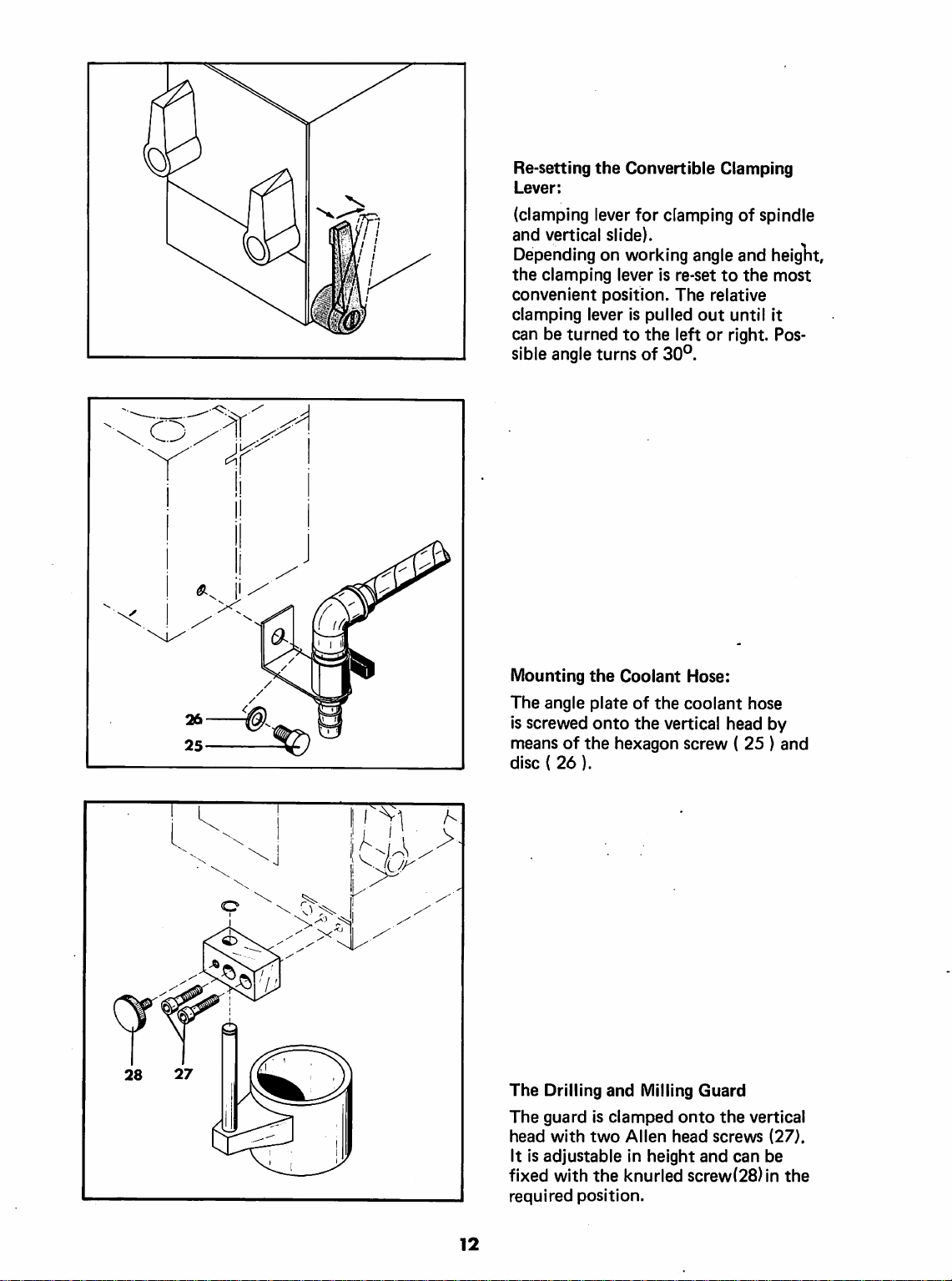
Re-setting
Lever;
(clamping
and
Depending
the
clamping
convenient
clamping
can
be
sible
the
lever
vertical
slide).
on
lever
position.
lever
turned
angle
turns
Convertible
to
for
clamping
working
is
of
angle
is
re-set
The
pulled
the
out
left
30°.
relative
or
Clamping
of
spindle
and
heiglit,
to
the
most
until
it
right.
Pos
Mounting
The
angle
is
screwed
means
disc ( 26).
The
The
head
It
fixed
required
of
the
Drilling
guard
with
is
adjustable
with
position.
the
Coolant
plate
of
onto
the
hexagon
and
is
clamped
two
Allen
in
the
knurled
Hose:
the
coolant
vertical
screw ( 25 ) and
Milling
height
Guard
onto
head
screws
and
screw(28)in
hose
head
the
vertical
can
by
(27).
