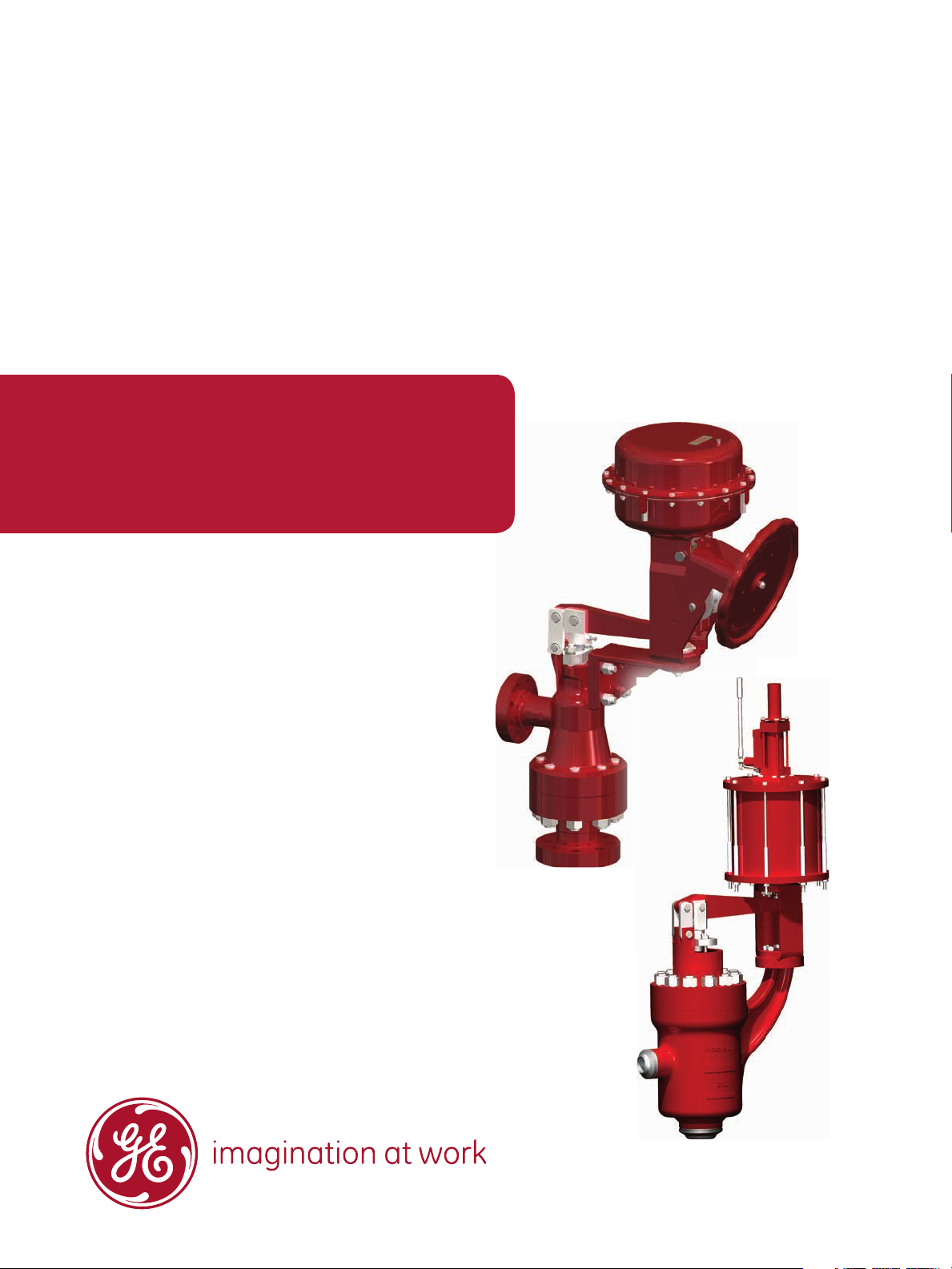
GE Oil & Gas
Masoneilan
*
77000 Series
High Pressure Labyrinth Trim Control Valves
Integrated Smart Engineered
Best Fit Solutions
• Engineering Expertise
• Leading Technology
• Longer Service Life
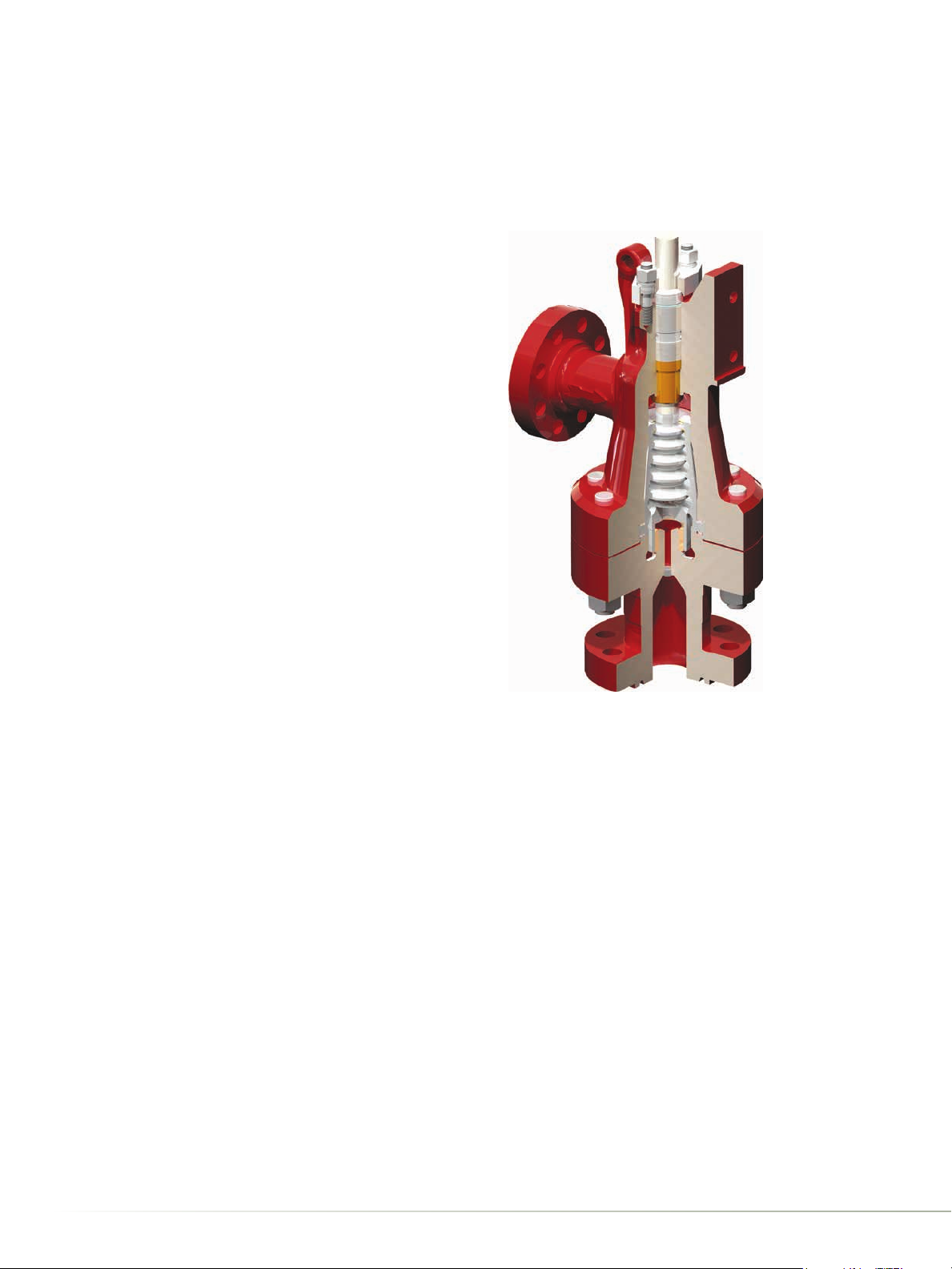
77000 Series: High-Pressure
Labyrinth Trim Control Valve
GE’s Masoneilan 77000 Series axial flow, labyrinth trim control
valve combines decades of engineering expertise with leading
technology and in-depth customer application knowledge.
With a multi-stage, expanding area flow passage, the 77000
Series valve is designed to effectively handle difficult pressure
reduction applications while managing noise and vibration
levels that can otherwise severely damage equipment. The
result is smoother process flow and longer service life, which
not only saves time and money, but also mitigates risks in
demanding and crucial applications.
