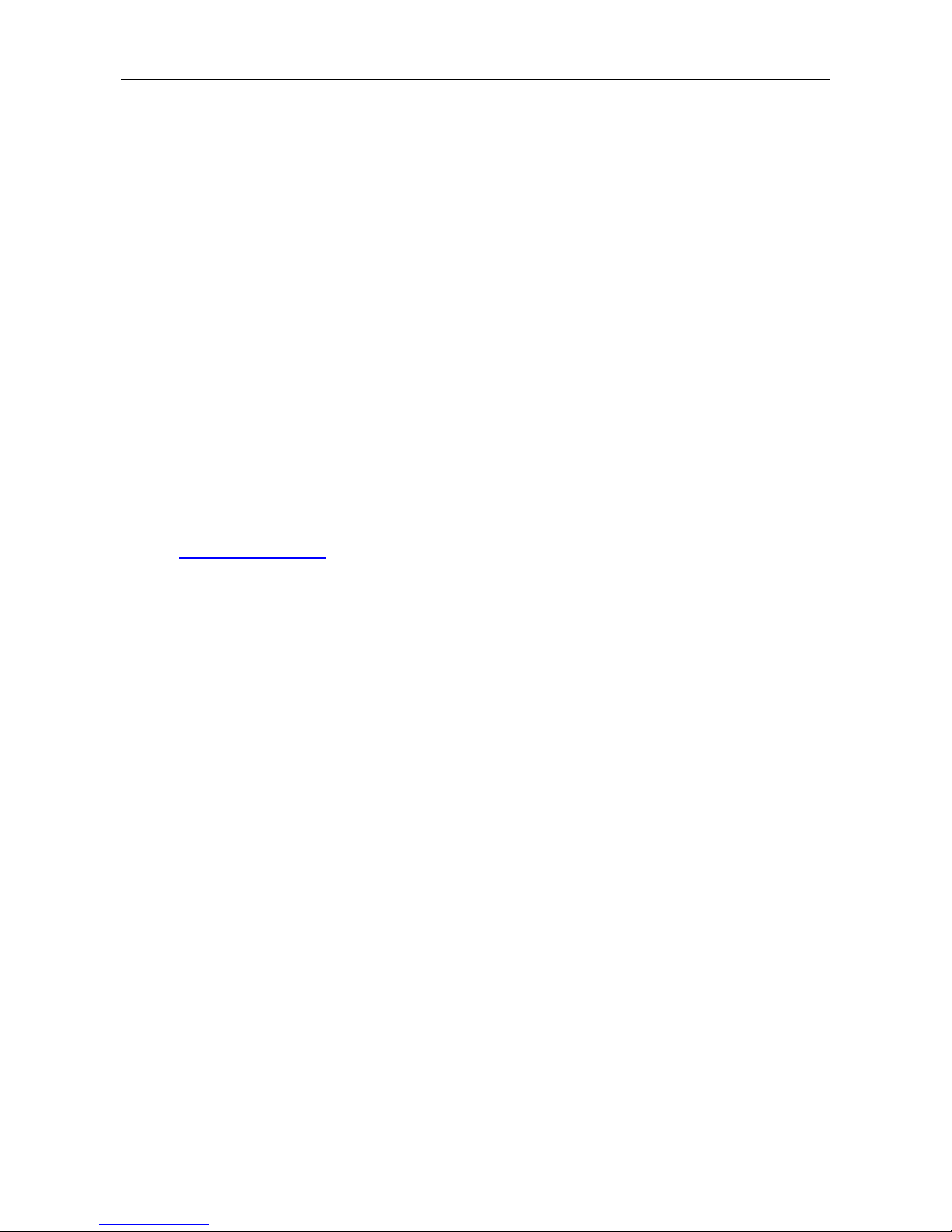
About this Manual
This service manual was written expressly for
Exmark service technicians. Exmark Mfg. Co. Inc.
has made every effort to make the information in
this manual complete and correct. Basic shop safety
knowledge and mechanical/electrical skills are
assumed. The Table of Contents lists the systems
and the related topics covered in this manual. An
electronic version of this service manual is available
on the Exmark Dealer Extranet. We are hopeful that
you will find this manual a valuable addition to your
service shop. If you have any questions or
comments regarding this manual, please contact us
at the following address:
Exmark Mfg. Co. Inc.
