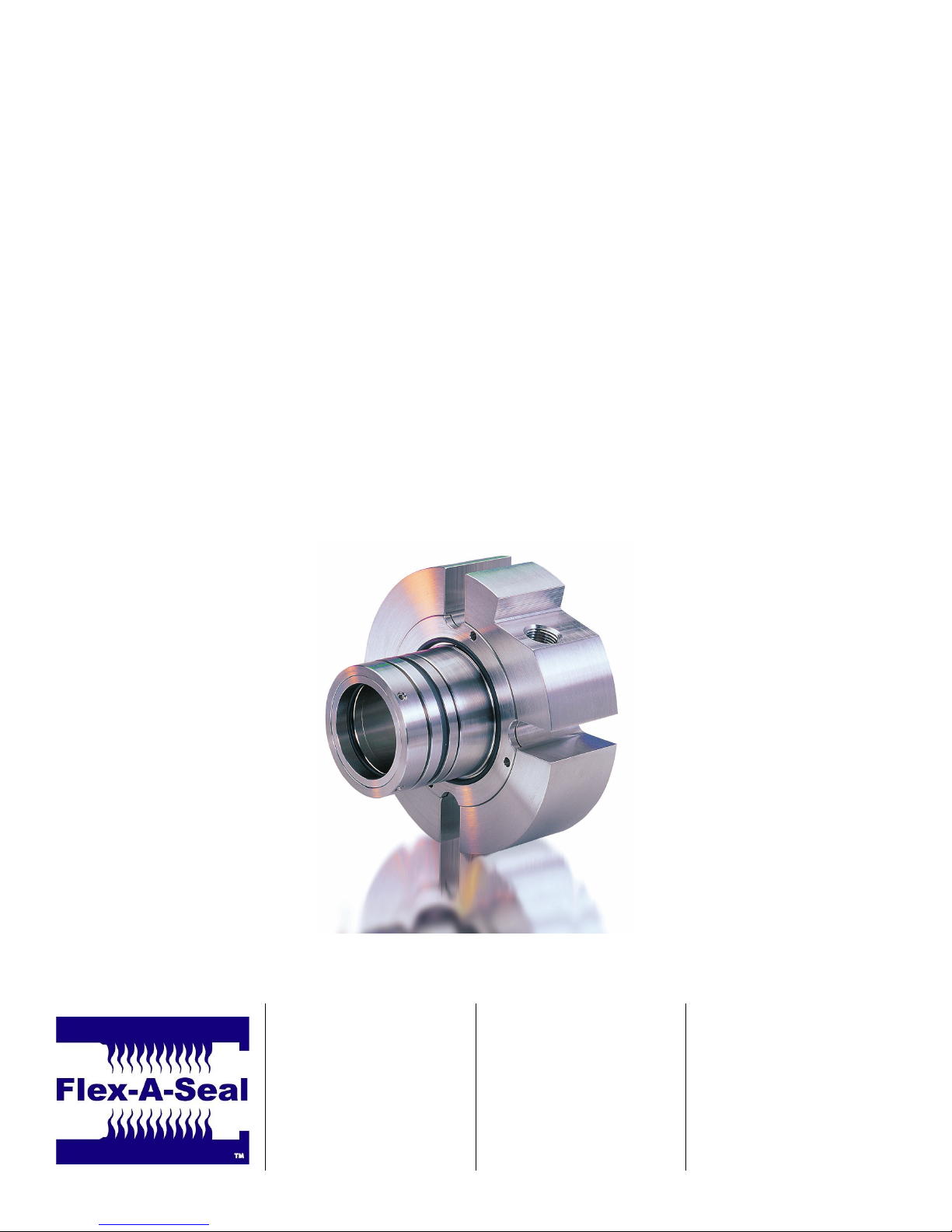
INSTALLATION,
OPERATION &
MAINTENANCE
GUIDE
STYLE 79
INTERNATIONAL BRAZIL SOUTHERN USA
HEADQUARTERS REPAIR & SERVICE
1 Jackson Street Rua Javaés, 441/443 1719 South Sonny Avenue
Essex Junction, VT 05452 Bom Retiro, Sao Paulo Gonzales, LA 70737
TEL: (802) 878-8307 TEL: 55-11-3736-7373 TEL: (225) 484-0007
FAX: (802) 878-2479 FAX: 55-11-3736-7355 FAX: (225) 341-8922
Brazil CEP 01130-010
REVISED: February 2019
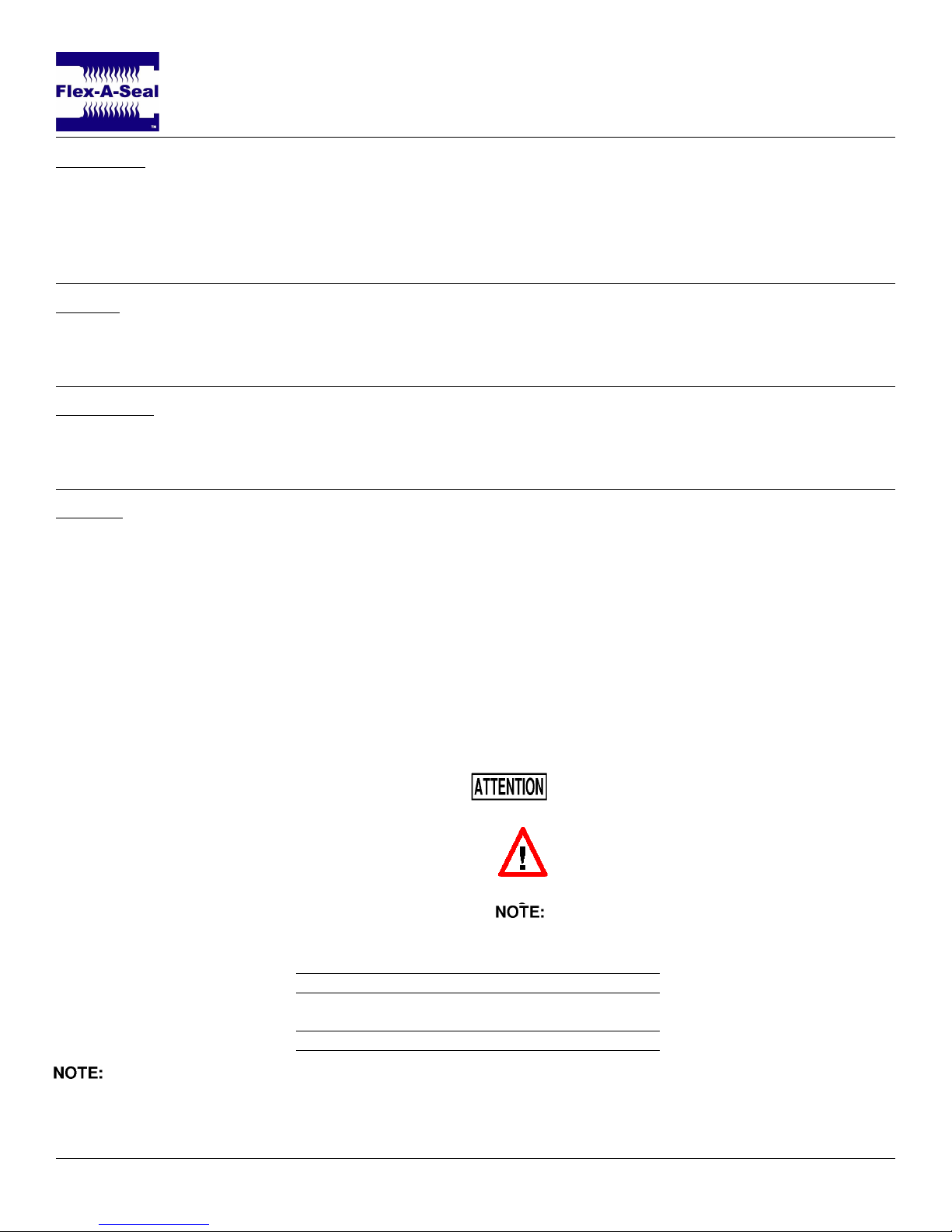
Installation, Operation & Maintenance Guide
Style 79
OVERVIEW
This guide outlines the installation, operation and maintenance of the Flex-A-Seal Style 79 Double Cartridge
Seals. The Style 79 is a highly engineered dual/tandem stationary multi-spring cartridge seal with an internal
pumping ring. The Style 79 can also be designed to comply with API 682 Standards, giving it the designation
Style 79A.This guide, in addition to the manuals provided by the pump manufacturer and the manufacturer of
any auxiliary equipment, should be read in its entirety prior to installation.
