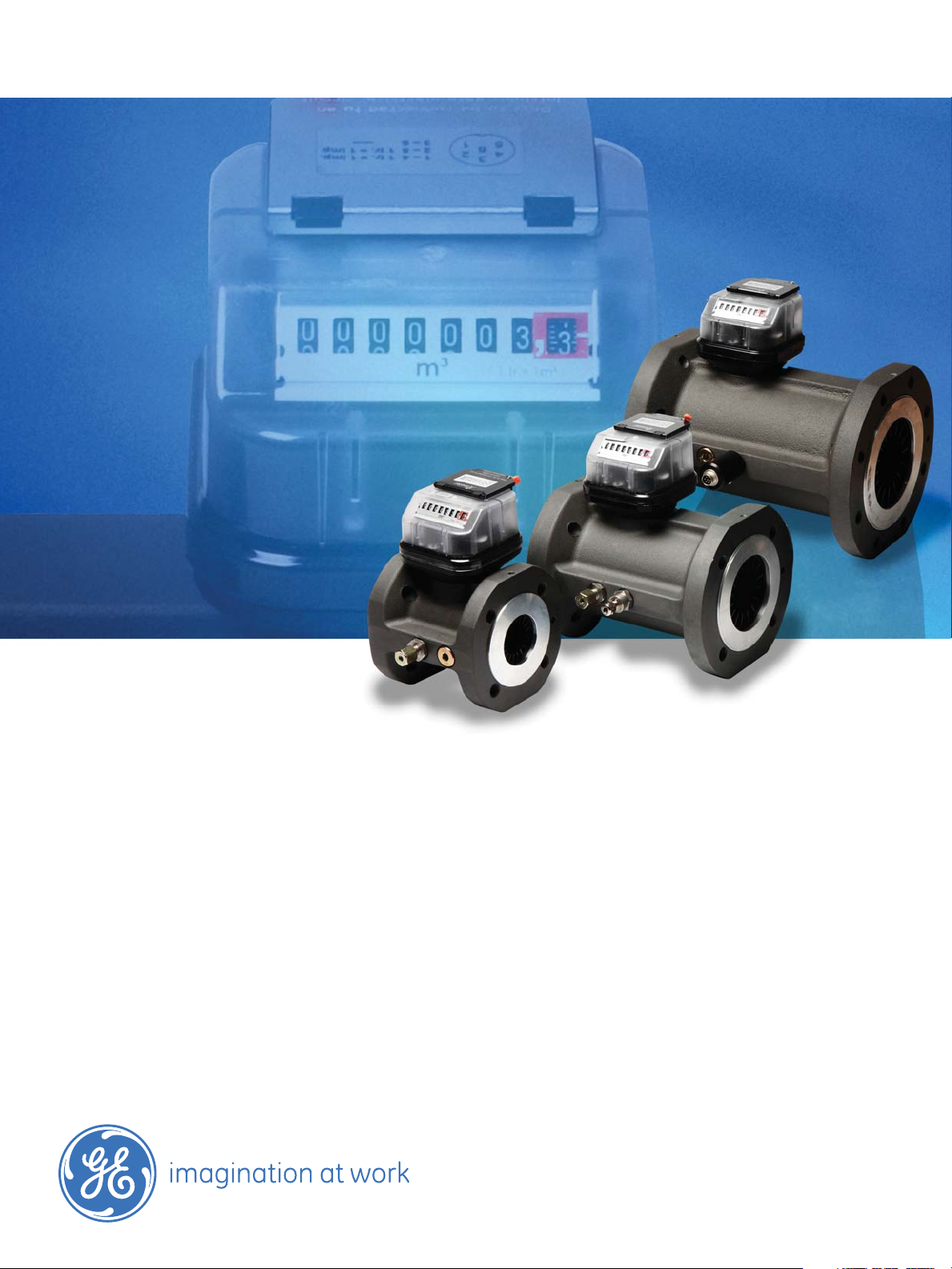
GE Oil & Gas
Dresser* Turbine Meters
Above all - accuracy and reliability
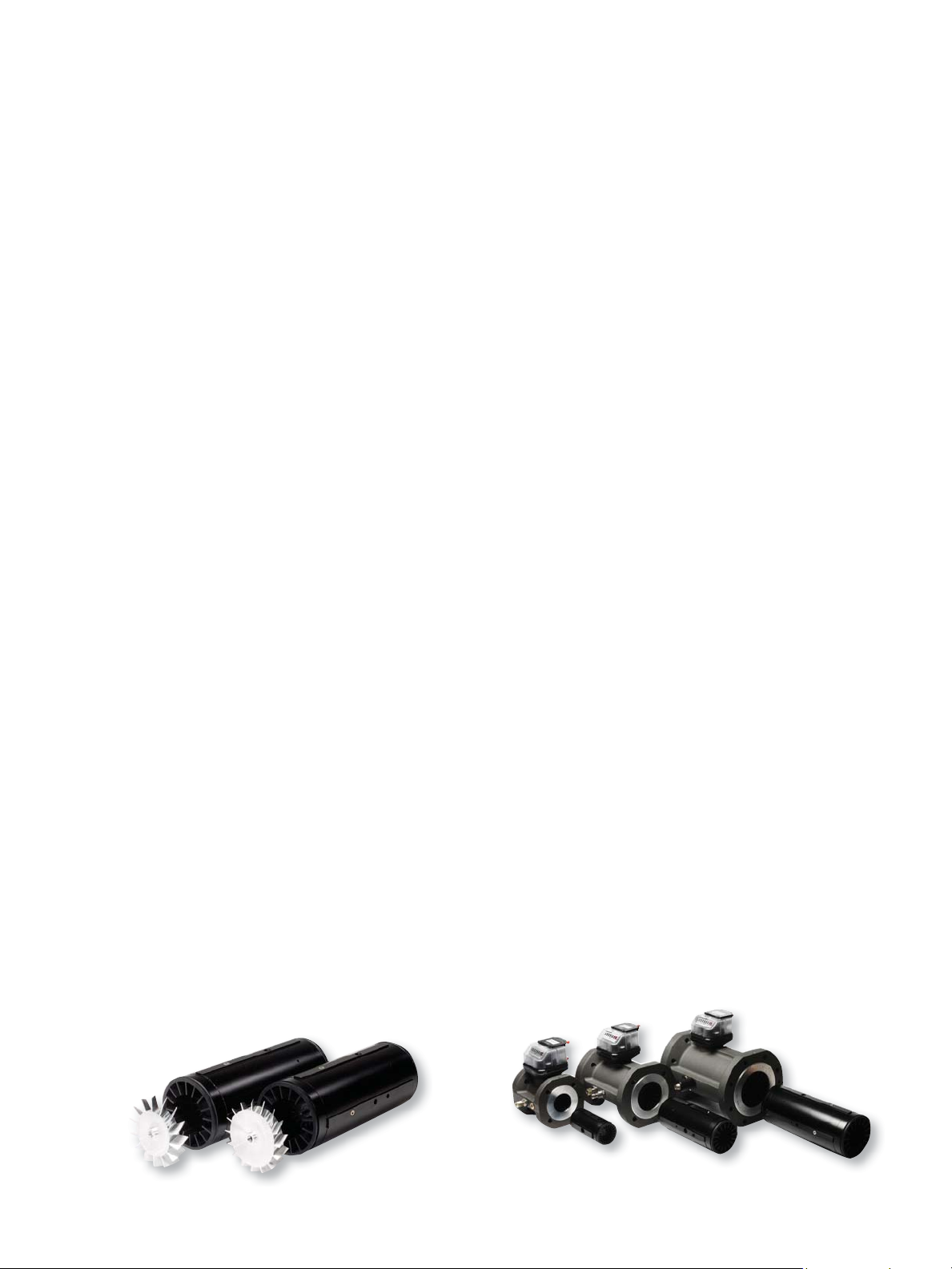
GE Oil & Gas’ innovative Dresser
Turbine Meter helps reduce installation
and maintenance costs while
improving measurement accuracy
Built with Operation in Mind
Designed to measure gas velocity, the operating
principle of the turbine meter incorporates an
innovative method of conditioning flow in the
meter body. A straightening section in the
meter body conditions the gas flow by removing
undesired swirl, and turbulence before it reaches
the turbine rotor. The dynamic forces from gas flow
initiate rotation of the turbine rotor. The precision
machined rotor, mounted on an axial shaft,
includes high quality, low friction stainless steel
ball bearings to allow world class measurement
accuracy.