be
the
12
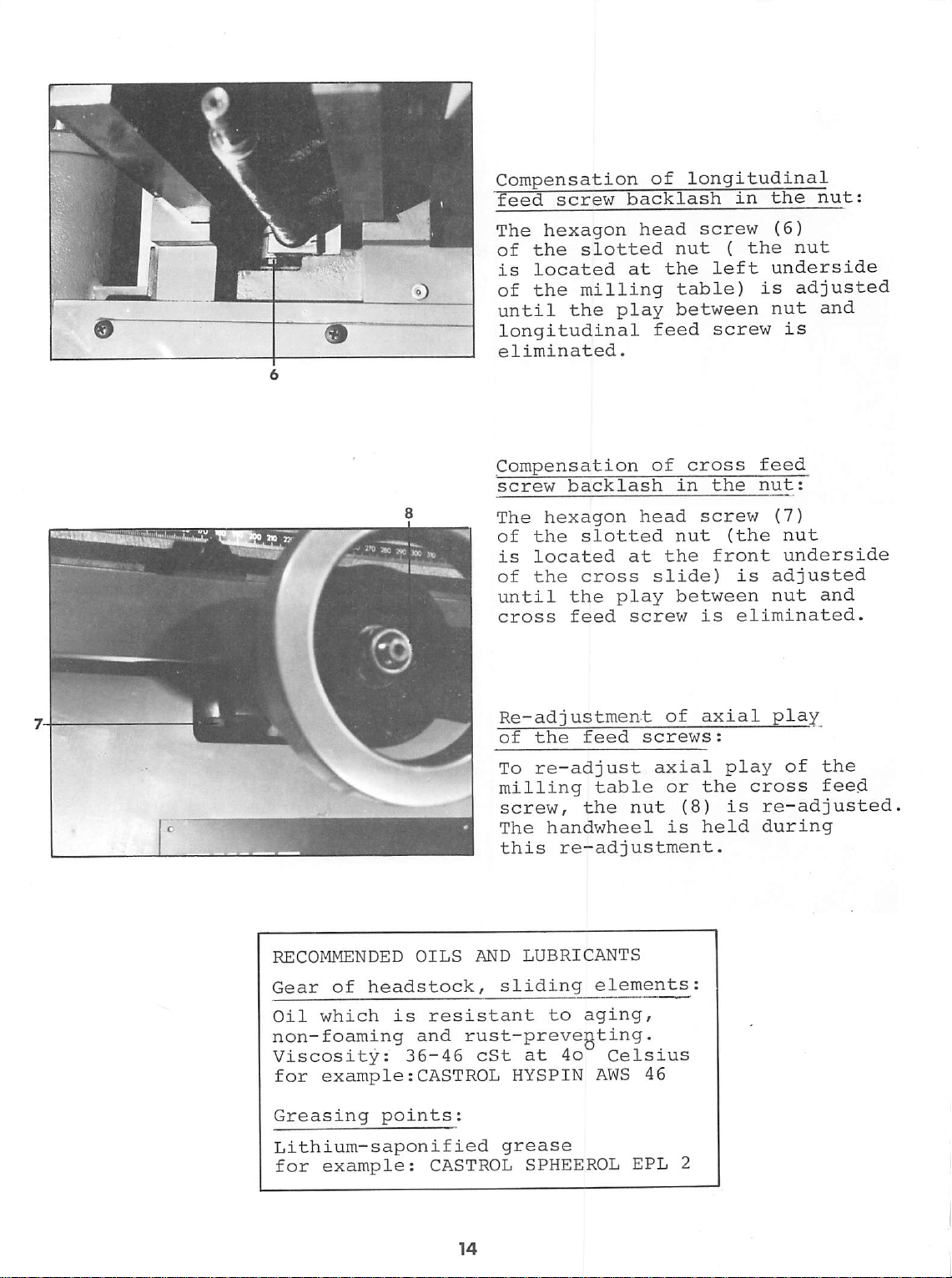
Compensation
feed
The
of
is
of
until
screw backlash
hexagon
the
slotted
located
the
milling
the
play
longitudinal
eliminated.
of
head
at
feed
longitudinal
in
screw
nut
(
the
the
left
table)
is
between
screw
the
nut:
(6)
nut
underside
adjusted
nut
and
is
Compensation
screw backlash
The
hexagon
of
the
slotted
is
located
of
the
until
cross
the
feed
at
cross
play
screw
Re-adjustment
of
the
feed
To
re-adjust
milling
screw,
The
this
table
the
nut
handwheel
re-adjustment.
of
in
head
nut
the
slide)
between
of
screws:
axial
or
(8)
is
cross
the
screw
(the
front
is
is
eliminated.
axial
play
the
is
held
feed
nut:
(7)
nut
underside
adjusted
nut
and
play
of
the
cross
feed
re-adjusted
during
RECOMMENDED
Gear
Oil
of
which
non-foaming
Viscosity:
for
example:CASTROL
Greasing
Lithium-saponified
for
example:
OILS
headstock,
is
resistant
and
36-46
points:
CASTROL
AND
LUBRICANTS
sliding
to
elements
aging,
rust-prevegting.
cSt
at
4o
Celsius
HYSPIN
grease
SPHEEROL
AWS
46
EPL
2

Clamping
Devices
for
Tools
—Y
CLAMPING
AND
COLLETS
Clamping
The
collet
with
round
1.
Collet
E
25
Collets
For
clamping
the
appropriate
Clamping
engraved
E
25
collets,
The
clamping
while
2.
Collet
ESX
25
(available
The
collets
greater
When
are
drawn
annular
The
collets
No.
225
WITH
Method
holder
shanks
Holder
range: h 13.
on
see
counterforce
Holder
Collets
from
of
clamping
the
clamping
off
ring
round
are
000)
THE
A
enables
and
of
(Order
with
collets
collet
the
collet. - For
the
brochure.
nut
is
tightened
is
exerted
(Order
mid-1981)
Type
ESX
ranges
nut
the
cone
the
collet
available
or
separately.
COLLET
HOLDER
clamping
drills.
No.
721
of
Type E 25,
for
each
The
clamping
the
with a hook
with
No.
520
25
enable
(see
table).
is
unscrewed,
of
the
collet
waist.
either
as a set
of
milling
000)
shank
diameter
Order
the
key
000)
you
holder
of
tools
for
Type
you
need
diameter.
is
Nos.
of
the
spanner
wrench.
for
Type
to
bridge
the
collets
by
the
14
(Order
Nominal
2,0
2,5
3,0
4,0
5,0
6,0
7,0
8,0
9,0
10,0
11,0
12,0
13,0
14,0
diameter
in
mm
individual
Chucking
capacity
1,5-2,0
2,0-2,5
2,5-3,0
3,0-4,0
4,0-5,0
5,0-6,0
6,0-7,0
7,0-8,0
8,0-9,0
9,0-10,0
10,0-11,0
11,0-12,0
12,0-13,0
13,0-14,0
collets
in
mm
ESX-25
Chucking
capacity
'As-Vm
^35
'/64
Va-yM-ya?
"/64-3A8
'%4-'/33-'Vm
'A-"/64
8/3J-
I9/»4-5As
3V64-"/32
33/(M-3/g_35/54
'V32-"/<14
Vi6-3»/64-IV3J
31/64-Vj
33/64-IV33-35/64
in
inches
The
using
it
can
the
milling
the
Spare
Order
No.
225
020
225
025
225
030
225
040
225
050
225
060
225
070
225
080
225
090
225
100
225
110
225120
225130
225140
21
machine
the
T-slot
also
be
table.
Parts
Important
Collets
721
into
vice
is
fitted
screws.
clamped
For
On
onto
the
List.
Note:
of
Type
000.
However,
collet
holder
onto
the
Maximat
the
screw
ESX
25
collets
520
000.
the
cross
slide
Super
angled
dimensions,
can
be
of
11,
plate
and
see
used
in
Type E 25
collet
holder
do
not
fit

Pos
1
2
3
4
5
6
7
8
9
10
11
12
13
14
15
16
17
18
19
20
21
22
23
24
25
26
27
28
29
30
31
32
33
34
35
36
37
38
39
40
41
42
43
44
45
46
F2A
F2A
F2A
F2A
F2A
F2B
F2A
F2A
F2B
F2A
F2B
F2A
F2B
F2A
F2A
F2A
F2A
F2A
F2A
D1A
D1B
F2A
F2A
F2A
F2A
F2A
B4A
B2A
B2A
D1Z
ZLG
ZSR
ZRG
ZFD
H4A
ZMU
ZSR
ZSR
ZSR
ZSR
ZSR
ZST
ZST
ZST
ZSR
ZSR
ZMU
ZSB
ZSR
ZFD
ZSB
Ref.