NOTICE
Flex-A-Seal does not assume responsibility for misuse, or any damages incurred as a result of the misuse of the
supplied sealing system. Contact a Flex-A-Seal representative before making any changes to the provided
system or design.
WARRANTY
Flex-A-Seal’s limited warranty covers material defects and workmanship for its goods and/or services for a
period of six (6) months for new items, or three (3) months for repaired items, from the date of their initial
use/installation or delivery, whichever occurs first.
SAFETY
1. Read all instructions thoroughly prior to
beginning installation. Review engineering
prints for special notes and/or instructions.
2. Removal, installation, operation, and
maintenance must only be carried out by
qualified personnel who have thoroughly read
all instructions.
3. The seal must only be used for its intended
application. Flex-A-Seal cannot be held liable
for use outside the scope of the recommended
application.
4. Inspect the replacement seal prior to removal
of the old seal or installation of the new seal
using the technical information provided in this
document. Contact a Flex-A-Seal
representative if there are any questions.
5. Follow plant safety regulations and procedures
throughout the disassembly/installation process
including, but not limited to, the following:
Style 79 Maximum Operating Conditions
Temperature 400◦F (204◦C)
Pressure
Speed 4500 fpm (22 m/s)
Inboard Differential: 400 psi (28 bar)
Outboard: 400 psi (17 bar)
• Lockout/tagout procedures
• SDS consultation for any hazardous
materials involved
• Use of proper personal protective
equipment
• Relief of any system pressure and
mechanical energy
6. The following symbols have been used
throughout the document to highlight important
information:
Instructions intended to prevent damage to
the seal or equipment.
7. Mandatory instructions intended to prevent
personal injury or extensive damage to
equipment.
8. Information to note while installing, or for
later use.
• Maximum temperature, pressure, and speed indicate operating extremes independently and
do not imply the seal will function at these extremes at the same time. Contact Flex-A-Seal if
in doubt.
