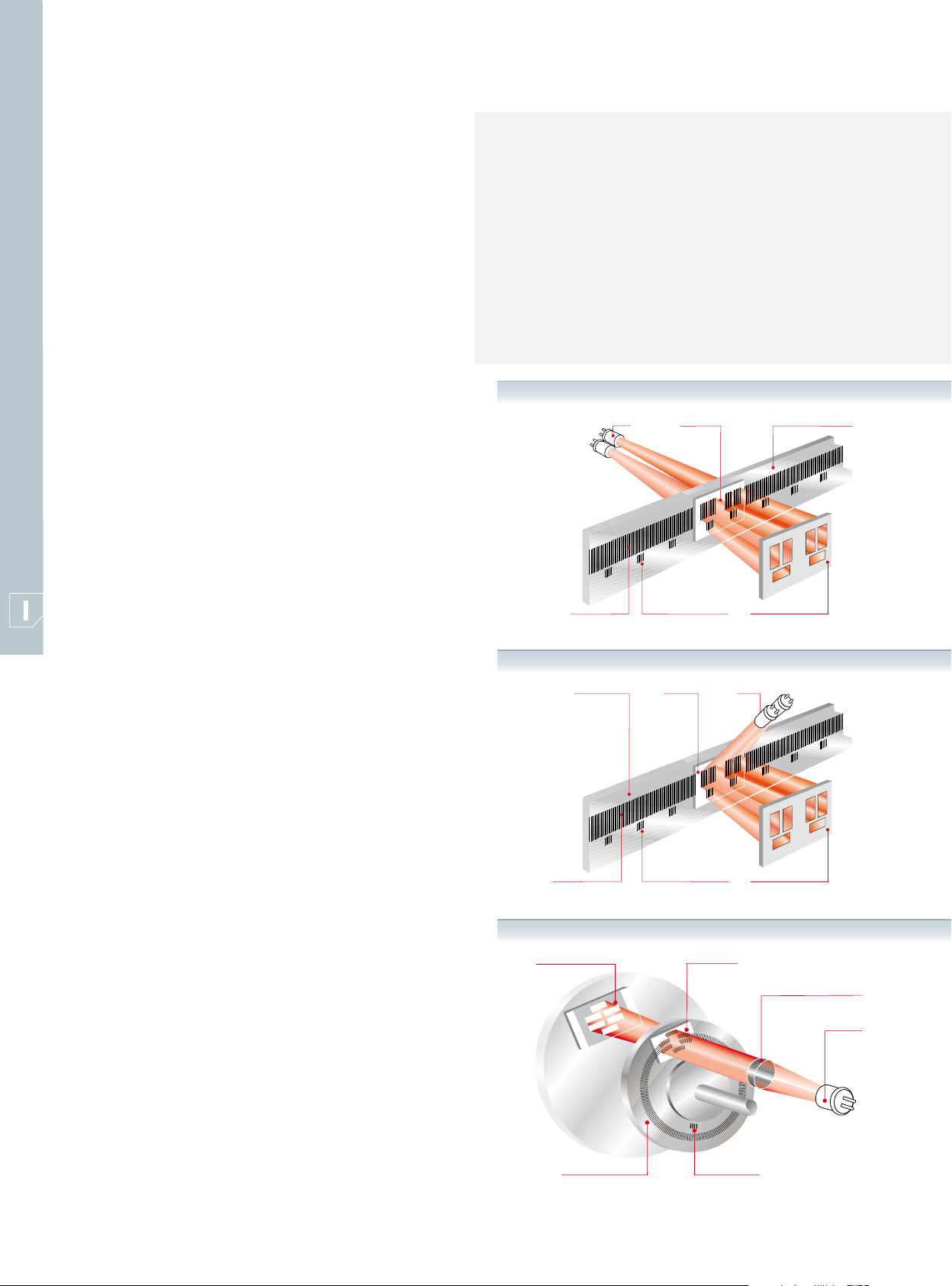
I N C R E M E N T A L
Technology
The incremental encoders provide direct
measure of machine position without using
any intermediate device. The positioning
errors originating from machine mechanics
are minimized as the encoder is directly
mounted to the machine surface and
the guide ways. The encoder sends the
real machine movement data to the CNC
and mechanical errors caused due to
thermal behavior of the machine, pitch
error compensation and backlash etc. are
minimized.
