
Close Control
Small System Range
Chilled Water Units
Installation, Operation & Maintenance Manual 50/60Hz
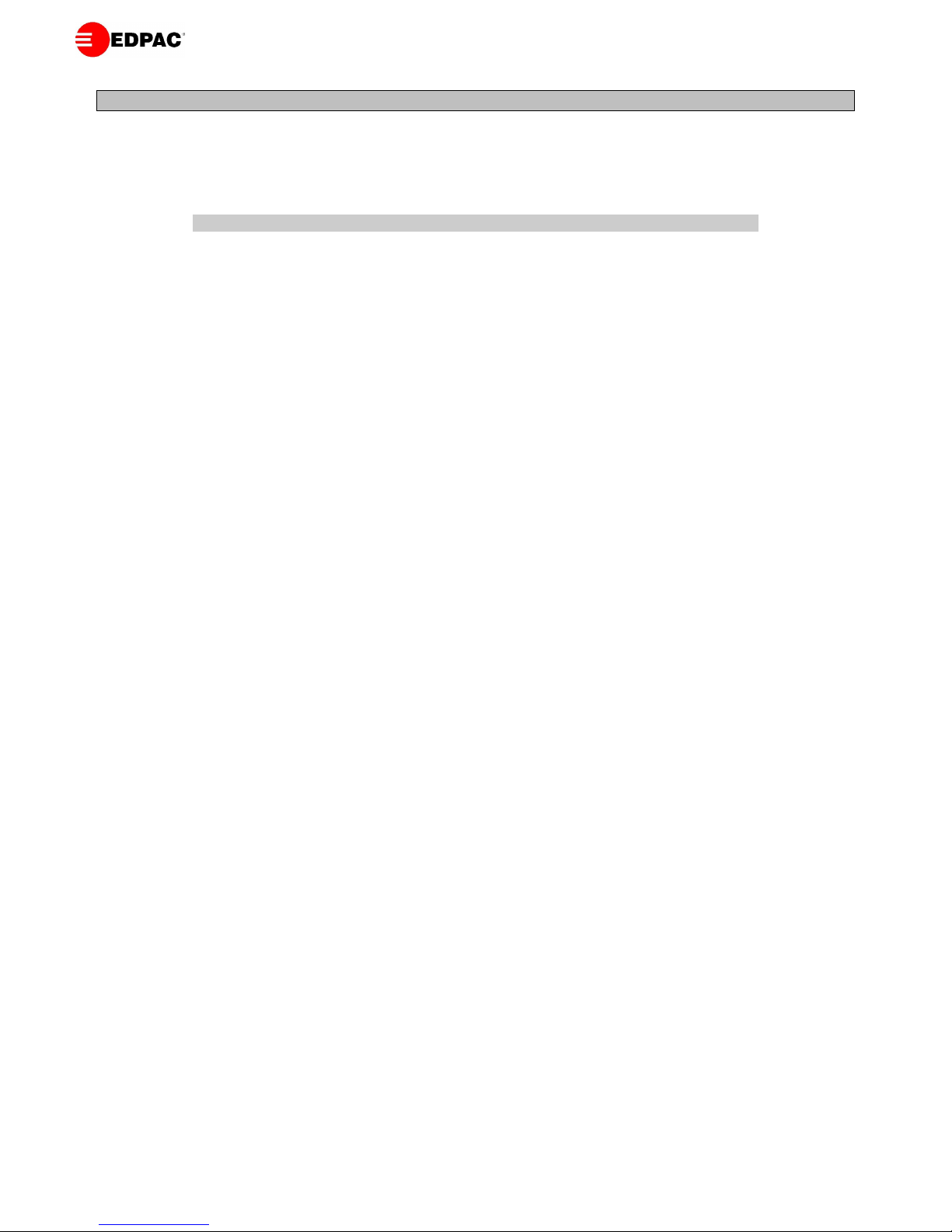
INSTALLATION OPERATION & MAINTENANCE MANUAL
Water and Drain Connections
Electric Panel – Inspection & Functional Tests
Steam Humidifier Canister Cleaning & Removal
Monthly Maintenance Inspection Check
Annual Maintenance Inspection Check
While every precaution has been taken to ensure accuracy and completeness in this manual, EDPAC assumes no responsibility, and disclaims all liability
for damages resulting from use of this information or for any errors or omissions. Document reference E4.19-02-06-04
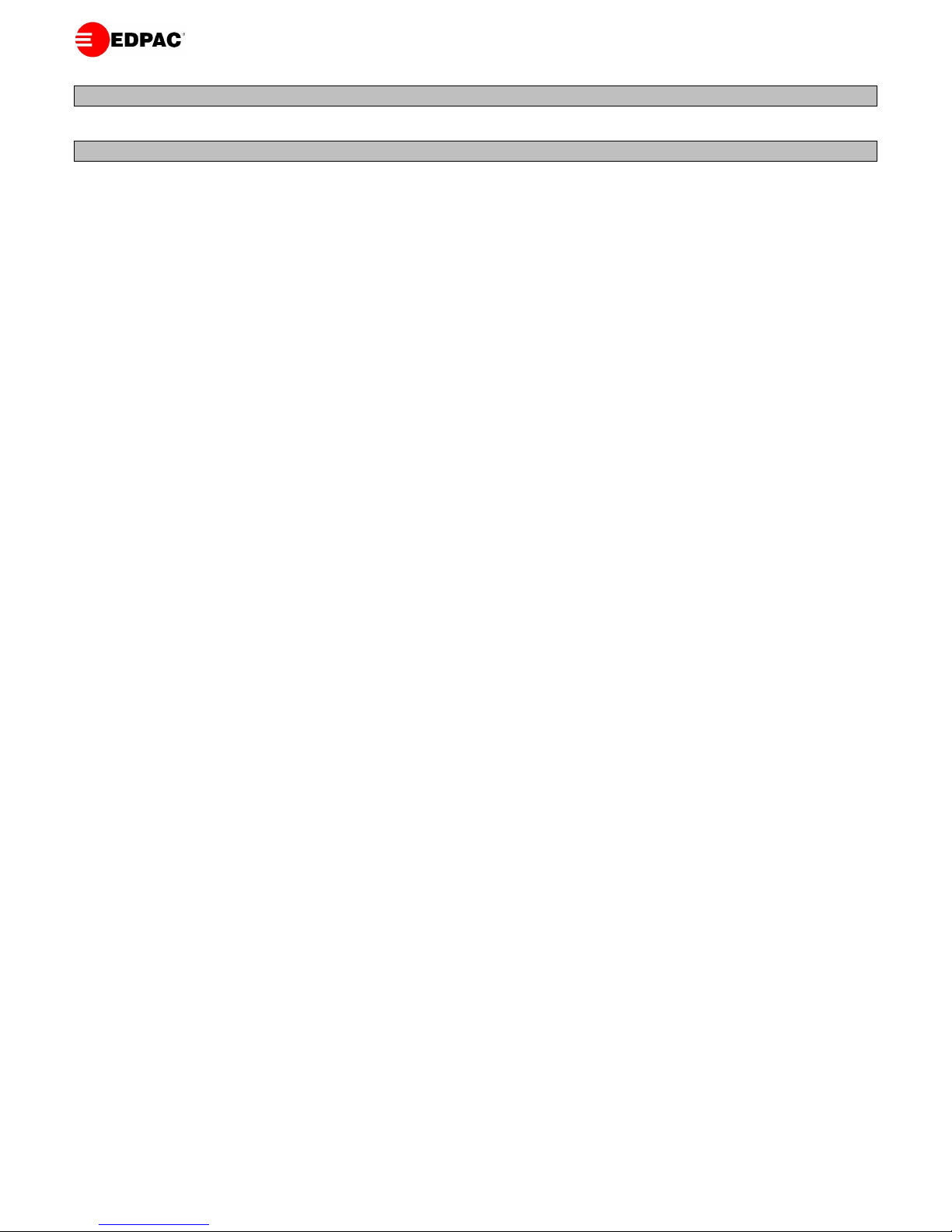
On receiving the equipment it should be checked to ensure that it is complete and in perfect condition. The carrier should be notified
immediately, in writing, of any damage that might have been caused in transit.
HANDLING
Always keep the unit vertically upright and do not leave it out in the open. The unit can be moved with a pallet truck. If a forklift is
being used ensure the forks extend beyond the pallet. Care should be taken not to damage the bottom of the unit. If a crane is being
used to move the unit leave the packaging intact and place spreader bars across the top of the unit to prevent the slings causing
damage. The unit should be moved as near as possible to the installation position before removing the cardboard packing and the
pallet.
UNPACKING THE UNIT
1) Cut the three straps binding the unit taking care to avoid any backlash caused by their tightness.
2) Remove the lid.
3) The cardboard sleeve will then unravel itself revealing a plastic dust cover.
4) Remove dust cover. If it is a downflow model, to remove the front panels use the key attached to the sensor on the top of the unit.
