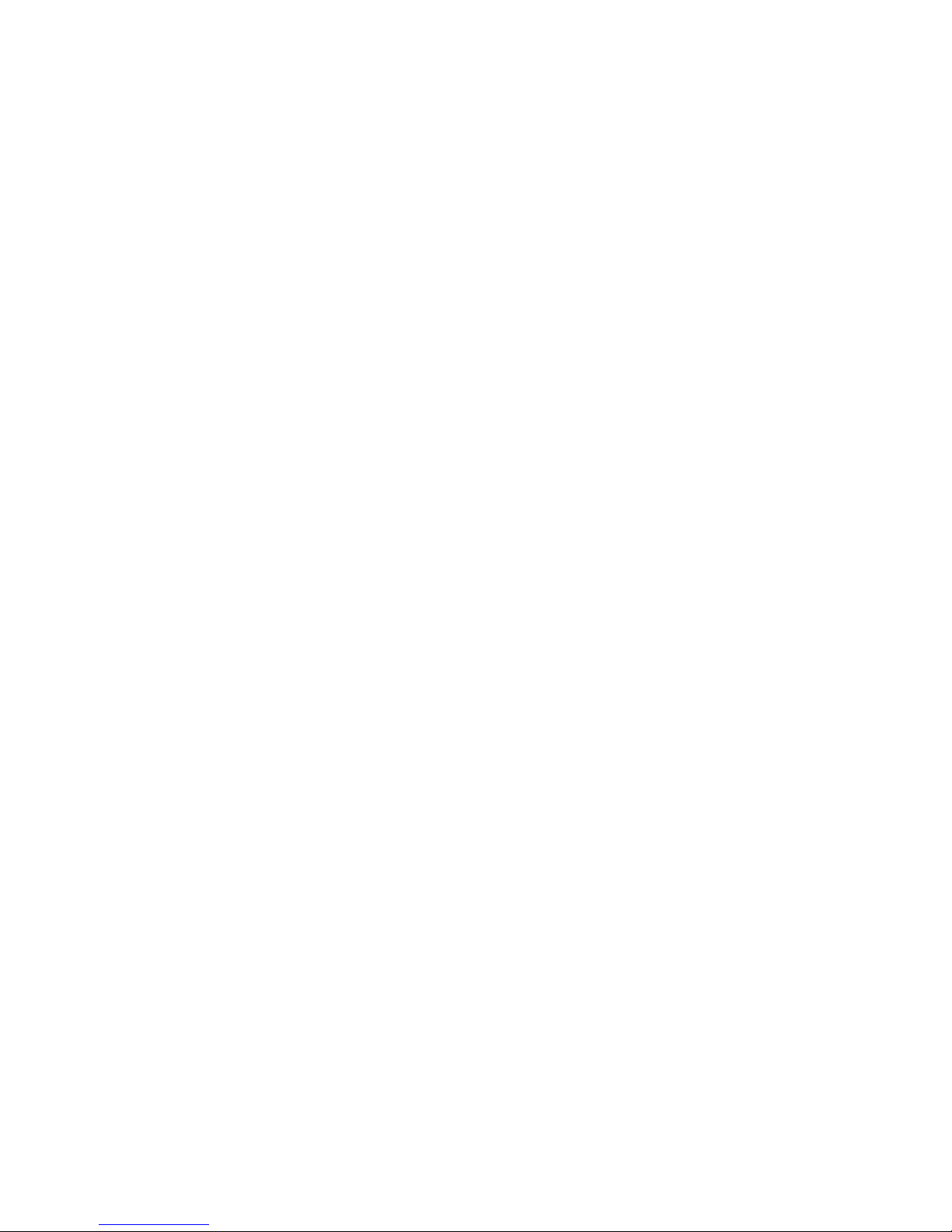
--
---_
- _
-
-=------
.-----.
.-
--
-.---
-------------
---------
-_.
__
..
_----
---
- -
.
_-
-"
.
__
. -"
'--'-'---'-
---
-
--
-===
----.
-
----
~----------
_.-._-------------_
- -
.-
--
--
--------
- '
~----
--
'--
.. -...
---'--
--
-----
._--_._--------
---.
-------
-----------------::...=-:.:..:.-~
---
--
- --
------
----
..
------------
----
----
.-
.... _ .. - .
.
-----------
-----
- . - _
...
---------------------
--
-.--
--
.----
...
_
-_
..
---_
-- .. _
--
.-
..
----
-
---
- --------
...
_----------_
_-----
---------_
--'---_.-----_
.---
-._----
..
--
----
.
----.----
-.-----
._-
- _.--_._-- -
---
--_
..•
--
..
---.--
---_
- -
-----
--
----
--
----------_.
..
~-
..
---
----_
-_.
---
---
---.-
...
------
--
-------
.
._.- -
---_.-
_-_
---
-------
..
_---
------
-.--
-_._-- --
...
--
--
-
==~
--------
------
_._---
-
~~:--===--=-~-
---
-
--------
---
- - -
...
==:~;~~,,;--_~_-
._---
------_
...
_------._---------------_.-
-----
---
_.---_.-
-------
-
--
-_.-
--=------------
--
-----_._----_.
--:;:;--
:.
~~-~
--=---
..
__
._--
----
--.-
..
--_.
---
-_._
.-
-
-=~---
~--:
~~
-~
:
-=~:
.
._
-- --...
--
.-
-----------
-
==-~~~=~-~:
-~---
.-
-
-------
- --.- ----
.
:-~
.:
--
~~-;:.
-=
~
:~
..
~=-'~cc~;-;.
~~
.
-~
=-:
-
~-=---
----------
. _
___ ___
-
-'
--
-
---
------_.-
-'-
==~----=--=--=----=----
=-~=~-----
--
~-====~~~~
..-
---
----------_
-
:;;
~~
---
---..
--
_.
_-_
-
·
---:.
_:_
-:..:=--=~
___
..
_.
__
. _
______ . _________
:-:--~--~
....
_.
--
-
~-==-~-~~=-
---
.
...
.'. -
-----t-
--
. - -
------_.-
- - .-
_--' .
---
--
..
~
...
~
--
- -
----
.---
.
-
-
..
_---------
. -
.-
--
.-
~-
J;VIN
~.
-
J 0 H N
---.-
-:..
.--
-_.--
"
1
-.~
..
_
1--1'~~""7
------
-~
=
--
--
.---._"
_-
"-_. - -
RU
."
..
_-
...
--=:--~
.-:---.
===--
- --
-
_u------
sat..
...
------
.-._-
---------
------
.
---
DE&.
I~
- .
-------
.
..
-
_.
=--=-~-=-
---
.--
------------
--
-----.---____
------ -
I
-
..........
--:-.:.~:~--.-
------
--
_
------
-
--
------ -
..
q
---
SNOWMOBILE
DIVISION/OUTBOARD
OUTBOARD
MARINE
MARINE
ervice
35
40
50
CORPORATION, 3031 NORTH 114th STREET,
CORPORATION OF
H P MODELS:
HP MODELS:
HP MODELS:
CANADA
LTD., PETERBOROUGH,
manual
E-134-A,
E-144-A ,
E-164-A,
MILWAUKEE,
CANADA.
J-134
-A
J-144-A
J-164-A
WISCONSIN 53222
PART
NO.
406226
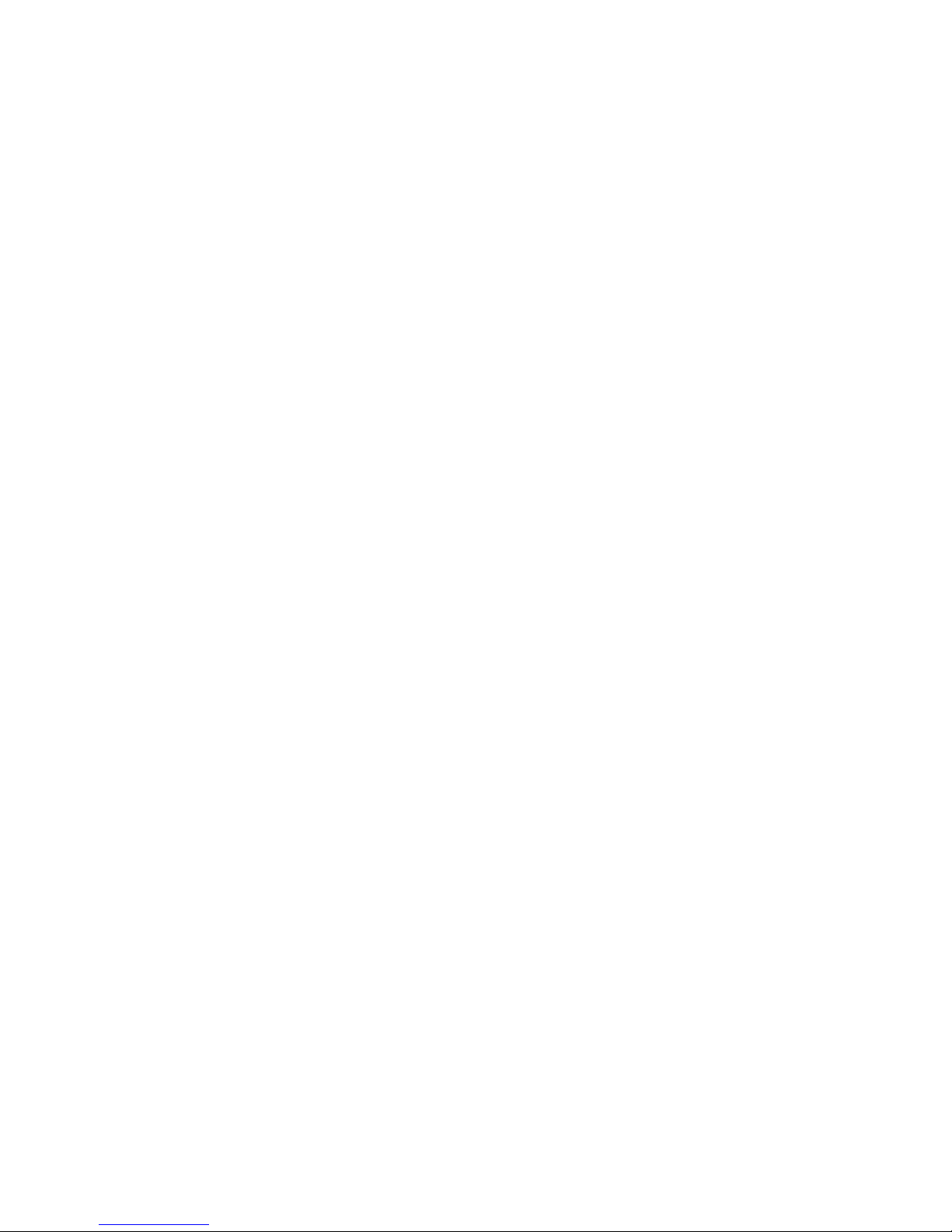
T
ABLE
OF
CONTENTS
(
Fuel
Recommendations
SECTION 1 INTRODUCTION AND
SECTION 2 SPECIFICATIONS
SECTION 3
SECTION 4 TROUBLE
Controls
Specifications
Torque
Snowmobile
GENERAL
Two
Carburetion
Ignition
Lighting
Power
Description
Trouble
. . . . . . . . . . . . . . . . . . . . . . . . . . . . .
Specifications.
Special
SNOWMOBILE INFORMATION
Stroke
Primary
Neutral
Secondary
Starting
Starting -Manual
Starting -Electric
Running -Low
Running
Running -High
Cycle
............................
System
Flow
Drive
Control
SHOOTING
Shooting
. . . . . . . . . . . . . . . . . . . . . . . . .
- High
. . . . . . . . . . . . . . . . . . . . . . . . .
.........................
.........................
Drive
..........................
..................
SAFETY
AND
SPECIAL
. . . . . . . . . . . . . . . . . . .
Service
Engine
•......................
.....................
....................
....................
Procedures.
Starter
Starter
Speed
Only
Speed
and
Low
WARNINGS
SERVICE
Tools
Theory
Only
Speed.
...........
...........
. . . . . . . . . . . . . .
......•........
..............
..............
..............
. . . . . . . . .
...•.
TOOLS
..
..
.
.
.
.
.
.
.
.
PAGE
iv
1-1
1-
2
2-1
2-2
2-3
3-1
3-1
3-2
3-3
3-3
3-3
3-4
3-4
4-1
4-2
4 - 2
4-3
4-3
4-3
4-3
4-4
."
r
-
SECTION 5 TUNE-
Description
Factors
Fuel
Ignition
Compression
New
TuneCompression
Ignition
Carburetor
Needle
Linkage
Spark
SECTION 6 FUEL
Description
Fuel
Carburetor.
Removal
Disassembly,
Installation.
Reed
Installation.
Fuel
Removal
Cleaning,
UP
PROCEDURES
Affecting
System
System
Vehicle
Up
Procedures
Timing
Adjustments
Valves
...........•...............
Plugs
SYSTEM
Flow
...........................
Valves
Pump.
.........................
Performance
. . . . . . . . . . . . . . . . . . . . . . . .
,~:
"
.
Deliverf':
Check
Check
......................
.........................
..............
. . . . . . . . . . . . . . . . . . . . . . . .
and
Cleaning
Repair,
'. . . . . . . . . . . . . . . . . . . . .
. . . . . . . . . . . . . . . . . . . . . . . .
. . . . . . . . . . . . . . . . . . . . . .
. . . . . . . . . . . . . . . . . . . . . • . .
..........................
Inspection
. . . . . . . . . . . . . . . . . .
~
,,~:
,
'
..................
..................
...................
....................
..................
. . . . . . . . . . . . . . . . . .
Reassembly
and
............
'.' . . . . . . . . .
.................
Repair
. . . . . . . . .
and
..
..
..
..
..
..
..
5-1
.
.
5-1
5-1
5-1
.
5-1
.
5-2
.
5-2
.
5-3
.
5-3
5-4
.
5-4
5-4
.
5-4
6-1
6-1
6-1
6-1
6-2
6-4
6-5
6-5
6-5
6-5
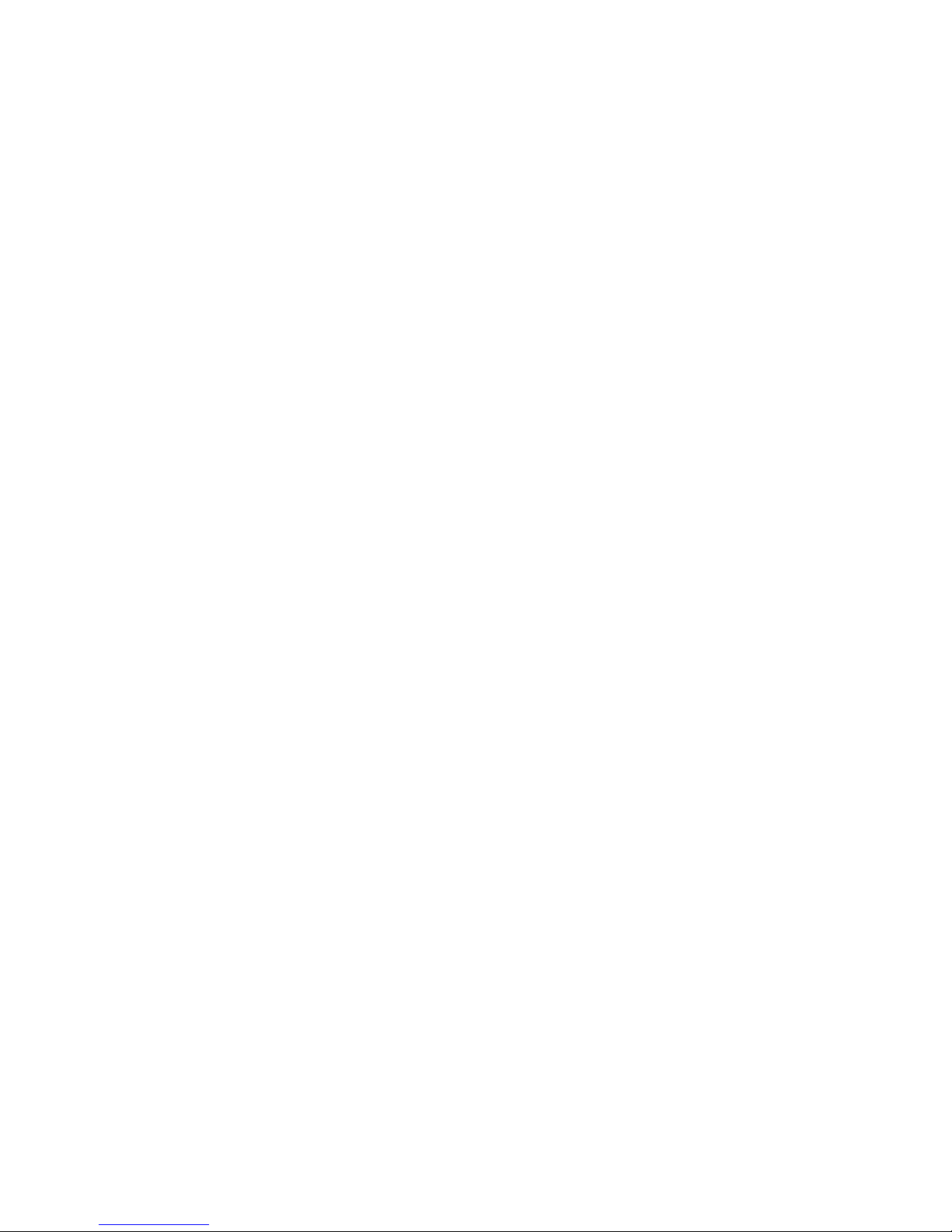
ii
TABLE
OF
CONTENTS (CONT)
SECTION 6
SECTION 7 IGNITION
FUEL
SYSTEM
Reassembly
Fuel
Primer.
Air
Silencer
Fuel
Tank
Fuel
Line
Description
Test
Equipment
C.D.
Ignition
Introduction
C.D.
Ignition
Test
#1
Test
#2
Test
#2A
Test
#3
Test
#4
Test
#5
Test
#5A
Timing
Test
#6
Check
Test
#7
Test
#8
Test
#9
Insulation
Test
#10
Lighting
Trouble
Lighting
Lighting
Dimmer
Brakelamp
Headlamp
Ignition
Spark
Battery
Starter
Headlamp
Timing
Plugs
Description
Specifications
Removal
Battery
Battery
Battery
Battery
Slow
Charging
Warranty
System
Description
Maintenance
Starter
Starter
Starter
Inspection
(CONT)
........................
. . . . . . . . . . . . . . . . . . . . . . .
. . . . . . . . . . . . . . . . . . . . . . . .
...........................
Tie
Strap
. . . . . . . . . . . . . . . . . . .
AND
ELECTRICAL
.........................
..•.•...•...•..•........
System
Ignition
Ignition
Ignition
Power
Charge
Retard
Advance
Check
Advance
..........................
Retard
Charge
Ignition
Kilovolt
System.
Shooting
Coils
Coil
Switch
Switch
Test
. .
............................
and
Servicing
Care
Testing
Charging
.....•....................
