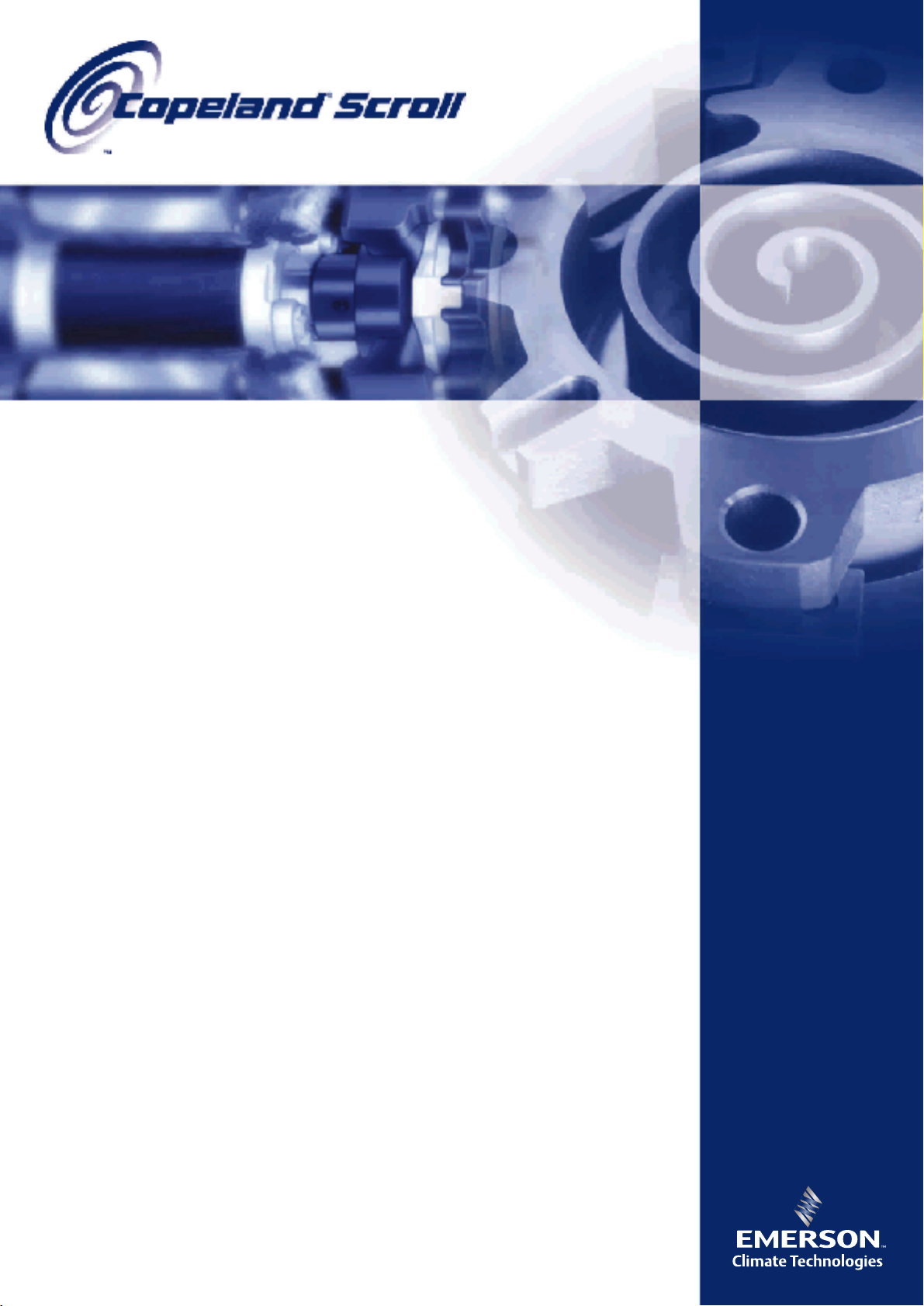
Horizontal Scroll compressors for
Horizontal Scroll compressors for
Refrigeration
Refrigeration
Application Guidelines
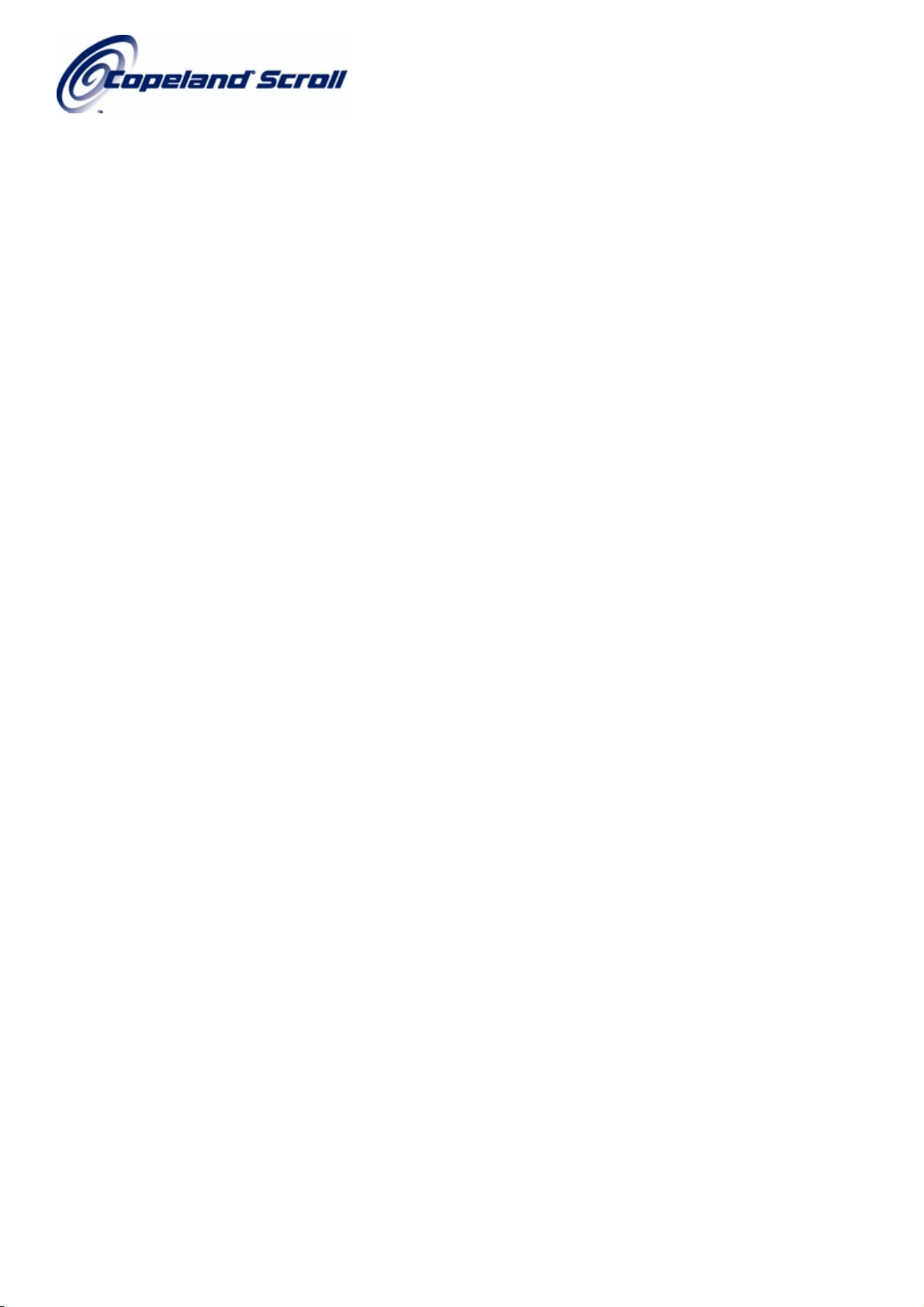
Contents
1 Introduction .............................................................................................................................................................3
2 Nomenclature .........................................................................................................................................................3
3 Qualified Refrigerants.............................................................................................................................................3
4 Lubrication ..............................................................................................................................................................4
5 Liquid Injection........................................................................................................................................................4
6 Refrigerant Migration ..............................................................................................................................................7
7 Crankcase Heaters.................................................................................................................................................7
8 Discharge Temperature Protection ........................................................................................................................7
9 Standard Motor Protection......................................................................................................................................7
10 Mufflers ...................................................................................................................................................................7
11 Low Ambient cut-out...............................................................................................................................................7
