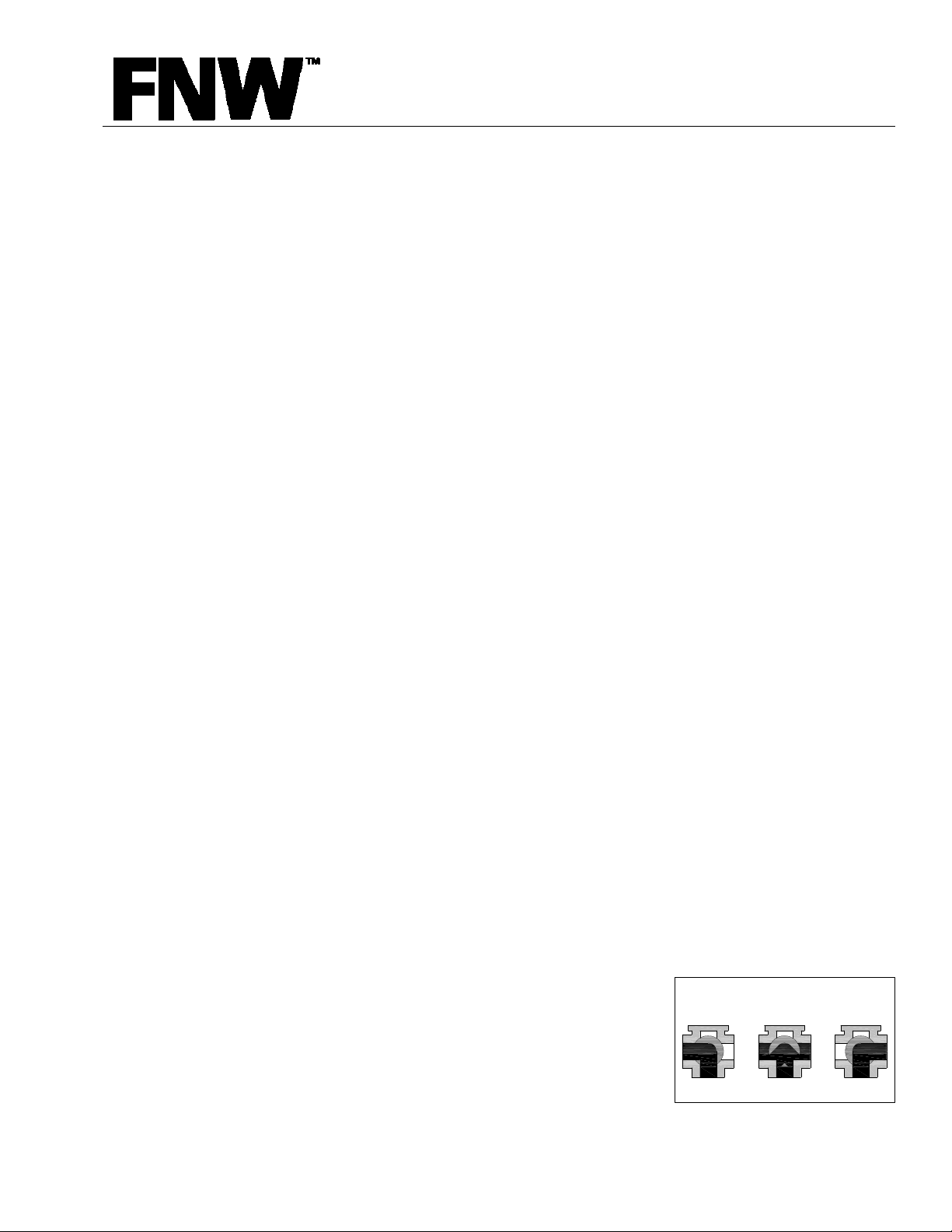
INSTALLATION, OPERATION & MAINTENANCE INSTRUCTIONS
FIGURE 233A 3-WAY BALL VALVE
INTRODUCTION
This instruction manual includes installation, operation and maintenance information for the figure 233A 3-way
ISO mount, 1000CWP, threaded end (NPT) ball valve.
INSTALLATION
WARNING
To avoid personal injury to your self, fellow workers, or damage to property from release of process fluid, before
installation:
a. Shut off all operating lines to the valve site
b. Isolate the valve site completely from the process
c. Release process pressure
d. Drain the process fluid from the valve site
1. Remove the protective plastic cap from the threaded ends and clean or flush the valve.
2. Before installing the valve, inspect the valve body port and associated equipment for any damage that may
have occurred and for any foreign matter that may have collected in shipping or storage. Make certain the
body interior is clean.
