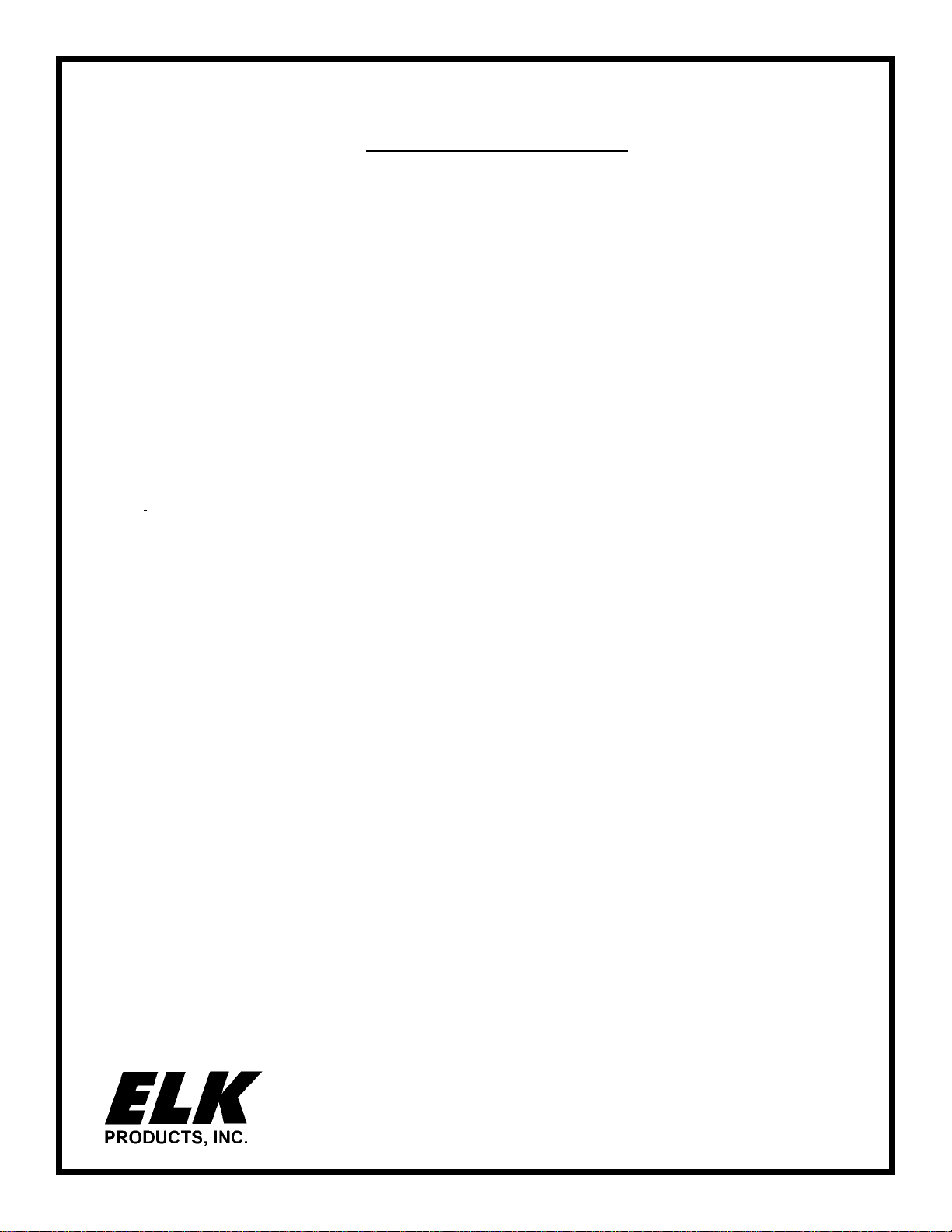
ELK-MM443
Magic Module Automation Controller
Features
• Re-Programmable Logic Controller
• Four (4) supervised inputs with analog or digital sensing.
• Four (4) dry contact SPDT relay outputs.
