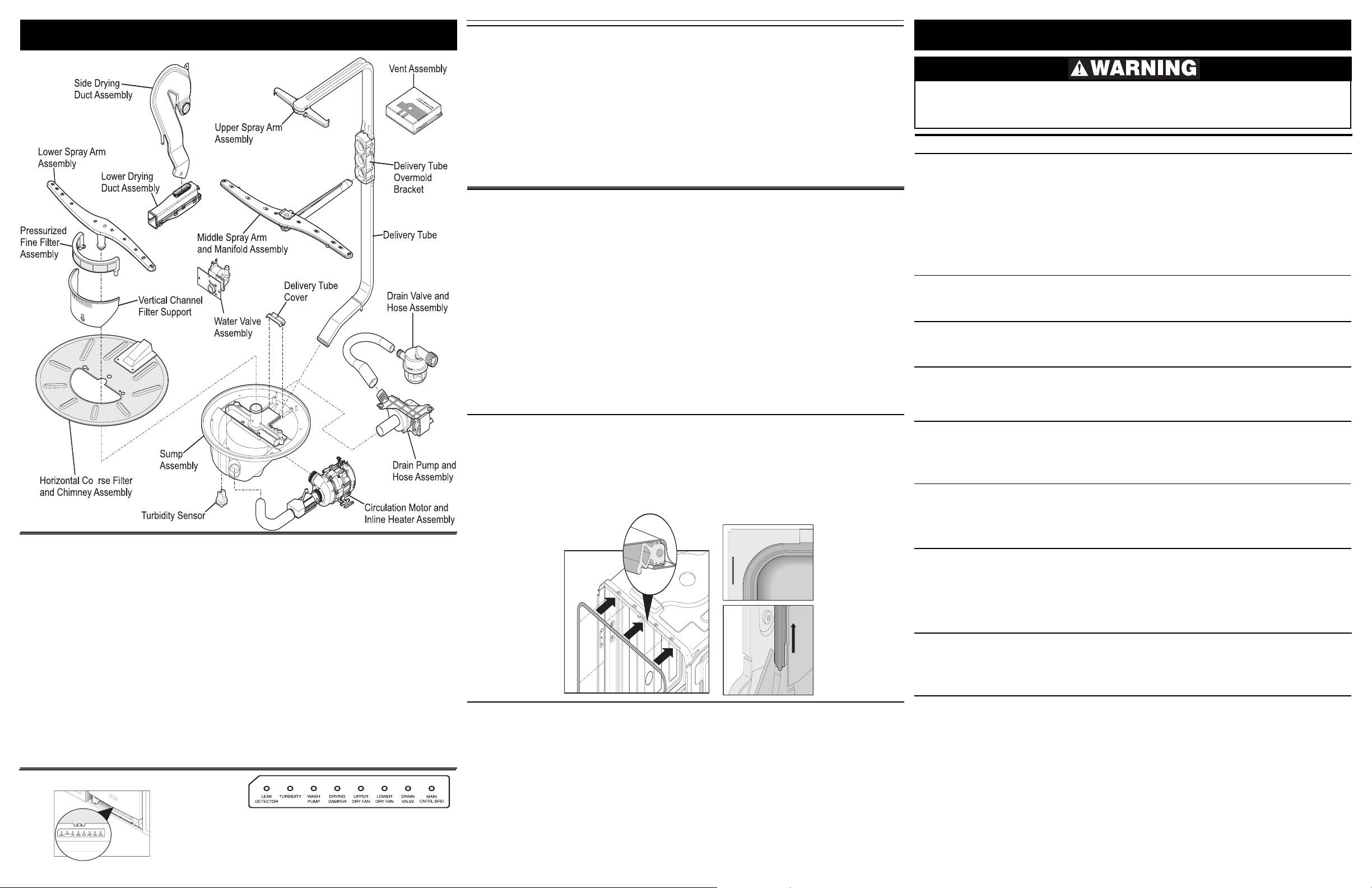
Standard Dry Air Flow
When the control advances to the “dry” portion of
the cycle, the lower fan located in the Lower
Drying Duct Assembly is activated. Then, the
Vent Assembly located in the top right corner of
the tub is activated. The vent fan draws in the air
from outside the tub forcing the hot, humid air out
the Side Drying Duct Assembly and into the
Lower Drying Duct Assembly. Cool dry outside
Detergent and Rinse Aid Dispenser
The detergent and rinse aid dispenser is a one
piece component consisting of a molded
detergent cup and a built-in rinse aid dispenser.