000
000 020
000
000
000
000 050
000
000
000
000 090
000
000
000
000
000
000
000
000150
000
020
020 070
000
000190
000
000
000
040
000
013
250
62
12
72
88
000
85
98
12
33
12
40
72
13
51
12
12
36
25
84
85
25
Nr.
010
030
040
050
060
070
070
090
100
100
110
120
130
140
160
070
180
200
210
220
011
080
000
060
0001
0616
3012
0337
300
1000
0003
0830
0625
1070
1030
0628
0616
0816
0816
0820
0800
0530
0510
4412
0640
DIN
M6x16DIN912-6.9
30x1,2
01N472
3x3,7
DIN
6888
M10DiN985-6
1,47x6,35
M8X30DIN912-6.9
M6x25DIN933-5.6
Ml
M10x30t)IN939-8.8
6x28DIN1472-6.8
M6X16DIN913-45H
M8x16DIN551-5.8
M8x16DIN912-6.9
M8x20DIN912-6.9
M8
B5,3
M5x10DIN84-4.8
A4x4x12DIN6885
B6,4
0x70
DIN
DIN
DIN
TYP
LL
DIN912-6.9
936-6
125
125
Benennung
Frastisch
Schlitten
Sockel
Saulantrager
Mutter
metr.
Mutter
USA
Spindeltr^er
Skalenring
Skalenring
Langsspindel
Langsspindel
Querspindel
Querspindel
Anschlag
Anschlagbolzen
Klemmschraube
Nachstelleiste
Nachstelleiste
Posltionsschild
Schild
Schild
Deckblech
Druckbolzen
Druckbolzen
Abstreifblech
Abstreiffilz
Handrad
Bogenfeder
G.
T-Nutenstein
Rillenkugellager
Zylinderschraube
Sicherungsring
Scheibenfeder
Zwischenring
Sechskantmutter
Hammerschraube
Zylinderschraube
Sechskantschraube
Zylinderschraube
Stiftschraube
PaBkerbstift
Gewindestift
Gewindestift
Zylinderschraube
Zylinderschraube
Sechskantmutter
Scheibe
Zylinderschraube
PaBfeder
Scheibe
metr.
USA
metr.
USA
metr.
USA
metr.
USA
1
2
100
Kegelgriff
Description
Milling
table
Slide
Pedestal
Column
support
Nut
metr.
Nut
USA
Screw
mount
Graduated
Graduated
Longitudinal
metr.
Longitudinal
USA
Cross
Cross
Stop
Bolt
Clamping
Gib
Gib
Setting
Scale
Scale
Cover
Adjusting
Adjusting
Wiper
Felt
Handwheel
Feed
Handle
T-nut
Ball
Allen
Circlip
Woodruff
Spacer
Hexagon
Screw
Allen
Hexagon
Allen
Stud
Grooved
Set
Set
Allen
Allen
Hexagon
Washer
Flat
Key
Washer
feed
feed
mark
mark
mark
sheet
plate
wiper
spring
bearing
head
head
head
screw
screw
head
head
head
ring
metr.
ring
USA
feed
feed
screw
screw
screw
metr.
USA
pin
1
pin
2
screw
key
nut
screw
head
screw
screw
adjusting
screw
screw
nut
screw
screw
screw
metr.
USA
pin
Designation
Table
de
fraisage
Chariot
Socle
support
Support-colonne
Ecrou
metr.
Ecrou
USA
Porte-broche
Bague
gradu^e
metr.
Bague
graduee
USA
Vis
filetle
longitudinale
Vis
filet§e
longitudinale
Vis
filetee
transversale
Vis
filet^e
transversale
Butee
Tige
de
butee
Vis
de
serr'age
Lardon
de
reglage
Lardon
de
reglage
Plaque
de
position
Echelle
metr.
Echelle
USA
Tole
de
protection
Boulon
de
pression
Boulon
de
pression
Plaquette
Racleur
Volant
Ressort
Levier
Ecrou
Roulement a bllles
Vis 6 pans
Anneau
Clavette
Douille
Ecrou 6 pans
Vis
Vis 6 pans
Vis
Vis 6 pans
Goujon
Cheville
Vis
Vis
Vis 6 pans
Vis 6 pans
Ecrou 6 pans
Rondelle
Vis
Clavette
Rondelle
de
en
feutre
arque
spherique
en
T
creux
de
retenue
d'&artement
creux
hexagonale
creux
de
posit
pointeau
pointeau
creux
creux
tete
cylindrique
racleur
metr.
USA
metr.
USA
1
2
postSrieur
post§rieur

Pos
47
48
49
50
51
52
53
54
55
56
57
58
59
61
62
63
64
65
66
67
68
69
70
71
72
73
74
75
76
/7
/8
.'M
Ref.
ZKG
ZST
ZNP
ZDK
F2A
F2A
F2B
F2A
F2B
F2A
ZMU
ZSB
ZSB
ZSB
ZSB
F2H
F2A
F2A
ZPG
ZPG
ZPG
ZPG
ZDK
ZSR
ZRG
ZMU
ZKO
ZEL
ZEL
ZEL
ZEL
ZEL
F2A
ZSR
ZEL
ZSR
ZRG
ZMU
ZDK
F2A
ZEL
Nr.
00
1060
11
0632
01
2000
60
0012
000
000
000
000
000
000
341000
251050
12
1001
121002
121003
100
100
100
10
0008
10
0007
20
1100
20
1350
60
0018
83
0416
28
0040
34
0401
26
0020
26
0030
26
3222
26
1221
26
3381
100
89
0510
01
0005
83
0325
28
0030
34
0300
60
0004
100
40
0002
270
240
240
250
250
230
020
020
030
040
010
'
DIN
6,0GK3DIN5401
6h11x32
INA
M10
B10,5
10x16x0,1
10x16x0,2
10x16x0,3
MZ
MZ
PG
PG
M4x16
B4
M4
M5X10DIN7985-
A
4.0
Bk6
M3x20
83
M3
Kapsto
B13
B11
11
13,5
DIN
DIN934
Q
KrG
DIN
DIN
NIP
DIN
DIN
DIN84-4.8
127
DIN84-4.8
127
934-5
F4
DIN
A2
934-6
125
Benennung
Stahlkugal
7
Zylinderstift
Schmiernippal
VerschluBstopfen
Positionsschlld
Ska
la 1 matr.
Skala 1 USA
Skala 2 matr.
