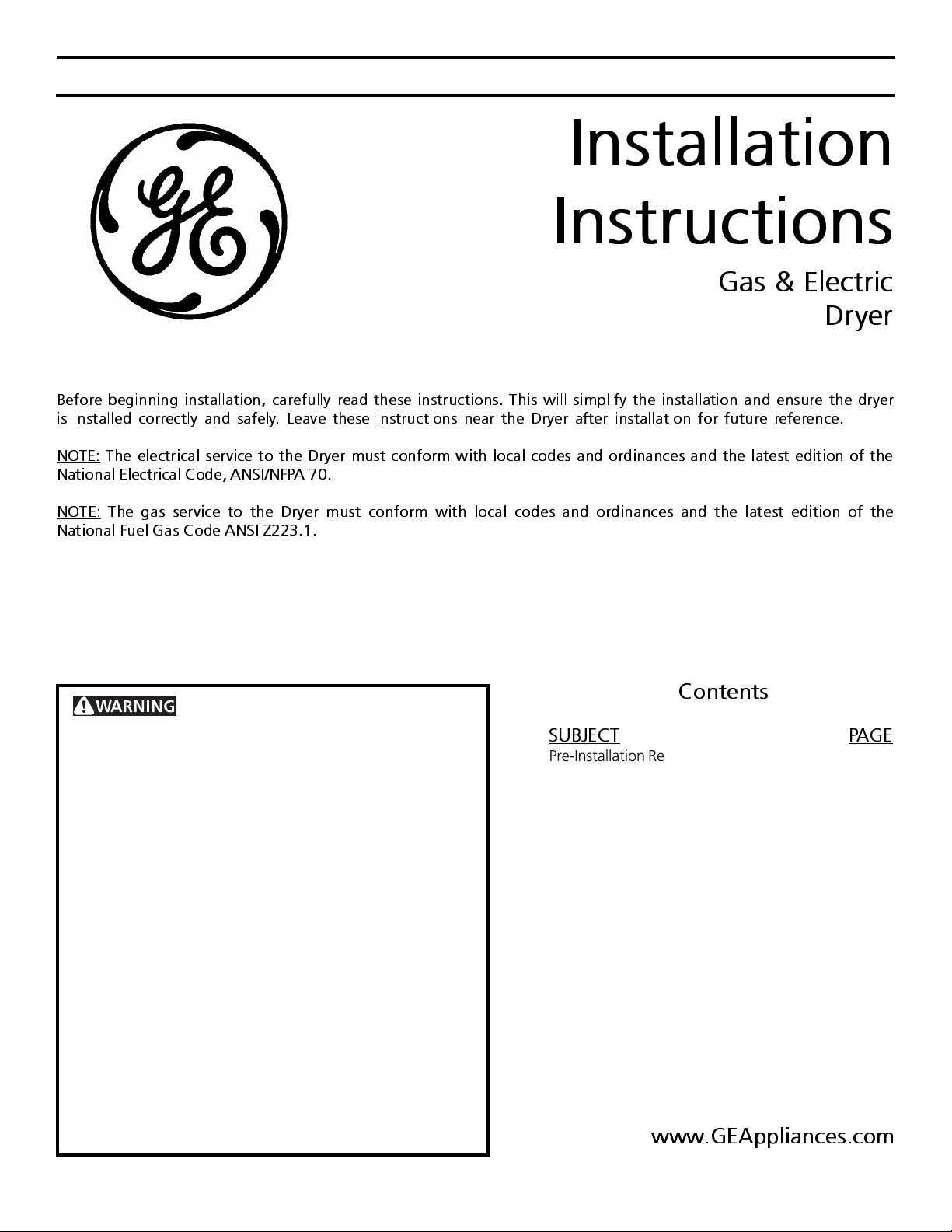
Installation
Instructions
Gas & Electric
Dryer
Before beginning installation, carefully read these instructions. This will simplify the installation and ensure the dryer
is installed correctly and safely. Leave these instructions near the Dryer after installation for future reference.
NOTE: The electrical service to the Dryer must conform with local codes and ordinances and the latest edition of the
National Electrical Code, ANSI/NFP A 70.
NOTE: The gas service to the Dryer must conform with local codes and ordinances and the latest edition of the
National Fuel Gas Code ANSI Z223.1.
For your safety the information in
this manual must be followed to minimize the risk
of fire or explosion or to prevent property damage,
personal injury or loss of life.