System
Circuit
Motor
of
Adjustment
Trouble
.......................
System
Coil
Safety
Switch
Pack
2S
Coil
Output
Sensor
and
.....................
Sensor
Sensor
Coil
Resistance
Coil
Checks
Check
. . . . . . . . . . . . . . . . . . . . . . .
....................
...•.•..•..•....•.•.•.
Resistance
Test
Test
..•.........•.........
. . . . . . . . . . . . . . . . . . . . . . . .
.......................
.......................
. . . . . • . . . . . . . . . . . . . . .
Installation
..•.................
.••...............•....
...........•..........
...................
.....................
.......................
.......................
.......................
Testing
Testing
Testing
Starter
Motor
. . . . . . . . . . . . . . . . . . . .
SYSTEMS
Shooting
Do's
and
Don'ts
Output
Continuity,
..................
Check
Stop
Switch
Check
Output
Coil
Retard
Coil
Coil
...............
Test
.................
................
. . . . . . . . . . . . . . . .
.......•........
................
................
..........
Check
Check
Input
Check
Sensor
Resistance
Resistance
Check
Power
..•...••.•.•
. . . . . . . . . . . . . .
........
.......
.,
......
Check
......
........
Check
....
.....
.....
and
..
..
..
..
..
.
.
.
.
.
.
.
.
.
.
.
.
.
.
.
.
.
.
.
.
.
.
.
.
.
.
.
.
PAGE
6-5
6-5
6-6
6-6
6-6
7-1
7-1
7-3
7-3
7-3
7-4
7-5
7-6
7-7
7-8
7-9
7-10
7-10
7-11
7-11
7-11
7-12
7-12
7-12
7-13
7-13
7-13
7-14
7-14
7-14
7-14
7-15
7-15
7-15
7-16
7-16
7-16
7-17
7-17
7-17
7-18
7-18
7-18
7-18
7-19
7-19
7-20
7-20
7-21
)
)
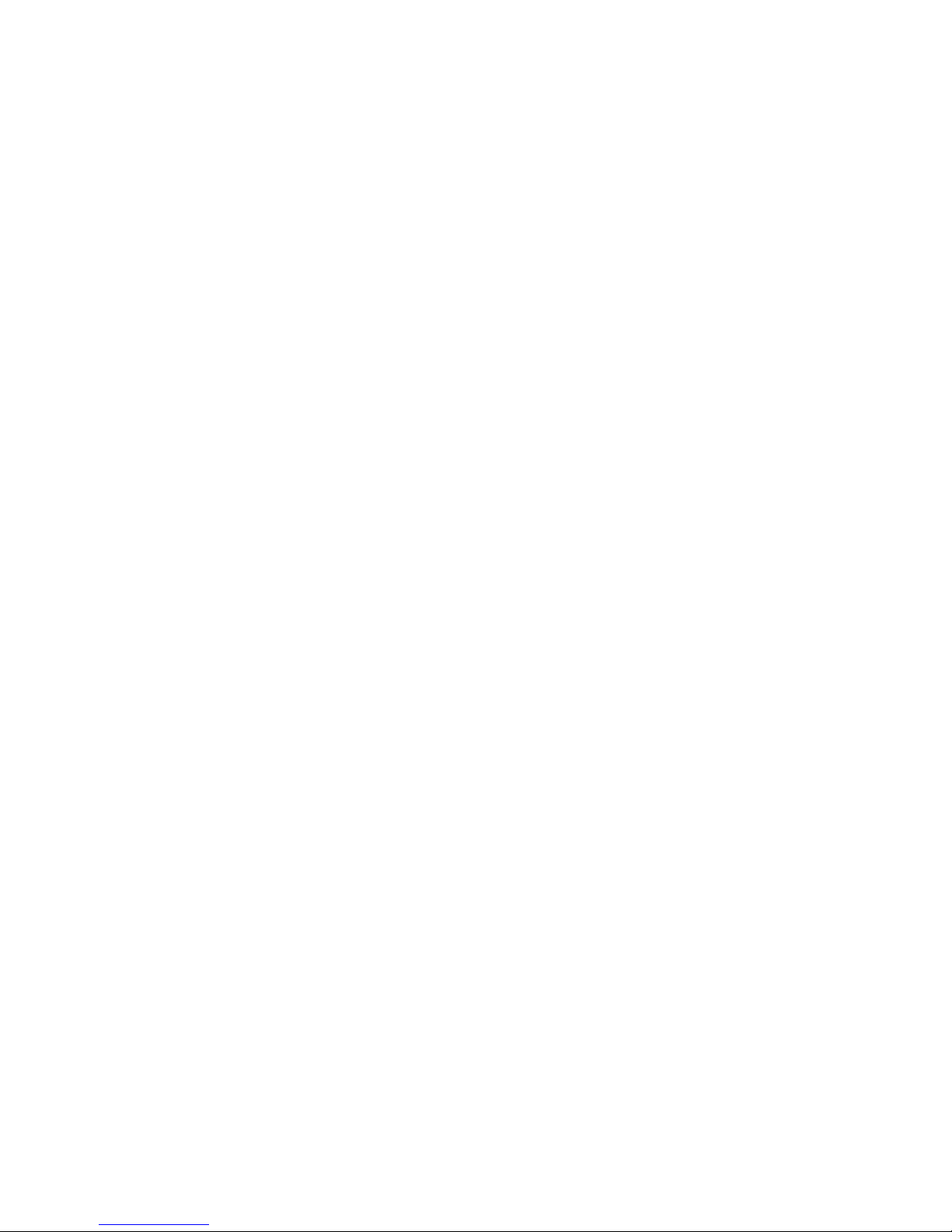
iii
-
SECTION
SECTION
SECTION
MANUAL
8
Description
Removal
Cleaning,
Reassembly
9 ENGINE
Description
Removal
Disassembly.
Assembly
Installation
Break-in
10
DRIVE
Description
Transmission
Brake
Primary
Disassembly
Disassembly
Cleaning,
Reassembly
Primary
Neutral
Secondary
Disassembly .........•.............
Servicing
Cleaning
Reassembly
Chain
Disassembly
Cleaning
Reassembly
STARTER
..........................
and
Disassembly.
Inspection
..........................
..........................
.........................
. . . . . . . . . . . . . . . . . . . . . . .
...........................
of
Engine
Period
TRAIN
.............................
Drive
Lockout
Drive
Case
.......................
.........................
Belt
.......................
............•••.•.......
of
Inspection
of
Flywheel
Drive
Reassembly
................•.•.•..
Secondary
and
Inspection
.....•.....•..••...•....
..........•.•..............
......•....•....••....•
and
Inspection
.••.••.....•.........•.•
and
Repair
Assembly
Inspection
Flywheel
and
Repair
.•....•....•....
Adjustment
Assembly
...............
......•.........
PAGE
8-1
. . . . . . . . . . . . . . . . 8- 1
. . . . . . . . . . . . . 8- 1
to
and
from
.•........
............
Chassis
Replacement
Engine
...•.......
•..•........
.....
..
......
.
. 9- 1
..
.
.
.
.
.
..
.
.
8- 2
9-1
9-2
9-5
9-10
9-
10-1
10-1
10-2
10- 3
10-3
10- 3
10-3
10-4
10- 4
10-4
10-5
10- 5
10- 5
10- 5
10-5
10-6
10-6
10- 6
10- 6
10
T ABLE OF CO
NTENTS (CONT)
SECTION
SECTION
Wiring
Diagrams
11
STEERING,
Description
Steering
Disassembly.
Reassembly
Ski
Alignment.
Track
Track
Track
Removal
12 LUBRICATION AND STORAGE
Engine
OMC 2+4
Lubrication
Preventive
Air
Fuel
Off
Season
After
TRACK
.....•.•.....•........
Column
and
Suspension
Tension
Alignment.
Lubrication
Silencer
Filter
Storage
Storing -Before
..•...•.......•.•......
. . . . . . . . . . . . . • . . . • . • •
• • . . . . . . • . • . . . . • . • . • .
. . . . . . . . • . . • . . . . . . . . . .
• • . . • . • • . • . . . . . . . . . • . .
....••.......•........
of
Trucks
Fuel
Conditioner
Recommendations
Maintenance
..•..•....•........•....
Screen,
. . . . . . . . . . . . . . . . . . . . . .
AND SUSPENSION
•............•.....
. . . . . . . . . . . . . • . • . .
and
Track
....................
......•...........
Fuel
Pump
Using
..
..
..
..
..
. . . . • . . . • .
.............
. . . . . . . . . . . . . .
....•......
............
At
Back
..
of
11- 1
11- 1
11-1
11-1
11-1
11- 2
1111- 2
11-3
.
12 - 1
.
12-1
12- 3
12-4
12- 4
12- 4
12 - 5
.
12 - 5
Manual
2
"
.'
I'
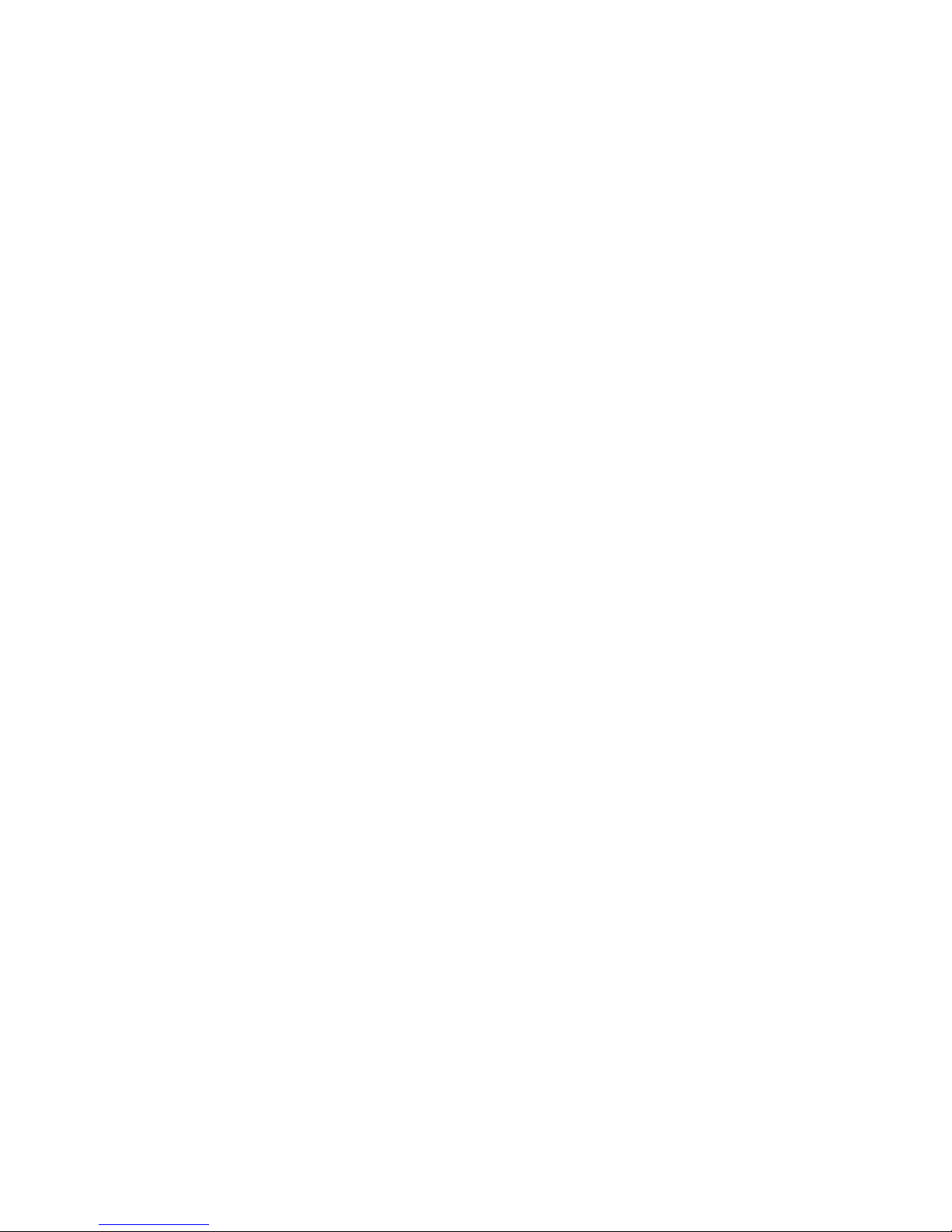
iv
~
-:-":::-
3':':':-':::/
"'J
CANADA
2.7025
FUEL
This
is a two-cycle
The
correct
leaded
OMC
In
use
engines.
If
oil
except
recognized
motive
oils
use
engine.
Use
Imperial
gasoline
2-cycle
some
this
recommended
mixed
in
engines
are
Evinrude
the
FOR
EVINRUDE
1/2
U.S.
1/2
Imp.
1 U.S.
1
Imp.
RECOMMENDATIONS
fuel
to
motor
gasolines
type
of
gasoline,
lubricant
at
24:1
ratio.
emergencies
that
automotive
formulated
and
or
following
measures:
LUBRICANT
pint
..
pint
..
pint
.. . Mix
pint
.. .
engine
mixture
one
oil.
the
Evinrude
for
Johnson
table
OR
JOHNSON LUBRICANT AND OMC 2
IMPERIAL
Mix
Mix
Mix
which
requires
ratio
is
part
amount
since
is
not
Automotive
when
oils
the
2-cycle
to
50 TO 1 MIXTURE RATIO CHART
U.S. MEASURE - 1
with
with
with
with
50
Evinrude
of
lead
has
phosphorus
available,
oils
the
recommended
are
formulated
or
Johnson
engine
Rotary
determine
Combustion
MEASURE - 1
U.S. MEASURE
parts
or
Johnson
been
use
and
50:1
installed
the
50:1
3 U.S.
3.7 U.S.
6 U.S.
7.5 U.S.
lubricant
of
a good
grade
50:1
replaced
is
detrimental
a BIA
24:1
oil
Lubricant
PINT
PINT -20 OZ.
gal.
gal.
gal.
gal.
CERTIFIED
premix
is
not
to
fit
the
in
your
Lubricant
fuel
and
- 16
GASOLINE
with
mixed
with
premium
Lubricant,
phosphorus.
when
fuels
should
available.
needs
and
OMC
snowmobile.
in
any
oil
mixture
CYCLE
OZ.
IMP.
2.4
3
Imp.
4.8
6
Imp.
the
gasoline.
or
or
in
used
in
SERVICE
not
It
should
of 4-
cycle
2-cycle
DO NOT
OMC
for
U.S.
MOTOR
MEASURE
Imp.
gal.
gal.
Imp.
gal.
gal.
regular
Canada
Do
not
2-cycle
TC-W
be
used
auto-
motor
2-cycle
and
OIL
be
U.S.A.
U.S.A.
"-
fVI
HR~
IUURIel'
22019
21246
Gasoline
ditions.
spark
1.
Always
2. Do
3.
To
container
lubricant.
To
ture.
unless
mixture
ture. A clean
pouring
DO NOT
TANK. USE
FUEL.
Whenever
(O°C),
The
lubricant
part
lubricant.
temperature
Do
not
tank,
use a clean
OMC 2+4
For
added
is
recommended.
•
Fuel
tem
•
Carburetor
fuel
•
Corrosion
parts
•
De-Icer -prevents
•
Absorbs
•
Extends
is
Always
near
use a separate
not
pour
prepare
completely
The
agitated.
to
the
POUR
AN
it
is
the
lubricant
above
use
kerosene
FUEL
protection
Stabilizer -prevents
for
one
system.
Resistance -protects
from
corrosion.
moisture
spark
&.
extremely
the
lubricant
the
half
mix
lubricant
the
required
funnel
fuel
GASOLINE
APPROPRIATE
necessary
should
Predilution
32° F
funnel
CONDITIONER
Available
year
Cleaner -dissolves
plug
flammable
stop
engine,
snowmobile
clean
or
snowmobile
the
amount
or
blend
adheres
Next,
add
ratiO
equipped
mixture
and
into
to
should
be
be
prediluted
when
or
fuel
equipped
to
your
of
storage.
carburetor
water
life
by
OR
of
snowmobile
from
reducing
when
gasoline
the
the
LUBRICANT
mix
prediluted
the
possible.
oils
with a fine
formation
icing
in
SAFETY
and
container
fuel
of
U
irlll!t
the
to
balance
of
CONTAINER
fuel
lubricant
for
your
Eliminates
fuel
WARNING
and
highly
do not
refueling
for
separately
properly,
gasoline
U NOTE
fuel,
thoroughly
the
bottom
50:1.
Again,
with a fine
vehicle
and
with
with
approximately
pre-mixing.
engine,
dealer.
of
gum
gum
and
carburetor,
and
gas
system.
fouling
explosive
smoke
or
mixing
into
pour
required
and
of
gasoline
thoroughly
screen
tank.