2101 Ashland Ave.
Beatrice, NE 68357
Customer Service All Call: 402-223-6375
e-mail - service@exmark.com
NOTES:
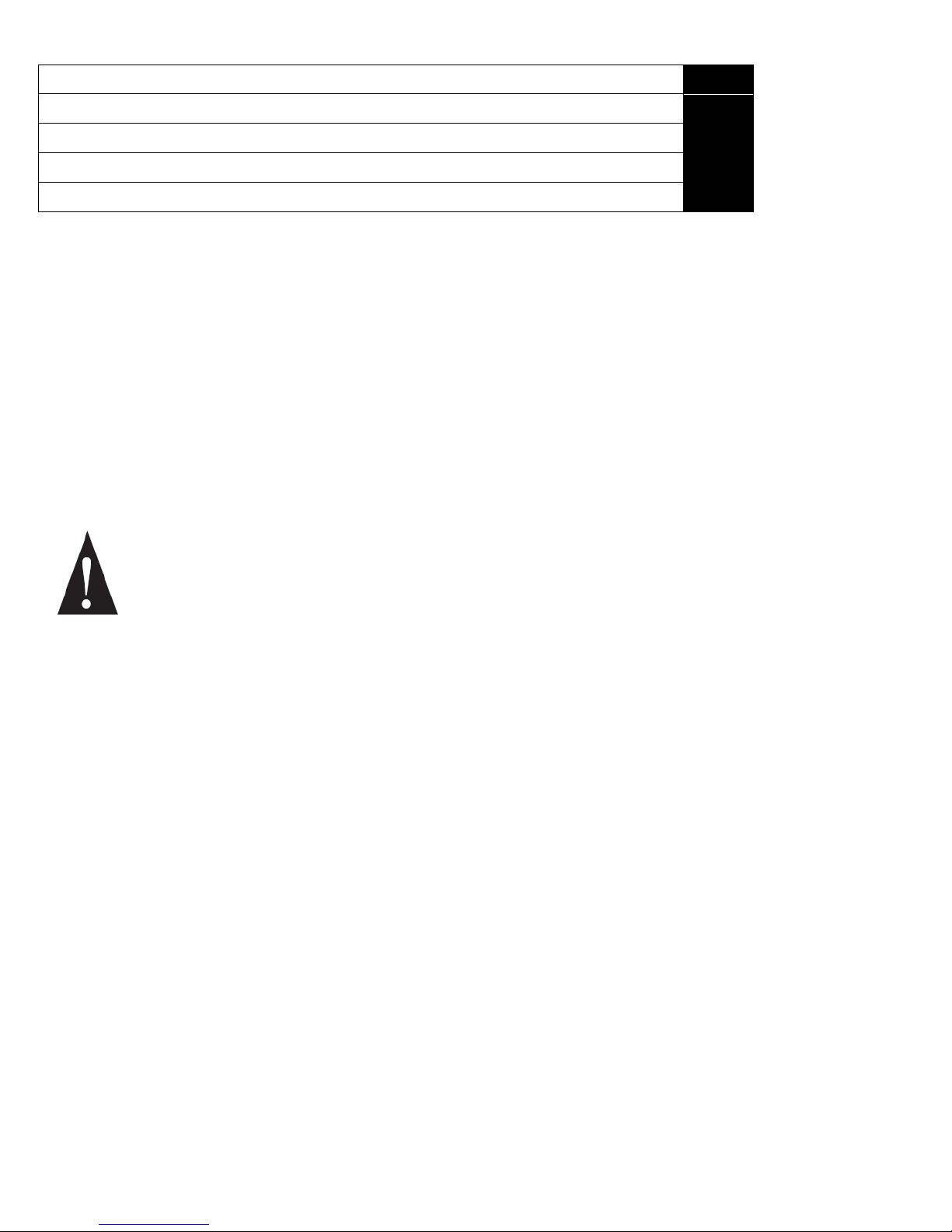
Chapter 1 – General Service Information
Chapter 2 - Specifications
Chapter 3 - Engine Service and Maintenance
Chapter 4 – Engine Disassembly and Service
– General Service Information
Safety
Safety Precautions
Service Rules
Engine Model / Serial Number Location
Torque Values
Engine Specifications
General Torque Specifications
Safety
Safety Information
Chapter 1
This symbol means WARNING or PERSONAL SAFETY INSTRUCTION – read the instruction because it has to do with
your safety. Failure to comply with the instruction may result in personal injury or even death.
This manual is intended as a service and repair manual only. The safety instructions provided herein are for
troubleshooting, service, and repair of the Toro engine. The Toro operator’s manual contains safety information and
operating tips for safe operating practices.
Avoid Unexpected Engine Start - Turn off engine and disconnect the spark plug before servicing engine.
Avoid Lacerations and Amputations - Stay clear of all moving parts while the engine is running.
Avoid Burns - Do not touch the engine, muffler, or other components which may increase in temperature during
operation, while the unit is running or shortly after it has been running.
Avoid Fires and Explosions - Avoid spilling fuel and never smoke while working with any type of fuel or lubricant. Wipe
up any spilled fuel or oil immediately. Never remove the fuel cap or add fuel when the engine is running. Always use
approved, labeled containers for storing or transporting fuel and lubricants.
Avoid Asphyxiation - Never operate an engine in a confined area without proper ventilation.
Avoid Injury From Batteries - Battery acid is poisonous and can cause burns. Avoid contact with skin, eyes, and
clothing. Battery gases can explode. Keep cigarettes, sparks, and flames away from the battery.
Avoid Injury Due To Inferior Parts - Use only original equipment parts to ensure that important safety criteria are met.
Avoid Injury To Bystanders - Always clear the area of bystanders before starting or testing power equipment.
Avoid Injury Due To Projectiles - Always clear the area of sticks, rocks, or any other debris that could be picked up and
thrown by the power equipment.
Avoid Modifications - Never alter or modify any part unless it is a factory approved procedure.