Used across a wide range of process applications, the 77000
Series controls high-pressure compressible fluids without
the erosion, vibration and high noise levels associated with
conventionally designed control valves. The 77000 Series is
also particularly well-suited for service applications involving
two-phase flow for either gas with entrained liquids/solids
or liquids with entrained solids. From upstream oil and gas
production to downstream refining and petrochemical
processing to some of the most severe steam applications in
power generation, the 77000 Series valve stands up to intense
temperatures and high pressures.
Customer Benefits
• Cost savings
• Improved process control
• Increased uptime
• Longer service life
• Maintenance simplicity
• Risk mitigation
Industries and Applications
UPSTREAM OIL AND GAS
High pressure, erosive-choke applications
Steam injection for tar sand oil extraction
DOWNSTREAM OIL AND GAS:
Refining and Petrochemical
High-pressure process control applications
Hot, high pressure separation
Delayed coker letdown
PTA crystallizer blow down
POWER GENERATION
Superheater bypass
Boiler blowdown
2 | GE Oil & Gas
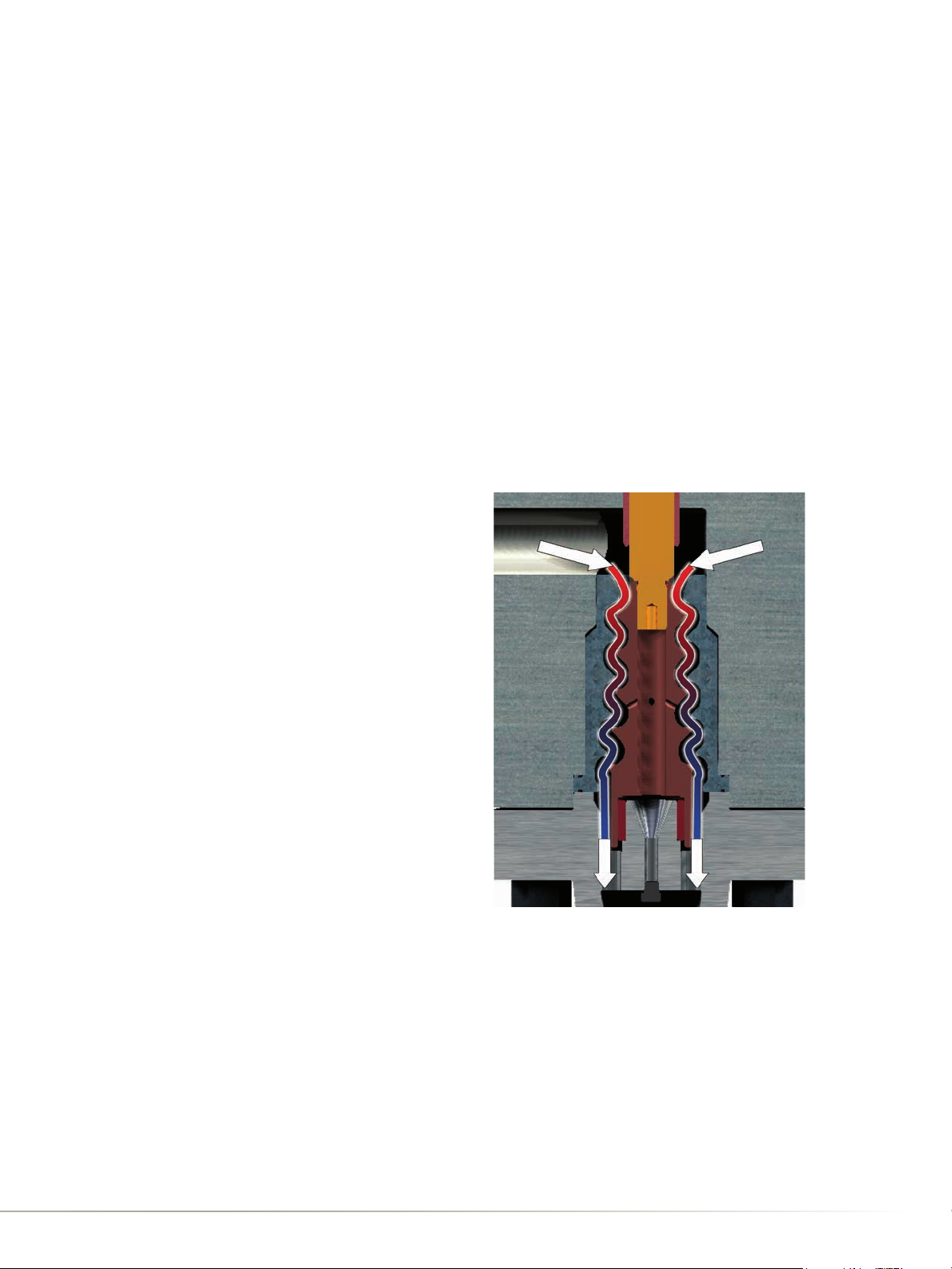
Proven Control
Through Advanced Design
Multi-Stage, Expanding Area
Pressure Reduction
Using proven principles of energy management technology,
the 77000 Series gradually reduces fluid pressure, yielding
dramatically reduced noise and vibration. The product features
a multi-stage trim design that creates flow path friction to
simulate the gradual pressure loss that occurs over long
pipelines. This effect is produced by passing the fluid through a
tortuous flow pattern with multiple restrictions, referred to as
pressure reduction stages. Consequently, energy is dissipated
through high head loss without undesirable shock waves.
