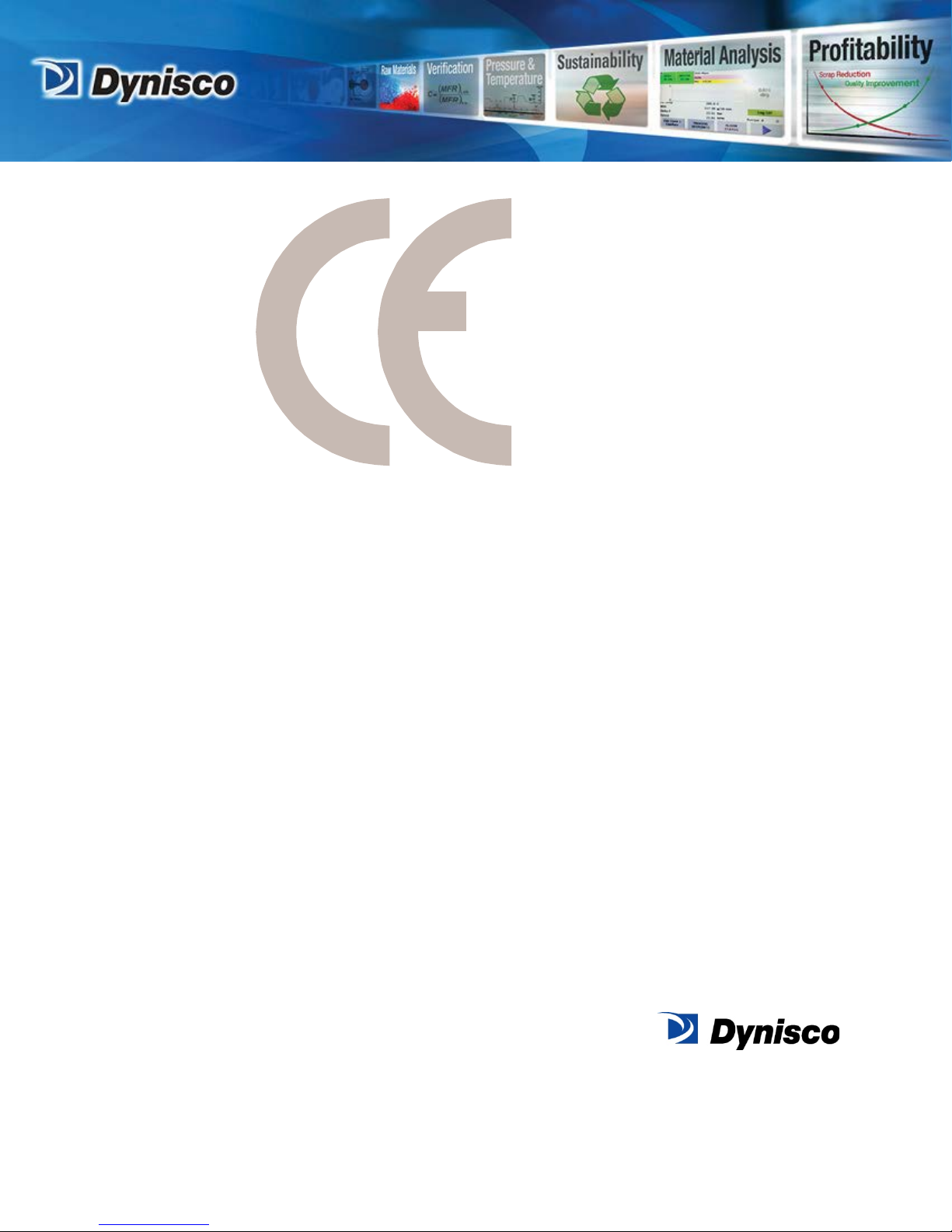
Dynisco BP420 Burst Plugs
providing a window into the process
Reliable, Secure Pressure-Relief System
Installation Instructions
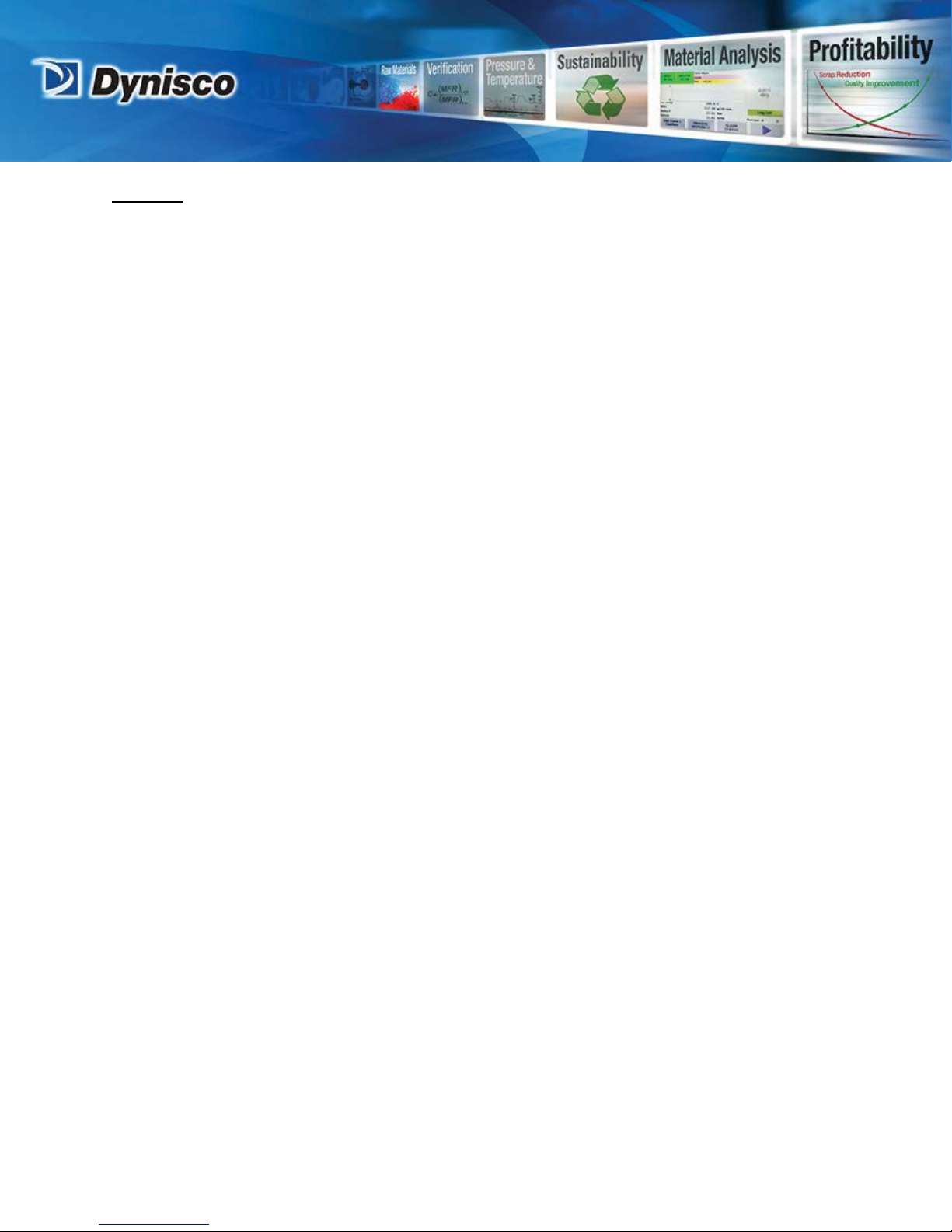
providing a window into the process
Warning:
a. Read the complete instructions before attempting to install the rupture disk.
