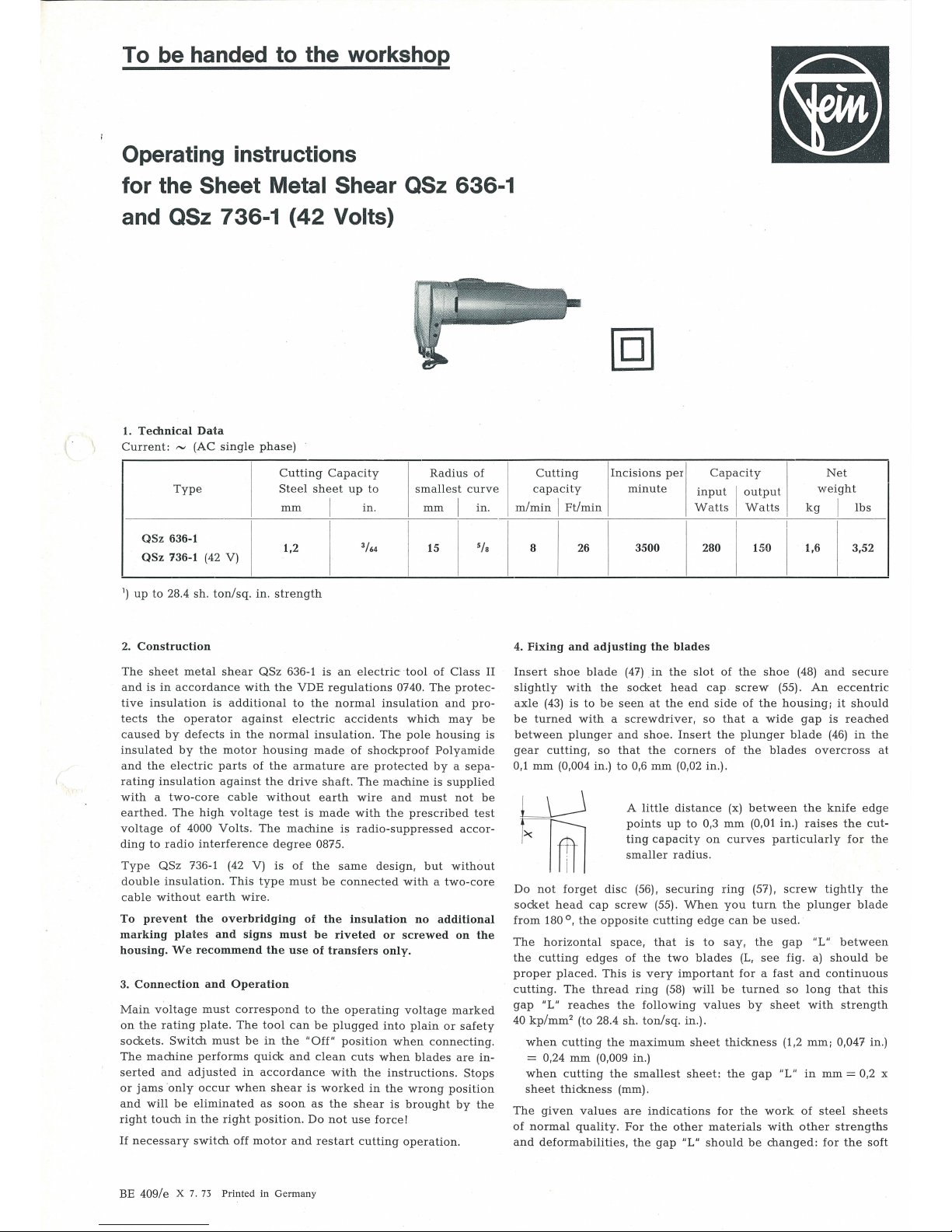
(
To be handed to the workshop
Operating instructions
for the
Sheet Metal Shear QSz 636-1
and
QSz 736-1
(42
Volts)
1.
Technical
Data
Current: ~ (AC
single
phase)
Cutting
Capacity
Radius
of
Type
Ste
el
sheet
up
to
smallest
curve
mm
I
in.
mm I in.
QSz
636-1
3
/64
>fa
1,2
15
QSz
736-1
(42 V)
1
)
up
to
28.4
sh.
ton/sq. in. strength
2.
