
597
r
--
-58- 59 60
67
I !
1-
1
1
--
-------
42
43
44
45
46 47 48
49
50
775
112
113
117
719
114
111
121
125
126
127
~~~
j
j
r
' I · I j
"j
j j j j
- / /
~F$
~~~mhttps://manualmachine.com/~
/-
//
rJ:;
//
~
129
134
735
I I
I
755
153
156
I I I
i
/
758
759
I
69a
82a 82
I l
~
~
~~
-
I
~ u ~
~ ~J
I I
~
I I I I I I I I I I I
T
r
~ZS
/// //.b 7 1
7
/ fi
!J
~
z\(
;\;
'v
~
178
122123720730731739
124
128
740
132
738
137
736
133 154
757
150
757
752
- I
--r-r--
I I i
I : ( I
~
I
••
77 72 i I ( I 67 i 37 138
I i I ! I I I
75 90 89
88 87
73
74
54
63
64
65
66
68
69 75a 40
41
94
79
-
-
~
78
77
~
81
76
Section A-B
99-----r
700
- -
~
t
96
--~
\
_
Y'Y
707
rn
Fr
ont Sect
ion
1
'¥\(
0)
~
-
----
__
_j
I
i
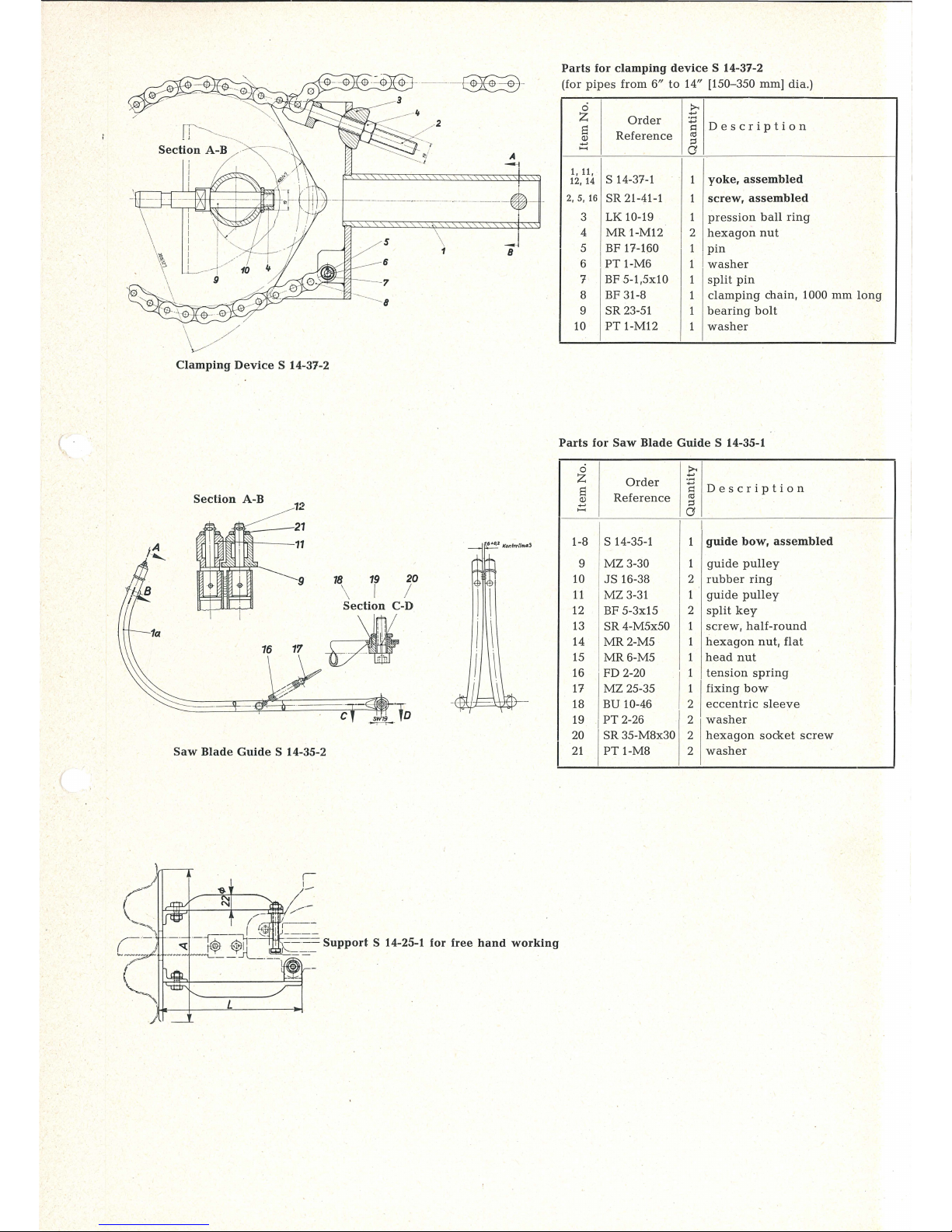
Parts
for
clamping
device
S 14-37-2
(for
pipes
from
6"
to
14" [150-350 mm] dia.)
0
£
z
Order
.....
Descrip
tion
s
.:
Reference
co
~
;:I
a
1, 11,
s 14-37-1
1
yoke,
assembled
12,
14
2, 5,
16
SR
21-41-1
1
screw,
assembled
3
LK 10-19
1
pression
ball
ring
4
MR
l-M12
I
2
hexagon
nut
5 BF 17-160
1
pin
6
PT
1-M6
1
washer
7
BF 5-1,5x10
1
split
pin
8
BF 31-8
1
clamping
chain, 1000
mm
long
9
SR
23-51 1
bearing
bolt
10
PT 1-M
12
1
washer
Clamping
Device
S 14-37-2
(
Parts
for
Saw
Blade
Guide
S 14-35-1
Section
A-B
12
0
.~
z
Order
s
-;:;
Description
Reference
co
~
;:I
a
