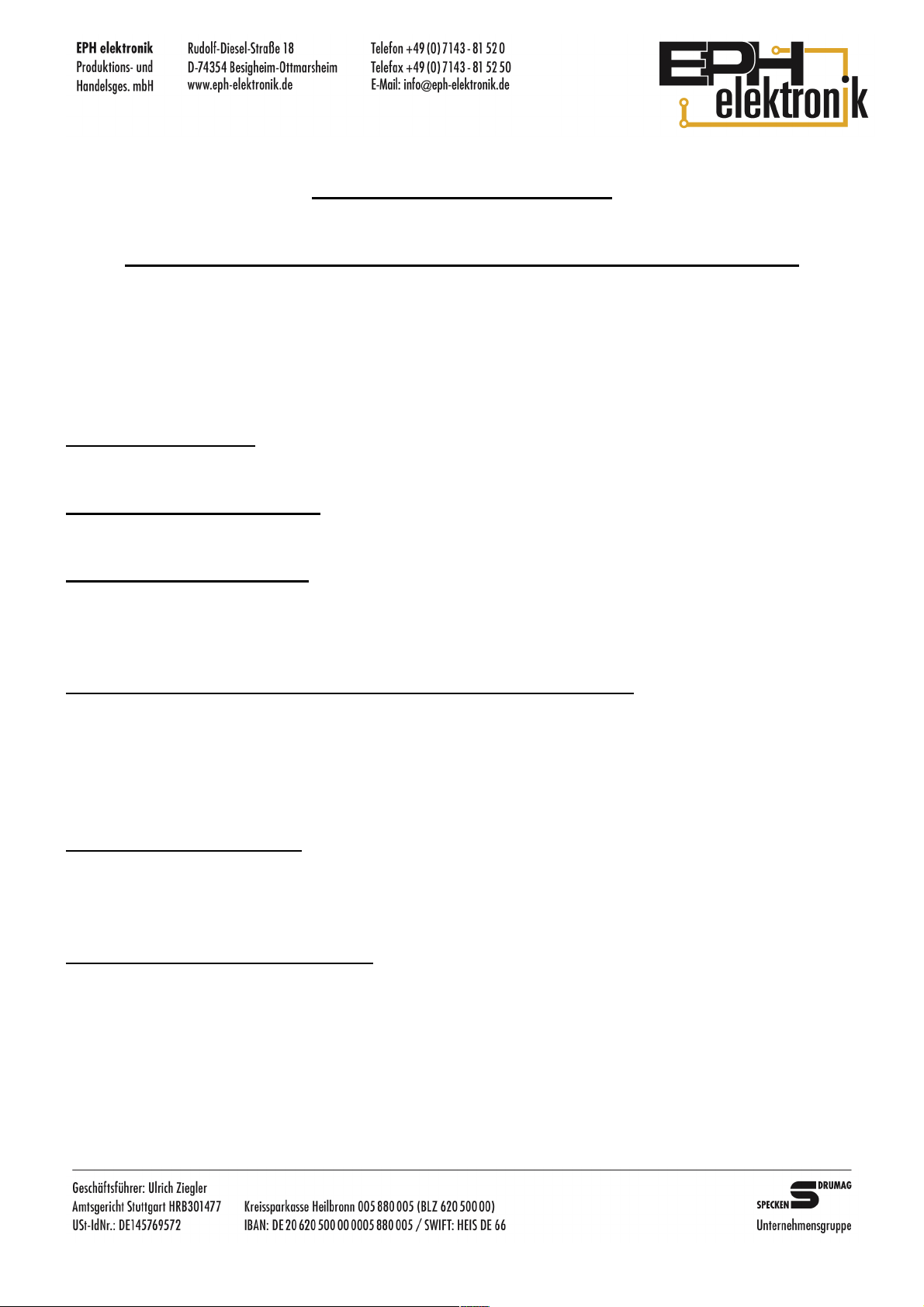
Technical Description
Transistor D.C. Chopper Controller Type GS 24 S
Table of contents
1. Getting started guide
2. General information
2.1. Characteristics
2.2. Accessories
3. Information about the Machine Directive 89/392/EWG
3.1. Delivery
3.2. Installation and start-up
3.3. EMC measures
3.4. Low Voltage Directive
4. Connection options
4.1. Option change of rotating direction
4.2. Connection for change of rotating direction option
5. Manufacturer’s declaration
Copyright © EPH-Elektronik GmbH. All rights reserved. We reserve the right of
ownership and copyright. Any reproduction or other use of the information or materials
provided herein is not permitted without our specific authorisation.