5) Remove the two bolts securing the unit to the skid (19 mm spanner).
6) Manoeuvre the unit carefully from the pallet. If it is necessary, use rollers underneath the unit to locate it in its final position.
7) If the unit requires a plenum fix same before final positioning.
8) Ensure the unit is positioned on a level floor.
POSITIONING
Single Circuit Units.
The Modular Range is built on a level base and its positioning is most important. The unit should be firmly supported on the floor
itself or on an optional floorstand.
Ensure that the unit is level in all directions as failure to do so will result in operational problems, particularly with regards to
drainage. Care should be taken in manoeuvring the unit as the paintwork could be damaged. Use rollers where possible and apply
pressure to the bottom of the unit for final positioning. Before final positioning ensure that inaccessible panels are correctly fitted and
plenums are secured.
ATTACHING THE PLENUM
The plenum and unit are pre-drilled. At the time of installation remove the grilles from the plenum and secure the plenum internally by
means of self tapping screws provided. Also secure to the back of the unit.
AIR COOLED CONDENSERS
Locate these as close to their final position as possible before uncrating. A full set of assembly instructions are attached to the unit.
Headers and return bends are not to be used in the moving of the condenser.
When locating the condenser ensure that it is in an open area with unrestricted airflow shaded from direct sunlight.
Install in an environment free of debris to avoid the fins becoming blocked.
Ensure that some form of vibration elimination is installed between the condenser legs and the roof of the building.
Condensers are not to be ducted on either side.
Where noise is critical in relation to the condenser make ensure that this is clearly specified at the time of order.
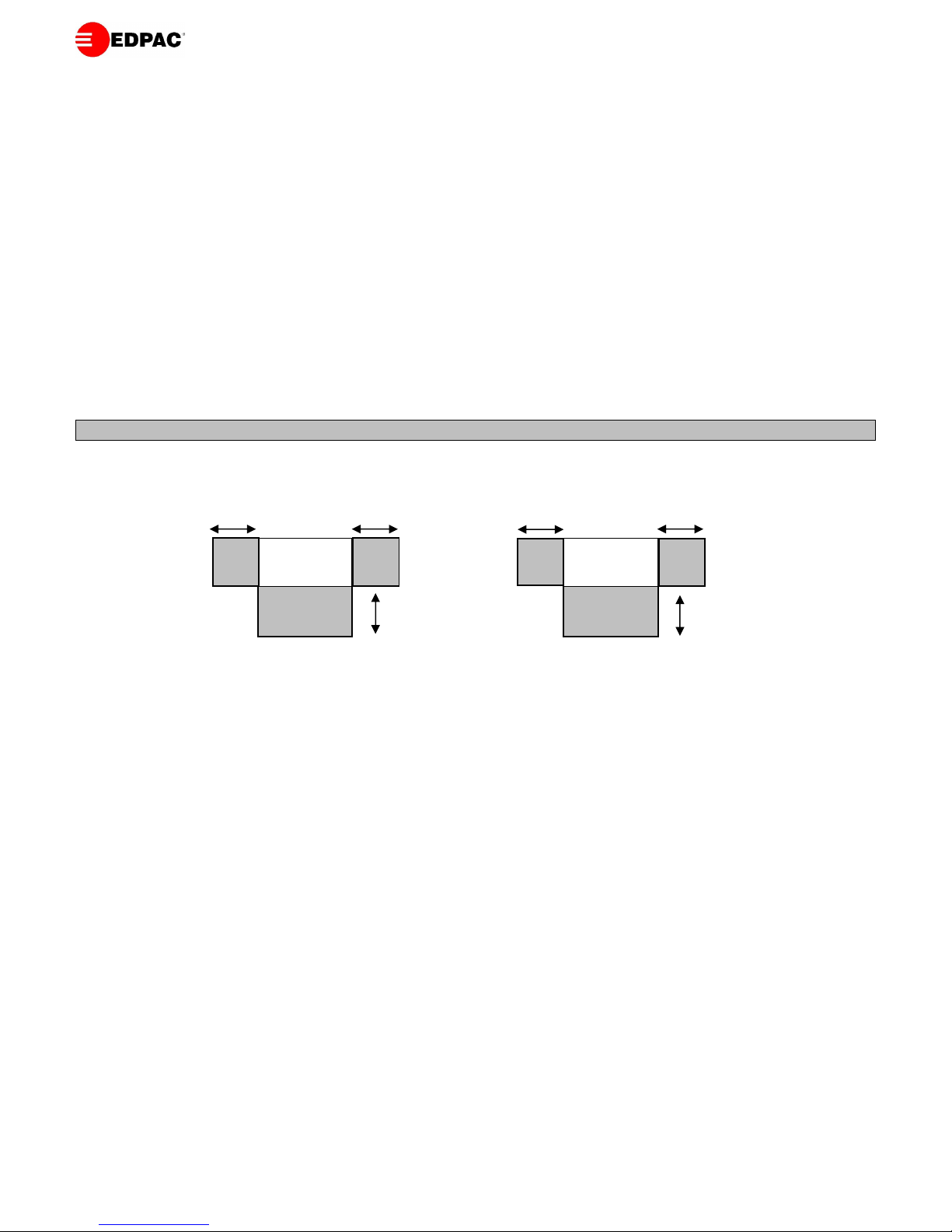
SERVICE ACCESS
Downflow Units
Service of a downflow unit can be generally completed from the front of the unit. To remove certain components from the unit it may
be easier and quicker to have side access to assist in these operations.
