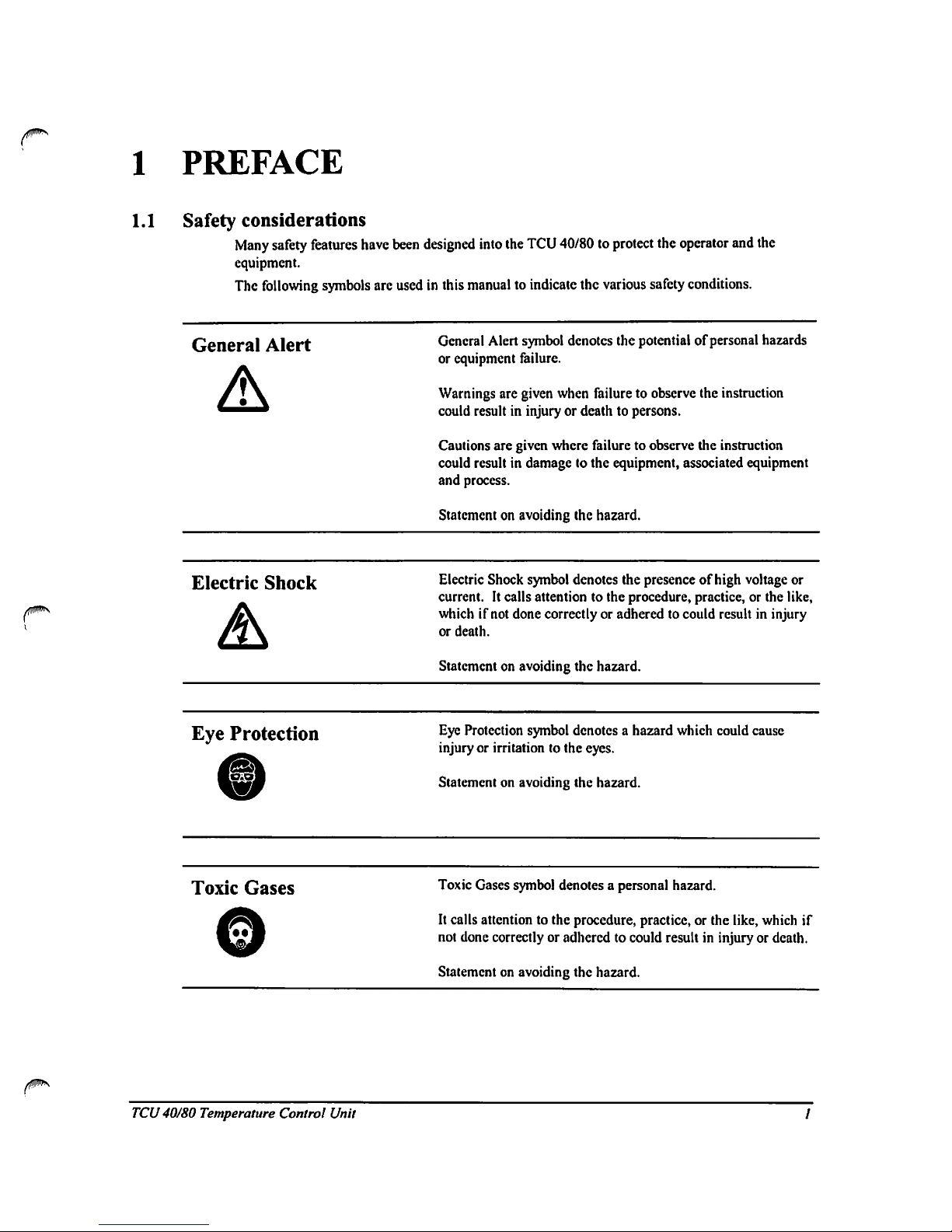
1
PREFACE
1.1
Safety
considerations
Many
safety features
have
been
designed
into
the
TCU
40/80toprotect
the
operator
and
the
equipment.
The
following
symbols
are
usedinthis
manualtoindicate
the
various
safety
conditions.
General
Alert
General
Alert
symbol
denotes
the
potential
of
personal
hazards
or
equipment
failure.
Warnings
are
given
when
failuretoobserve
the
instruction
could
resultininjuryordeathtopersons.
Cautions
are
given
where
failuretoobserve
the
instruction
could
resultindamagetothe
equipment,
associated
equipment
and
process.
Statementonavoiding
the
hazard.
Electric
Shock
Electric
Shock
symbol
denotes
the
presenceofhigh
voltage
or
current.Itcalls
attentiontothe
procedure,
practice,orthe
like,
whichifnot
done
correctlyoradheredtocould
resultininjury
or
death.
Statementonavoiding
the
hazard.
Eye
Protection
Eye
Protection
symbol
denotesahazard
which
could
cause
injuryorirritation
to
the
eyes.
Statementonavoiding
the
hazard.
Toxic
Gases
Toxic
Gases
symbol
denotesapersonal
hazard.
It
calls
attentiontothe
procedure,
practice,orthe
like,
which
if
not
done
correctly
or
adheredtocould
resultininjury or death.
Statementonavoiding
the
hazard.