DIRECTLY
FOR
lubricant
gasoline
should
When
screen.
the
and
need
varnish
fuel
line
freeze-up.
and
misfire.
under
or
allow
servicing
fuel.
vehicle
into
and
shake
sidewalls
necessary
should
MIXING AND STORING
at
temperatures
to
one
take
place
pouring
use
of
varnish
for
draining
deposits
system
certain
open
flames
the
fuel
system.
tank.
a SEPARA
add
all
the
this
partial
of
the
container
to
bring
agitate
the
be
used
INTO VEHICLE
improve
part
OMC
deposits
and
its
gasoline
with
the
fuel
Fuel
fuel
in
carburetor
internal
below
mixability.
into
Conditioner
in
for
con-
or
TE,
clean
required
mix-
the
mi.xwhen
FUEL
THE
32° F
to
lubricant
vehicle
fuel
sys-
storage.
engine
one
and
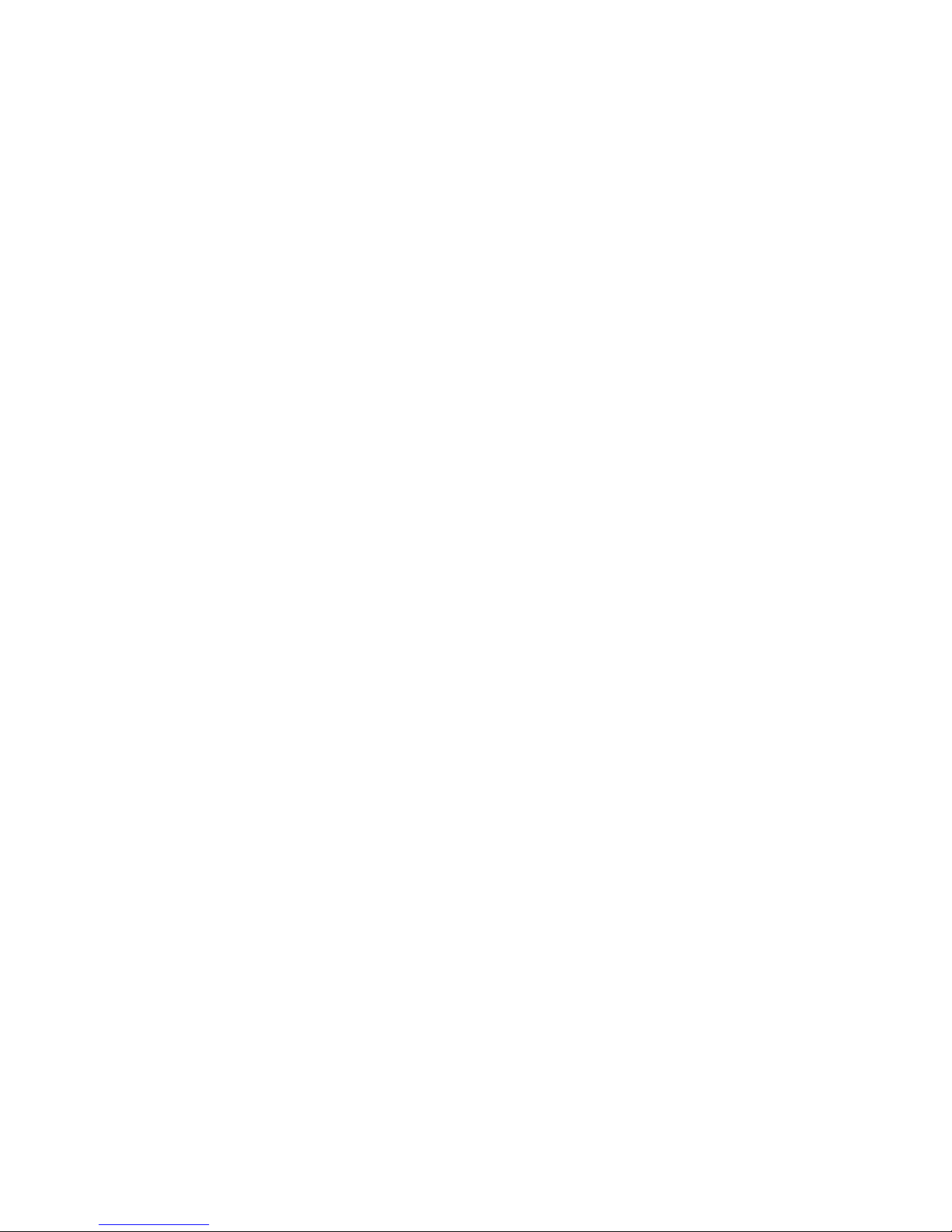
1-1
The
snow
machine
performance.
to
receive
It
is
important
service
This
Parts
to
service
manual
perienced
the
guidance
The
for
replacement.
sequence
reference
The
any
desired
snowmobile.
troubleshooting,
5
of
tailed,
justment
formation.
and
practice
experienced
specific
vide
ship
between
skilled
which will
manual,
Catalogs,
this
that
will
serviceman,
of
Parts
of
all
during
Table
of
section.
this
manual.
step-by-step
procedures.
In
serviceman
service
unimpeded
illustration
has
It
is
important
and
thorough
to
the
service
maintain
together
provide
the
Catalogs
disassembly
Contents
All
and
this
are
information.
reading
the
snowmobile.
not
only
but
less
experienced
contain
In
addition,
parts.
Section 2 lists
general
tune up
Sections 6 through
disassembly
Section
way,
not
intermixed.
of
and
INTRODUCTION
been
designed
to
every
service
dealer
the
customer's
with
the
regularly
serviceman
An
serve
as a ready
will
also
complete
the
This
catalog
and
reassembly.
on
page i enables
information,
procedures,
and
12
provides
the
texts
to
reread
Illustrations
explanatory
text.
exploded
and
built
snow
machine
for
his
vehicle
to be
able
to
offer
satisfaction.
issued
with
all
the
effort
man.
treat
has
been
reference
provide
This
discussions
more
listings
views
can
be
of
the
reader
complete
including 2 cycle
are
given
11
provide
reassembly
lubrication
each
topic
makes
placed
test,
and
AND
for
dependable, high
owner
when
necessary.
the type
service
literature
basic
of
illustrate
considerable
specifications
in
fully
instructions
it
unnecessary
of
in
permit
bulletins
made
to
book
for
information
the
parts
the
to
locate
engine
Sections 3 through
illustrated,
and
storage
separately;
theory
the
close
along with
margins
to
be
able
of
skilled
and
necessary
produce
the
ex-
for
required
correct
help
as
quickly
on
the
theory,
de-
and
ad-
in-
theory
for
the
pro-
relation-
SAFETY
a
a
SECTION
WARNINGS
1
Figure
47011
1-1
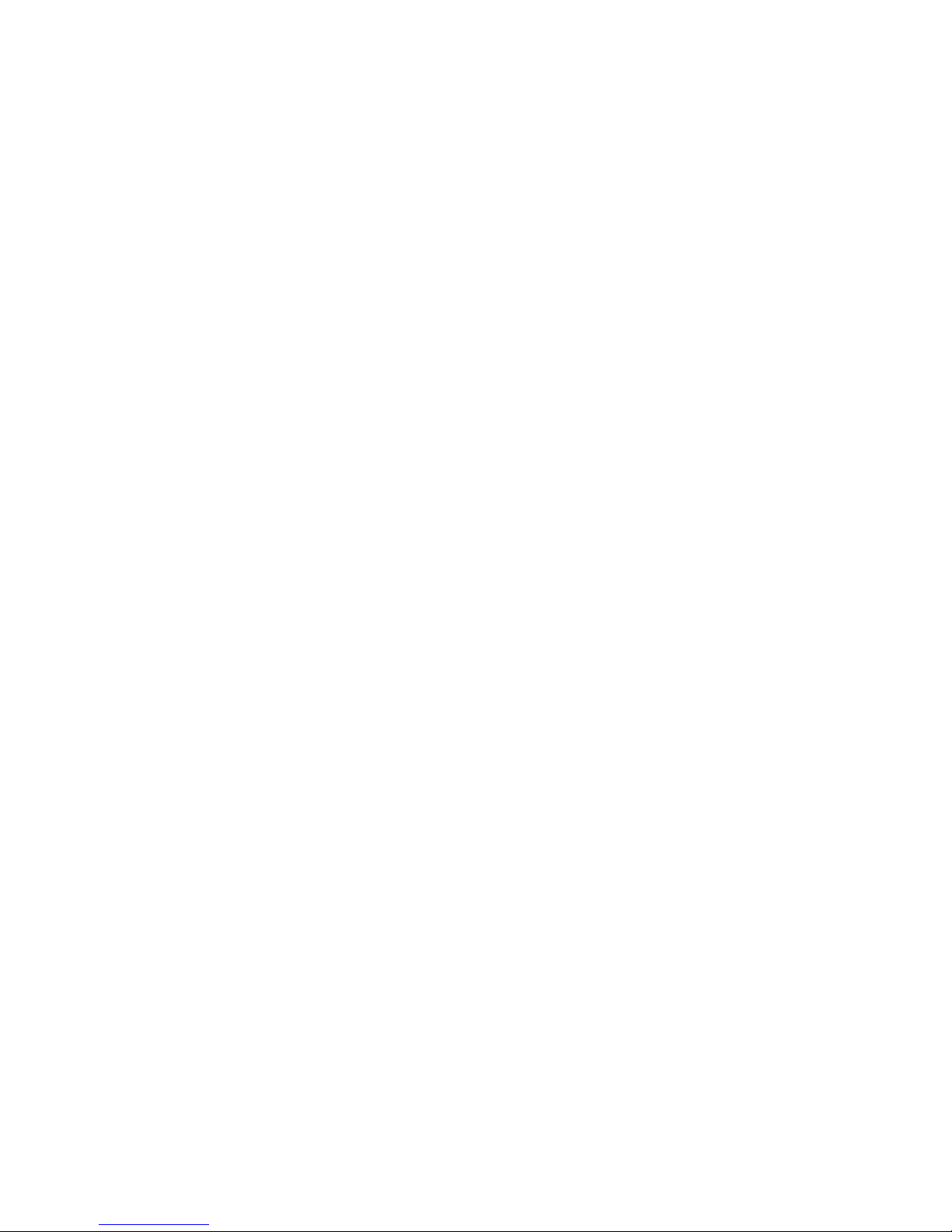
1- 2
Read
this
procedures
shop
for
viceman
build
This
however,
does
to
the
complete
number.
All
literature
publication.
notice.
to
and
maintain a reputation
service
not
appear
Service
information,
manual
as
described,
use
as a reference.
give
better
manual
new
service
to
Department
information,
are
based
The
right
carefully
then
service
covers
situations
be
answered
for
including
illustrations,
on
the
product
is
reserved
to
become
keep
it
If
properly
to
the
for
reliable
all
phases
sometimes
in
this
additional
model
and
information
to
thoroughly
readily
snowmobile
manual,
specifications
make
used,
service.
of
servicing
arise.
help.
number
changes
available
you
Always
available
it
If
will
owner,
a
are
and
at
familiar
in
the
enable
and
the
snowmobile,
service
invited
be
sure
vehicle
contained
at
the
any
time
with
the
service
the
ser-
thereby
question
to
write
to
give
serial
in
this
time
of
without
CONTROLS
Refer
Figure
to
Figure
1-2
for
location
of
1. NEUTRAL CONTROL KNOB
The
out.
out.
push
neutral
When
To
neutral
control
starting
engage
control
locks
engine,
transmission,
knob
in.
A SAFETY WARNlNG
Engine
be
2. HAND BRAKE
RPM
locked
To apply
in
neutral.
brake,
must
be
under
squeeze
brake
1-2
the
following
the
transmission
neutral
reduce
2000
RPM
lever.
components:
control
engine
before
in
neutral
knob
must
speed
transmission
when
be
to
idle
47012
pulled
pulled
and
can
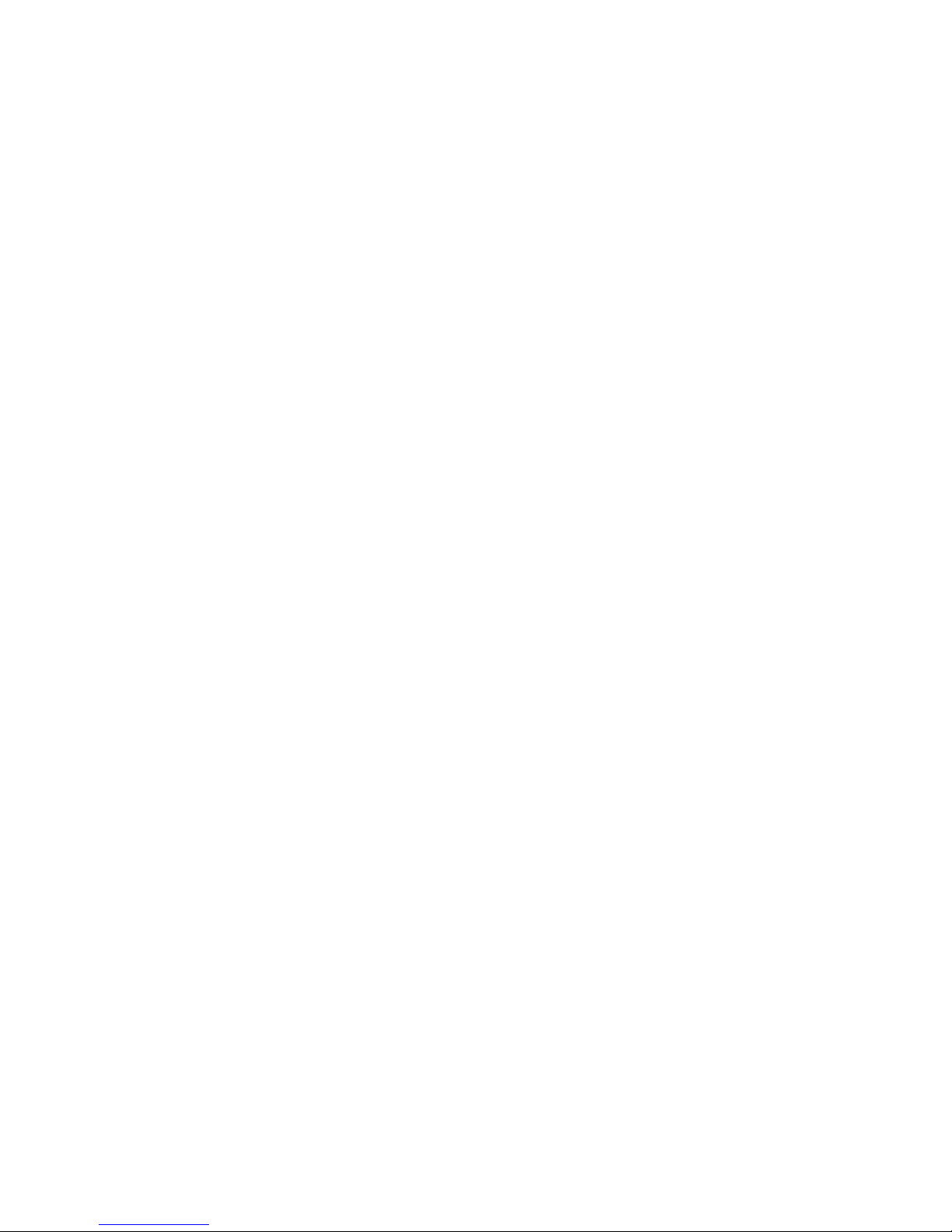
3.
IGNITION/ LIGHTS SWITCH
The
key
LIGHTS'
'ST
4.
PARKING LOCK
To
position.
5.
HI~LOW
The
when
6.
SPEEDOMETER/ODOMETER
The
traveled,
7. TACHOMETER
The
8.
SAFETY
This
Rotate
Rotate
9.
THROTTLE
The
steering
power
returns
operated
(operate
ART'
(for
apply
parking
To
BEAM HEADLAMP SWITCH
headlamp
ignition
speedometer/odometer,
is
tachometer,
STOP
switch
switch
switch
thumb
bar.
is
transmitted
to
idle.
ignition
use
with
release,
beam
switch
an
accessory.
SWITCH
allows
to
to
operated
Squeezing
with
lock,
which
either
"RUN"
switch
lights),
accessory
with
squeeze
switch
is
in
the
indicates
the
operator
side
throttle
the
to
the
has
'RUN'
electric
brake
engaged,
brake
lever.
selects
RUN/LIGHTS
which
engine
to
of "RUN"
position
throttle
track.
to
lever
When
four
positions,
(operate
start).
either
indicates
stop
allow
is
located
increases
lever
without
flip
high
beam
position.
RPM,
engine
position
restarting
engine
is
'OFF,'
parking
or
MPH
is
an
power
to
stop
on
the
released,
'RUN/
lights),
and
accessory.
right
speed
and
lock
into
low
beam
miles
instantly.
engine.
of
engine.
hand
and
engine
1-3
10. CHOKE C.ONTROL KNOB
The
choke
control
enrich
11.
PRIMER
Pushing
manifold. A cold
12.
MANUAL
Snowmobile
the
fuel-air
the
STARTER
is
primer
engine
started
&:.
- All
operators
hicle.
- When
gear
DO
etc.
or
mended
requirements
- Do
- Keep
-
Use
headlight
Many
operating a snowmobile,
such
NOT WEAR LOOSE CLOTHING
Such
other
not
overload
feet
headlight
must
dangerous
as a brightly
clothing
objects
that
operator
of
ANSI Z90.1 - 1971
vehicle
on
running
for
in
heavily
be
could
and
board
early
wooded
is
used
mixture
knob
should
HANDLE
by
pulling
SAFETY
properly
situations
colored
get
cause
and
passenger
with
passenger.
at
all
morning,
areas
during
to
the
engine.
manually
be
the
WARNINGS
instructed
are
wear
helmet
entangled
personal
or
times.
evening
during
starting
Pull
pumps
primed
created
protective
such
equivalent.
manual
in
as
as
with
bodily
wear
the
day.
prior
the
by
well
the
helmets
and
and
engine
to
choke.
fuel
to
starter
operation
negligence.
clothing
as
padded
scarves,
machinery,
injury.
which
night
warm-up
into
the
starting.
handle.
of
the
and
clothes.
tassel
branches
It
is
recom-
meet
operation.
to
intake
ve-
head-
caps,
the
Use
not
not
operate
operate
area.
as
ice,
- Do
-
Do
charted
start,
track.
vehicle
vehicle
Be
certain
stones,
on
at
maximum
etc.,
or
around
no one
may
be
speeds
is
behind
thrown
sled,
in
other
unit
into
ski,
and
toboggan
than a supervised,
when
the
making a fast
air
by
lugs
hills.
on
the
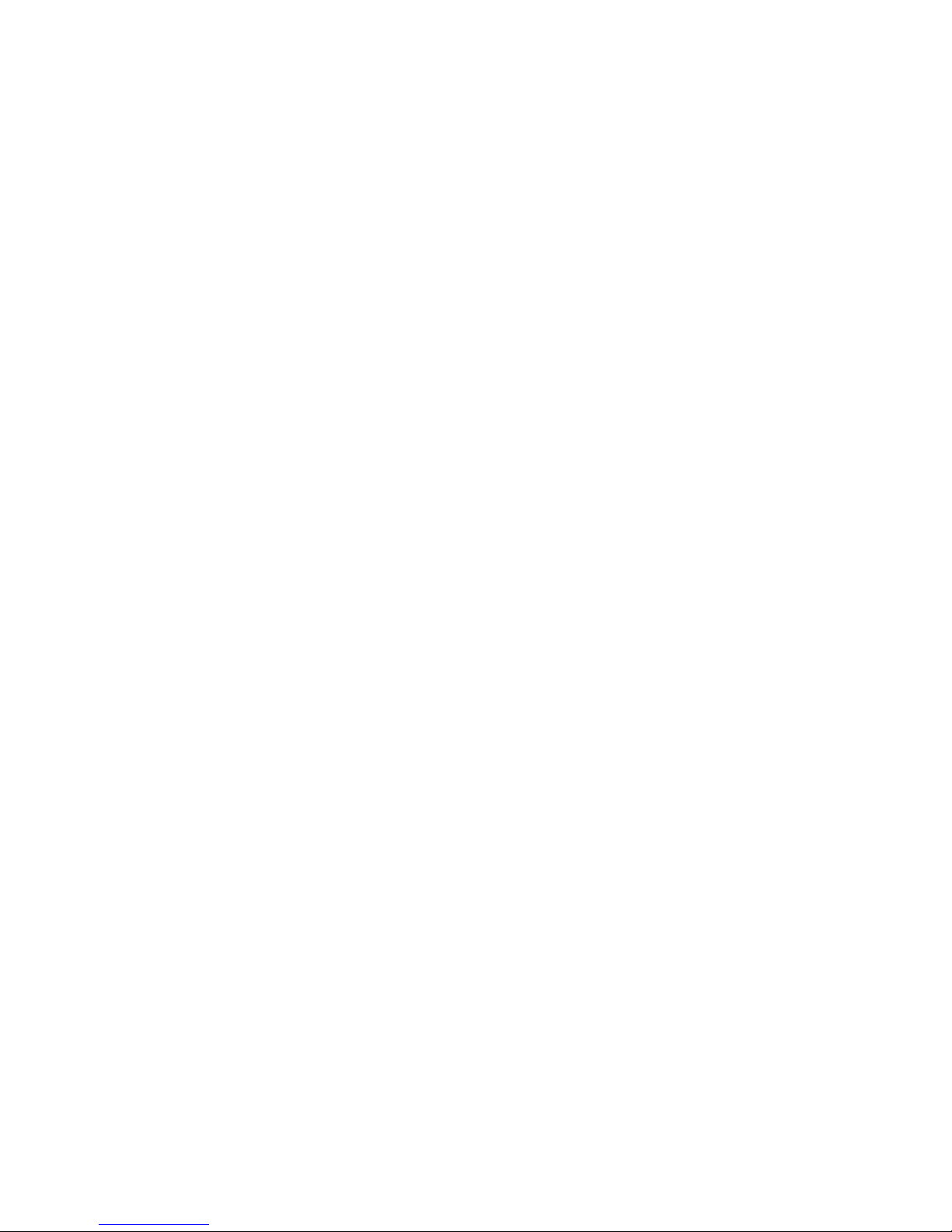
1-4
-
Extra
control
two hands
caution should be
is
greatly
for
reduced
steering.
exercised
on
ice.
when
Beware
using
vehicle
of thin
on
ice.
ice.
