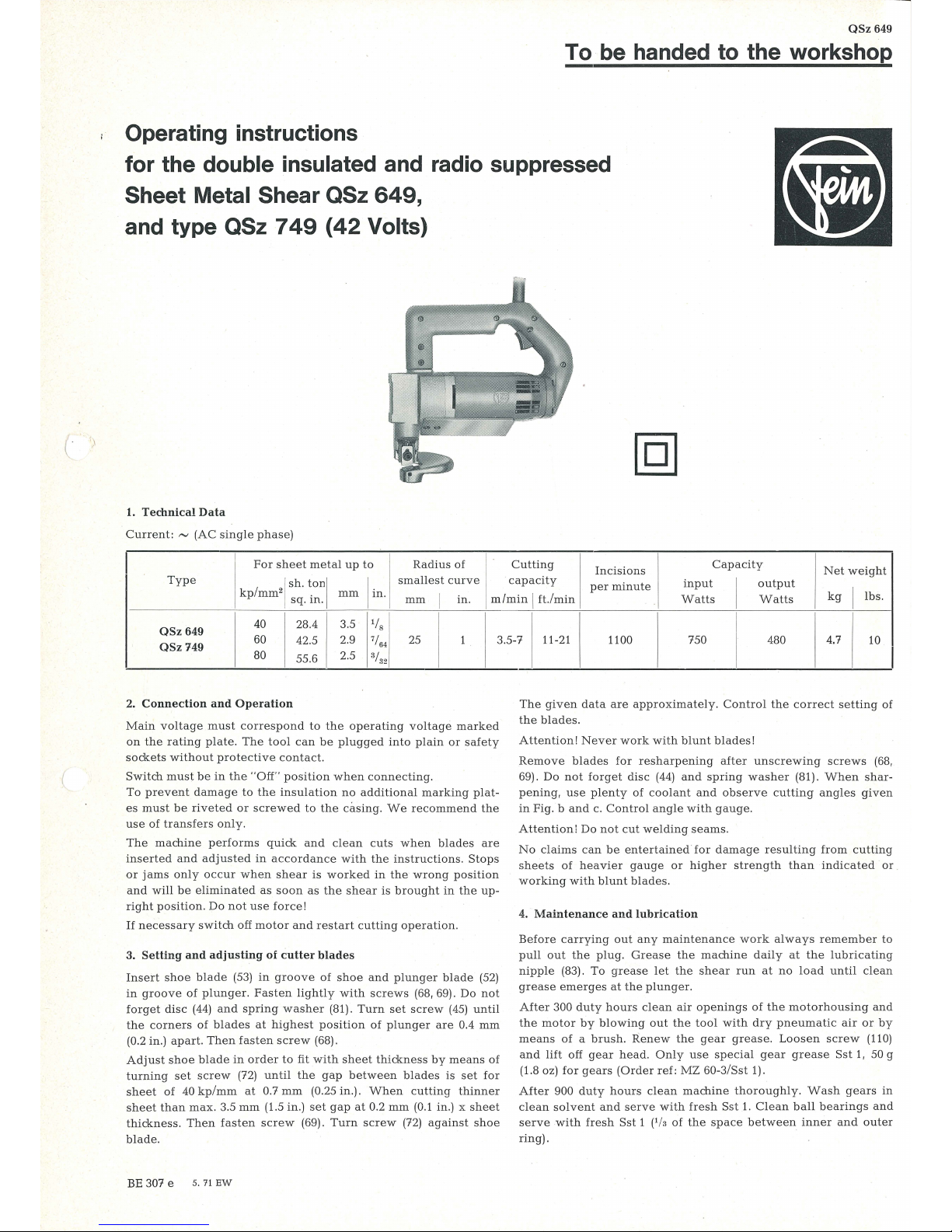
(
QSz
649
~
be handed to the workshop
Operating instructions
for the
double insulated and radio suppressed
Sheet
Metal Shear QSz
649,
and type QSz 7
49
(42
Volts)
1. Technical
Data
Current: ~ (AC
single
phase)
I
For
sheet
metal
up
to
Radius
of 1·
Cutting
Incisions
Capacity
Net
weight
Type
I j
sh.
ton
i
I
in.
smallest
curve
capacity
per
minute
input
I
output
kp
mm
2
.
mm
mm I in
. 1
m/min I ft./min
Wa
tts
Watts
kg I lbs
.
