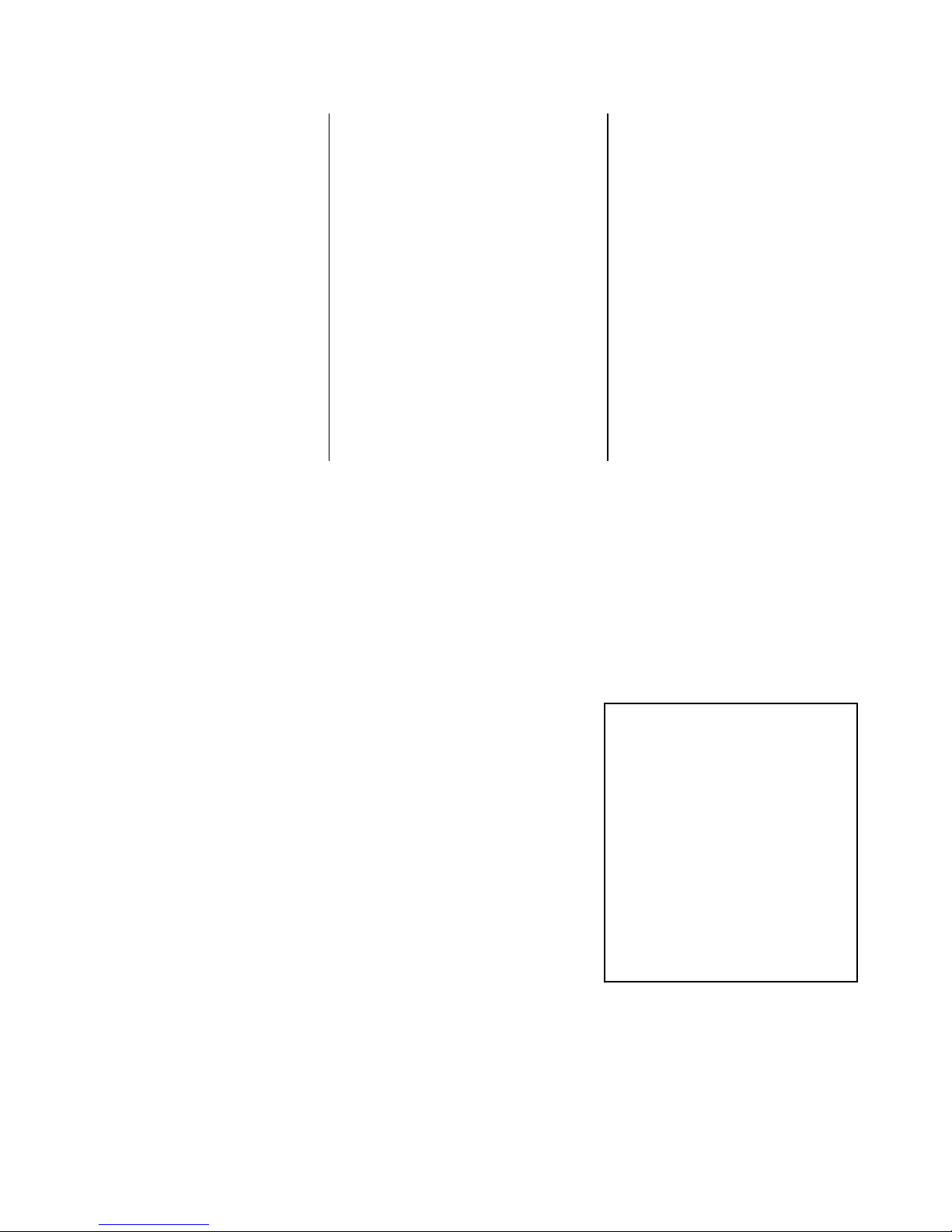
If you have questions concerning the
information in the manual,
replacement parts, or the operation of
the vendor, note your machine’s
Model and Serial Numbers before
contacting:
VendNet
165 North 10th Street
Waukee, Iowa 50263 - USA
Parts: (888) 259-9965
Service: (800) 833-4411
Parts Fax: 515-987-4447
All Other: (888) 836-3638
E-Mail: Vendnet@vendnetusa.com
TABLE OF CONTENTS
INTRODUCTION .............................. 2
SPECIFICATIONS ............................. 3
VENDOR SET UP ............................. 4
UNPACKING ................................................... 4
INSTALLATION ................................................ 4
GROUNDING (EARTHING) & ELECTRICAL ........ 4
COMPONENT LOCATION ................................ 5
REFRIGERATION OPERATION ......................... 6
CARD READER ACCESS .................................... 6
LOADING SNACK PRODUCTS .......................... 7
SPIRAL AND TRAY ADJUSTMENT .................... 7
SPIRAL TIMING ............................................... 7
PRODUCT PUSHERS ........................................ 7
LOADING BEVERAGE PRODUCTS .................... 8
LOADING COIN MECHANISM.......................... 9
BILL VALIDATOR OPERATION (OPTIONAL) ...... 9
SALES MODE .................................. 9
DISPLAY CREDIT - ELECTRONIC PRICING ......... 9
"USE EXACT CHANGE" LED OPERATION .......... 9
The Model and Serial numbers are needed for you to obtain quick service and parts information for your vendor. The numbers are given on
the identification plate located on the back of the vendor. Write them into the spaces below for your records.