Always
Steering
use
- When
-
- Do
-
- Do
-
- Remove key
-
crossing
snow banks
Do
not
may
and
Do
passengers
erages,
Never
Wear
branches,
requirements
VESCO -
Do
running.
Before
connect
turn
age
shock.
operate
be
reduced.
not
execute
excessive
not
smoke
not
operate
narcotics
leave
goggles to
8.
not
attempt
servicing
spark
the
ignition
capacitor.
as
as
the
from
and
plowed
you
vehicle
"blind
drop
while
well
vehicle
or
machine
vehicle
from
of
Vehicle
to
any
plug
switch
A
roads,
might
on
jumps."
offs.
operating
as
operator.
while
other
unattended while engine
whenever
protect
wind and
perform
part
wires
to
charged
approach
find
yourself
bare
ground
Snow
vehicle.
under
habit
forming
it
the
eyes
sun
Equipment
repairs
of the engine
to
prevent
"OFF"
position
capacitor
with
in
the
path
or
gravel
drifts
can
Ashes
the
influence
drugs.
is
not
in
from
lashing
glare.
Goggles should
Safety
on
your
or
accidental
to
could give a
caution.
of oncoming
as
steering
hide
tree
can
be
of intoxicating
is
running.
use.
tree
Commission
vehicle
drive
discharge
while engine
unit:
start
of engine; and
the
severe
Do not jump
traffic.
response
stumps,
dangerous
always
logs
bev-
and
shrub
meet
the
regulation
dis-
high
volt-
electrical
to
is
Never
Never
Always
nipple.
tie
raps
~
-
Operation
Operation
legal
remove
attempt
assemble
Improper
should
PROHIBITED
to do
on
private
of
so.
a fuel
to
be
vehicle
hose
install
the
tie
assembly
located
property
on public
without
a fuel
rap
could
in
the
hose
after
result
original
without
roads,
first
with a
the
fuel
assembled
owner's
streets
removing
tie
hose
in a leak.
permission.
or
highways
the
tie
rap
preassembled.
is
assembled
All
reassembled
location.
rap
clamp.
unless
to
it
the
is
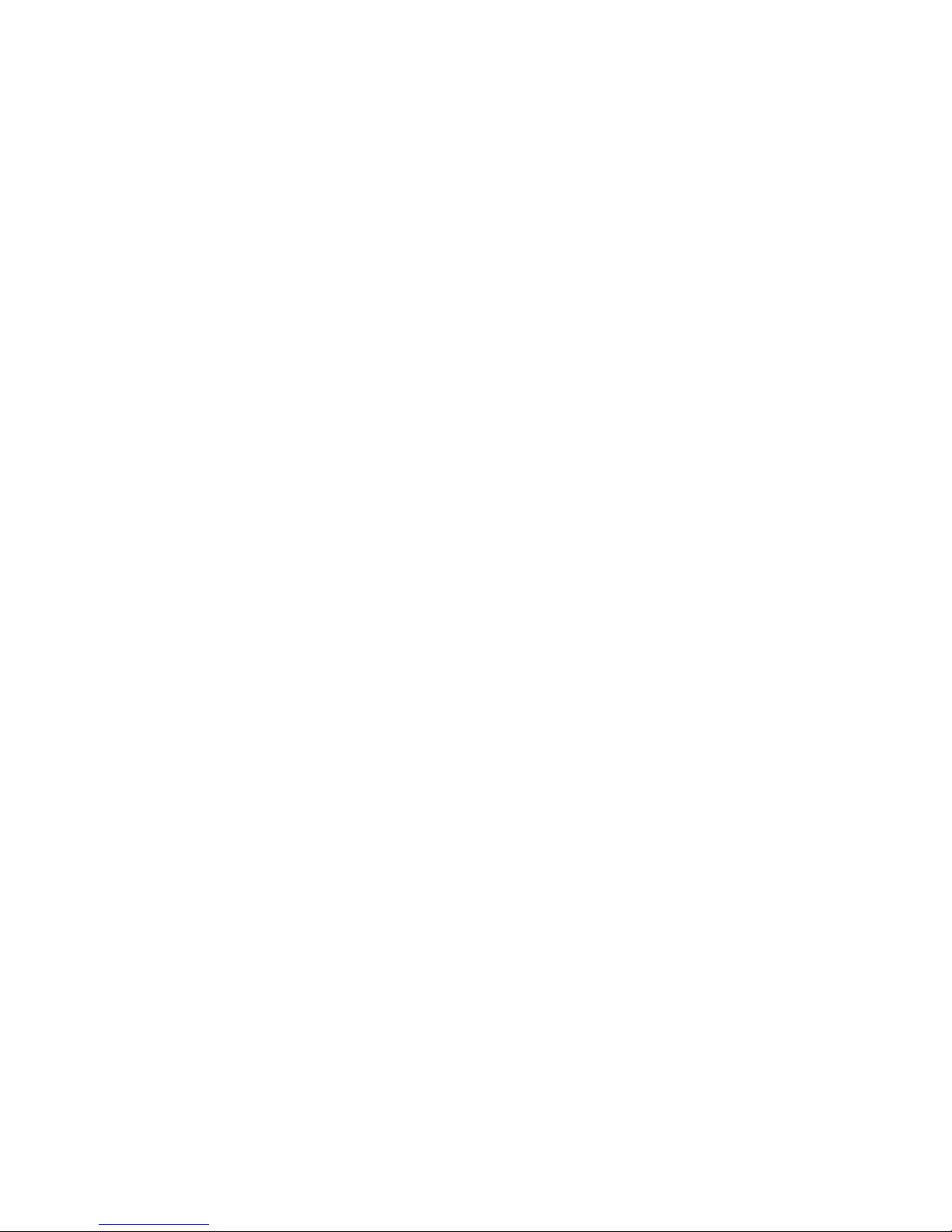
2-1
SECTION
SPECIFICATIONS
SPECIFICATION
o
PROHIBITED:
use
and
the
manufacturer
all
the
Length
Width
Height.
Engine
Rating
Starter
Variable
Overall
Final
drive
Sprocket
devices
.•..........••.•.•...•.....•••••.••.
•..••.•.•.••.•
•.•....••.•.•....•••••.•.
ratio
legally
•......••.••.•••.••••.•••••••••...
• . . • • • . • • • • . • . . • • • . • • •
•.••.••••••.•...•..•••..•...•.•.•
speed
drive
...•..•.......•.•..•..••••••••..•
..•.••••.•••••••••••••...•
ratio
(
Muffler
Brake
Throttle.
Track
Skis
Seat
Hood
Headlamp
Taillamp/Stoplamp.
Acc.
Fuel
Fuel
Lubrication ......................
Carburetor
RPM
Ignition
• • • . . . . • • . . • . . . • . .
• • • . . . . • • • • • . . • . . • . . •
• • • . . • • . . . • • • • . . . . • • . . . . • • . • •
. . . • • . . . • • . . .
Width.
Idle
Transmission
Maximum
Breakerless
Spark
Advance
Retard
Charge
Ignition
Ignition
Lighting
Stop
Bore
. • • • • . • . • . . . • • • . • • • • • . . . • • • . . • . •
•.....•..•.•
.••••.•...
..•.•...•....•.••••••••..•••••••
....••.•....•...•...
Speedometer/Tachometer
tank
•....••••..
. . . . . . . . . . . . . . . . . . . . . . . . .
needle
Ratings
.•.....•••••••••.••..•••..••....•..•.
belt
RPM
at
magneto
plug
••.•••••••••••••••••••••••
sensor
sensor
coil
light
and
coil
coil
coil
coil
Stroke.
coil
resistance
primary
secondary
resistance
resistance
S
Snow
Vehicles
does
not
represent
required
..••.
standard
Formed
•
Vinyl
. . . . . • • . . • • • . . • • • . . • • . • . • . •
adjustment
engaging
which
C.D.
coil
resistance.
resistance
resistance
. . . . . . . . . . . . . . .
for
such
OMC 2 -
Centrifugal
••.•.......•
.•
coated
Capacity
speed
neutral
(Capacitor
(2
coils)
resistance.
headlight/taillight
...................
cycle
..
•.
Rubber -Polyester
steel
equipped
springs
cover,
lamp
.........
••.....••••••.••.
- 5
••••.•...•••.••••
control
. . . . . . . . . . . . .
...
........
total
. . . . . . . . . . . . .
. . . . . . . . . . . . 1900 ± 300
AND
are
not
manufactured
that
they
use.
•.
43.4
inches
34.9
inches
Alternate
399CC
436CC
646CC 50
operated
Tuned
Caliper -Flange
and
molded
Sealed
Imperial
..
will
Discharge)
of . . . . . . . .
..
sheave
,.........
for
maximum
Cords
with
replaceable
urethane
beam
gallons,
Gasoline -regular
OMC
Tillotson
operate
.....
.........
399CC
436CC 2.875 x
646CC
SPECIAL
for
highway
are
equipped
103.2
35.4
with
windshield
without
Firing
35
40
Silent
..
shock-absorbing
Molded
Westinghouse
brand
HD
ignition
Champion
..
..
..
2.75 x 2.05
3.25
windshield
- 2
Cylinder
HP
at
6750
HP
at
6750
HP
at
6750
Manual
engages V -belt
4.43
Drive
13'4
- 17:39
144 - 19:39
164 - 19:39
performance
on
secondary
Thumb
.•••.•..
'
operated
fully
adjustable
•.
15.5
wear
runners.
foam
cushion
fiberglass
•.
GE 1157
GE 1816
6 U.S.
gallons
50: 1 lul::ricant
diaphragm
1300 ± 100
3300 ± 300
UL-77V
17
to
19
28
to
30
600 ± 50
0.1
± .05
1.3 ± .3
4.25
to 1 ohms
2.05
x 2.375
with
inches
inches
RPM
RPM
RPM
rewind
to
Chain
inches
leaf
7700
leaded
type
2000
ohms
ohms
ohms
ohms
ohms
ohms
inches
inches
inches
SERVICE
1
TOOLS
2
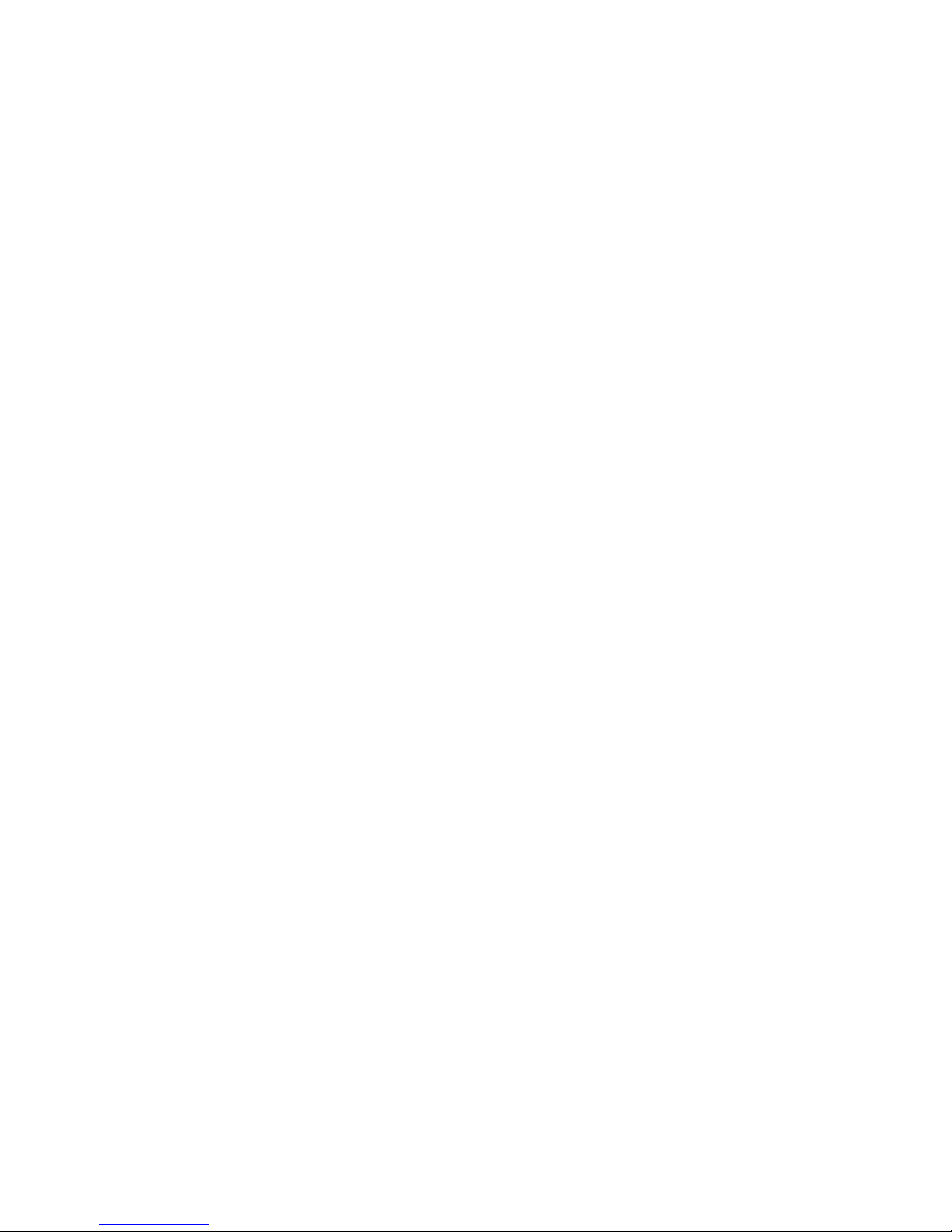
2-2
TORQUE
PART
*Nut
* Nut Rod
Screw
Screw
Nut (4)
*Nut (2)
*Nut
(2)
*Nut
(4)
*Screws
*
Nuts
Screws
*Nut
Screws
Care
*Nut
Nut
*Screw
*Screw
*Screw
Nut
*
Nut
Nut
*Nut
*Nut
*Nut
*Screw
*Bolt
*
*Nut
*Nut
*Screw
Nut
Screw
Screw
Screw
Screw
Screw
Screw
Screw
* Nut
*Screw
*Screw
Screw
should
be
SPECIFICATIONS
APPLICATION
Ball
Joint
to
Steering
End
Mounting
Steering
Steering
Ski
Runner
Rear
Track
Trucks
Engine
Fuel
Throttle
Brake
used
Bearing
Cable
Connecting
Crankcase
Crankcase
Crankcase
Cylinder
Drive
Exhaust
Flywheel
Front
Idler
Primary
Spark
Steering
Steering
Truck
Saddle
Cylinder
Power
Power
Check
Arm
(Drag
Column
and
Spring
to
Ski
Axle
Pivot
Adjusting
to
Frame
Mounting
Pump
Control
Hand
Lever
in
tightening
Cup
to
to
Solenoid
Rod
Drain
to
Crankcase
Sprocket
Manifold
and
Rear
Axle
to
Frame
End
Cap
Plug
Arm
to
Arm
to
to
Frame
to
Springs
General
Torque
Requirements
Head
Pack
Cover
Pack
Cover
Valve -Primer
Arm
to
U -
Bracket
to
hardware
Chassis
to
Truck
Ball
Ski
Piston
Cylinder
End
Specifications
and
Jam
Link)
bolts
Main
to
Cylinder
to
Crankshaft
Column
gap.
without
Arm
Nuts
Screw
Screw
to
Frame
Handle
Axles
Joint
displacement
and
against
35
HP
399CC
40
HP
436CC
50
HP
646CC
compression
. . . . . . . . . . . . . . . . . . . . . . . . . . . . . . . .
and
obligation
Steering
Frame
Bars
tie
........................
features
towards
Column
rod
end
ball
may
vehicles
to
prevent
3/8-24
.................
.............
.................
be
changed
previously manufacturer.
SIZE
3/8-24
3/8-24
3/8-24
5/16-18
5/16-18
5/16-18
5/16-24
3/8-16
3/8-16
#
10-24
3/8-16
5/16-18
3/8-24
1/2-20
5/16-24
5/8-18
3/8-16
3/4-16
3/8-24
3/8-24
7/16-14
#6
#8
#10
#12
1/4
5/16
3/8
5/16-24
1/4-20
#
10-32
at
distortion
120-140
220-240
145-150
any
LBS. LBS.
90-100
25-35
30-40
13-15
36-60
25-30
15-22
25-35
35-40
60-80
40-50
24-36
25-30
IN./
or
7-10
24.35
.. ..
26.62
100
..
time
without
TORQUE
binding.
cu.
cu. in.