3. Before installing the valve, inspect the pipe line and mating pipe threads, making sure the pipe is free of
foreign material and the threads are clean and have no burrs or pits that could cause leakage.
4. Cycle the valve a couple of times before installation. Valves that are tested to MSS SP-110 may have water
trapped between the ball and body cavity. This can be removed by partially opening the valve, exposing the
cavity to the through port of the ball. Allow the water to drain out.
5. Use applicable sealant (e.g. - PTFE tape, high temperature pipe seal, etc.) to seal threaded ends on the
pipeline.
6. To prevent distortion or damage to the valve, do not apply torque through the valve. When tightening the
valve, always use a wrench on the end nearest the pipe being tightened. It is preferred that the pipe be
screwed into the valve, holding the valve stationary at the end being connected. Do not use the handle to
tighten the assembly as damage to the valve may occur.
7. Clean/flush the pipeline and leak test the system prior to using.
8. The square stem and notched mounting pad allow the handle to be installed in any of the four quadrants to
facilitate a clear stroke path for opening and closing the valve.
OPERATION
1. Ensure that the valve materials are compatible with the service and that the operating characteristics are
below the valve maximums.
2. Fluids containing particles or coagulating agents are not acceptable as they can reduce the life of the seats
and cause the torque to increase dramatically.
3. Care must be taken if throttling the valve (operation in partially open position). Critical pressure drops and
high flow rates can decrease the life of, or damage, the seats. For optimum operation, open/close
applications are recommended.
4. Slide the locking plate up the lever before operating. Open and close the valve by turning the handle onequarter turn (90°).
5. The top of the valve stem has an “L” etched in it. The direction of the “L”
indicates the valve’s port positions (i.e. – They point to the threaded ends
that the ball ports are connecting).
6. Flow plan A pictured to the right, demonstrates that the valve flows in all
ports while the lever is in mid position.
90° L-PORT PATTERN
POSITION 2POSITION 1 MID-POSITION
FLOW PLAN A
DOC: IOM_FNW233A_ ver_4-2011 Page 1 of 4
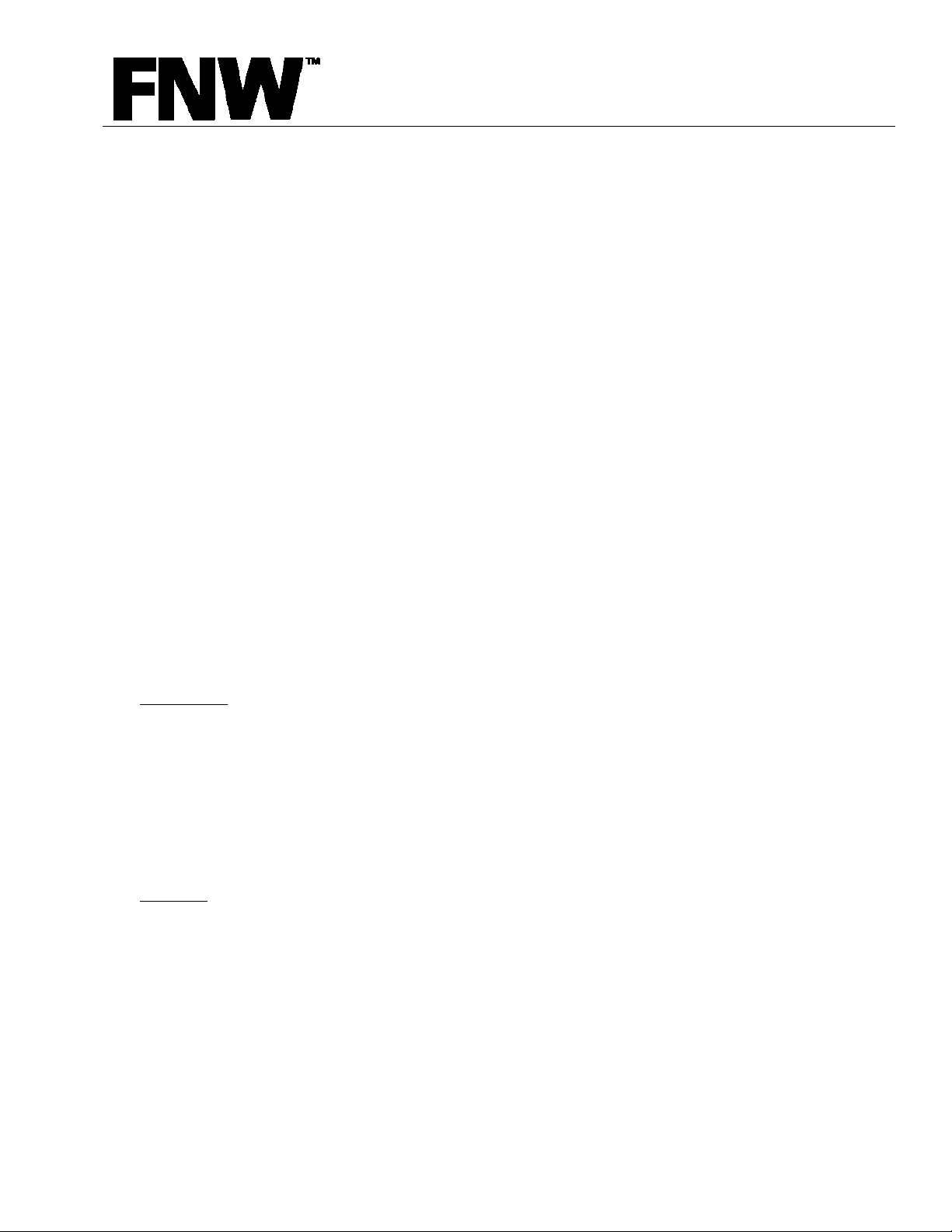
INSTALLATION, OPERATION & MAINTENANCE INSTRUCTIONS
FIGURE 233A 3-WAY BALL VALVE
MAINTENANCE
Valve parts are subject to normal wear and must be inspected and replaced as necessary. Inspection and
maintenance frequency depends on the severity of the service conditions. This section includes instructions for
