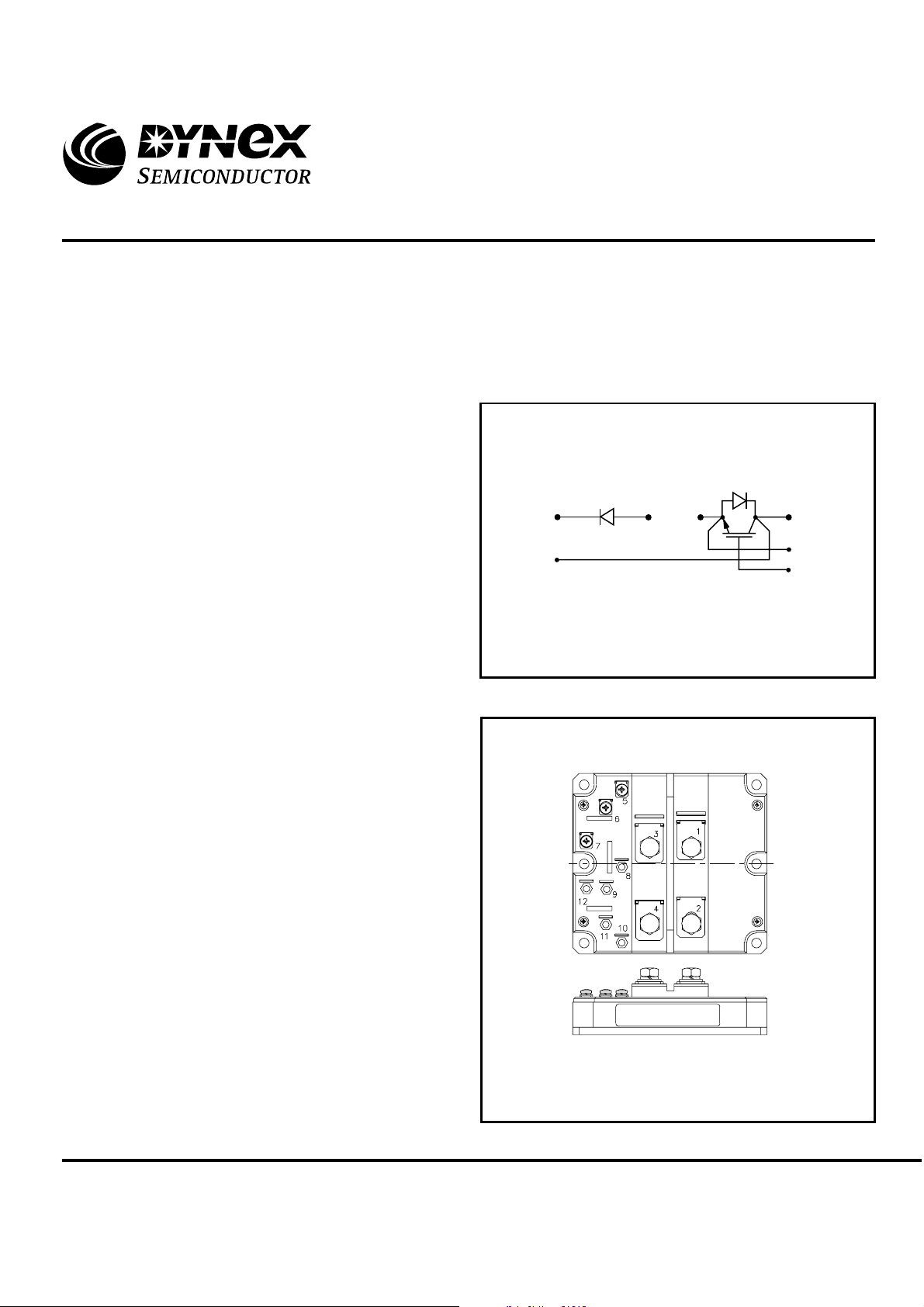
GP801DCM18
GP801DCM18
FEATURES
■ Low V
■ 800A Per Module
■ High Thermal Cycling Capability
■ Non Punch Through Silicon
■ Isolated MMC Base with AlN Substrates
CE(SAT)
APPLICATIONS
■ High Reliability
■ Motor Controllers
■ Traction Drives
■ Low Loss System Retrofit
Hi-Reliability Chopper Switch Low V
KEY PARAMETERS
V
V
I
C
I
C(PK)
CES
CE(sat)
(typ) 2.6V
(max) 800A
(max) 1600A
2(C
)
2
1
7(C
)
1800V
4(E2)
1(E1)
CE(SA T)
IGBT Module
DS5365-3.0 January 2001
3(C1)
5(E
6(G
1
)
1
)
The Powerline range of high power modules includes dual
and single switch configurations covering voltages from 1200V to
3300V and currents up to 4800A.
The GP801DCM18 is an 1800V, n channel enhancement
mode, insulated gate bipolar transistor (IGBT) chopper module.
Designed with low V
module is of particular relevance in low to medium frequency
to minimise conduction losses, the
CE(SAT)
applications. The IGBT has a wide reverse bias safe operating
area (RBSOA) ensuring reliability in demanding applications.
This device is optimised for traction drives and other applications
requiring high thermal cycling capability.
The module incorporates an electrically isolated base plate
and low inductance construction enabling circuit designers to
optimise circuit layouts and utilise earthed heat sinks for safety.
ORDERING INFORMATION
Order As:
GP801DCM18
Note: When ordering, please use the complete part number.
Fig. 1 Dual switch circuit diagram
GPxxxDCxxx-xxx
Outline type code: D
(See Package Details for further information)
Fig. 2 Electrical connections - (not to scale)
Caution: This device is sensitive to electrostatic discharge. Users should follow ESD handling procedures. 1/10
www.dynexsemi.com
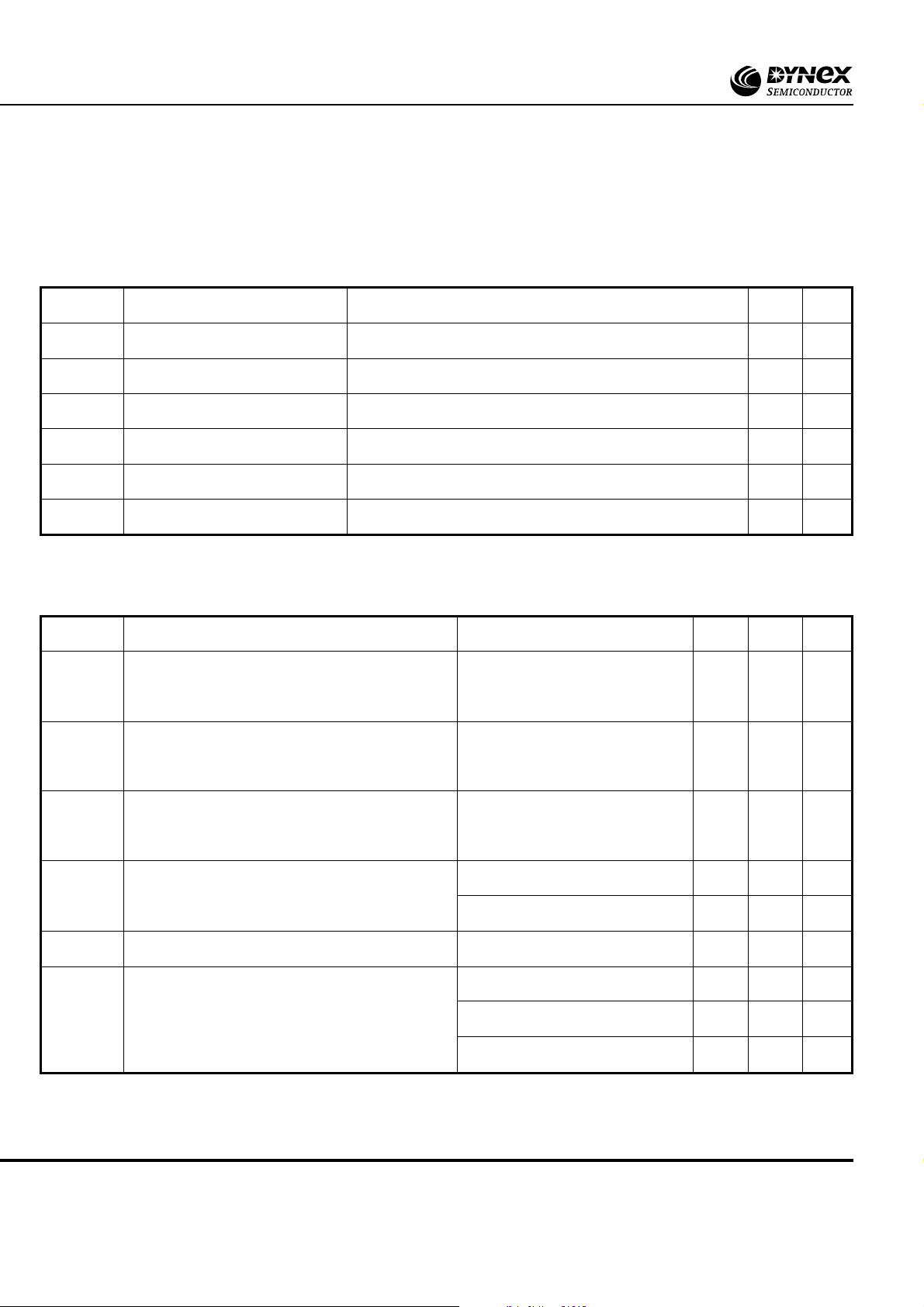
GP801DCM18
ABSOLUTE MAXIMUM RATINGS - PER ARM
Stresses above those listed under 'Absolute Maximum Ratings' may cause permanent damage to the device. In extreme
conditions, as with all semiconductors, this may include potentially hazardous rupture of the package. Appropriate safety