"MAKE ANOTHER SELECTION" LED
OPERATION .................................................... 9
VEND CYCLE ................................................. 10
CHANGE RETURN ......................................... 10
DEX CAPABILITY (OPTION) ........... 10
BEVERAGE AREA OPERATION ....... 11
SOLD OUT VEND SEQUENCE ......................... 11
SERVICE MODE ............................. 12
SERVICE MODE BUTTTON ............................. 12
KEYPAD OPERATION ..................................... 12
PROGRAMMING .......................... 12
TUBE FILL AND DISPENSE COINS MODES ..... 12
MOTOR COUNT MODE ................................. 13
OPTIONS MENU ........................................... 13
FORCE VEND OPTION ................................. 13
BILL ESCROW OPTION ................................ 13
MULTI VEND OPTION ................................. 14
FREE VEND OPTION .................................... 14
FAST CHANGE ............................................. 14
OPTICS OPTION .......................................... 15
POS MESSAGE............................................. 15
TEMPERATURE SETPOINT ........................... 15
CONFIGURATION MENU .............................. 16
VENDOR CONFIGURATION ......................... 16
VENDOR SPACE-TO-SALES .......................... 16
PRICING ........................................................ 17
PRICE ALL SELECTIONS ................................ 17
PRICE BY ROW / TRAY ................................. 17
PRICE BY SELECTION ................................... 17
SET COUPON VALUE ................................... 18
SET TOKEN VALUE ...................................... 18
ACCOUNTING MODE .................................... 19
ADVANCED OPTIONS .................................... 21
TEST VEND SELECTION MODE ...................... 21
TEST VEND ALL SELECTIONS MODE .............. 21
DIAGNOSTICS MODE .................................... 22
PREVENTATIVE MAINTENANCE...... 25
PARTS ORDERING PROCEDURE ...... 25
BEFORE CALLING FOR SERVICE ...... 25
MODEL NUMBER: _______________
SERIAL NUMBER: _______________
INTRODUCTION
This manual contains instructions, service and installation guidelines for the Futura Combo
Vendor. The Futura Combo Vendor is designed as a combination snack and beverage
merchandiser. The vendor is capable of dispensing a wide variety of snacks and beverages.
The Futura Combo Vendor is equipped with an electronic control system. All vending
functions, pricing, and features are programmed through the controller. Changes can be
made without any additional accessories or remote parts.
Selections can be priced individually from $.05 to $99.95 in five cent increments (US
currency).
Accountability mode records Total Cash and Credit transactions and Total Vend cycles
performed by the vendor. Information for individual selections, complete rows or total vendor
can be compiled and used for inventory and ordering records.
Control System malfunctions are recorded and displayed when the vendor is placed in
Service Mode. Non-functioning motors or selections are indicated. Each selection has an
individual motor. When one selection motor fails the other selections are unaffected and will
continue working.
The vending sequence is “first-in, first-out” for each selection, eliminating the need for stock
rotation to ensure product freshness.
Read this manual thoroughly. Become familiar with the vendor’s components and features. The initial setup of a vendor is a very important
step towards insuring that the equipment operates trouble-free. Carefully follow the instructions for the initial installation of the vendor to avoid
service problems and minimize setup time.