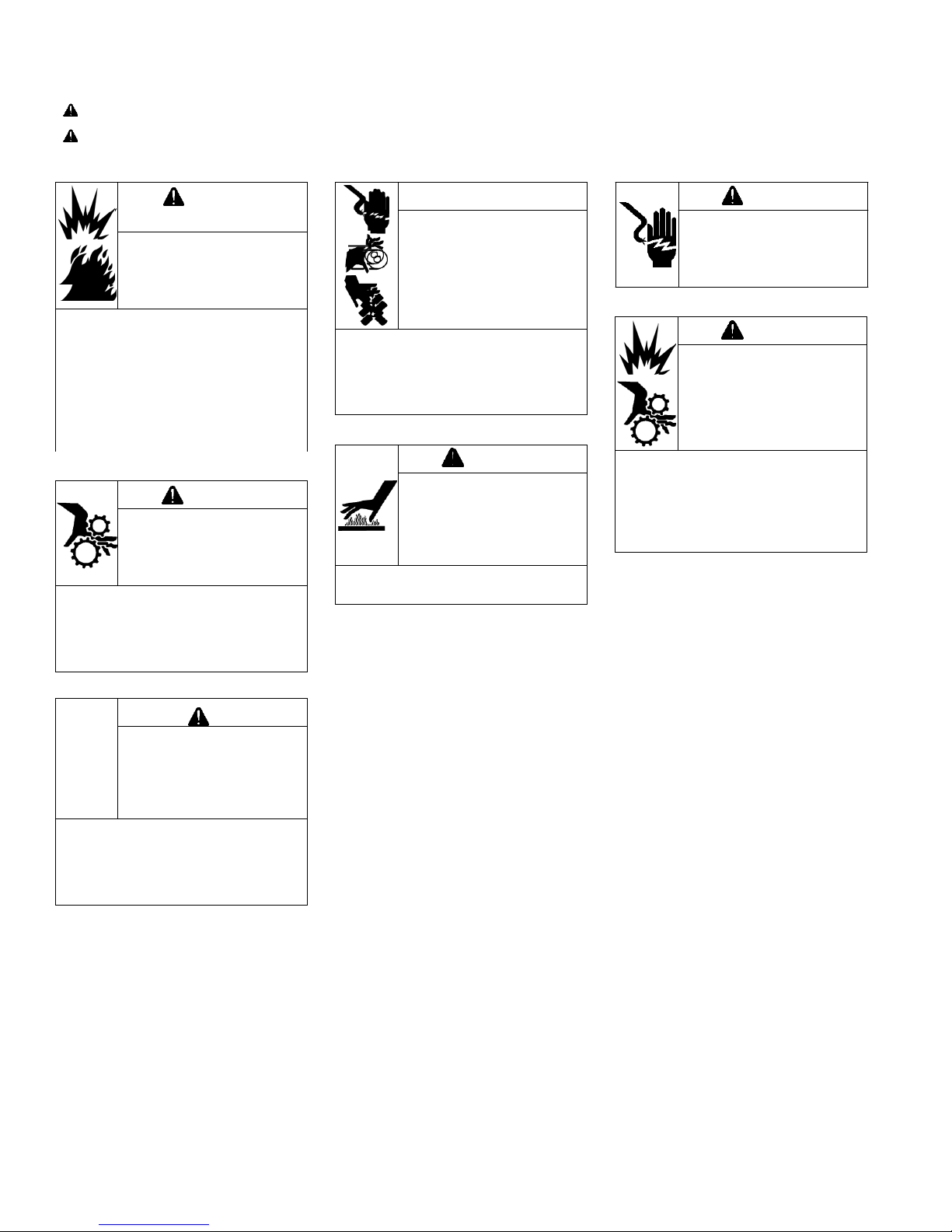
Explosive Fuel can cause
fires and severe burns.
Do not fill fuel tank while
engine is hot or running.
Gasoline is extremely flammable
and its vapors can explode if
ignited. Store gasoline only in
approved containers, in well
ventilated, unoccupied buildings,
away from sparks or flames.
Spilled fuel could ignite if it comes
in contact with hot parts or sparks
from ignition. Never use gasoline
Accidental Starts can
cause severe injury or
death.
Disconnect and ground
spark plug lead(s) before
servicing.
Before working on engine or
equipment, disable engine as
follows: 1) Disconnect spark plug
lead(s). 2) Disconnect negative (–)
battery cable from battery.
Damaging Crankshaft
and Flywheel can cause
personal injury.
Using improper procedures can
lead to broken fragments. Broken
fragments could be thrown from
engine. Always observe and use
precautions and procedures when
installing flywheel.
Hot Parts can cause
severe burns.
Do not touch engine
while operating or just
after stopping.
Never operate engine with heat
shields or guards removed.
Rotating Parts can cause
severe injury.
Stay away while engine
is in operation.
Keep hands, feet, hair, and
clothing away from all moving
parts to prevent injury. Never
operate engine with covers,
shrouds, or guards removed.
Carbon Monoxide can
cause severe nausea,
fainting or death.
Avoid inhaling exhaust
fumes.
Engine exhaust gases contain
poisonous carbon monoxide.
Carbon monoxide is odorless,
colorless, and can cause death if
inhaled.
SAFETY PRECAUTIONS
WARNING: A hazard that could result in death, serious injury, or substantial property damage.
CAUTION: A hazard that could result in minor personal injury or property damage.
NOTE: is used to notify people of important installation, operation, or maintenance information.
CAUTION
Electrical Shock can
cause injury.
Do not touch wires while
engine is running.
