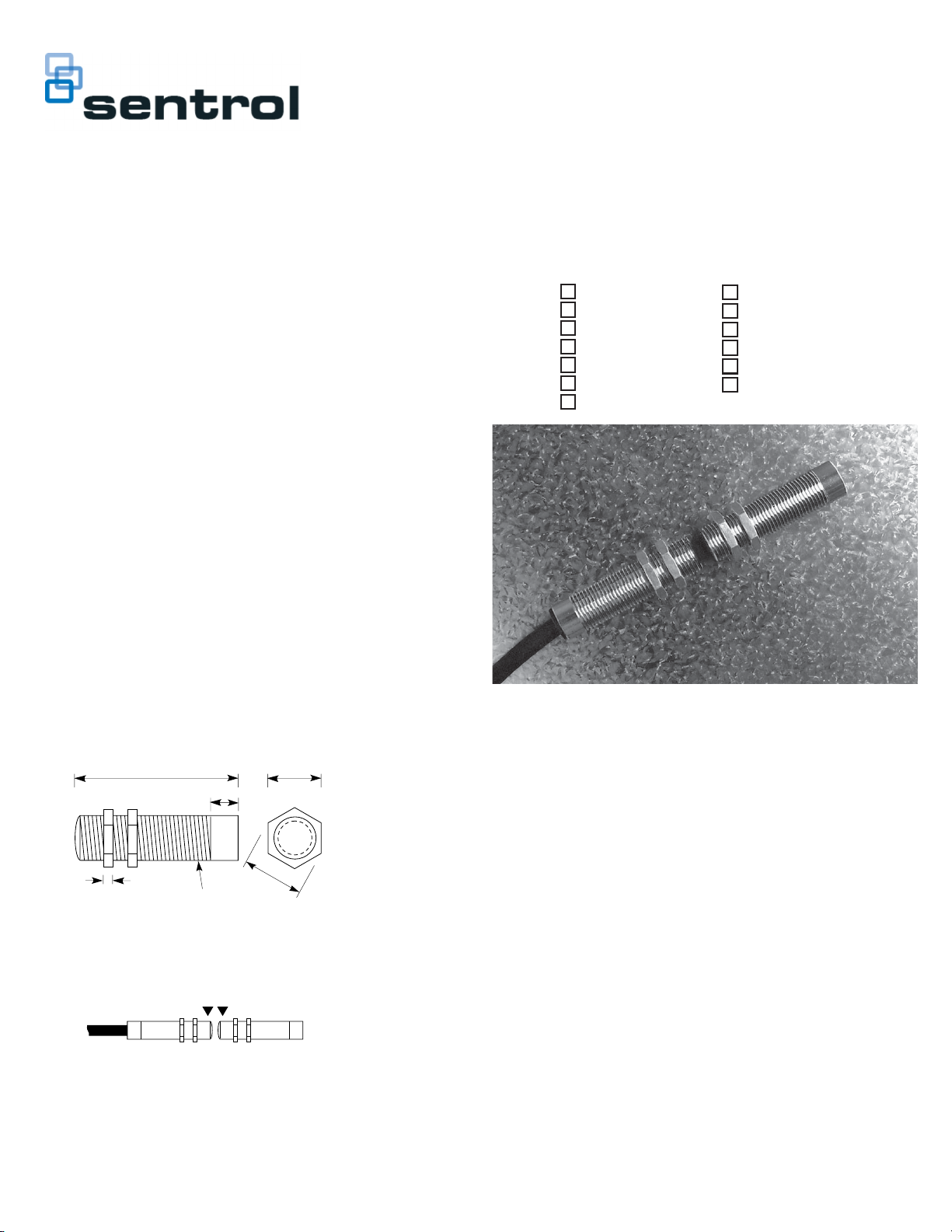
www.edwardssignaling.com
P/N 11503 • REV C1 • REB 21FEB13
Warning! To avoid switch failure determine the actual load of the switch circuit and
take steps to protect the switch from voltage spikes, current inrush and line/load
capacitance using the following recommendations.
• Surges from coils, motors, contactors, solenoids and tungsten filaments. Transient
protection, such as back-to-back zener diodes (Transorb) or an RC network, is
recommended for such loads to ensure that maximum ratings of the switch are
not exceeded.
• Line capacitance and load capacitance. An in-line resistor can be added in series
immediately before the load to limit the inrush current. The resistor can only be
added in series with the last wire just before the load. The voltage drop and the
power rating of the resistor must also be calculated as follows:
Voltage drop = I • R
2
Watts = I
( I = maximum continuous current of the load)
To verify switch operation with an ohmmeter:
Set range at 20 mega ohms (switches with triac output, set ohm range at 20 kilo
ohms). For a normally open switch, the meter will read a high impedance with the
actuator away. It will read very high to infinity range (triac switches will read high kilo
ohm to infinity range) with the actuator within sense range. You will see the opposite
reading for a normally closed switch.