The turbine rotor has helical blades and a known
angle relative to the gas flow. The turbine rotor
angular velocity is proportional with the gas
velocity. The rotating movement of the turbine
rotor and primary gear train, all fitted in a
pressurized body; drive an externally mounted
exchangeable 8-digit mechanical counter. The
counter assembly provides readout represented
in engineering units such as cubic meters. Two LF
(low frequency) pulse outputs are included in the
standard counter assembly.
GE’s turbine meters are approved for custody
transfer applications and used by natural gas
transmission and gas distribution companies.
Design Features
■
Removable meter cartridge assembly
■
Optimized bearing construction
■
Oil flushing and lubrication system
■
Multi-stage flow conditioner
■
Multi-functional Index assembly
■
Light weight aluminum body
Meter Cartridge Assembly
GE’s Dresser Turbine Meter product line extends
from G40 through G4000. Aluminum bodies can
operate up to 8” (20 bar) and steel bodies up to
12” (100 bar). All sizes incorporate an innovative,
removable measurement cartridge assembly.
The removable cartridge enables users to change
the meter’s volume capacity or perform critical
maintenance by removing and installing a new
cartridge. The flexibility of the removable cartridge
provides cost savings for common meter repairs,
upgrades, and testing. The removable cartridge
also gives users flexibility in designing cost effective meter stations, especially when end user
requirements call for an increase in meter capacity.
The Dresser Turbine Meter is available with
enhanced volumetric capacity by utilizing four
different cartridge sizes for each meter body.
2
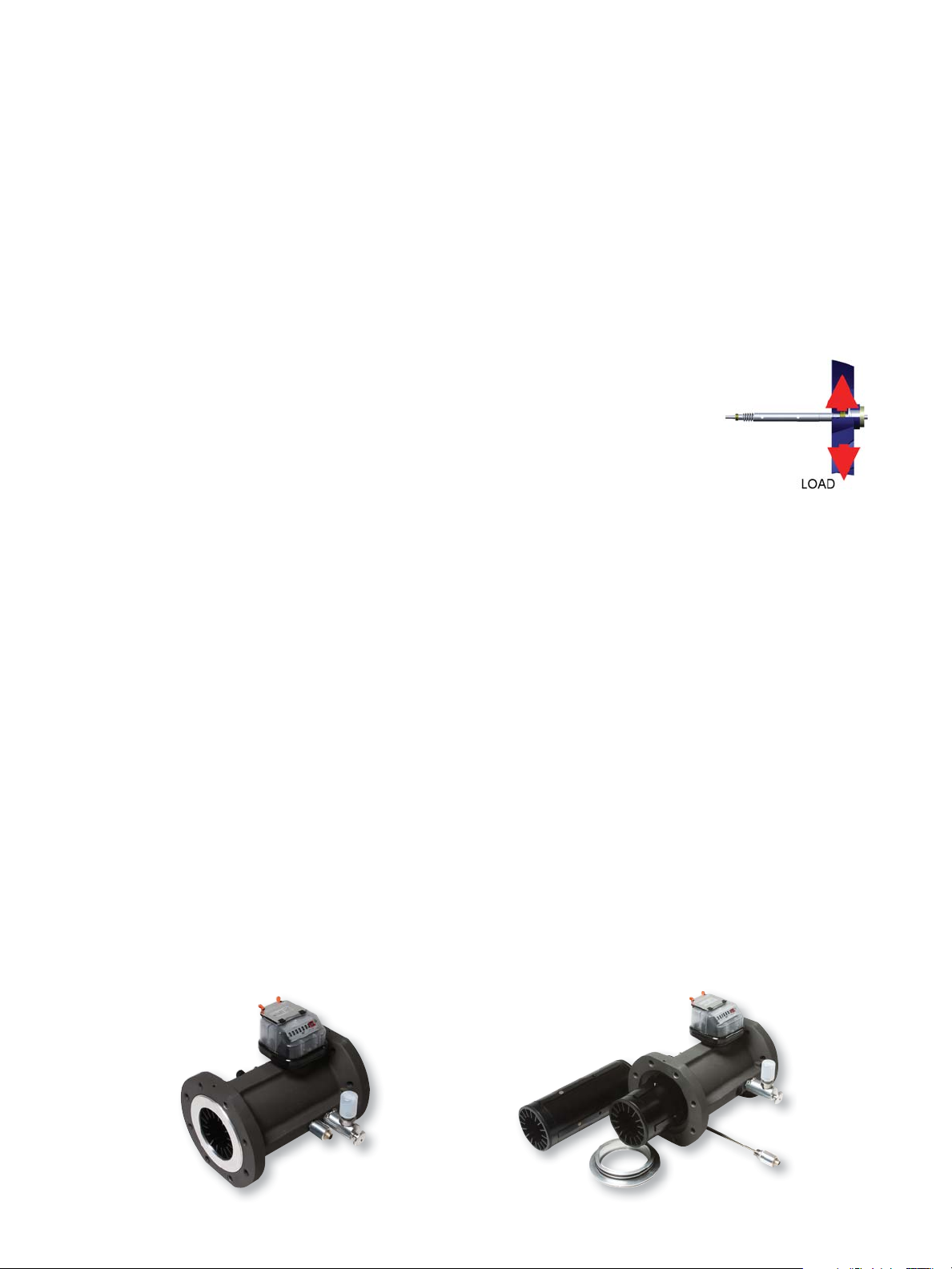
This feature offers modular flexibility in terms of
minimum and maximum capacity. In accordance
with European Standard EN 12261, 6.4 Removable
meter mechanism, 6.4.1 Integrity, 6.4.1.1
Requirements that states “the design and integrity
of a meter with removable mechanism or cartridge
shall not be affected by the removal or replacement
of the measuring element or cartridge. A meter will
be deemed to meet this requirement if it remains leak
tight, as defined in 6.2.3, when subjected to the test
given in 6.4.2”.
For example, the 6” turbine meter body may be
ordered with a Qmax of 650 m3/h, 1000 m3/h,
1600 m3/h, or 2500 m3/h.
If load parameters change customers can change