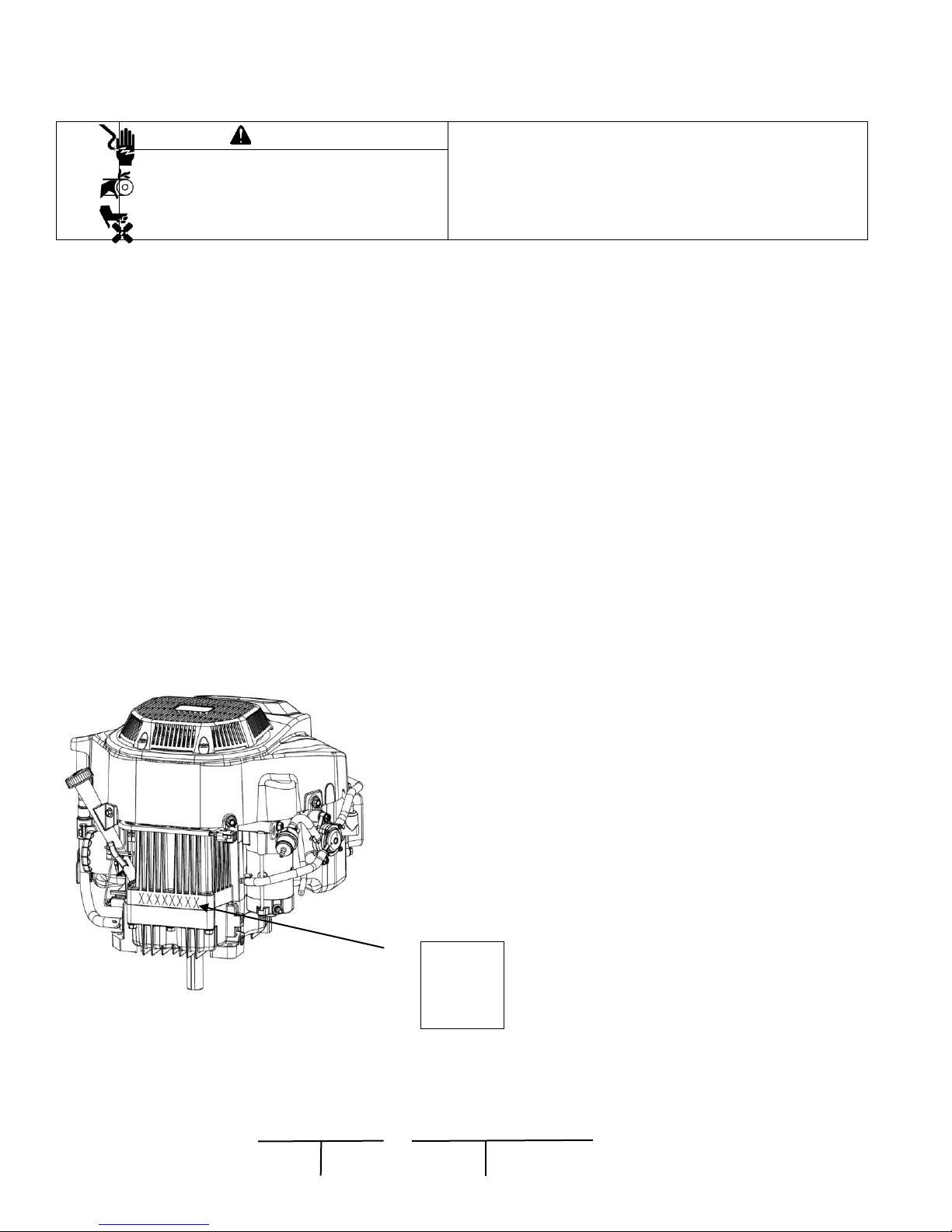
Before working on engine or equipment, disable engine as
follows: 1) Disconnect spark plug lead(s). 2) Disconnect
negative (–) battery cable from battery.
Accidental Starts can cause severe injury or
death.
Disconnect and ground spark plug lead(s)
before servicing.
Engine
Model
& Serial
Number
1. Only use genuine Exmark parts and lubrication products.
2. Always install new gaskets, O-rings and seals when assembling engine.
3. Always torque fasteners to specification and in sequence.
4. Always lubricate friction components with clean engine oil or engine assembly lube
when assembling engine.
MAINTENANCE INSTRUCTIONS
Normal maintenance, replacement or repair of emission control devices and systems may be performed by any repair
establishment or individual; however, warranty repairs must be performed by an authorized Exmark dealer.
Service Rules
Engine Model / Serial Number Location
The engine model and serial number are stamped into the block, there will also be a label attached to
a new engine with this information on it as well.
XXX-XXXX XXXXXXXXXXX
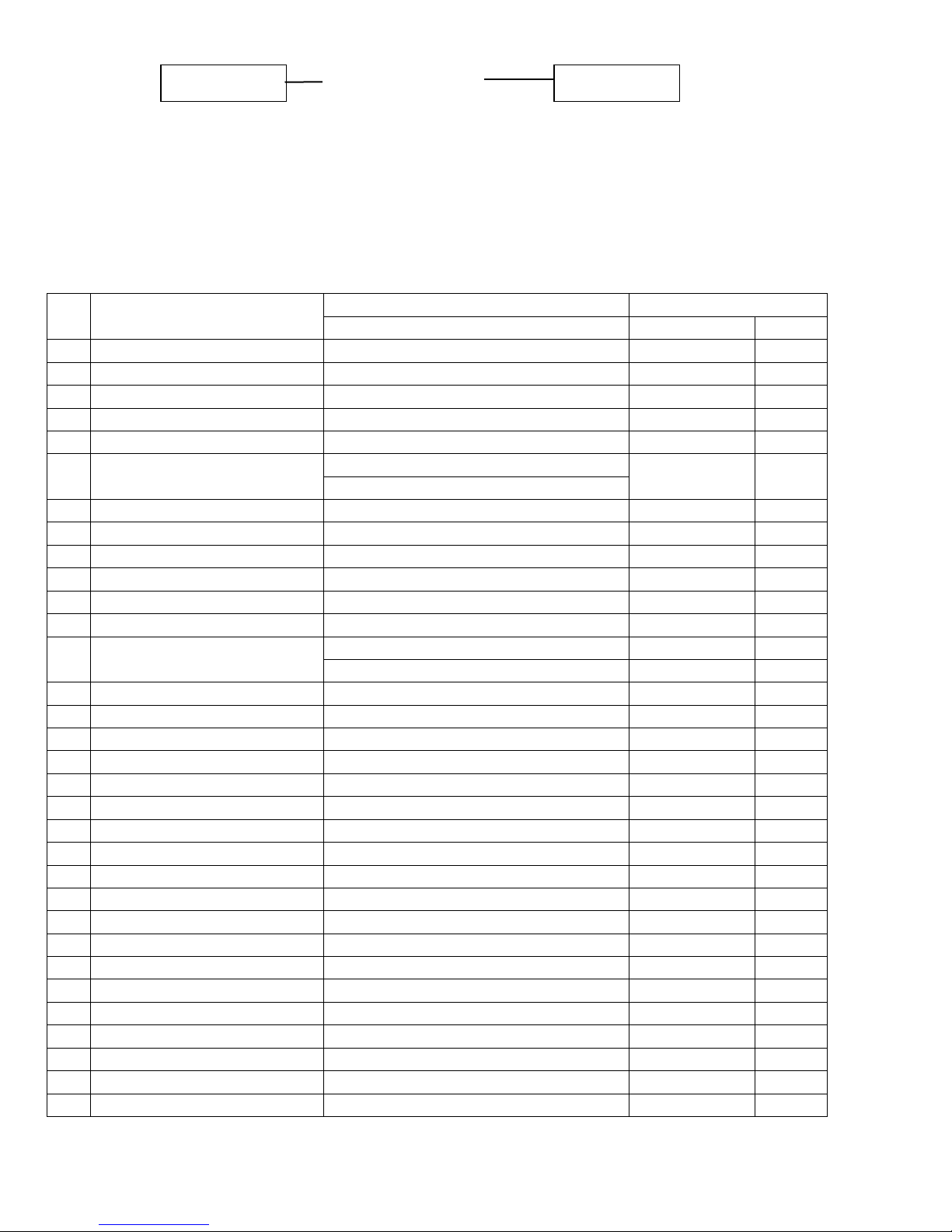
Cylinder Head
Hex Flange Bolt M10×1.25×70
Hex Flange Bolt M10×1.25×50
Push Rod Location Limit Plate
Valve Lash Inspection(Q1)
Inlet Pipe
Hex Flange Bolt M6×35
Hex Flange Step Bolt 6×21.8-8×10.8
Hex Flange Step Bolt 6×16.8-8×5.8
Screw Inner Six Angle M6×25
1.1 Torque values
Note: For unspecified bolts and nuts listed, refer to the table of standard torque values.
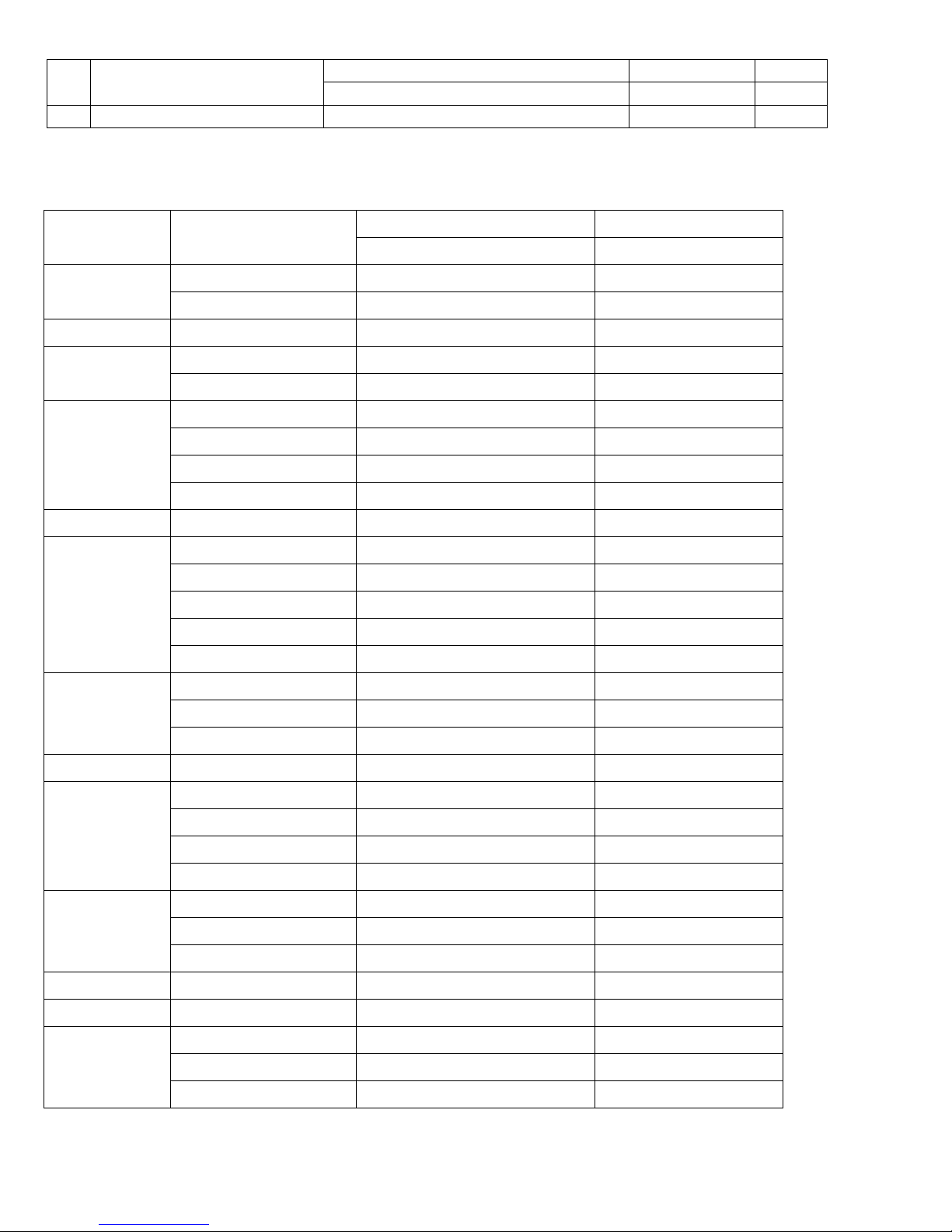
Cylinder Head
Stud Bolt M8×39
Sleeve Taper / Out of Round
3.0315”-3.0319” (77 – 77.01 mm)
3.0301-3.0305” (76.965-76.975 mm)
0.00098-0.0017” (0.025-0.045 mm)
Piston pin bore inside diameter
0.66937- 0.66961” (17.002-17.008 mm)
0..00016-0.00063” (0.004-0.016 mm)
0.6689-0.6692” (16.992-16.998 mm)
Ring to Groove (Top and Middle
0.0008-0.0024” (0.02-0.06 mm)
End gap (top and middle )
0.0079-0.01578” (0.20-0.40 mm)
0.0382-0.0390” (0.97-0.99 mm)
0.0460-0.0469” (1.17-1.19 mm)
0.0650-0.0728” (1.65-1.85 mm)
Small end inside diameter
0.6695-0.670” (17.006-17.017 mm)
1.575-1.576” (40.015-40.025 mm)
0.0010-0.0031” (0.024-0.079 mm)
Connecting Rod Journal Diameter
1.5735-1.5744” (39.966-39.991 mm)
0.004-0.006” (0.10-0.15 mm)
Clearance(cold) (exhaust)
0.006-0.008” (0.15-0.20 mm)
0.258-0.259” (6.565-6.58 mm)
0.257-0.258” (6.545-6.56 mm)
Inside diameter (intake, exhaust)
0.259-0.260” (6.6-6.615 mm)
Stem to guide clearance (intake)
0.0008-0.0020” (0.02-0.05 mm)
Stem to guide clearance exhaust)
0.0016-0.0027” (0.04-0.07 mm)
0.0027-0.0031” (0.7-0.8 mm)
1.55-1.60” (39.5-40.5 mm)
1.15-1.18” (29.95-30.05 mm)
1.15-1.18” (29.95-30.05 mm)
Outside diameter (bearing)
0.628-0.629” (15.966-15.984 mm)
1.2 Engine Specifications