aTr,--
- 21
rm;rtt-f'rt--
--
11
Is 14-35-1
I
1-8
1
guide
bow,
assembled
9
MZ
3-30
1
guide
pulley
16
18
19
20
\ I I
Section
C-D
-~if
-",..,;..,..,
Saw
Blade
Guide
S 14-35-2
10
JS
16-38 2
rubber
ring
11
MZ
3-31 1
guide
pulle
y
12 BF 5-3x15 2
split
key
13 SR 4-M5x50 1
screw,
half-round
14
MR2-M5
1
hexagon
nut,
flat
15
MR6-M5
1 h
ead
nut
16 FD 2-20
I
1
tension spring
17
MZ
25-35
1
I
fixing
bow
18
BU 10-46 2
eccentric
sleeve
19
1
PT
2-26
2
washer
20
SR
35-M8x30 2 h
exagon
socket screw
.__I
21--'-1 P_T
1--M
8 -----'----'-2 w_ash_er --·J
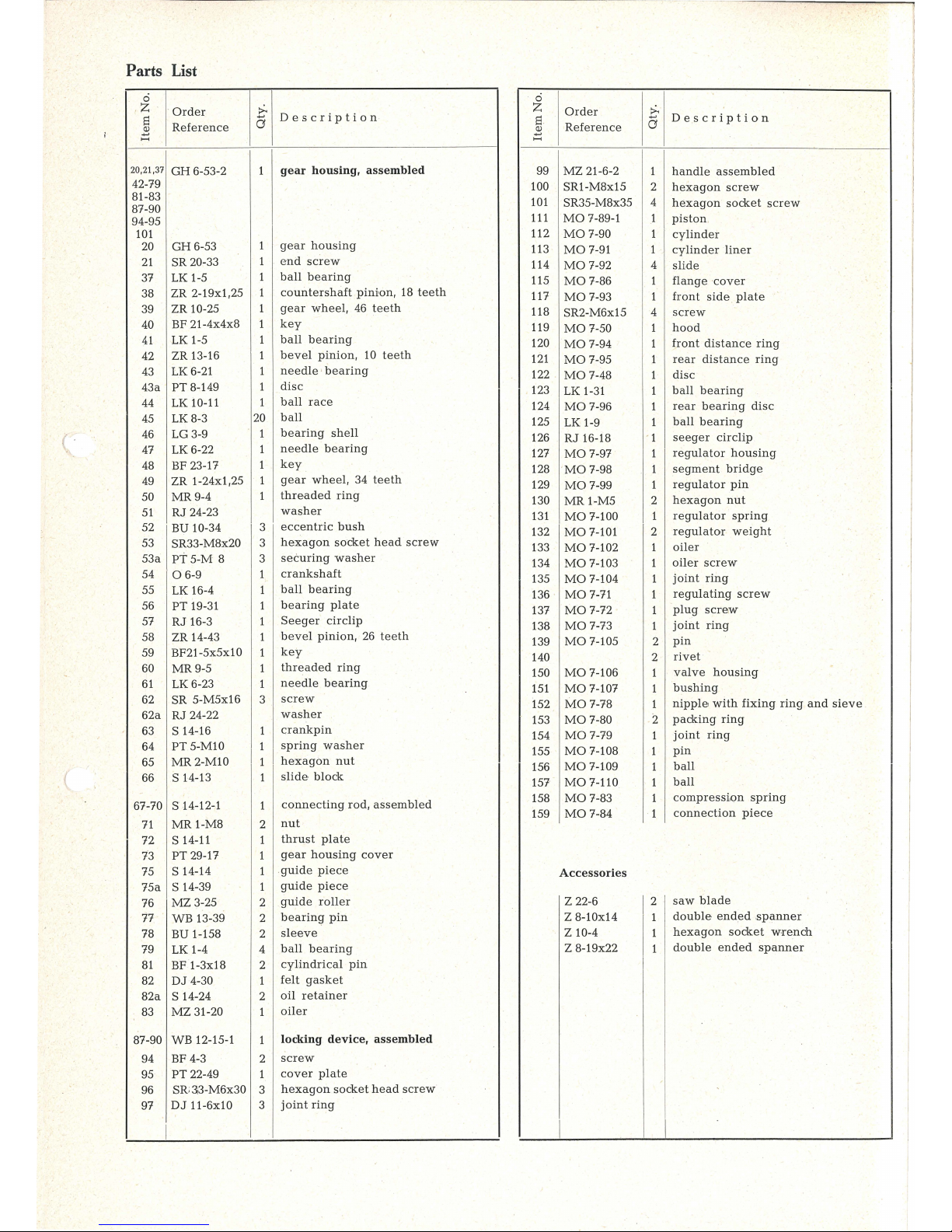
Parts List
0
z
·
Order
:>.
Description
s
a
~
Reference
0
z
Order
:>.