TCU
40/80
Temperature
Control
Unit
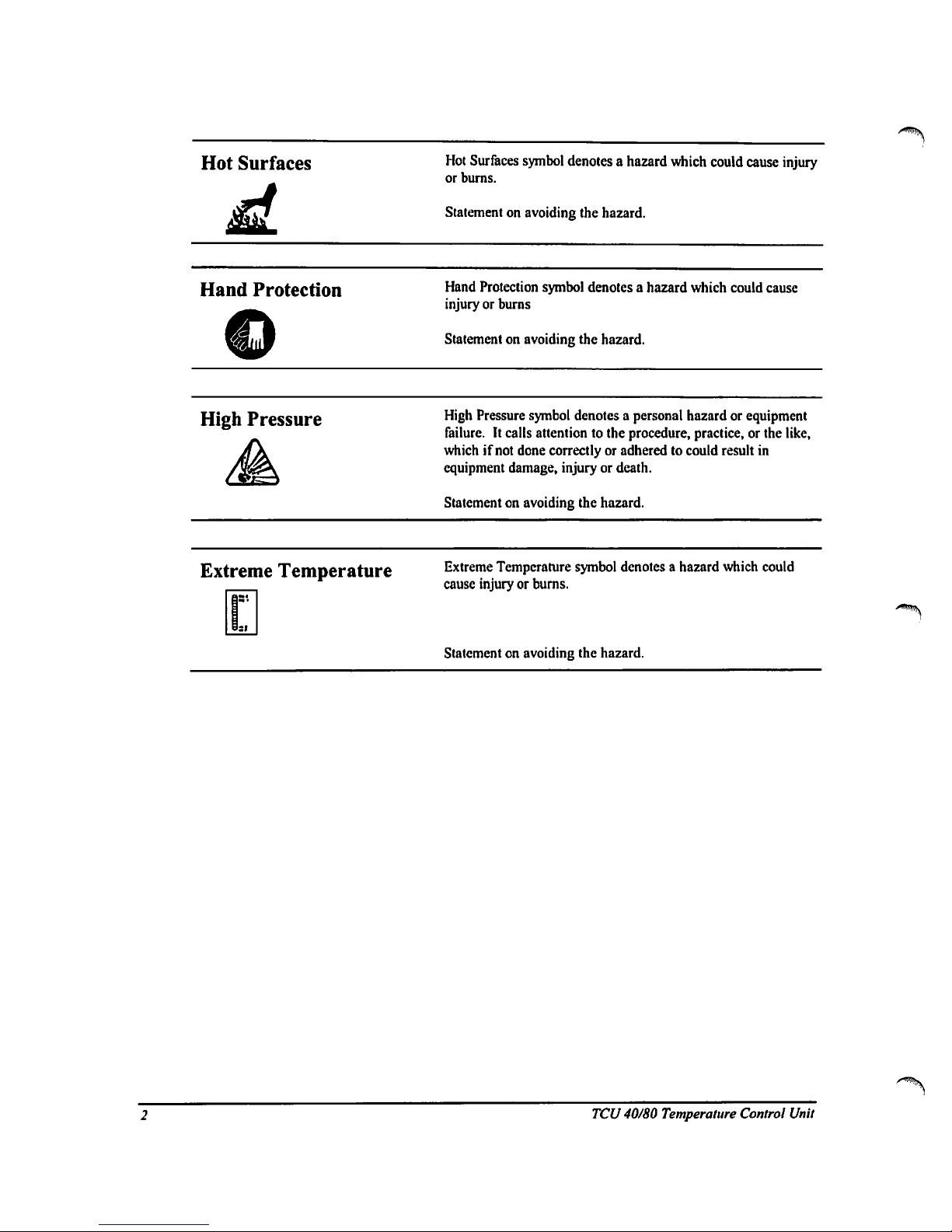
Hot
Surfaces
Hot
Surfaces
symbol
denotes a
hazard
which
could
cause
injury
or burns.
Statementonavoiding
the
hazard.
Hand
Protection
Hand
Protection
symbol
denotes a
hazard
which
could
cause
injuryorburns
Statementonavoiding
the
hazard.
High
Pressure
High
Pressure
symbol
denotesapersonal
hazardorequipment
failure.
It
calls
attention
to
the
procedure,
practice,
or
the
like,
whichifnot
done
correctlyoradheredtocould
result
in
equipment
damage,
injury
or death.
Statementonavoiding
the
hazard.
Extreme
Temperature
Extreme
Temperature
symbol
denotesahazard
which
could
cause
injuryorburns.
Statementonavoiding
the
hazard.
^
TCU
40/80
Temperature
Control
Unit
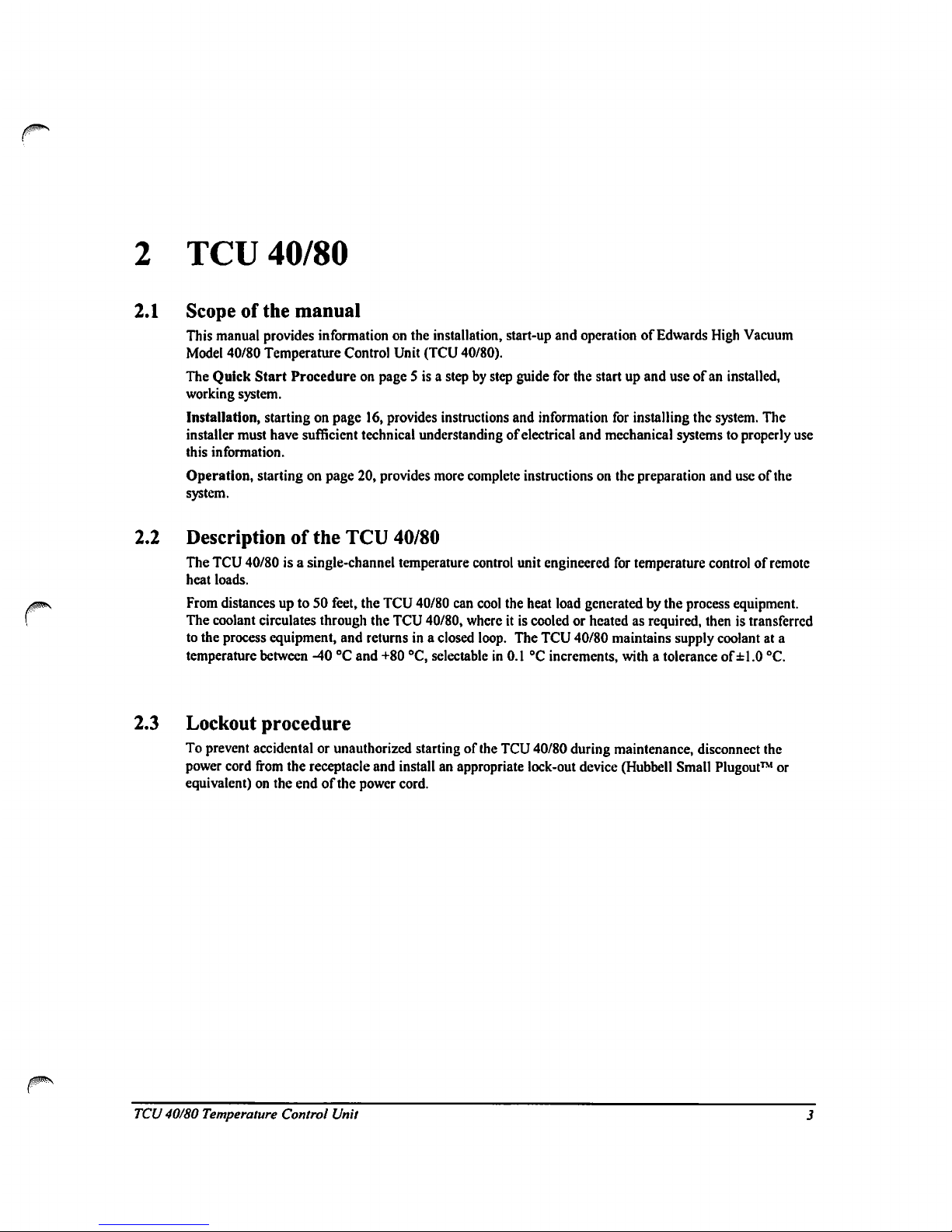
2
TCU
40/80
2.1
Scopeofthe
manual
This
manual
provides
informationonthe
installation,
start-up
and
operationofEdwards
High
Vacuum
Model
40/80
Temperature
Control
Unit
(TCU
40/80).