39.40
cu
to
120
.007 - .017
noti
FT./
18-20
10-12
18-20
18-20
10-12
12-15
12-15
25-30
18-20
6":'8
29-31
18-20
10-12
18-20
25-35
10-12
145-150
35-45
20-25
90- 100
18-20
18-20
18-20
25-30
25-35
2-3
3-4
5-7
10-12
18-20
in.
in.
psi
ce
Specifications
vehicles
*Use
Torque
and
previously
Wrench
features
manufactured.
may
be
changed
at
any
time
without
notice
and
without
obligation
towards
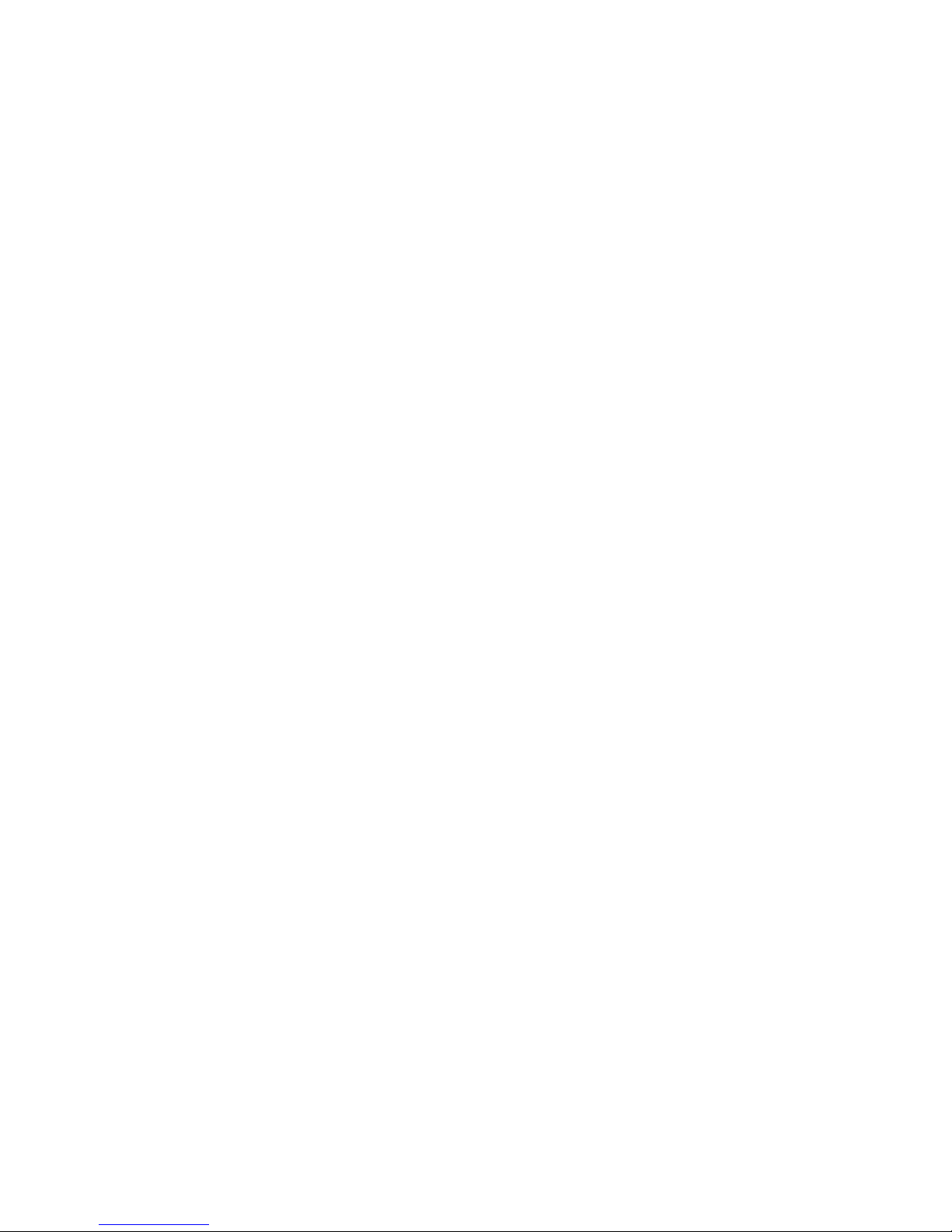
2-3
-
SNOWMOBILE
PART
NO.
114595
318502
114594
263308
312019
316613
114584
114585
114586
114587
319924
114611
378103
SPECIAL
DESCRIPTION
Wrench -Flywheel
Screw -Use
Retainer -Flywheel
Sheave
Rod
Seal
Installer -Front
Disassembly
Ring
Compressor
Ring
Compressor
Ring
Compressor -3.250
Cone -Wrist
Wrench -Cylinder
Flywheel
with
Holding
Tool -Primary
Pin
Puller
Flywheel
Tool
- 2.750
- 2.875
Retainer
SERVICE
Nut
Bearing
to
Crankcase
Puller
Bore
Bore
Bore
TOOLS
#378103
Drive
Nuts
263472
380658
375632
114146
317829
Truarc
Slide
Spark
Spline
Driver
Pliers
Hammer
Plug
Wrench
Wrench
Set
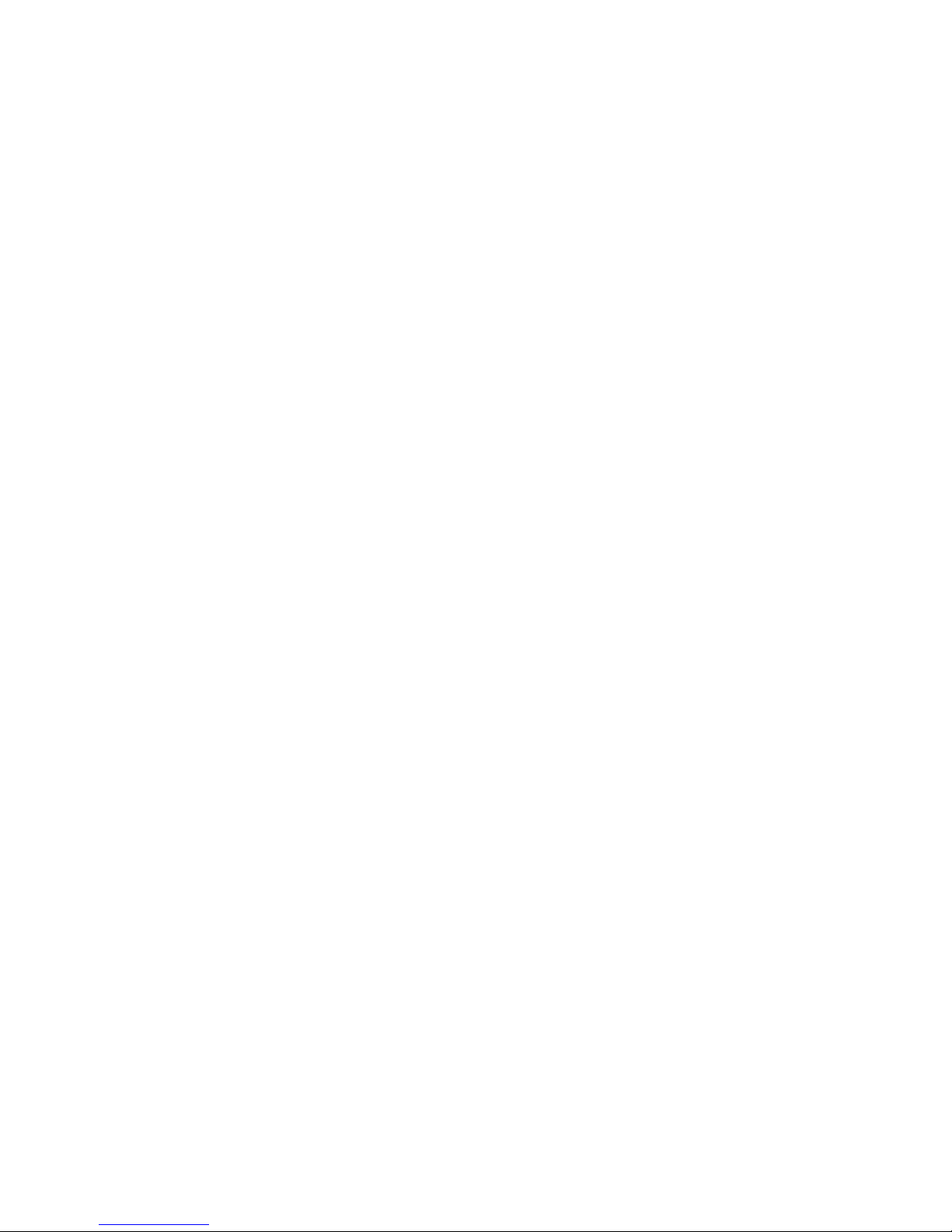
)
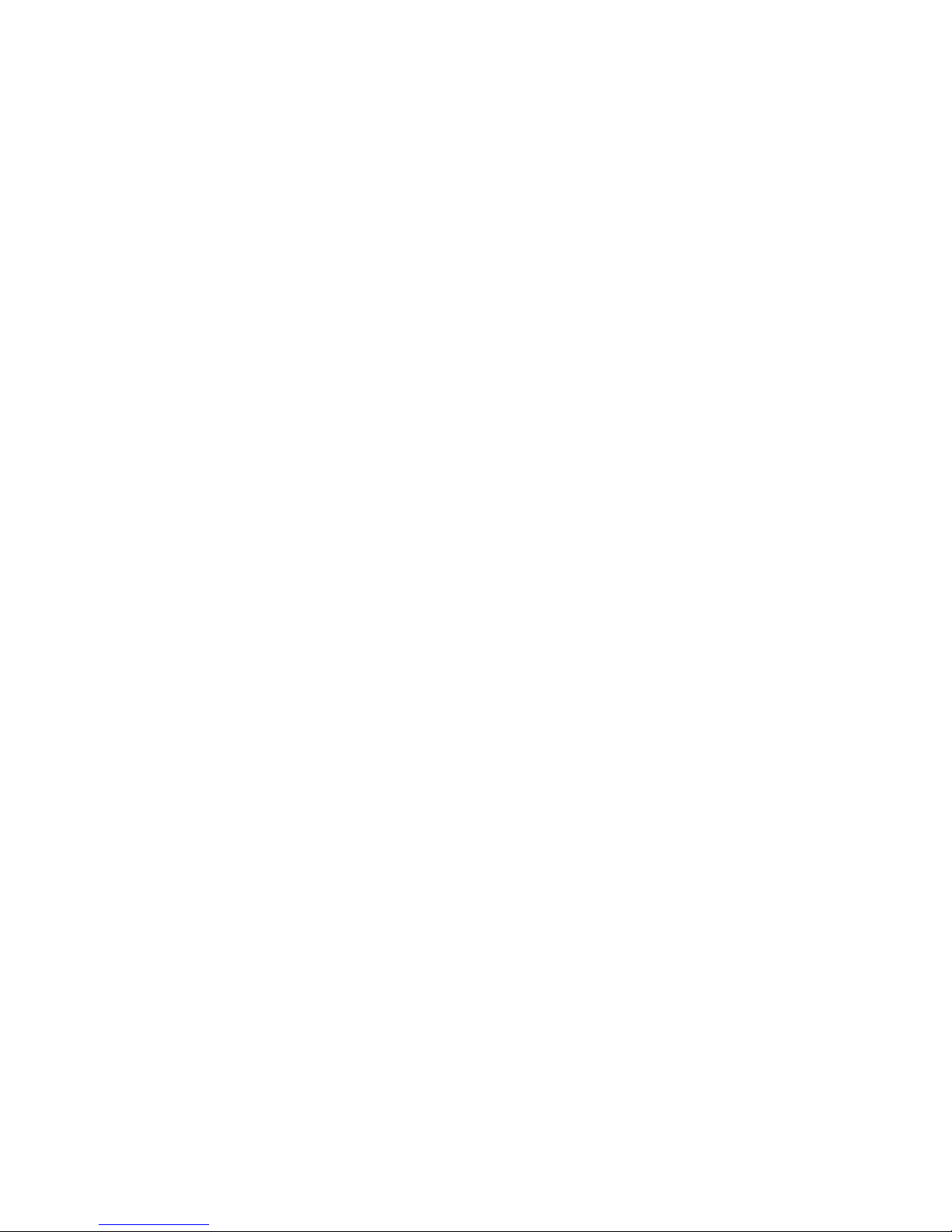
3-1
TWO-STROKE
As
the
piston
sion
in
the
crankcase
is
added
to
this
fuel
mixture
crankcase. The
the
charge
the
transfer
the
combustion
direction
exhaust
takes
place
charge
by
the
top
edge
to
leave
fer
port
out
while
closing
the
secondary
(charge)
in
the
port
and
in
port
respectively.
at
this
is
ignited
burning
of
the
the
cylinder. A little
and
the
the
piston
the
transfer
compression
leaves
air
in
next
crankcase
the
chamber
moving
time.
by
means
gases
piston
incoming
GENERAL
CYCLE
bottom
causing
the
then
time
pressurized
forces
uncovers
moves
port
air
proper
passes
the
and
side
of
toward
The
As
the
of
an
the
more
charge
past
and
mentioned
dead
proportion
piston
as
the
TDC
secondary
electric
the
subsequently
ENGINE
center
to
flow
thru
the
moves
the
charge
piston.
it
piston
piston
exhaust
travel
forces
BDC.
earlier.
SNOWMOBILE
(BDC),
in
thru
for
combustion
reed
spring
toward
top edge of
is
forced
The
closes
the
compression
nears
the
spark.
back
port,
of
the
the
As
it
moves
the
toward
the
piston
remaining
THEORY
it
creates a depres-
the
carburetor.
and
inlet
valve
BDC
it
compresses
the
piston
into
the
cylinder
piston
transfer
top
The
exhaust
then
port
of
of
the
pressure
BDC. When
burned
opens
back
gases
burned
toward
port
the
to
uncovers
reverses
and
the
charge
stroke
formed
the
trans-
gases
it
begins
Fuel
air-
the
on
the
this
the
begin
TDC
SECTION
INFORMATION
3
-
This
cycle
repeats
of
two
strokes
to
BDC.
a
two-stroke
It
can
be
the
same
engine.
four-stroke
transfer,
during
The
two
of
Consequently
cycle
seen
then
operation
intake,
cycle
secondary
strokes
CARBURETION
GaSOline,
flame.
the
mixture
effect.
portioned
accomplish
Gasoline
12:1
to
for
different
leaner
conditions;
tor
is
engine
The
and
valve
in
However,
becomes
To
obtain
and
thoroughly
this.
vapor
18:1 by
purposes.
mixture
avoid
designed
for
these
carburetor
system
its
weight.
is
to
various
itself
once
the
piston,
the
engine.
that
as
the
compression,
engine
compression,
of
the
liquid
when gaSOline
highly
best
results,
will
burn
desirable
lean
mixtures
deliver
is
essentially a simple
allows a constant
one
engine
the
two-stroke
more
commonly
become
piston.
state,
inflammable
the
mixed.
when
Mixtures
Idling
conditions.
requires a relatively
for
for
the
correct
each
engine
from
BDC
utilizing
cycle
power
the
induction,
power
burns
is
It
maximum
relatively
combined
fuel
is
the
mixed
of
different
high
speed
proportion
metering
fuel
revolution
to
this
basic
engine
understood
and
and
exhaust
with
and
burns
and
air
function of
with
air
proportions
economy
operation.
supply
which
consists
TDC
and
one
from
principle
achieves
four-stroke
exhaust
primary
all
Slowly
air
to
with
must
be
the
in a proportion
rich
under
of
fuel
device. A diaphragm
to
be
maintained
is
called
basically
strokes
compression,
form a vapor,
correctly
carburetor
are
The
and
taking
with
an
an
explosive
required
mixture;
normal
carbure-
air
of
place
to
in
TDC
cycle
the
even
pro-
to
from
load
the
the
INDUCED
-~~
LOW
PRESSURE
______
VENTURI
L
~·~*~n
---+
I=======~==~===
a
FUEL FORCED UPWARDS
BY ATMOSPHERIC PRESSURE
1713
6
Figure
3-1
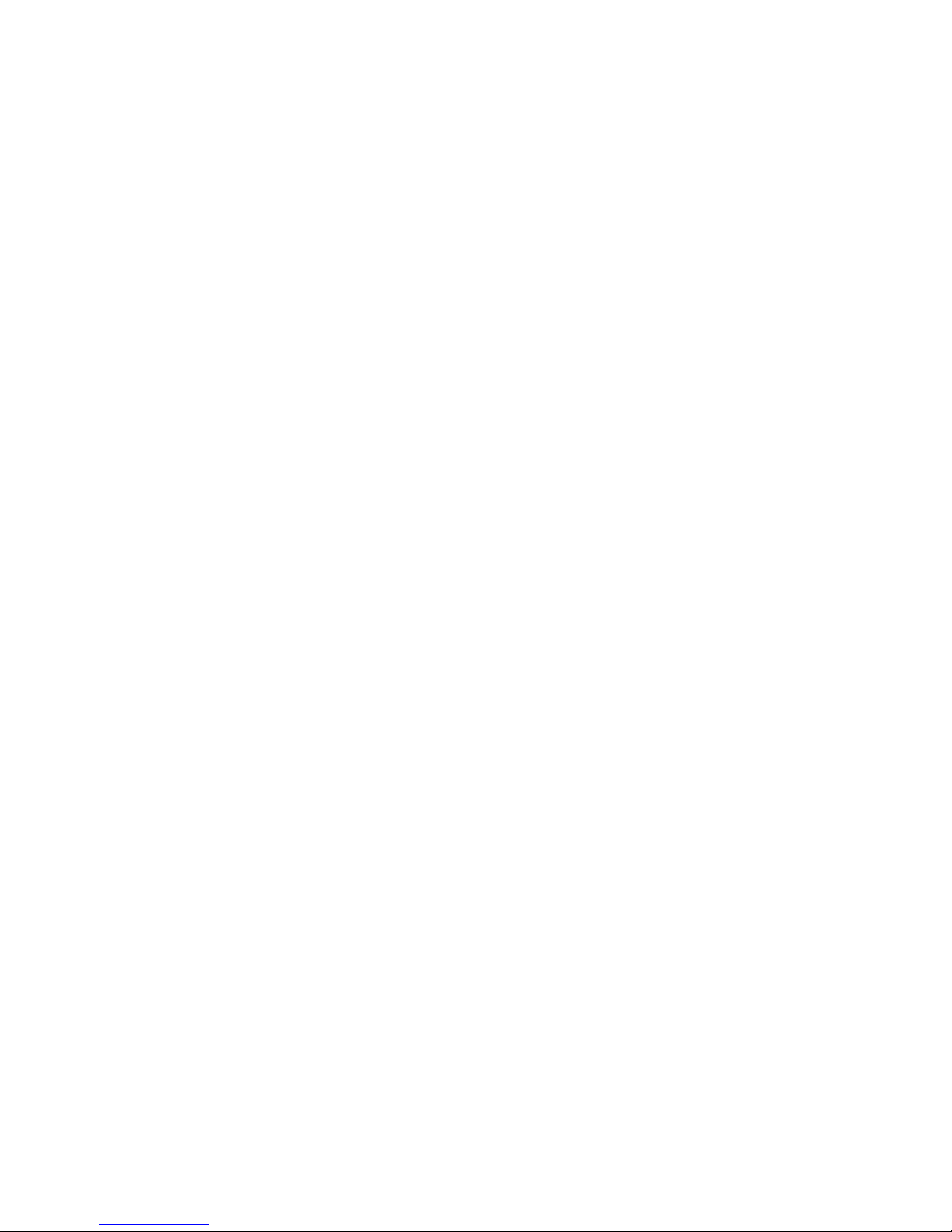
3-2
/'
/'
REED PLATE AND BASE ASSEM.
Figure
3- 2
metering
valves
chamber
suction
throat
Figure
'ij'
)
air
charge
swirled
A
drawn
throttle
drawn
A
ond
to
restrict
oline
fuel -
choke
flow
The
two
pose
thin,
fold and
When
170
88
crankcase.