- Do not store or use gasoline or other flammable
vapors and liquid in the vicinity of this or any other
machine.
- WHAT TO DO IF YOU SMELL GAS
· Do not try to light any machine.
· Do not touch any electrical switch; do not use
any phone in your building.
· Clear the room, building or area of all
occupants.
· Immediately call your gas supplier from a
neighbor’s phone. Follow the gas supplier's
instructions.
· If you cannot reach your gas supplier, call the
fire department.
Installation and service must be performed by a
qualified installer, service agency or the gas
supplier.
Contents
SUBJECT PAGE
Pre-Installation Requirements 2
Electrical Requirements 2
Exhaust System Requirements 2-3
Gas Supply Requirements 3
Location of Your Dryer 4
Rough-In Dimensions 5
Unpacking 5
Reversing Door Swing 5
Electrical Installation 6
Grounding Requirements 6
Electrical Connections—3-wire 7
Electrical Connections—4-wire 7
Installation 8
Replacement Parts 8
Lint Blade Retaining Pin Location 8
www.GEAppliances.com
Printed in U.S.A.
Pub # 31-15540
P/N 134206400 (0212)
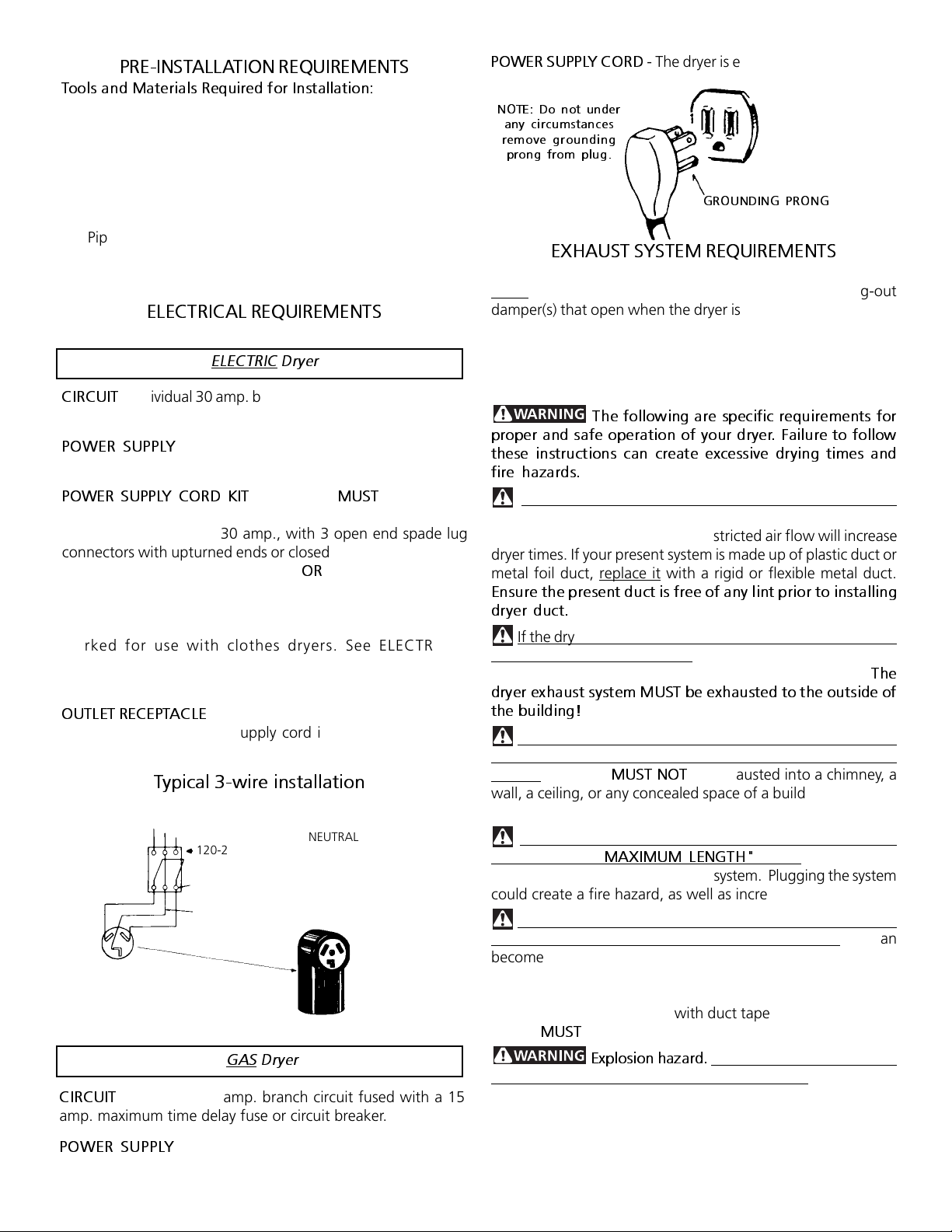
PRE-INST ALLATION REQUIREMENTS
Tools and Materials Required for Installation:
1. Phillips head screwdriver.
2. Channel-lock adjustable pliers.
3. Carpenter's level.
4. Flat or straight blade screwdriver.
5. Duct tape.
6. Rigid or flexible metal 4 inch (10.2 cm) duct.
7. Vent hood.
8. Pipe thread sealer (Gas).
9. Plastic knife.
ELECTRICAL REQUIREMENTS
ELECTRIC Dryer
CIRCUIT
- Individual 30 amp. branch circuit fused with 30 amp.
minimum time delay fuses or circuit breakers.
POWER SUPPLY
- 3 wire, 240 volt, single phase, 60 Hz,
Alternating Current.
POWER SUPPLY CORD KIT
- The dryer
MUST
employ a 3conductor power supply cord NEMA 10-30 type SRDT rated at
240 volt AC minimum, 30 amp., with 3 open end spade lug
connectors with upturned ends or closed loop connectors and
marked for use with clothes dryers, OR a 4-conductor power
supply cord NEMA 14-30 type SRDT or ST (as required) rated at
240 volt AC minimum, 30 amp., with 4 open end spade lug
connectors with upturned ends or closed loop connectors and
marked for use with clothes dryers. See ELECTRICAL
CONNECTIONS FOR A 4-WIRE SYSTEM.
OUTLET RECEPT ACLE
- NEMA 10-30R or 14-30R receptacle to
be located so the power supply cord is accessible when the
dryer is in the installed position.
Typical 3-wire installation
POWER SUPPLY
OUTLET
RECEPTACLE
(COPPER)
SUBJECT TO LOCAL REGULATIONS
CIRCUIT
- Individual 15 amp. branch circuit fused with a 15
amp. maximum time delay fuse or circuit breaker.
POWER SUPPLY
Alternating Current.
3 WIRE GROUNDED NEUTRAL
120-240 VOLT 60 CYCLE
MAIN FUSE BOX
30 AMP DELAYED ACTION
FUSES
OR CIRCUIT BREAKER
NEUTRAL WIRE
NEMA 10-30R (COPPER)
GAS Dryer
- 3 wire, 120 volt single phase, 60 Hz,
POWER SUPPL Y CORD
- The dryer is equipped with a 120 volt
3-wire power cord.
NOTE: Do not under
any circumstances
remove grounding
prong from plug.
GROUNDING PRONG
EXHAUST SYSTEM REQUIREMENTS
Use only 4 inch (10.2 cm) diameter (minimum) rigid or flexible
metal duct and approved vent hood which has a swing-out
damper(s) that open when the dryer is in operation. When the
dryer stops, the dampers automatically close to prevent drafts
and the entrance of insects and rodents. To avoid restricting the
outlet, maintain a minimum of 12 inches (30.5 cm) clearance
between the vent hood and the ground or any other obstruction.
The following are specific requirements for
proper and safe operation of your dryer. Failure to follow
these instructions can create excessive drying times and
fire hazards.
Do not use plastic flexible duct to exhaust the dryer.
Excessive lint can build up inside exhaust system and create a
fire hazard and restrict air flow. Restricted air flow will increase
dryer times. If your present system is made up of plastic duct or
metal foil duct, replace it with a rigid or flexible metal duct.
Ensure the present duct is free of any lint prior to installing
dryer duct.
If the dryer is not exhausted outdoors, some fine lint will be
expelled into the laundry area. An accumulation of lint in any
area of the building can create a health and fire hazard.
dryer exhaust system MUST be exhausted to the outside of
the building!
Do not allow combustible materials (for example: clothing,
draperies/curtains, paper) to come in contact with exhaust
system. The dryer
wall, a ceiling, or any concealed space of a building which can
accumulate lint, resulting in a fire hazard.
Exceeding the length of duct pipe or number of elbows
allowed in the "
accumulation of lint in the exhaust system. Plugging the system
could create a fire hazard, as well as increase drying times.