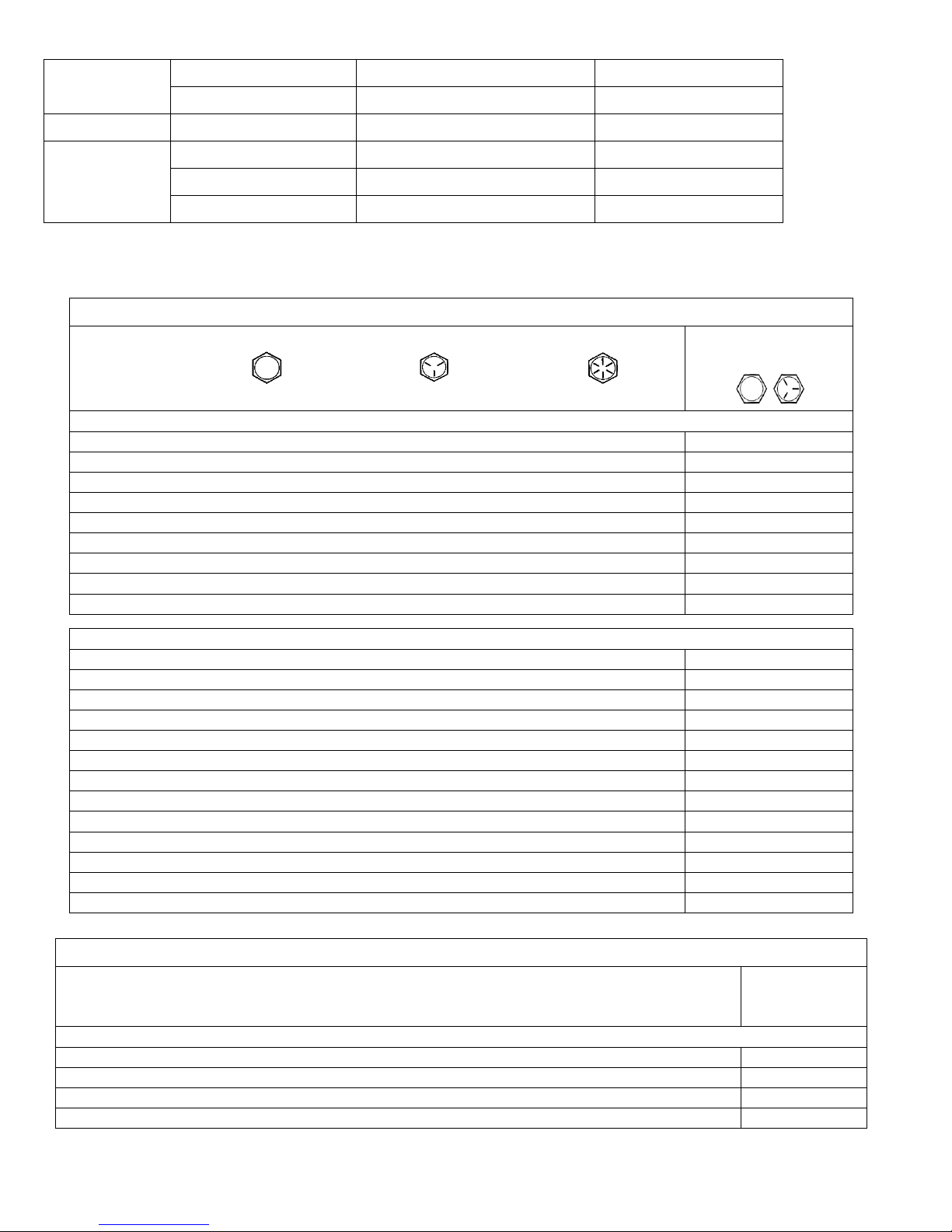
0.629-0.630” (16-16.018 mm)
1.575-1.576” (40.009-40.025 mm)
0.0027-0.0031” (0.7-0.8 mm)
0.015-0.016” (0.4±0.1 mm)
English Fastener Torque Recommendations for Standard Applications
Bolts, Screws, Nuts and Fasteners Assembled Into Cast Iron or Steel
Size Grade 2 Grade 5 Grade 8
Grade 2 or 5 Fasteners
Into Aluminum
Tightening Torque: N·m (in. lb.) ± 20%
10-24 3.6 (32) 4.5 (40) —
10-32 3.6 (32) 4.5 (40) —
1/4-20 7.9 (70) 13.0 (115) 18.7 (165)
1/4-28 9.6 (85) 15.8 (140) 22.6 (200)
5/16-18 17.0 (150) 28.3 (250) 39.6 (350)
5/16-24 18.7 (165) 30.5 (270) —
Tightening Torque: N·m (ft. lb.) ± 20%
3/8-16 — 47.5 (35) 67.8 (50)
3/8-24 — 54.2 (40) 81.4 (60)
7/16-14 47.5 (35) 74.6 (55) 108.5 (80)
7/16-20 61.0 (45) 101.7 (75) 142.5 (105)
1/2-13 67.8 (50) 108.5 (80) 155.9 (115)
1/2-20 94.9 (70) 142.4 (105) 223.7 (165)
9/16-12 101.7 (75) 169.5 (125) 237.3 (175)
9/16-18 135.6 (100) 223.7 (165) 311.9 (230)
5/8-11 149.5 (110) 244.1 (180) 352.6 (260)
5/8-18 189.8 (140) 311.9 (230) 447.5 (330)
3/4-10 199.3 (147) 332.2 (245) 474.6 (350)
3/4-16 271.2 (200) 440.7 (325) 637.3 (470)
Metric Fastener Torque Recommendations for Standard Applications
Property Class
Size
4.8 5.8
8.8 10.9 12.9
Noncritical
Fasteners
Into Aluminum