(see
crankcase.
crankcase
sealing
closing
reeds
chamber
permit
to
which
. At a
3- 1). The
stream,
port.
about
throttle
through
opens
into
richer
shutter,
and
air
mixture.
is
from
system
cycle
as
the
flexible
crankcase.
the
Figure
off
may
must
at
just
a
precise
the
carburetor
draws
air
particular
venturi
creating a partial
As
it
is
the
air
butterfly
the
carburetor.
or
closes,
mixture
a choke,
of
air.
air
is
allowed
or
the
fuel
called
the
less
in
engine.
flow
When
opened
the
engine
and
carburetor.
which
consists
intake
metal
piston
is
the
controls
valves
strips
on
Atmospheric
3-2),
When
charge,
the
occur
be
opening
the
forcing
crankcase
in
thin
and
piston
flexible.
slightly
amount
throat.
through
point
has
rushed
stream
valve
regulating
is
required
is
When
normal
standard
of a
on a
mounted
the
up-stroke,
pressure
the
from
excess
the
the
vacuum
along to
and
in
placed
into
operating
the
set
four
the
is
on
reeds
the
of
below
of
The
the
throat
effect
vaporized.
the
throat
To
vary
the
for
into
the
choke
the
air
ratio
intake
of
valves
cycle
between
it
forces
passage
the
down-stroke,
against
carburetor.
seven
atmospheric
fuel
to flow
upstroke
leaf
valves
is
restricted
of
reducing
which
draws
the
firing
pressure.
from
of
the
and the
air
fuel
chamber,
regulates
the
speed
amount
of
starting a cold
the
throat
forward
shutter
stream
is
closed,
resulting
temperature
of
gasoline
of
the
which
engine.
the
and
fuel-air
serve
The
carburetor
creates a partial
the
reeds
away
between
the
it
the
passage
8ince
thousand
times
Needle
the
metering
piston
creates
carburetor
by a
venturi
pressure
from
the
the
fuel
the
amount
of
the
engine,
fuel-air
mixture
engine. A sec-
of
the
more
in a richer
is
reached,
air
allowed
mixture
the
same
reed
valves
intake
vacuum
from
the
carburetor
compresses
opening, and
the
opening
per
minute,
(see
in
the
dis
of
air
the
jets,
gas-
the
in
the
pur-
are
mani-
in
the
body
and
the
and
the
is
to
a
I
-
IGNITION
Two
charge
the
flywheel.
alternator
as
the
flywheel
300
volts
in
the
Power
part
of
the
One
thing
coils.
RPM,
Power
generates
Power
automatic
The
small
electronic
the
300
plug. When
and
sensor
reverse
the
volts
coil
other
ignition
spark
opens
second
a
electronic
into
COils,
The
same
stator
also
rotates.
A.C.
is
converted
Pack
28
flywheel hub,
to
Below
the
Pack
note
the
retard
28. At
enough
Pack
28
before
electronic
voltage
switches
stored
steps
the
the
allows
the
magnet
polarity
switch
voltage
in
ignition
are
mounted on
flywheel
generate
No
external
to D.C.
capacitor.
passes
in
this
idle
RPM
sensor
RPMs
voltage
to
the
advance
generated
in
the
POWER PACK 28.
in
the
capacitor
voltage
capaCitor
charge
gap,
the
coils
opposite
in
the
POWER PACK 28, and
magnets
about 300
in
One gap
the
sensor
h
lw,lm
U NOTE
system
range
turns
over
turn
retard
built
in
the
up
to
is
to
in
sensor
the
on
coil.
alternator
which
volts
voltage
the
source
Power
between
coil,
is
that
and
up to
the
electronic
900
the
on
the
electronic
sensor
into
into
the
sensor
one of
30,000
does.
system.
coil
volts,
discharged,
again
charge
polarity
coil.
from
This
discharges
stator,
induce
A.C.
Pack
also
there
in
is
the
under
are
current
the
required.
28,
sensor
two
apprOximately
switch
advance
sensor
switch
80, we
activates
This
switch
the
ignition
which
the
electronic
the
capacitor.
the
first,
activates
located
charge
and
is
magnets,
the
flywheel.
sensor
900
in
the
coil
in
the
have
one
discharges
coils.
is
fed
generates
the
second
the
capacitor
under
in
the
coils
The
stored
an
of
two
The
to
the
switch
The
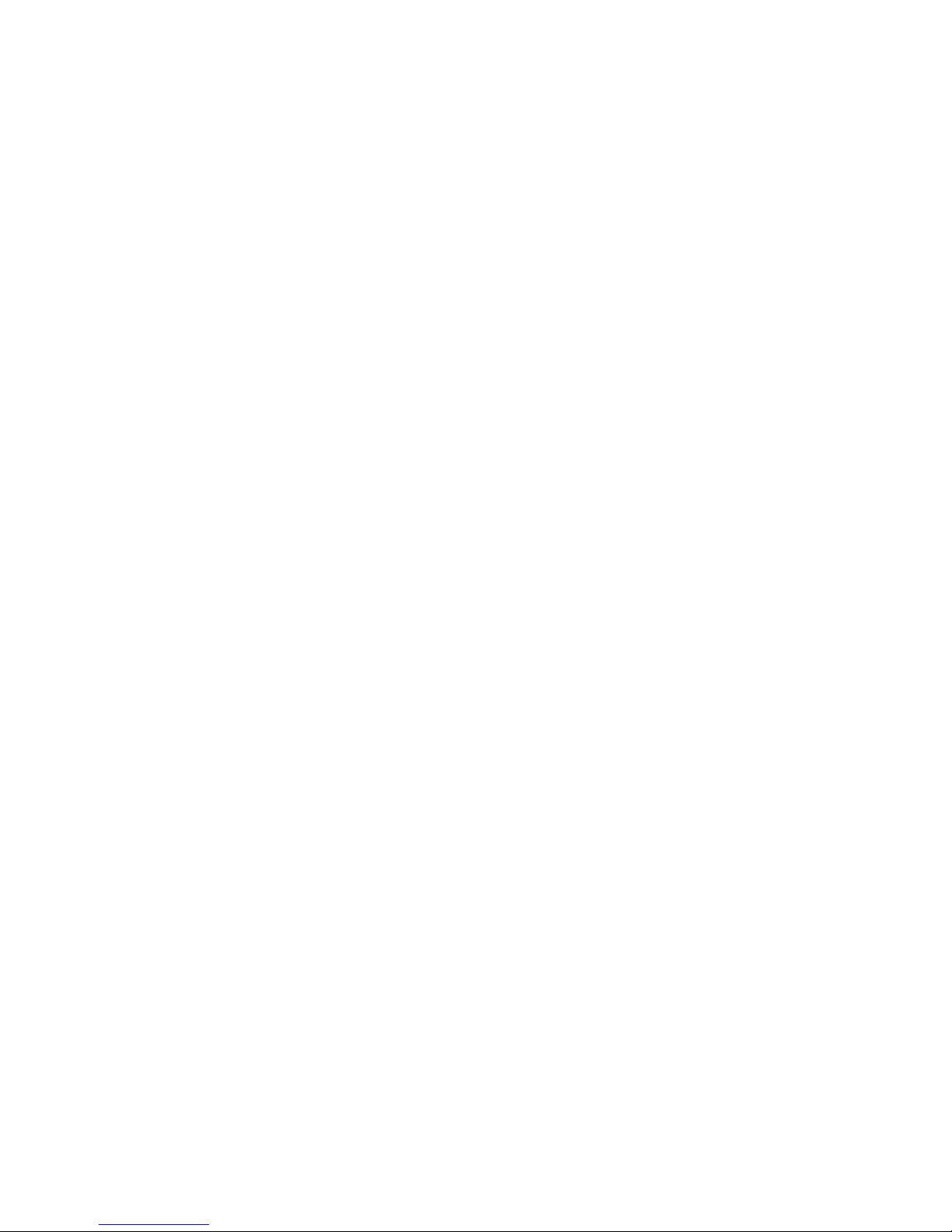
3-3
LIGHTING
The
The
alternator
at
approximately
alternator
frequency
speed.
POWER
The
The
axle
than
primary
engine
transmission
which
assembly
assembly
the
primary
belt.
belt
when
is
belt
sheave
halves
sheave
front
sheave
sheave
eter
transmission
PRIMARY DRIVE
mission
the
transmission
primary
sembly
movable
SYSTEM
coils
A.C.
FLOW
assembly
propels
is
attached
has
sheave
the
rotating
rides
assembly
are
separated
half.
produce
output
the
its
own
sheave
is
centrifugally
engine
at
on a
(see
alternating
constant
is
used
transmits
vehicle
directly
mounting
assembly.
speed
idle
speed
ball
Figure
by a
E
voltage
to
operate
power
along
to
the
crankshaft.
pedestal
The
operated
reaches
or
below
bearing
3 -3) .
compression
current
in
lamps.
the
3000 - 3600
between
The
which
proportion
from
the
track.
and
is
two
are
and
engages
3000 - 3600
primary
spring
changes
to
engine
The
The
larger
connected
RPM.
the
halves
sheave
in
the
the
engine
to
the
primary
secondary
in
diam-
by
the
trans
When
RPM,
the
of
the
as-
hub
of
the
in
a
-
-
As
the
spring
axially
together,
diameter
Figure
sheave
eter.
presenting
the
in
against
halves
In
speed
B
0
N
M
L
engine
the
the
of
3-4).
this
the
at
speed
end
cap
the
transmission
the
primary
Since
spread
way,
the
engine
which
it
TRANSMISSION
increases,
outward
movable
the
apart,
with a
is
operating.
sheave
belt
sheave
belt
allowing
engine
mechanical
LOCKED
Figure
centrifugal
against
half.
is
forced
assembly,
length
the
transmits
IN
NEUTRAL
3-3
the
remains
belt
power
advantage
effect
contour
As
the
outward
increasing
constant,
to
ride
through a variable
forces a garter
of
sheaves
to
ride
on a
most
the
end
are
on a
belt
speed
the
secondary
smaller
favorable
G
cap
and
brought
larger
(see
diam
ratio,
for
Flywheel
A.
B.
Emergency
Sheave
C.
Garter
Spring
D.
End
E.
Movable
F.
Transmission
G.
Fixed
H.
Ball
Spring
I.
J.
Compression
K.
Neutral
L.
Splined
M.
Bolt,
Shaft
N.
Spring
o.
Neutral
P.
Spacer
-
Nut
Starting
(Activating)
Cap
Half
of
Sheave
Belt
Sheave/Flywheel
Bearin
g
Cup
Spring
Lockout
Shaft
End
Lockout
Balls
(crankshaft)
Cap
to
Splined
Rod
37138
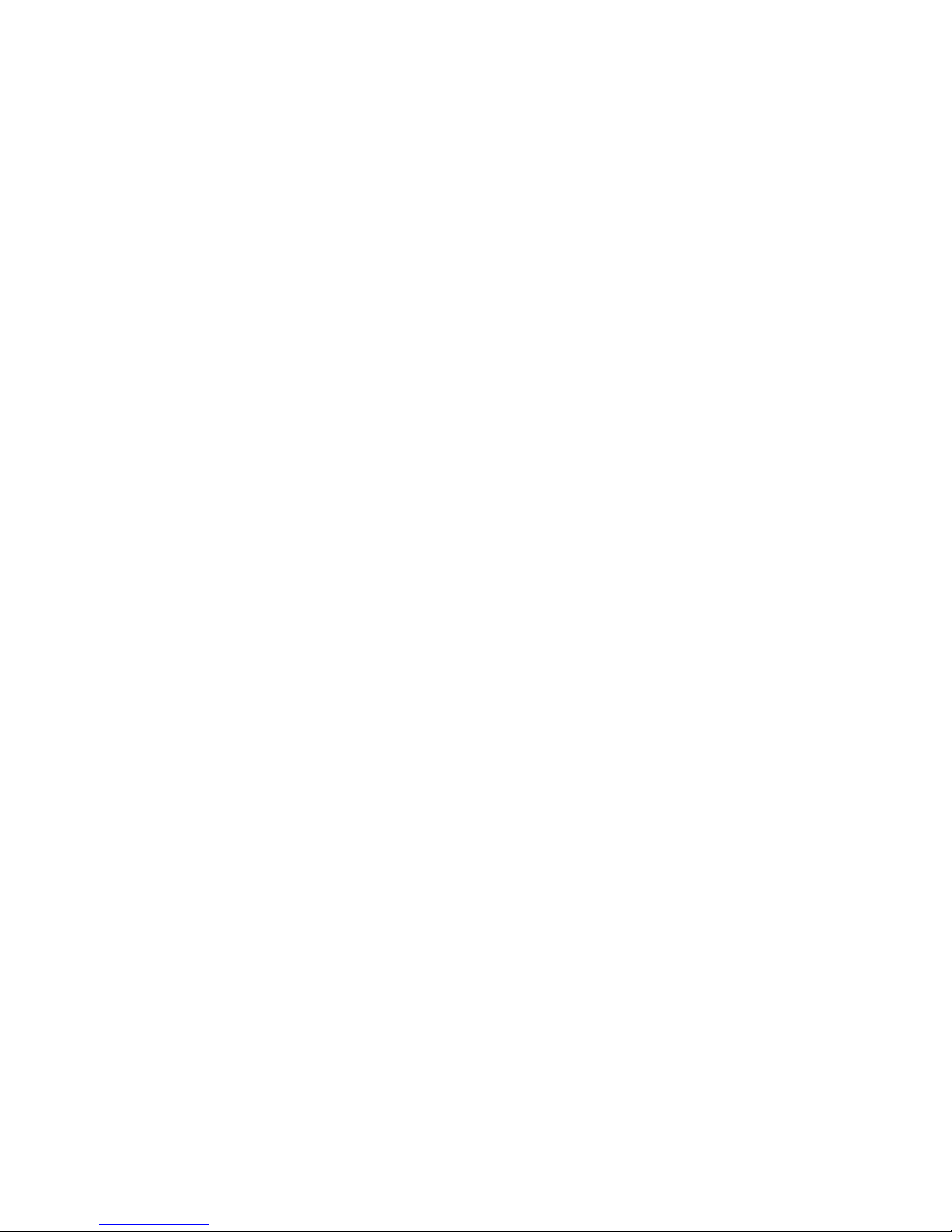
3-4
NEUTRAL
CONTROL
A neutral control mechanism
ing
during
plunger
through
the
movable
neutral
is
below
starting,
is
actuated, a cone
the
splines
sheave
control
is
spring
approximately
warm-up
of
the
half,
2000
is
period,
on
the
primary
preventing
actuated
RPM.
used
and
end
sheave
and
to
prevent the drive from engag-
idle.
When
the
neutral
of
the
it
will
from
plunger
assembly
engaging
engage
and
only
raises
into
the
when
two
the
belt.
the
lockout
balls
path
of
The
engine
)
TRANSMISSION HIGH
POSITION -
BELT
ENGAGED
SPEED
Figure
3-4
371
39
When
the
engine
spring
spring
sheave
covered
not
reduced
movable
be
will
will
toward
the
pushed
to
below
half
expand
then
the
holes
into
of
the
ride
2000
SECONDARY DRIVE
The
that
The
gether
the
drive
The
yields
mitted
the
front
secondary
detects
mechanism
to
lower
chain
drive
an
overall
from
axle.
drive
the
need
immediately
the
and
ratio
drive
the
secondary
NEUTRAL
FUNCTIONING BECAUSE
RPM
is
running
by
centrifugal
up
fixed
in
the
the
sheave
TOO HIGH
the
sheave.
splined
locked
RPM,
to
CONTROL NOT
above
ramp
the
move
mechanism
for
more
forces
transmission
track.
varies
from 3 to 1 in
range
of
approximately
sheave
Figure
3-5
approximately
effect.
In
shaft
position.
garter
away
of
dOing
the
and
from
See
end
this,
the
If
spring
Figure
cap
the
neutral
the
will
the
incorporates a torque
power
for
the
ratio
assembly
steep
secondary
and
provide a higher
low
to 1 to
4.4
through a drive
2000
3-5.
and
push
movable
lockout
engine
close
fixed
sheave.
inclines
sheaves
.68
to
1.
RPM
the
speed
and
sensing
or
in
Power
the
The
movable
sheave
balls
allow
deep
closer
torque
high
is
chain
37140
garter
garter
has
can
is
now
the
device
snow.
to-
to
which
trans
to
-
The
17:39
ratio
or
between
19:39.
the
secondary
sheave
assembly
and
the
front
axle
is

4-1
DESCRIPTION
This
section
chine.
formance
snow
systematic
be
ance
which
mixtures,
Engine
discussed
outlined
Familiarity
an
is a great
Steps
are
Being
able
machine
located
Any
1.
2.
3.
Familiarity
engine
and
service
Identifying
Determining
Correcting
is
important
affect
compression,
theory,
on
asset
to
outlined.
to
is
approach
identified
operation
with
engine
in
Section
page
with
are
provides
be
locate
as
the
the
the
compression,
factors
similiarly
here.
trouble
followed
the
important
to
trouble
in
oan
problem
cause
problem.
the
factors
in
making a correct
performance
ignition,
3.
