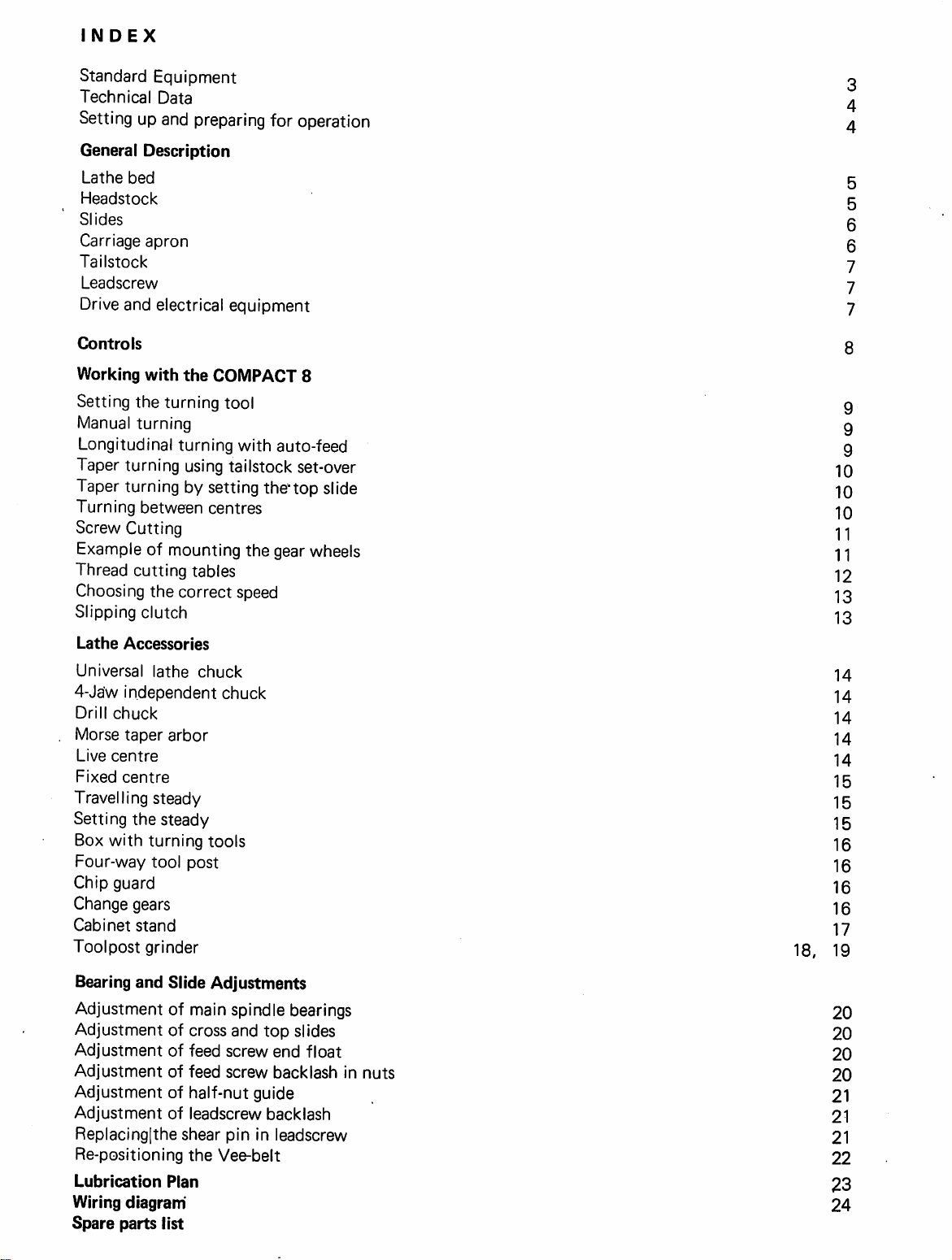
INDEX
Standard
Technical
Setting
General
Lathe
Equipment
Data
up
and
preparing
Description
bed
Headstock
Slides
Carriage
Tailstock
Leadscrew
Drive
Controls
Working
Setting
Manual
Longitudinal
Taper
Taper
Turning
Screw
Example
Thread
Choosing
Slipping
apron
and
electrical
with
the
the
turning
turning
turning
turning
turning
using
by
between
Cutting
of
mounting
cutting
tables
the
correct
clutch
setting
centres
for operation
equipment
COMPACT
tool
with
tailstock
the
speed
8
auto-feed
set-over
the-top
gear
slide
wheels
3
4
4
5
5
0
5
7
7
7
3
g
g
g
10
1q
10
11
11
12
I3
I3
Lathe
Accessories
Universal
4-Ja'w
Drill
Morse
Live
Fixed
Travel
Setting
Box
Four-way
Chip
Change
Cabinet
Toolpost
Bearing
Adjustment
Adjustment
Adjustment
Adjustment
Adjustment
Adjustment
Replacinglthe
Re-positioning
Lubrication
Wiring
Spare
lathe
chuck
independent
chuck
taper
arbor
centre
centre
ling
steady
the
steady
with
turning
tool
guard
tools
post
gears
stand
grinder
and
Slide
of
main
of
cross
of
feed
of
feed
of
half-nut
of
leadscrew
shear
the
Plan
diagram
parts
list
chuck
Adjustments
spindle
and
screw
screw
pin
Vee-belt
bearings
top
slides
end
float
backlash
guide
backlash
in
leadscrew
in
nuts
18^
14
14
14
14
14
I5
I5
I5
15
15
15
15
17
19
20
20
20
20
21
21
21
22
23
24
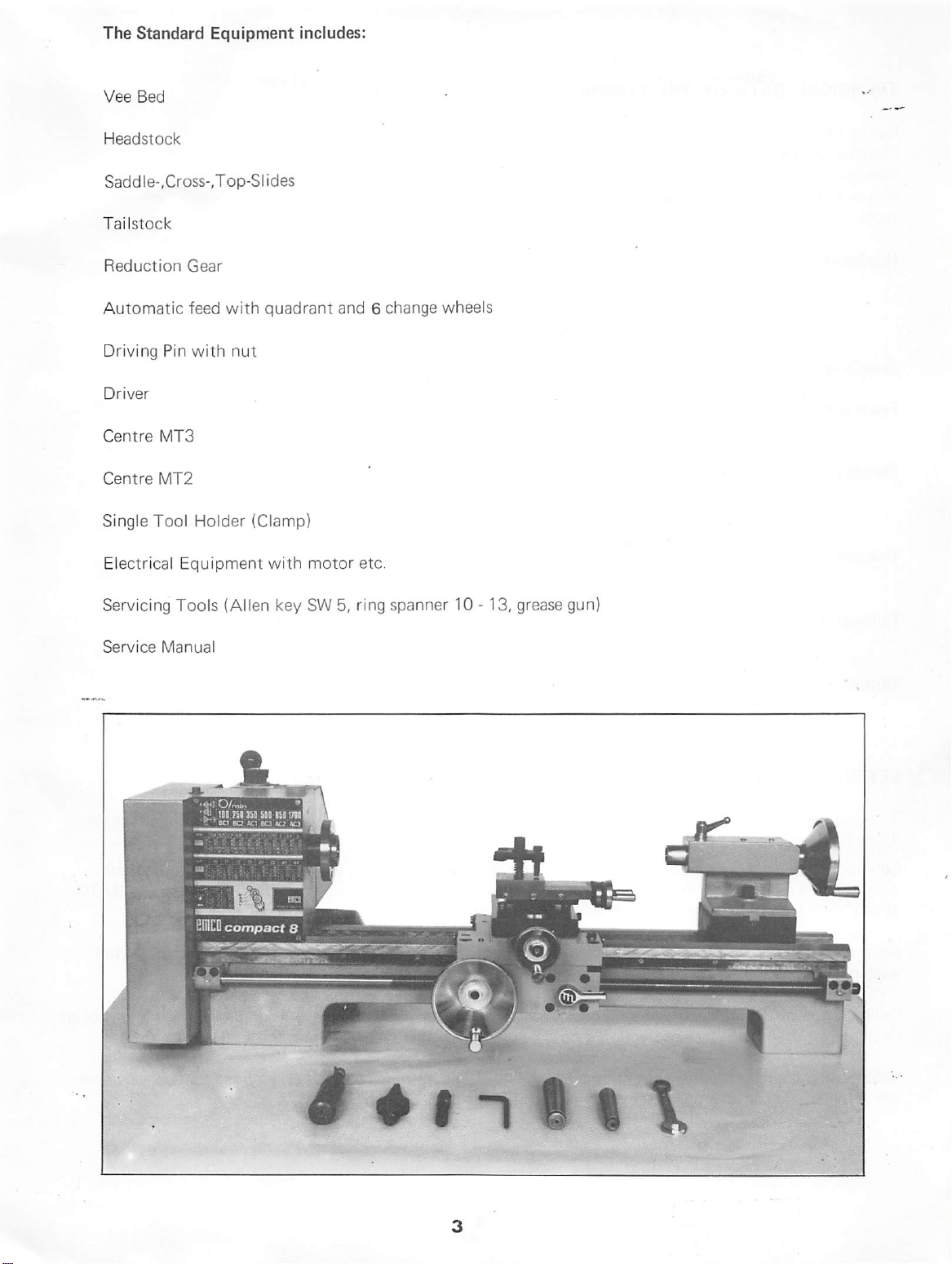
The
Standard
Vee
Bed
Headstock
Saddle-.Cross-,Top-Slides
Tai
lstock
Equipment
includes:
Reduction
Automatic
Driving
Driver
Centre
Centre
Single
Electrical
Servicing
Service
Gear
feed
Pin
with
MT3
MT2
Tool
Holder
Equipment
Tools
Manual
with
quadrant
nut
(Clamp)
with
(Allen
key
and 6 change
motor
SW
5,
ring
etc.
