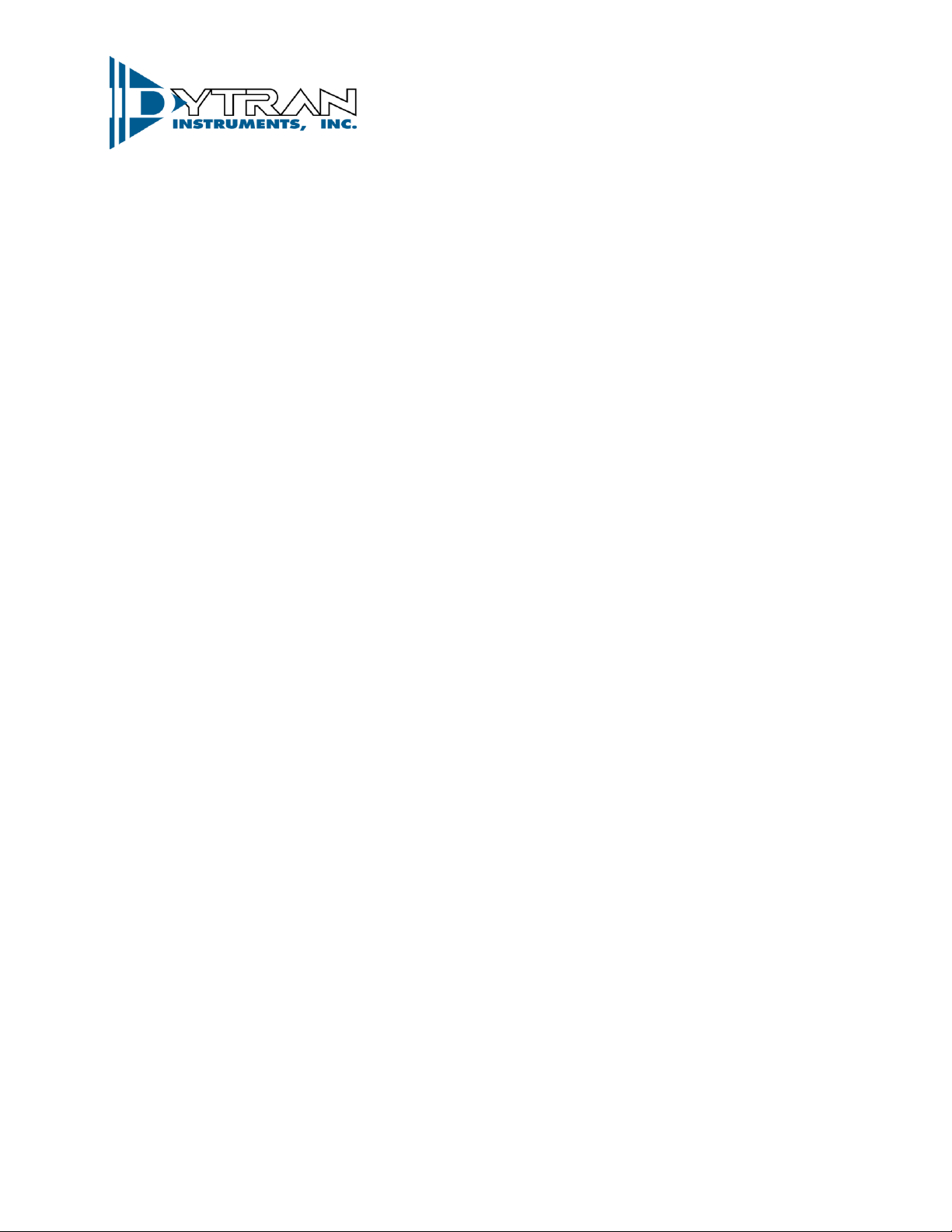
D y n a m i c T r a n s d u c e r s a n d S y s t e m s
2 1 5 9 2 M a r i l la St. • Chat s w o r t h , C A 9 1 3 1 1 • P hone 8 1 8 -700-7818
w w w . d y t r a n . c o m • e -mai l : i n f o @ d y tr an.com
OG1060C.docx 1-25-01
OG1060C.docx ECN 9708 3-6-13
Rev B, ECN 12920 08-23-16
OPERATING GUIDE
MODEL 1060C
CHARGE MODE DYNAMIC FORCE SENSOR
This manual contains:
1) Outline/Installation drawing 127-1060C
2) Operating Instructions Model 1060C
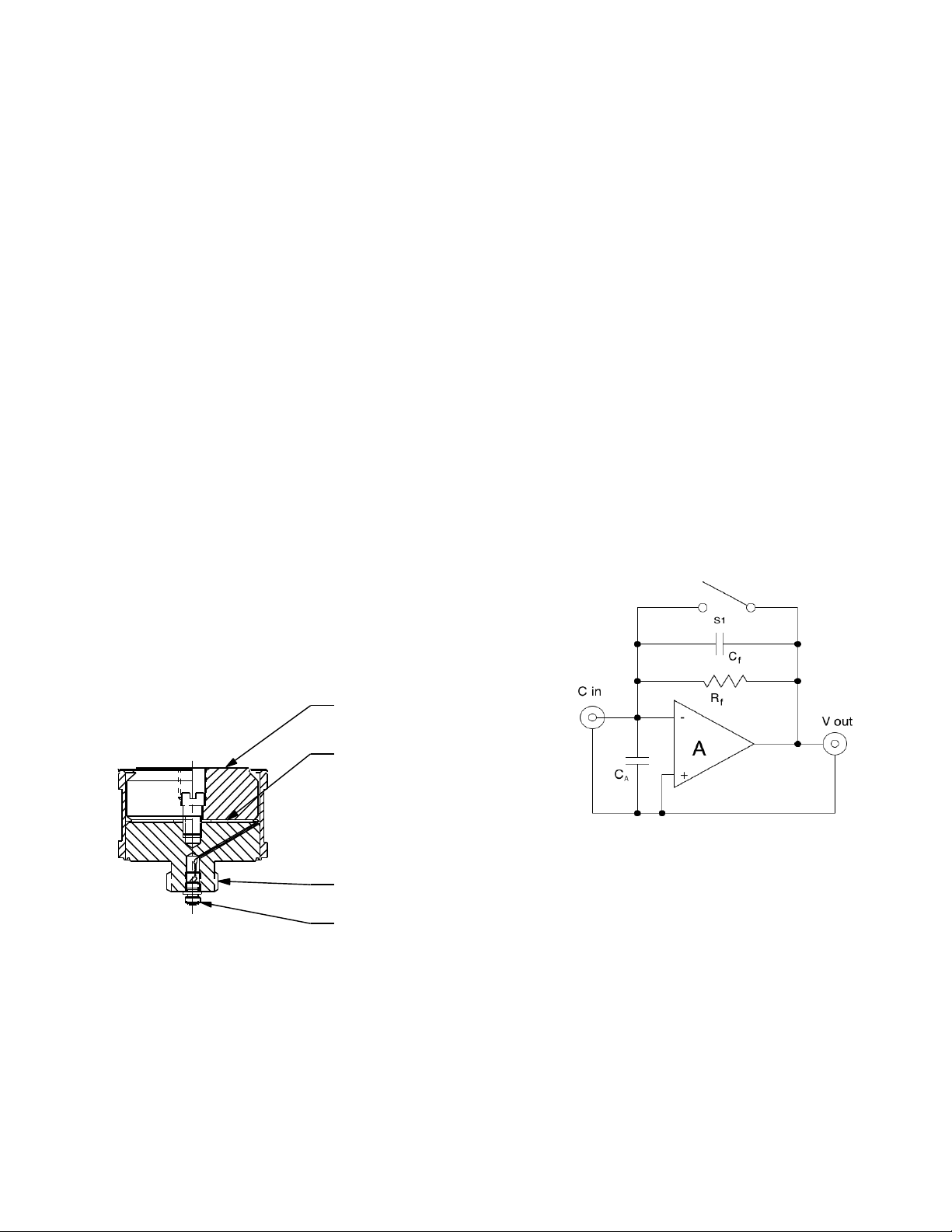
OPERATING INSTRUCTIONS MODEL 1060C
PLATEN
QUARTZPLATE
AND INSULATOR
10-32COA XIAL
CONNECTOR
THREADED
MOU NTING STEM
CHARGE MODE DYNAMIC FORCE SENSOR
INTRODUCTION
The 1060C force sensor is designed to
measure compressive and tensile forces over a
wide dynamic range, e.g., from 10 Lbs full scale to
25,000 Lbs full scale over a very wide frequency
range, (quasi static to 50 kHz.) This sensor can
measure to 500 Lbs full scale in tension.
A thin x-cut quartz crystal held under very
high preload, provides an electrostatic charge output
analogous to dynamic force input. The output
polarity is negative-going for compression and
positive-going for tension.
Model 1060C features an integral axial
mounting stud (threaded stem) which protrudes from
the bottom of the unit. The 10-32 coaxial electrical
connector is at the end of this stud.
DESCRIPTION
Refer to figure 1 below for a representative
cross section of Model Series 1060C force sensor.
Series 1060C features an integral threaded
(11/16-12 thread) mounting stud for convenient
mounting where radial space is limited. As
previously stated, the electrical connector is located
at the bottom end of the stud.
Referring to Figure 1, the upper threaded
member (called the platen) distributes the force