The
Quick
Start
Procedureonpage5isastepbystep
guide
for
the
startupand
use
of an
installed,
working
system.
Installation,
startingonpage
16,
provides
instructions
and
information
for
installing
the
system.
The
installer
must
have
sufficient
technical
understanding
of
electrical
and
mechanical
systemstoproperly
use
this
information.
Operation,
starting
on page
20,
provides
more
complete
instructions
on
the
preparation
and
useofthe
system.
2.2
Description
of
the
TCU
40/80
The
TCU
40/80isa
single-channel
temperature
control
unit
engineered
for
temperature
controlofremote
heat
loads.
From
distancesuptoSOfeet,
the
TCU
40/80
can
cool
the
heat
load
generatedbythe
process
equipment.
The
coolant
circulates
through
the
TCU
40/80,
whereitis
cooledorheatedasrequired,
thenistransferred
to
the
process
equipment,
and
returnsina closed
loop.
The
TCU
40/80
maintains
supply
coolantata
temperature
between
-40°Cand
+80
°C,
selectable
in
0.1°Cincrements,
withatoleranceof±1.0
°C.
2.3
Lockout
procedure
To
prevent
accidental
or
unauthorized
startingofthe
TCU
40/80
during
maintenance,
disconnect
the
power
cord
from
the
receptacle
and
installanappropriate
lock-out
device
(Hubbell
Small
Plugoutâ„¢
or
equivalent)
on
the
endofthe
power
cord.
0
TCU
40/80
Temperature
Control
Unit
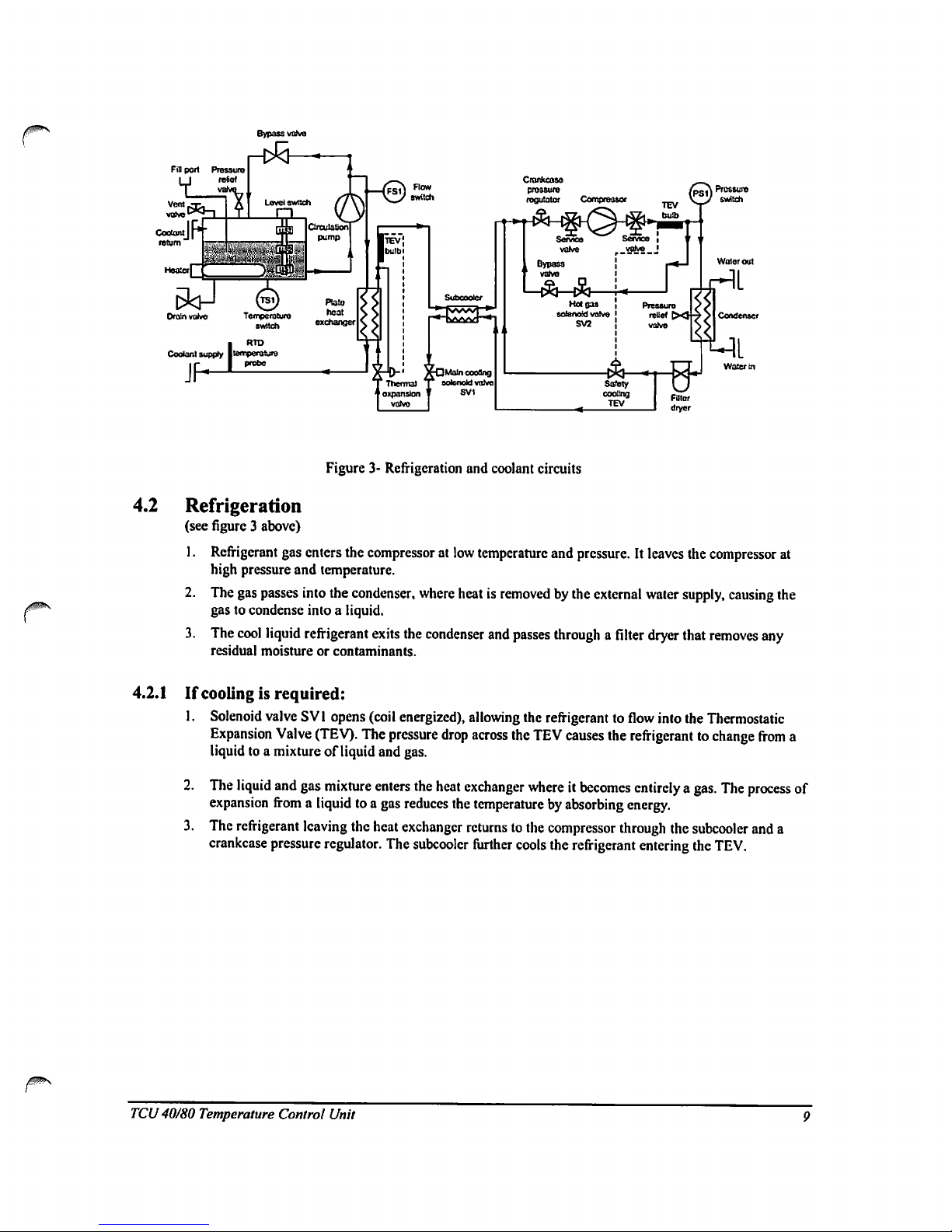
/
Bypass
vaSn
Oran
valve
I
RID
temperature
probe
Profisure
Gwlttfc
Figure3-Refrigeration
and
coolant
circuits
4.2
Refrigeration
(see
figure3above)
1.
