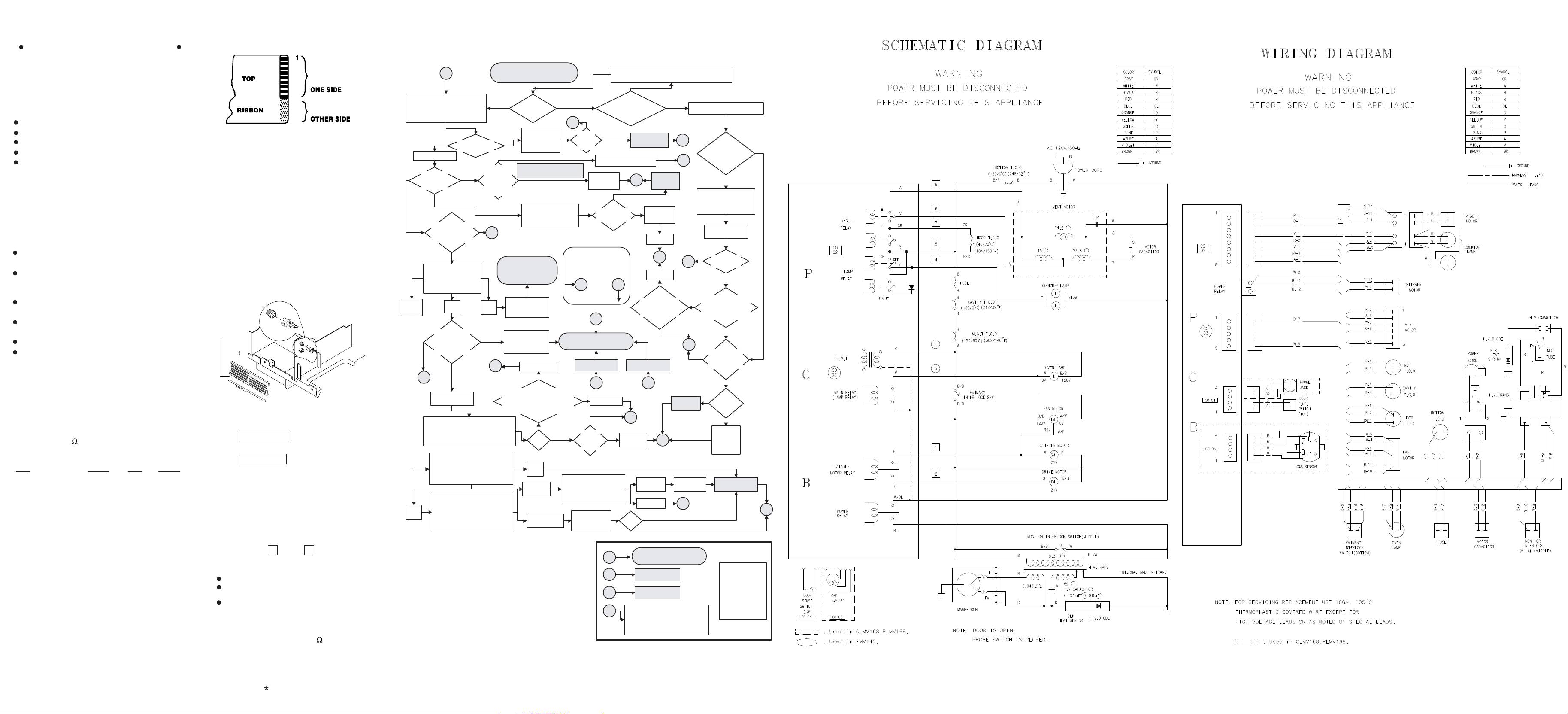
TECHNICAL DATA SHEET
MWO TROUBLESHOOTING FLOW CHART
SMART BOARD
The SMART BOARD contains the power relay,
LVT, vent blower triac, surface light relays, and
other components to perform the proper
switching circuits. Several disconnect plugs are
also located on the SMART BOARD:
CON 01 - Ribbon Connector
CON 02 - Vent Blower Connector
CON 03 - Primary L.V.T & Main Relay
CON 04 - Door Sensing & Probe Connector
CON 05 - Gas Sensor Connector
(PLMV168, GLMV168)
Many diagnostic circuit tests can be made at the
disconnect plugs. (Refer to diagnosis flow chart
and simplified schematic in mini-manuals.)