evenly across the quartz crystals while sealing the
instrument against moisture and other contaminants.
The very thin quartz crystal comprise a relatively
small portion of the length of the sensor which
results in a very high stiffness and high rigidity and
natural frequency. The overall stiffness of this
instrument is almost comparable to a solid piece of
steel of similar dimension.
Refer to the Outline/Installation drawing,
127-1060C, supplied with this manual, for a
dimensioned outline of Model 1060C.
THEORY OF OPERATION
Force compressing the load cell stresses the
crystals causing an electrostatic charge to be
generated which is exactly analogous to the applied
force. A special type of amplifier called a Charge
Amplifier because of its high impedance level must
read out this charge. Refer to Figure 2 below.
Figure 2: THE CHARGE AMPLIFIER
(SIMPLIFIED SCHEMATIC)
A charge amplifier has the ability to read out
the very small signal from the force sensor without
Figure 1: CROSS SECTION, MODEL 1060C
Model 1060C is recommended for use
where radial space is limited such as in some drop
shock testers, in impact hammers or when
instrumenting shafts or pushrods where there is no
space around the machine for the electrical
connector to exit radially.
OG1060C, Rev B, ECN 12920 08-23-16
changing the signal. The charge amplifier converts
the charge mode signal generated by the crystals to
a low impedance voltage which may then be fed
directly to almost any type of readout instrument.
A charge amplifier is essentially a very high
input impedance-inverting amplifier with infinite gain
and with capacitive feedback. It can be shown that
as the gain of the amplifier (-A) approaches infinity,
the transfer function of the charge amplifier
becomes: