
KDZ
RAILWAY DIESEL STARTING
BATTERIES
INSTALLATION AND OPERATING INSTRUCTIONS
CAUTION - READ THE ENTIRE INSTALLATION AND OPERATING INSTRUCTIONS BEFORE PLACING BATTERIES IN SERVICE.
1 . SAFETY
1.1 Follow your company’s Safety Instructions
when working with or near diesel starting
batteries. Observe the caution label affixed
to the battery. Thoroughly familiarize yourself
with industry and government guidelines
(OSHA, ANSI) for charging, handling and
maintaining diesel batteries.
1.2 Assign battery and charger care to properly
trained personnel.
1.3 This battery contains sulfuric acid. Avoid
contact with skin, eyes, or clothing. Wear
rubber apron, gloves, boots and goggles or
face shield when handling, checking, filling,
charging or repairing batteries.
1.4 Keep water readily available for flushing
spilled electrolyte from eyes or skin. Use
plain water only and obtain medical attention
immediately. Special deluge showers and
eye wash basins are required.
1.5 Batteries produce hydrogen during charge.
Keep open flames away. Do not check
electrolyte level with a cigarette lighter or
match. Use a flashlight or permanent lights.
Do not smoke or create sparks.
1.6 Lift batteries with a hoist, crane, lift truck,
or similar equipment. Move batteries on
trucks, conveyors or rollers. Be sure to place
a rubber mat or similar insulating material
across tops of batteries without covers when
handling. Make sure equipment is of ample
strength and properly installed.
CAUTION: Do not use chain or wire rope slings.
1.7 Never lay metal tools, such as wrenches or
other material on top of a battery.
1.8 Disconnect the battery from the locomotive
when performing maintenance and repair
on the motor or electrical system.
1.9 Open or “break” the battery circuit before
attempting repairs to terminal connections.
1.10 Apply a strong neutralizer, like baking soda,
when acid is spilled on the floor. Check local
regulations regarding disposal of neutralized
waste.
2. RECEIVING BATTERIES
Immediately upon receipt of shipment, examine
the outside of the packing for signs of rough
handling before accepting battery from carrier.
Wet spots on the shipping pallet may be an
indication of leaking jars broken in shipment.
If there is evident damage, the receipt should be
signed and both copies (carrier’s and receiving
copies) marked “Shipment Received Damaged”.
The carrier should be called immediately and
asked to make a “Carrier’s Inspection for Damage
Report”.
If “concealed” damage is later detected, the carrier
should be called immediately and requested
to make a “Carrier’s Inspection for Concealed
Damage Report”. After inspection by the carrier,
arrangements should be made with the local
®
Industrial Power representative to have
GNB
the battery repaired before placing it in service.
CAUTION
Before placing a battery in service,
review and adhere to the Safety
Guidelines listed in Section 1.
3. INITIAL FRESHENING CHARGE
Remove the vent caps from each cell and check
to see that the electrolyte level is above the plates.
During shipment of the battery, low temperatures
and/or normal shock and vibration often results in
a drop in the electrolyte level. If the level is below
the plates, recheck it after three hours of charging.
If the level remains below the plates, add water
until the plates are covered. If it is obvious that
electrolyte has spilled out of any cells, replace
it with electrolyte of the same specific gravity as
found in the other cells of the battery.
Replace the vent caps and give the battery a
freshening charge of 3 to 6 hours or by continuing
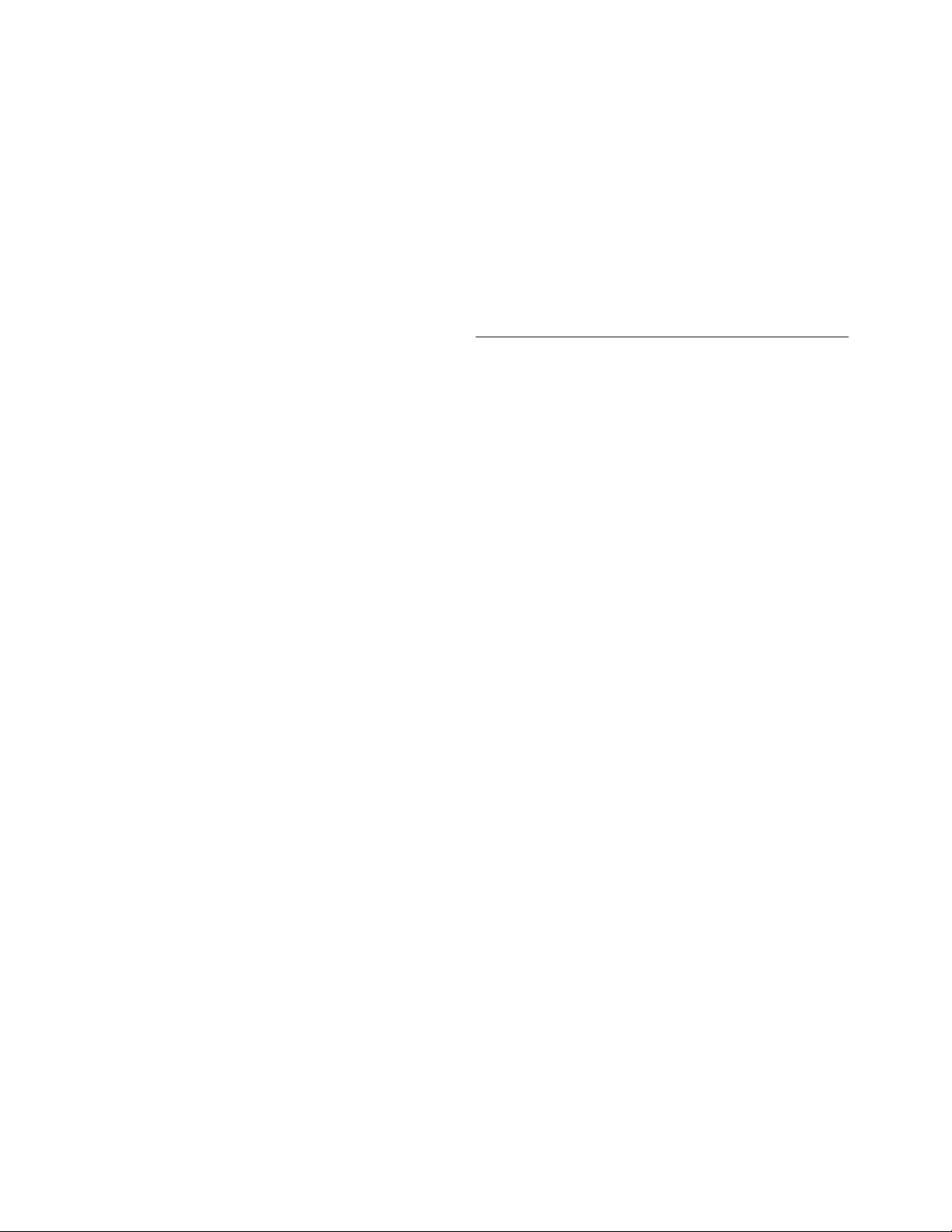
the charge until there is no increase in specific
gravity for three hydrometer readings taken at
one hour intervals. CONTINUE CHARGING
AND MAKE FINAL ADJUSTMENT OF THE
ELECTROLYTE LEVEL TOWARD THE END OF
THE CHARGE.
Upon completion of the freshening charge, the