• Two relay outputs may be jumper programmed for transistor open collector outputs.
• RS-485 four-wire data bus for networking to other Magic Modules, accessories, and personal computer .
• X-10® Power Line Carrier Interface. PL513, PSC04 (Transmit Only), or TW523, PSC05 (Two Way).
• Four (4) Accumulator Counters, range 0 to 255.
• Four (4) Timers, range 1/10 second to over 255 hours.
• 16,384 program bytes using SIMPLE programming language.
• EEProm “non-volatile” memory maintains program in the event of power loss.
• Analog transmissions between MM443’s and Preset Dim Commands.
• Dallas iButton™ TouchKey Reader with optional ELK-MA290 interface.
• Programs the ELK-MM220 (two inputs, two relay outputs module).
• Emulates ELK-MM220 for code development.
• Mounts to single or double gang electrical box.
• Optional DIN Rail Mounting. PCB mounts into 4 inch SnapTrack.
• Lifetime Limited Warranty.
Specifications
• Operating Volt age: 9.5 to 15 V olts D.C., well regulated.
• Nominal Current Draw: ~10mA., 130mA Maximum with all relays active.
• Analog Inputs: (4) rated for 0 to 13.6 volts. Optional 2k ohm End-of-line resistor supervision.
Inputs have selectable pull up or pull down jumper but may be left floating.
Software programmable high/low threshold levels.
• Analog Input impedance (floating input) - 100K ohms.
• Relay outputs: (4) form “C” relays rated for 10 Amp s at 120VAC, 7 Amps at 28VDC.
Relays 3 & 4 may be configured as open collector transistor outputs, 100 ma. Maximum.
• X-10 or Access Control Interface Connector: Telephone style RJ-11 4-wire female connector is com-
patible with PL513 and PSC04 1-way modules, TW523 and PSC05 2-way modules, or with MA290
Access Module.
• Accessory Connector (J1), 5 pin male: For optional MC100 Real Time Clock, MT100 Temperature
Sensor Module, or connection for programming ELK-MM220 modules.
• RS-485 Data Bus: For connection of up to 31 additional data bus devices.
Maximum length: 4000 feet w/22 A WG wire.
• Enclosure: White plastic, 6.5”W x 4.375”H x 2”D.
ELK PRODUCTS, INC.
PO Box 100 • 3266 US Hwy. 70 West
Hildebran, NC 28637 • USA