wheels
spanner
10-13,
grease
gun)
O
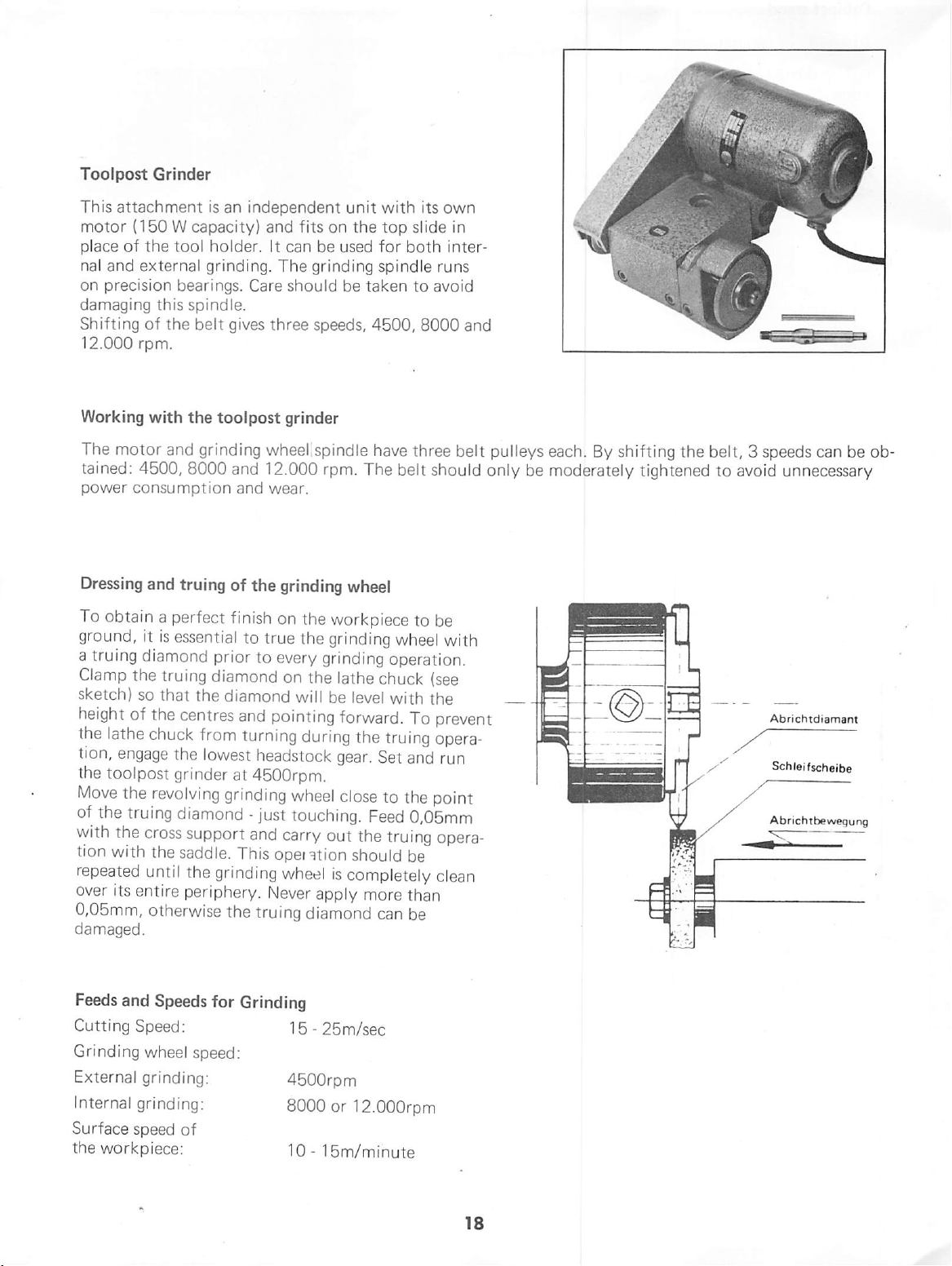
Toolpost
This
motor
place
nal
on
precision
damaging
Shifting
12.000
Grinder
attachment
{150 W capacity)
of
the
and
external
this
of
rpm.
is
an
tool
holder.
grinding.
bearings.
spindle.
the
belt
gives
independent
and
fits
It
can
The
Care
should
three
unit
on
be
used
grinding
be
speeds,
with
the
top
for
spindle
taken
4500,
its
own
slide
both
inter
runs
to
avoid
8000
in
and
Working
The
tained:
power
Dressing
To
ground,
a
truing
Clamp
sketch)
height
the
tion,
the
Move
of
the
with
tion
repeated
over
0,05mm,
damaged.
with
the
motor
and
4500,
8000
consumption
and
truing
obtain a perfect
it
is
essential
diamond
the
truing
so
that
of
the
centres
lathe
chuck
engage
toolpost
the
the
with
its
the
grinder
revolving
truing
diamond - just
cross
support
the
saddle.
until
the
entire
periphery.
otherwise
toolpost
grinding
and
and
of
the
wheel
12.000
wear.
finish
to
true
prior
to
diamond
the
diamond
and
pointing
from
turning
lowest
headstock
at
4500rpm.
grinding
and
This
grinding
Never
the
truing
grinder
.spindle
rpm.
grinding
on
the
the
every
grinding
on
the
will be
have
The
wheel
workpiece
grinding
lathe
level
forward.
during
the
gear.
wheel
close
touching.
carry
operation
wheel
apply
diamond
Feed
out
the
should
is
completely
more
three
belt
belt
should
to
be
wheel
with
operation.
chuck
(see
with
the
To
prevent
truing
Set
to
opera
and
run
the
point
0,05mm
truing
opera
be
clean
than
can
be
pulleys
only
each.
