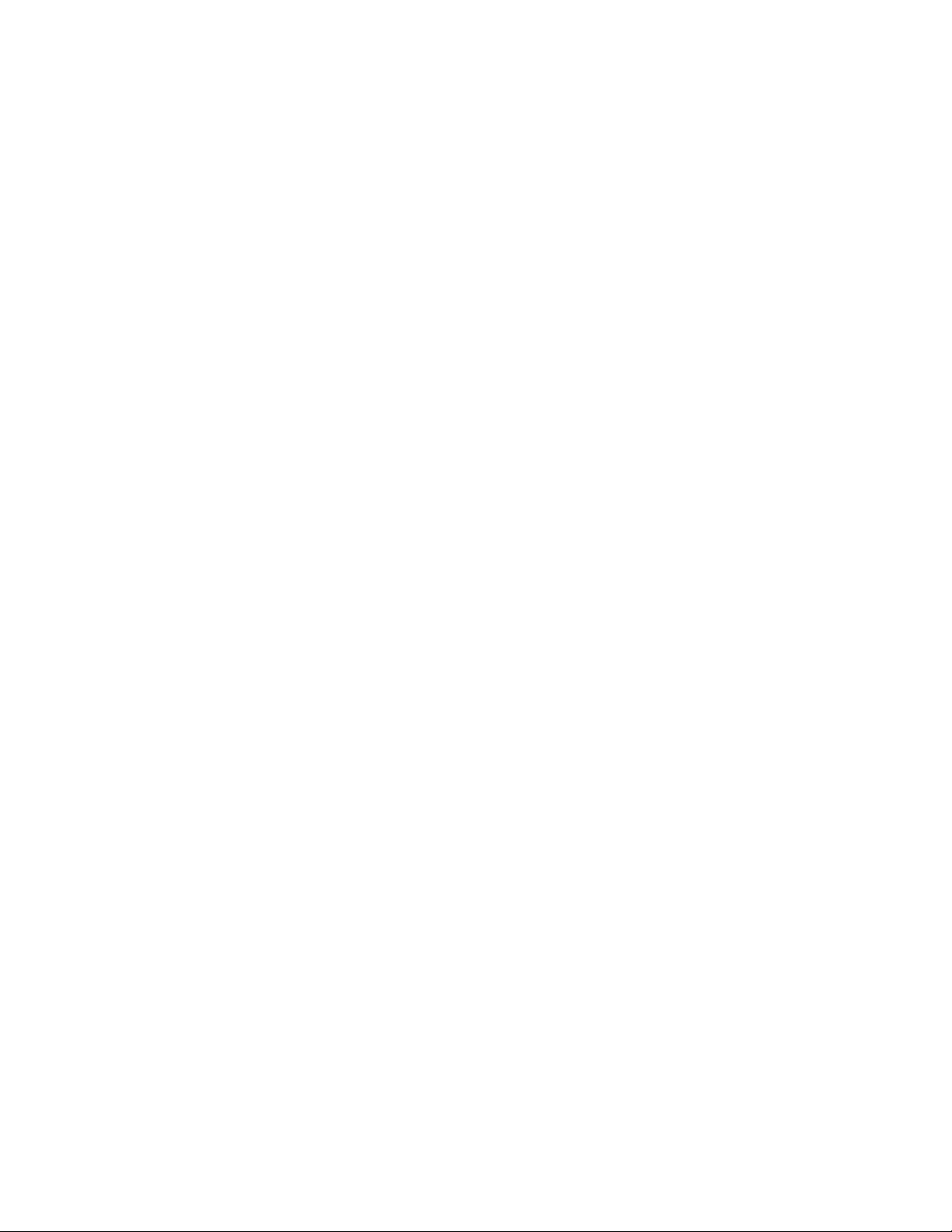
Series TFXD
Transit Time Ultrasonic Flow Meter, Clamp-on, Liquid, Single-Channel
Part 1. General
1.1 Scope
A. This section describes the requirements for an ultrasonic
flow measurement transmitter plus transducers.
B. Under this item, the contractor shall furnish and install the
flow measurement equipment and accessories as indicated
on the plans and as herein specified.
1.2 Submittals
A. The following information shall be included in the
submittal for this section:
1. Data sheets and catalog literature for
microprocessor-based transmitter and transducer.
2. Interconnection and dimensional drawings.
3. List of spare parts
Part 2. Products
2.1 Transit Time Ultrasonic Flow Meter
A. The transit time ultrasonic flow measurement system shall
be a microprocessor based transit time (time of flight)
measuring type providing an electronic output signal
proportional to the flow of liquid in closed piping systems
as may be required. It shall consist of a transmitter and one
transducer set connected by up to 990 feet [300 meters] of
cable.