Stand: Februar 2011
Z 385 engl
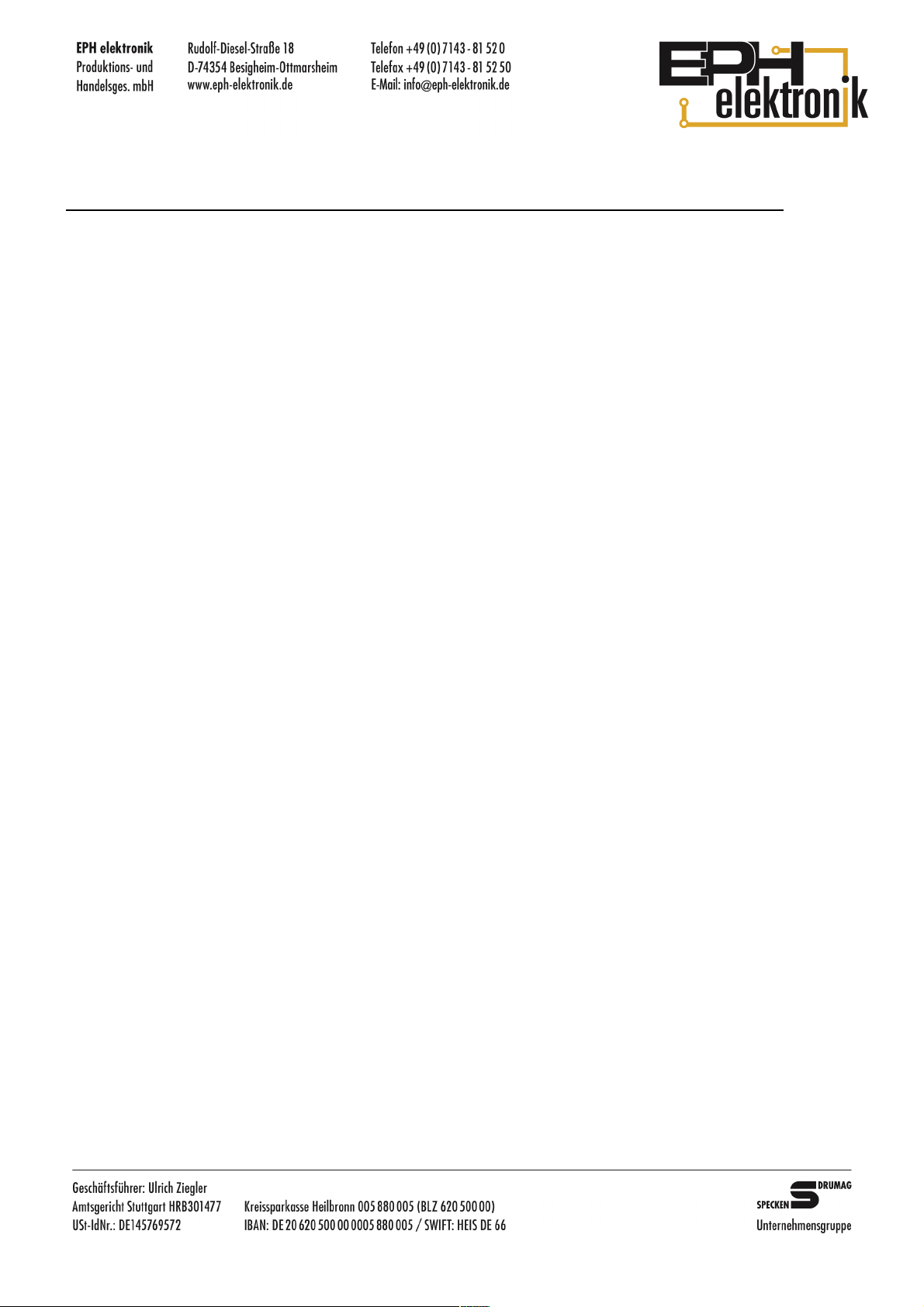
1. Getting started guide: GS24S/xx-360 with 9-pole screw terminal block
1. Select operating mode on J1 (the default internal mode is Standard, which is obtained
by setting J1 on I).