Construction
The
sheet
metal
shear
QSz
636-1
is
an
electric -tool
of
Class
II
and
is
in
accordance
with
the
VDE
regulations
0740.
The
protec-
tive
insulation
is
additional
to
the
normal
insulation
and
pro-
tects
the ope
rator
against
electric
accidents
which
may
be
caused
by
defects
in
the
normal
insulation.
The
pole
housing
is
insulated
by
the
motor
housing
made
of
shockproof
Polyamide
and
the electric
parts
of
the
armature
are
protected
by a sepa-
rating
insulation
against
the
drive
shaft.
The
machine
is
supplied
with a two-core
cable
without
earth
wire
and
must
not
be
earthed.
The
high
voltage
test
is
made
with
the
prescrib
ed
test
voltage
of
4000
Volts.
The
machine
is
radio-suppressed
accor-
ding
to
radio
interference
degree
0875.
Type
QSz
736-1 (42 V)
is
of
the
same
design,
but without
double insu
lation.
This
type
must
be conne
cted
with a two-core
cable
without
earth
wire.
To
prevent
the
overbridging
of
the
insulation
no
additional
marking
plates
and
signs
must
be
riveted
or
screwed
on
the
housing.
We
recommend
the
use
of
transfers
only.
3.
Connection
and
Operation
Main
voltage
must
correspond
to
the
operating
voltage
marked
on
the
rating
plate.
The
tool
can
be
plugged
into
plain
or
safety
sockets.
Switch
must
be
in
the
"Off"
position
when
connecting.
The
machine
performs
quick
and
clean
cuts
when
blades
are
in-
serted
and
adjusted
in
accordance
with
the
instructions. Stops
or
jams ·only
occur
when
shear
is
worked
in
the
wrong
position
a
nd
will
be eliminated
as
soon
as
the
shear
is
brought
by the
right
tou
ch
in
the
right
position.
Do
not
use
force!
If
necessary
switch
off
motor
and
restart
cutting
operation.
BE 409/e X 7.
73
Printed
in
Germany
Cutting
Incisions
per
Capacity
Net
I
capacity
minute
i
nput I output
weight
m/min I Ft/min
Watts
Watts
kg
I
lbs
I
I
I
8
26
3500
280
150
1,6
3,52
4.
Fixing
and
adjusting
the
blades
Insert
shoe
blade
(47)
in the
slot
of
the
shoe
(48)
and
secure
slightly with
the
socket
head
cap
screw
(55).
An
eccentric
axle
(43)
is
to
be
seen
at
the
end
side
of
the
housing;
it
should
be
turn
ed
with a screwdriver, so
that a wide
gap
is
reached
between
plunger
and
shoe
. Insert
the
plunger bla
de
(46)
in
the
gear cutting,
so
that the
corne
rs
of
the
blades
overcross
at
0,1
mm (0,004 in.)
to
0,6
mm
(0,02 in.).
A
little
distance
(x)
between the
knife
edg
e
points
up
to
0,3
mm
(0,01
in.) raises
the
cut-
ting
capacity on
curves
particularly
for
the
smaller
radi
us.
Do
not
for
get
disc
(56).
securing
ring
(57).
screw
tightl
y t
he
socket
head
cap
screw
(55).
When
you
turn
the
plunger
blade
from
180 °,
the
opposite
cutting
edge
can
be
used
.
The
horizontal
space, that
is
to
say,
the
gap
"L"
between
the
cutting
edges
of the
two
blades
(L,
see
fig
. a)
should
be
proper
placed. This
is
very
important
for a fa
st
and
continuous
c
uttin
g.
The
thr
ead
ring
(58)
will
be
turned
so long
that
this
gap
"L"
reac
hes the fo
llo
wing values
by
sheet with
strength
40 kp/
mm2 (to 28.4
sh.
ton/sq.
in.).
when
cutting
the
maximum
sheet
thickness (1,2 mm; 0,047 in.)
