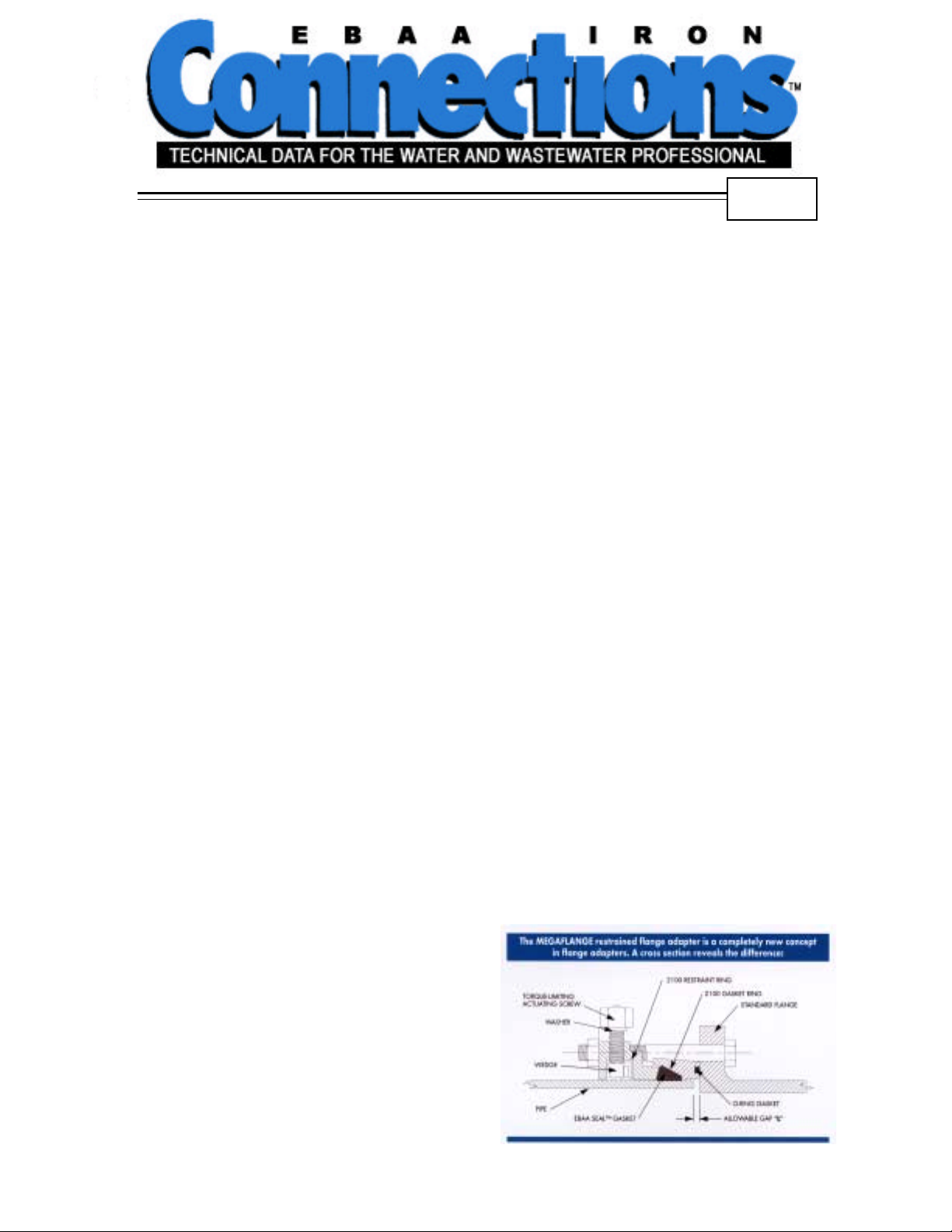
BACKGROUND AND TESTING OF THE
MEGAFLANGE
®
FLANGE ADAPTER
INTRODUCTION
EBAA Iron developed the Series 2100
MEGAFLANGE
®
flange adapter to make the
installation of flanged piping and fitting more
field adaptable. The Series 2100 utilizes wedges
rather than set screws to grip the pipe. The
MEGAFLANGE flanging system provides a
fully restrained joint with deflections
capabilities. It is availab l e in sizes 3 inch through
36 inch. The Series 2100 has been subjected to
several kinds of hydrostatic pressure tests on a
variety of piping material. This report details the
3 through 12 inc h si zes.
BACKGROUND
Although the installation proce dure for the
flanged joint is very simple and straight forward,
there are several problems associated with the
flanged joint that make it difficult to install in the
field. For example, the flanged joint requires an
excessive amount of torque on the bolts to
achieve a good seal. The pipe layout must be
precisely planned to avoid misalignment errors
due to deviations in appurtenances or pipe
fabrication.