Do not screen the exhaust ends of the vent system, nor use
any screws or rivets to assemble the exhaust system. Lint can
become caught in the screen, on the screws or rivets, clogging
the duct work and creating a fire hazard as well as increasing
drying times. Use an approved vent hood to terminate the duct
outdoors, and seal all joints with duct tape. All male duct pipe
fittings
MUST
gasoline or other flammables are kept or stored. If the dryer is
installed in a garage, it must be a minimum of 18 inches (45.7
cm) above the floor. Failure to do so can result in death, explosion,
fire or burns.
2
MUST NOT
MAXIMUM LENGTH"
be exhausted into a chimney, a
charts can cause an
be installed downstream with the flow of air.
Explosion hazard.
Do not install the dryer where
The
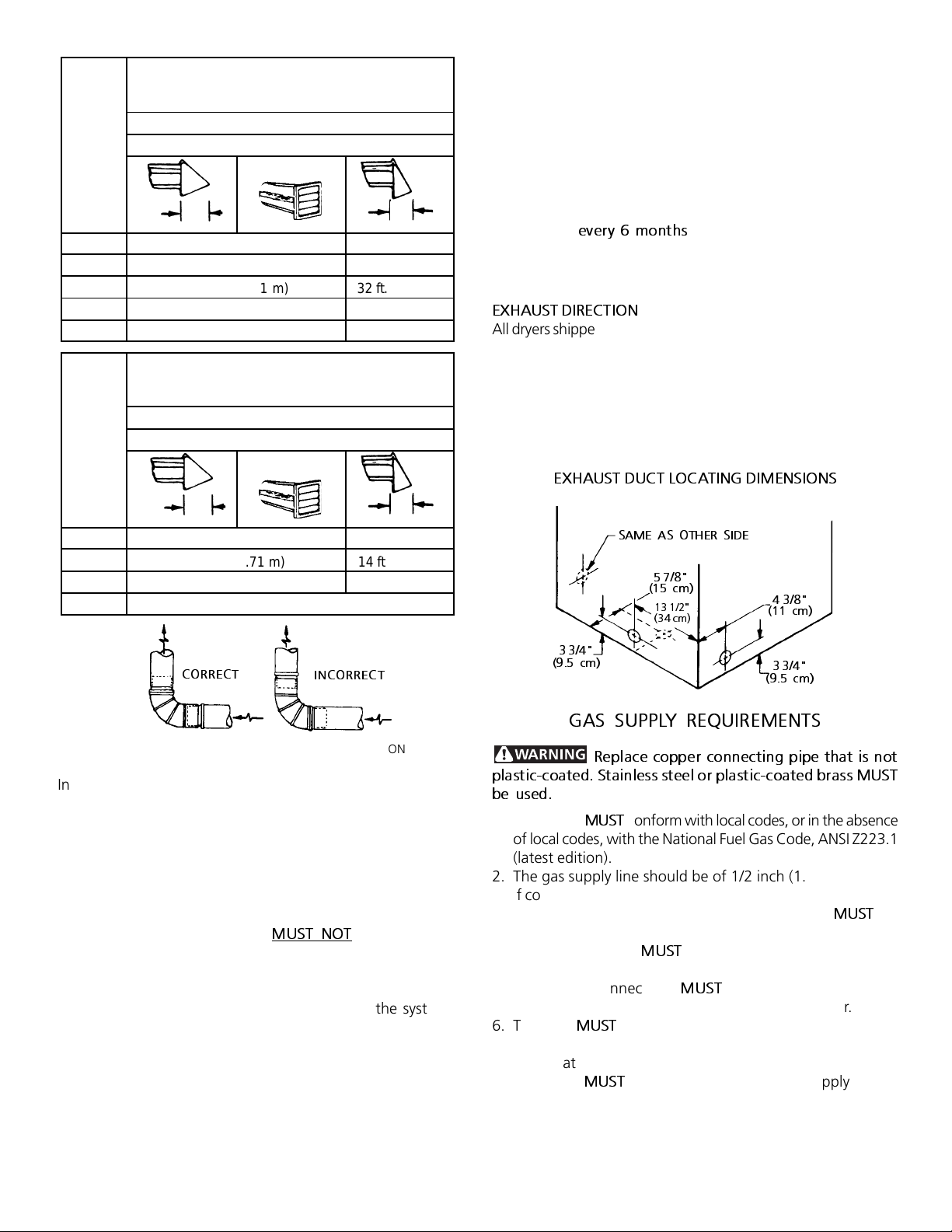
MAXIMUM LENGTH
of 4” (10.2 cm) Dia. Rigid Metal Duct
VENT HOOD TYPE
(Preferred)
Number
of
90°
Turns
0 60 ft. (18.28 m) 48 ft.(14.63 m)
1 52 ft. (15.84 m) 40 ft.(12.19 m)
2 44 ft. (13.41 m) 32 ft. (9.75 m)
3 32 ft. (9.75 m) 24 ft. (7.31 m)
4 28 ft. (8.53 m) 16 ft. (4.87 m)
4”
(10.2 cm)
Louvered
2½"
(6.35 cm)
MAXIMUM LENGTH
of 4” (10.2 cm) Dia. Flexible Metal Duct
VENT HOOD TYPE
(Preferred)
Number
of
90°
Turns
0 30 ft. (9.14 m) 18 ft. (5.49 m)
1 22 ft. (6.71 m) 14 ft. (4.27 m)
2 14 ft. (4.27 m) 10 ft. (3.05 m)
3 NOT RECOMMENDED
4”
(10.2 cm)
Louvered
2½"
(6.35 cm)
• Venting vertical through a roof may expose the exhaust
system to down drafts causing an increase in vent
restriction.
• Running the exhaust system through an uninsulated area
may cause condensation and faster accumulation of lint.
• Compression or crimping of the exhaust system will cause
an increase in vent restriction.
The exhaust system should be inspected and cleaned a
minimum of
every 6 months
with normal usage. The more
the dryer is used, the more often you should check the
exhaust system and vent hood for proper operation.
EXHAUST DIRECTION
All dryers shipped from the factory are set up for rear exhausting.
However, on electric dryers, exhausting can be to the right or
left side of the cabinet or the bottom of the dryer. On gas dryers,
exhausting can be to the right side of the cabinet or the bottom
of the dryer. Directional exhausting can be accomplished by
installing Exhaust Kit, P/N 131456800, available through your