Correct
iv,
and
which
shooting
in
determining
cause
minimum
of
helpful.
of
as
shooting
be
broken
the
problem,
which
include
and
carburetion,
fuel
blending
contribute
trouble
being
time.
down
affect
proper
fuel
The
procedures
causes
in
able
to
is
important
into
and
two-cycle
service
the
quality
drive
ignition
mixture
is
discussed
to
abnormal
skilled
for
of
unsatisfactory
an
improperly
correct
if
three
steps:
diagnosis.
of
system
and
for
this
mechanic's
TROUBLE
the
snow
operating
the
trouble.
the
trouble
engine
perform-
Factors
the
fuel
and
adjustment.
power
performance
flow
snowmobile
in
Section
experience
ma-
per-
is
fuel
are
12.
to
is
of
A
SECTION
SHOOTING
4
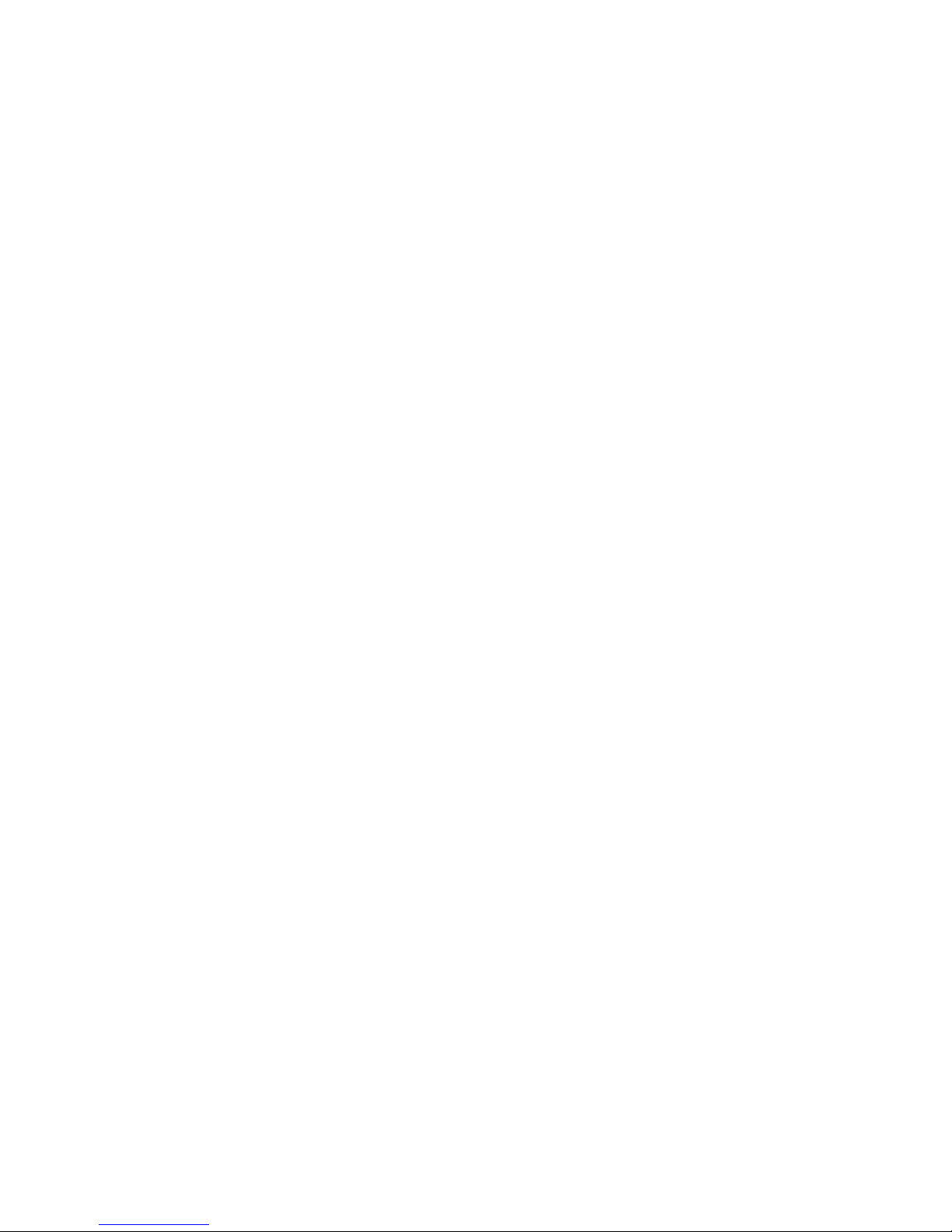
4-2
TROUBLE
PROCEDURES
Trouble
operating
lowing
a.
b.
c.
performance.
An
for
trouble
provide
clue
to
A
preliminary
ing
checks.
a.
b.
c.
d.
e.
f.
revolution
pression
STARTING
1.
a.
shooting
problem
steps:
Obtaining
Preliminary
Use
accurate
the
Correct
Throttle
Tank
mixture
Spark
Carburetor
Compression.
recoil
can
spin
Hard
Empty
an
of
Trouble
description
shooting.
valuable
cause
spark
linkage
filled
at
each
starter.
be
felt
exists
very
easily.
to
start
gas
of
SHOOTING
to
determine
may
be
broken
accurate
inspection.
information
of
the
inspection
plugs
with
spark
adjusted
Turn
when
the
or
tank
description
Check
of
The
problem.
should
properly
fresh,
plug
correctly
flywheel by
If
compression
turning
flywheel.
in
both
won't
start
Chart
the
trouble
owner's
which
include
adjusted
clean
through
If
cylinders,
the
cause
down
of
to
analyze
comments
will
fuel
of
hand
is
one
little
of
into
the
the
trouble.
engine
is
essential
serve
the
follow-
the
proper
or
present,
complete
or
no
engine
any
fol-
may
as
with
com-
will
it
m.
Faulty
n.
Spark plugs fouled, dirty
o.
Loose
ignition
p.
Sheared
q.
Faulty
r.
Key
wire
s.
Binding
a
t.
Faulty
or
2. Engine
a.
Cylinder
bearing
b.
Engine
3.
Cranks
a.
Spark
b.
Cylinder
c.
Rings
d.
Faulty
4.
Won't
a.
Spark
b.
Reed
c.
Timing
light)
gaskets
or
broken
system
flywheel
coils
switch,
in
engine
sensor,
connecting
won't
turn
wall
improperly
over
extremely
plug(s)
or
worn
or
cylinder
start,
but
plug
leads
valves
out
of
wire
wiring
key
connector
charge
wiring.
over
corrosion,
loose
pistons
carboned
head
kicks
crossed
broken
adjustment
or
or
coils,
assembled
easily
scored
gasket
back
and
or
not
or
broken
frayed
grounded
Power
seized
backfires
seating
(check
insulation
switch
Pack
piston
after
repair
with
timing
)
in
2S
or
b.
Incorrect
c.
Old fuel,
d.
Fuel
e.
Fuel
f.
Engine
g.
Clogged
h.
Clogged
i.
Carburetor
j.
Low
k.
Engine
1.
Reed
gas-lubricant
or
line
improperly
line
kinked
not
fuel
check
speed
flooded
valves
water
or
or
severely
primed
line
or
valve
adjustments
needle
bent
not
functioning
ratio
dirt
in
connected
fuel
filter
too
or
bowed
fuel
pinched
lean
properly
system
d.
e.
5. No
a.
b.
6. No
a.
b.
c.
d.
e.
Retard
Power
spark
Faulty
Faulty
spark
Faulty
Faulty
Faulty
Grounded
Broken
Pack
one
ignition
Power
both
charge
sensor
Power
or
sensor
2S
cylinder
cylinders
ignition
poor
faulty
faulty
coil,
Pack
coil
coils
Pack
ground
Wire,
2S
2S
switch
or
or
and/or
out
of
adjustment
connections
wire
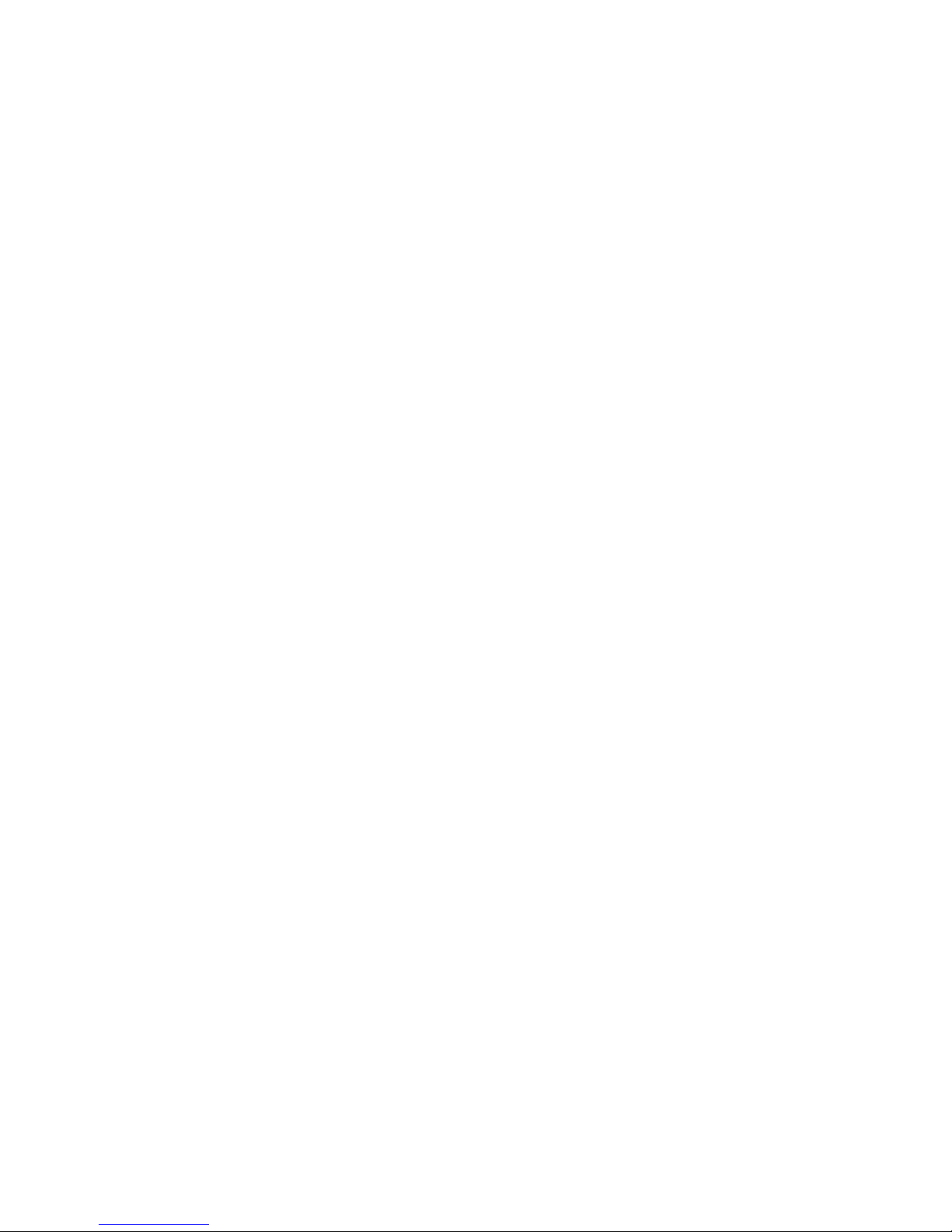
--------
~
f.
Flywheel
-
---
4-3
not
properly
charged
b.
Loose
or
corroded
connections
(
g.
Faulty
7.
Weak
a.
Ignition
b.
Weak
c.
Weak
d.
Weak
e.
Poor
8.
Engine
out
a.
Fuel
b.
Carburetor
c.
Fuel
d.
Fuel
inlet
e.
Carburetor
STARTING - MANUAL
1.
Manual
engage
a.
Friction
b.
Pinion
c.
Pinion
d.
Roll
2.
Starter
a.
Return
b.
Grease
c.
Not
3.
Clattering
a.
Bearing
b.
Pinion
c.
Main
d.
Pinion
spark
when
enough
ignition
both
switch
charge
Power
ignition
ground
can
be
primer
pump
inoperative
line
to
filter
screen
screen
starter
flywheel
spring
or
rope
frozen
pin
fallen
rope
does
spring
on
return
manual
missing
or
rope
spring
return
Pack
started
needle
carburetor
clogged
inoperative
preload
improperly
coils
cylinders
or
connection
coil
output
2S
coil
output
by
is
not
used
valves
in
STARTER
pulls
out,
bent
pulley
(water)
out
or
not
return
broken
spring
on
starter
or
worn
pulley
spring
or
leads
output
using
clogged
fuel
pump
but
burred
in
place
broken
or
binding
return
worn
assembled
broken
leakage
primer,
closed
starter
spring
or
carburetor
but
does
dies
not
c.
Faulty
d.
Worn
armature
e.
Faulty
2.
Starter
a.
b.
c.
d.
e.
f.
g.
h.
i.
RUNNING - LOW
1.
Low
a.
b.
c.
d.
e.
f.
g.
h.
i.
j.
k.
will
Weak
battery
Loose
or
Broken
Faulty
ignition
Faulty
MOisture
Broken
springs
Faulty
Dirty
Incorrect
Carburetor
rich
Reed
Spark
Loose
Spark
Weak
Cylinder
aged
Leaking
seal
Arcing
nition
Loose
of
2S,
switch
starter
bendix
speed
valve
plugs
or
plug
coil
switch
connections
leads
charge
starter
armature
not
corroded
wire
in
or
armature
SPEED
miss
broken
crankcase
around
solenoid
brushes
crank
in
harness
key
solenOid
starter
worn
ONLY
gas -lubricant
idle
standing
dirty
ignition
terminal
output
gasket
ignition
in
the:
coils,
or
or
(shorted
engine
connections
or
switch
or
motor
brushes
(shorted
ratio
adjustment
open
or
broken
coil
loose
or
reed
gaskets
coils
or
intermittent
ignition
sensor
solenoid
springs
or
open
connector
solenOid
or
bendix
or
broken
or
open
too
lean
or
preloaded
wires
plate
gasket
or
or
arCing
coil,
Power
coils,
and
wiring
windin
gs)
wiring
brush
windings)
or
too
shut
dam-
crankshaft
in
ig-
grounding
Pack
ignition
ST ARTING -
1.
Starter
a.
Weak
ELECTRIC
cranks
too
battery
STARTER
slowly
RUNNING - HIGH
1.
High
speed
a.
Water
in
SPEED
miss
fuel
ONLY
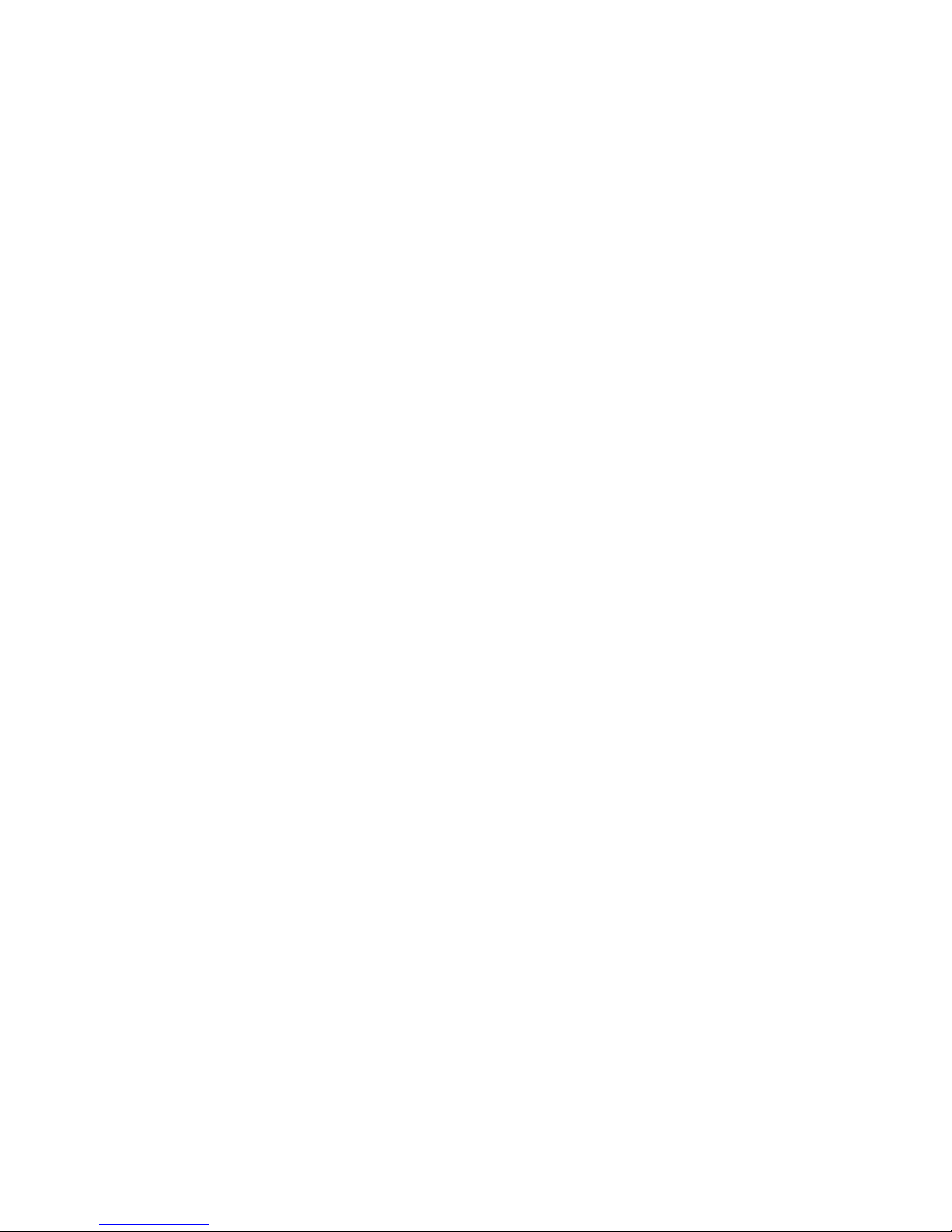
4-4
2.
b.
c.
d.
e.
f.
g.
h.
i.
j.
Poor
a.
b.
c.
d.
Carburetor
Spark
plugs
Ignition
Engine
coil -weak
improperly
Exhaust
Combustion
Arcing
nition
Loose
of
2S,
around
switch
connections
leads
charge
switch
Check
valve
acceleration,
Incorrect
Old
fuel
Fuel
hoses
Fuel
filter
retor)
inlet
needle
dirty
or
cracked
output
timed
ports
or
exhaust
chambers
ignition
or
in
the:
ignition
COils,
sensor
needle
top
sticking
rpm
gas -lubricant
plugged
or
restricted
sticking
insulator
system
carboned
coils
or
intermittent
COil,
COils,
is
low
ratio
kinked
(fuel
pump
carboned
arcing
grounding
Power
and
ignition
or
in
Pack
carbu-
ig-
c.
4.
Faulty
d.
Faulty
e.
Fuel
f.
High
g.
Dirt
h.
Choke
i.
High
j.
Advance
Engine
fuel
check
tank
speed
behind
partly
speed
sensor
runs
pump
valve
vent
nozzle
needles
closed
needle
at
high
or
clogged
faulty
primer
a.
Fuel
lines
b.
Fuel
c.
Fuel
d.
Dirt
e.
Carburetor
f.
Fuel
line
leaks
pump
behind
cap
vent
filters
or
or
not
supplying
needles
adjustments
clogged
RUNNING - HIGH AND LOW
pulse
clogged
and
set
too
speed
passages
fuel
filter
or
seats
SPEED
line
seats
lean
only
obstructed
enough
or
rich
by
using
obstructed
fuel
hand
3.
m.
q.
Idles
a.
e.
Fuel
f.
Incorrect
g.
Faulty
h.
Inlet
i.
No
j.
Spark
k.
Loose,
sion
1.
Ignition
Reed
n.
Piston
o.
Excessive
head
p.
Exhaust
Charge
throttle
Fuel
b.
Fuel
pump
needle
spark
plugs
leads
valves
well,
lines
filter
or
carburetor
check
advance
broken,
coil
rings
carbon
ports
coils,
but
or
clogged
pulse
valve
and
seat
dirty
or
badly
weak
output
not
properly
stuck
or
on
or
exhaust
Power
acceleration
passages
line
faulty
adjustments
worn
or
insulated
seated,
piston
scored
pistons
system
Pack
2S
poor,
obstructed
sticky
and
carboned
faulty
high
or
dies
ten-
broken
cylinder
up
at
full
1.
2.
3.
Engine
a.
Incorrect
mixed
b.
Engine
pair
c.
Lean
d.
COOling
e.
Fan
Engine
a.
No
b.
Rod
c.
Cylinder
d.
Fan
e.
Cooling
Engine
a.
Incorrect
b.
Flywheel
c.