Refrigerant
gas
enters
the
compressor
at
low
temperature
and
pressure.
It
leaves the
compressor
at
high
pressure
and
temperature.
2.
The
gas
passes
into
the
condenser,
where
heatisremovedbythe
external
water
supply,
causing
the
gastocondense
intoaliquid.
3.
The
cool
liquid
refrigerant
exits
the
condenser
and
passes
throughafilter
dryer
that
removes
any
residual
moistureorcontaminants.
4.2.1Ifcoolingisrequired:
1.
Solenoid
valve
SV1
opens
(coil
energized),
allowing
the
refrigerant
to
flow
into
the
Thermostatic
Expansion
Valve
(TEV).
The
pressure
drop
across
the
TEV
causes
the
refrigerant
to
change
from
a
liquidtoa
mixtureofliquid
and
gas.
2.
The
liquid
and
gas
mixture
enters
the
heat
exchanger
whereitbecomes
entirely
a
gas.
The
process
of
expansion
fromaliquidtoa
gas
reduces
the
temperature
by
absorbing
energy.
3.
The
refrigerant
leaving
the
heat
exchanger
returnstothe
compressor
through
the
subcooler
and
a
crankcase
pressure
regulator.
The
subcoolcr
further
cools
the
refrigerant
entering
the
TEV.
TCU
40/80
Temperature
Control
Unit
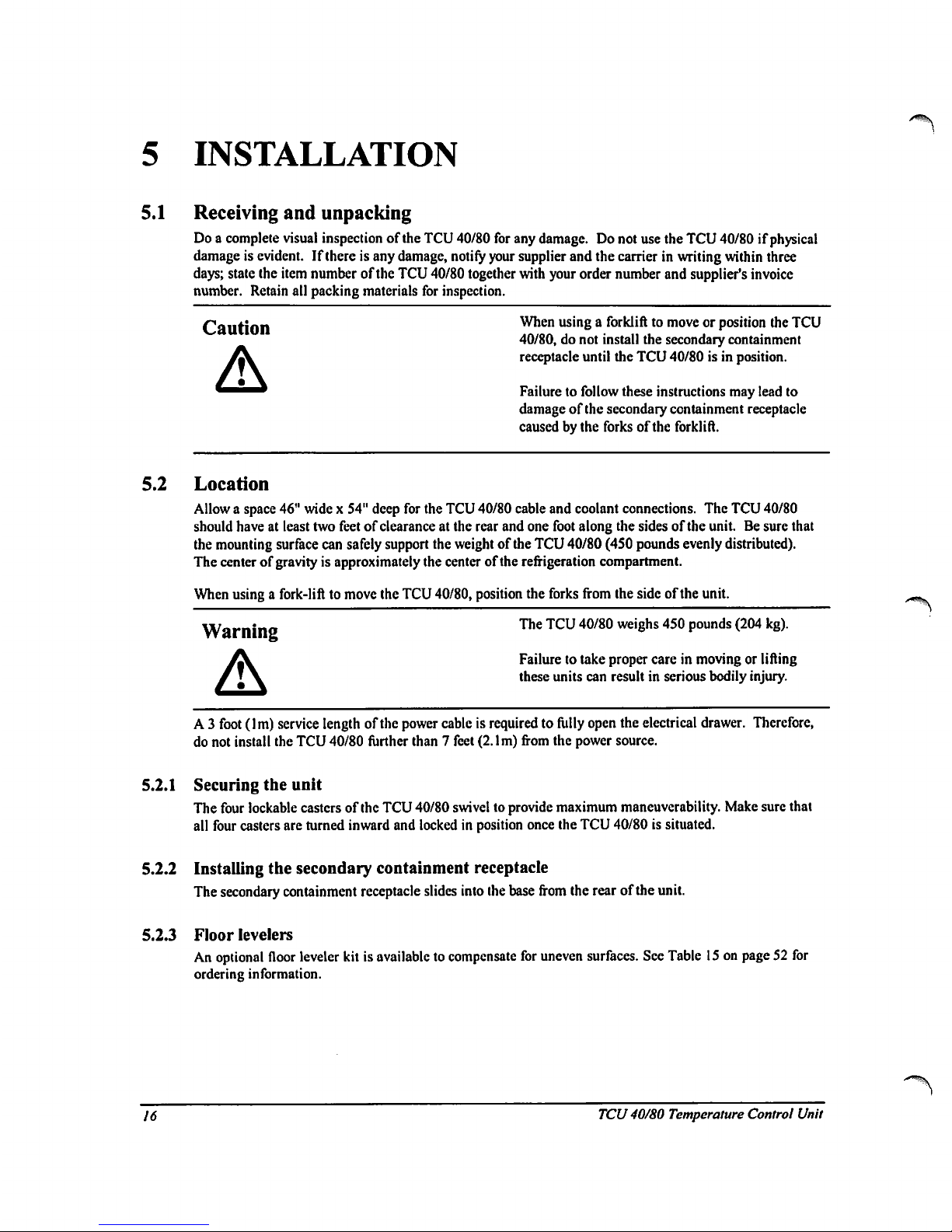
5
INSTALLATION
5.1
Receiving
and
unpacking
Doacomplete
visual
inspection
of
the
TCU
40/80
for
any
damage.Donot
use
the
TCU
40/80ifphysical
damageisevident.Ifthereisany
damage,
notify
your
supplier
and
the
carrierinwriting
within
three
days;
state
the
item
numberofthe
TCU
40/80
together
with
your
order
number
and
supplier's
invoice
number.