Tightening Torque: N·m (in. lb.) ± 10%
M4 1.2 (11) 1.7 (15) 2.9 (26) 4.1 (36) 5.0 (44)
M5 2.5 (22) 3.2 (28) 5.8 (51) 8.1 (72) 9.7 (86)
M6 4.3 (38) 5.7 (50) 9.9 (88) 14.0 (124) 16.5 (146)
M8 10.5 (93) 13.6 (120) 24.4 (216) 33.9 (300) 40.7 (360)
GENERAL TORQUE VALUES
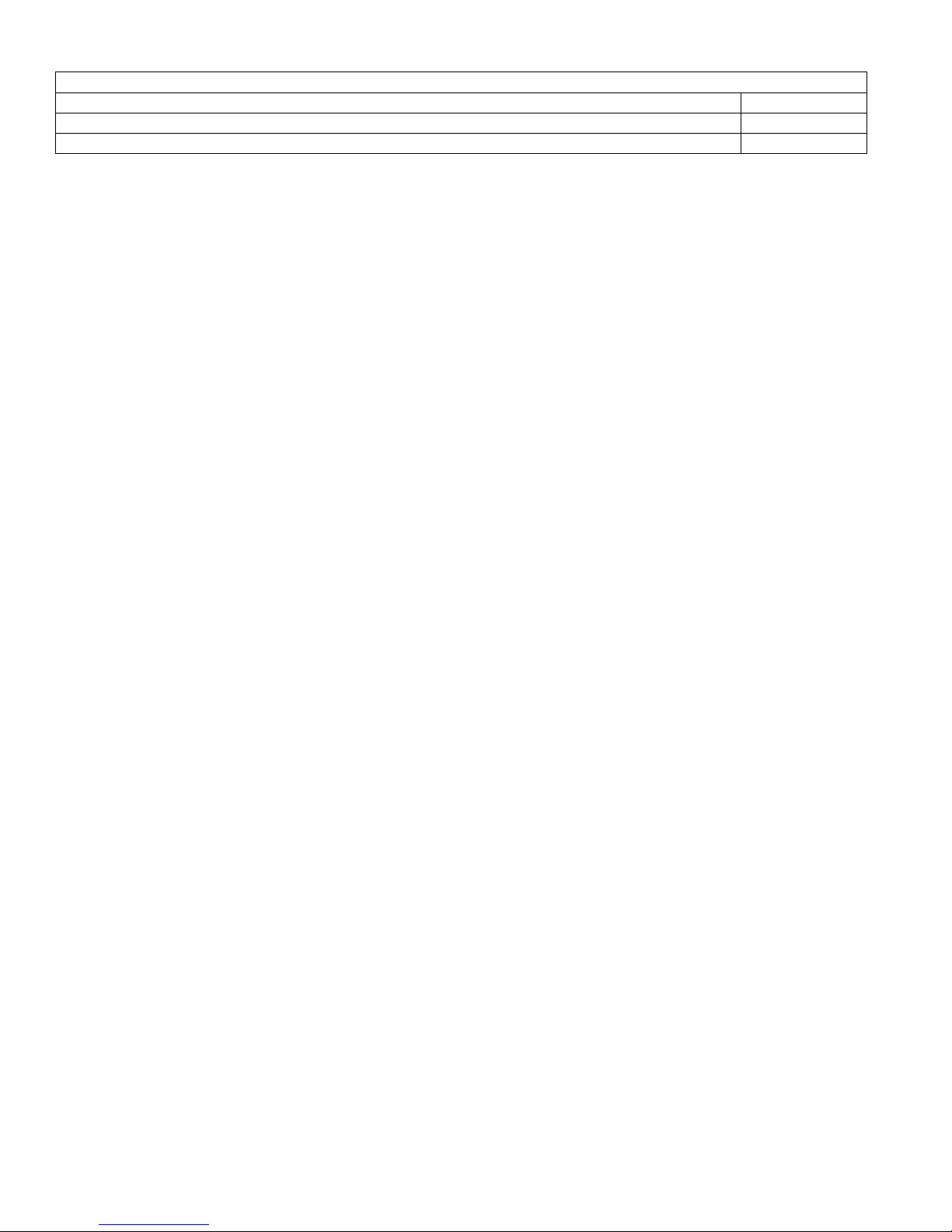
Tightening Torque: N·m (ft. lb.) ± 10%
M10 21.7 (16) 27.1 (20) 47.5 (35) 66.4 (49) 81.4 (60)
M12 36.6 (27) 47.5 (35) 82.7 (61) 116.6 (86) 139.7 (103)
M14 58.3 (43) 76.4 (56) 131.5 (97) 184.4 (136) 219.7 (162)
Torque Conversions
N·m = in. lb. x 0.113 in. lb. = N·m x 8.85
N·m = ft. lb. x 1.356 ft. lb. = N·m x 0.737

2-1
2. Specifications
2.1 Specifications--------------------------------------------------2—2
2.2 Dimensional drawings----------------------------------------2—2
2.1 Specifications
2.2 Dimensional Drawings in Millimeters
OHV, V-twin –Air Cooled 4-Stroke
43.20 Cubic Inches (708 cc)
Counter Clockwise(from P.T.O. side)
Intake valve:0.004” - 0.006” , Exhaust valve:0.006” – 0.008”
0.0027” - 0.0031” (0.7~0.8mm)
Transistorized Magneto Ignition
Unleaded gasoline, minimum 87 Octane
18.44” x 18.61” x 15.06” (468.4×472.7×382.7 mm)

3-1
3 Maintenance
3.1 Maintenance schedule-----------------------------------------3-2