Skala 2 USA
Frontschlld
Sechskantmuttar
Schaibe
PaBscheiba
PaSschaiba
PaBschaibe
Gr.
E-Ausriistung
Description
Ball
Dowel
pin
Grease
nipple
Stopper
Setting
mark
Scale 1 metr.
Scale 1 USA
Scale 2 metr.
Scale 2 USA
Front
plate
Hexagon
Washer
Compensating
Compensating
Compensating
Electrical
nut
equipment
washer
washer
washer
Designation
Bille
acier
Tige
de
serrage
Graisseur
Boucho'n
Plaque
de
position
Echelie 1 metr.
Echelle 1 USA
Echelie 2 metr.
Echelle 2 USA
Plaque
frontale
Ecrou 6 pans
Rondelle
Rondelle
Rondelle
Rondelle
Ens.
de
compensation
de
compensation
de
compensation
equipment
electrique
compl.
Deckel
Dackel
Deckel
Kabelvarschraubung
Kabalvarschraubung
Geganmuttar
Gegan
VerschluBstopfen
Zylinderschrauba
Fedarring
Ms
Sechskantmuttar
Kondensator
Schaltar-Standard
(Wechselstrom)
Schaltar-Standard
Schalter
Schalter-VDE
Schaltar-VDE
Dichtung
Linsanschraube
Klemmanleista
Zylinderschrauba
Fedarring
Sechskantmutter
VerschluBstopfen
Erdungsleiste
Pilztaster
links
links
rachts
mutter
franz.
franz.
220V
380V
(Dreh.)
380
V
|
Cover
left
left
right
type
nut
nut
trench
conduit
conduit
Cover
Cover
Screw
Screwtype
Lock
Lock
Stopper
Flat
head
screw
Spring
washer
Hexagon
Condenser
Switch-standard
nut
single-
phase
Switch-standard
Switch
Switch-VDE
Switch-VDE
Seal
Filister
head
Connection
Flat
head
Spring
washer
Hexagon
trench
220V
380
screw
strip
screw
nut
three-ph.
380
Stopper
Grounding
Push
connection
button
switch
fitting
fitting
V
V
1
Couvercle a gauche,France
Couvercle a gauche
Couvercle a droite
Raccordement a vis
Raccordement a vis
^ Centre
ecrou
Centre
ecrou
Bouchon
Vis
tSte
cylindrique
Rondelle a ressort
Ecrou 6 pans
Condensateur
Interrupteur
Interrupteur
Interrupteur
Interrupteur-VDE
Interrupteur-VDE
Joint
Vis a tete
Lardon
Vis
tSte
Rondelle ^ ressort
stand,
stand,
trance
d'etancheite
cylindr.
de
serrage
cylindrique
monophase
triphase
220V
380V
bomb§e
Ecrou 6 pans
8ouiihon
Lardon
prise
de
terre
Interrupteur d bouton
poussoir
380
V

Pos
Ref.
Nr.
DIN
Benennung
Description
Designation
1
2
3
4
5
6
7
8
g
10
11
12
13
14
15
16
17
18
19
20
21
22
23
24
25
26
27
28
29
30
E3A
000
E3A
000 040
E3A
000 050
E3B
000
E3A
000 060
E3A
000 070
E3A
000 080
E3A
000 090
E3A
000
E3A
000
E3B
000
El A 000
E1B
000
B2A
000
B2B-
000
B4A
040
C6A
130000
B2A
000
ZLG
60
2SR
87
ZNA
760144
ZSR
14
ZST
17
ZMU
34
ZST
11
ZST
16
ZRG
72
ZFD
88
ZMU
80
ZSB
25
ZSR
84
E3A
000
ZSR
33
ZSR
12
031
050
100
130
130
080
080
060
060
011
080
0002
1040
0256
0620
0600
0528
0610
6525
0337
0800
0840
0525
180
0812
0620
6000 - 2Z
Ml0x40
1,4x4
DIN1476-4.6
BM2,5x6
M6x20
M6
DIN934-6
5h11x28
M6x10
65x2,5
3x3,7
DIN
NM8
DIN980-8
B8,4
DIN
M5x25
M8x12
M6x20
DIN
787
DIN7513
01N417-5.8
DIN
7
DIN916-45H
DIN
472
6888
125
DIN
84-4.8
DIN933-5.6
DIN912-6.9
Aufbaumontage
Vertikaischlitten
Spindeltrager
Skalenring
Skalenring
Einstell
Druckleiste
metr.
USA
mutter
Tragerplatte
Gradskala
Nonius
Vertikalspindel
Vertikalspindel
Vertikalmutter
Vertikalmutter
Skalenschild
Skalenschild
Handrad
metr.
USA
metr.
USA
metr.
-USA
100
Kegelgriff
Bogenfeder
Rillenkugellager
T-Nutschraube
Kerbnagel
Gewi
ndesch
nei
dsch
Gevuindestift
Sechskantmutter
Zylinderstift
Gewindestift
Sicherungsring
Scheibenfeder
Sicherungsmutter
Scheibe
Zylinderschraube
Kabelhalter
Sechskantschraube
Zylinderschraube
raube
Assembly
Vertical
slide
Screw
mount
Scale
ring
Scale
ring
Adjusting
Gib
Plate
Graduated
Vernier
Vertical
screw
Vertical
screw
Vertical
nut
Vertical
nut
Graduated
Graduated
Handwheel
Handle
Feed
spring
Ball
bearing
T-nut
screw
Rivet
Self
tapping
Set
screw
Hexagon
Dowel
Set
nut
pin
screw
Circlip
Circlip
Securing
Washer
Flat
Cable
nut
head
holder
Hexagon
Allen
head
metr.
USA
nut
scale
metr.
USA
scale
scale
screw
screw
head
screw
metr.
USA
metr.
USA
screw
Assemblage
Support
Porte-broche
^
Bague
Bague
Ecrou
Lardon
poupee
echelle
metr.
echelle
USA
reglage
blocage
coulissant
Plaque
Echelle
Vernier^
Vis
mere
metr.
Vis
mere
USA
Ecrou
metr.
Ecrou
USA
Echelle
metr.
Echelle
USA
Volant
Levier
spherique
Lame
ressort
d'entrainement
Roulement a billes
Boulon
en
T
Rivet
de
fixation
Vis
taraud
Vis
pointeau
Ecrou 6 pans
Tige
de
serrage
.
