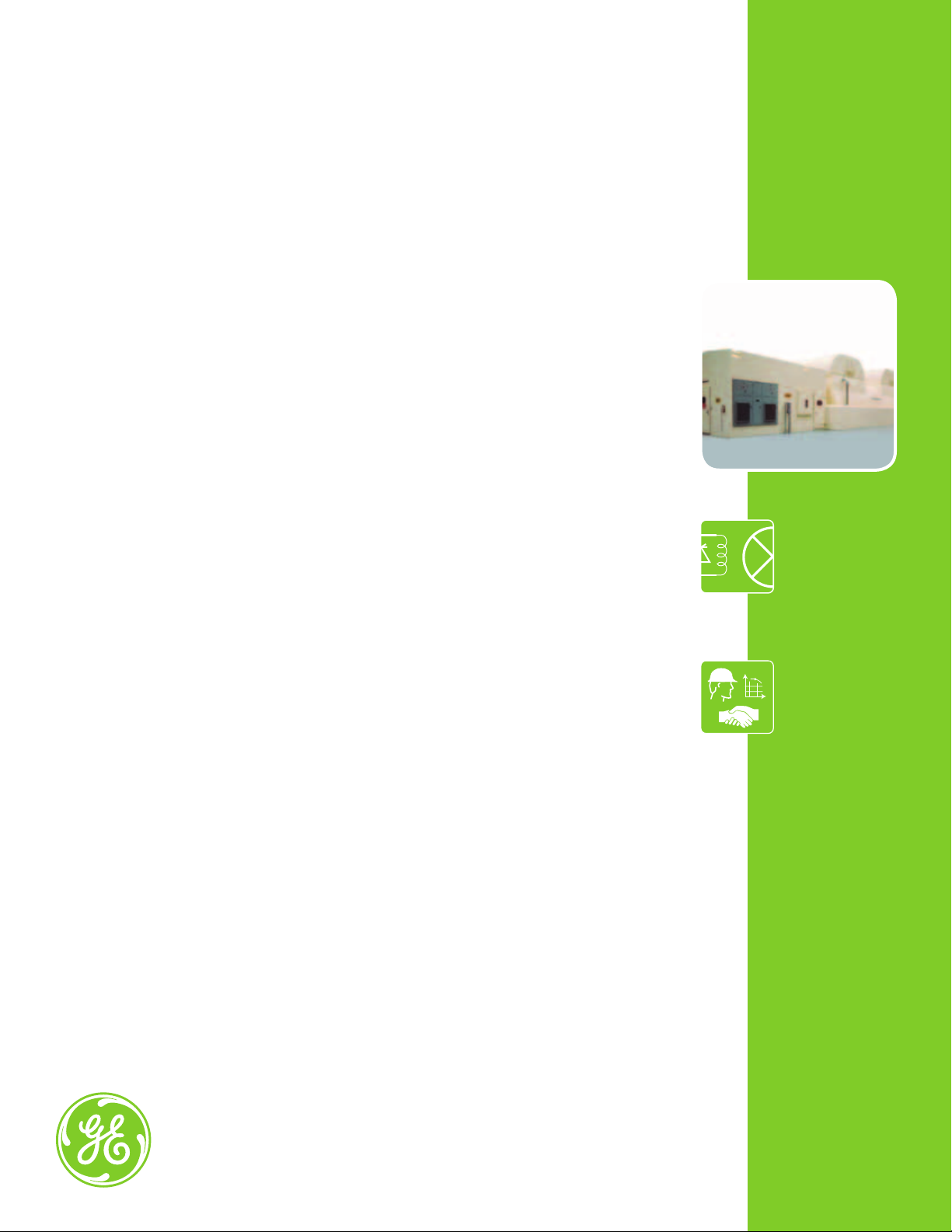
GE Energy Services
CUSTOMER SUCCESS STORY
CONTROL SOLUTIONS
DTE ENERGY: DETROIT EDISON MONROE UNIT 4, MONROE, MICHIGAN
“ Detroit Edison values continuous improvement and GE Energy Services
provided a great example of this. They worked with us through schedule
constraints, listened to our concerns and were creative in scheduling and
managing the people working on our equipment. They accomplished in 14
days what typically takes four weeks. It was a pleasure to work with them.”
—Mark Kimmel – Turbine Outage System Lead – DTE Energy, Monroe Michigan
PROBLEM
Detroit Edison, one of the largest operating subsidiaries of DTE Energy, generates and distributes
electricity to 2.2 million customers in southeastern Michigan. Detroit Edison’s Monroe Power Plant
is the largest generating plant in DTE Energy’s system and the fourth largest coal-fired plant
in the country. A brief scheduled outage presented an opportunity to proactively refurbish the
plant’s Alterrex excitation systems with new diode bridges. This procedure typically takes up to
28 calendar days; however the plant had just 22 calendar days to complete the upgrade. Without
a commitment to this schedule the plant would have postponed the upgrade until the next
scheduled outage; risking an unscheduled outage if the existing bridges failed.
SOLUTION
GE committed to the accelerated schedule and replaced each diode bridge assembly
with its latest EX2100 Alterrex diode bridges. The new bridges feature:
• One continuous stainless steel cooling tubing per bridge, with all stainless tubing, isolation
valves and standard industrial fittings throughout the diode stator water cooling loop.
• A new diagnostic interface panel providing thermal monitoring via bridge mounted thermistors,
fuse monitoring and remote alarm connections as well as DCS and unit control interface.
• A simplified bridge alarm annunciation panel with LED indicators and test provisions.
By working overtime and weekends, and collaborating with suppliers, the GE factory in Longmont,
Co. was able to shave three days off the already tight schedule.
Power Generation – Coal-Fired
EX2100 Generator
Controls
Service & Expertise
Delivered
RESULT
Through the commitment and effort by GE Energy Services, the units were installed on line earlier
than anticipated. During the upgrade, GE acted on customer feedback and implemented several
product enhancements, including intuitive labeling of the water inlet and outlet valves at each
bridge, and extra terminal blocks to facilitate field wiring.
BENEFITS
• New Technology Improves Performance – Stator water system cooling insures full rating
without the risk of problems associated with air cooled offerings, such as heat sink fouling,
plugged filters and fan failures.
• Smooth Project and Quick Turn-around – Flexibility and commitment to work with customers
and third-party vendors ensures projects are completed on time, and to specification.
• Responsiveness Adds Value – Acting on customers’ feedback yields product enhancements.
Copyright © 2010 General Electric Company, all rights reserved.
GEA17992 (02/10)
www.ge-energy.com/ocsuccess