s
a
Description
~
Reference
20,21,37
GH
6-53-2 1
gear
housing,
assembled
99
MZ
21-6-2
1
handle
assembled
42-79
81-83
87-90
100 SR1-M8x15
2
hexagon
screw
101
SR35-M8x35 4
hexagon
socket
screw
94-95
111
MO
7-89-1
1
piston
101
20
GH
6-53
1
gear
housing
21
SR
20-33
1
end
screw
112
MO
7-90
1
cy
linder
113
MO
7-91 1
cylinder
lin
er
114
MO
7-92 4
slide
37
LK 1-5
1
ball bearing
38
ZR 2-19x1,25
1
countershaft
pinron,
18
teeth
115
MO
7-86 1
flange
cover
117
MO
7-93
1
front
side
plate
39
ZR 10-25 1
gear
wheel,
46
teeth
118
SR2-M6x15
4
screw
40
BF 21-4x4x8 1
key
119
MO
7-50
1
hood
41
LK 1-5 1
ball
bearing
120
MO
7-94
1
front
distance
ring
42
ZR 13-16 1
bevel
pinion,
10
teeth
43
LK 6-21 1
needle· bearing
121
MO
7-95 1
rear
distance
ring
122
MO
7-48 1
disc
43a
PT
8-149
1
disc
44
LK 10-11
1
ball
race
45
LK8-3
20
ball
46
LG 3-9
1
bearing
shell
47
LK 6-22
1
needle
bearing
48 BF 23-17
1
key
49
ZR 1-24x1,25
1
gear
whee
l, 34
teeth
50
MR9-4
1
threaded
ring
51
RJ
24-23
washer
52
BU 10-34
3
eccentric
bush
53
SR33-M8x20
3
hexagon
socket
head
screw
53 a
PT 5-M
8
3
securing
washer
123
LK 1-31 1
ba
ll
bearing
124
MO
7-96
1
rear
bearing
disc
125
LK 1-9
1
ball
bearing
126
RJ
16-18
' 1
seeger
circlip
127
MO
7-97 1
regulator
housing
128
MO
7-98 1
segment
bridge
129
MO
7-99
1
regulator
pin
130
MR
1-M5
2
hexagon
nut
131
MO
7-100
1
regulator
spring
132
MO
7-101
2
regulator
weight
133
MO
7-102
1
oiler
134
MO
7-103 1
oiler
screw
54
0 6-9
1
crankshaft
55
LK 16-4
1
ball
bearing
56
PT
19-
31
1
bearing
plate
57
RJ
16-3 1
Seeger
circlip
58
ZR
14-43 1
b
evel pinion,
26 teeth
59
BF21
-5x5x
10
1
key
135
MO
7-104 1
joint
ring
136
MO
7-71 1
regulating
screw
137
M07-72
1
pl
ug
screw
138
MO
7-73
1
joint
ring
139
MO
7-105
2
pin
140 2
rivet
60
MR9-5
1
threaded
ring
61
LK 6-23 1
needle
bearing
150
MO
7-106
1
valve
housing
151
MO
7-107 1
bushing
62
SR
5-M5x16
3
screw
62a
RJ
24-22
washer
63
s 14-16 1
crankpin
64
PT
5-MlO 1
I
spring
washer
65
MR2-M10
1
h
ex
agon
nut
152
MO
7-78
1
nipple
with
fixing
ring and
sieve
153
MO
7-80 2
pack
ing
ring
154
MO
7-79
1
joint
ring
155
MO
7-108
1
pin
156
MO
7-109
1
ball
66
s 14-13 1
slide
block
157
MO
7-110
1
ball
67-70
s 14-12
-1
1
connecting
rod,
assembled
71
MR
1-M8 2
nut
158
MO
7-83 1
compressi.on
spring
159
MO
7-84
1
connection
piece
72
s 14-11 1
thrust
plate
73
PT
29-17 1
gear
housing
cover
75
s 14-14
1
guide piece
Accessories
75a
s 14-39
1
guide
piece
76
MZ
3-25 2
guide
roller
77
WB
13-39 2
bearing
pin
z 22-6
I
2
saw
blade
Z 8-10x14
1
doub
le
ended
.spanner
78 BU 1-158
2
sleeve
z 10-4
1
hexagon
socket
wrench
79 LK 1-4
4
ball
bearing
Z 8-19x22
1
do
uble
ended
spanner
81
BF 1-3x18 2
cy
lindri
cal
pin
82
DJ
4-30
1
felt
gasket
82a
s 14-24 2
oil
retainer
83
MZ
31-20
1
oiler
87-90
WB
12-15-1
1
locking
device,
assembled
94
BF 4-3 2
screw
95
PT
22-49
1
cover
plate
96
SR
;33-M6x30
3
hexagon
socket head scr
ew
97
DJ
11-6x10 3
joint
ring
I