Page 1 of 7
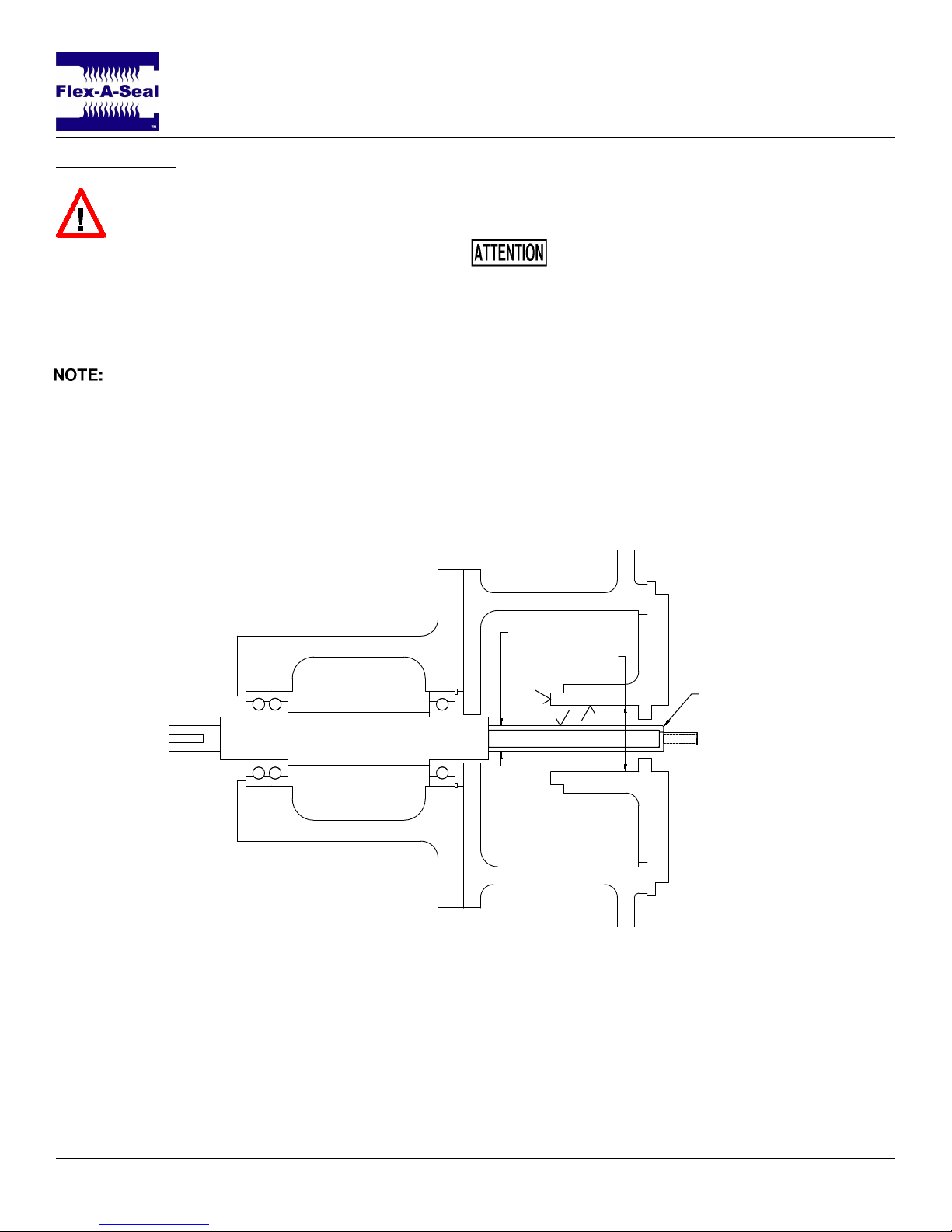
PREPARATION
(B) BORE ID
(A) SLEEVE OD
.030 MIN. x 30°
63
63
63
Installation, Operation & Maintenance Guide
Style 79
• Verify that equipment has been properly
shut off and rendered inoperative according
to plant safety protocol (e.g. lockout/tagout
procedures).
1. Disassemble the pump seal chamber, in
accordance with the pump OEM instructions, to
expose the existing seal.
Document how the seal chamber is
disassembled for re-assembly.
2. Carefully remove the existing sealing device,
taking care not to damage the shaft.
3. Clean the shaft, shaft sleeve (if present), and
seal chamber face of rust, burrs, grit, sharp
edges, and set screw damage using fine emery
cloth. Wipe clean.
Avoid making flat spots or reducing the
shaft diameter.
4. If the pump is equipped with a shaft sleeve,
verify the condition of its O-ring or gasket and
ensure that it is properly located (fully engaged
against step/hook/snap ring).
5. Sealing surfaces and the shaft or shaft sleeve
must have at least a 63 Ra-µin surface finish as
seen in Figure 1.
6. For ease of installation, the leading edge of the
shaft or sleeve should be chamfered as shown
in Figure 1 and all parts should be deburred.
Figure 1: Surface finish and chamfer locations. Fully assembled pump without seal.
Page 2 of 7