12 Pressure Controls...................................................................................................................................................8
13 Internal Pressure Relief Valve ................................................................................................................................8
14 Pump Down ............................................................................................................................................................8
15 Shut-Off ..................................................................................................................................................................8
16 Starting ...................................................................................................................................................................8
17 Deep Vacuum Operation ........................................................................................................................................8
18 Electrical Installation...............................................................................................................................................8
19 Three Phase Models ..............................................................................................................................................9
20 Cable Connectors...................................................................................................................................................9
21 Compressor Functional Check ...............................................................................................................................9
22 High Potential Testing ..........................................................................................................................................10
23 Motor Codes .........................................................................................................................................................10
24 Installation.............................................................................................................................................................10
25 Shut-off Valves and Adapters...............................................................................................................................11
26 Shell Temperature ................................................................................................................................................11
27 System Evacuation and Charging Procedure ......................................................................................................11
28 Unbrazing System Components...........................................................................................................................12
29 Compressor Replacement....................................................................................................................................12
30 Suction Line Noise and Vibration .........................................................................................................................13
31 Application Envelopes ..........................................................................................................................................14
C6.2.7/0302-0903/E 2
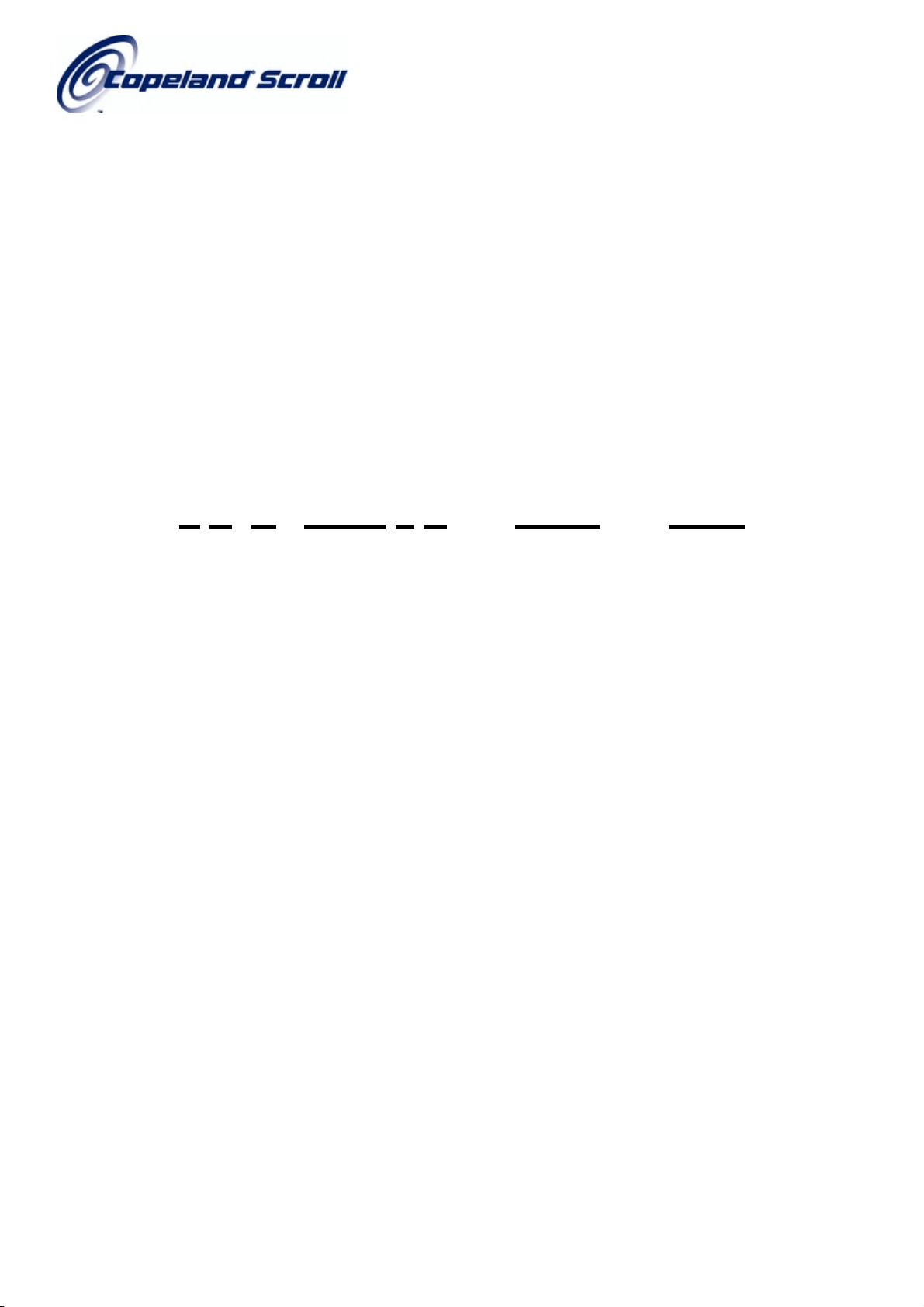
1 Introduction
The Copeland ScrollTM compressor – using the compliance principle - has been under development at Copeland since
1979 and is the most efficient and durable compressor Copeland has ever developed for air-conditioning, refrigeration
and heat pump applications. It offers very low vibration and sound levels and is tolerant to stresses caused by liquid
slugging, flooded starts, and debris commonly found in refrigeration systems.
Available product range in this family is from 2.0 to 6 HP. For detailed information, please, refer to the Copeland
Selection Software accessible free of charge from the Copeland Website at www.ecopeland.com or printed
performance brochures.