be
moderately
By
shifting
tightened
the
belt, 3 speeds
to
avoid
/"
can
be
unnecessary
Abrichtdismant
Schletfscheibe
Abrichtbewegung
ob
Feeds
and
Cutting
Grinding
External
Internal
Surface
the
Speed:
wheel
grinding:
grinding:
speed
workpiece:
Speeds
for
speed:
of
Grinding
15 - 25m/sec
4500rpm
8000
10 - 15m/minute
or
12.000rpm
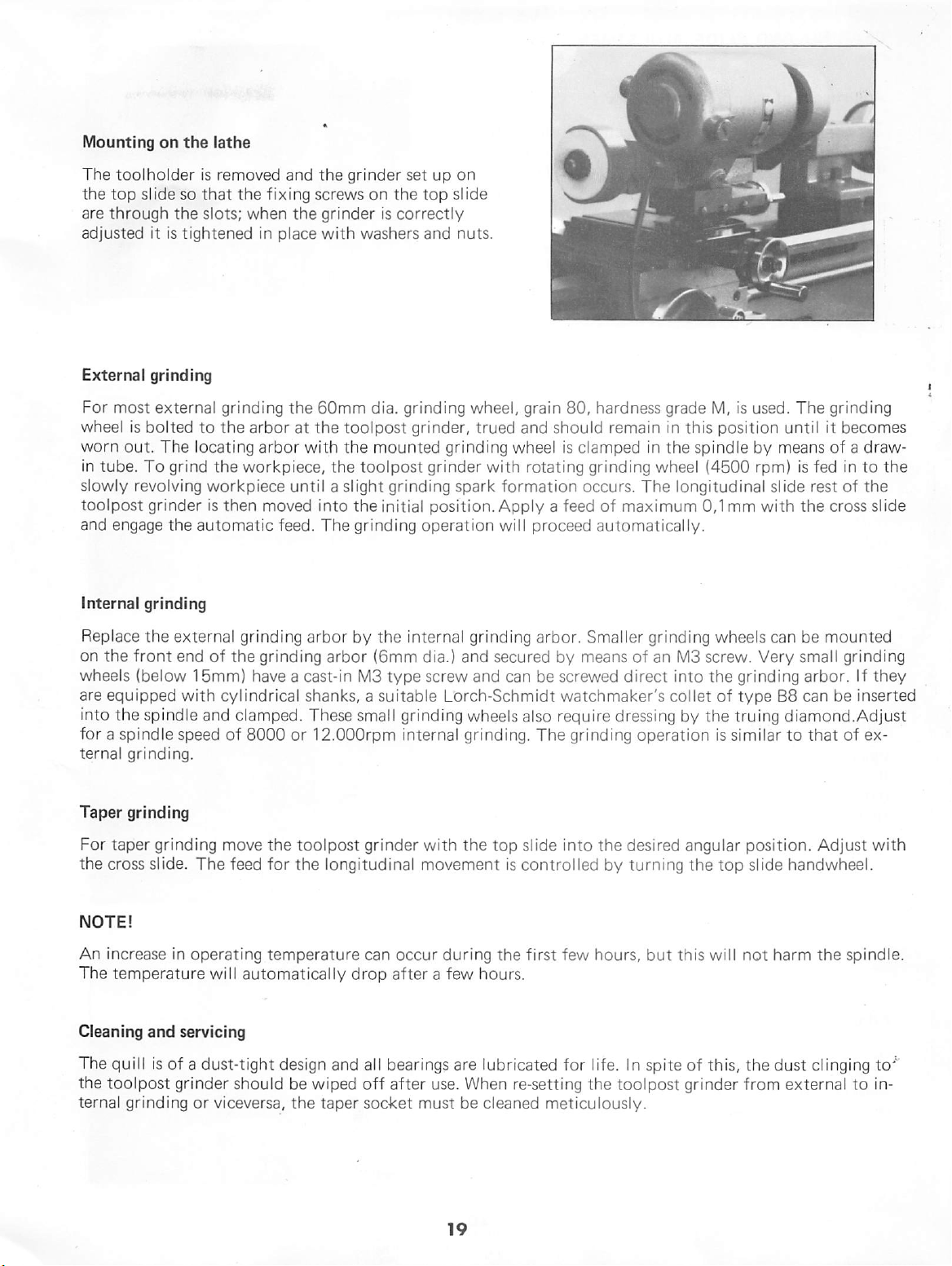
Mounting
The
toolholder
the
top
slide
are
through
adjusted
it
on
the
iathe
is
removed
so
that
the
slots;
is
tightened
the
when
in
and
the
fixing
screws
the
grinder
place
with
grinder
set
on
the
is
correctly
washers
up
on
top slide
and
nuts.
External
For
wheel
worn
in
tube.
slowly
toolpost
and
Internal
Replace
on
wheels
are
into
for a spindle
ternal
Taper
For
the
grinding
most
external
is
bolted
out.
The
To
grind
revolving
grinder
engage
the
grinding
the
the
front
(below
equipped
the
spindle
grinding.
grinding
taper
grinding
cross
slide.
external
end
15mm)
with
speed
grinding
to
the
arbor
locating
arbor
the
workpiece,
workpiece
is
then
moved
automatic
feed.
grinding
of
the
grinding
have a cast-in
cylindrical
and
clamped.
of
8000
move
the
The
feed
for
the
60mm
at
the
with
until a slight
into
The
arbor
shanks, a suitable
These
or
12.000rpm
toolpost
the
dia.
grinding
toolpost
the
the
toolpost
grinder,
mounted
grinding
the
initial
grinding
by
the
internal
arbor
(6mm
M3
type
small grinding
internal
grinder
longitudinal
wheel,
grinding
grinder
spark
position.
grain
trued
and
wheel
with
rotating
formation
Apply a feed
operation wil l
grinding
dia.)
and
secured
screw
and
can
Lorch-Schmidt
wheels
also
grinding.
with
the
top
slide
movement
is
control
80,
hardness
should
remain
is
clamped
grinding
occurs.
of
proceed
arbor.
be
The
automatically.
Smal
by
means
screwed
watchmaker's
require
dressing
grinding
into
the
led
by
grade
in
this
in
the
spindle
wheel
(4500
The
longitudinal
maximum
ler
grinding
of
direct
an
col
0,1
M3
screw.
into
let
by
the
operation
desired
turning
angular
the
M,
is
used.
position
by
rpm)
slide
mm
with
wheels
the
of
can
Very
grinding
type
truing
is
simi
lar
position.
top
slide
The
grinding
until
it
becomes
means
B8
of a draw-
is
fed
in
rest
of
the
cross
be
mounted
small
grinding
arbor.
can
be
to
the
the
slide
If
they
inserted
diamond.Adjust
to
that
of
ex
Adjust
with
handwheel.
NOTE!
An
increase
The
temperature
Cleaning
The
the
ternal
and
quill is
toolpost
grinding
in
operating
will
servicing
of a dust-tight
grinder
or
viceversa,
temperature
automatical
design
should
be
the
ly
drop
and all
wiped
off
taper
socket
can
occur
after a few
bearings
after
must
during
are
use.
When
be
the
first
few
hours.
lubricated
for
re-setting
cleaned
meticulously.
hours,
life.
In
the
toolpost
but
this
spite
of
grinder
will
not
this,
the
from
harm
the
spindle.
dust clinging
external
to
to'^
in

Antrieb
Drive
Entrainement
Pos
6
8
9
10
11
12
13
14
15
16
17
18
19
20
21
22
23
24
25
26
27
28
29
30
31
32
33
34
35
36
37
38
39
40
1
2
3
4
5
7
81A
81A
ZSR
ZRG
ZS8
ZSR
ZSR
ZS8
81A
BIB
ZSR
81A
81A
ZSR
ZNP
ZRG
ZS8
81A
82A
81A
ZKG
81A
ZLG
ZRG
81A
ZRM
ZRM
ZS8
ZRG
ZMU
ZSR
ZRG
81A
81A
81A
81A
81A
ZSR
ZS8
C3A
81A
ZSR
81A
ZMU
Ref.No.
060
000
12
28
25
63
84
25
000
000
84
210
000
12
01
71
10
211
030
000 090
00
000
77
71
000
45
51
25
28
34
12
28
000
215
000
000
000
12
21
062
000
12
000
34
000
060
0612
ooSo
0640
0512
0508
0530
180
180
0406
000
210
0820
1000
1210
2181
000
130
1060
340
2542
2512
320
0690
7170
1050
0100
1000
0520
0050
100
000
080
130
120
0620
0640
040
050
0622
110
0600
M6x12DIN
86
DIN 127
86,4
DIN
M5x12
M5x8
85,3
DIN
M4x6
M8x20
12x1
DIN
22x18x1
6,0GK3
AS
2542
25x1,2
Gates
5M-690
170XL
810,5
810
DIN
M10
DIN
M5x20
85
DIN
M6x20
A6,4
DIN
M6x22
M6
DIN
DIN
DIN
DIN
DIN
DIN
DIN
DIN
050
DIN
DIN
127
DIN
DIN
125
84
125
84
471
125
127
934
9021
934
963
912
5401
471
912
912
912
912
BENENNUNG
G.
Deckel
Abdeckblech
Zylinderschraube
Federring
Scheibe
Senkschraube
Zylinderschraube
Scheibe
Frontschild
Frontschild
metr.
USA
Zylinderschraube
G.
Tragerplatte
Tragerplatte
Zylinderschraube
Schmiernippel
Sicherungsring
Stutzscheibe
G.
Kupplung
Bundlager
Vorgelegeriemenscheibe
Stahlkugel
Druckfeder
Axiallagerscheibe
Sicherungsring
Kupplungsriemenscheibe
Keilriemen
Zahnriemen
Scheibe
Federring
Sechskantmutter
Zylinderschraube
Federring
Scheibe
G.
Motorriemenscheibe
Motorriemenscheibe
Aniaufring
Aniaufscheibe
Zylinderschraube
Scheibe
Druckfeder
Klemmleiste
Zylinderschraube
Riemenscheibenwelle
Sechskantmutter
DESCRIPTION
Cover
Covermount
Round
head
Clip
Washer
Flat
head
screw
Round
head
Washer
Plate
metr.
