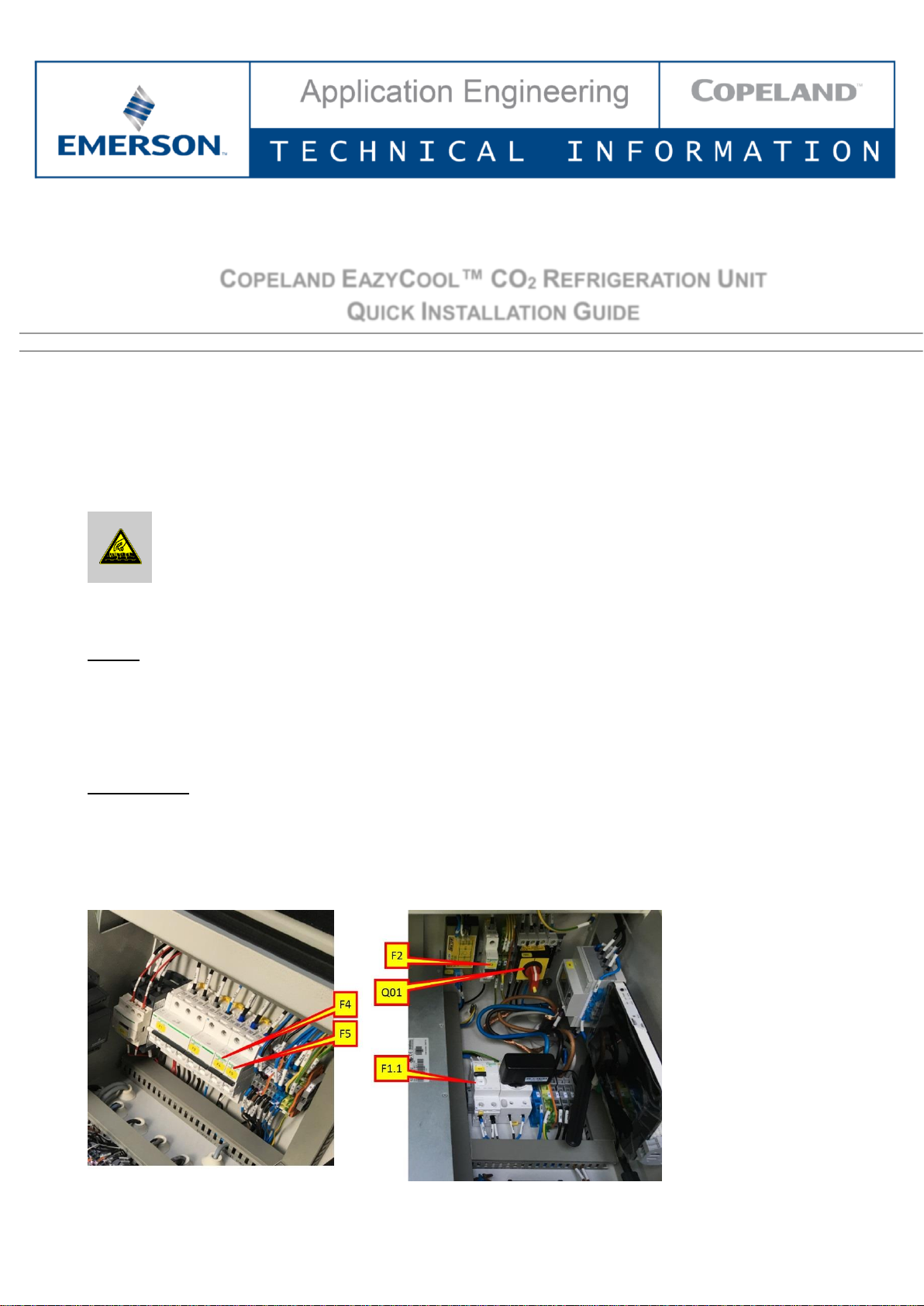
Date of last update: May-19
Application Engineering Europe
COPELAND EAZYCOOL™ CO
2
REFRIGERATION UNIT
QUICK INSTALLATION GUIDE
1 Introduction
This quick installation guide provides information on Copeland™ EazyCool CO2 refrigeration units and
describes the first steps for successful commissioning. It is not intended to replace the application guidelines,
to explain the functionality of the refrigeration unit or to help optimize the system parameters.
