
KEYSTONE
Non return valve Dubex
Installation and maintenance instructions
Please read these instructions carefully.
This symbol indicates important
messages and safety instructions.
Intended valve use
The valve is intended to be used in
applications within the pressure/temperature
limits as indicated in the P/T diagram of the
product manual only.
Type of valve
Material identification
Uni- or Bidirectional
Size
Sales order number
1. Storage and handling
1.1. Storage
Storage should be off the ground in a clean, dry, indoor area.
1.2. Handling
To prevent damage during lifting the valves should be lifted with appropriate lifting
equipment. Valves are shipped with counterweight disassembled. The disc is secured against
inadvertent movement. Remove securing device after mounting the counterweight. Possible
flange protection caps need to be removed prior to mounting it in the pipeline. Lift the valve
with great care from the transport package (crate, pallet). Prevent any damage to the valve,
the pneumatic/electric/hydraulic actuator or any other instrumentation.
2. Spare parts
Only original RMI spare parts are allowed to be used. Safe operation can not be guaranteed if third
party spare parts are used.
3. Installation
WARNING
For safety reasons it is important to take the following precautions before starting to work on
the valve:
1. Personnel making any adjustment to the valves should utilize suitable equipment. All required
personal protection means should be worn.
2. The line must be depressurized before installing the valve.
3. Installation and handling of the valves should only be done by personnel that is trained in all
aspects of manual and mechanical handling techniques.
4. Misuse of the valve is not allowed. The valve, handles, actuators and other parts may not be
used as ‘climbing tools’
5. Ensure that valve pressure/temperature limitations marked on the valves tagplate are within
the service conditions. The trim number on the valves tagplate identifies the valve materials.
See product manual for valve specific P/T diagram and trim number definition.
6. Ensure that valve materials are compatible with the pipeline fluid.
7. The valve has to be installed in a horizontal pipeline with the shafts horizontal.
Q max/min
www.valves.emerson.com
3.1. Visual valve inspection
1. Confirm that the materials of construction listed on the valve tagplate are appropriate for the
service intended are as specified.
2. Tagplate identification
Fabricator Emerson RMI
Figure DBX NRV
Material trim e.g. 804
Direction U(nidirectional) or B(idirectional)
Size e.g. DN1000
Tag no. If required
Design pressure e.g. PN16
Design temperature e.g. -20°C to +80°C
Year of construction e.g. 2004
Mass e.g. 2500 kg
3.2. Flange and pipe compatibility
Check matching of flange drilling pattern of valve and pipe flange before assembly.
Flanges have to meet the following requirements:
• The face inside diameter should be:
D min: The valve Q dimension + adequate disc clearance.
D max: The inside diameter (ID) of standard pipe for the nominal size ISO 4200.
Use flange bolting in agreement with appropriate standard.
Emerson reserves the right to change the contents without notice RMISB-0014-EN-1306
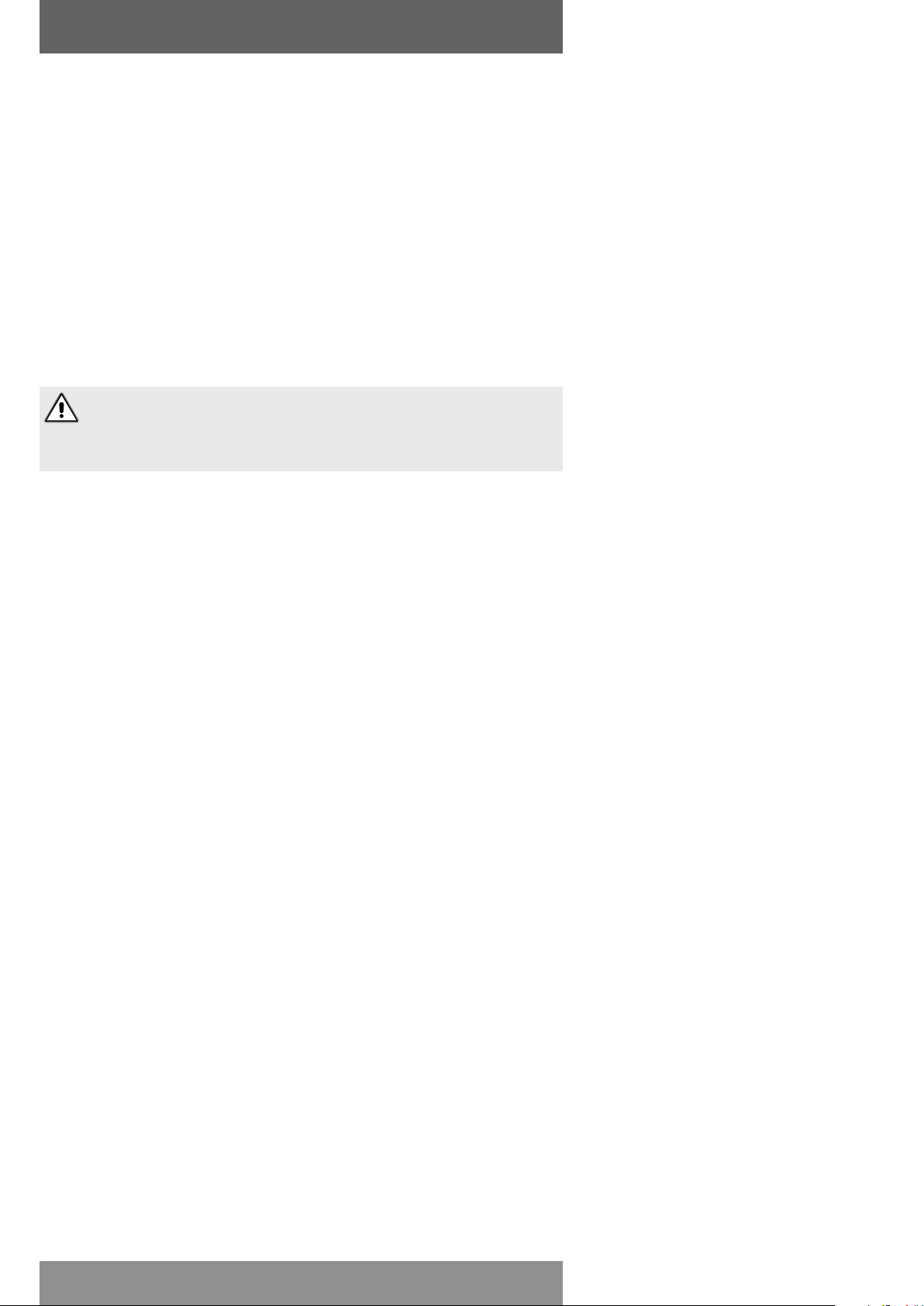
Non return valve Dubex