Plate
Round
Bracket
Bracket
Round
Grease
USA
head
plate
plate
head
nipple
screw
screw
Clips
Washer
Clutch
Bearing
bush
Countershaft
Ball
Feed
spring
Thrust
bearing
Clip
Belt
pulley
Vee
belt
Drive
belt
Washer
Clip
Nut
Round
head
screw
Clip
Washer
Pulley
Pulley
Start
sleeve
Spacer
Round
head
screw
Washer
Feed
spring
Clamp
piece
Round
head
screw
Belt
pulley
shaft
Hexagon
nut
screw
screw
pulley
washer
DESIGNATION
Couvercle
T6le
Vis
Rondelle
Rondelle
Vis
Vis
Rondelle
Plaque
Plaque
Vis
Plaque
Plaque
Vis
Graisseur
Circlip
Rondelle
Embrayage
Palier
Poulie
crantee
Bille
Ressort
Disque
Circlip
Poulie
Courroie
Courroie
Rondelle
Rondelle
Ecrou
Vis
Rondelle
Rondelle
Poulie
Poulie
Douille
Disque d rainure
Vis
Rondelle
Ressort
Lardon
Vis
Arbre
Ecrou
assemble
de
couverture
tSte
cylindrique
grover
plate
tdte
fraisee
tete
cylindrique
grover
frontale
frontale
t§te
cylindrique
support
assemblee
support
seule
t^te
cylindrique
plate
assemble
d'assemblage
de
renvoi
acier
de
compression
trapezoidale
trapezoidale
crantee
plate
grover
hexagonal
tete
cylindrique
grover
plate
epaul^e
moteur
assemblee
moteur
seule
entretoise
tSte
cylindrique
plate
de
compression
de
blocage
t§te
cylindriques
des
poulies
hexagonal
pour
metr.
USA
courroie
de
I'embrayage
de
clavette
1
'
<
.
;

E — Ausriistung
Electrical
equipment
Equipement
^lectrique
Pbs
2
3
4
5
6
7
8
9
10
11
12
13
14
15
16
17
M6x12
B6
DIN
M4
A4,3
M5x8
A5,3
DIN
DIN
DIN
DIN
DIN
DIN
127
934
912
6797
933
6798
Ref.
No.
1
B1A
170
000
ZSR
12
0612
28
101
100
100
100
Nr.
Nr.
Nr.
0060
000
030
020
010
34
0401
97
0430
*■
20
1100
01
0002
10
0003
33
0508
0530
98
siehe
Tabelle
see
table
voir
tableau
ZRG
B1A
B1A
B1A
HIE
ZMU
ZSB
ZEL
ZKO
ZPG
ZEL
ZPG
ZSR
ZSB
ZMO
Ref.
Ref.
Ref.
BENENNUNG
G.
E—Gehause
Zyiinderschraube
Federring
G. E —
Deckel
Schalterschild
Isolierplatte
Erdungsschild
Sechskantmutter
Zahnscheibe
Schalter
Kondensator
Gegenmutter
Bruchklemme
PG — Verschraubung
Sechskantschraube
Facherscheibe
Motor
DESCRIPTION
E—housing
Flat
head
screw
Clip
Roofing
Switch
signboard
Insulating
Earthing
Nut
Serrated
Switch
Condenser
Lock
Breakage
Screw
Hexagon
Washer
Motor
plate
plaid
lock
nut
clamp
coupling
screw
washer
DESIGNATION
Boitier
§lectrique
Vis
t§te
cylindrique
Rondelle
Couvercle
Plaquette
contacteur
Plaquette
Connexion
Ecrou
Rondel
Interrupteur
Condensateur
Contre - 6crou
Domino
Passe-fil
Vis
Rondelle
hexagonal
le
fpour
tete
hexagonale
grover
du
indicatrice
isolate
pour
dent§e
§ventail
Moteur
assemble
boitier
mise a la
cable
d'alimentation
assemble
pour
le
"terre"
:
|
^
Spannung
Voltage
Tension
Standard
VDE
USA
CSA
(V)
220
220
115
115
100
100
110
220
230
240
250
Frequenz
Frequency
Frequence
50
50
60
60
50
60
50
60
50
50
50
Ref.
Ref.
Ref.
ZMO
ZMO
ZMO
ZMO
ZMO
ZMO
ZMO
ZMO
ZMO
ZMO
ZMO
Nr.
Nr.
Nr.
fiir
Motor
for
motor
moteur
95
95
96
94
95 1100
96
95 1110
96 1220
95 1230
95
95 1250
1220
1220
1115
1115
1100
1240
Ref.
Ref.
Ref.
ZKO
ZKO
ZKO
ZKO
ZKO
ZKO
ZKO
ZKO
ZKO
ZKO
ZKO
Nr.
Nr.
Nr.
fiir
Kondensator
for
condenser
condensateur
15
4212
15
4212
15
2540
15
2540
15
2550
15
2540
15
2550
15
4210
15
4212
15
4212
15
4212
Ref.
Ref.
Ref.
ZEL
ZEL
ZEL
ZEL
ZEL
ZEL
ZEL
ZEL
ZEL
ZEL
ZEL
Nr.
fiir
Nr.
for
Nr.
interrupteur
22
22
22
22
22
22
22
22
22
22
22
Schalter
switch
3318
4348
3318
3318
3318
3318
3318
3318
3318
3318
3318
11

Raderschere
Quadrant
Lyre
Pos
10
11
12
13
14
15
16
17
18
19
3
4
5
6
7
8
g
1
2
Ref.No.
B1A
ZSR
B2A
B2A
B2A
B2A
B2A
B2A
ZSR
B2Z
B2A
B1A
B2Z
B2A
B2A
B2A
B1A
B1A
ZNP
000
010
12
0630
000
300
000
310
000
350
000
270
000
280
000
450
33
0610
200
010
000
270
000
190
200
020
000
310
071
020
071
040
000 020
000
040
01
1000
M6x30
M6x10
DIN
DIN
DIN
912
933
BENENNUNG
Schere
Zylinderschraube
Scheibe
Keilhiilse
Scherstift
Wechselrad
80
Zwischenring
Sicherungsring
Sechskantschraube
Wechselrad
Wechselrad
Zahnrad
Wechselrad
Keilhiilse
Scheibe
Nutenstein
Scherbolzen
Scheibe
25
80
80
30
Schmiernippel
DESCRIPTION
Quadrant
Flat
head
Washer
Bush
Bushing
Gear
80
Bushing
Clip
Hexagonal
Gear
25
Gear
80
Gear
80
Gear
30
Bush
Washer
T-nut
Shaft
Washer
Grease
fitting
screw
screw
DESIGNATION
Lyre
nue
Vis
tetecylindrique
Rondelle
Douille • clavette
Goupille
Engrenage
Douille • entretoise
Rondelle
Vis
Engrenage
Engrenage
Engrenage
Engrenage
Douille - clavette
Rondelle
Ecrou
Boulon—axe
Rondelle
Graisseur
tSte
hexagonale
en
plate
de
cisaillement
80
dents
fer a cheval
25
dents
80
dents
80
dents
30
dents
plate
T
fer a cheval
13

700
010
G.
Radersatz
Set
of
change
gears
Jeu
d'engrenages
assembles
Pos
.
6
8
9
1
2
3
4
5
7
Ref.No.
B2A
B2A
B2Z
B2Z
B2Z
B2Z
B2Z
B2A
B2A
000
000
200
200
200
200
200
000
000
250
290
030
050
060
080
090
260
280
DIN
BENENNUNG
Wechselrad Z =
Wechselrad Z =
Wechselrad Z =
Wechselrad Z =
Wechselrad Z =
Wechselrad Z =
Wechselrad Z =
Wechselrad Z =
Zwischenring
DESCRIPTION
20
35
40
50
55
65
70
75
Change
Change
Change
Change
Change
Change
Change
Change
Bushing
gear
gear
gear
gear
gear
gear
gear
gear
DESIGNATION
Engrenage
Engrenage
Engrenage
Engrenage
Engrenage
Engrenage
Engrenage
Engrenage
Douille-entretoise
20
35
40
50
55
65
70
75
dents
dents
dents
dents
dents
dents
dents
dents
Pos
10
11
12
13
14
15
16
17
18
1
2
3
4
5
6
7
8
9
Ref.No.