828-397-4200 • FAX 828-397-4415
http://www.elkproducts.com • Email: info@elkproduct s.com
06/03
Page # 1
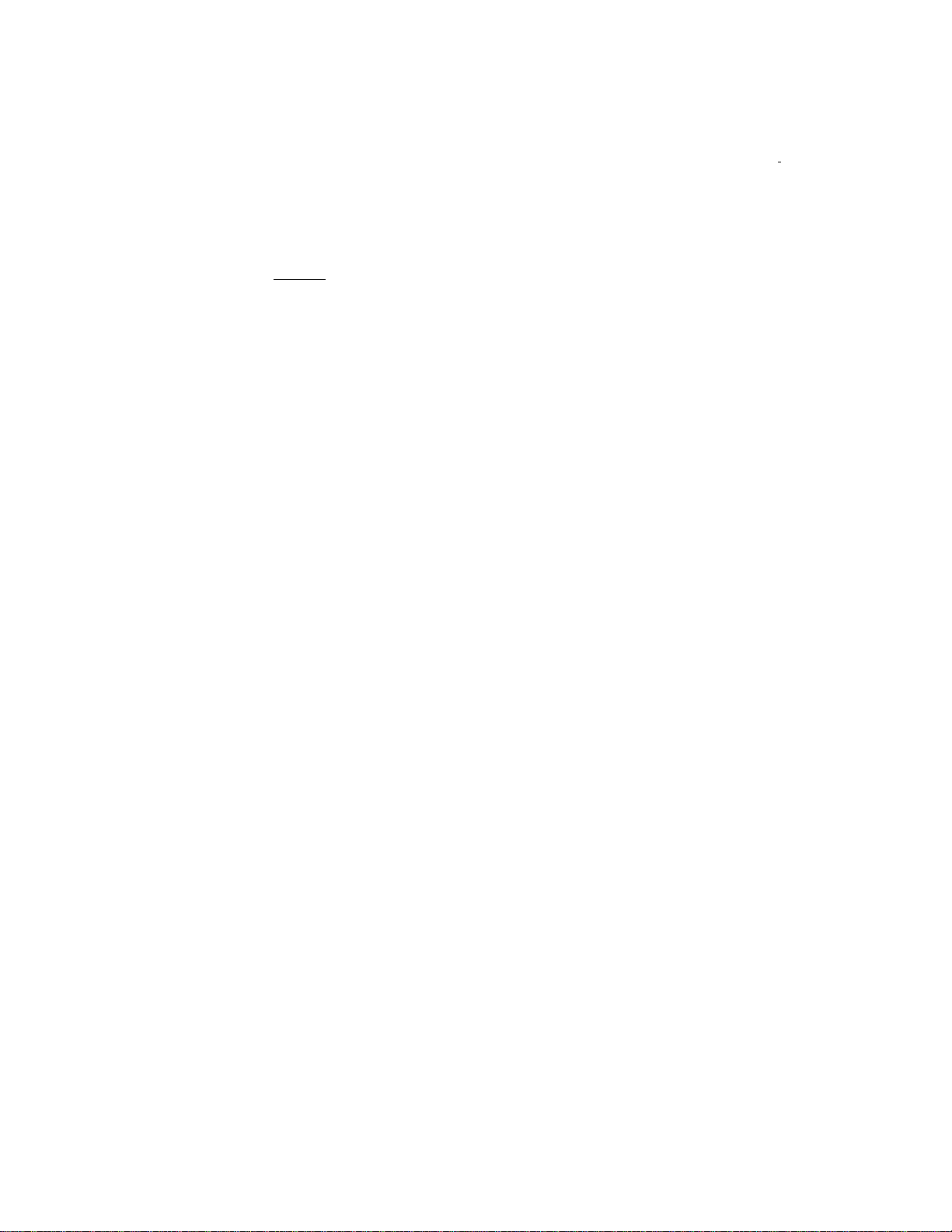
OVERVIEW
The MM443 has virtually no limits and can be used as a stand alone field programmable controller in a vast array of applications
from timers, door controllers, simple process controllers, etc. or as a networked controller with other modules connected on a
common RS-485 data bus. All data bus modules are assigned a device type and up to 31 of each type may interconnected together.
A telephone style RJ-11 connector allows an X-10 Power Line Interface to be added for transmitting and receiving signals across the
AC power line. This same connector can alternately be used with our Access Interface (MA290) for reading Dallas iButton™ ID
devices or Proximity cards for identification and access control applications.
The MM443 uses the same programming software as the MM447 and MV480. The software and peripheral components are available in our Programming Kit (MK485) or Starter Development Kit (MK400). Programming is accomplished by way of a Personal
Computer (windows based) using ELK’s Magic Module Development software. Programs may be written using either the automatic
Code Writer or Application Writer interfaces which construct programs from a visual question list into a lower level Intermediate Code.
The Intermediate Code, known as SIMPLE, is a Basic-like high level language that compiles the Intermediate Code into code byte’s.
The code is then downloaded from the computer to the MM443 over the data bus using the computer’s serial port and a RS-232 to
RS-485 converter (MB485 included in the programming kit). The code is stored in Electrically Erasible Programmable Read Only
Memory(EEProm memory). The microprocessor reads out of EEProm memory and executes the code through a built in operating
system. Once programmed, the MM443 may be disconnected from the data bus or the computer may be turned off. The latest
updates to the ELK Product’s Magic Module Development Software are available at: www.elkproducts.com.