Access to the service area of this vendor should be permitted only to individuals having knowledge and practical experience in vendor setup
and loading, especially in areas of safety and hygiene.
2 4223074.001 F u t ura Service Manua l R E V A

551 lbs. (254kg) / 600 lbs. (272kg)
Snack Window Size
(tempered glass only)
22 17/32" X 25 1/4" X 1/8" Thick
(626mm X 641mm X 3mm)
Live Display Window Size
(tempered glass only)
9 1/4" X 25 1/4" X 1/8" Thick
(235mm X 641mm X 3mm)
Standard Capacity (may vary)
Live Display Can Selections
Live Display Bottle Selections
Total Beverage Capacity (may vary)
Industry Standard MDB
Coin Mechanisms, Bill Validators and Card
Readers
(OPTIONALLY EQUIPPED)
Suitable for indoor use only. This appliance is not suitable
for installation in an area where a water jet could be used.
Produces less than 70 dBA during normal operation.
Recommended
Operating
Temperature
Between 32° and 100° F° (0° and 37.8° Celsius)
SPECIFICATIONS
DIMENSIONS
STANDARD SNACK TRAY CONFIGURATION (MAY VARY)
STANDARD BEVERAGE TRAY CONFIGURATION (MAY VARY)
ELECTRICAL
COINAGE (NOTE: DOLLAR BILL VALIDATOR AND/OR CARD READER IS OPTIONAL)
VENDOR OPERATION
3 4223074.001 F u t ura Service Manua l R E V A

VENDOR SET UP
NOTE: If the power supply cord is damaged, it must be replaced by the manufacturer, its service agent, or similarly
qualified individual in order to avoid hazard.
NOTICE: The vendor must be level and there must be a minimum of 4” between the back of the vendor and the wall
for proper air flow.
UNPACKING
This vendor was thoroughly inspected before leaving the factory and the delivering carrier has accepted responsibility for this vendor. Note
any damage or irregularities at the time of delivery and report them to the carrier. Request a written inspection report from the claims
inspector to file any claim for damage. File the claim with the carrier (not the manufacturer) within 15 days after receipt of the vendor.
CAREFULLY REMOVE THE OUTSIDE PACKING MATERIAL BEING CAREFUL NOT TO DAMAGE THE
VENDOR’S FINISH OR EXTERIOR. INSPECT THE VENDOR FOR CONCEALED SHIPPING DAMAGE.
REPORT ANY DAMAGE HIDDEN BY THE SHIPPING MATERIAL DIRECTLY TO THE DELIVERING
CARRIER ON A HIDDEN DAMAGE REPORT.
INSTALLATION
Position the vendor in its place of operation. Make sure to level the vendor by placing a bubble level on the top of the machine and adjusting
the vendor leg levelers. Position the vendor so the power cord easily reaches the power outlet or receptacle (DO NOT USE AN EXTENSION
CORD). Check that the door will open fully without interference.
Retrieve the vendor keys from the coin return cup. Open outer door and remove all internal packing material.
GROUNDING (EARTHING) & ELECTRICAL
NOTE: SEE SAFETY MANUAL
Consult local, state, and federal codes and regulations before installing the vendor.
Refer to the Safety Installation Guidelines document found in the service package
shipped with your vendor.
Before connecting the vendor, the integrity of the main electrical supply must be
checked for correct polarity, presence of ground (earth) and correct voltage. These
checks should be repeated at six-month intervals with the routine safety electrical
testing of the vendor itself.
If the receptacle is not properly grounded or polarized, contact a licensed electrician to
correctly polarize and/or ground the receptacle to ensure safe operation.
For proper operation of any equipment utilizing electronically controlled components,
the equipment should be placed on an isolated, or dedicated, noise-free circuit
properly polarized and grounded. Use of a surge suppressor is recommended for
locations where electrical noise is present.
After all set up has been completed turn on the Power Switch (see Component
Locations diagram later in manual).
4 4223074.001 F u t ura Service Manua l R E V A

REFRIGERATION OPERATION
NOTICE: There must be a minimum of 4” between the back of the vendor and the wall for proper air flow.
NOTICE: DO NOT MAKE LARGE ADJUSTMENTS TO THE FACTORY TEMPERATURE SETTING. DOING SO MAY
RESULT IN A FREEZ UP OF THE EVAPORATOR COIL AND/OR BEVERAGES. PROLONGED FREEZE UPS WILL
CAUSE THE REFRIGERATION TO OVERHEAT AND MAY CAUSE PERMANENT DAMAGE TO THE SYSTEM.
CLEAN SCREEN UNDER CABINET MONTHLY
The Vendor's refrigeration system will operate trouble-free for many years and with highest
efficiency with proper operation and maintenance. It is critical that the machine be positioned with
a minimum of a 4" space between the back of the machine and the wall. Also, it is critical that the
bottom screen and refrigeration compartment be kept clean. Clean/vacuum the screen under the
cabinet monthly.
CARD READER ACCESS
Please follow below steps to access the Card Reader.
1. Turn OFF power to the machine and then unplug the coin mech harness.
2. Remove coin chute by unscrewing 2 X #6-20 screws. (This step is required to access #8 nuts for next step). See FIG. 1
3. Keeping the coin mech on coin mech mount bracket, unscrew 2 X #8-32 nuts at the top and 2 X #8 screws at the bottom of coin
mech mount bracket. See FIG 2 & 3.
4. Remove coin mech mount bracket to access the Card Reader. See FIG. 4
6 4223074.001 F u t ura Service Manua l R E V A

ADJUST SPIRAL END POSITION BY PINCHING
SNAP TABS OF SPIRAL COUPLING ON BACK
OF MOTOR - PULL OUT OF MOTOR THEN
SNAP BACK INTO DESIRED POSITION
IF AFTER ADJUSTING THE SPIRAL END THE
PRODUCT STILL DOESN'T FALL OFF TRAY … SNAP
PROVIDED PRODUCT PUSHERS ONTO END OF
SPIRALS TO ENSURE PRODUCT WILL FALL
ADJUST SPIRAL END POSITION FOR SUCCESFUL VEND.
MOST PRODUCTS VEND PROPERLY AT THE
6:00 (0'CLOCK) SETTING
SHOWN ABOVE
ADJUST SPIRAL
COUNTER
CLOCKWISE FOR
THICKER PRODUCTS
(i.e. 3:00 (0'CLOCK))
ADJUST SPIRAL
CLOCKWISE FOR
THINNER PRODUCTS
(i.e. 7:00 (0'CLOCK))
LOADING SNACK PRODUCTS
Lift the tray up slightly and pull forward until the tray stops then tilt down for ease of loading.
Load product from front to back making sure all items fit freely between the spirals. Do not attempt to force oversized products or packages
into the spaces. Do not skip a space. Place the product on the bottom of the compartment on the spirals with the labels facing the front of the
vendor for easy identification by the customer.
To vend properly the product must be wider and taller than the diameter of the spiral being used. Undersized products may cause vend
problems.
SPIRAL AND TRAY ADJUSTMENT
The shape, size and thickness of a product affect how well it falls off the tray. Most products can be vended successfully when the spiral end
is positioned at 6 o’clock. If vending problems occur with spiral ends at the standard 6 o’clock position, adjust the drop-off either by retiming
the spiral or installing a Product Pusher.
SPIRAL TIMING
Each spiral can be rotated in 45º (degree) increments for
a different drop-off point. Most products can be vended
successfully when the spiral end is positioned at the
position of 6 o’clock.
The general rule is:
The narrower the product, the higher the timing.
Thick Products - 4-6 o’clock
Most products – 6 o’clock
Thin Products - 6-8 o’clock
To change the spiral end position:
1. Remove the tray to have access to the back of the motors.
2. Pinch the snap tabs of the spiral coupling and push out until it separates from the motor.
3. Rotate the spiral to the desired position and reinsert the spiral coupling into the motor.
4. Make sure the spiral coupling snaps fully into the motor as shown.
5. Replace the tray and test vend the selection to make sure product vends correctly.
PRODUCT PUSHERS
If the product still will not vend properly after re-timing of the spiral then install a Product Pusher. The Product Pushers are provided in the
service package of the vendor. Snap onto spirals only as necessary as shown.