Measuring Methods
Fagor Automation uses two measuring methods in their
incremental encoders:
• Graduated glass: Linear encoders with a measuring
length of up to 3 040 mm use optical transmission. The
light from the LED goes through a graduated glass and a
reticule before reaching the receiving photo diodes. The
period of the generated electrical signals is the same as the
graduation pitch.
• Graduated steel: Linear encoders over 3 040 mm
measuring length use graduated steel tape and image
captured through diffused light as a measuring principle.
The reading system consists of an LED as a light source, a
mesh to make the image and a monolithic photo detector
element in the plane of the image specially designed and
patented by Fagor Automation.
Enclosed design
The robust aluminum profile encasing the graduated glass
provides the primary protection. The sealing lips provides
protection against contaminants and liquids as the reader
head travels along the profile. The reader head movement
along the graduated glass provides a perfectly balanced
system accurately capturing the machine movement. The
reader heard travels on precision bearings with minimum
contact with the profile hence minimizing the friction.
The optional air inlet at both ends of the encoder and at the
reader head provides increased protection levels against
contaminants and liquids.
Graduated glass encoder
LED’s Graduated glassGrid
Incremental graduation
Graduated steel encoder
Graduated steel Grid
Reference marks
Receiving photo-diodes
LED’s
Types of incremental encoders
• Linear encoder: Ideal for milling, grinding, lathe and
boring mill applications requiring federates of up to
120 m/min and vibrations of up to 20 g.
• Angular encoder: Used as an angular movement sensor
on machines/devices requiring high resolution and
accuracy. Fagor Angular encoders offer from 18 000 to
360 000 pulses/turn and accuracy levels of
±
and
2” depending on the model.
• Rotary encoder: Used as a measuring sensor for rotary