2 First steps
WARNING
Hot surfaces! Burning! If the temperature on the bottom of the compressor (crankcase)
is below 20°C, the crankcase heater is automatically activated. Do not touch the
crankcase heater.
When the low-pressure side piping has been finalized and the electrical supply has been connected by
qualified personnel, please follow the steps below in preparation for commissioning:
Safety:
✓ Verification of necessary safety devices in the system
✓ Visual inspection of the refrigerant pipes and especially of all connections
✓ Visual inspection of the electrical wiring of the supply line
✓ Checking the refrigeration unit and connected cooling stations for damage of any kind
✓ Ensuring that no section of the system is under safety charge with dry air
Functionality:
✓ Switch on the device main switch (Q01)
✓ Switch on the disconnector for the single-phase power supply (F2)
✓ Switch on the safety chain transformer isolator switch (F5)
✓ Switch on the disconnector for the crankcase heater (F4)
✓ Switch on the RCCB for online monitoring (F1.1 = power supply to the router), if available
Figure 1: Switch on control system & small electrical components
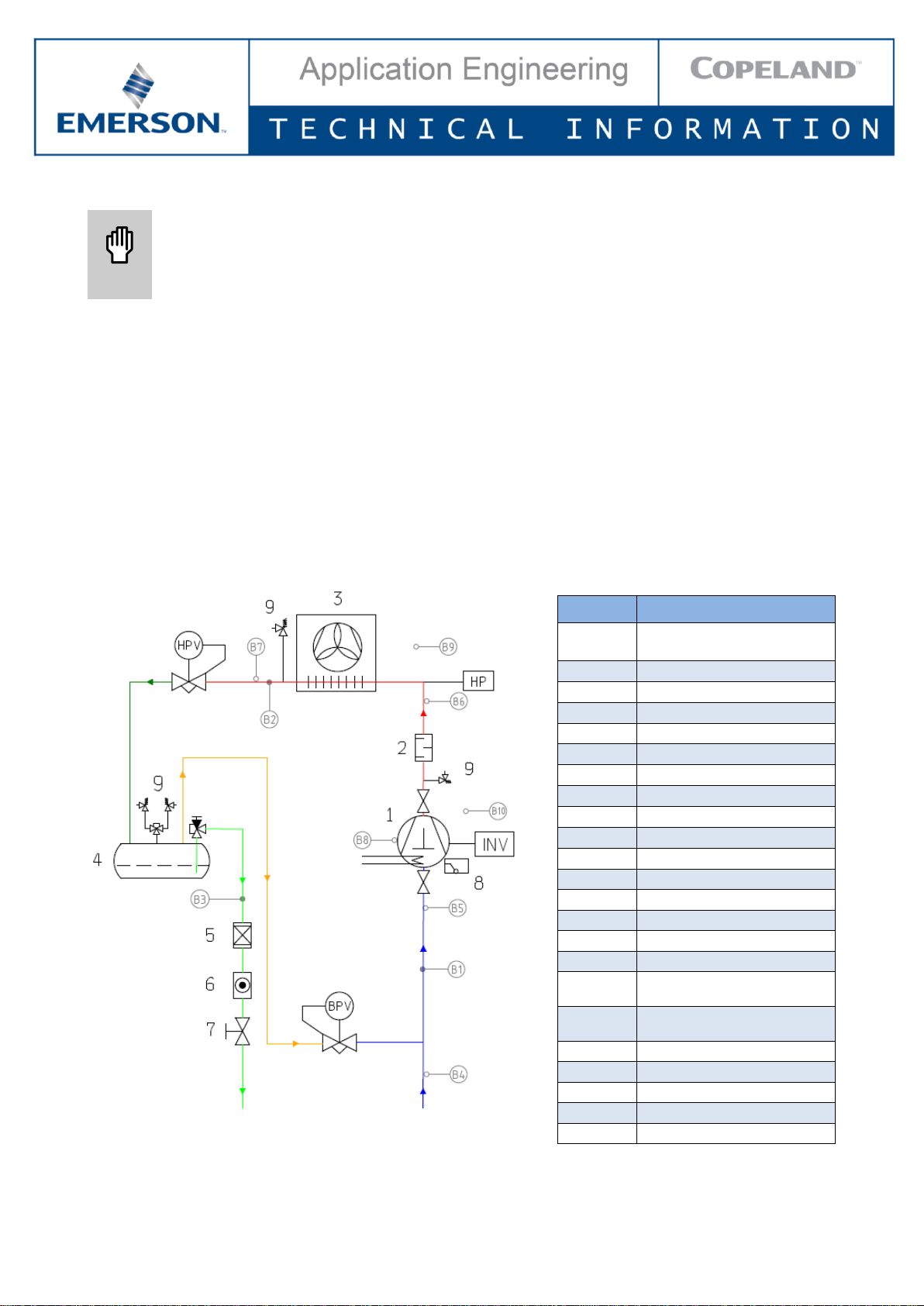
CC7.8.9/0519/E 2/7
3 Pressure resistance test and leak test
CAUTION
The system must be properly evacuated before filling the cooling circuit with refrigerant.
This should result in a reduction of the residual moisture content to approx. 50 ppm.