Carbon
ports,
overheats
gas -lubricant
fuel
not
(binding)
mixture
fan
belt
broken
seizes
lubricant
or
main
or
belt
broken
fan
knocks
gas -lubricant
loose
in
or
on
assembled
(carburetor
obstructed
or
slipping
(stops
suddenly)
in
gas,
or
bearing
piston
scored
obstructed
excessively
combustion
pistons
ratio
correctly
adjustment)
no
fuel
seized
or
ratio
chambers
or
seized
and
improperly
during
re-
exhaust

(
d.
e.
f.
4.
Excessive
a.
b.
c.
5.
Vibrates
a.
b.
c.
d.
Worn
or
loose
Loose
assemblies,
Manual
Carburetor
Deteriorated
Carburetor
Too
Idle
Air
Faulty
starter
fuel
excessively
much
or
high
passage
ignition
bearings,
pinion
consumption
casting
carburetor
improperly
lubricant
speed
needles
to
carburetor
bolts,
hitting
porous
adjusted
or
runs
mixed
or
pistons
or
screws
the
gaskets
rough
with
gas
too
rich
obstructed
flywheel
and
smokes
7.
8.
f.
g.
b.
c.
d.
Spark
a.
b.
e.
Cylinder
High
Spark
Engine
a.
Spark
Grounding
Ignition
Grounding
switch
e.
Loose
coils,
on
Ignition
Power
scored
speed
adjustment
plugs
misfires
plugs
coil
or
wire
connections
Power
only
one
coils
Pack
or
fouled
dirty,
or
leakage
faulty
leakage
or
connection
Pack
cylinder
2S
output
rings
lean
or
misfiring
fouled
at:
2S,
and
stuck
of
secondary
of
ignition
ignition
sensor
coils,
coils
4-5
leads
switch,
charge
e.
6. No
a.
b.
c.
d.
Deteriorated
power
under
Faulty
Faulty
Ignition
Carbon
ports,
carburetion
ignition
timing
build-up
or
exhaust
engine
heavy
coil(s)
off
system
mounts/washers
load
on
piston
head,
exhaust
9.
Engine
erating
a.
Check
b.
Check
c.
Check
10.
Transmission
a.
Sheaves
will
advance
Power
timing
are
start
belt
and
sensor
Pack
out
idle,
2S
flips
of
alignment
coil
output
over
but
and
in
quits
leads
sheaves
(see
Section
on
accel-
10)
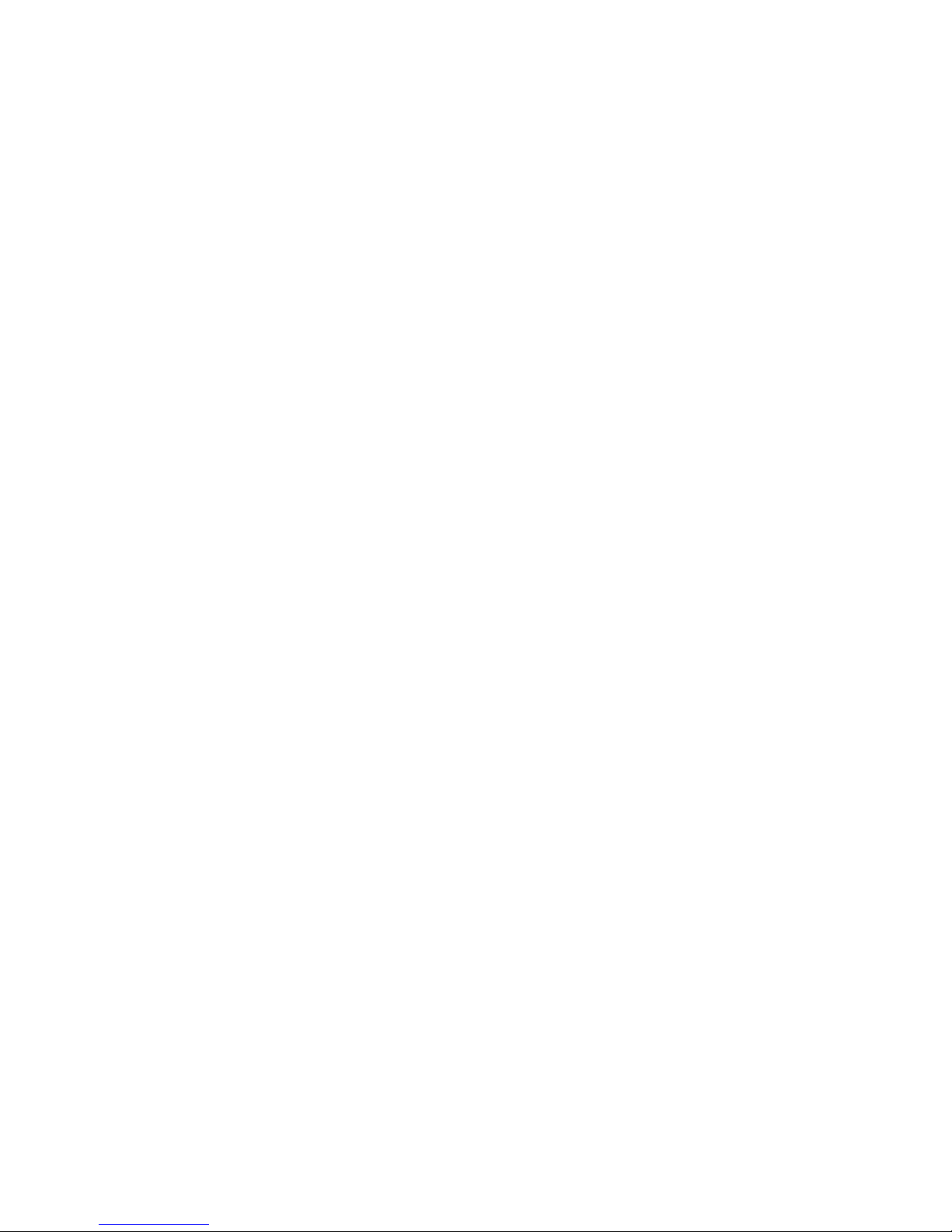
)
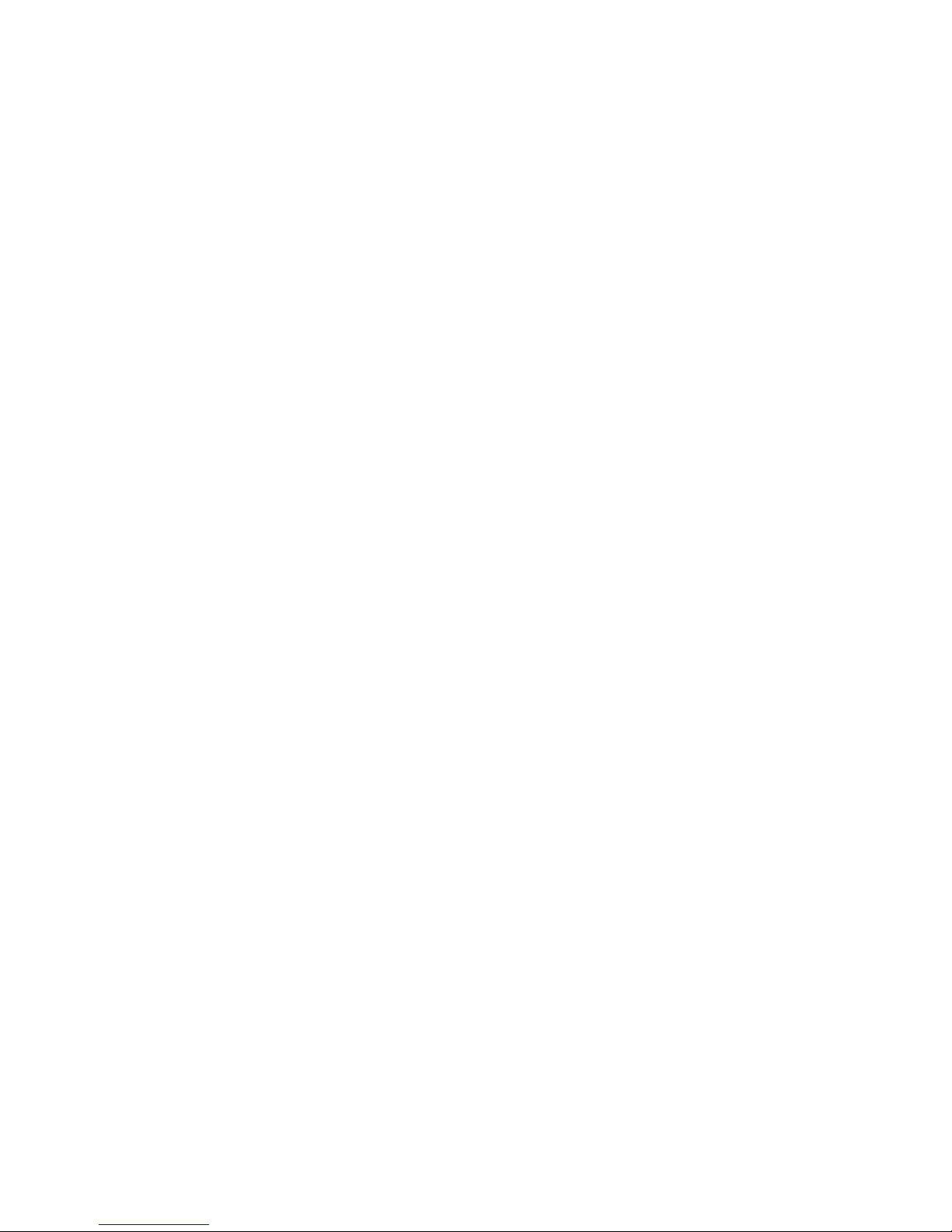
5-1
r
(
DESCRIPTION
The
purpose
have
been
lost
the
snow
machine.
an
understanding
miliarity
plete
and
dures
with
tune-up
to
and
procedures.
Section 4 for
instructions
factors
FACTORS
In
the
aware
long
assured
preferably
It
ing
obtained
by
correcting
normal
of
the
period
if a complete
at
is
seldom
one
or
two
by following a
decrease
of
the
advisable
items
all
of a
tune-up
through
of
wear
The
successful
principles
affecting
trouble
for
AFFECTING
operation
in
time.
start
items
Economical,
tune-up
of
the
to
only.
definite
affecting
is
to
restore
or
deterioration
of
two-cycle
performance.
Refer
to
Section 3 for
shooting
storage
performance
attempt
of
an
season.
Time
and
power
are
engine,
is
performed
to
will
power
completion
procedures.
included
and
of
of a tune-up
engine
This
principles
in
Section
PERFORMANCE
the
operator
which
takes
trouble-free
improve
be
saved
thorough
and
performance.
operation
at
performance
and
procedure
TUNE-UP
performance
one
or
more
operation,
section
Lubrication
12.
may
place
slowly
least
once
more
lasting
of
parts
depends
and a fa-
gives
of
operation,
proce-
not
be
can
best
each
by
correct-
results
analysis
which
com-
fully
over
year,
and
of
on
be
SECTION
5
PROCEDURES
a
FUEL
SYSTEM
A
fresh
fuel
mixture,
is
necessary
emptied
at
the
ture
may
fuel
delivery,
effect
ments
eration
hard
starting,
discussion
IGNITION SYSTEM
A good
formance.
system
speed
are
frequently
the
operation
theory,
COMPRESSION
Comp~'ession
cylinde'C
check
is
cannot
that
compression
for
peak
of
old
fuel,
beginning
cause
high
may
or
ignition
components,
performance.
and
to
important
be
of
hard
as
speed
cause
incorrect
rough
on
carburetion.
A
weak
checked
of
the
Section 7 for
must
realize
tuned
successfully
with
engine
rinsed
the
season
starting,
the
result
performance.
operating
use
of
running,
system
because
be
is
spark,
will
cause
The
spark
first
engine.
complete
be
well
maximum
checked
the
correct
performance.
out,
installed
and
stalling,
of
a faulty
Incorrect
difficulties
the
manual
or
poor
of
prime
which
hard
plugs
in a
tune-up
See
Section 3 for a discussion
ignition
sealed
power
an engine with low
to
give
before
ratio
The
and
at
every
and
faulty
fuel
at
any
choke
fuel
economy.
importance
may
be
starting,
and
ignition
because
system
by
the
piston
and
performance. A compression
peak
performance.
proceeding
of
lubricant
tank
refilled
tune-up. A stale
operation.
pump
or
carburetor
speed.
by
the
operator
for
the
result
misfiring,
system
of
analysis.
and
or
uneven
with
should
with a
clogged
needle
Faulty
See
Section 3 for
peak
of
faulty
or
their
importance
piston
It
an
engine
and
be
compression
gasoline,
removed,
fresh
supply
fuel
mix-
Inadequate
filter,
will
adjust-
choke
op-
may
cause
engine
components
rings
is
ignition
poor
high-
on
ignition
in
essential
tune-up.
per-
the
a
to
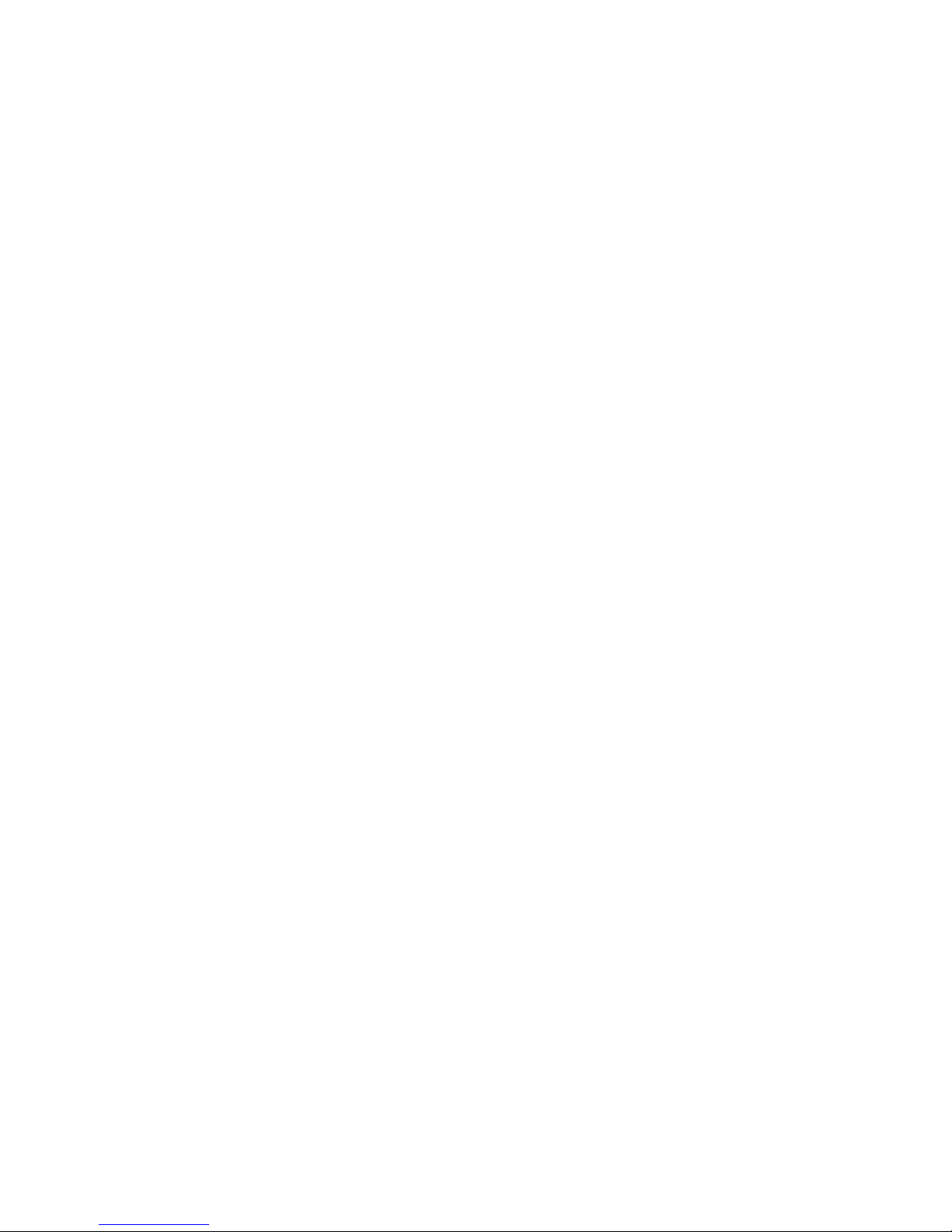
5-2
NEW
Complete
included
each
understands
of
eration.
a.
b.
c.
d. Caution the
e.
VEHICLE
in
snowmobile.
important
Be
sure
gaskets
Be
sure
terminals.
Be
sure
mixture
power
time,
tomer
Manual.
Be
sure
correctly,
TUNE-UP
instructions
the
Owner's
the
instructions
things
spark
in
place.
spark
the
correct
into
tank
customer
until
at
short
periods
to
follow
that
the
especially
PROCEDURES
DELIVERY
for
putting
Manual and
Be
sure
the
given
to
check
plugs
least
the
are
plug
wires
gasoline
through
not
one tankful of fuel
of
full
break-in
customer
such
a new
assembly
customer
in
it.
when
putting
installed
are
and
a fine
mesh
to
operate
power
procedure
understands
things
snowmobile
instructions
receives
The following
a new
and
torqued
securely
lubricant
a new engine
may
as
the
mixture
strainer.
has
been
be
used.
described
how to
neutral
attached
into
operation
packed
this
manual
listis a reminder
snowmobile
with
is
at
continuous
used. During
Instruct
in
operate
control
to
used.
the
and
into
spark
spark
the
Owner's
the
engine
choke.
are
with
and
op-
plug
plug
Pour
full
this
cus-
Components
vided
into
three
1.
items
affecting
2.
items
affecting
3.
items
Any tune - up
Correction
all
items
affecting
factorily.
fiCiencies by
performance
those
ing
for
tion
shooting,
a.
Attempts
parts
performance.
4.
Repair
is
Test
run
1.
Neutral
Can
and
2.
Function of
which
affecting
procedure
of
items
altering
or
of a tune -up which
covered
vehicle,
transmission
engine
affect
groups,
compression,
ignition,
carburetion.
affecting
compression
to
increased
and
replacement
in
checking
control
at
idle
brake
namely:
should
overcome
carburetor
fuel
Trouble
Sections 6 through
be
speed?
engine
locked
power
cover
carburetion
and
ignition
compression
settings
consumption.
involve
shooting
of
parts,
particularly
in
and
performance
these
groups
should
have
or
will
This
adjustments,
procedures
as
determined
11.
the
following:
neutral
when
in
not
be
been
corrected
ignition
result
section
cleaning,
are
machine
can
the
order
attempted
system
in
poor
covers
and
covered
through
is
be
di
given.
until
satis-
de-
overall
only
check-
in
Sec-
trouble
at
rest
-
3.
Engine
4.
Ski
5.
After
neutral
celerate
control
performance
alignment
running
control
engine
cannot
and handling
snowmobile,
knob out to
to
see
if
be engaged
reduce
lock
transmission
engine
transmission
above
approximately
speed
is
in
neutral.
to
in
idle
and
neutral.
Neutral
2000
pull
Ac-
RPM.