The detergent cup has a spring loaded cover
and the rinse aid dispenser has a removable
cover.
Liquid rinse aid is added to the dispenser up to
the fill line indicator. The amount of rinse aid
released can be adjusted by turning the arrow
indicator from one, being the least amount, to
four, being the greatest amount.
air is mixed with hot, humid air existing the tub
in the Lower Drying Duct Assembly. This lowers
the temperature and humidity of the air exiting
the unit through the toe and kickplate. The
addition of cooler, dryer outside air helps to
speed evaporation of water from the hot dishes.
To replace dispenser:
• shut off electricity to dishwasher,
• remove outer door panel assembly and foam
barrier,
• disconnect wiring to the dispenser,
• remove the six screws and bracket,
• remove the dispenser,
• replace and reinstall in reverse order,
• rewire actuator.
Trouble Shooting TipsExploded View of Wash System
Personal Injury Hazard
Always disconnect the dishwasher from the electrical power source before adjusting or
replacing components.
Symptom
Dishwasher will not operate when
turned on.
Motor hums but will not start or run.
Motor trips out on internal thermal
overload protector.
Check the Following
1. Fuse (blown or tripped).
2. 120 VAC supply wiring connection
faulty.
3. Electronic control board defective.
4. No 12 VAC power to control.
5. Motor (inoperative).
6. Door switch (open contacts).
7. Door latch not making contact with
door switch.
8. Touch pad circuit defective.
9. No indicator lamps illuminate when
START or OPTIONS are pressed.
1. Motor (bad bearings).
2. Motor stuck due to prolonged
non-use.
1. Improper voltage.
2. Motor windings shorted.
3. Glass or foreign items in pump.
Remedy
1. Replace fuse or reset breaker.
2. Repair or replace wire fasteners at
dishwasher junction box.
3. Replace control board.
4. Replace control board.
5. Replace motor/impeller assembly.
6. Replace latch assembly.
7. Replace latch assembly.
8. Replace console assembly.
9. Replace console assembly.
1. Replace motor assembly.
2. Rotate motor impeller.
1. Check voltage.
2. Replace motor/impeller assembly.
3. Clean and clear blockage.
a
Pump Assembly
The pump assembly is driven by a permanent
split capacitor motor. When looking at the output
shaft, rotation is in the counterclockwise direction
at 3300RPM when driven by 120V 60Hz AC
signal. The motor drives a pump which supplies
100% filtered water at the rate of approximately
19 GPM to all three spray arms at once.
Draining is accomplished by using a small
seperate synchronous drain pump mounted to
the sump. The drain pump is connected to the
sump by a small rubber hose and two mounting
points. A check valve is located at the discharge
end of the drain pump.
Component Error LED Indication
The drain valve is connected to the drain pump
by a rubber hose and is mounted to the
dishwasher base. The drain valve maintains
pressure in the pressurized fine filter. The
intermediate drain hose is attached by a worm
gear clamp to the discharge end of the drain
valve.
The drain hose must have a loop at a minimum
height of 32 inches in order to ensure proper
drainage.
The main pump is removed by disconnecting
both attached clamps and hoses, removing the
three screws that secure the motor base to the
dishwasher base, unlatching the leak detector,
and disconnecting the wiring harness
connections to the pump assembly.
To gain access to the Control Housing
Assembly, remove kickplate assembly. LED
indicates which component is the source of
the error.