3.2 Engine oil ------------------------------------------------------ 3-2
3.3 Air cleaner ------------------------------------------------------3-3
3.4 Spark plug ------------------------------------------------------3-4
3.5 Valve clearance ------------------------------------------------3-4
3.6 Carburetor ----------------------------------------------------- 3-5
3.7 Governor -----------------------------------------------------3-5
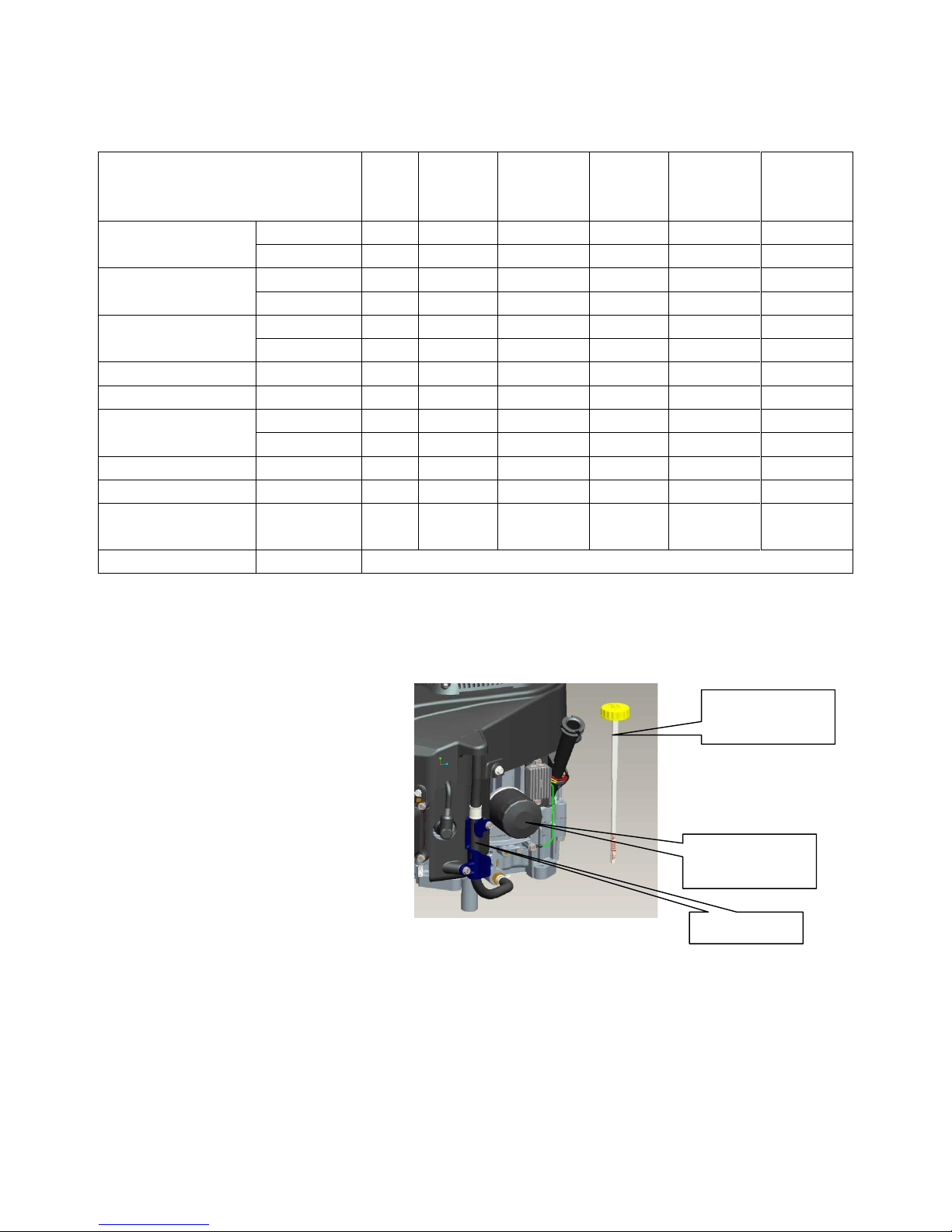
3-2
3.1 Maintenance Schedule
(1)Service more frequently when used in dusty condition areas.
(2)These items are to be maintained by designated dealers unless the user has special tools
and skills for maintenance.
3.2 Engine Oil
Drain the oil while the engine is warm to
assure rapid and complete draining.
1. Clean the area around the oil filler
cap/dipstick. Remove
the oil filler cap/dipstick.
2. Drain the engine oil into a suitable
container using one of the following
methods.
Oil Drain:
a. Unwind the tube from the cleat
b. Pull hose down from the fitting
c. Allow the oil to drain into a suitable container.
d. Replace hose fully
Every 3
months or
25 hours
Every 6
months or
50 hours
Every 2
years or
200 hours
Air cleaner paper
element
Remove engine
shroud and clean
Every 3 years (Replace sooner if necessary) (2)