1
sq.
m.
40
28.4
3.5
lfs
I
QSz
649
QSz
749
60
42.5
2.9
7
/64
1
25
1
3.5-7
11-21
1100 750 480 4.7
10
80
55.6
2.5
3
/32
2.
Connection
and
Operation
Main
voltage
must
correspond
to
the
operating
voltage
marked
on
the
rating
plate.
The
tool
can
be
plugged
into
plain
or
safety
sockets
without
protective
contact.
Switch
must
be
in
the
"Off" position when
connecting
.
To
prevent
damage
to
the
insulation
no
additional
mar
king plat-
es
must
be
riveted
or
screwed
to
the
casing.
We
recommend
the
use
of
transfers
only.
The
machine
performs
quick
and
clean
cuts
when
bla
des
are
inserted
and
adjusted
in
accordance
with
the
instru
ctions. Stops
or
jams
only
occur
when
shear
is worked
in
the
wrong
pos
ition
and
will
be eliminated
as
soon
as the
shear
is
brought
in the
up-
right
position.
Do
not
use
force!
If
necessary
switch
off
motor
and
restart
cutting
operation.
3.
Setting
and
adjusting
of
cutter
blades
Insert
shoe
blade
(53)
in
groove
of
shoe
and
plunger blad
e (52)
in
groove of
plunger.
Fasten lig
htly with
screws
(68, 69).
Do
not
forget
disc
(44)
and
spring
washer
(81).
Turn
set
screw
(45) until
the
corners
of
blades
at
highest
position
of
plunger
are
0.4
mm
(0.2 in.)
apart.
Then
fasten
screw
(68).
Adjust
shoe
blade
in
order
to
fit
with
sheet
thickness
by
mea
ns
of
turning
set
screw
(72)
until
the
gap
between
blades
is
set
for
sheet
of
40
kp/mm
at
0.7
mm
(0.25 in.).
When
cutting
thinner
sh
eet
than
max.
3.5
mm
(1.
5 in.)
set
gap
at
0.2 mm
(0.1
in.) x
sheet
thickness.
Then
fasten
screw
(69).
Turn
scr
ew
(72)
against
shoe
blade.
BE 307 e 5. 71
EW
I
The
given data
are
approximately.
Control
the
correct
setting
of
the
blades.
Attention! Never
work with
blunt
blades!
Remove
blades
for
resharpening
after
unscrewing
screws
(68
,
69).
Do
not
forget
disc
(44)
and
spring
washer (81
).
When
shar-
pening, use
plenty
of
coolant
and
observe
cutting
angles given
in
Fig. b
and
c.
Control
angle
with gauge.
Attention!
Do
not
cut wel
ding
sea
ms.
No
claims
can
be
entertained
for
damage
resulting
from cutt
ing
sheets
of
heavier
gauge
or
high
er
strength
than
indicated
or
working
with blunt
blad
es.
4.
Maintenance
and
lubrication
Before
carrying
out any
mainte
nance
work alw
ays
remember
to
pull
out
the
plug.
Grease
the
machine
daily
at
the
lubricat
ing
n
ipp
le (83).
To greas
e l
et the
shear
run
at
no
load until
clean
grease
eme
rges
at
the
plunger.
After
300
duty
hours
clean air
openings
of
th e mot
orhousi
ng
and
the
motor
by
blowing
out the
tool
with
dry
pneumatic
air
or
by
means
of a brush.
Rene
w t
he
gear
grease.
Loosen
screw
(110)
and lift
off
gear
head. On
ly
use
special
gear
grease
Sst
1, 50 g
(1.8 oz) f
or
gears
(Ord
er
ref:
MZ
60-3/Sst
1).
After
900
duty
hours
clean
mac
hine thorough
ly.
Wash
gears
in
clean
solvent
and
serve
with fres
h S
st
1. Clean
ball
bearings and
ser
ve
with fresh
Sst
1 (lh of t
he
space
bet
ween
inn
er
and outer
ring).