normal fully charged specific gravity should be
1.245 to 1.255 at 77°F.
is indicated by decreasing electrolyte specific
gravities.
The correct operating or battery float voltage to
be set on the regulator is that which will maintain
the battery in a fully charged condition. This
correct setting depends on two factors—operating
temperature and locomotive work schedule. It is
recommended that voltage regulator adjustments
be made while the engine is at operating speeds.
4. INSTALLING BATTERY (BLOCKING)
Negligence in properly blocking a battery in the
compartment is apt to permit shifting and may
cause damage. All trays should be securely
blocked, but care should be taken to avoid
overtight wedging. Clearance of about 1/8" should
be left between the blocking and the battery trays.
5. TERMINAL CONNECTIONS
Make
in-lb. Inspect terminal connections regularly
and keep them clean and tight to 100 in-lb.
6. VOLTAGE REGULATOR
The battery is only one part of a total system,
all of the parts of which are inter-related and
interdependent. The battery simply stores energy
in a chemical form for use when the generating
system is not running. It is not a source of power
but merely a reservoir. The battery supplies power
for starting but, as soon as the engine is running,
the generating system must replace the power
withdrawn from the battery.
Input from the generating system to the battery is
controlled by the voltage regulator. It is important
to make sure that the regulator is known to be in
satisfactory operating condition and adjusted to
the correct operating voltage.
If the voltage regulator is not in good operating
condition or is adjusted to an incorrect operating
voltage, the battery will not function satisfactorily
because the charge it receives will be insufficient
(undercharged) or excessive (overcharged). In
severe cases of bad regulation and overcharging,
failure can take place within a year. Overcharge
is indicated by faster water loss than normal.
A bad regulator or one set too low can cause
undercharge—a condition which will literally
starve the battery to death. In this case, more
power is drawn out of the battery than is replaced.
As a result, the battery gradually runs down until
it is so low that it fails completely. Undercharge
original connections clean and tight to 100
Correct battery float voltage at different
environmental temperatures are as follows:
Float Voltage
Temperature (Volts/Cell)
Greater than 80°F 2.25-2.30
50°F to 80°F 2.30-2.33
Less than 50°F 2.33-2.38
The effect of locomotive work schedule on
the correct float voltage is determined with
experience. If a battery is used for starting
very frequently, float voltages should be set at
the higher end of the range indicated at the
appropriate temperature; similarly, for infrequent
battery usage, float voltages should be set at the
lower end of the range.
7. VENTILATION
As explained in Section 2, gases produced
from a charging battery are explosive! Clean all
ventilating openings to remove any collection of
dirt or dust that might prevent the free circulation
of air.
8. WATER ADDITION
All lead acid batteries, in the course of normal
operation, generate hydrogen and oxygen from
water in the electrolyte.
Gassing or water consumption in a battery
is a function of float voltage and operating
temperature. Excessive water consumption
indicates the voltage regulator setting is too high
and should be reduced. Normally, it should not
be necessary to add water to the battery more
than once every 30-180 days in the summer and
once every 60-180 days in the winter.
If the gravity reading shows a continual lowering,
or consistently remains 10 to 20 points below the
fully charged gravity, the voltage regulator is set
too low for the locomotive’s work schedule and
it should be increased to allow more charge. Do
not increase or decrease the voltage regulator
setting more than 1/2 volt at a time. Recheck