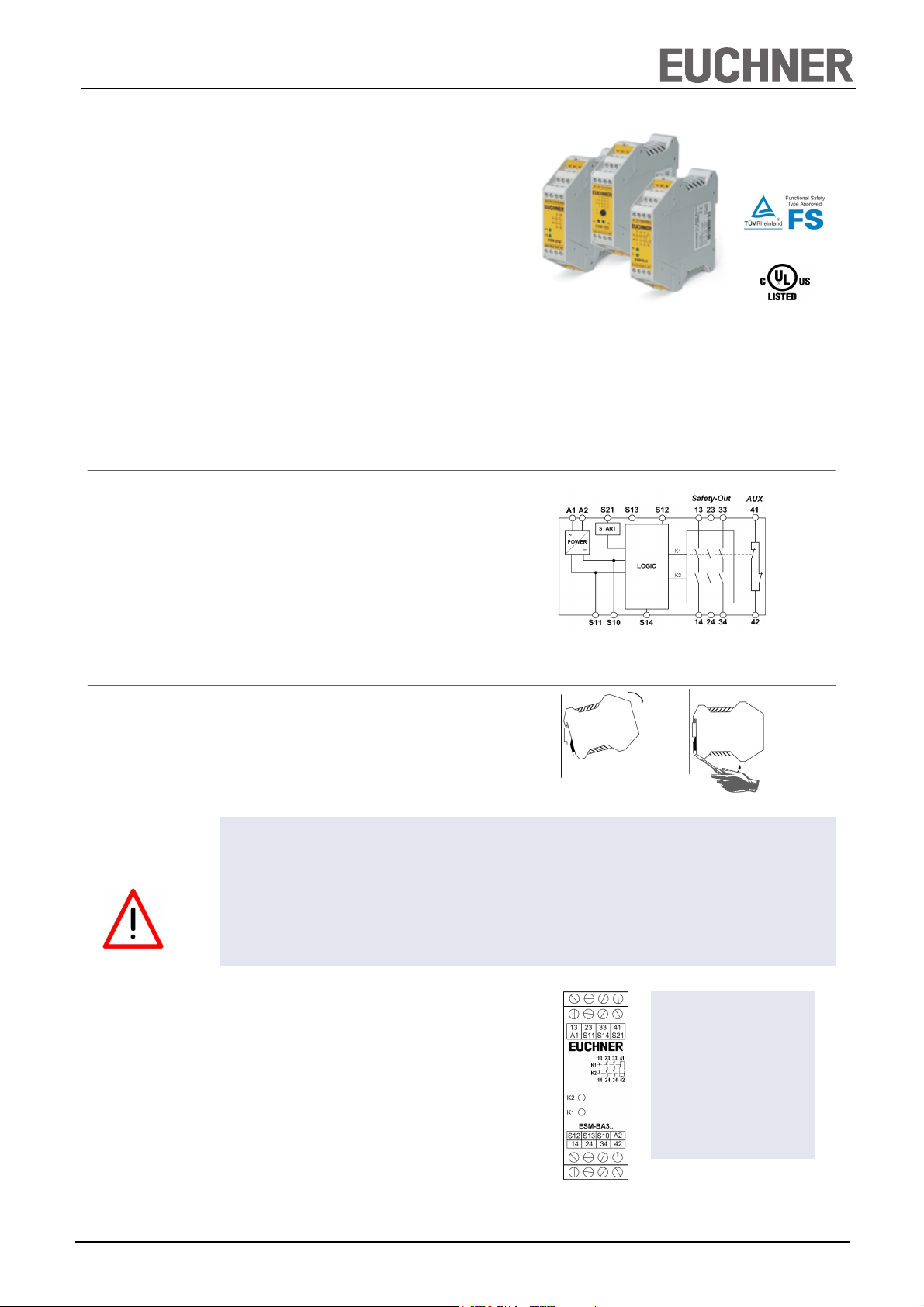
Emergency Stop Safety Relay ESM-BA3..
User Information
Correct Use
Features
Function
The ESM-BA3.. is a universal emergency stop safety switching
device with three safe relay outputs that can quickly and safely
stop the moving parts of a machine or system in case of danger.
Applications for the ESM-BA3.. include single or dual-channel
emergency stop circuits and guard monitoring on machines and
systems.
•
3 safe, redundant relay outputs
1 auxiliary contact (signaling contact)
•
Connection of:
- Emergency stop buttons
- Safety switches
- Non-contact safety switches
- OSSD-Outputs
•
Single and dual-channel operation possible
•
Feedback loop for monitoring downstream contactors or
expansion modules
The emergency stop safety switching device ESM-BA3.. is
designed for safe isolation of safety circuits according to
EN 60204-1 and can be used up to safety category 4, PL e
according to EN ISO 13849-1.
The internal logical system closes the safety contacts when
the start button is pressed.
When the safety switch is opened, the positively driven
safety contacts are opened and safely switch the machine
off. It is ensured that a single fault does not lead to a loss of
the safety function and that every fault is detected by cyclical self-monitoring no later than when the system is switched off and switched on again.
•
Cyclical monitoring of the output contacts
•
Indication of the switching state via LED
•
2 start behaviors possible:
- Monitored manual start
- Automatic start
•
Short circuit and earth fault monitoring
•
Up to PL e, SILCL 3, category 4
Fig. 1 Block diagram ESM-BA3..
(not for plug-in terminals)
Installation
Safety
Precautions
Electrical
Connection
As per EN 60204-1, the device is intended for installation in
control cabinets with a minimum degree of protection of
IP54. It is mounted on a 35 mm DIN rail according to DIN
EN 60715 TH35.
•
Installation and commissioning of the device must be
performed only by authorized personnel.
•
Observe the country-specific regulations when installing
the device.
•
The electrical connection of the device is only allowed to
be made with the device isolated.
•
The wiring of the device must comply with the instructions in this user information, otherwise there is a risk
that the safety function will be lost.
•
When the 24 V version is used, a safety transformer
according to EN 61558-2-6 or a power supply unit with
electrical isolation from the mains must be connected.
•
External fusing of the safety contacts (6A slow-blow or
8A quick-action or 10 A gG) must be provided.
•
A maximum length of the control lines of 1000 meters
with a line cross section of 0.75 mm
ceeded.
•
The line cross section must not exceed 2.5 mm2.
•
If the device does not function after commissioning, it
must be returned to the manufacturer unopened. Opening the device will void the warranty.
2
must not be ex-
Fig. 2 Installation / removal
•
It is not allowed to open the device, tamper with the device or bypass the safety devices.
•
All relevant safety regulations and standards are to be
observed.
•
The overall concept of the control system in which the
device is incorporated must be validated by the user.
•
Failure to observe the safety regulations can result in
death, serious injury and serious damage.
A1: Power supply
A2 : Power supply
S11: DC 24V control voltage
S10: Control line
S21: Start control line
S13: Control line
S14: Control line
S12: Control line
13-14: Safety contact 1
23-24: Safety contact 2
33-34: Safety contact 3
41-42: Auxiliary contact
Fig. 3 Connections
EUCHNER GmbH + Co. KG Kohlhammerstraße 16 D-70771 Leinfelden-Echterdingen Tel. +49/711/75 97-0 Fax +49/711/75 33 16 www.euchner.de info@euchner.de
1
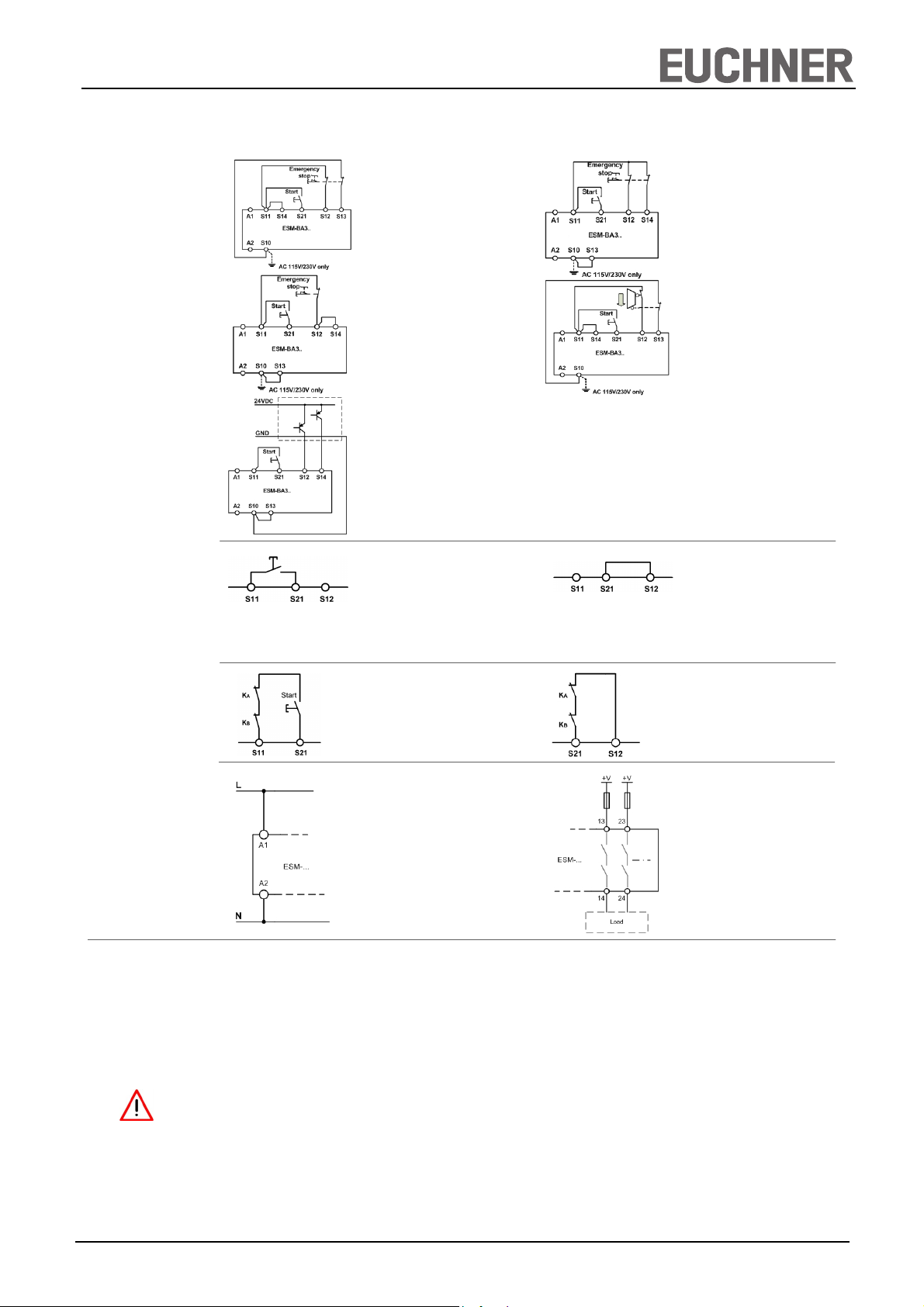
Emergency Stop Safety Relay ESM-BA3..