When positioned there should be a minimum clearance in front of the unit of 0.6m. If it is feasible, leave a distance of 0.6m at the
side of the unit. Access to the back of the unit is not necessary. It is strongly recommended to leave a distance of 0.6m at both sides of
the unit. There is a minimum distance of 150mm needed above the unit to allow removal of the filters.
Upflow Units
Unlike the downflow, side access is necessary for servicing the upflow. When installing ensure the left-hand side of the unit has access
for the purpose of servicing, especially the motor. On the small frame the motor is actually mounted 'piggy-back' on the blower and on
the mid and large frame the motor is located on the left-hand side of the blower
Access to the back of the unit is not required. It is strongly recommended to leave a distance of 0.6m at both sides of the unit. The
filters are located in the bottom front panel; a minimum distance of 1m is needed to allow the return air to enter the unit.
Space above the unit will be determined by location. If a standard plenum is being installed the overall height of the unit is extended
to 2380mm.
SYSTEM APPLICATION
To achieve maximum performance and efficient energy usage following considerations should be given:
1) The room should be sealed effectively against air and vapour to minimise the loss and infiltration of uncontrolled humidity through
concrete slab, walls, ceiling, roof, doors or any other opening or aperture.
2) Room location and orientation should be considered with regard to heat load and external variables should be reduced to a
minimum.
3) The room should be kept at a positive pressure by introduction of pre-treated fresh air.
4) Low resistance to conditioned air distribution can be achieved by providing the maximum raised flooring height, minimum cable
bunching and correct position of pipework (i.e. parallel to air flow).
5) Pipework that is not isolated or is fastened inadequately can transmit vibration along its full length.
Downflow Small System Unit
Service Access
Upflow Small System Unit
Service Access
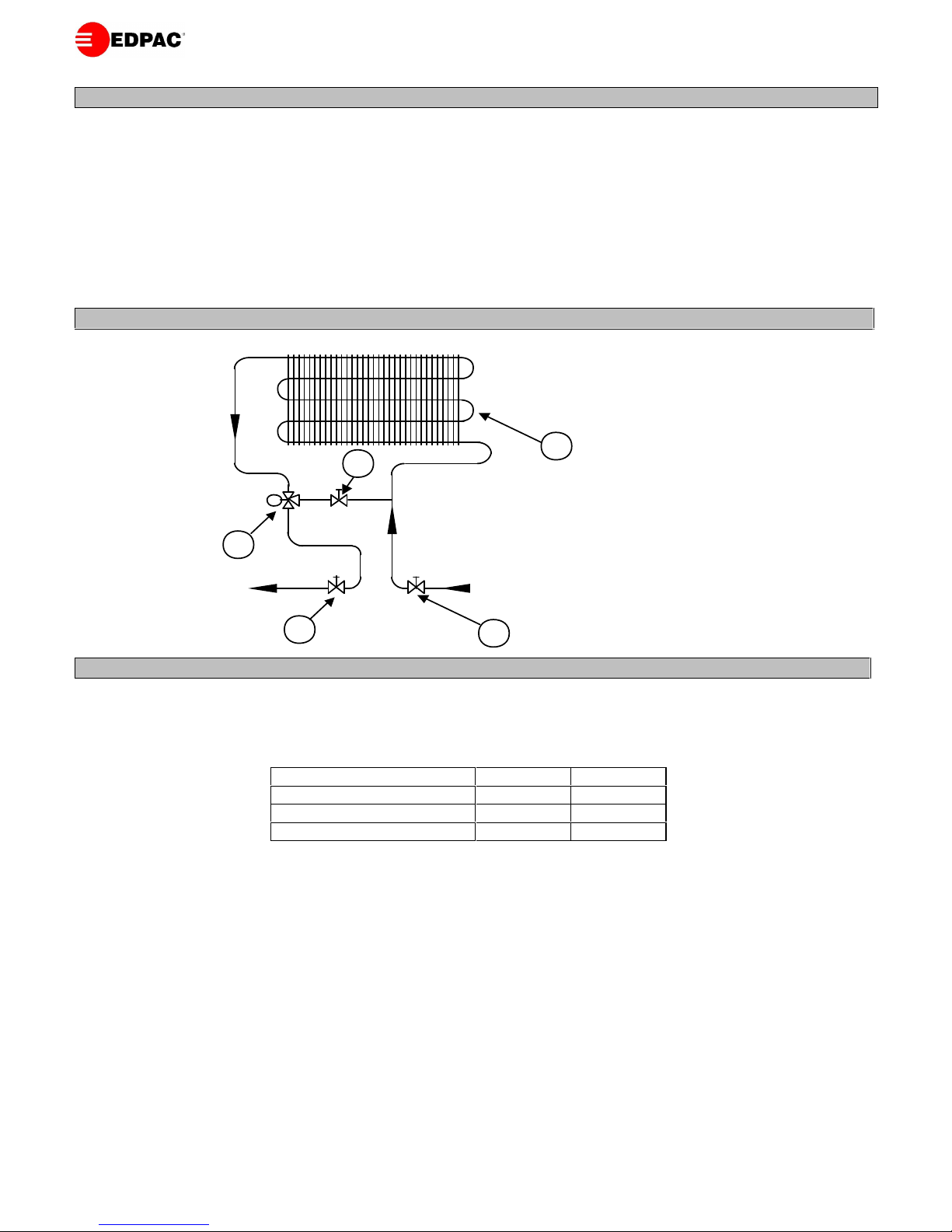
CHILLED WATER PIPING CONSIDERATIONS
Chilled water units are shipped with the flow and return pipes terminated with soft solder caps. The complete system is pressurised to