By reducing fluid velocity throughout the throttling process, the
77000 Series’ advanced design eliminates the damaging erosive
effects caused by high kinetic energy spikes and vibration.
The unique flow area of the 77000 Series trim gradually
increases at successive trim stages and offers an enlarged
outlet connection. The expanded flow areas are designed
to compensate for the change in gas density resulting from
pressure reduction, thus making the 77000 Series well-suited
for high-pressure-drop off-gassing applications. With more
than 30 years of installed experience, the Masoneilan 77000
Series has performed successfully in some of the most extreme
high-pressure-drop environments. The 77000 Series’ advanced
design results in minimized fluid velocity, which reduces erosion
damage to the trim and downstream process equipment,
particularly in applications—such as wellhead chokes in the oil
and gas industry—that include particulate in the flow stream.
Additionally, the 77000 Series’ low velocity outlet area minimizes
phase transformation process effects. That is an advantage for
many applications that experience flashing or hydrate service
conditions, such as startup valves in supercritical power plants,
hot high-pressure separator letdown valves in refineries, and
gas injection valves in gas extraction plants.
77000 Series - Axial Flow Labyrinth Trim Control Valves | 3
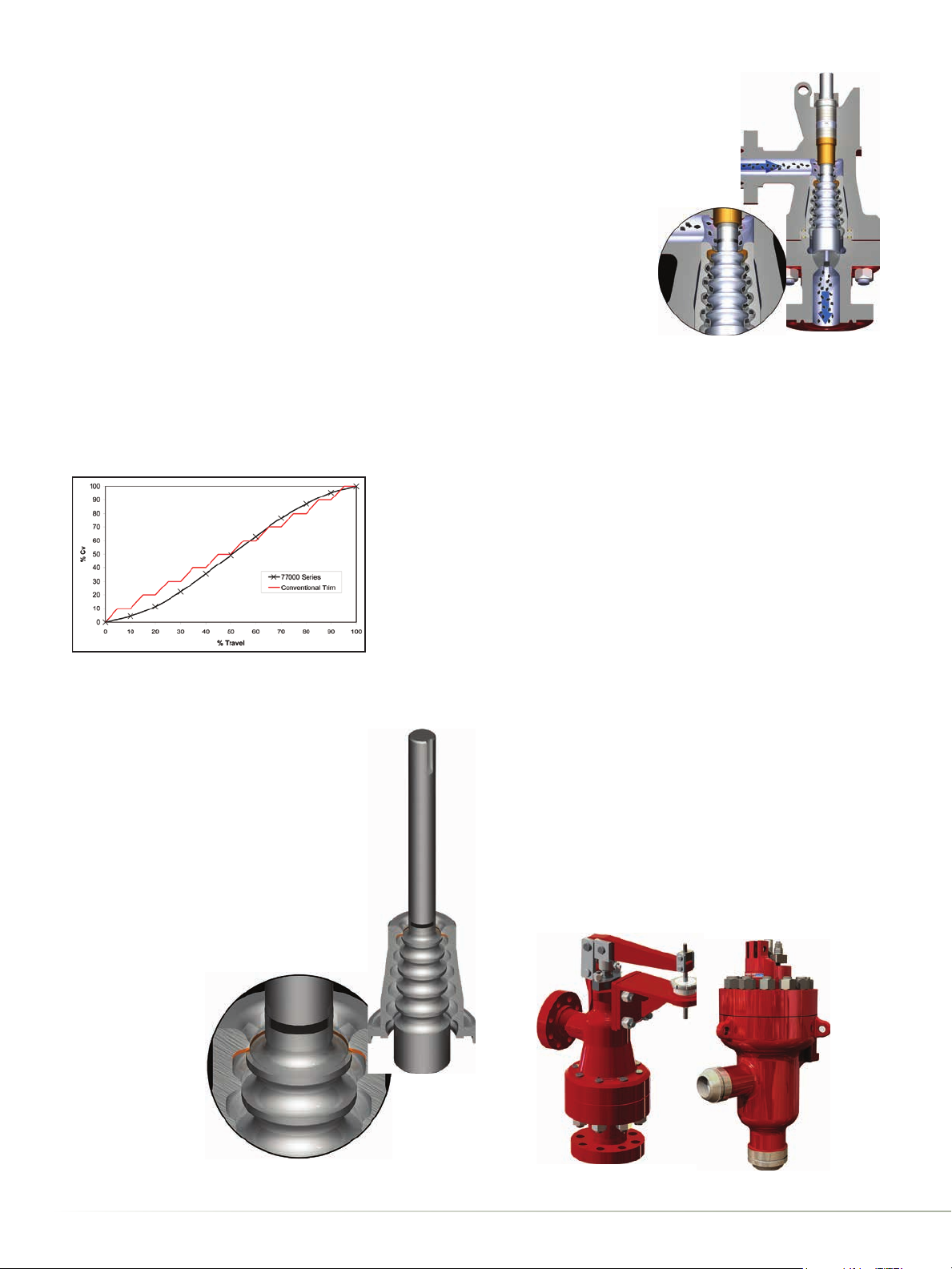
Engineered Features
Axial Flow, Unison Throttling
The 77000 Series design separates itself from more conventional
pressure-reducing valves by nature of its multi-stage axial flow
path design. Unlike radial flow path designs, the 77000 Series
throttles the fluid across successively larger stages along the axis
of the valve plug. With up to nine separate stages, the control
valve positions each stage so that they all operate in unison as
the plug strokes, ensuring that the fluid energy is managed in a
controlled manner to avoid cavitation. This design concept avoids
the stair-step performance that can characterize many radial
flow path designs. No single stage or radial flow path trim can