Products such as the flange adapter and the
flanged coupling adapter were introduced to
make flanged joints easier to assemble in the
field. While these products have been helpful,
they are limited. Typical flange adapters use a
standard mechanical joint gasket for both the
pipe and the flange seal and are still prone to
leaks. The flanged coupling adapter separates the
pipe seal from the flange seal but most are not
restrained. In most cases, unrestrained flange
adapters and flange coupling adapters must be
restrained. In some cases, set screws are
incorporated to restrain these devices, but set
screw restraints are ineffective when compared
to the “pull out strength” of the standard flanged
joint. However, the MEGAFLANGE adapter
from EBAA Iron provides a field fabricated,
fully restrained flanging system for use on plain
end ductile iron, steel, and PVC pipe. The
MEGAFLANGE flange adapter not only
provides a way of connecting plain end pipe to a
flanged fitting, it also delivers flexibility, up to
5° in three through eight inch sizes and up to 3°
FL-2
9-94
in the ten and twelve inch sizes, both during and
after assembly.
SERIES 2100 MEGAFLANGE FLANGING
SYSTEM
For years, EBAA has produced flange adapters
similar in design to any other flange adapter.
Consequently, EBAA’s flange adapters
encountered the same problems as the others on
the market. The Series 2100 MEGAFLANGE
adapter from EBAA is a completely new
product. The cross section of the Series 2100 can
be seen in Fig. 1. As can be seen in the figure,
the Series 2100 is comprised of two rings. The
first is the restraint ring. Wedges, around the
circumference of the ring, grip the pipe. The
wedge style of restraint offers enormous pullout
strength when compared to that of the set screw
type restraint. The resiliency of the wedge style
restraint allows the Series 2100 to withstand
severe moment loads. The second ring, the
gasket ring, separates the seals dedicated to each
sealing surface. This ring allows the pipe to be
cut in the field at the tolerance of 0.6 inch or
more. The gasket ring also enables the joint to
deflect during assembly.
The MEGAFLANGE flange adapter can be
deflected five degrees d uring assembly through
the eight inch size and three degrees in the ten
and twelve inch sizes. The deflection capabilities
provided by the gasket ring allows offset of
almost nineteen inches of an eighteen foot length
of pipe through the eight inch size. The ten and
twelve inch sizes are capable of an eleven inch
offset or greater over an eighteen foot span.
However, the gap between the pipe end and the
flange face should never be greater than the
dimension “L”.
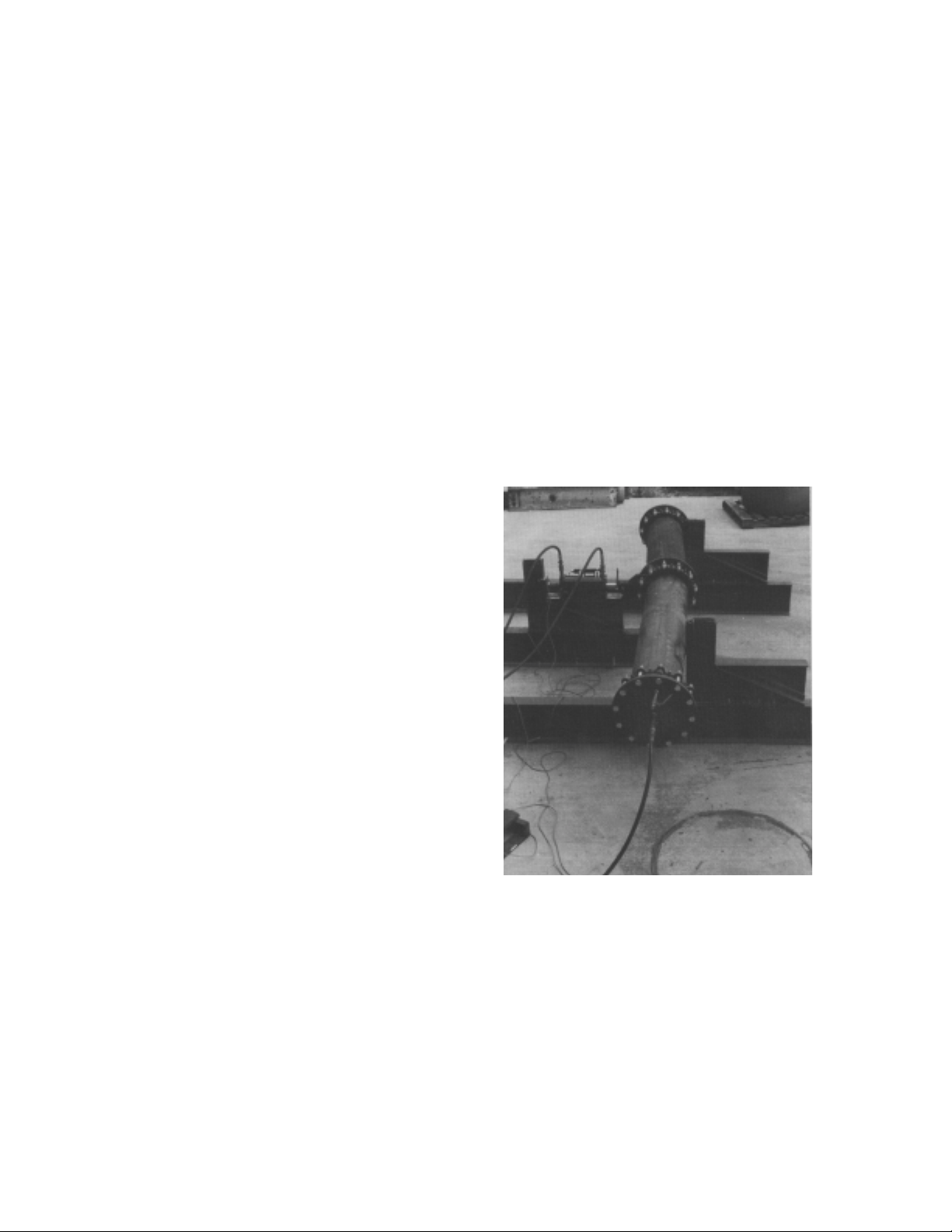
TESTING
The Series 2100 has been subjected to several
hydrostatic pressure tests. The testing procedure
was as follows:
1) A test section was made using a length of pipe
closed with the Series 2100 restraint and blind
flanges.
2) The test section was filled with water and