INSTALLATION and HOOKUP
1. Set the RS-485 DATA BUS ADDRESS Jumpers. Each MM443 must be set to its own individual data bus address. There are 5
plug-on DATA BUS ADDRESS Jumpers located along the top of the board. See Figure 1. Each jumper has a position of [0] or [1] and
a binary value (1, 2, 4, 8, 16) which can be read directly above each jumper. The addition of the binary values (sum total) for
jumper(s) set to the [1] position determines the data bus address. For example: Data bus address 5 is set by placing jumpers 1 and
4 in the [1] position (1 + 4 = 5). All five jumpers are required to set the address, none can be missing.
2. Connect the four wires of the RS-485 Data Bus to any remote or additional modules, or to a RS-232 to RS-485 Data Converter
(MB485). For proper operation Data “A” must connect to Data “A” and Data “B” must connect to Data “B” on the other modules. There
are two sets of Data Bus connections:
A. Screw Terminals A & B
B. Four pin header connector J2 - Pin 3 is Data “A” and pin 2 is Data “B”.
3. Connect the Inputs as needed. Four analog or digital inputs with programmable low and high level switching thresholds accepting input voltages directly up to 13.6 volts DC are available at terminals 5 thru 10. Higher voltages can be used by using resistors on
the input as a voltage divider. Each input is jumper programmable for a 2K ohm input resistor pulled to 12VDC, ground, or no resistor
input voltage bias. The input loop response time may be adjusted with the set INxFilter command in 1/10-second increments from
100 milliseconds to 25.5 seconds. See Figure 2 for input configurations.
The Inputs may be used as:
A. Normally Open (Short to ground). Set JP1 thru JP4 jumper (according to the input), to the “1”(+12V) pull up setting.
B. Normally Open (Short to +12VDC). Set JP1 thru JP4 jumper (according to the input), to the “0”(GND) pull down setting.
C. End Of Line Resistor (EOLR) at 2000 ohms with Normally Open contacts across the resistor and/or Normally Closed contacts in
series with the resistor. Set JP1 thru JP4 jumper (according to the input), to the “1”(+12V) pull up setting.
D. Analog Voltage Input (0 to 13.6 VDC). Remove the JP1 thru JP4 jumper (according to the input). Use the if Inx <= value to select
what to do next in the program according to the input voltage level.
4. Connect the Relay Outputs as needed. Four form C relay outputs with contacts rated at up to 10 amps are available at screw
terminals 11 thru 22. Two relay outputs are jumper programmable (JP11 for relay 3 & JP12 for relay 4) to switch the output through an
open collector NPN transistor (100 ma maximum) to the COM terminal instead of through the relay for higher speed applications
such as flashing LED’s where the click of the relay is not desired.
5. Connect an X-10 or Access Interface as needed. To communicate over the AC powerline connect a PL513 or PSC04 X10
module (transmit only), or a TW-523 or PSC05 X10 module (two-way) to connector J5 using a single RJ-11 four wire telephone
cable. Jumper JP10 selects between the one way or two way modules. Alternatively, for Access control applications you may
connect an ELK-290 Proximity/iButton Reader Interface to connector J5. The MM443 supports both Proximity Cards and Dallas
iButtons. Note: X-10 and Prox/Ibutton applications cannot be used simultaneously.
6. Connect Power from a well regulated 12VDC power source using any of four different locations on the printed circuit board.
A. Power Input Jack, J3, (Center Pin is Positive, Barrel is Negative).
B. RS-485 Data Bus Screw terminals 1(+12V) and 4(NEG).
C. RS-485 Data Bus Four pin header connector, J2, Pins 4(+) and 1(-).
D. X-10 and iButton Interface Eight pin telco type connector, J5, Pins 2(+) and 7(-).
7. The Accessory Connector (J1) is used to program ELK-MM220 controller modules and for optional components like the ELKMC100 or ELK-MT100 modules. Note: To program ELK-MM220 moldules, the MC100 or MT100 modules must be temporarily
removed in order to gain access to J1.
Page # 2