B2A
B2A
B2A
B4A
B2A
B2A
B2A
HI
A
B2A
B2A
B2B
B2A
B2A
ZHL
ZSR
ZFD
ZRG
ZRG
ZKG
010
010
010
020
030
010
Oil
010
010 050
010
060
010
070
000
380
010
090
000
011
000
oil
000
012
000
013
81
0322
12
0630
93
2001
21
0100
0080
21
00
1040
DIN
3x22
DIN
M6x30
DIN
20x10,2x0,9
2093
WR
10
WR
8
4,0GK3
DIN
1481
912
DIN
5401
G.
SchloBplatte
BENENNUNG
SchloKplatte
Zwischenrad
Ritzel
Handrad
SchloBscheibe
Nachstellschraube
Fiihrungsschiene
Druckfeder
Einstellschraube
Gr.
SchloBmutter
Or.
SchloBmutter
Gr.
SchloBhebel
Gr.
Kegelgriff
Spannhiilse
Innensechskantschraube
Tellerfeder
Sprengring
Sprengring
Stahlkugel
Apron
DESCRIPTION
Apron
casting
Gear
Shaft
gear
Hand
wheel
Locking
cam
Adjusting
Guide
Feed
spring
Adjusting
Half
nut
Half
nut
Handle
Handle
Grooved
Allen
Spring
pin
head
washer
Clip
Clip
Ball
screw
screw
screw
Tablier
assemble
DESIGNATION
Tablier
nu
Pignon
double
Pignon
du
volant
Volant
Verrou
de
la
noix
Vis-pointeau
Languettes
Ressort
Vis-pointau
Noix = 2
Noix = 2
Levier
Manneton
Goupille
Vis
tete
Rondelle
Rondelle
Rondelle
Bille
de
de
de
compression
de
demi-noix
demi
d'enclenchement
assemble
fendue
six
pans
assiette
grower
grower
acier
intermediaire
r6glage
guidage
r^glage
noix
assemble
creux
15

Langs-
und
Querschlitten
Saddle
and
Cross
Slide
Trainard
at
chariot
transversal
Pos
6
8
10
11
12
13
14
15
16
17
18
19
20
21
22
23
24
25
26
27
28
29
30
31
32
33
34
35
36
37
38
39
41
2
3
4
5
7
9
1
Ref.No.
84A
B4A
B2A
828
82A
B4A
84A
84A
84A
82A
82A
82A
82A
82A
84A
ZSR
2ST
ZMU
ZKG
ZSR
ZSR
ZST
ZS8
ZSR
ZSR
ZS8
ZNP
ZSR
ZSR
ZSR
84A
848
84A
848
84A
82A
828
84A
848
82A
82A
82A
82A
ZFD
ZST
ZNA
ZSR
000
110
000
120
000
130
000130
000
180
000
170
000
180
000
190
000
200
000
660
000
150
000
140
000
210
000
220
000
240
63
0612
51
0412
34
0400
00
2316
12
0616
84
0408
08
0512
25
0530
33
0516
31
0635
25
0640
01
1000
12
0835
12
0630
12
0830
020
000
020
000
020 010
020 010
020
020
000 060
040 030
020
030
020 030
000
080
000 070
000
100
013
000
88
0337
51
0806
76
0144
12
0616
DIN
M6x12
DIN
M4x12DIN551
M4
DIN
934
3/16GK3
M6x16
DIN
M4x8
DIN
548x12
85,3
86,4
M5x16
M6x35
M8x35
M6x30
M8x30
3x3,7
M8x6
1,4x4
M8x16
DIN
DIN
DIN
DIN
DIN
DIN
DIN
DIN
DIN
DIN
DIN
DIN
'
963
DIN5401
912
84
7
125
933
931
125
912
912
912
6888
551
1476
912
BENENNUNG
Schlitten
Querschlitten
Quermutter
Quermutter
8ettleiste
Abstreifer
Abstreiffilz
Abstreifer
Abstreiffilz
Klemmstiick
Senkscheibe
Nachstellschraube
Einstelleiste
Druckstift
Deckblech
Senkschraube
Gewindestift
Sechskantmutter
metr.
USA
Stahlkugel
Innensechskantschraube
Zylinderschraube
Zylinderstift
Scheibe
Sechskantschraube
Sechskantschraube
Scheibe
Schmiernippel
Innensechkantschraube
Innensechskantschraube
Innensechskantschraube
G.Querspindel
G.Querspindel
Querspindel
Querspindel
metr.
USA
metr.
USA
Querspindeltrager
Skalenschlld
Skalenschild
Skalenring
Skalenring
metr.
USA
metr.
USA
8ogenfeder
Handrad
Mutter
Gr.
Kegelgriff
Scheibenfeder
Gewindestift
Kerbnagel
1 n nensechskantsch
rau
DESCRIPTION
Carriage
Cross-slide-table
Cross-slide-nut
Cross-slide-nut
Gib
Cover
Way
Cover
Way
Binding
Bushing
Adjusting
Gib
Stud
Cover
Flat
Set
screw
Nut
Ball
Allen
Flat
Flat
Washer
Hexagon
Hexagon
Washer
Grease
Allen
Allen
Allen
Lead
Lead
Lead
Lead
Lead
Plate
Plate
Micrometer
Micrometer
Spring
Handwheel
Nut
Handle
Key
Set
screw
Rivet
Allen
be
mount
cover
mount
cover
piece
mount
head
head
head
screw
fitting
head
head
head
screw
screw
screw
screw
screw
metr.
USA
head
screw
screw
screw
screw
head
head
screw
screw
screw
compl.
compl.
metr.
USA
mount
.
collar
collar
screw
metr.
USA
screw
screw
metr.
USA
metr.
USA
DESIGNATION
Trainard
Transversal
Noix
Noix
Languette
Plaquette
Racleur
Plaquette
Racleur
Plaque
Douille
Vis-pointau
Lardon
Cheville
T&le
Vis
Vis
Contre-^crou
Bijle
Vis
Vis
Cheville
Rondel
Vis
Vis
Rondelle
Graisseur
Vis
Vis
Vis
Broche
Broche
Broche
Broche
Support-pal
Plaquette
Plaquette
Vernier
Vernier
Lame
Volant
Ecrou 2 pans
Manneton
Clavette
Vis-pointau
nu
nu
du
transversal
du
transversal
de
couvre-racleur
en
feutre
couvre-racleur
en
feutre
de
blocage
fraisSe
de reglage
de
pression
de
recouvrement
t§te
frais6e
de
reglage
acier
t6te 6 pans
tdte
cylindrique
le
plate
tSte
hexagonale
t6te
hexagonale
plate
t§te 6 pans
t§te 6 pans
tdte 6 pans
de
commande
de
commande
de
commande
de
commande
ier
graduee
gradu^
metr.
USA
ressort
demi-lune
Rivet
Vis
t§te 6 pans
guidage
de
rgglage
creux
creux
creux
creux
de
courbe
de
reglage
creux
metr.
USA
du
transversal
du
transversal
du
du
broche
metr.
USA
r
I
transversal
transversal
r
I
17

G.
Obersupport
Compound
Chariot
superieur
Pos
10
11
12
13
14
15
16
17
18
19
20
21
22
23
24
25
26
27
28
29
30
31
2
3
4
5
6
7
8
9
1
Ref.No.
B4A
B2A
B2A
B2A
B2A
B2A
B2B
B2A
B4A
B2A
B2A
B2A
ZSR
ZSR
ZSR
ZST
ZMU
ZMU
ZHL
ZHL
B4A
B4A
B4A
B4A
B4B
B2A
B2B
B2A
B2B
B2A
828
B4A
B2A
ZFD
B2A
B2A
ZST
050
010
050
020
050 030
050
041
050
050
050
060
050
060
050
070
050
080
050
090
050
040
61
0830
84
0512
84
0610
51
0410
34
0400
34
0600
81
0212
81
0312
050
050
050
051
000
051
000
051
010
051
010
051
020
051
020
020
030
020
030
051
010
040
051
88
0337
080
000
000
100
51
0806
100
100
110
120
130
AM8x30
M5x12
M6x10
M4x10
M4
DIN
M6
DIN
2x12
3x12
3x3,7
M8x6
DIN
DIN
DIN
DIN
DIN
DIN
DIN
DIN
DIN
934
934
84
84
551
1481
1481
6888
551
561
BENENNUNG
Obersupport
Oberplatte
Einstelleiste
Klemmring
Skalenring
Obermutter
Obermutter
Einstellschraube
Schraube
Nutenschraube
Druckstift
Sechskantmutter
Sechskantschraube
metr.