• R
GuardSwitch™ Series 100
Non-Contact Interlock/Position Switch
125-7Y-12K
125-8Y-06K
125-8Y-06K-SER25
125-8Y-12K
125-8Y-12K-SER25
125-__________
125
125-3N-06K
125-3Y-06K
125-4Y-06K
125-4Y-12K
125-6Y-06K
125-6Y-12K
125-7Y-06K
Dimensions
2.49"
6.32cm
0.13"
0.33cm
Figure 1
Switch
0.42"
1.07cm
0.63" x 18NC
sensing faces
0.72"
1.83cm
0.83"
2.11cm
Actuator
Installation
1. Using the following guidelines, determine a suitable mounting location:
• The switch and actuator must be within the listed sense range. See Ordering/
Electrical Specifications.
• The actuator must be aligned with the switch—labels facing the same direction.
(See Figure 1.)
Important: When mounting in proximity to ferrous material (steel), the sense
range can be reduced 50% minimum depending on the shape and type of
material. Test the switch in specific applications to determine the actual
sense range.
• When mounting on a ferrous material (steel), a 1/4" nonferrous (plastic or
aluminum) spacer may be used around the actuator and switch to restore most
of the lost gap.
• When mounting on a hinged gate or door, mount the switch and actuator at least
6" away from the hinges to achieve the maximum movement.
• The switch and actuator must move in one of the approved directions.
See Figure 2.
• Do not mount for parallel actuation. An on-off-on signal may result when the
actuator passes by the switch.
2. Mount the switch on the stationary frame of the machine and connect the electrical
wiring. When mounting the switch on an ungrounded machine, connect the ground
lead to one of the mounting screws.
3. Mount the actuator on the movable guard, door, or gate.
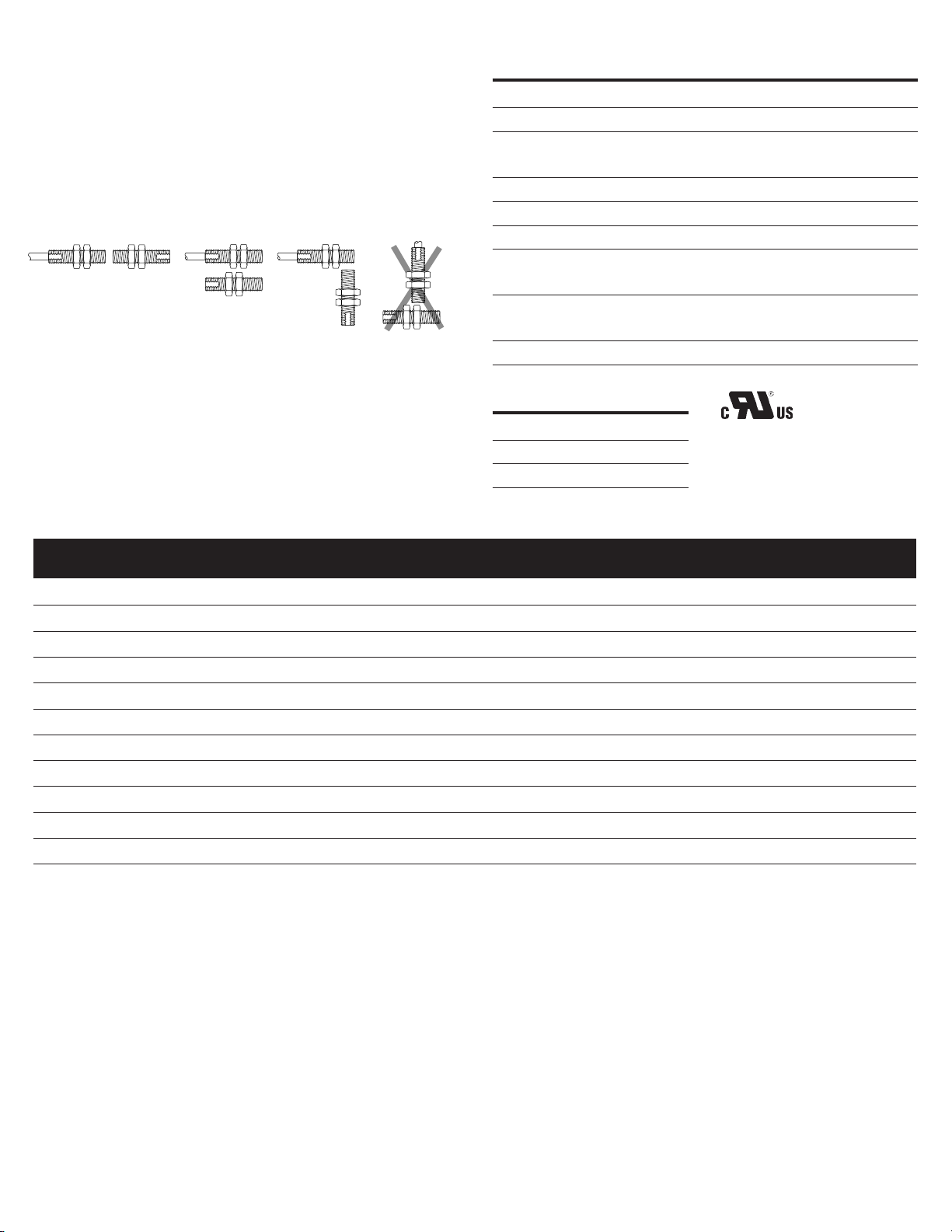
4. Slightly over-drill holes for easy insertion. The switch and actuator should easily
slide or screw into the predrilled holes – DO NOT force or hammer. This may
damage switch.