Tub Gasket
The door gasketl is pressed into the tub channel
for an interference fit. To install the gasket:
1. Locate the center mark on the gasket and
press into place.
2. Press the gasket across the header using
your thumb.
Product Specifications
Electrical
Rating ...................................120 Volts, 60Hz
Separate Circuit..15 amp min.- 20 amp max.
Motor (Amps) ........................................... .75
Heater Wattage .....................................1200
Total Amps (load rated) ........................ 10.0
TempAssure .............................. 140°F ±5°F
(60°C±3°C) [with outer door in place]
TempBoost ............ 145°F ±5°F (63°C ±3°C)
Heated Wash/Heated Rinse
Sanitize .................. 150°F ±5°F (66°C ±3°C)
Hi-Limit Thermostat ............... 200°F (93°C)
3. Press the gasket while stretching around
the corners .
NOTE: There should be no wrinkles or
puckers in the corners.
4. Place the gasket end at the bottom and
then press the gasket in from the bottom up.
Water Supply
Suggested minimum incoming water
temperature ............................ 120°F (49°C)
Pressure (PSI) min./max. .................. 20/120
Connection (NPT) .....................................
Consumption (Normal Cycle) ......................
............ 4.9 - 9.7 U.S. gal., 18.5 - 36.7 liters
Water valve flow rate (U.S. GPM) ............ .83
Water recirculation rate (U.S. GPM) ..............
.................................................... approx. 19
Water fill time ................................... 87 sec.
3
/8"
Dishwasher runs but will not heat.
Detergent cover will not latch or
open.
Dishwasher will not pump out.
Dishwasher will not fill with water.
Dishwasher water siphons out.
Detergent left in dispenser.
1. Heater element (open).
2. Electronic control board defective.
3. Wiring or terminal defective.
4. Hi-Limit thermostat defective.
1. Latch mechanism defective.
2. Electronic control board defective.
3. Wiring or terminal defective.
4. Broken spring(s).
5. Defective actuator.
1. Drain restricted.
2. Electronic control board defective.
3. Defective drain pump.
4. Blocked impeller.
5. Open windings.
6. Wiring or terminal defective.
7. Defective Drain Valve. 7. Repair or replace.
1. Water supply turned off.
2. Defective water inlet fill valve.
3. Check fill valve screen for
obstructions.
4. Defective float switch.
5. Electronic control board defective.
6. Wiring or terminal defective.
7. Float stuck in “UP” position.
1. Drain hose (high) loop too low.
2. Drain line connected to a floor drain
not vented.
3. Drain valve or pump stuck open.
1. Detergent allowed to stand too long in
dispenser.
2. Dispenser wet when detergent was
added.
3. Detergent cover held closed or blocked
by large dishes.
4. Improper incoming water
temperature to properly dissolve
detergent.
5. See "Detergent cover will not open."
6. Spray arm blocked.
7. Is water getting into unit.
1. Replace heater element.
2. Replace control board.
3. Repair or replace.
4. Replace thermostat.
1. Replace dispenser.
2. Replace control board.
3. Repair or replace.
4. Replace dispenser.
5. Replace dispenser.
1. Clear restrictions.
2. Replace control board.
3. Replace pump.
4. Check for blockage, clear.
5. Replace pump assembly.
6. Repair or replace.
1. Turn water supply on.
2. Replace water inlet fill valve.
3. Disassemble and clean screen.
4. Repair or replace.
5. Replace control board.
6. Repair or replace.
7. Clean or replace float.
1. Repair to proper
height
.
2. Install air gap at counter top.
3. Repair or replace.
1. Instruct customer/user.
2. Instruct customer/user.
3. Instruct customer/user on proper
loading of dishes.
4. Incoming water temperature of
120°F is required to properly
dissolve dishwashing detergents.
6. Instruct customer/user.
7. Check fill valve repair or replace.
32-inch minimum
010108