packing adjustments, repacking, seat replacement and seating adjustment.
WARNING
To avoid personal injury, fellow workers, or damage to property from release of process fluids, before installation:
a. Shut off all operating lines to the valve.
b. Isolate the valve completely from the process.
c. Release process pressure.
d. Drain the process fluid from the valve.
1. Ball valves, if properly used, do not require internal lubrication or maintenance. However, a visual inspection
should be part of a regular maintenance program. A higher frequency of inspection is recommended for
valves operating under extreme conditions. Also, for proper operation it is recommended that the valve be
opened and closed at least twice a year.
2. Before any maintenance, open and close the valve at least once to release the pressure completely from the
valve body.
3. The valve includes live loaded packing that reacts to pressure changes and packing fatigue to reduce the
intervals needed for packing adjustments. If the stem packing leaks, remove the operator to access the lower
stem nut. Use a long reaching socket over the stem to turn the stem nut clockwise at 30° to 60° intervals until
the leak stops. If the stem nut can not be turned clockwise any further, or if the stem packing continues to
leak, it will have to be replaced or repaired. NEVER REPLACE VALVE PACKING WHILE THE VALVE IS IN
SERVICE.
4. The valve can be rebuilt by using a “Soft Goods” repair kit from FNW.
Disassembly
A. Place the valve in a vise in one of the end positions. Do not over-tighten the vise or the valve may be
B. Remove the first stem nut (13), handle (16), handle gland (14), stop-lock-cap (15), second stem nut
C. With a crescent or strap wrench, remove the end caps (2), seats (4), and the body gaskets (19).
D. Remove the ball (3) and final seat (4).
E. Push the stem (5) down through the body (1), and then remove the o-ring (8) and thrust washer (7)
F. Remove the bushing (10) and packing (9) from the body.
Assembly
A. Rebuild the valve by using all the replacement parts of the rebuild kit.
B. Ensure that all parts are clean and undamaged.
C. Assemble the valve in reverse order of the disassembly instructions, except install the packing and
It is recommended to cycle and test the valve prior to resuming service. After reinstallation into the piping system,
it may be necessary to adjust the stem nut/packing gland as described in step 3.
deformed.
(13), belleville washers (12), and gland (11).
from the stem.
bushing after the stem is inserted.
DOC: IOM_FNW233A_ ver_4-2011 Page 2 of 4