Installation and maintenance instructions
3.3. Valve installation
A non return valve is equipped with an arrow on the body. The arrow points in the direction
of the intended flow. Check that the arm with counterweight can move freely when the valve
disc travels from open to close and vice versa. Do not use the valve to spread the flanges.
Notes
• Do not use the valve as a support for the pipeline construction.
• Adjacent piping must be positioned so that minimal piping stresses are transmitted to the
valve flanges during or after installation.
• Handling and lifting of the valves during installation MUST be performed following the
same instructions described in the previous paragraph ‘1.2 Handling’.
• There should be a safety fence or other means of protection around the arm with
counterweight to prevent possible injury caused by movement of the counterweight.
• For smooth performance it is recommended to have a straight pipe of 10 to 20 times the
diameter at the inlet, and a straight pipe of 5 to 10 times the diameter at the outlet.
Important
Mating flange faces should be in good condition and free of dirt and/or inclusions.
Both pipe insides to be well cleaned.
1. Place the valve with flange face vertical and shaft horizontal. Assemble counterweight and
remove disc locking provisions cautiously. Keep the disc in closed position.
2. Check whether the distance between flanges meets the face to face valve dimension.
Spread the flanges with adequate tooling for easy installation of the valve.
3. Insert the valve with the gaskets between the flanges. Center the valve body and insert all
flange bolts.
4. Maintain the valve flange alignment while gradually removing the flange spreaders and
tighten the flange bolts hand tight.
5. Cross tighten all bolting to the proper torque.
3.4. Sources of possible danger
This section contains some examples of possible foreseen danger sources.
3.4.1. Mechanical
Available space should be checked in order to avoid interference between moving parts
(cylinder, counterweight) and surroundings. Mechanical sparks caused on impact of valve
and e.g. tooling are a potential source of ignition of surrounding atmosphere. The arm with
counterweight and cylinder should not be accessible while operating. Install a surrounding
fence or other means of protection.
3.4.2. Electrical
If static charges or stray electric currents can initiate explosions the valve should be grounded.
3.4.3. Thermal
If the valve is used in applications with a fluid temperature >40°C or <-20°C the outside of the
body should be protected against touching to avoid burning by means of isolation. In case the
valve is used in hot gas/fluid applications that might give exothermic reactions, precautions
should be taken that the surface of the valve can not lead to danger for people or the direct
environment
3.4.4. Operational
Closing a valve to fast may result in water hammer in the upstream part of the pipeline.
Waterhammer results in excessive stresses in the valve and causes severe damage.
Waterhammer should be avoided under all circumstances. The damping action of the
hydraulic cylinder should be set properly and carefully
Take care when unlatching or removing the valve operating mechanism.
Emerson reserves the right to change the contents without notice Page 2