Retain
all
packing
materials
for
inspection.
Caution
When
usingaforklift
to
moveorposition
the
TCU
40/80,donot
install
the
secondary
containment
receptacle
until
the
TCU
40/80isin
position.
Failuretofollow
these
instructions
may
lead
to
damageofthe
secondary
containment
receptacle
causedbythe
forksofthe
forklift.
5.2
Location
Allowaspace
46"
widex54"
deep
for
the
TCU
40/80
cable
and
coolant
connections.
The
TCU
40/80
should
haveatleast
two
feetofclearance
at
the
rear
and
one
foot
along
the
sidesofthe
unit.Besure
that
the
mounting
surface
can
safely
support
the
weightofthe
TCU
40/80
(450
pounds
evenly
distributed).
The
centerofgravityisapproximately
the
centerofthe
refrigeration
compartment.
When
usingafork-lift
to
move
the
TCU
40/80,
position
the
forks
from
the
sideofthe
unit.
The
TCU
40/80
weighs
450
pounds
(204
kg).
Failuretotake
proper
careinmovingorlifting
these
units
can
resultinserious
bodily
injury.
A3foot
(1m)
service
lengthofthe
power
cableisrequiredtofully
open
the
electrical
drawer.
Therefore,
do
not
install
the
TCU
40/80
further
than7feet
(2.1m)from
the
power
source.
5.2.1
Securing
the
unit
The
four
lockable
castersofthe
TCU
40/80
swiveltoprovide
maximum
maneuverability.
Make
sure
that
all
four
casters
are
turned
inward
and
lockedinposition
once
Ihe
TCU
40/80issituated.
5.2.2
Installing
the
secondary
containment
receptacle
The
secondary
containment
receptacle
slides
into
the
base
from
the
rearofthe
unit.
5.2.3
Floor
levelers
An
optional
floor
leveler
kitisavailable
to
compensate
for
uneven
surfaces.
See
Table15on
page52for
ordering
information.
16
TCU
40/80
Temperature
Control
Unit

6.5
Remote
set-point
To
use
the
remote
set-point,
wire
the
J72J2
mating
connectorasillustrated
on
page
56.
24vac
mustbeappliedtopins3and
4.
The
AUX
LEDonthe
temperature
controller
will
illuminate
indicating
remote
setpoint
enable
mode
as
soonasthe
mating
connectorisinstalled.
6.6
Flow
rate
adjustment
Caution
Do
not
exceed
coolant
pressureof100
psi.
Exceeding
the
coolant
pressure
may
resultindamage
to
the
pump.
The
Fluorinert
flow
rateofthe
TCU
40/80isfactory
settoprovide
approximately
3
gpmat60
psig/20°C
foraunit
operatingat208vac/3-ph/60Hz.
If
the
flow
rate
requires
adjustmenttoaccommodate
the
process
equipment
suppliers
recommendations,
follow
the
steps
below.
The
flow
rate
maybemeasured
usingaflow
meter
externaltothe
TCU
40/80.
1.
Open
the
left
side
access
door.
2.
Peel
back
the
insulation
covering
the
by-pass
valve.
RefertoFigure1on
page
6.
3.
The
valve
handle
canbefoundinthe
plastic
bag
securedtothe
pump.
Reduce
the
flowbyturning
the
valve
stem
clockwise.Toincrease
the
flow,
turn
the
stem
counter
clockwise.
The
valveisa
1/4
turn
valve.
4.
Once
the
required
flow
rate
has
been
achieved,
return
the
valve
handletothe
bag
for
future
use,
glue
the
insulation
backinplace,
and
secure
the
access
door.
22
TCU40/80
Temperature
Control
Unit

7
MAINTENANCE
This
section
contains
information
that
will
allow
youtosafely
keep
your
TCU
40/80inworking
order.
It
contains
important
Hazard
Warnings,aPreventive
Maintenance
Scheduleonpage
27,
and
a
Troubleshooting
Guideonpage
41.
Maintenance
to
the
electrical
systemofthe
TCU40/80
shouldbeperformedbyqualified
personnel
only.
Warning
The
refrigeration
units
are
scaled
and
are
not
user
serviceable.
Only
trained
and
licensed
refrigeration
personnel
should
perform
repairs
on
this
equipment.
All
applicable
EPA
regulations
apply.
7.1
Hazard
warnings
High
Pressure
Water and
the
coolant
arc
pressurized
within
this
equipment.
Water
pressure
will
depend
upon
utility
supply,
but
usuallyisupto60
psig.
The
coolant
canbeat
pressuresupto
100
psig.
Refrigerant
pressures
canbeupto300
psig.
Do
not
open
lines
with
pressure
present.
Toxic
Gases
The
coolant
breaks
down
above
215
°C.Ifthe
coolantisallowedtoreach
these
temperatures,
toxic
gasses
maybedischarged
from
the
unit.
Refertothe
Appendix
for
Material
Safety
Data
Sheets
for
the
coolant
and
refrigerant
usedinthis
system.
High
Pressure
The
reservoir
may
become
pressurized
due
to
changesintemperature.
Undernocircumstances
should
the
reservoir
pressure
relief
valveberemovedorcapped
off.
TCU
40/80
Temperature
Control
Unit
23

High
Pressure
The
refrigerant
lines
areathigh
pressure.
Undernocircumstances
should
the
refrigerant
pressure
relief
valveberemovedorcapped
off.
Eye
Protection
Hand
Protection
Leakageorfailureofhigh
pressure
circuits
may
cause
injuryorirritation
of
the
eyes.
Eye
protection
shouldbeworn
when
working
with
fluid
systems.
Hotorcold
fluids
and
surfaces
can
cause
injury or
irritation
of
the
hands.
Hand
protection
shouldbeworn
when
working
with
these
fluid
systems.
Electric
Shock
Ensure
that
all
electrical
power
has
been
removed
and
the
main
circuit
breaker
has
been
turned
off
priortoopening
the
electrical
drawer.