These guidelines are not meant to replace the system expertise available from system manufacturers.
2 Nomenclature
The model numbers of Copeland Scroll compressors have been designed to include a coded nominal capacity at ARI
operating conditions in BTU/h at 60 Hz.
All refrigeration scroll compressors are charged with polyolester oil, which is indicated by the letter “E”.
Model Designation
Z S H 3 0 K 4 E - T F D - 5 5 1
12 3 4 56 7 8
1 Z = compressor family: Z = Scroll
2
S = High / Medium Temperature
F = Low Temperature
B = High / Medium Temperature
3 H = Horizontal Orientation
4 nominal capacity [BTU/h] @ 60 Hz and ARI conditions using multipliers
"K" for 1000 and "M" for 10 000
5 - model variation
6 - POE oil
7 - motor version
8 - bill of material number
550: Brazed stubs, oil sight glass, schraeder connection for oil fill, or drain, and Discharge thermostat
551: Rotalock threaded stubs, oil sight glass, schraeder connection for oil fill, or drain,
Discharge thermostat.
555 Rotalock threaded stubs, oil sight glass schraeder connection for oil fill, or drain,
Discharge thermostat and DTC Valve. (ZF Compressors only).
556: Brazed stubs, oil sight glass schraeder connection for oil fill, or drain,
Discharge thermostat and DTC Valve. (ZF Compressors only).
3 Qualified Refrigerants
R404A is qualified for all horizontal refrigeration scroll compressors.
ZBH compressors are also qualified to operate with R407C. R404A and R134a.
Data availability should be checked with Copeland Selection software.
It is essential that the glide with refrigerant blends (primarily R407C) be given careful consideration when adjusting
pressure and superheat controls.
C6.2.7/0302-0903/E 3

The application envelopes for each refrigerant are shown in section 31 and Copeland Selection software.
4 Lubrication
The oil level should be maintained at mid-point of the sight glass. If an oil regulator is being used the level should be
set within the top half of the sight glass.
An internal positive displaced oil pump, draws oil from the compressor base via a dip tube for lubrication of the
bearings.