CONTROL PERFORMANCE TEST
Set Clock-Touch clock pad, enter time of day,
AM/PM touch start pad.
Alternately touch each function pad and enter
time or temperature selection for the function.
Also change power levels.
Touch Clear-Off after each function test to
clear that function.
Repeat procedure for each function to
exercise each pad.
Control and display should respond to each entry.
Display should revert to Time-Of-Day after each
Clear-Off. Refer results to Diagnostic Flow Chart.
KEY PANEL TEST
If necessary the key panel pads can be verified
by a continuity test. For ease of handling the key
panel should be removed and placed on a flat
surface.
Check continity between connections at end of
ribbon (Use high scale).
RIBBON
PAD CONN. PAD CONN.
ADD 30SEC 4-11 REHEAT 8-11
BEVERAGE 9-11
POWER LEVEL 3-14 TIMER 4-13
DEFROST START 3-11
4-15
BEEPER VOLUME 9-12
AUTO NITE LIGHT 6-12 POTATO 6-10
AM/PM 9-13 1 9-16
SURFACE LIGHT
7-12 2 8-16
VENT FAN 8-12 3 7-16
TURNTABLE 5-12 4 6-16
REMINDER 5-13 5 5-16
TIME COOK 5-15 6 4-16
DELAY START 6-13 7 9-15
CLEAR 3-12 8 8-15
POPCORN 7-11
TEMPCOOK/ROAST 3-15
GROUND MEATS 3-10
VEGETABLE 9-10
- FMV145 -
BEVERAGE 6-11
REHEAT 9-11
POPCORN 5-11
PUB. NO. 31-40015
CLOCK 7-13
HELP 4-12
9 7-15
0 6-15
1~9
9
10
10~16
16
ERROR MESSAGE
Display Signal
• F1 Open thermal sensor(convection)
• F2
• F3
Shorted thermal sensor(convection)
Keypanel shorted for > 60seconds
• F4 Open humidity sensor
• F5
Shorted humidity sensor
* Error sound will beep for 3 cycles (2 second on,
1 second off) loudey in upper condition.
SENSOR COOKING
The Sensor Cooking function uses a special gas
sensor which detects both humidty (steam) and
hydrocarbons (food odors) during the cooking
process, The sensor is a plug-in device located in
the vent area at the top left hand corner of the
cavity behind the grille.
Bracket Barrier
SENSOR COOKING TEST
1. Place 1/3 cup tap water in oven.
2. Touch
3. Control Beeps and shuts off.
4. Touch
VEGETABLE
CLEAR/OFF
A) Test OK - Normal
B) Test Fails - Check Sensor
C) Test Fails - See Sensor Test Below
Condition
(PLMV168, GLMV168)
(PLMV168, GLMV168)
, the oven starts immediately.
SENSOR TEST (QUICK TEST)
(PLMV168, GLMV168)
1. With 2 fingers touch and hold the following
pads at the same time:
and
87
2. Observe diagnostic number in display
(numbers approximate)
15-185 (Normal-verify with "detection test")
213 or Higher (sensor failed to open, sensor
unplugged, wiring or smart board)
Less than 6 (shorted sensor, or smart board).
NOTE:
Only heater terminals (H : Black
and Red leads) can be checked
with ohmmeter (30 ).
CAUTION :
DO NOT ATTEMPT TO CHECK
SENSOR TERMINALS(White
and Orange leads).
CAN DAMAGE SENSOR.
D
1. SET CLOCK (IF NEEDED)
2. PLACE CUP OF WATER AND
NEON LIGHT TESTER IN UNIT
3. PROGRAM UNIT TO COOK
YES
UNIT ABLE TO
PRESS START
SERVICE
BREAKER
TRIPS?
NO
WATER HEATS /
NEON TESTER
INSTALL CLAMP ON
AMMETER TO MWO's
INTERNAL FUSE
ABOUT
5A
BLOWER AND
CAVITY LIGHT
NO
B
CHECK VOLTAGE ACROSS POWER
RELAY ON PCB (DOOR CLOSED,
NO COOKING PROGRAMMED) -
CMO ONLY - IF AN OTR, GO TO
INSTALL CLAMP ON AMMETER
1. UNPLUG UNIT
2. DISCHARGE HVC
> 8A
3. SET DVM ON 2K OHM SCALE
4. MEASURE HVD SIDE OF HVC
TO GROUND
PROGRAM?
IMMED
AFTER A
FEW SEC
LIGHTS?
NO
LEAD
< 2A
MAGNETRON
ON?
YES
PRIMARY
SWITCH OK
SHOULD GET ABOUT 120V
"OTR START" BLOCK
TO A MAGNETRON LEAD
OTR START
START - VERIFY MWO POWER
CORD PLUGGED INTO OUTLET
YES
IS DISPLAY
LIT?
NO
MONITOR
DOOR
SWITCH
OK?
A
YES
PROBLEM - CALL TAG
> 8A
CAVITY
LIGHT
ONLY ON
B
YES
PERFORM
KEY PANEL
"*" REFER TO FRONT
PAGE FOR MORE INFO
NO
CHECK RESISTANCE
OF HVC - 2K OHM
INTERMITTENT
TEAM FOR
RESOLUTION
MAGNETRON &
HV COMPTS
ARE GOOD
REPLACE
PRIMARY DOOR
SWITCH
ABOUT 120V
PROGRAM UNIT FOR
COOKING AND START -
CHECK VOLTAGE AT RELAY
INFINITE
(OPEN)
RESISTANCE
SCALE ON DVM
AGAIN
120V?
< 1A
DVM - DIGITAL VOLT METER
HVC - HIGH VOLTAGE CAPACITOR
HVD - HIGH VOLTAGE DIODE
HVT - HIGH VOLTAGE TRANSFORMER
LVT - LOW VOLTAGE TRANSFORMER
TCO
- THERMAL CUT OUT
(TEMPERATURE SENSOR)
PCB - PRINTED CIRCUIT BOARD
TEST
SOME
NO
B
PANEL
CIRCLE NODES:
ARROWS - EXAMPLE:
RETEST & REASSEMBLE -
REPLACE PCB REPLACE HVT
YES
CHECK RESISTANCE
OF SECONDARY SIDE
OF HVT (SINGLE LEAD
REPLACE HVD
& HVC AND
VERIFY OUTLET
VOLTAGE PRESENT
YES
KEY
OK?
FOLLOW THE
A A
NO
HVT IS GROUNDED
REPAIR /
REPLACE
YES
RESISTANCE
< 2K OHMS?
THEN
GO TO
A
END
B
ABOUT 0V
YES
WIRING
TO HVT
RETEST
OK?
TO HVC)
NONO
A
B
C
D
CHECK FUSE/CIRCUIT BREAKER - RESET
BREAKER/REPLACE FUSE IF NEEDED
NO
UNPLUG & DISASSEMBLE
A
C
INSTALL SERVICE
BREAKER ACROSS
YES
D
SERVICE BREAKER
TRIPPED BEFORE
YES
NO
B
YES
IS INTERNAL
MWO 15A/20A
FUSE OK?
NO
FUSE HOLDER
PLUG IN UNIT
IS DISPLAY
PROGRAMMING
FOR COOK?
VOLTAGE AT
LVT ON PCB?
REPLACE
KEY PANEL
REPLACE
A
NO
HVC IS
MISWIRED
REPAIR
REPAIR
ANY SHORTED
OR PINCHED
WIRING?
YES
HVC
A
YES
C
REPLACE
TCO(s)
C
REPAIR
OK?
1. SET CLOCK (IF NEEDED)
2. PLACE CUP OF WATER AND
NEON LIGHT TESTER IN UNIT
3. PROGRAM UNIT TO COOK
A
70 - 150
OHMS
OTHER
NO
YES
RETEST & REASSEMBLE -
END
REPLACE PCB
REPLACE HVT
OPEN
HVT IS OK
C
LIT?