User Information
Applications
Emergency Stop
Circuit
Depending on the application or the result of the risk assessment according to EN ISO 13849-1, the device must be wired as
shown in Fig. 1 to Fig. 11.
Fig. 1:
Two-channel emergency stop
circuit with short circuit and earth
fault monitoring.
(category 4, up to PL e)
Fig. 2:
Two-channel emergency stop
circuit with earth fault monitoring.
(category 3, up to PL d)
Starting Behavior
Feedback Loop
Fig. 3:
Single-channel emergency stop
circuit with earth fault monitoring.
(category 1, up to PL c)
Fig. 5:
Two-channel emergency stop
with pnp-outputs/OSSD-outputs
with short circuit monitoring.
(category 4, up to PL e)
Fig. 6:
Monitored manual start.
It is monitored that the start
button was opened before the
emergency stop button closes.
(Prerequisite: operating voltage
must not be interrupted.)
Fig. 8:
Feedback loop for monitored manual
start:
The feedback loop monitors contactors
or the expansion modules .
Fig. 4:
Two-channel sliding guard
monitoring with short circuit and
earth fault monitoring.
(category 4, up to PL e)
Notice:
In order to activate earth fault monitoring, S10 must be connected to PE (protective earth) on the AC115/230V devices.
With AC/DC 24V, connect PE only to the power supply unit
according to EN60204-1.
Fig. 7:
Automatic start.
Max perm. delay during closing
of the safety switches on S12
Warning:
Safety contacts switch
immediately when the
power supply is connected.
and S13:
S12 before S13: 300 ms
S13 before S12: any
Fig. 9:
Feedback loop for automatic start:
The feedback loop monitors contac-
tors or the expansion modules .
Power supply
and
Safety contacts
Commissioning
Procedure
Fig. 10:
Power supply A1 and A2.
(Power supply according to techn.
data )
Note: The items listed under “Electrical connection” must be observed during commissioning.
1. Wiring emergency stop circuit:
Wire the emergency stop circuit according to the required
Performance Level determined (see Fig. 1 to Fig. 5).
2. Wiring start circuit:
Wire the start circuit according to Fig. 6 or Fig. 7 to set the
starting behavior.
Warning:
If “Automatic start” is set, bear in mind that the safety con-
tacts will switch immediately after the power supply is
connected. If “Monitored manual start” is set, the start
button must be opened after wiring.
3. Wiring feedback loop:
If your application provides for external contactors or expansion modules, connect them to the device according to
Fig.8 or Fig. 9.
4. Wiring power supply:
Connect the power supply to terminals A1 and A2 (Fig. 10).
5. Starting the device:
Switch the operating voltage on.
Warning:
If the “Automatic start” starting behavior is set, the safety
contacts will close immediately.
If the “Monitored manual start” starting behavior is set, close
the start button to close the safety contacts.
LEDs K1 and K2 are lit.
6. Triggering safety function:
Open the emergency stop circuit by actuating the connected safety switch. The safety contacts open immediately.
7. Reactivation:
Close the emergency stop circuit. If “Automatic start” is
selected, the safety contacts will close immediately.
If the “Monitored manual start” starting behavior is set, close
the start button to close the safety contacts.
Warning: Wiring only in de-energized state.
Fig. 11:
Connecting load to safety contacts.
(Figure shows example.
Voltage „+V“ according to techn.
data)
EUCHNER GmbH + Co. KG Kohlhammerstraße 16 D-70771 Leinfelden-Echterdingen Tel. +49/711/75 97-0 Fax +49/711/75 33 16 www.euchner.de info@euchner.de
2