match the performance of the 77000 Series.
Travel vs C
v
Tight Shutoff, Upstream Seat,
Durable Trim Design
Unbalanced,
Flow-to-Open
Design
The 77000 Series employs
a simple unbalanced plug
design that eliminates any
secondary leak paths that
could compromise shutoff integrity. The resulting high-actuator
loads are managed by using an offset actuator where loading
forces are multiplied by the actuator lever arm. The flow-toopen trim orientation can be useful for applications where
service conditions warrant a reliable failure mode.
Trash-Tolerant, Robust Design
The 77000 Series provides large flow paths that allow for
the passage of flow-entrained particulate, which can clog
conventional drilled-hole or stacked-disk trim. The smooth axial
flow path allows particulate to move through the valve without
navigating complex trim geometry. This prevents plugging
and galling of the trim, which can lead to loss of capacity or
premature valve failure. The 77000 Series has a proven track
record in many high-pressure, dirty-service applications where
a robust valve design delivers essential reliability.
Seat protection in a high-pressure valve
design is critical to prevent premature seat
wear leading to unwanted and undetected
leakage. A damaged valve seat can lead to wire
drawing and eventually to rapid trim damage
from cavitation or flashing when the valve is in
the closed position. Seat damage effects are
minimized in the 77000 Series by locating the
seat on the upstream section of the trim. This
design feature ensures that the seat is isolated
from the most severe and potentially damaging
pressure-reduction
stages, which
are located in the
downstream section
of the trim.
Flexible Platform, Ease-of-Maintenance
The 77000 Series design comes in two styles for easy trim access
in the field. A bottom-loaded, flanged-end connection is ideal
for process plants, while a top-loaded, butt-weld end design
works well in high- pressure power applications. Both styles offer
flex- ibility and simple field maintenance for reduced service
complexity and cost.
4 | GE Oil & Gas