precautions should always be followed. Exposure to Absolute Maximum Ratings may affect device reliability.
T
= 25˚C unless stated otherwise
case
Symbol
V
CES
V
GES
I
C
I
C(PK)
P
max
V
isol
Collector-emitter voltage
Gate-emitter voltage
Continuous collector current
Peak collector current
Max. transistor power dissipation
Isolation voltage
Parameter
THERMAL AND MECHANICAL RATINGS
Symbol
R
th(j-c)
R
th(j-c)
Thermal resistance - transistor (per arm)
Thermal resistance - diode (per arm)
Parameter
Test Conditions
= 0V
V
GE
-
= 80˚C
T
case
1ms, T
T
case
= 110˚C
case
= 25˚C, Tj = 150˚C
Commoned terminals to base plate. AC RMS, 1 min, 50Hz
Test Conditions
Continuous dissipation -
junction to case
Continuous dissipation -
Min.
-
-
Max.
1800
±20
800
1600
6940
4000
Max.
18
40
Units
V
V
A
A
W
V
Units
˚C/kW
˚C/kW
junction to case
R
th(c-h)
Thermal resistance - case to heatsink (per module)
Mounting torque 5Nm
-
˚C/kW
8
(with mounting grease)
T
Junction temperature
j
Transistor
Diode
T
stg
-
Storage temperature range
Screw torque
Mounting - M6
-
Electrical connections - M4
Electrical connections - M8
-
-
–40
-
-
-
150
125
125
5
2
10
˚C
˚C
˚C
Nm
Nm
Nm
2/10 Caution: This device is sensitive to electrostatic discharge. Users should follow ESD handling procedures.