NO
NO
HAVE
NO
CHECK
TCO(s)
CLOSED
CHECK/
REPAIR
TCO
WIRING
REPLACE
MAGNETRON
THIS IS A
LEGEND -
FIND
THESE
ON MAIN
CHART
YES
MODULARITY-OTR-FRIGIDAIRE
MODEL NO. :
PLMV168KC4, GLMV168KB4,
GLMV168KQ4, GLMV168KS4,
FMV145
A
MODULARITY-OTR-FRIGIDAIRE
MODEL NO. :
PLMV168KC4, GLMV168KB4,
GLMV168KQ4, GLMV168KS4,
FMV145
Printed in Malaysia
DE99-00140B
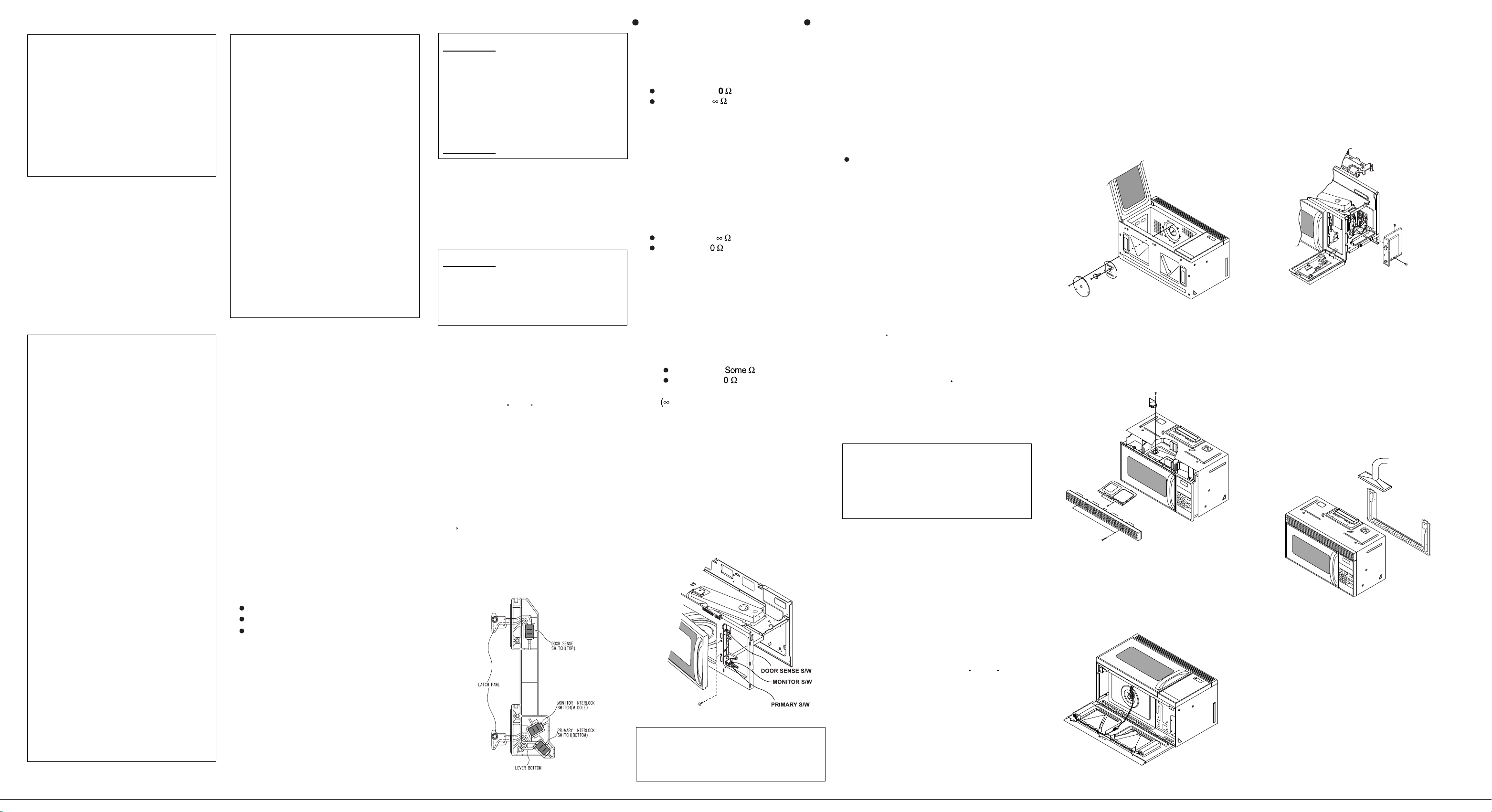
MICROWAVE OVEN HOODS
IMPORTANT SAFETY NOTICE
THIS INFORMATION IS INTENDED FOR USE
BY INDIVIDUALS POSSESSING ADEQUATE
BACKGROUNDS OF ELECTRICAL, ELECTRONIC
AND MECHANICAL EXPERIENCE. ANY
ATTEMPT TO REPAIR A MAJOR APPLIANCE
MAY RESULT IN PERSONAL INJURY AND
PROPERTY DAMAGE. THE MANUFACTURER OR
SELLER CANNOT BE RESPONSIBLE FOR THE
INTERPRETATION OF THIS INFORMATION, NOR
CAN IT ASSUME ANY LIABILITY IN
CONNECTION WITH ITS USE.