B. Transducer:
1. Operating principle: Two ultrasonic transducers
function as both transmitters and receivers. Flow
measurement is made by transmitting acoustic
impulses alternately between two ultrasonic
transducers positioned lineally, a known distance
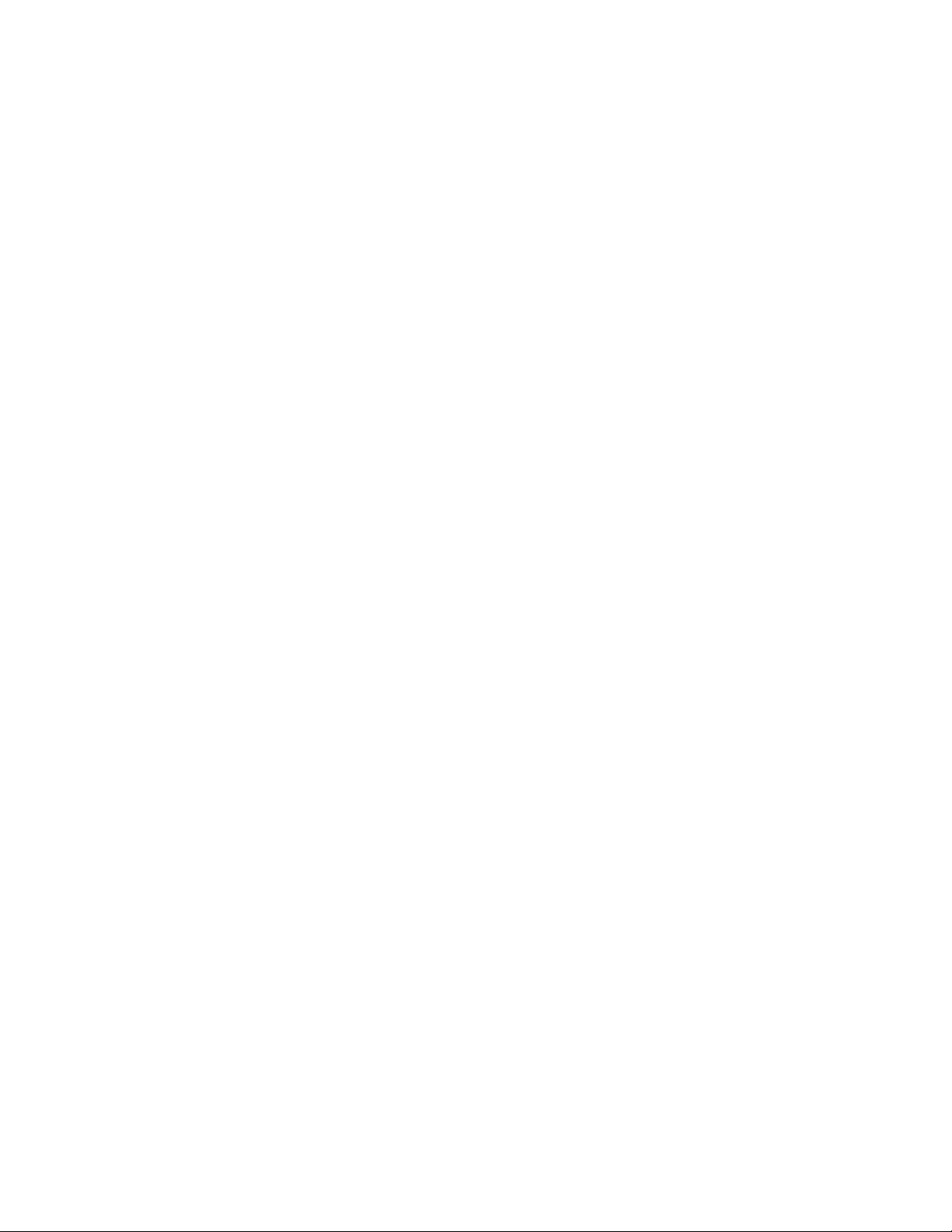
apart, on the outside pipe wall of a closed conduit.
Pulse travel time between the two transducers is
measured and the difference time calculated –
contrapropogation. Difference time is directly
proportional to fluid velocity, with a system
Reynolds Numbers correction factor applied.
2. Primary Sensor: The compression-mode acoustic
transducer shall contain a polarized Zirconium
crystal with impedance matched wave-guide.
a. Universal transducers shall operate on pipe
sizes ranging from 2” through 100” [50
through 2540 mm].
b. Small-pipe transducers shall operate on pipe
sizes from 1/2” through 2” [12 through 50
mm] and are specific to a pipe outside
diameter.
c. Transducer housing shall be PVC, CPVC,
Teflon, Ultem or Vespel.
d. Process connection shall be 1/2” NPT
e. Standard operating temperature shall be -40
o
to 250oF [-40° to +121° C]
f. Optional operating temperature shall be -40
o
to 400oF [-40° to +200° C]
C. Transmitter
1. Enclosure shall be NEMA 4X polycarbonate
2. Power supply shall be 115/230 VAC +/- 15% @
50/60 Hz or 9-28 VDC
3. Power consumption shall be 5 VA
4. Operating temperature shall be -40
o
C.
to 85
o
to 185o F [-40o
5. Input/output options: The transmitter shall accept
up to two input/output options to be installed.