7 4223074.001 F u t ura Service Manua l R E V A

PUSH IN ON TRAY LATCHES ON BOTH
SIDES AND PULL OUT TO LOAD
IMPORTANT:
LOAD BOTTLED PRODUCTS
CAP DOWN AND
TILTED BACK AS SHOWN
Pre-Cool Area
For 12 oz. Cans
LOAD CANS HORIZONTALLY
AS SHOWN WITH CAN TOP
ORIENTED TO RIGHT
(HINGE) SIDE
LOADING BEVERAGE PRODUCTS
Push in on latches simultaneously on both sides of trays then pull forward until the tray stops to load.
Load product from front to back making sure all items fit freely between the spirals. Do not attempt to force oversized products into the
spaces. Do not skip a space. Place the product on the bottom of the compartment on the spirals.
To vend properly the product must be wider and taller than the diameter of the spiral being used. Undersized products may cause vend
problems.
Load bottle products cap down in bottle trays as shown. Load cans horizontally. See page 11 to identify which selections are 16 oz. only and
which selections are 12 oz. only
8 4223074.001 F u t ura Service Manua l R E V A

PRESS SERVICE
MODE BUTTON
AND ENTER
TUBE FILL
MODE (PRESS 1)
LOADING COIN MECHANISM
INSERT COINS THROUGH
FRONT DOOR COIN INSERT
TO FILL COIN TUBES
NOTE: When using the Bill Validator, having the coin tubes full will provide the best bill acceptance operation.
The Coin Mechanism must be loaded with a minimum of one roll each
of nickels, dimes and quarters in order for the vendor to operate
properly. The coins need to be loaded into the coin mechanism by
inserting them into the front coin insert. First enter the SERVICE
MODE then enter the TUBE FILL MODE (See SERVICE MODE
instructions, pg.12).
Each tube should be kept loaded with at least one roll of coins. This
will ensure the coins are above the tube low level sensors. Once the
tubes are loaded the Dollar Bill Validator (if equipped) will accept bills.
If one or more of the coin tubes fall below the low level sensor the
Dollar Bill Validator may stop accepting bills and the front display will
light the "EXACT CHANGE ONLY" indicator LED.
Alternatively, you can load the coins into the slots above the respective
coin tubes. This is not the preferred method. By using TUBE FILL mode
the control board can then accurately determine coin levels.
On some Coin Mechanisms there are buttons above each tube to dispense the coins (may vary
depending on which coin mechanism that is used). The coins can also be dispensed within the Service
Mode described later.
More advanced and brand specific Coin Mechanism operating instructions can be obtained on the
Service portion of the website listed at the beginning and end of this manual
BILL VALIDATOR OPERATION (OPTIONAL)
To remove the bills from the Dollar Bill Validator push the tab on the top of the bill box and lift up. To clear jams or cleaning unlatch lower unit
as shown. Dollar Bill Validator cleaning instructions as well as more advanced service information can be obtained on the Service portion of
the website listed at the beginning and end of this manual.
SALES MODE
The vendor automatically defaults to Sales Mode after it is turned on. In the Sales Mode, the vendor accepts money deposits, pays out
change and dispenses product to the customer.
DISPLAY CREDIT - ELECTRONIC PRICING
This vendor is equipped with the Electronic Pricing feature. The customer verifies the price by pressing the selection number (i.e. 22) before
inserting money. If a selection is made and credit has not been established, the price for that selection is displayed and will flash. When
money or credit is accepted, then the amount of credit is displayed.
"USE EXACT CHANGE" LED OPERATION
If the coin levels in the coin mechanism tubes are below the low-level sensors, the indicator LED next to “USE EXACT CHANGE” will
illuminate. This indicates the Coin Mechanism does not have enough coins in the coin mech tubes to make change. This also indicates that
the Dollar Bill Validator may be disabled until change can be made.
"MAKE ANOTHER SELECTION" LED OPERATION
If a selection is made that is not available (i.e. 79 is not a good selection) or if there is a selection motor failure the indicator LED next to
“MAKE ANOTHER SELECTION” will illuminate. If this is a motor failure the controller will display which motor has failed upon entering the
Service Mode (described later in this manual).
9 4223074.001 F u t ura Service Manua l R E V A