75psi with dry nitrogen. This pressure should be rechecked and discharged before caps are unsoldered. Supply and return pipes are
clearly marked. Check the site piping to ensure that the flow is in the proper direction.
The maximum allowable static pressure for the chilled water circuit is 1000kPa. If static pressure exceeds 1000kPa special valves
should be installed. Consideration of the minimum water temperature to be supplied from the chiller will determine if the need exists
to insulate the supply and return lines.
It is recommended that isolating valves be field fitted on both flow and return lines from the unit for isolation and maintenance
operations. Automatic air bleed valves should also be fitted in appropriate locations.
GENERAL ARRANGEMENT DRAWING
System Components
1. Evaporator Coil.
2. Balancing Valve
3. 3 Way Modulating Valve
4. Isolating Valves
Note: Item 4 is field fitted by others.
WATER AND DRAIN CONNECTIONS
WATER SUPPLY
Water is fed from the mains supply to the humidifier inlet solenoid valve. The connection to the solenoid valve is a 3/4” male
connection. The feed water characteristics should comply with the following values:
In the case of high water pressure a pressure reducing valve calibrated to between 3 - 4 bar should be fitted. Inlet water temperature
must not exceed 50oC. It is recommended to install a shut-off valve and a mechanical filter with the wire mesh size less than 50µm.
The humidifier pan drain connection is a 22 mm female connection. The humidifier drain can be discharged into the standard drainage
system via a rubber or plastic hose suitable for temperatures up to 100oC. The hose should have a minimum internal diameter of
22mm. A trap or vertical loop should be fitted in the tubing to prevent blow back or odours and ensure that the drain has a fall of not
less than 1:50.
Note: Do not feed demineralised water into the humidifier.
CONDENSATE DRAIN
Install a drain pipe from the base of the drainpan (typically a 1" female B.S.P. fitting). Insulating this drain pipe is not necessary. It is
advised to fit a trap in this drainpipe. On a twin circuit unit there are knockouts on the side panels to route drain hoses through to a
single outlet. Copper pipe should be used for drains on units with humidifiers. If the system is equipped with a condensate pump,
install a check valve on the discharge line of the pump to prevent backfilling the pump reservoir.