Select J2 (Standard is internal RF).
2. Connect the following digital input
(Connect terminal 7 to terminal 9; Input for enabling the regulator when J2 is set on
External).
3. Connect the following analogue inputs
Input N set point (terminal 8) voltage 0 to + 10 V or potentiometer (10kOhm)
between terminal 4 and terminal 7, tap from terminal 8.
4. Connect DC motor to terminals 5 and 6.
5. Connect power supply to terminal 3 (-) and terminal 2 (+) (approx. 20 – 36 V DC).
6. Proceed to energise the power supply.
7. LED (power on) lights up on circuit board.
8. The motor turns and the rotation speed can be adjusted via the voltage on terminal 8
(n set-point).
Stand: Februar 2011
Z 385 engl
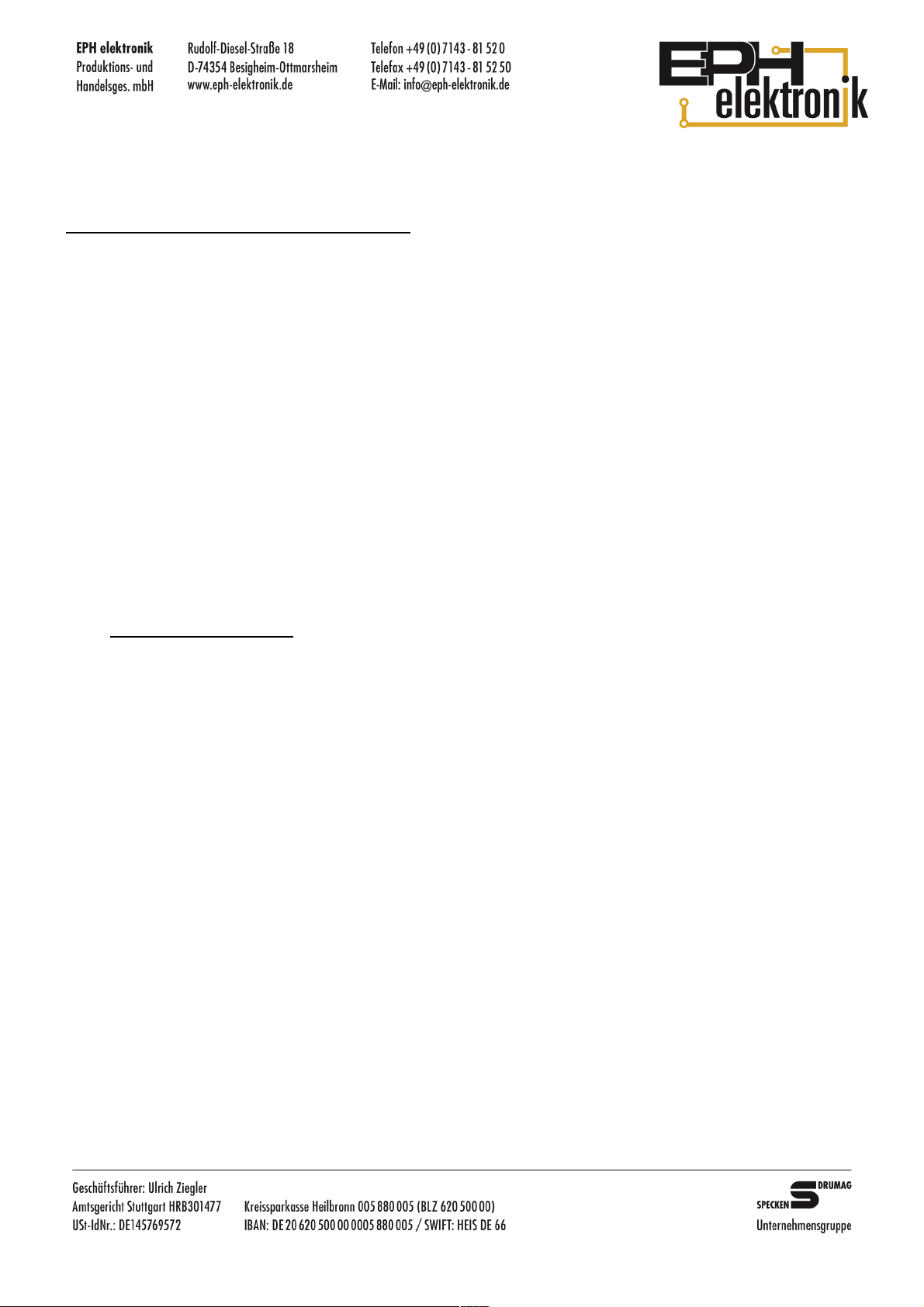
2. General information / Operation
The series GS 24 S/xx-360 transistor speed controllers are inexpensive devices with
compact dimensions of 72 x 100 mm for the stepless speed control of any DC motors
at low voltages and motor currents of up to 10 A. The input voltage range is 20 to
36 V DC makes a battery operation possible, e.g. from an on-board electrical supply
system or through series SNT 24/xx mains adapters connected upstream. The
stepless speed adjustment can take place through either an internal/external
potentiometer (10kOhm) or through an external reference voltage 0....10 V DC (pre-
selection via jumper set-point). An internal potentiometer acts as an overload