The
EMERGENCY
OFF
circuit
(EMO)
does
not
disconnect
all
power
from
the
electrical
drawer.
Extreme
caution
mustbeobservedifperforming
maintenance
operations
with
the
drawer
open.
Hot
Surface
Refrigeration
and
circulating
fluid lines
can
attain
temperatures
as
highas110
°C.
Caution
mustbeobserved.
24
TCU
40/80
Temperature
Control
Unit

7.5
Temperature
probe
calibration
The
Edwards
Temperature
Controller
comes
equipped
withafactory
calibrated
internal
+10V
remote
input/output
option
making
calibration
unnecessary.
7.6
Preventive
maintenance
schedule
Table10shows
the
maintenance
requiredtokeep
the
TCU
40/80ingood
working
order.
Failuretofollow
this
schedule
may
resultindegradationofsystem
performance.
Table10-
Preventive
maintenance
schedule
Frequency
Semi
annual
ly
Annually
Operation
Verify
system
status
Check
coolant
level
Check
lamps
Coolant
leak
check
Refrigeration
leak
check
Insulation
repair
Water
leak
check
Replace
solenoid
coils
SV1
and
SV2
System
check
Lamp
replacement
Hazard
(Type
3)
(Type
3)
(Type
3)
(Type
3)
(Type
3)
(Type
3)
(Type
3)
(Type
3)
Note:
All
maintenance
should be
recordedonthe
Preventative
Maintenance
Record
label
locatedonthe
insideofthe
left-hand
side
access
panel.
TCU
40/80
Temperature
Control
Unit
27

ReturnofEdwards
Equipment-Procedure
(Form
HS1)
i^"ft\
Introduction
Before
you
return
your
equipment
you
must
warn
your
supplierifthe
substances
you
used
(and
produced)inthe
equipment
canbedangerous.
You
mustdothistocomply
with
health
and
safetyatwork
laws.
You
must
complete
the
Declaration
(HS2)onthe
next
page
and
sentitto
your
supplier
before
you
dispatch
the
equipment.Ifyoudonot,
your
supplier
will
assume
that
the
equipmentisdangerous
andhewill
refuse
to
accept
it.Ifthe
Declaration
is
not
completed
correctly,
there
maybea
delayinprocessing
your
equipment.
Guidelines
Take
noteofthe
following
guidelines:
•
Your
equipmentis'uncontaminatcd'
ifithas
not
been usedorifithas
only
been
used
with
substances
that
are
not
dangerous.
Your
equipmentis'contaminated'
ifithas
been
used
with
any
dangerous
substances.
•Ifyour
equipment
has
been
used
with
radioactive substances,
you
must
decontaminate
it
before
you
returnitto
your
supplier.
You
must
send
independent
proofofdecontamination
(for
exampleacertificate
of
analysis)
to
your
supplier
with
the
Declaration
(HS2).
Phone
your
supplier
for
advice.
•
We
recommend
that
contaminated
equipmentistransported
in
vehicles
where
the
driver
does
not
share
the
same
air
spaceasthe
equipment.
PROCEDURE
Use
the
following
procedure:
1.
Contact
your
supplier
and
obtainaReturn
Authorization
Number
for
your
equipment.
2.
Turntothe
next
page(s),
photocopy
and
then
complete
the
Declaration
(HS2).
3.
Drain
all
fluids
from
the
equipment
and
its
accessories.
4.
Disconnect
all
accessories,
suchaslevelers
and
host
connectors,
from
the
equipment.
5.
Close
the
drain,
supply
and
return
valves.
6.
Ensure
that
the
electrical
drawer
and
all
access
doors
are
fastened
securely.
7.
Coil
the
main
power
cord
and
secure.
8.
Wrap
the
TCUinbubble,
polythene,
or
shrink
wrap
and
encloseinthe
originalorreplacement
shipping
crate
(Edwards
part
number
P90150100).
9.Ifthe
equipment
is
contaminated,
label
the
pallet
(or
box)inaccordance
with
laws
covering
the
transport
of
dangerous
substances.
10.
Faxorpostacopyofthe
Declaration
(HS2)toyour
supplier.
The
Declaration
must
arrive
before the
equipment.
11.
Giveacopyofthe
Declaration
to
the
carrier.
You
must
tell
the
carrierifthe
equipmentiscontaminated.
12.
Seal
the
original
Declaration
inasuitable
envelopes
attach
the
envelope
securely
to
the
outsideofthe
equipment
package.
WRITE
YOUR
RETURN
AUTHORISATION
NUMBER
CLEARLY
ON
THEOUTSIDEOFTHE
ENVELOPEORON
THE
OUTSIDEOFTHE
EQUIPMENT
PACKAGE.
58
TCU
40/80
Temperature
Control
Unit

ReturnofEdwards
Equipment-
Declaration
(FormHS2)
/0
Return
Authorization
Number
You
must:
•
Know
about
allofthe
substances
which
have
been
used
and
producedinthe
equipment
before
you
complete
this
Declaration
•
Read
the
Procedure
(HS1)onthe
previous
page
before
you
attempttocomplete
this
Declaration
•
Contact
your
suppliertoobtainaReturn
Authorization
Number
andtoobtain
adviceifyou
have
any
questions
•
Send
this
formtoyour
supplier
before
you
return
your
equipment
SECTION1:
EQUIPMENT
Equipment
model
_
Serial
Number
Hours
Has
the
equipment
been
used,
tested,oroperated?
yesâ–¡GotoSection2noâ–¡GotoSection
4
FOR
SEMICONDUCTOR
APPLICATIONS
ONLY:
Tool
Reference
Number
Process
Failure
Date
Serial
NumberofReplacement
TCU
SKCTION2:
SUBSTANCESINCONTACT
WITH
THE
EQUIPMENT
Are anyofthe
substances
usedorproducedinthe
equipment
•
Radioactive
yesQ
noQ
•
Biologically
active
yesD
noD
•
Dangerous
to
human
health
and
yesQ
noD
safety?
If
you
have
answered
'no'toall
of
these
questions,goto
Section
4.