parts distributor. Follow the instructions supplied with the kit.
EXHAUST DUCT LOCA TING DIMENSIONS
SAME AS OTHER SIDE
5 7/8"
(15 cm)
13 1/2"
(34 cm)
4 3/8"
(11 cm)
CORRECT
INSTALL MALE FITTINGS IN CORRECT DIRECTION
INCORRECT
In installations where the exhaust system is not described in the
charts, the following method must be used to determine if the
exhaust system is acceptable:
1. Connect an inclined or digital manometer between the
dryer and the point the exhaust connects to the dryer.
2. Set the dryer timer and temperature to air fluff (cool
down) and start the dryer.
3. Read the measurement on the manometer.
4. The system back pressure
MUST NOT
be higher than
0.75 inches of water column. If the system back
pressure is less than 0.75 inches of water column, the
system is acceptable. If the manometer reading is
higher than 0.75 inches of water column, the system is
too restrictive and the installation is unacceptable.
Although vertical orientation of the exhaust system is
acceptable, certain extenuating circumstances could affect the
performance of the dryer:
• Only the rigid metal duct work should be used.
3 3/4"
(9.5 cm)
3 3/4"
(9.5 cm)
(9.5 cm)
GAS SUPPLY REQUIREMENTS
Replace copper connecting pipe that is not
plastic-coated. Stainless steel or plastic-coated brass MUST
be used.
1. Installation
of local codes, with the National Fuel Gas Code, ANSI Z223.1
(latest edition).
2. The gas supply line should be of 1/2 inch (1.27 cm) pipe.
3. If codes allow, flexible metal tubing may be used to connect
your dryer to the gas supply line. The tubing
constructed of stainless steel or plastic-coated brass.
4. The gas supply line
5. A 1/8 inch (0.32 cm) N.P.T. plugged tapping, accessible for
test gauge connection,
upstream of the gas supply connection to the dryer.
6. The dryer
system during any pressure testing of the gas supply piping
system at test pressures in excess of 1/2 psig (3.45 kPa).
7. The dryer
system during any pressure testing of the gas supply piping
system at test pressures equal to or less than 1/2 psig (3.45
kPa).
MUST
conform with local codes, or in the absence
MUST
have an individual shutoff valve.
MUST
be installed immediately
MUST
be disconnected from the gas supply piping
MUST
be isolated from the gas supply piping
MUST
be
3