USA
Zylinderschraube
Zylinderschraube
Gewindestift
Sechskantmutter
Sechskantmutter
Spannhiilse
Spannhijlse
Spannklaue
Ballenscheibe
Druckfeder
G.Oberspindel
G.Oberspindel
Oberspindel
Oberspindel
Oberspindeltrager
Oberspindeltrager
Skalenring
Skalenring
Handrad
metr.
USA
metr.
USA
metr.
USA
metr.
USA
Kegelgriff
Scheibenfeder
Bogenfeder
Mutter
Gewinde.-tift
DESCRIPTION
Compound
Swivel
base
Gib
Clamping
Micrometer
Lead
screw
Lead
screw
Adjusting
Screw
T-nut
screw
Stud
Nut
Hexagon
Flat
Flat
Set
Nut
Nut
Lock
Lock
Tool
Washer
Spring
Lead
Lead
Lead
Lead
Lead
Lead
Micrometer
Micrometer
Handwheel
Handle
Key
Spring
Nut
Set
head
head
screw
pin
pin
clamp
screw
screw
screw
screw
screw
screw
screw
head
screw
screw
ring
collar
nut
nut
screw
metr.
USA
metr.
USA
mount
mount
collar
collar
metr.
USA
screw
metr.
USA
metr.
USA
DESIGNATION
Chariot
superieur
Support-glissidre
Lardon
de
Bague
de
Embase
gradu^e
Noix
metr.
Noix
USA
Bague-ecrou
Boulon
de
Boulon
en
Cheville
Ecrou
hexagonal
Vis a t§te
Vis
tete
cylindrique
Vis
t@te
cylindrique
Vis-pointau
Contre-^crou
Ecrou
hexagonal
Goupille
Goupille
Bride
Rondelle
Ressort
Broche
assemblee
Broche
assemblee
Broche
Broche
fendue
fendue
de
serrage
spherique
de
du
du
nue
nue
Palier-support
Palier-support
Vernier
metr.
Vernier
USA
Volant
Manneton
Clavette
Lame
Ecrou 2 pans
Vis
ressort
de
reglage
demi-lune
nu
r^glage
blocage
de
r^glage
fixation
T
hexagonale
de
reglage
d'outil
compression
chariot
metr.
chariot
USA
metr.
USA
de
broche
de
broche
courhe
du
porte-outil
superieur
superieur
metr.
USA
19

G.
Reitstock
Tailstock
compl.
Poupee
mobile
assemblee
Pos
6
10
11
12
13
14
15
16
17
18
19
20
21
22
2
3
5
7
8
1
4
g
Ref.No.
B2A
B2B
B2A
B2B
B2A
B2A
B2B
B4A
B2A
B2A
B2A
B2A
B2A
B2B
B2A
B2A
B4A
B2A
B4A
ZST
B2A
ZFD
ZST
ZSR
ZNA
ZNP
B2A
040
010
040
010
040
020
040
020
040 030
000
060
040
030
010
040
040
050
040 060
040 070
080
040
000
OSO
020
030
080
000
100
000
041
000
010
041
020
041
17
0630
000
013
88
0337
0806
51
0650
31
0144
76
01
1000
090
040
M6x30
3x3,7
M8x6
M6x50
1,4x4
DIN
DIN
DIN
DIN
DIN
DIN
417
6888
551
931
1476
BENENNUNG
Reitstock
Reitstockpinole
Triebschraube
Triebschraube
Bundbiichse
Skalenschild
Skalenschild
Handrad
Knebelgriff
Klemmbacke
Klemmstiick
Fiihrungsschraube
Skalenring
Skalenring
Bogenfeder
Mutter
G.
Reitstock
Reitstockplatte
Gewindestift
G.
Scheibenfeder
Gewindestift
Sechskantschraube
Kerbnagel
Schmiernippel
Klemmplatte
pinole
metr.
USA
metr.
USA
metr.
USA
metr.
USA
Reitstockplatte
Kegelgriff
DESCRIPTION
Tailstock
Tailstock
Lead
Lead
Bushing
Plate
Plate
Handwheel
Lever
Clamp
Binding
Guide
Micrometer
Micrometer
Feed
Nut
Tailstock
Tailstock
Tailstock
Set
Handle
Key
Set
Hexagonal
Rivet
Grease
Clamping
ram
ram
screw
screw
metr.
USA
piece
pin
spring
base
base
screw
screw
fitting
metr.
USA
collar
collar
screw
plate
metr.
USA
metr.
USA
DESIGNATION
Canon
metr.
Canon
USA
Broche
metr.
Broche
USA
Douille
d'assemblage
Plaquette
Plaquette
Volant
Levier
de
blocage
Mors
de
blocage
Mors
de
blocage
Vis
de
guidage
Bague
du
vernier
Bague
du
vernier
Lame
ressort
Ecrou 2 pans
Embase
de
assemblee
Corps
de
la
Embase
nue
Vis
de
reglage
post§rieure
Manneton
Clavette
demi-lune
Vis
de
r6glage
Boulon
tete
Rivet
Graisseur
Plaque
de
graduee
metr.
graduee
USA
du
canon
superieur
inf^rieur
metr.
USA
courbe
la
contre-poupee
contre-poupee
anterieure
hexagonale
blocage
nue
ou
21

747
*
0
Supportschleifapparat
Tool
post
grinder
Rectifieuse
adaptable
Pos
10
11
12
13
14
15
16
17
18
19
20
21
22
23
24
25
26
27
28
29
30
31
32
33
1
2
3
4
5
6
7
8
9
Ref.No.
SOB
SOA
SOA
SOA
SOA
SOA
SOA
A2Z
A2Z
A2Z
A2A
ZLG
ZLG
ZRG
ZST
ZFD
A2Z
A2Z
A2Z
ZRM
ZSR
ZST
ZST
ZMU
ZHL
SOA
SOA
A2A040
A2A
A2Z
ZSR
ZSB
ZWZ
ZMO
000
000
000
000
000
010
010
280
280
280
040
281
280
280
000
000
090
410
DIN
010
020
030
040
070
000
010
010
020
030
060
4903
80
1307
00
0170
21
06
0156
88
0226
000
050
060
0352
05
12
0630
17
0612
16
0808
0800
31
0220
81
050
060
060
020
050
84
0310
0320
25
0016
55
0 •
50
NA4903/C
E
13
K7
WR17
1,5
M6x6
2x2.6
DIN
352x5x3
M6x30
M6x12
AM8x8
M8
DIN
2x20
DIN
M3x10
A3.2
DIN
DIN
DIN
DIN
6331
DIN
152
DIN7
6888
912
417
1481
84
125
NA
916
BENENNUNG
Korper
Riemenschutz
Motorbolzen
Riemenscheibe
Scheibenschutz
G.
Schleifpinole
Riemenscheibe
Spannzangenpinole
Spindel
Verschraubung
Mutter
Nadellager
Kugellager
Sprengring
Zylinderstift
Scheibenfeder
G.
Anzugspindel
Zugrohr
Spannrad
Keilriemen
Innensechskantschraube
Gewindestlft
Gewindestift
Sechskantmutter
Spannhiilse
Dorn
Spindel
Mutter
Gegenscheibe
Zylinderstift
Zylinderschraube
Scheibe
Schleifscheibe
Motor
DESCRIPTION
Housing
Cover
Bolt
Pulley
Guard
Quill
Pulley
Quill
Tapered
Screw
Spring
Pin
Draw
Draw
Draw
V-belt
Allen
Set
Set
Pin
Tapered
Tapered
Washer
Pin
Washer
Grinding
Nut
Needle
Ball
bearing
Key
bar
bar
bar
head
screw
screw
Nut
Nut
Flat
head
Motor
arbor
joint
bearing
washer
arbor
arbor
wheel
wheel
screw
screw
DESIGNATION
Corps
Protecteur
Boulon
Poulie
Protecteur
Broche
Poulie
Fourreau
Broche
Ecrou
Ecrou
Roulement a aiguilles
Roulement a billes
Circiip
Cheville
Clavette
Tige
Tige
Volant
Courroie
Vis
Vis
Vis
Ecrou
Goupille
Tasseau
Tasseau
Ecrou
Contre-flasque
Tige
Vis
Rondel
Meule
Moteur
de
courroie
d'articulation
du
moteur
de
meule
de
rectification
de
la
broche
de
la
de
fermeture
cylindrique
demi-lune
de
rappel
assemblee
de
rappel
de
serrage
trap^zoidale
BTR
pointau
pointau
hexagonal
fendue
porte-meule
porte-meule
cylindrique
t§te
cylindrique
le
plate
exterieure
*
broche
seule
exterieure
int§rieure
du
moteur
assemblee
*)
Bei
In
your
A
la
Bestellung
commande
orders
bitte
please
specifier
Spannung
indicate
voltage.
le
voltage.
angeben.