Vis
pointeau
Anneau
de
retenue
Clavette
Ecrou
de
surete
Rondelle
Vis
tete
cylindrique
Support
calde
Vis
hexagonale
Vis 6 pans
creux
31
33
34
35
36
37
38
'39
4o
41
E3A
ZSR
E3A
E3A
E3A
E3A
ZSR
ZSB
ZSR
ZST
ZST
020 000
84
040
040
040
040 030
23
25
31
08
13
0512
0516
1050
o87o
o65o
08I0
000
010
020
M5x12
DIN84-4.8
M5X16DIN923-5.8
810,5
DIN
125
M8x7o
DIN
931-5.6
oh8x5o
DIN
MBxlo
DIN
913-45H
Vertical
Vertikalsaule
Zylinderschraube
Gruppe
Klemmhebel
Klemmhebel
Schraube
Druckfeder
Schraube
Scheibe
Sechskantschraube
Zyli
ndersti
7
Gewindestift
ft
'
column
Allen
head
screw
Clamping
Clamping
Screw
lever
lever
Spring
Screw
Washer
.irA.itjiMl
Dov/el
Set
Jli.-tld
pin
screw
compl.
jLI'v-V."
Colonne
Vis 6 pans
Ens.
Levier
Vis
Vis
levier
de
Ressort
Rondelle
Vib
hexagonale
Tige
de
Vis
pointeau
verticale
creux
de
serrage
serrage
de
compression
serrage

Pos.
1
2
3
4
5
6
7
8
9
lo
11
12
13
14
15
16
17
18
19
2o
21
22
23
24
25
26
27
28
29
3o
31
32
33
34
35
36
37
38
39
4o
41
42
43
44-45
44
45
46-47
46
47
48-49
48
49
5o
E3A
E3A
E3A
E3A
E3A
ZSR
ZSR
ZSB
E3A
E3A
E3A
E3A
E3A
E3A
E3A
E3A
E3A
E3A
E3A
E3A
ZOR
E3A
E3A
B2A
E3A
ZLG
ZSR
ZRG
ZST
ZSR
ZSB
ZSR
ZSR
ZSR
ZSR
ZFD
ZFD
ZSB
ZSB
ZOR
E3A
ZSR
ZRG
E3A
E3A
E3A
E3A
E3A
E3A
E3A
E3A
E3A
E3A
Ref.
No.
000
000
000
000
000
33
12
25
olo
olo
olo o4o
olo
olo
olo
olo o8o
olo
olo
olo
olo
olo
8o
olo
olo
o3o o6o
olo
16
0093
13
71
17
o4o5
12
o61o
lo
63
o41o
79
o412
12
0625
12
o62o
85
332o
85
4432
12
6oo5
98
o432
o4
6o31
oil
o8
1415
o5
1418
ol2
ol2
olo
ol3
ol3
ol3
ol4
ol4
ol4
ol5
o2o
llo
12o
14o
15o
o62o
M6x2o
M5xl2
0512
o64o
B6,4
o2o
o3o
o5o
o6o
o7o
llo
M45xl
12o
22o
23o
27o
1824
G18x24x3
3oo
33o
34o
16009/C3
12oo
Mlox2oo
1812
W18xl,2
M4x5
Moxlo
2181
SS12xl8xl,2
M4xlo
M4xl2
M6x25
M6x2o
A3x3x2o
A4x4x32
PS6ox75xo,5
V4,3
OR
46-3
000
M14xl,5
14x18x1,5cuDIN76o3
000
olo
o9o
000
olo
o2o
000
olo
o2o
000
DIN
DIN933-5.6
DIN912-5.9
DIN
125
DIN912-10.
DIN
DIN417-5.8
DIN912-6.9
DIN963-4.8
DIN7991-8.8
DIN912-6.9
DIN912-6.9
DIN6885
DIN5885
DIN
6798
DIN908-4.6
471
DIN988
Benennung
Motorflansch
Dichtung
Dichtung
Fbrderschnecke
2
4
Adapter
Sechskantschraube
Zylinderschraube
Scheibe
Getriebedeckel
Schiebewelle
Schaltwelle
Zahnrad
Schiebezahnrad
Zahnradblock
Schutzhaube
Mutter
42
Spanndeckel
Dichtung
Druckscheibe
Anlaufscheibe
3
Dichtring
Abdrlickmutter
Scheibe
Druckscheibe
Druckfeder
Rillenkugellager
9
Zylinderschraube
Sicherungsring
Gewindestift
Zylinderschraube
Seeger
StUtzscheibe
Senkschraube
Senkschraube
Zylinderschraube
•
Zylinderschraube
PaRfeder
PaBfeder
Seeger
PaBscheibe
Facherscheibe
0-Ring
Gr.
Pinole
VerschluBschraube
Dichtring
Gr.
Lagerdeckel
Lagerdeckel
Lagerblichse
Gr.
Zahnrad
Zahnrad
33
33
Lagerblichse
Gr.
Zahnrad
Zahnrad
Lagerblichse
Zahnrad
47
Description
Flange
Seal
2
Seal
4
Worm
Adaptor
Hexagonal
Allen
head
Washer
Gearing
Spline
Control
Gear
Sliding
Gear
Cover
Nut
Cover
Seal
Pressure
Washer
Sealing
Nut
Washer
Disc
Spring
Ball
Allen
Circlip
Set
Allen
Washer
Countersunk
Countersunk
Allen
Allen
Key
Key
Washer
Serrated
0-ring
Quill
Screw
Sealing
Bearing
Bearing
Bearing
Gear
Gear
Bearing
Gear
Gear
Bearing
Gear
cover
shaft
shaft
42
gear
bank
3
ring
bearing
head
screw
head
head
head
compl.
plug
ring
cover
cover
bush
33
compl.
33
bush
compl.
bush
47
head
screw
washer
screw
screw
screw
screw
screw
screw
lock
screv^
washer
compl.
Fausse
Joint
Joint
Vis
Adapteur
Vis
Vis 6 pans
Rondelle
Couvercle
Abre
Abre
Element
Train
Bloc
Couvercle
Ecrou
Couvercle
Joint
Disque
Rondelle
Bague
Ecrou
Rondelle
Rondelle
Ressort
Roulement a billes
Vis 6 pans
Anneau
Vis
Vis 6 pans
Rondelle
Vis
Vis
Vis 6 pans
Vis 6 pans
Clavette
Clavette
Rondelle
Rondelle
Bague-0
Ens.
Bouchon
Bague
Ens.
Chapeau
Bague
Ens.
Engrenage
Bague
Ens.
Engrenage
Bague
Engrenage
Designation
bride
d'etancheite
d'etancheit&
sans
fin
hexagonale
creux
rainure
de
debrayage
dente
42
baladeur
baladeur
d'etancheite
de
pression
d'etanch&ite
pointeau
de
compression
creux
de
retenue
pointeau
creux
tete
fraisee
tete
fraisee
creux
creux
canon
filete
d'etancheite
chapeau
de
de
palier
palier
de
engrenage
33
de
palier
engrenage
de
palier
47
palier
33
dents
2
4
3

Sr>annung
Voltage
(V)
Tension
Frequenz
Frequency
Frequence
Wechselstromausfiihrung
Single
Equipment
Ref.
