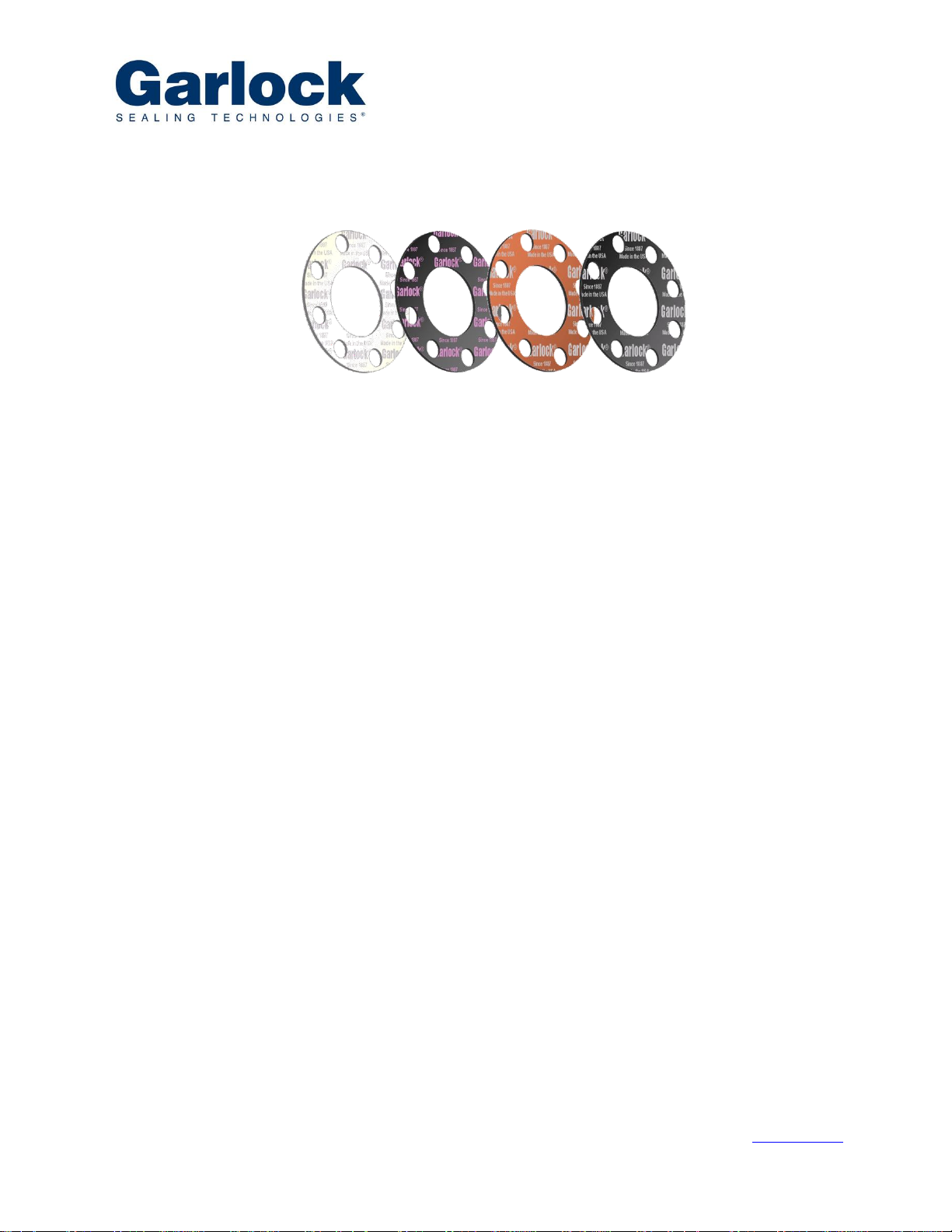
Installation Guide for Garlock Premium Grade
Elastomeric (Rubber) Gaskets
Factors Affecting Gasket Performance
A gasket has one basic function: to create a positive seal between two relatively stationary
parts. The gasket must do several different jobs well to function properly - first, create an
initial seal; second, maintain the seal over a desired length of time; third, be easily removed
and replaced. Varying degrees of success are dependent on how well the gasket does the
following:
1. Seals system fluid.
2. Chemically resists the system fluid to prevent serious impairment of its physical
properties.
3. Deforms enough to flow into the imperfections on the gasket seating surfaces to provide
intimate contact between the gasket and the sealing surfaces.
4. Withstands system temperatures without serious impairments of its performance
properties.
5. Is resilient and creep resistant enough to maintain an adequate portion of the applied
load.
6. Has enough strength to resist crushing under the applied load and maintain its integrity
when being handled and installed.
7. Does not contaminate the system fluid.
8. Does not promote corrosion of the gasket seating surfaces.
9. Is easily and cleanly removable at the time of replacement.
During the gasket selection process that follows, we recommend that these nine (9) factors
be used as a checklist from the viewpoint of the user's degree of need for each factor and
the manufacturer's degree of compliance.