Electric Conductivity at 25oC
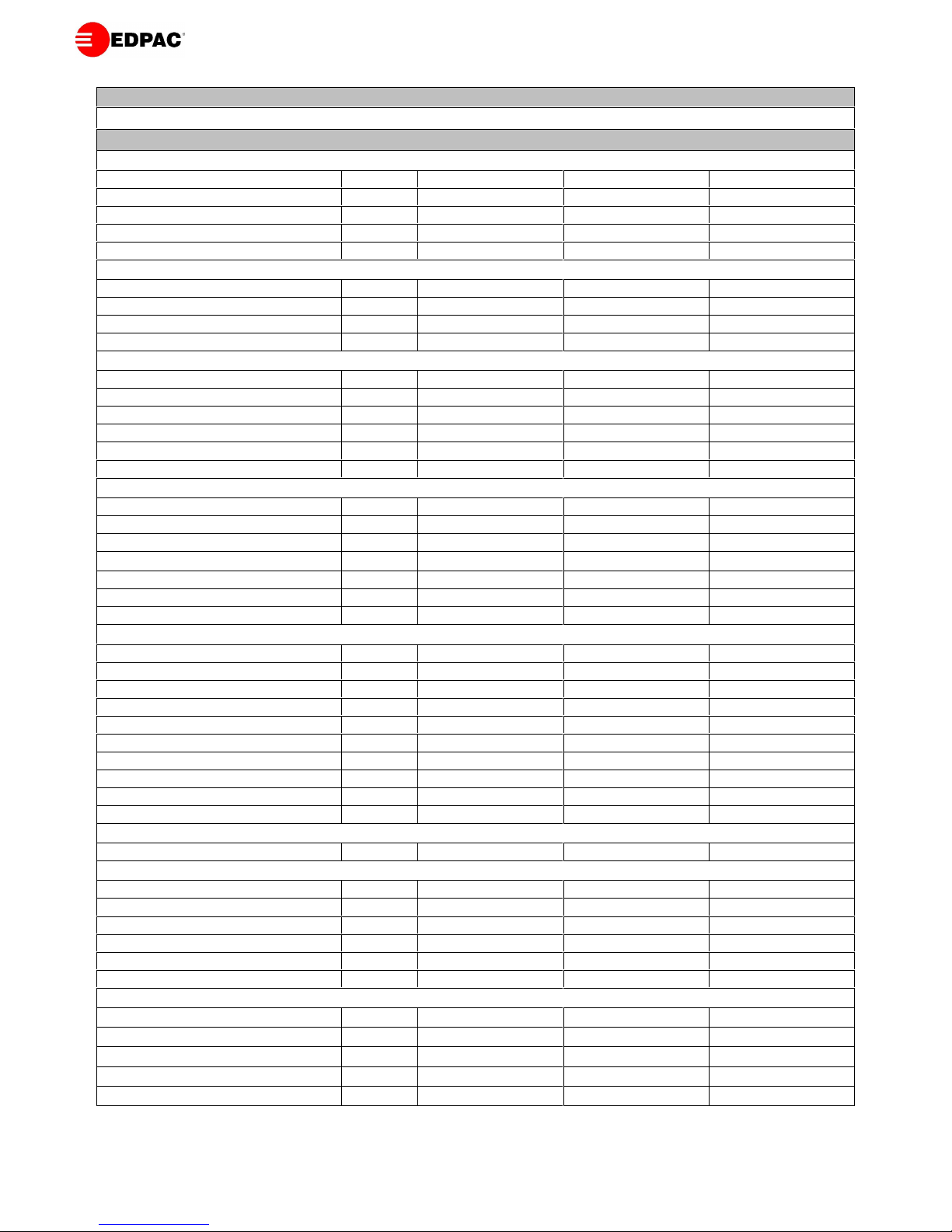
External Static Pressure ESP
Chilled Water F&R Pipe Size
Coil Face Area – DX and C. Water
Coil Drain Connection BSPF
Condenser Conns. Inlet/Outlet 30°C
Condenser Conns. Inlet/Outlet 35°C
Condenser Conns. Inlet/Outlet 40°C
Condenser Conns. Inlet/Outlet 45°C
Condenser Conns. Inlet/Outlet 50°C
Water Feed Electrical Conductivity
French Degrees Water Hardness
Optional Electric Reheat Data