Ref.
Ref.
phase
monophase
Nr.
fiir
Nr.
for
Nr.
condensateur
equipment
Kondensator
condenser
Ref.
Ref.
Ref.
Nr.
Nr.
Nr.
fiir
for
moteur
Motor
motor
220
115
ICQ
250
240
230
220
110
100
60
60
60
50
50
50
50
50
50
ZKO
ZKO
ZKO
ZKO
ZKO
ZKO
ZKO
ZKO
ZKO
15
15
15
15
15
15
15
15
15
4208
2430
2540
4606
4606
4208
4208
2430
2540
Drehstromausfuhrung
Three
Equipment
phase
triphase
equipment
ZMO
ZMO
ZMO
ZMO
ZMO
ZMO
ZMO
ZMO
ZMO
56
56
56
55
55
55
55
55
55
1220
1115
1100
1250
1240
1230
1220
1110
1100
Spannung
Voltage
(v)
Tension
440
220
500
350
440
380
220
Frequenz
Frequency
Frequence
60
60
50
50
50
50
50
13
Ref.
Nr
fiir
Motor
Ref.
N.
lor
motor
Ref.
Nr.
moteur
■
ZMO
ZMO
ZMO
ZMO
ZMO
ZMO
ZMO
56
56
55
55
55
55
55
3440
3220
3500
3350
3440
3380
3220

Pos.
1
2
3
4
5
6
7
8
9
lo
11
12
13
14
15
16
17
18
19
Ref.
76o
F2Z
ZSR
ZDK
ZDK
ZSB
76o
F2Z
F2Z
ZSR
ZMU
ZSB
ZXM
ZXM
ZMU
ZSR
ZSR
ZSB
ZDK
ZME
ZSB
o3o
211
12
7o
6o
64
22o
221
223
72
34
25
o2
3o
34
33
57
25
lo
o9
25
No.
ooo7
000
lo2o
oool
oolo
o3o5
000
000
2916
o5oo
o53o
2ooo
oool
looo
lo45
o87o
o84o
looo
lo5o
Mlox2o
6ox4ox3
Flo
Mlo
B2,9xl6
M5
DIN934-5
B5,3
DIN125
Mlo
DIN934-6
Mlox45
8x7o
DIN571-4.6
B8,4
DIN125
Slo
Bio,5
DIN
DIN912-8.8
DIN7972
DIN933
DIN125
Benennung
Spanewanne
Spanwanne
Zylinderschraube
Lame!lenstopfen
VerschluBstopfen
Schraubensicherung
Maschinenuntersatz
Maschinenuntersatz
Tlir
Blechschraube
Sechskantmutter
Scheibe
AnschlagschloS
Scharnier
Sechskantmutter
Sechskantschraube
Holzschraube
Scheibe
Dubel
Schllissel
Scheibe
Description
Chip
tray
Chip
tray
Socket
head
Plug
Plug
Lockwasher
Machine
Machine
Door
Sheet
stand
stand
metal
Hexagonal
Washer
Lock
Frame
joint
Hexagonal
Hexagon
Hexagon
Washer
head
wood
Plug
Key
Washer
nut
nut
screw
screw
screw
screw
Designation
Bac a copeaux
Bac i copeaux
Vis 6 pans
Bouchon
Bouchon
Rondelle
Socle-machine
Socle
Porte
Vis
Ecrou 6 pans
Rondel
Serrure
Charniere
Ecrou b pans
Vis
Vis a bois
Rondelle
Cheville
Cle
Ronaelle
creux
filete
filetfe
machine
en
tole
1e
hexagonale
15

Pos
Ref.
Nr.
DIN
Benennung
Description
Designation
525
330
1
ZME
11
3000
2
ZME
113010
3
ZMU
34
0400
4
ZSR
12
0410
5
ZME
11
3001
6
ZME
11
3002
7
ZME
11
3003
8
ZME
113011
g
ZSR
12
0410
10
ZME
11
3004
11
ZME
11
3005
12
ZME
11
3006
13
ZME
113012
14
ZME
11
3013
15
ZSR
12
0618
16
ZME
113014
17
ZME
11
3011
18
ZME
11
3007
19
ZME
113014
20
ZME
113015
21
ZWZ
11
0500
22
ZWZ
11
0300
23
ZWZ
11
3016
24
ZME
11
3008
25
ZME
11
3009
M4x12
M4
DIN
M4x8
DIN
M4x8
DIN
M4x8
DIN
DIN
6888
M6x16DIN
M4x6DIN916
M4x8
DIN
M4x4DIN916
6x6x40
SW5
DIN
SW3
DIN
SW2
DIN
DIN
934
916
912
916
912
912
916
911
911
911
Ausdrehkopf
Ausdrehkopf
Gewindestift
Sechskantmutter
Zylinderschraube
Spindeltrager
Skalenring
Mutter
Gewindestift
Zylinderschraube
Schlitten
Spindel
Mutter
Sicherungsring
Scheibenfeder
Zylinderschraube
Gewindestift
Gewindestift
Stahlhalter
Gewindestift
Ausdrehstahl
Schraubendreher
Schraubendreher
Schraubendreher
Einmaulschliissel
Holzkassette
Boring
head
Boring
head
Set
screw
Hexagonal
Socket
head
Bracket
Micrometer
Round
nut
Set
screw
Socket
head
Slide
Feed
screw
Feed
nut
Snap
ring
Key
Socket
head
Set
screw
Set
screw
Boring
bar
Set
screw
Boring
bit
Allen
key
wrench 5 mm
Allen
key
wrench 3 mm
Allen
key
wrench 2 mm
Spanner 7 mm
Wooden
boix
nut
screw
collar
screw
screw
Tdte
d'alesage
Tete
d'alesage
Vis
pointeau
Ecrou 6 pans
Vis 6 pans
Porte-broche
Bague
Ecrou
Vis
Vis 6 pans
Chariot
Vis
Ecrou
Anneau
echelle
pointeau
filetee
de
creux
creux
retenue
Clavette a disque
Vis 6 pans
Vis
Vis
Porte-outil
Vis
Outil
Cle a ecrous
Cle a ecrous
Cle a ecrous
Cle
Bolte
pointeau
pointeau
pointeau
d'alesage
de
service
en
bois
creux
19

15
16
Pos
1
2
3
4
5
6
7
8
9
10
11
12
13
14
15
16
Ref.