protection by providing a continuously variable motor current limitation.
The possibility to change the rotating direction through a relay is available as an
option using an additional EPH 393 type circuit board. Rotation in the left or right
direction can be pre-selected during standstill via a 12 to 48 V DC control signal.
2.1. Characteristics
● The high pulse frequency of 18 kHz allows for a quiet operation.
● Form factor F < 1.05 guarantees reduced motor heating and high MD reserves.
● Adjustable rotation speed through 0..10 V interface or potentiometer (10kOhm)
(external or internal).
● Enable-input for output stage activation, internal/external (pre-selection
through jumper RF).
● Overload protection of motor or drive through stepless current limitation.
Stand: Februar 2011
Z 385 engl
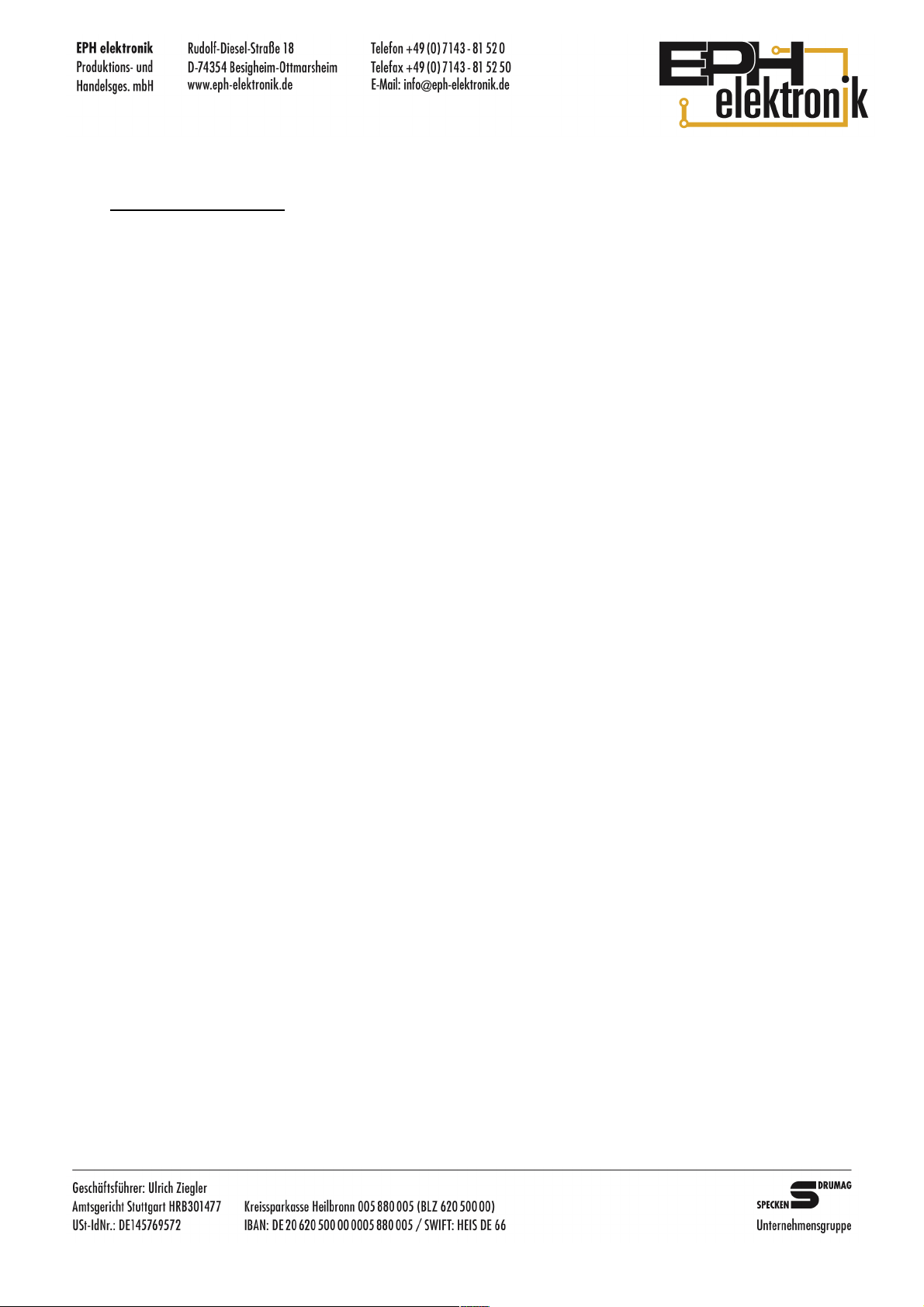
2.2. Accessories
● Module carrier for 35 mm mounting rail installation.
● Module carrier for screw fastening.
● Suppressor diodes in motor vehicle applications with high inductive spikes.
● Potentiometer for set point adjustment 1 gang or 10 gang (10kOhm).
● Mains adapter SNT 24/ 05; NT 24/ 10 input voltage 230 V / 50 Hz.
3. Information and recommendations on the use of EPH motor controller cards in
electrical drive systems pursuant to the current EU Machine Directives 89/392
EWG, EMC-Directive 89/338 EWG and Low Voltage Directive 73/23 EWG.
According to the Machine Directive only complete machines can bear the CE marking.
An electronic card or an electric motor are parts of a machine/electrical equipment, a
system or a process, and are treated within the scope of the EU Directive as a complex
component part and a CE marking requirement is therefore not given.
These components can not be operated by the user on a standalone basis and are
manufactured exclusively for their further processing by industry, trade or other
businesses with a specific EMC expertise.
Processing of the components is permissible only for their further adequate and correct
use by trained qualified personnel, who can warrant a proper installation, start-up and
maintenance.
EPH control devices in circuit board form are classified as power electronics equipment for
the control of electrical power / Protection class IP 00. They are intended for the use in
machines for speed control of electric motors.
To comply with the Low Voltage Directive 73/23 EWG in end user devices EPH Elektronik
also offers versions with enclosures that include a protection device as an alternative to
the circuit board version (at least protection class IP 20).
The user has to ensure that the devices and the corresponding components and
equipment are installed and connected in accordance with the local legal and technical
regulations.
Stand: Februar 2011
Z 385 engl