b. It is the user’s responsibility for the design of adequate venting and installation of adequate
vent piping or directional flow after rupture occurs with the rupture disk as intended. When size
is specified, Dynisco LLC assumes that adequate provisions have been made by the purchaser
and/or user for proper venting of a system to relieve the specific pressure. Locate the rupture
disk where people or property will not be exposed to the system discharge in the event of
rupture. Vent toxic or flammable fumes to a safe location to prevent personnel injury or
property damage.
c. It is the user’s responsibility to specify the burst pressure rating at the coincident temperature
at which the rupture disk is to be used. A rupture disk is a temperature sensitive device. The
burst pressure of the rupture disk is directly affected by its exposure to the coincident
temperature. Failure to utilize a rupture disk at the specified coincident temperature could
cause premature failure or over pressurization of the system.
d. Particles may discharge when the rupture disk ruptures. These particles may be part of the
rupture disk itself, or other environmental matter in the system. It is the user’s responsibility to
ensure that the particles are directed to a safe area to prevent personnel injury or property
damage.
e. Rupture disk service life is affected by corrosion, creep and fatigue, and physical damage. These
conditions will derate the rupture disk to a lower pressure. The user should be prepared to
handle a premature failure of the rupture disk. The media or other environmental conditions
should not allow for any build-up or solidification of media on the rupture disk. This may
increase the burst rating of the rupture disk.
f. Dynisco rupture disks, when installed correctly, will provide a very good seal for liquids and
most gases or vapors. However, Dynisco cannot guarantee the leakage rate of the disk seal
without prior knowledge of the requirement and details of the piping layout. Consult ZOOK
Enterprises, LLC, ZOOK Europe Ltd., or ZOOK Canada Inc. for guidance if leakage is critical to the
installation.
g. The customer and/or its installer shall be responsible for the proper installation of rupture disk
device into a system. Recommended torque values do not consider piping stress or alignment.
h. Customer and/or its installers shall be responsible for improper installation and physical damage
resulting there from, including, but not limited to, damage resulting from leakage, improper
torquing, and/or failure to follow installation instructions.
i. Dynisco standard Terms and Conditions of Sale apply unless otherwise stated in writing by the
manufacturer.

providing a window into the process
Removal, Inspection and Preparation:
1. Removing the existing Assembly
a. Depressurize the equipment before attempting to remove the assembly even if it has
burst.
b. Loosen and remove the burst assembly with the appropriate tool. Take care not to
damage the receiving equipment.
2. Inspect The Receiving Equipment
a. Inspect the seat area for any scratches, dents, or nicks. Imperfections on these surfaces
can cause leaks. DO NOT USE if any scratches, dents or nicks are detected, (contact
Dynisco immediately for instructions).
b. Inspect and clean the receiving threads, use thread chase or other suitable cleaning
device. Threads must be in good condition to receive the rupture disk device. Utilize the
Dynisco Machining tool kit for proper hole sizing.
3. Inspect The Rupture Disk Device
a. Carefully remove the rupture disk device from its packaging and check the seat area,
exposed threads and pre-bulged surface of the disk for any scratches, dents, or nicks.
Imperfections on these surfaces can cause leaks. DO NOT USE if any scratches, dents or
nicks are detected, contact Dynisco immediately for instructions.
b. Installation of a damaged assembly may result in premature rupture of the disk.
Installation
1. Insert the new assembly into the pre-taped opening in the receiving equipment.
2. Start threading by hand to ensure the threads are matched and in good condition. DO NOT
FORCE THE THREADS. Continue threading the assembly by hand until fully seated.
3. Tighten as required to prevent leakage with the appropriate tool (wrench, screwdriver, spanner,
etc.) DO NOT OVER TIGHTEN as this can damage sealing surfaces and threads.
4. For assemblies having tapered pipe threads; use Teflon tape or other suitable pipe thread
sealants as required if compatible with the process medium.