E. BEFORE TURNING ON MICROWAVE
F. ANY DEFECTIVE OR MISADJUSTED
DISCONNECT POWER BEFORE SERVICING
IMPORTANT · RECONNECT
ALL GROUNDING DEVICES
ALL PARTS OF THIS APPLIANCE CAPABLE OF
CONDUCTING ELECTRICAL CURRENT ARE
GROUNDED. IF GROUNDING WIRES, SCREWS,
STRAPS, CLIPS, NUTS OR WASHERS USED TO
COMPLETE A PATH TO GROUND ARE REMOVED
FOR SERVICE, THEY MUST BE RETURNED TO
THEIR ORIGINAL POSITION AND PROPERLY
FASTENED.
G.
GROUNDING SPECIFICATIONS
PRECAUTIONS TO BE
OBSERVED BEFORE AND
Leakage Current 0.5 mA. (Max.)
Ground Path Resistance 0.14 ohms (MAX.)
DURING SERVICING TO
AVOID POSSIBLE
EXPOSURE TO
EXCESSIVE MICROWAVE
ENERGY
A.
IF OVEN IS OPERATIVE PERFORM
MICROWAVE EMISSION CHECK
PRIOR TO.
B. DO NOT OPERATE OR ALLOW THE
OVEN TO BE OPERATED WITH THE
DOOR OPEN.
C. IF THE OVEN OPERATES WITH THE
DOOR OPEN :
1) INSTRUCT THE USER NOT TO
OPERATE THE OVEN AND
2) CONTACT THE MANUFACTURER
AND THE CENTER FOR DEVICES
RADIOLIGICAL HEALTH
IMMEDIATELY.
D.
CHECK THE FOLLOWING SAFETY
ITEMS ON ALL MICROWAVE OVENS
(MWO) BEFORE ACTIVATING THE
MAGNETRON. MAKE REPAIRS AS
NECESSARY :
1. INTERLOCK OPERATION
2. PROPER DOOR CLOSING
3. SEAL AND SEALING SURFACES
(CHECK FOR ARCING, WEAR, AND
OTHER DAMAGE)
4. DAMAGE TO OR LOOSENING OF
HINGES AND LATCHES
5.
EVIDENCE OF DROPPING OR ABUSE
PUB. NO. 31-40014
INSTALLATION REQUIREMENTS
ELECTRICAL
MWO Power 950 Watts
Power Source 120 VAC, 60 Hz.
Line Current 13.5 Amps. (1580Watts)
Over Current Protection 20 Amps *
* Requires 120 Volt, 20 Amp. parallel,
grounded separate circuit.
Working Voltage 105-130 VAC.
MICROWAVE LEAKAGE TEST
1. Place 275 ml. water in 600 ml. beaker
2. Place beaker in center of oven shelf.
3. Set meter to 2450 MHz scale.
4. Turn oven "on" for 5 minute test.
5. Hold probe perpendicular to surface being
6. Maximum leakage 4 MW/CM
7. Record data on service invoice and
NOTE :
Inform the manufacturer of any oven found to
have emission in excess of 5 MW/CM
repairs to bring the unit into compliance at no
cost to owner and try to determine cause.
Instruct owner not to use oven if it has not
been brought into compliance.