1666 Division Street • Palmyra, New York 14522 USA • 1-315-597-4811 • Toll Free:1-800-448-6688 • Fax:1-315-597-3216 • www.garlock.com
An EnPro Industries Company
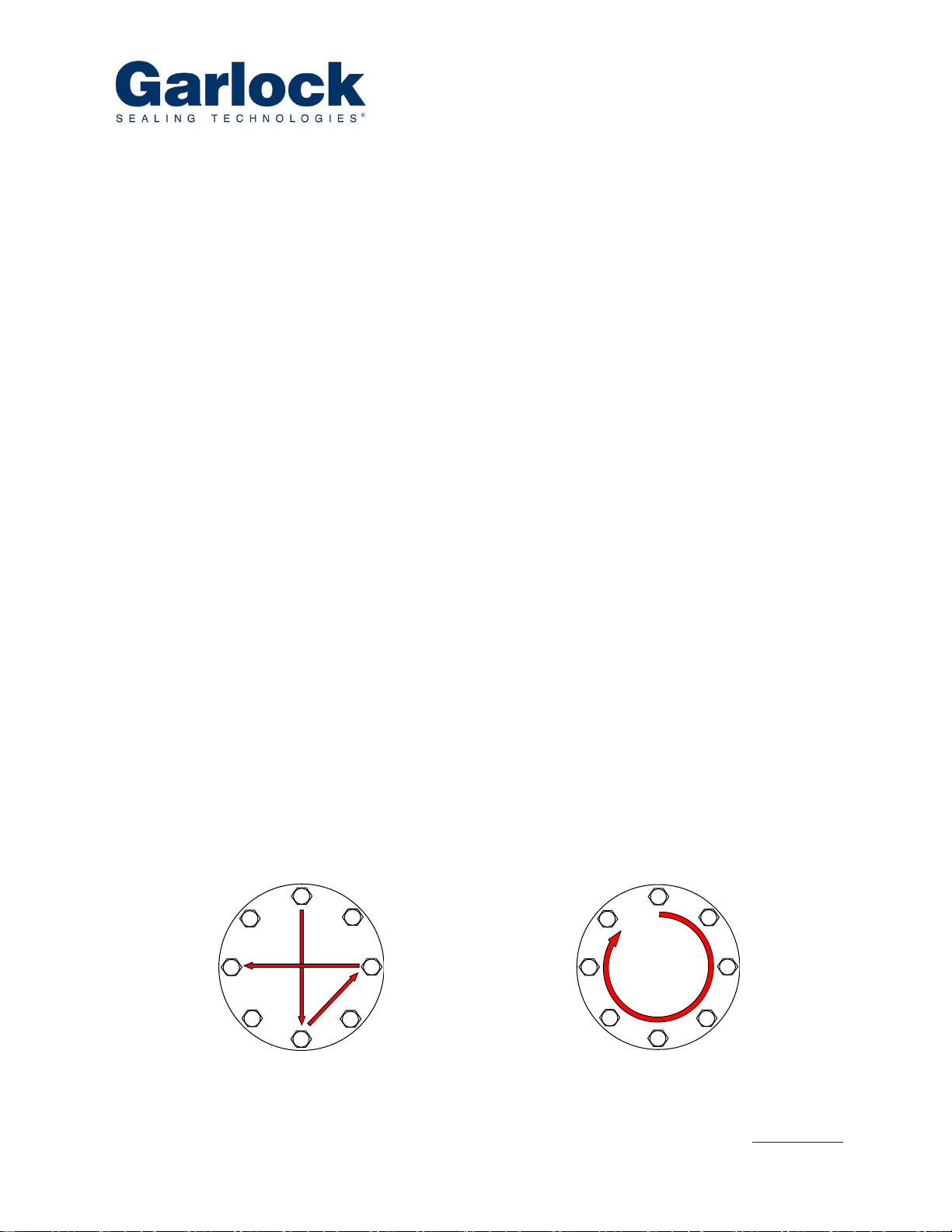
1666 Division Street • Palmyra, New York 14522 USA • 1-315-597-4811 • Toll Free:1-800-448-6688 • Fax:1-315-597-3216 • www.garlock.com
An EnPro Industries Company
Elastomeric (Rubber) Gasket Installation
A few simple precautionary measures must be observed during installation to ensure the
most satisfactory joint.
A few simple steps must be followed during installation to ensure optimum performance:
1. Verify the flange faces are clean, free of debris/fluids, and in good working condition (flat,
aligned, no major defects, etc.).
2. Bolts/studs and nuts should be in good working order (ideally new) and turn together
freely.
3. Bolt/stud threads should be lubricated with a good quality thread lubricant and installed
with at least one hardened flat washer under each nut being turned to reduce friction and
optimize load translation.
4. Finger-tighten and lightly snug all bolts/studs and nuts using a crossing pattern (see
Figure 1) prior to beginning the torqueing process.
5. Using a calibrated torque wrench, tighten the nuts in multiple steps using a crossing
pattern (see Figure 1) to evenly compress the gasket.
6. Once the final torque is achieved make a final pass at the final torque moving
consecutively from bolt to bolt (see Figure 2).
7. Retorque 12-24 hours after initial installation when possible (see Figure 2). For safety
reasons, Garlock does not recommend retightening a flange connection once it is
brought up to temperature and/or pressure. All applicable safety standards including
lockout/tagout procedures should be observed.
• NOTE: Never use liquid or metallic based anti-stick or lubricating compounds on the
gaskets. Premature failure could occur as a result.
Correct Bolting Pattern
Figure 1 – Crossing Pattern
Figure 2 – Final Pass / Retorque