25

750
000
G.
Maschinenstander
Machine
stand
Socle-armoire
Pds
10
11
12
13
14
15
16
17
18
19
20
21
22
23
24
1
2
3
4
5
6
7
8
9
Ref.No.
B2Z
B2Z
C4Z
C4Z
C4Z
B2Z
B2Z
B2Z
C4Z
C4Z
C4Z
C4Z
C4Z
C4Z
B2Z
B2Z
ZSR
ZMU
ZRG
ZMU
ZSR
ZSB
ZSR
ZMU
360
360
220
220
220
360
360
360
220
220
220
220
220
220
360
360
DIN
010
020
030
040
050
030
040
070
110
140
161
150
090
100
050
060
M8x12
DIN
DIN
DIN
DIN
934
127
934
DIN
DIN
DIN
934
933
933
125
933
33
0812
34
0800
27
0080
34
0600
33
1035
1050
25
33
0508
34
0500
M8
A8
DIN
M6
Ml0x35
810,5
M5x8
M5
BENENNUNG
Linker
StanderfuS
Rechter
StanderfuS
Mittelteil
Spanwanne
Tiir
Linke
Tasse
Rechte
Tasse
Einlageplatte
Winkel
Auflageblech
Deckel
AbfluBgitter
Gummieinlage
Gummieinlage
Moosgummi
Moosgummi
Sechskantsch'raube
Mutter
Federring
Mutter
Sechska
ntsch
rau
be
Scheibe
Sechska
ntsch
rau
be
Mutter
DESCRIPTION
Table
leg
left
Table
leg
right
Mid-section
Chip
tray
Door
Holder
left
Holder
right
Insert
Angle
plate
Face
plate
Cover
Sink
grid
Rubber
packing
Rubber
packing
Sectional
Sectional
Hexagon
Hexagon
Spring
Hexagon
Hexagon
Washer
Hexagon
Hexagon
strandrubber
strandrubber
head
nut
washer
nut
head
head
nut
screw
screw
screw
DESIGNATION
Fut
de
gauche
FQt
de
droite
Panneau
Bac a copeaux
Porte
Plateau
Plateau
Etag&res
Cornidres
Barrettes
Caches
Crepine
Insert
Insert
Bande
Bande
Vis
Ecrou
Rondelle
Ecrou
Vis
Rondelle
Vis
Ecrou
de
de
de
de
en
caoutchouc
en
caoutchouc
de
caoutchouc
de
caoutchouc
tSte
hexagonale
hexagonal
grower
hexagonal
t§te
hexagonale
t§te
hexagonale
hexagonal
gauche
droite
plate
jonction
tdle
mousse
mousse
27

Pos.
Ref.
242
090
Nr.
DIN
BENENNUNG
G.
Spannzangenhalter
DESCRIPTION
Collet
attachment
DESIGNATION
Ens.
porte-pince
1
BIZ
040
010
2
BIZ
041
010
3
ZSR
39
0820
4
ZMU
34
0800
5
ZST
11
0710
M8x200IN93g-5.6
M8
DIN
934-6
ShllxlOO
DIN
7
Spannmutter
Zangenhalter
Stiftschraube
Sechskantmutter
Zylinderstift
Locking
Collet
Stud
Hexagon
Dowel
ring
holder
nut
pin
Ecrou
de
serrage
Porte-pince
Goujon
Ecrou 6 pans
Tige
de
serrage
Pos.
1
2
3
4
5
700
A5Z
BIZ
ZSR
ZMU
ZST
Ref.
060
o4o o2o
o61
39
34
11
No.
do
o82o
oBoo
o71o
DIN
M8x2o
DIN
MB
DIN
934-6
6hll X loo
939-5.9
DIN
Benennung
Gr.
Spannzangenhalter
fiir
Spannzangen
ESX
25
Spannmutter
Zangenhalter
Stiftschraube
Sechskantmutter
7
Zylinderstift
Description
Collet attachment
compl.
for
ESX
Locking
Collet
Stud
Hexagon
Dowel
collets
25
ring
holder
nut
pin
Ens.
pinces
Ecrou
Porte-pince
Goujon
Ecrou 6 pans
Tige
Designation
porte-pince
ESX
25
de
serrage
de
serrage
pour
29

Pos.
1
2
3
4
5
6
7
8
9
10
11
12
13
14
15
16
17
18
19
20
21
22
23
24
25
26
27
28
29
30
31
32
BIZ
BIZ
BIZ
BIZ
C3A
C3B
C3A
B2A
B2A
ZSR
ZSR
ZST
ZKG
ZST
ZMU
C3A
C3B
C3A
C4A
C3A
B2A
B2A
B2A
B2B
B2A
C4A
ZSR
ZFD
ZST
ZNA
BIZ
BIZ
B4Z
ZSR
ZMU
ZSB
ZHL
Ref.Nr.
700
120
030
030
030
020
052
052
052
000
000
12
12
08
00
51
34
051
051
051
051
051
000
000 080
000 060
040
051
020 060
14
88
51
76
030 040
020 040
170
12
34
25
81
010
020
030
030
030
030
060
220
210
0612
0616
0512
2316
0412
0400
010
010
020
030
040
100
030
040
0266
0337
0806
0144
020
0620
0600
0640
0424
DIN
M6x12DIN912-6.9
M6x16DIN912-6.9
5h8x12
DIN
7
3/16GK3DIN5401
M4x12DIN551-5.8
M4
DIN
934-5
BM2,5x6DIN7513
3x3.7
DIN
6888
M8x6DIN551-5.8
1,4x4
DIN1476-4.6
M6
M6x20DINgi
M6DIN
934-6
86,4
DIN
125
4x24
DIN
1481
2-6.9
BENENNUNG
Frasschlltteneinheit
Fiihrungsgehause
Querschlitten
Skalenring
Skalenring
Obermutter
Obermutter
Gewindebtichse
Druckstift
Einstelleiste
Zylinderschraube
Zylinderschraube
Zyiinderstift
Stahlkugel
Gevuindestift
Sechskantmutter
Oberspindel
Oberspindel
Obersplndeltrager
Handrad
Aniaufscheibe
Mutter
Bogenfeder
Skalenschild
Skalenschild
Kegelgriff
Firmenschild
Gewindeschneidschraube
Scheibenfeder
Gewlndestift
Kerbnagel
Zustellrad
Zustellrad
Nutenschraube
Zylinderschraube
Sechskantmutter
Schelbe
Spannhijlse
52
metr.
USA
metr.
USA
metr.
USA
metr.
USA
metr.
USA
0,2
mm
DESCRIPTION
Vertical
milling
drilling
device
Guide
housing
Cross
slide
Graduated
Graduated
Lead
Lead
Locking
Adjusting
Gib
Allen
Allen
Dowel
Ball
Set
Hexagon
Lead
Lead
Lead
Handwheel
Compensating
Nut
Feed
Scale
Scale
Handle
Name
Self
Circlip
Set
Rivet
Feed
Feed
T-nut
Allen
Hexagon
Washer
Lock
screw
screw
nut
head
head
pin
screw
nut
screw
screw
screw
spring
mark
mark
plate
tapping
screw
wheel
wheel
screw
head
nut
pin
ring
ring
nut
nut
pin
screw
screw
metr.
USA
mount
metr.
USA
screw
metr.
USA
screw
and
metr.
USA
metr.
USA
washer
DESIGNATION
Ens.
chariot
BoTte
de
guidage
Chariot
transversale
Bague
gradu^e
Bague
graduee
Noix
du
chariot
Noix
du
chariot
Bague
filetee
Boulon
de
pression
Lardon
de
reglage
Vis 6 pans
Vis 6 pans
Tige
Bille
Vis
Ecrou 6 pans
Broche
Broche
Palier
Volant
Rondelle
Ecrou
Ressort
Echelle
Echelle
Levier
Plaque
Vis
Clavette
Vis
Rivet
Volant
Volant
Boulon
Vis 6 pans
Ecrou 6 pans
Rondelle
Goupille
de
serrage
acier
pointeau
metr.
USA
de
broche
de
arque
metr.
USA
spherique
taraud
pointeau
de
fixation
de
de
en
serrage
creux
creux
la
la
T
creux
de
fraisage
metr.