POWER FOR ANY SERVICE TEST OR
INSPECTION WITHIN THE MICROWAVE
GENERATING COMPARTMENTS,
CHECK THE MAGNETRON, WAVE
GUIDE, AND CAVITY FOR PROPER
ALIGNMENT, INTEGRITY, AND
CONNECTIONS.
COMPONENTS IN THE INTERLOCK,
MONITOR, DOOR SEAL, AND
MICROWAVE GENERATION AND
TRANSMISSION SYSTEMS SHALL BE
REPAIRED, REPLACED, OR ADJUSTED
BY PROCEDURES DESCRIBED IN THIS
MANUAL BEFORE THE OVEN IS
RELEASED TO THE OWNER.
A MICROWAVE LEAKAGE CHECK TO
VERIFY COMPLIANCE WITH THE
FEDERAL PERFORMANCE STANDARD
SHOULD BE PERFORMED ON EACH
OVEN PRIOR TO RELEASE TO THE
OWNER.
(WB64X5010)
tested and scan surfaces at rate of one
inch/sec.
Test the following areas:
Entire perimeter of door and control panel
Viewing surface of door window
Exhaust vents
microwave leakage report.
Maximum allowable leakage is 5 MW/
2
. 4 MW/CM2is used to allow for
CM
measurement and meter accuracy.
2
2
. Make
WARNING!
TO PREVENT ELECTRICAL SHOCK, USE
EXTREME CAUTION WHEN DIAGNOSING
OVEN WITH OUTER CASE REMOVED AND
POWER "ON". THE HIGH VOLTAGE SECTION
OF THE POWER SUPPLY, INCLUDING
FILAMENT LEADS HAVE THE POTENTIAL
WITH RESPECT TO GROUND TO REACH
4000 VOLTS!
HIGH VOLTAGE CAPACITOR
The high voltage capacitor has an internal shunt
resistor to automatically discharge the capacitor
when the oven turns "off". Under normal
operation the capacitor should fully discharge
within 30 seconds.
WARNING!
Always be certain the capacitor is
discharged before servicing.
Discharge by placing an insulated handle
screw driver between the diode connection of
the capacitor and oven chassis ground.
PERFORMANCE TEST
1. Measure line voltage (loaded). This test is based
on normal voltage variations of 105V to 130V.
Low voltage will lower output power and
temperature rise.
2. Place WB64 X0073 beaker containing one liter
water (1000ml, 59
F~75 F) on turn table and
record the starting water temperature with
an accurate thermometor.
(DO NOT USE ANY OTHER LOAD OR DISH AS
RESULTS WILL VERY FROM STANDARD!)
3. Set at HIGH power for 2 minutes, and 3 sec.
4. Turn on the oven.
5. Record end water temperature.
The minimum difference between the initial
and ending temperature should be:
40 F @ 120 V
INTERLOCKS (DOOR Latch Switches)
Interlocks are designed as follows:
Primary - Bottom switch operated by bottom
latch pawl connected to line (L) leg.
TECHNICAL DATA SHEET
HOW TO TEST INTERLOCKS
1. Disconnect power, open control panel,
and discharge capacitor.
Primary
2. Check Continuity of Com and N.O. :
Door Closed –
Door Open –
MONITOR SWITCH
The monitor switch is located between the top
and bottom interlocks. The monitor switch is
operated indirectly by the bottom latch pawl.
HOW TEST MONITOR
1. Disconnect power, open control panel, and
discharge capacitor.
2. Disconnect monitor switch leads, and test at
terminals:
Door Closed –
Door Open –
3. Reconnect switch wiring.
4. Test Circuit Operation:
A) Connect temporary jumper across relay
contacts and primary switch to simulate
shorted switch contacts. Locate
convenient connections in circuit to be
certain COM and N.O. terminals are used.
B) Connect OHM meter (Low Scale) across
the two line terminals of appliance power
cord.
Continuity must show:
Door Close –
Door Open –
C) Remove 20 Amp. Fuse
Ohms). If not check wiring of monitor
and interlock circuits.
D)
WARNING!
jumper leads from interlocks and relay.
Reconnect monitor switch leads, replace
fuse.
E)
Replacement of any parts in monitor
After test remove temporary
– Circuit must open
circuit requires repeating this entire
test procedure.