The interlock switch and actuator magnet should be mounted in only three
configurations for actuation:
Figure 2
Barrel Switch Mounting Configurations
End-to-End Side-by-Side
OK OK NO
Perpendicular
OK
“T”
Three configurations are appropriate for recessed interlock applications. Moving the
actuator parallel to the switch can result in on/off/on signal if the actuator passes by
the switch rather than coming to rest in proximity to it. This is NOT a recommended
configuration for interlock/position applications. The "T" configuration results in
non-actuation.
General Specifications
Enclosure Nickel-plated Aluminum
Temperature Range -40°F to 180°F (-40°C to 80°C)
Environmental Hermetically Sealed Contact Switch
Sealed in Polyurethane
NEMA Rating 1, 2, 3, 4, 4X, 5, 6, 12
Protection Class IP 67
Response Time 1 msec; (150VA)
Life Cycles 100,000 Under Full Load;
Up to 200,000,000 Under Dry Circuit
Lead Type 18/2 SJTOW (K)/0.30" (0.76cm)
18/3 SJTOW (K)/0.33" (0.84cm)
UL All Models
Wire Color Code
Black COM
White N.O.
Red N.C.
File E 122942
Ordering/Electrical Specifications
PART NUMBER CONTACT
125-3N-06K N.C. 100VA/84W 120V@0.8A 28V@3.0A33.0A3@34V 3.0A3@28V 1.0 Ohms Switch Only Switch Only 6'(1.8m)
125-3Y-06K N.C. 100VA/84W 120V@0.8A 28V@3.0A33.0A3@34V 3.0A3@28V 1.0 Ohms 0.5"(1.3cm) 0.9"(2.3cm) 6'(1.8m)
125-4Y-06K SPDT 100VA/84W 120V@0.8A 28V@3.0A33.0A3@34V 3.0A3@28V 1.0 Ohms 0.5"(1.3cm) 0.9"(2.3cm) 6'(1.8m)
125-4Y-12K SPDT 100VA/84W 120V@0.8A 28V@3.0A33.0A3@34V 3.0A3@28V 1.0 Ohms 0.5"(1.3cm) 0.9"(2.3cm) 12'(3.6m)
125-6Y-06K N.O. 25VA/25W 120V@0.2A 120V@0.2A 0.7A@35V 1.0A@25V 0.2 Ohms 0.6"(1.5cm) 1.4"(3.6cm) 6'(1.8m)
125-6Y-12K N.O. 25VA/25W 120V@0.2A 120V@0.2A 0.7A@35V 1.0A@25V 0.2 Ohms 0.6"(1.5cm) 1.4"(3.6cm) 12'(3.6m)
125-7Y-06K N.O. 100VA/84W 120V@0.8A 28V@3.0A33.0A3@34V 3.0A3@28V 1.0 Ohms 0.5"(1.3cm) 0.9"(2.3cm) 6'(1.8m)
125-7Y-12K N.O. 100VA/84W 120V@0.8A 28V@3.0A33.0A3@34V 3.0A3@28V 1.0 Ohms 0.5"(1.3cm) 0.9"(2.3cm) 12'(3.6m)
125-8Y-06K-SER255N.O./ 150VA/NA 120V@1.25A NA 1.25A@120V4NA NA 1.0"(2.5cm) 1.3"(3.3cm) 6'(1.8m)
125-8Y-12K-SER255N.O./ 150VA/NA 120V@1.25A NA 1.25A@120V4NA NA 1.0"(2.5cm) 1.5"(3.3cm) 12'(3.6m)
125-Y Actuator Only Included with all switches unless otherwise noted.
Warning— Each electrical rating is an individual maximum and cannot be exceeded!
1
Configuration with actuator away from the switch
2
Proximity of ferrous materials usually reduces sense range — typically by 50%. The shape and type of material cause a wide diversity of effects.
Testing is required to determine actual sense range for specific applications.
3
Rated at 3.0A for 6,000 cycles only. Other ratings are at 100,000 cycles.
4
Can withstand inrush surge up to 4 amps. Voltage Drop 1.5V. Minimum switch current 30mA.
5
Maximum 10 switches in series; SER25 – Maximum 25 switches in series.
1
LOAD RATING SWITCHING VOLTAGE SWITCHING CURRENT CONTACT SENSE RANGE2BREAK RANGE LEAD LENGTH
CONFIG. AC/DC MAXIMUM, AC/DC MAXIMUM, AC/DC RESISTANCE NOMINAL NOMINAL NOMINAL
triac
output
triac
output