The compressor is supplied with an initial oil charge. The standard oil charge is a Polyolester (POE) lubricant ICI
Emkarate RL 32 CF (32 cSt). In the field, the oil level could be topped up with either ICI Emkarate RL 32 CF or Mobil
EAL Arctic 22 CC. The values can be taken from Copeland’s brochure.
They must be operated with these specific oils only. Under no circumstances are polyolester oils to be mixed with
mineral oil and/or alkyl benzene when used with chlorine-free refrigerants.
Ester oil behaves extremely hygroscopically (see figure 1), and this influences the chemical stability of the oil.
The number of start/stop cycles should be limited to 10 per hour. A high cycling rate will pump oil into the system and
may lead to lubrication failure. Oil leaves the compressor at start up regardless of the low oil carry over of the Scroll.
Short running time is insufficient to return the oil to the compressor and possibly results in a lack of lubricant.
Figure 1: Absorption of moisture in ester oil in comparison to mineral oil (ppm) by weight at 25°C and 50%
relative humidity. h = hours
It must be considered that the entire system will be coated with oil to some extent. Oil viscosity changes with
temperature. System gas velocity changes depending on temperature and load. In low load conditions gas velocity
may not be high enough to return oil to the compressor. System piping should be designed to return oil under all
operating conditions, including part loads.
The system should be evacuated down to 0.3 mbar/ 0.22 Torr or lower. If there is uncertainty, as to the moisture
content in the system, an oil sample should be taken from various points and tested for moisture. The residual
moisture in the installation should be brought below 50 PPM by good evacuation practice (refer to section 25 System
Evacuation and Charging Procedure) and the use of a suitable filter drier (solid core XH9 or higher is recommended).
Sight glass/moisture indicators currently available can be used with the HFC refrigerants and lubricants; however, the
moisture indicator will indicate the moisture content of the refrigerant. The actual moisture level of POE could be
higher than the sight glass specifies. This is a result of the high hygroscopicity of the POE oil.
5 Liquid Injection
For low temperature applications ZFH models, liquid injection is required to keep discharge gas temperatures within
allowable limits.