Your
supplier
will
not
accept
deliveryofany
equipment
thatiscontaminated
with
radioactive
substances,
unless
you:
•
Decontaminate
the
equipment
•
Provide
proofofdecontamination
YOU
MUST
CONTACT
YOUR
SUPPLIER
FOR
ADVICE
BEFORE
YOU
RETURN
SUCH
EQUIPMENT
SECTION3:
LISTOKSUBSTANCESINCONTACT
WITH
THE
EQUIPMENT
Substance
name
1
2
3
4
5
6
Chemical
symbol
Precautions
required
(for
example,
use
protective
gloves,
etc.)
Action
required
after
spillage
or
human
contact.
SECTION4:
RETURN
IN!
ORMATION
Reason
for
return
and
symptomsofmalfunction:
If
you
haveawarranty
claim:
•
who
did
you
buy
the
equipment
from
?
•
give
the
supplier's
invoice
number
Print
your
name:
Print
your
organization:
Print
your
address:
Telephone
number:
SECTION5:
DECLARATION
Print
your
job
title:_
Daleofequipment
delivery:
_
I
have
made
reasonable
inquiry
andIhave
supplied
accurate
informationinthis
Declaration.
I
have
not
withheld
any
information.
I
have
followed
the
ReturnofEdwards
Equipment
Procedure
(HSl) on
the
previous
page.
Signed:_
Date:
TCU
40/80
Temperature
Control
Unit
59

Legal
notices,
limitations
and
disclaimers
Foraperiodoftwelve
(12)
months
from
the
dateoforiginal
shipmenttoPurchaser,
the
apparatus
and
each
partofcomponent
manufactured
be Edward's
High
Vacuum
International
(Edwards)iswarranted
to
be
free
from
functional
defectsinmaterials
and workmanship.
The
foregoing
warrantyissubjecttothe
condition
that
regular
periodic
maintenance
and
servicebeperformedorreplacements
made
in
accordance
with
instructions
providedbyEdwards.
The
foregoing
warranty
shall
not
applytoany
apparatus,
part,orcomponent
that
has
been
repaired
other
thanbyEdwardsoran
authorized
Edwards
representative orinaccordance
with
written
instructions
providedbyEdwards,
that
has
been
altered
by
anyone
other
than
Edwardsorthat
has
been
subjecttoimproper
installation
or
abuse,
misuse,
negligence,
accident,orcorrosion.
Purchaser's
sole
and
exclusive
remedy
under
the
above
warrantyislimited
to,atEdward's
option,
repair
or
replacement
of
defective
partsofcomponentsorreturntoPurchaserofthe
priceofthe
apparatus.
The
defect
mustbepromptly
reportedtoEdwardsorPurchaser
must
return
the
partorcomponent
with
a
statement
of
the
observed
deficiency
no
later
than
seven
(7)
days
after
the
expiration
dateofthe
warranty
to
the
address
designated
by
Edwards,
transportation
charges
prepaid.
In the
event
that
Edwards
elects
to
refund
the
purchase
price,
the
apparatus
shallbethe
propertyofEdwards
and
shallbeshippedtoEdwards
at
Edward's
expense.
This
Mechanical
Warranty
shallbevoid
and
the
apparatus
shallbedeemedtobe
purchasedASISinthe
event
that
the
entire
purchase
price
has
not
been
paid
within
thirty
(30)
days
of
original
shipmentofapparatus.
THERE
ARE
NO
EXPRESSORIMPLIED
WARRANTIES
THAT
EXTEND
BEYOND
THE
WARRANTY
HEREIN
ABOVE
SET
FORTH.
THEREISNO
PARTICULAR
WARRANTY
OF
MERCHANT
ABILITYORFITNESS
FORAPARTICULAR
PURPOSE
WITH
RESPECTTOTHE
APPARATUSORANY
PARTORCOMPONENT
THEREOF
AND
NO
WARRANTY
SHALL
BE
IMPLIEDBYLAW.
Items
notofEdwards's
manufacture
but
resoldbyEdwards
are
the
productsofother
manufacturers
and
their
warranty,
if
any,
shall
apply.
THERE
ARENOWARRANTIESOFANY
KINDONPRODUCTS
OF
OTHER
MANUFACTURERS
RESOLDBYEDWARDS
EXCEPT
THE
WARRANTYOFTITLE.
ANDNOWARRANTIES
SHALLBEIMPLIEDBYLAW.
THEREINNOT
EXPRESSORIMPLIED
WARRANTYOFMERCHANT
ABILITYOROF
FITNESS
FORAPARTICULAR
PURPOSE
WITH
RESPECTTOPRODUCTSOFOTHER
MANUFACTURERS.
Innoevent
shall
the
Purchaserbeentitled
to
any
special,
indirect,
or
consequential
damages.
60
TCU
40/80 Temperature
Control
Unit

HANDLING
AND
STORAGE
Handling
(Personnel)
Avoid-breathing
vapor.
Avoid
liquid
contact
with
eyes
and
skin.
Use
with
sufficient
ventilation
to
keep
employees
exposure
below
recommended
limits.
Contact with
chlorineorother
strong oxidizing
agents
should
alsobeavoided.
See
Fire
and
Explosion
Data
section.
Storage
Clean,
dry
area.Donot
heat
above52degC(125
deg
F).
EXPOSURE
CONTROLS/PERSONAL
PROTECTION
Engineering
Controls
Avoid
breathing
vapors.
Avoid
contact
with
skinoreyes.
Use
with
sufficient
ventilation to
keep
employee
exposure
below
the
recommended
exposure
limit.
Local
exhaust
shouldbeusediflarge
amounts
are
released.
Mechanical
ventilation
shouldbeusedinloworenclosed
places..
Personal
Protective
Equipment
Impervious
gloves
shouldbeusedtoavoid
prolonged
or
repeated
exposure.
Chemical
Splash
goggles
shouldbeavailable
for
useasneededtoprevent
eye
contact.
Under
normal
manufacturing
conditions,
no
respiratory
protection
is
required
when
using
this
product.
Self-contained
breathing
apparatus
(SCBA)
is
requiredifa
large
release
occurs.
Exposure
Guidelines
Applicable
Exposure
Limits
PENTAFLUOROETHANE
(HFC-125)
PEL
(OSHA)
None
Established
TLV
(ACGIH)
None
Established
AEL
*
(Du
Pont)
1000
ppm,8&12Hr.
TWA
ETHANE.
1, 1,
l-TRIFLUORO-(HFC-143a)
PEL
(OSHA)
None
Established
^
TLV
(ACGIH)
None
Established-.
'
AEL*
(DuPont)
1000ppm,
8&12Hr.
TWA
ETHANE,
1, 1,
1,2-TETRAFLUORO-
(HFC-134a)
PEL
(OSHA)
None
Established
TLV
(ACGIH)
None
Established
AEL
•
(Du
Pont)
1000
ppm,8&
12
Hr.
TWA
WEEL
(AIHA)
1000
ppm,
8 Hr.
TWA
*
AELisDuPont's
Acceptable
Exposure
Limit.
Where
governmental
imposed
occupational
exposure
limits
which
are
lower
than
the
AEL
areineffect,
such
limits
shall
take
precedence.
(Continued)
64
TCU
40/80
Temperature
Control
Unit

PHYSICAL
AND
CHEMICAL
PROPERTIES
Physical
Data
Boiling
Point -46.7C(-52,1F)
Average
Vapor
Pressure
182.1
psiaat25
degC(77
deg
F)
%Volatiles
100WT%
Evaporation
Rate
(CL4=1)
Greater
than
1
Solubility
in
Water
Not
determined
Odor
slight
ethereal
Form
Liquefied
gas
Color
Clear,
colorless
Specific
Gravity
1.05
@25C(77F)
STABILITY
AND
REACTIVITY
Chemical
Stability
Materialisstable.
However,
avoid
open
flames
and
high
temperatures.
Incompatibility
with
Other
Materials
Incompatible
with
active
metals,
alkalioralkaline
earth
metals-powdered
Al,
Zn,
Be,
etc.
Polymerization
Polymerization
will
not
occur.
Other
Hazards
Decomposition
Decomposition
products
are
hazardous.
"SUVA"
HP62
canbedecomposed by
high
temperatures (open
flames
glowing
metal
surfaces,
etc)
forming
hydrochloric
and
hydrofluoric
acids,
and
possibly
carbonyl
halides.
TOXICOLOGICAL
INFORMATION
Animal
Data
The
blendisuntested.
HFC-125
Inhalation
4-hour
ALC:
>709,000
ppminrats
Single
high
inhalation
exposures
caused
decreased
activity,
labored
breathing
and
weight
loss.
Cardiac
scnsitization
occurredindogs
exposedtoconcentrations
of
10-30%inair
and
givenanintravenous
epinephrine
challenge;
no
cardiac
sensitization
occurredata
concentration
of
7.5%.
No
animal
data are
available
to
define
carcinogenic
hazards.
HFC-125
did not
cause
cmbryotoxicity
or
developmental
toxicityinratsorrabbitsatinhalation
concentrations
up
(continued)
TCU
40/80
Temperature
Control
Unit
65

TOXICOLOGICAL
INFORMATION
(Continued)
to
50,000
ppm.
HFC-126
does
not
produce
genetic
damageinbacterial
or
mammalian
call
cultures
or
when
testedinanimals.
HFC-134a
Inhalation
4-hour
LC50:
567,000
ppm
in rats
A5or10second
sprayofvapor
produced
very
slight
eye
irritation
anda24-hour
occlusive
application
produced
slight
skin
irritation
in
rabbits.
The
compoundisnotaskin
sensitizer
in
animals.Notoxic
effects
were
seeninanimals
from
exposuresbyinhalation
to
concentrations
up
to
81,000
ppm.
Lethargy
and
rapid
respiration
were
observed
atavapor
concentration
of
305,000
ppm
and
pulmonary
congestion,
edema,
and
central
nervous
system
effects
occurred
atavapor
concentration
of
750,000
ppm.
Cardiac
sensitization
occurredindogsat75,000
ppm
following
an
epinephrine
challenge.
No
effectsinanimals
occurred
from
repeated
inhalation-exposures
to
99,000
ppm
for
two
weeksorhigher
concentrations
to
50,000
ppm
for
three
months.
Repeated
exposures
to
higher
concentrations
caused
transient
tremors,
incoondination
and
some
organ
weight
changes.
Long-term
exposures
produced
increased
testes
weights
and
increased
urinary
fluoride
levels.Noadverse
effects
were
observed
in
male
and
female
rats
fed
diets
containing
300
mg/kg/day
of
HFC-134a
for52weeks.
Animal
testing
indicates
that
this
compound
does
not
have
carcinogenic
or
mutagenic
effects.
Inhalation
of50000
ppm
for
two
years
caused
an
increase
in
benign
testicular
tumorsinmale
rats.Noeffects
were
observedatlower
concentrations.
The
tumors
were
late-occurring
and
were
judged
nottobe
life-threatening.
Embryotoxic
activity
has
been
observedinsome
animal
tests
but
onlyathigh
concentrations
that
were
also
maternally
toxic.
HFC-143a
Inhalation
4-hour
LC50:
>540,000
ppm
in rats
Single
exposures
by
inhalation
to
500,000
ppm
caused
anesthesia
butnomortality
at
540,000
ppm.
Cardiac
sensitization
occurredindogsat600,000
ppm
following
an
intravenous
challenge
with
epinephrine.
Two,
4-week
inhalation
have
been
conducted.
In the
first
study,
pathological
changesinthe
testes
were
observedatall
exposure
concentrations;
no
effects
were
observedinfemales.
The
testicular
effect
was
considered
relatedtothe
method
usedtoexpose
the
ratstoHFC-143a.Inthe
second
study using
the
same
exposure
concentrations,
no
effects
were
notedinmalesatany
concentration.
Data froma90-day
study
revealednoeffectsinmaleorfemale
rats
at
exposuresupto
40,000
ppm.
Long-term
exposure
caused
significantly
decreased
body
weightsinmale
rats
fed
300
(continued)
66
TCU
40/80 Temperature
Control
Unit