Notes
1. Indoor unit Free field SPL dBA levels are measured at 3m.
2. For correct installation pipe sizes refer to refrigerant and water pipe sizing tables.
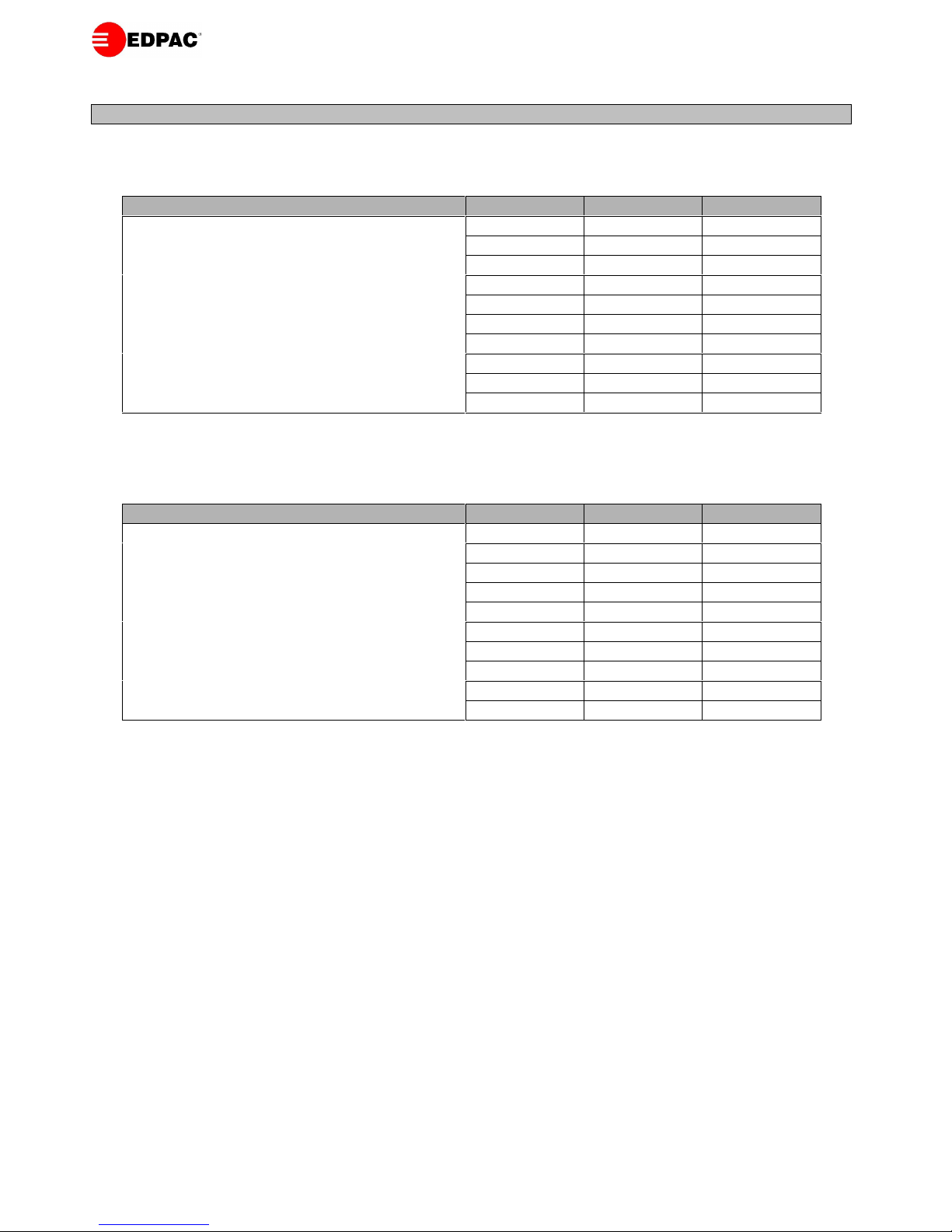
Max Unit FLA - Cooling only
Max Unit FLA - Cooling & Dehumidification
Max Unit FLA - Heating and Humidification
Max Unit FLA - Cooling only
Max Unit FLA - Cooling & Dehumidification
Max Unit FLA - Heating and Humidification
Notes:
1. FLA = Full Load Amps.
2. Unit maximum FLA is the total of the components, which operate during maximum electrical load conditions.
3. Max FLA of Cooling only unit : FLA = Controls + Fans
4. Max FLA of unit with reheat only in dehumidification : FLA = Controls + Fans + Reheat.
5. Max FLA of units with heating & humidifiers : FLA = Controls + Fans + Reheat + Humidifier.
6. Max Fuse is the recommended value of the unit overcurrent protection device.
ELECTRICAL DETAILS – CHILLED WATER UNITS
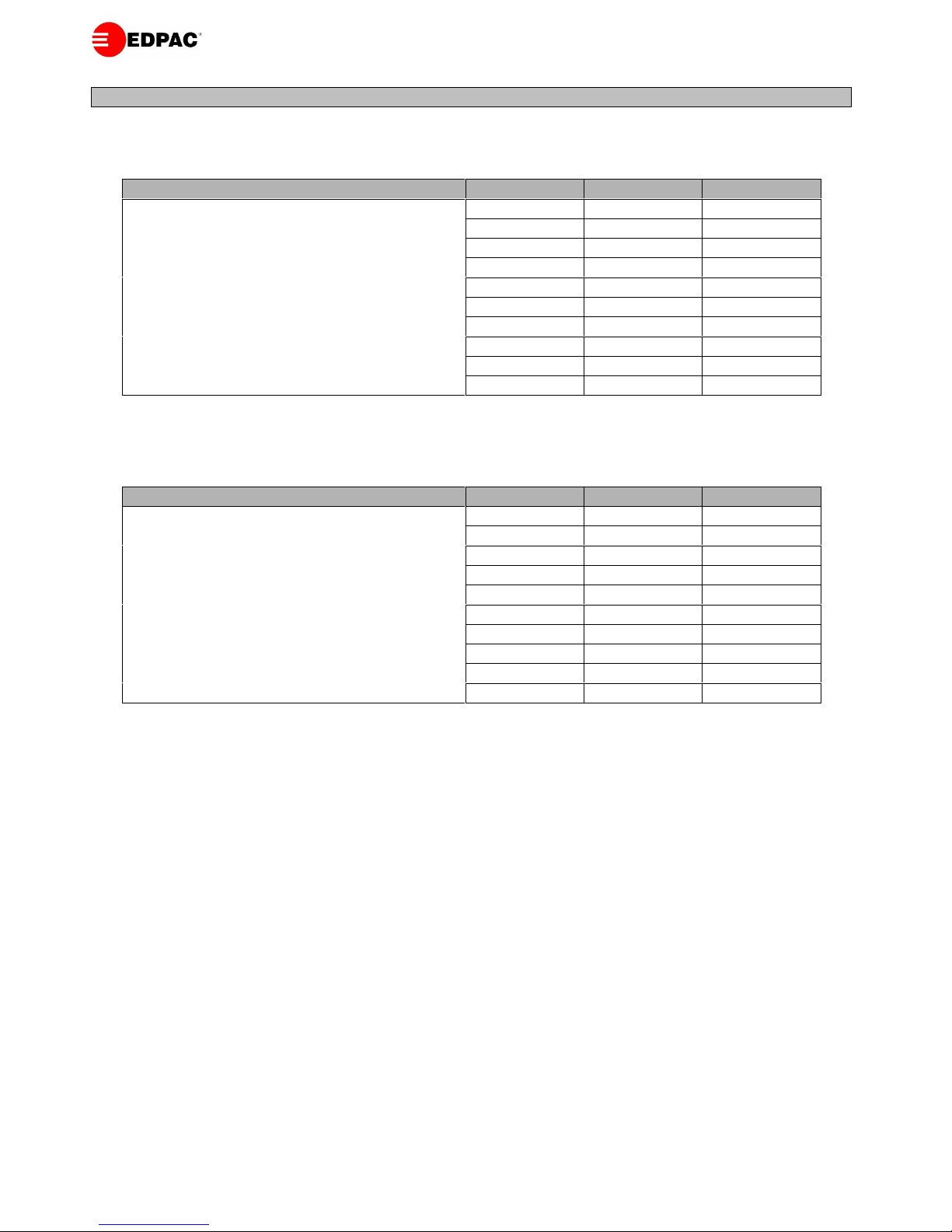
Max Unit FLA - Cooling only
Max Unit FLA - Cooling & Dehumidification
Max Unit FLA - Heating and Humidification
Max Unit FLA - Cooling only
Max Unit FLA - Cooling & Dehumidification
Max Unit FLA - Heating and Humidification
Notes:
1. FLA = Full Load Amps.
2. Unit maximum FLA is the total of the components, which operate during maximum electrical load conditions.
3. Max FLA of Cooling only unit : FLA = Controls + Fans
4. Max FLA of unit with reheat only in dehumidification : FLA = Controls + Fans + Reheat.
5. Max FLA of units with heating & humidifiers : FLA = Controls + Fans + Reheat + Humidifier.
6. Max Fuse is the recommended value of the unit overcurrent protection device.
ELECTRICAL DETAILS – CHILLED WATER UNITS