www.dynexsemi.com
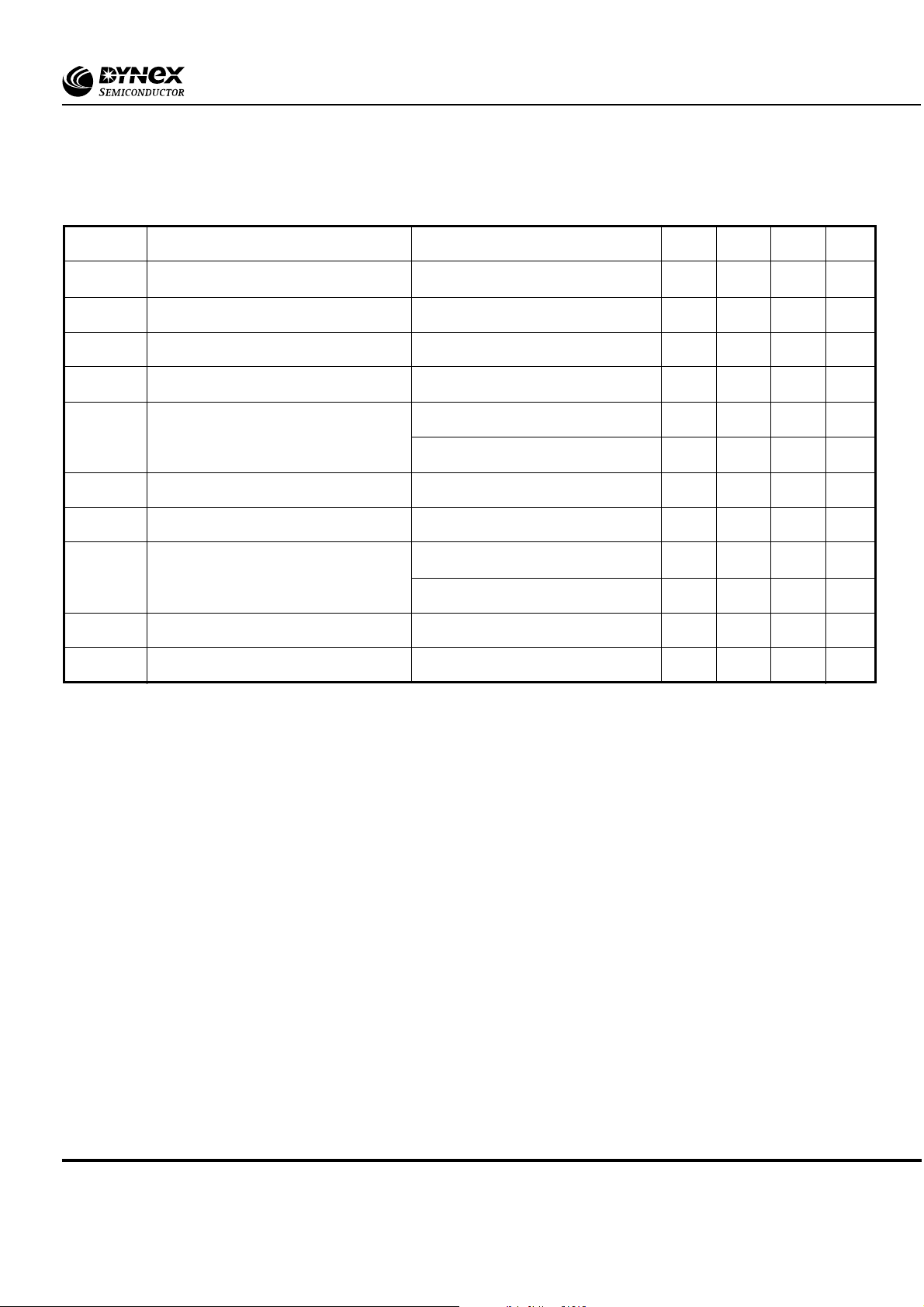
ELECTRICAL CHARACTERISTICS
T
= 25˚C unless stated otherwise.
case
GP801DCM18
Symbol
I
CES
I
GES
V
GE(TH)
V
CE(sat)
I
F
I
FM
V
F
C
ies
L
M
Parameter
Collector cut-off current
Gate leakage current
Gate threshold voltage
Collector-emitter saturation voltage
Diode forward current
Diode maximum forward current
Diode forward voltage
Input capacitance
Module inductance
Test Conditions
= 0V, VCE = V
V
GE
VGE = 0V, VCE = V
= ±20V, VCE = 0V
V
GE
= 40mA, VGE = V
I
C
CES
CES
, T
CE
VGE = 15V, IC = 800A
= 15V, IC = 800A, , T
V
GE
DC
= 1ms
t
p
= 800A
I
F
= 800A, T
I
F
= 25V, VGE = 0V, f = 1MHz
V
CE
= 125˚C
case
-
= 125˚C
case
case
= 125˚C
Min.
-
-
-
4.5
-
-
-
-
-
-
-
-
Typ.
-
-
-
5.5
2.6
3.3
-
-
2.2
2.3
90
20
Max.
1
25
4
6.5
3.2
4
800
1600
2.5
2.6
-
-
Units
mA
mA
µA
V
V
V
A
A
V
V
nF
nH
Caution: This device is sensitive to electrostatic discharge. Users should follow ESD handling procedures. 3/10
www.dynexsemi.com