F2Z
F2Z
F2Z
F2Z
F2Z
F2Z
B2Z
C4Z
ZSR
ZSR
ZST
ZNP
ZSB
ZRG
ZMU
ZSB
Nr.
761
310
310
310
310
310
310
310
030
12
0616
121020
17
0625
01
2000
10
4201
71
1410
34
0800
25
0840
310
010
020
030
040
050
060
080
020
DIN
SW
10
M6x160IN912-6.9
Ml
0x20
DIN912-8.8
M6x25DIN417-5.8
14x20x1,5
W14x1
DIN
471
M8
DIN
934-6
88,4
DIN
125
Benennung
Gruppe
Maschinen-
schraubstock
Korper
Backe
Spindeltrager
Einsatz
Druckleiste
Spindel
Schlussel
Nutenschraube
Zylinderschraube
Zyllnderschraube
Gewindestift
Schmiernippel
Stiitzscheibe
Sicherungsring
Sechskantmutter
Scheibe
Description
Vice
compl.
Body
Moving
jaw
Screw
mount
Jaw
Plate
Operating
Key
T-Bolt
Allen
Allen
Set
Grease
Washer
Circlip
Hexagonal
Washer
wrench
head
head
screw
fitting
screw
screw
screw
nut
3 10
13
Designation
Ens.
Etau-machine
Corps
Mors
mobile
Porte - broche
Garniture
Plaquette
Broche
Cle
Boulon-T
Vis 6 pans
Vis 6 pans
Vis
pointeau
Graisseur
Rondelle
Anneau
de
Ecrou 6 pans
Rondelle
de
mors
creux
creux
retenue
14
20

Ausdrehkopf
Boring
head
T§te
d'alesage
18
(Ref.
17
16
Nr.
524
030)
Pos.
1
2
3
4
5
6
7
8
9
10
11
12
13
14
15
16
17
18
19
20
21
E3Z
E3Z
ZST
ZST
E3Z
ZST
E3Z
ZSR
E3Z
ZST
A3Z
A3Z
E3Z
E3Z
E3Z
ZST
ZST
ZST
ZWZ
ZUZ
ZWZ
Ref.
o3o
o3o o4o
13
14
o3o o5o
13
o3o
12
o3o o2o
16
loo
loo
o3o o8o
o3o
o3o
13
14
14
11
11
11
No.
olo
oSlo
o6o8
o6o6
o3o
o4o8
o4o4
o3o
o2o
o7o
o6o
o4o8
0616
o4o8
o2oo
o3oo
o5oo
M6xlo
M6x8
M6x6
M4x8
M4x4
M4x8
M6xl6
M4x8
SU2
SW3
SW5
DIN
DIN
DIN
DIN
DIN
DIN
DIN
DIN
DIN
DIN
DIN
DIN
913
914
913
912-6.9
916
913
914
914
911
911
911
Benennung
Ausdrehkopf
Schlitten
Gewindestift
Gewindestift
Spindel
Gewindestift
Skalenring
Zylinderschraube
Spindeltrager
Gewindestift
Plandrehstahl
Drehstahl
Stahlhalter
Stahlhalter
Mutter
Gewindestift
Gewindestift
Gewindestift
Schraubendreher
Schraubendreher
Schraubendreher
Rohling
Description
Boring
head
Slide
Set
screw
Set
screw
Feed
screw
Set
screw
Micrometer
Socket
head
Bracket
Set
screw
Boring
bit
Unground
Boring
bar
Boring
bar
Nut
Set
screw
Set
screw
Set
screw
Allen
key
Allen
key
Allen
key
collar
screw
bit
wrench
wrench
wrench
Designation
T§te
d'alesage
Chariot
Vis
pointeau
Vis
pointeau
Vis
filetee
Vis
pointeau
Bague
d'echelle
Vis 6 pans
Porte-broche
Vis
pointeau
Outil
d'al&sage
Acier
brute
Porte-outil
Porte-outil
Ecrou
Vis
pointeau
Vis
pointeau
Vis
pointeau
C1& a gcrous
Cle i bcrous
C1& a ecrous
creux

1.
REMOVE
OUTLET.
2.
Dismount
the
3.
Remove
mount basic
screw-type
with
Remove
padding.
Thread
element
(5)
trated
base
lock
onto
.
MACHINE
both
of
plug
conduit
nut
left
lock
(4)
the
PLUG
covers
the
machine.
on
left
element
(2)
.
cover
nut
(3),
and
rubber
cable
ELECTRICAL
FROM
from
cover,
(1)
of
fitting
and
rubber
cone
ring
as
illus
CONNECTION
1 2
3
4.
Clamping
the
right
a)
Single-phase
Clamp
the
(yellow/green)
contact
ing
strip
The
blue
(Mp,
tact
R)
points
the
cable
housing
model
grounding
point
and
are
(6)
.
brown
clamped
1
of
and
ends
cover;
wire
to a free
the
ground
wires
to
2.
onto
con
Three-phase
Clamp
the
(yellow/green)
contact
ing
strip
The
blue,
wires
to
NOTE;
With
is
in
(R,S.T)
contact
three-phase
possible
the
wrong
direction
5.
does
arrow
In
ple,
be
Mount
not
on
this
the
interchanged.
right
padding,
screw-type
on
left
model
grounding
to a free
point
(6)
.
brown
of
are
points
that
direction
of
the
correspond
the
motor
case
blue
2
and
wires
cover
tighten
conduit
housing
wire
the
ground
and
black
clamped
1,2
and
execution,
the
motor
(feed
milling
wit
switch
(for
brown)
with
cable
rubber
with
fitting
cover.
3.
it
runs
table
the
plate)
exam
must

Pos
Ref.
No.