the measurement cartridge. This unique feature
offers a distinct cost savings advantage, reducing
the need to replace a complete meter or redesigning
the metering station.
The length of the meter is three times the pipe
diameter (3d) in compliance with the European
directives for turbine meters. The cartridge and
turbine wheel are machined from high quality
aluminum to offer long term reliability and stability.
All cartridges are hard-coated (anodized) to reduce
wear and corrosion of the flow channels caused by
contaminates within the gas stream.
Customers can purchase new, pre-calibrated
cartridges with a calibration certificate. As an
option and at an additional charge, we can supply
the cartridge with certified calibration at elevated
pressure by an independent test facility. The existing
measurement cartridge can then be exchanged
with a new, light weight, pre-calibrated cartridge by
removing the special ring that positions and holds
the cartridge inside the meter body.
Optimized Bearing Construction
with Axial Load Compensation
Since the axial load on the bearings is proportional
to the density of the flowing gas, this load increases
significantly when the meter operates at elevated
pressures. The Dresser Turbine Meter reduces the
axial load on bearings operating at elevated pressures with our innovative Axial Load Compensation
(ALC) design feature. The Axial Load Compensation
design feature induces slightly
higher pressure
downstream of the turbine
wheel, thus reducing mechanical friction on the bearings. To
further enhance bearing life
we located bearings and gears
upstream of the turbine wheel.
This protects bearings from
contaminates, especially contaminates that tend to
accumulate around the turbine wheel.
Oil Refreshing & Flushing
Lubrication System
The Dresser Turbine Meter product incorporates
high quality precision bearings that should be kept
clean and lubricated. Meter performance is optimized
by flushing contamination from the bearings
and refreshing or adding of oil during operation.
Recommendations as to when to lubricate turbine
meters varies by product design, customer procedures, and regulatory requirements. Many regulatory
agencies extend turbine meter re-calibration intervals when utilizing an automatic lubricating system.
For example, Germany extends the re-calibration
frequency from eight to twelve years when users
utilize a turbine meter with a lubrication device or
system.
3