The compressor is supplied with a 13/16" UNF diameter injection stub to accept a DTC (Discharge temperature
control) valve for liquid injection. The same DTC valve can be used for all compressors and approved refrigerants.
Inside the compressor, injection takes place into two distinct pockets of the scroll involute without influencing the
suction process. Injection increases the mass flow through the system slightly.
The ZFH compressor (BOM 555 and 556) incorporates a thermal well in the discharge cap, to accommodate the DTC
bulb, combined with a valve cap.
C6.2.7/0302-0903/E 4
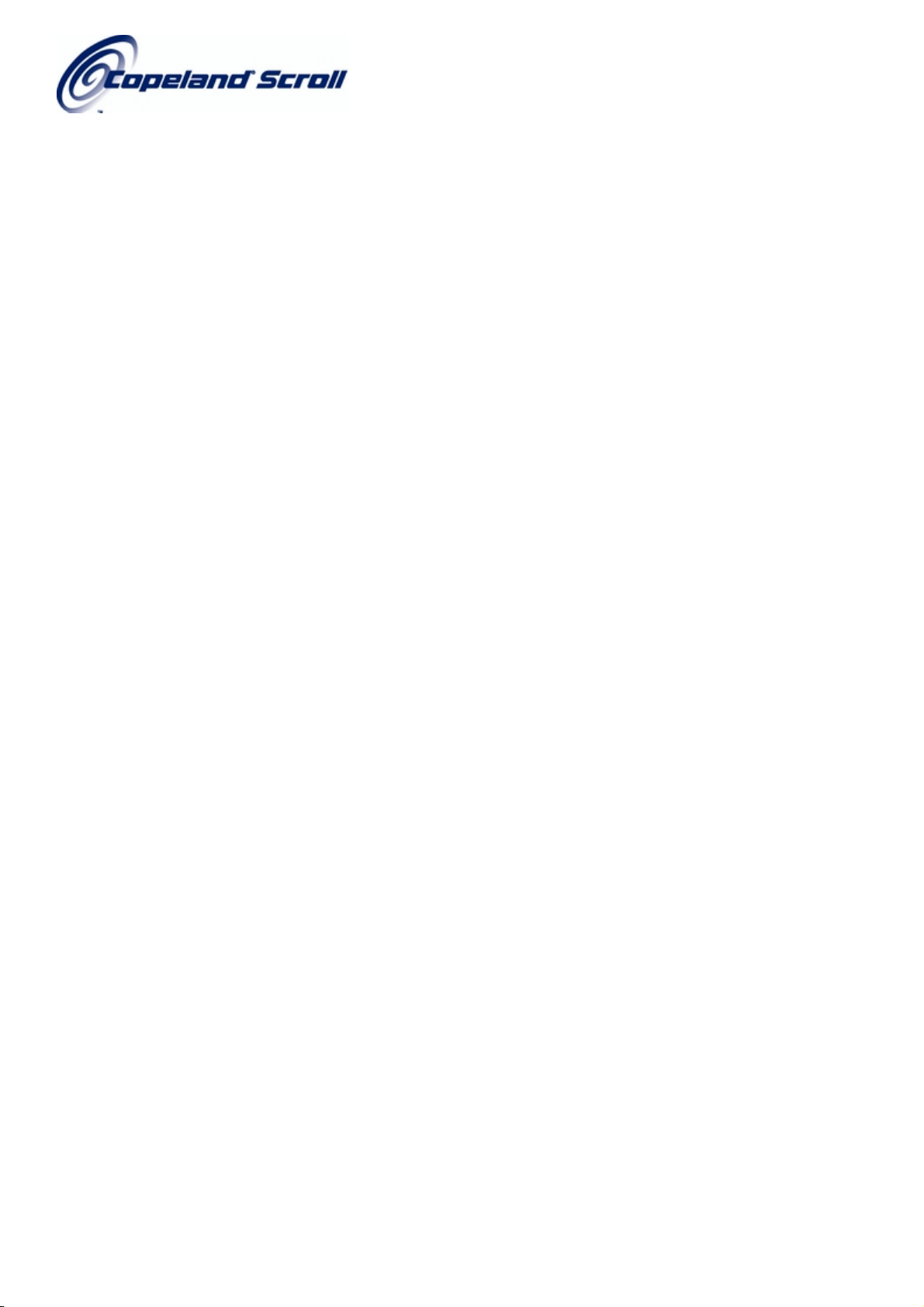
The Copeland DTC valve is equipped with a custom bulb profile, which must be installed in the thermal well of the top
cap of the compressor, sensing the temperature closest to the discharge port. The DTC valve injects only when
cooling is needed and in the required amounts. The connection to the liquid line is a 3/8" braze
Valve Specifications
Set Point: 89.4°C ± 2.4°C (193°F ± 5°F)
Liquid Line Connection: 3/8"
Valve Installation
The valve bulb must be installed in the discharge cap thermal well to adequately control discharge temperatures. The
valve should be tightened on the injection fitting to a torque of 24-27 Nm (216-245 in. lbs.) It is also reccommended
that the valve is located perpendicular to the compressor orientation, in relation to the liquid inlet to the DTC valve,
however it will function properly in any orientation. The capillary tube connecting the valve to the bulb should be
positioned at least 13 mm away from the side of the scroll body to avoid contact during operation.
An insulating cap is supplied with the DTC Valve, which is applied over the DTC sensing bulb. The valve cap could be
replaced with thermal grease, if misplaced. This grease should be applied (minimum of 6 mm thick) to insulate and
protect the valve. It is recommended to spread a thin film of thermal grease around the DTC Valve bulb before
installing into the top cap well. We also recommend that a shut off valve in the liquid line is installed before the DTC
valve, for ease of service.(See Fig. 2: Compressor valve assembly procedure)
Compressor or Valve Service
Replacing a ZF compressor using the DTC Valve: We recommend replacing both the DTC Valve and the compressor
at the same time. If the the existing DTC valve is not replaced, then the removable valve filter should be cleaned
and/or replaced.
C6.2.7/0302-0903/E 5