USA
superieur
sup6rieur
de
r^lage
compensation
vis-mere
vis-mere
metr.
USA
metr.
USA
31

15
12
30
33
5
21
20
Spannung
Voltage
Tension
115
115
loo
loo
llo
22o
23o
24o
25o
22o
22o
(V)
Frequenz
Frequency
Frequence
6o
6o
CSA
5o
6o
5o
6o
5o
5o
5o
5o
VDE
5o
SEV
Ref.Nr.
Ref.No.
Ref.Nr.
ZMO
76
ZMO
77
ZMO
75
ZMO
76
ZMO
75
ZMO
76
ZMO
75
ZMO
75
ZMO
75
ZMO
75
ZMO
75
fur
for
pour
1115
1115
lloo
lloo
lllo
1220
1230
1240
1250
1221
1222
Gr.
E-Ausriistung
electr.
ens.
electrique
equipment
compl.
equipement
34
Ref.Nr.
Ref.No.
Ref.Nr.
ZME
2o
ZME
2o
ZME
2o
ZME
2o
ZME
2o
ZME
2o
0073
ZME
2ooo73
ZME
2o
ZME
2o
ZME
2o
0073
ZME
2o
0073
fiir
for
pour
0071
0071
0072
0072
0071
oo73
0074
Kondensator
condenser
condesateur

Pos.
1
2
3
4
5
6
7
8
9
lo
11
12
13
14
15
16
17
18
19
2o
21
22
23
24
25
26
27
28
29
3o
31
32
33
34
35
36-43
36
37
38
39
4o
41
42
43
44-49
44
45
46
47
48
49
A5Z
A5Z
A5Z
A5Z
A5Z
A5Z
A5Z
A5Z
A5Z
A5Z
H8A
A5Z
ZSR
ZSR
ZSR
ZSR
ZSR
ZSR
ZSR
ZMU
ZST
ZSB
ZSB
ZST
ZGF
ZRM
ZFD
A3Y
A3Y
A5Z
ZSB
ZSB
ZRG
ZSR
ZST
A5Z
ZME
A5Z
A5Z
ZLG
ZSB
ZSB
A5Z
ZSB
ZMO
ZME
ZME
ZPG
A5A
A5B
ZME
Ref.
No.
loo
loo
loo
loo
loo
loo
loo
loo
loo
loo
000
loo 15o
12
12
12
12
12
12
33
34
13
21
22
72
19
4o
93
loo
loo
loo
25
25
21
12
11
lol
4oo
lol
lol
6o
lo
lo
loo
12
2o
lo
2oo
2oo
2o
olo
o2o
o3o
o4o
o5o
o6o
o7o
o9o
12o
13o
12o
o5o8
0635
o64o
o82o
0416
0512
0516
o6oo
o6o8
o43o
o53o
o3o6
25o6
5260
15ol
llo
12o
14o
o53o
o84o
ol2o
o61o
o71o
000
loo
o2o
o3o
o2o2
o282
2181
o8o
2210
0036
ooo8
15o
15o
oo3o
DIN
M5x8
DIN
M6x35
DIN
M6x4o
DIN
M8x2o
DIN
M4xl6
DIN
M5xl2
DIN
M5xl6
DIN
M6
DIN
934-6
M6x8
DIN
A4, 3 DIN
B
5,3
DIN
3x6
DIN
C25xM6
TX
DIN
5x260
15x8,2xo.7,DIN2o93
B5,3
DIN
B8,4
DIN
WR12
M6xlo
DIN
6xloo
DIN
6oo2-2Z
SS2ox28x2
SS12xl8xl,2
PS22x32xl
*
*
MZB
13
*
Ref.
* Ref.
* Ref.
912-6.9
912-6.9
912-6.9
912-8.8
912-6.9
912-6.9
933-5.6
913-45H
9o21
9o21
1472-6.8
319
125
125
912-6.9
7
Nr.
siehe
Nr.
see
Nr.
voir
•
Tabelle
table
tableau
Benennung
Vertikale
Bohrvorrichtung
Sockel
K1emmkopf
Pinolenhalter
Vertikalsaule
Ritzel
Knebel
Gradskala
Mo
torn'
Distanzh'tilse
Raderdeckel
Zeiger
Distanzscheibe
Zylinderschraube
Zylinderschraube
Zylinderschraube
Zylinderschraube
Zylinderschraube
Zylinderschraube
Sechskantschraube
Sechskantmutter
Gewindestift
Scheibe
Scheibe
PaBkerbstift.
Kugelknopf
Keilriemen
Tell
Schutzring
FUhrungslasche
Schraube
Scheibe
Scheibe
Sprengring
Zylinderschraube
Zylinderstift
Gruppe
Tragerplatte
Vertikalspindel
Riemenscheibe
Rillenkugellager
Stlitzscheibe
Stlitzscheibe
Druckfeder
PaBscheibe
E-Ausrlistung
Motor
Lufterhaube
Kondensator
Kabelverschraubung
Drehzahlschild
Drehzahlschild
Schalter
35
emensche i be
erfeder
Pinole
mit
Fras-
Gehause
und
5o
6o
Hz
Hz
Description
Vertical
compl.
Pedestal
Headstock
Quill
Vertical
Pinion
attachment
adapter
holder
column
Toggle
Graduated
Motor
scale
pulley
Spacer
Cover
Pointer
Distance
Socket
Socket
Socket
Socket
Socket
Socket
Hexagon
Hexagonal
Set
Washer
Washer
Grooved
Ball
V-belt
Disc
washer
head
head
head
head
head
head
head
nut
screw
adjusting
knob
spring
Protection
Guide
sheet
Screw
Washer
Washer
Retaining
Socket
Dowel
Quill
Carrier
Vertical
ring
head
pin
compl.
plate
spindle
Pulley
Ball
bearing
Supporting
Supporting
Compression
Ring
Drive
unit
Motor
Fan
cover
Condenser
Screw
type
Speed
plate
Speed
plate
Switch
screw
screw
screw
screw
screw
screw
screw
pin
ring
screw
ring
ring
spring
cond.fittg
5o
Hz
6o
Hz
Designation
Ens.
dispositif
Socle
support
Support
Porte
Colonne
vertical
fourreau
verticale
Pignon
Genouillere
Echelle
Poulie
de
moteur
Douille
Couvercle
d'ecartement
Aiguille
Rondelle
Vis 6 pans
Vis 6 pans
Vis 6 pans
Vis 6 pans
Vis b pans
Vis 6 pans
Vis
creux
creux
creux
creux
creux
creux
hexagonale
Ecrou 6 pans
Vis
pointeau
Rondelle
Rondelle
Chevelle
de
position
Sphere
Courroie-V
Ressort
Anneau
Tole
Vis
Rondel
Rondelle
Bague
Vis 6 pans
Tige
Ens.
beleville
de
protection
de
guidage
1e
elastique
creux
de
serrage
Canon
Support
Broche
verticale
Poulie
Roulement a billes
Rondelle
Rondelle
Ressort
Rondelle
Ens.
Moteur
Carter
Condensateur
Raccordement a vis
Plaquette
Plaquette
de
compression
Entrainement
de
ventilateur
de
vitesses
de
vitesses
Interrupteur
vertical
de
poupee
5oHz
5oHz

Pos.
1
2
3
4
5
6
A3Y
A3Y
A3Y
A3Y
ZSR
ZST
Ref.
151
llo
llo
llo
llo
llo
12
o6
No.
oil
o2o
o3o
o4o
o63o
o42o
M6x3o
4m6x2o
DIN
DIN
DIN
912-6.9
7
Benennung
Gr.
Vertikalfeinzu-
stellung
Lagerstock
Zustellschnecke
Zustellritzel
Scheibe
Zylinderschraube
Zylinderstift
Description
Fine
feed
Bearing
Worm
Splined
Washer
Allen
head
Dowel
pin
attachment
block
shaft
screw
Designation
Ens.
rfeglage
Support
Comniande
Pignon
Rondelle
Vis b pans
Vis
de
de
de
t§te
cylindrique
vertical
parlier
r&glage
r&glage
creux
fin
Pos.
1
2
3
2oo
A5Z
A5Z
ZST
Ref.
o5o
oSo
o4o o2o
11
No.
o71o
olo
6xloo
DIN
DIN
Benennung
Spannzangenvorri
Zangenhalter
Spannmutter
7
Zylinderstift
chtung
Description
Collet
holder
Collet
holder
Locking
Dowel
pin
ring
Designation
Porte-pinces
Porte-pinces
Ecrou
de
serrage
Tige
de
serrage
36