Evacuation should be carried out to less than 3 mbar and, if necessary, the vacuum
should be broken with dried nitrogen.
Depending on the installation, pressure strength tests and leak tests must be carried out on different pressure
layers. The shut-off of system sections may be necessary.
Several shut-off devices are installed in the CO2 refrigeration unit. These are suction and pressure shut-off
valves of the compressor, high-pressure control valves at the gas cooler outlet, flash-gas bypass valves
between the liquid receiver and suction line, shut-off valves at the liquid receiver and shut-off valves in the
liquid line at the outlet from the refrigeration unit.
It is the responsibility of the user to decide which barriers are to be opened/closed in order to carry out the
pressure tests. For the evacuation process, it is recommended that all shut-off devices be opened and
evacuated from both sides via the connections on the suction side and the connection on the liquid receiver.
The shut-off valves at the discharge port, on the suction side of the compressor, at the outlet of the liquid
receiver and the shut-off valve in the liquid line can traditionally be operated manually.
To open the high-pressure control valve and the flash-gas control valve, please follow the instructions in
section 4 next page.
Figure 2: Shut-off valves in the CO2 refrigeration unit
Copeland Stream
compressor
Suction gas temperature
unit
Suction gas temperature
compressor
Discharge line temperature
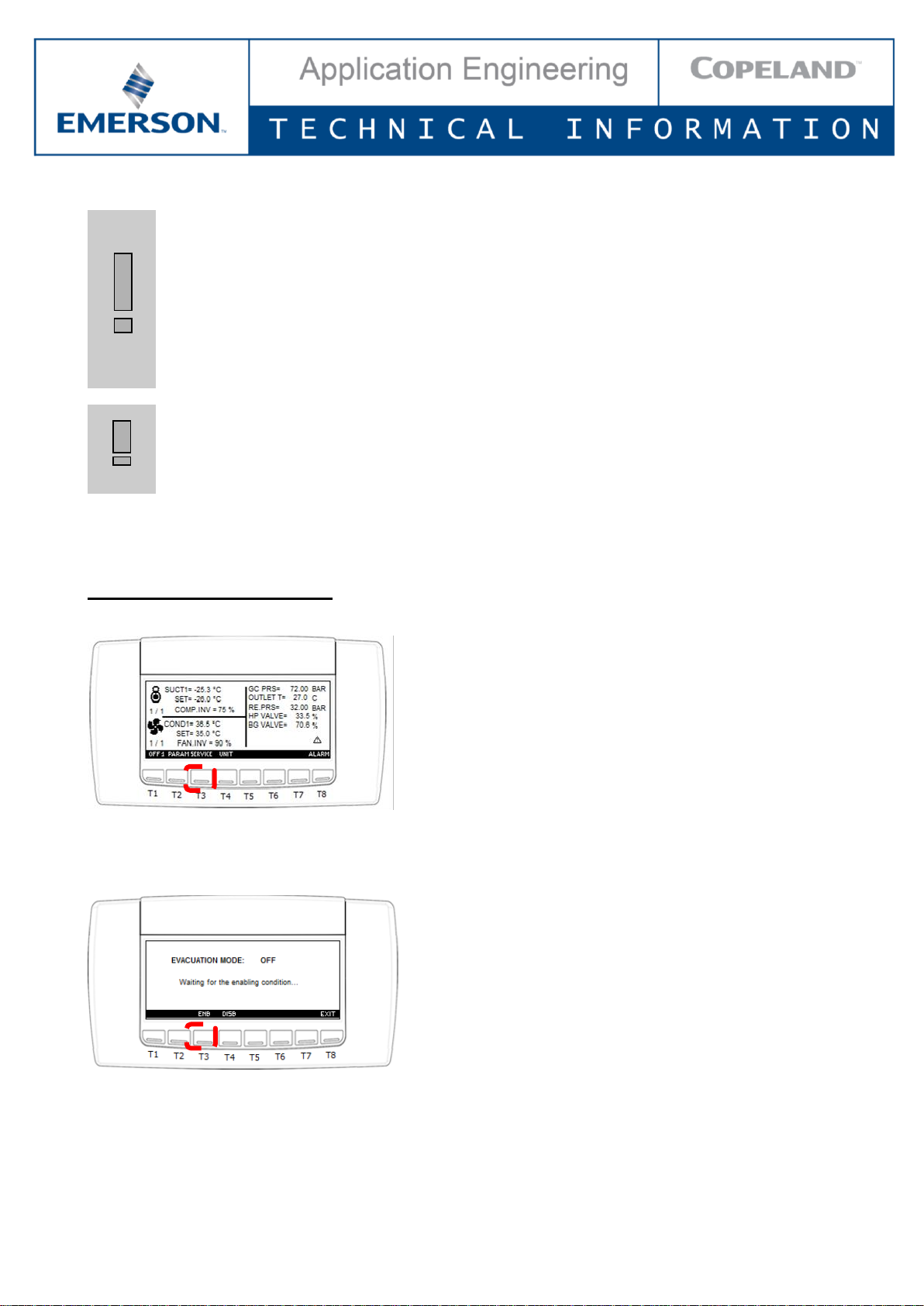