DIN
Benennung
DescriDtion
Desianation
Feed
Vorschubgetriebe
1
F9A
000
010
2
F9A
000 020
3
F9A
000
030
4
F9A
000 040
5
F9A
000 050
6
F9A
000
060
7
F9A
000
070
8
F9A
000 080
9
F9A
000
090
10
F9A
000110
11
F9A
000
120
12
F9A
000
130
13
F9A
000
140
14
F9A
000
150
15
F9A
000
160
16
F9A
000
170
17
F9A
000
180
18
F9A
000
190
19
F9A
000
200
20
D1A
000
390
21
E3A
010
100
22
E3A
010
090
23
ZLG
62
0101
24
ZLG
60
0001
25
ZFD
85
6636
26
ZFD
85
4418
27
ZFD
85
4480
28
ZSR
12
0508
29
ZSR
12
0816
30
ZSR
89
0408
31
ZRG
71
1210
32
ZRG
71
1010
33
ZHL
81
0324
34
ZKG
00
1060
35
ZRG
21
0200
36
ZGF
15
2108
37
ZBU
50
1003
38
ZBU
50
1002
39
ZBU
50
1004
40
ZSB
10
2181
41
ZSB
12
1201
ZSB
12
1203
ZSB
12
1205
42
ZSB
25
0530
43
ZSR
33
0516
F9A
010
000
44
F9A
010 010
45
F9A
010
020
46
F9A
011
000
47
C4A
180
020
6201 - Z
6000 - Z
A6x6x36DIN6885
A4x4x18DIN6885
A4x4x80DIN6885
M5x8DIN912-6.9
M8x16DIN912-6.9
M4x8DIN7g85-4.8
12x1
DIN
471
10x1
DIN
471
3 X 24
DIN
1481
6GK3DIN5401
INA
WR
20
21XM8GN
L12G7x18r6x20
DIN
L16G7x22r6x20
DIN
L12G7x18r6x12
DIN
12x18x1,2
12x18x0,1
12x18x0,3
12x18x0,5
B5,3
M5X16DIN933-5.6
1850
1850
1850
DIN
513
DIN988
DIN988
DIN988
DIN988
125
Vorschubgehause
Schnecke
Schaltwelle
Welle
Schiebezahnrad
Schneckenrad
Zahnrad
Zahnrad
Zahnrad
24
15
39
Distanzring
Stange
Funktionsschild
Getriebetrager
Schaltbolzen
Schaltnabe
Distanzscheibe
Scheibe
Motorflansch
Frontschild
Druckfeder
Gleitstein
Lagerbuchse
Rillenkugellager
Rillenkugellager
PaBfeder
PaBfeder
PaBfeder
Zylinderschraube
Zylinderschraube
Linsenschraube
Sicherungsring
Sicherungsring
Spannhulse
Stahlkugel
Sprengring
Zylinderknopf
Buchse
Biichse
Buchse
Stiitzscheibe
PaBscheibe
PaBschelbe
PaBscheibe
Scheibe
Sechskantschraube
Gruppe
Kupplung
Gehause
Gewindering
Zentrierstiick
Kupplungsscheibe
mechanism
Housing
Worm
Control
shaft
Shaft
Sliding
gear
Worm
gear
wheel
Gear
24
Gear
15
Gear
39
Compensating
Bar
Indicator
Mounting
Operating
Hub
Washer
Washer
plate
element
bolt
Flange
Front
plate
Compression
Slider
Bearing
bush
Ball
bearing
Ball
bearing
Key
Key
Key
Allen
head
screw
Allen
head
screw
Filister
head
screw
Circlip
Circlip
Lock
pin
Ball
Retaining
Knob
Bush
Bush
Bush
Washer
ring
Compensating
Compensating
Compensating
Washer
Hexagon
Coupling
head
compl.
Housing
Threaded
Centering
Coupling
ring
piece
washer
ring
spring
washer
washer
washer
screw
Mecanisme
Botte
Vis
Arbre
Arbre
Train
Roue a vis
Engrenage
Engrenage
Engrenage
Bague
Tige
Plaquette
Lardon
Boulon
Moyeu
Rondel
Rondelle
Bride
Plague
Ressort
Crosse
Douille
Roulement a billes
Roulement a billes
Clavette
Clavette
Clavette
Vis 6 pans
Vis 6 pans
Vis a tSte
Anneau
Anneau
Goupille
Bille
Bague
Bouton
Douille
Douille
Douille
Rondelle
Rondelle
Rondelle
Rondelle
Rondelle
Vis
Ens.
Corps
Bague
Piece
Rondelle
d'avance
d'avance
sans
fin
de
commande
baladeur
sans
24
15
39
d'ecartement
indicatrice
de
montage
de
manoeuvre
le
frontale
de
compression
de
palier
creux
creux
lentiforme
de
retenue
de
retenue
de
en
acier
de
retenue
cylindrique
de
compensation
de
compensation
de
compensation
hexagonale
embrayage
filetee
de
centrage
d'embrayage
fin
serrage

Pos,
48
49
50
51
52
53
54
55
56
C4A
C4A
ZEL
ZEL
ZPG
ZPG
ZPG
ZMO
ZKO
ZME
Ref.
180
180
21
21
10
20
10
20
No.
030
040
0012
0013
0008
1350
0009
0020
DIN
MZB
13
PG
13,5
STP
11
•
•
Benennung
Druckfeder
Scheibe
Gruppe
E-Ausriistung
Schalter
Schalter
Kabelverschraubung
Gegenmutter
Kabelverschraubung
Motor
Kondensator
Liifterhaube
Wechselstrom
Drehstrom
fiir
Motor
Description
Compression
Washer
Electrical
Switch
Switch
Screw-type
Lock
Screw-type
Motor
Condenser
End
shield
spring
equipment
single
phase
threephase
conduit
nut
conduit
compl.
fitting
fitting
Designation
Ressort
de
compression
Rondelle
Ens.
equipement
Interrupteur
Interrupteur
Raccordement a vis
Contre-ecrou
Raccordement a vis
Moteur
Condensateur
Capot
de
electrique
monophase
triphasS
ventilateur
Wechselstromausfiihrung
Spannung
Voltage
Tension
100
110
220
230
240
250
100
115
220
(V)
Frequenz
Frequenzy
Frequence
50
50
50
50
50
50
60
60
60
Single
Equipement
Ref.
Ref.
Ref.
ZKO
ZKO
ZKO
ZKO
ZKO
ZKO
ZKO
ZKO
ZKO
phase
Nr.
fiir
Kondensator
Nr.
for
condenser
Nr.
condensateur
18
18
18
18
18
18
18
18
18
equipment
monophase
4512
4512
4003
4003
4003
4003
4512
4512
4003
Drehstromausfiihrung
Three
phase
equipment
Equipement
tri
phase
Ref.
Ref.
Ref.
ZMO
ZMO
ZMO
ZMO
ZMO
ZMO
ZMO
ZMO
ZMO
Nr.
Nr.
Nr.
fiir
for
moteur
58
58
58
58
58
58
59
59
59
Motor
motor
1100
1110
1220
1230
1240
1250
1100
1115
1220
Spannung
Voltage
Tension
220
380
440
350
500
220
440
(V)
Frequenz
Frequency
Frequence
50
50
50
50
50
60
60
10
Ref.
Ref.
Ref.
ZMO
ZMO
ZMO
ZMO
ZMO
ZMO
ZMO
Nr.
Nr.
Nr.
fiir
for
moteur
58
58
58
58
58
59
59
Motor
motor
3220
3380
3440
3350
3500
3220
3440