movements, angular speeds and also linear movement
when connected to a mechanical device like ball screw.
They are also used on various types of machine tools and
robotic applications.
±
±
5”,
2.5”
Incremental graduation
Graduated glass disk
Receiving photo-diodes
Reference marks
Receiving photo-diodes
Grid
Flat convex lens
LED
32
Graduated glass disk
Reference marks
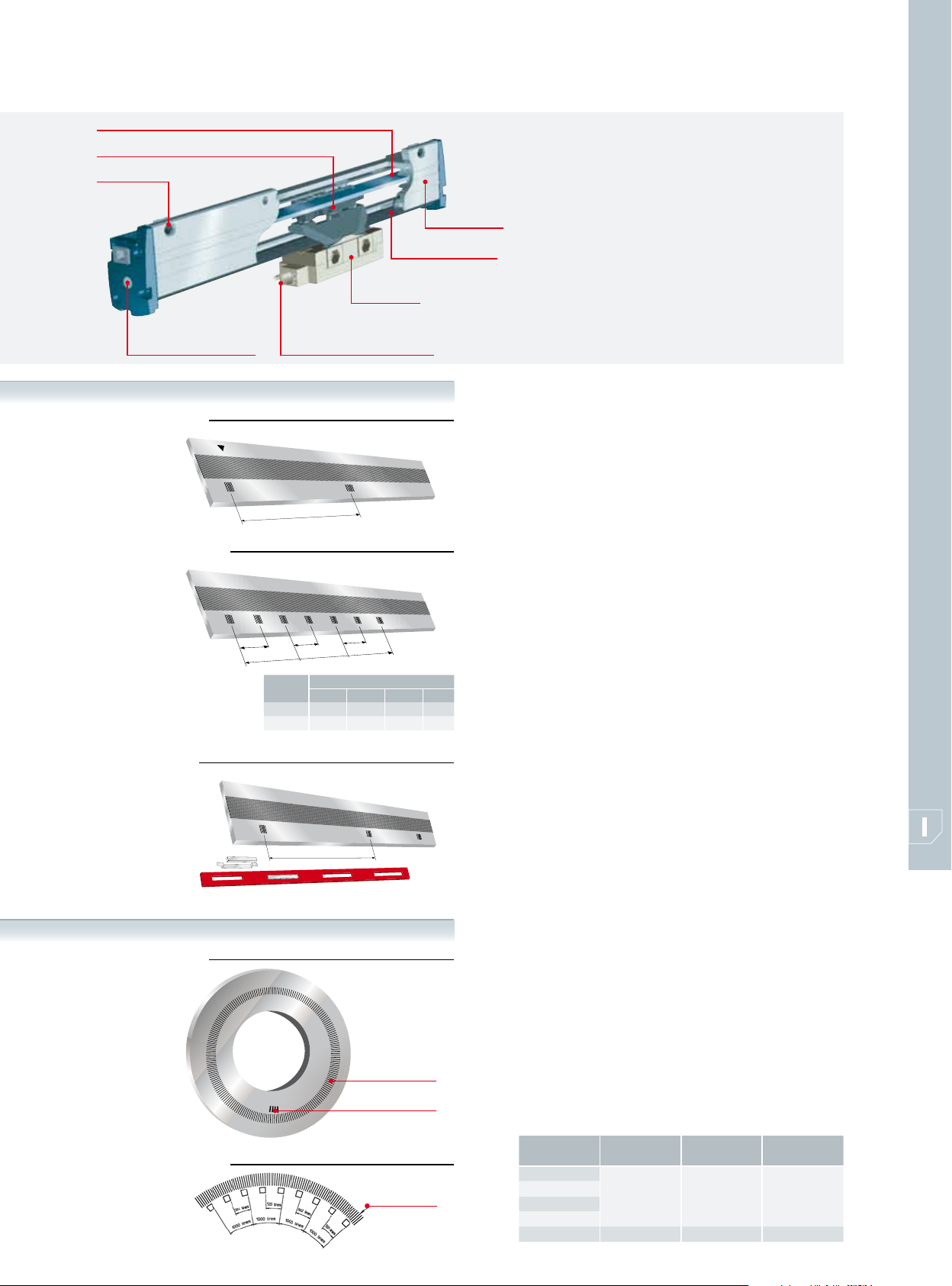
Graduated glass /steel tape
Cursor
Thermal Determined Mounting System
TM
(TDMS
)
Aluminum profile
Sealing lips
Reader head
Air intake at both ends
Incremental
Distance-coded
Selectable
Air intake on the reader head
Linear encoder
50
a
b
d
Series
L 40.04 40.08 40.12 80
G and S 10.02 10.04 10.06 20
c
d
d
Distances
a b c d
50
Reference signals (I0)
It is a reference signal etched on a graduation and when
scanned by the measuring system generates a pulse.
Reference marks are used to validate and restore the
machine zero position specially after turning on the machine
power.
Fagor Automation encoders have three types of reference
marks
I
:
0
• Incremental: The reference signal obtained is
synchronized with the feedback signals to ensure perfect
measuring repeatability.
Linear: One every 50 mm of travel.
Angular and rotary: One signal per turn
• Distance-coded: Both on linear and angular encoders
each distance coded reference signal is graduated in a non
linear way based on the predefined mathematical function.
The machine position value can be restored by moving
through two consecutive reference signals. The machine
movement needed to know the real position is always
very small and this is a very useful feature for large travel
machines.
• Selectable: With selectable linear encoders the customer
can select one or more reference points and ignore the
rest by simply inserting a magnet at the selected point or
points.
Incremental
Distance-coded
Angular encoder
etching
reference signals
reference signals
Series
H-D90
S-D90
S-D170
H-D200
H-D200 36
Nr. of
lines
18
000 36 20º
000 72 10º
Nr. of
references
Angle
33