CC7.8.9/0519/E 3/7
4 Evacuation
IMPORTANT
The evacuation procedure is based upon achieving an actual system vacuum standard
and is NOT TIME DEPENDENT! The installation has to be evacuated with a vacuum
pump before commissioning. Proper evacuation reduces residual moisture to 50 ppm.
The installation of adequately sized access valves at the furthest point from the
compressor in the suction and liquid lines is advisable. The system must be evacuated
down to less than 3 mbar. If required break the vacuum with dry nitrogen. Pressure must
be measured using a vacuum pressure gauge on the access valves and not on the
vacuum pump. This serves to avoid incorrect measurements resulting from the pressure
gradient along the connecting lines to the pump.
IMPORTANT
Care must be taken that all components (solenoids, expansion devices, regulators, shut
off valves, etc…) in the refrigeration cycle, which separate a part of the installation when
de-energized, are manually opened to guarantee successful evacuation in the whole
piping system.
NOTE: The controller must be turned on before starting the evacuation.
NOTE: For proper evacuation, both the HPV and BPV regulating valves must be opened using the
evacuation mode in the unit controller.
To activate the evacuation mode:
1) Press the SERVICE key to enter the "Service" menu
Figure 3: Service key
2) Use the UP and DOWN keys to select the "Evacuation mode" sub-menu
3) Press ENB to enable the evacuation mode (see Figure 4):
Figure 4