vented of all the air.
3) The section was pressurized to the specified
requirements.
The testing co nducted on PVC involved a quick
burst, high pressure test, and a long term test.
Our quick burst test requirement was that the test
section was to be pressurized to or beyond the
minimum burst pressure for various dimension
ratios (DR’S or SDR’s). For example, DR18
PVC pipe was tested to 755 psi and DR14 PVC
pipe was tested to 985 psi.
The long term pressure test consisted of the test
sections being pressurized to a specific pressure
for 1000 hours. The pressure is determined by a
stress regression line equation developed by
Robert T. Hucks. A DR18 sample should be able
to hold 615 psi for 1000 hours. The Series 2100
has been tested on DR18 PVC pipe at 615 psi for
1000 hours without failure.
The testing preformed on steel and ductile iron
pipe was conducted according to Underwriters
Laboratory standard UL213. This standard
required three separate tests: a leakage test, a
hydrostatic test, and a flexural test.
The leakage test required the test section to
withstand twice the rated pressure without
leaking for one minute. The hydrostatic test
required the test sample to withstand for one
minute a multiple of the rated pressure without
rupture. The three through six i nch sizes were
required to withstand a pressure five times the
rated pressure. The eight and ten inch sizes were
tested to four times the rated pressure and the
twelve inch size was subjected to a pressure
three times three times the rated pressure.
The final test was the flexural test. The pipe and
joint were required to withstand a bending
moment based on twice the weight of water
filled pipe over twice the maximum distance
between pipe supports as specified in the
“Standard for Installation of Sprinkler”, NFPA
13-1991. The test was conducted with the test
section at rated pressure. The photograph to the
right shows the test set up for the flexural test.
The moment requirements are listed below.
Nominal Fitting Size Moment Requirements
(Inches) (Ft-lbs.)
3 2426
4 3845
6 7085
8 11304
10 16785
12 22950
The tests were conducted on SCH40 steel and
PC350 ductile iron pipe. An additional pipe
damage test was conducted on the ductile iron
samples according to paragraph 9 of the
Underwriters Laboratories standard UL194. The
purpose of this test was to confirm the fact that
the Series 2100 does not damage the pipe wall or
the mortar lining.
SUMMARY
The Series 2100 MEGAFLANGE adapter
provides a strong, resilient and field adaptable
flanging system. The MEGAFLANGE adapter is
listed for above ground use by Underwriters
Laboratories in sizes three through twelve inch
for joining plain end Schedule 40 steel or ductile
iron pipe to flanged fittings. The Series 2100
may also be used on C900 and IPS PVC at the
full pressure rating of the pipe. The
MEGAFLANGE adapter is simple to install and
allows a greater tolerance in plant layout than