= 0,24
mm
(0,009 in.)
when
cutt
ing
the
smallest
sheet:
the
gap
"L" in
mm
= 0,2 x
sheet thickness
(mm),
The giv
en
values
are
indications
for
the
work
of
steel
sheets
of
normal
quality. For
the
other
materials
with other
strengths
and
deformabilities,
the
gap
"L"
should
be
changed:
for
the
soft
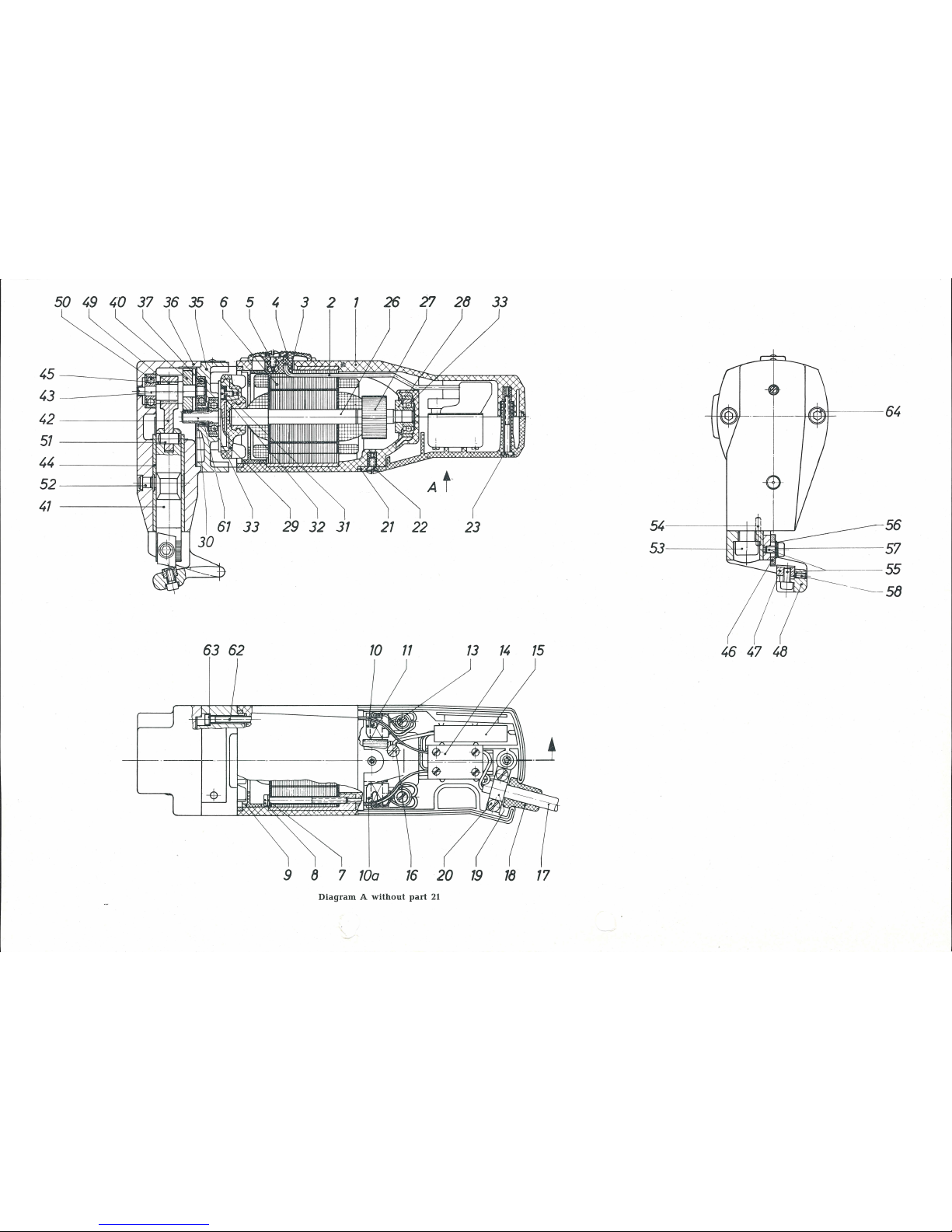
50
49
4D
37 36 35 6 5 4 3 2 1
26
27
28
33
45------~~~~~
43
--
----~~~~ii~~::::::~~~IJ~~fl
42 - -
--!Lt----ll-----00
~
I
~
-
-
64
44
--
-~
52
~::±:-:71Y
A t·
I
,.
47
--
------v-
rt--
33
29
32
31
22 23
54
~56
53 .
..
57
-
55
-----
58
13
14
15
46 47 48
--+-
- -
-+-
H---+l-1--- · @ ) ' \ I
HI
p - . ' I
}#t(~·_j
9 8 7
10a
16
20
19
18
17
Diagram A without
part
21