IMPORTANT
Door, Interlock
:
Check for microwave leakage
after replacing or adjusting
switches or
brackets.
FUSE
WARNING!
to operation of the monitor switch, the monitor
switch must be replaced. Also replace relays
and / or interlock switches when continuity
check shows contacts shorted.
When 20 Amp. fuse is blown due
INTERLOCK REPLACEMENT
The switch housing is not adjustable. It is fixed
on the front cavity with 2 screws.
IMPORTANT - CHECK FOR MICROWAVE
LEAKAGE AFTER REPLACING OR
ADJUSTING DOOR, INTERLOCK
SWITCHES OR BRACKETS.
CAUTION !
When safety interlocks and monitor switches are
repaired or replaced, check microwave leakage.
Perform microwave leakage check, if leakage
does not exceed 4 MW/CM it is performing
properly.
2
AUTOMATIC FAN FEATURE
Exhaust fan turns "ON" automatically during
some surface unit heavy use conditions.
(Cannot be turned off manually - will turn off
automatically.) May stay on up to 15 mins.
after range and lower oven controls are
turned off.
HOOD THERMOSTAT
Single pole thermostat mounted ON R.H. side
duct in control compartment. Contacts close at
approx. 158 F.
BOTTOM THERMOSTAT
Single pole thermostat mounted on base plate.
Contacts open at approx. 248 F.
DOOR ASSEMBLY (NOT ADJUSTABLE)
The door assembly is serviceable as an
assembly or with parts.
MICROWAVE LEAKAGE TEST
A microwave leakage test must be performed
any time a door is removed, replaced,
disassembled, or adjusted for any reason.
THE MAXIMUM LEAKAGE IS
4 MW/CM
2
MICROWAVE OVEN HOODS
WARNING
NEVER TOUCH OR SERVICE THE
HIGH VOLTAGE CIRCUIT WITHOUT
DISCHARGING CAPACITOR BY
SHORTING ACROSS ITS TERMINALS.
TO AVOID POSSIBLE ELECTRICAL
SHOCK.
OVEN THERMAL CUTOUT
(FLAME SENSOR)
The Oven Thermal Cutout is located on the top
side of the Oven Cavity beside Exhaust duct
with a temperature rating of 212 F.(100 C.) The
cutout is tightly held to the top of the oven cavity
by a spring clip.
NOTE :
If cutout cannot be removed from clip
oven will have to be removed from
installation and outer case removed.
ANTENNA
The antenna is motor driven and located on the
upper side of the cavity. The oven uses a top
feed wave guide. The antenna blade is located in
the wave guide and the motor is located on the
wave guide.
To Service Antenna Blade
1. Disconnect power and open the door.
2. Remove the clip and turn the antenna cover
left.
3. Remove antenna cover and the antenna will
come with it.
To Service Antenna Motor
1. Disconnect power and remove grille
screws(2).
2. Remove grille and the bracket duct upper
screw.
3. Remove the bracket duct upper and
disconnect the antenna motor wire.
4. Remove antenna motor screws(2) and pull the
antenna motor.
To Service Turntable(on/off) Motor
1. Disconnect power and remove bottom plate
screws(7).
2. Remove bottom plate and disconnect the
turntable motor wire.
3. Remove turntable motor screws(2) and pull
the turntable motor.
CAPACITOR AND DIODE REMOVAL
The high voltage capacitor and diode can be
serviced through Control Panel after removing
grille.
1. Disconnect power and discharge capacitor.
2.
Disconnect capacitor leads and remove 1 screw.
3. Remove bracket-capacitor.
MAGNETRON, MAGNETRON FAN, VENT
BLOWER AND POWER TRANSFORMER
Oven must be removed from wall.
REMOVING OVEN FROM WALL
(2 PEOPLE REQUIRED)
Oven hooked on metal tabs at bottom of wall
mounting plate and fastened to cabinet by (3)
top cabinet bolts.
CAUTION :Oven weights about 62 lbs.
Requires 2 people for removal.
1. Disconnect Power Cord, Top vented models disconnect duct and remove damper assembly.
2. Remove top cabinet bolts(3).
3. Pull unit forward slowly, providing adequate
support to prevent dropping unit during
removal of last top cabinet bolt.