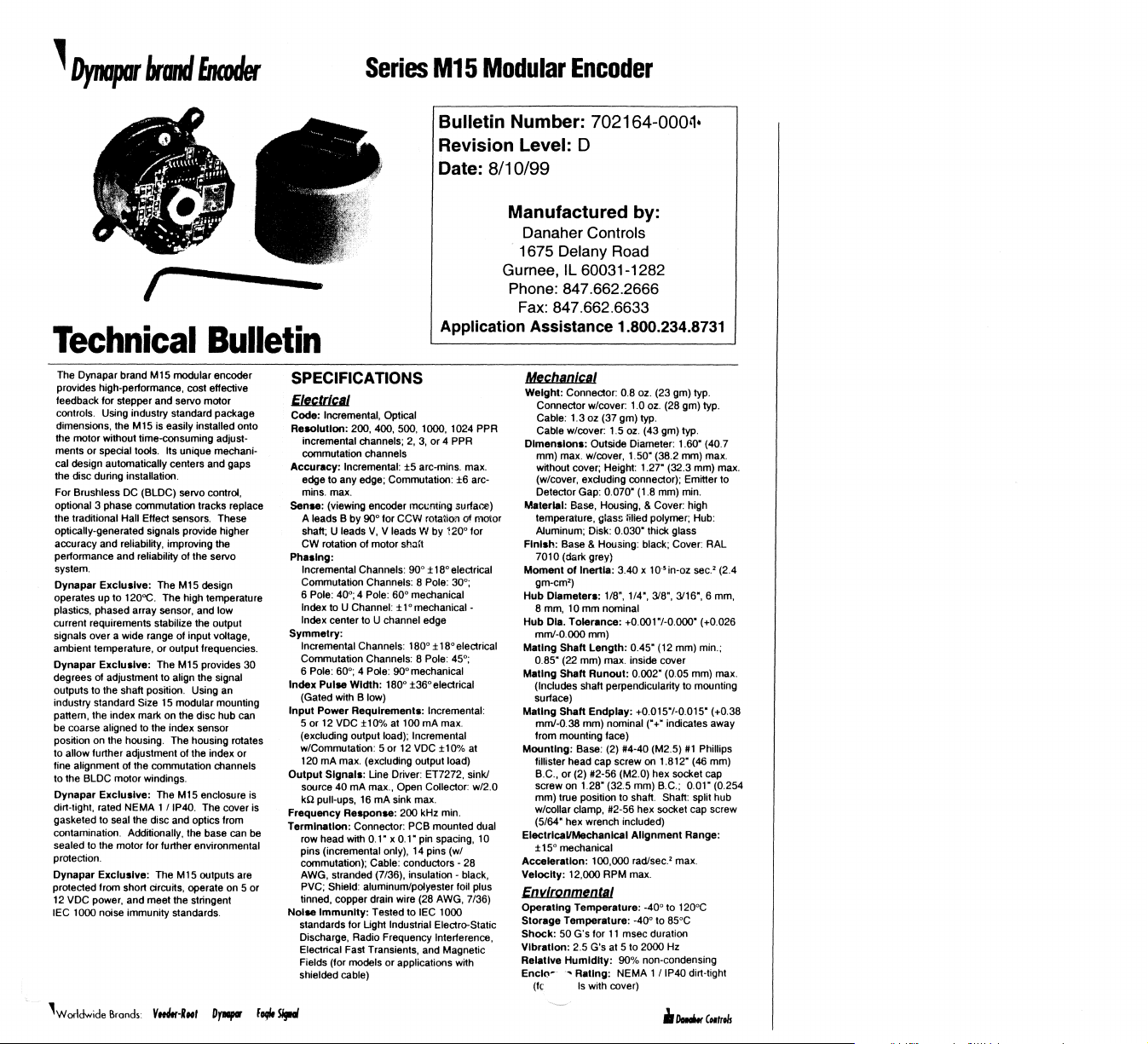
~
Dynapor
brand
Encoder
Series
M15
Modular
Encoder
f"'--~
Technical
The Dynapar brand M15 modular encoder
provides high-performance, cost effective
lor
leedback
controls.
dimensions, the M15 is easily
the motor without
ments or special tools. Its unique mechani·
cal
the disc during
For Brushless DC (BLOC) servo control,
optional 3 phase commutation tracks replace
the traditional
optically-generated signals provide higher
accuracy and reliability, improving the
performance and reliability
system.
Dynapar
operates up
plastics, phased array sensor, and low
current requirements stabilize the output
signals over a wide range
ambient temperature,
Dynapar
degrees
outputs to the shaft position.
industry standard
pattern, the index mark on the disc hub can
be coarse aligned
position on the
to
allow lurther adjustment
line alignment
to the
Dynapar
dirt-tight, rated NEMA t
gasketed to seal the disc and optics
contamination. Additionally, the base can
sealed to the motor
protection.
Dynapar
protected
12 VDC power, and meet the stringent
IEC 1000 noise immunity standards.
~Worldwide
stepper and servo motor
Using industry standard package
time·consuming adjust-
design automatically centers and gaps
installation.
Hall Effect sensors. These
Exclusive:
to
120"C. The high temperature
Exclusive:
01
adjustment to align the signal
Size 15 modular mounting
to
the index sensor
hOUSing.
01
the commutation channels
BLOC motor windings.
Exclusive:
lor
Exclusive:
Irom short circuits, operate on 5 or
Brand,
The
V_-R
Bulletin
installed onto
01
the servo
The
MIS
design
01
input Voltage,
or
output frequencies.
The
MIS
provides 30
Using an
The housing rotates
01
the index
or
The
MIS
enciosure is
IIP40.
The cover is
lrom
lurther environmental
MIS
outputs are
.. ' D,.
SPECIFICATIONS
Electrical
Code:
Incremental, Optical
Resolution:
Accuracy:
Sense: (viewing encoder mccnting surfa;:,;)
Phasing:
Symmetry:
Index
Input
Output
Frequency
Termination:
be
Noise
standards for Ught Industrial Electro-Static
Discharge, Radio Frequency Interference,
Electrical Fast Transients, and Magnetic
Fields
shielded cable)
r",
S/gHI
200, 400, 500, 1000, 1024 PPR
incremental channels;
commutation channels
Incremental:
edge to any edge; Commutation:
mins.
max.
A leads B by 90° for CCW rotation
shaft;
U leads
V,
V leads W by 120° for
CW rotation of motor
Incremental Channels: 90° ±
Commutation Channels: 8
6 Pole: 40°; 4 Pole:
Index to U Channel: ± 1 ° mechanical Index center to U channel edge
Incremental Channels: 1
Commutation Channels: 8
6 Pole: 60°; 4 Pole: 90° mechanical
Pulse
(Gated with
Power
5 or 12 VDC ±10%
(excluding output load);
wlCommutation: 5 or 12 VDC ±10% at
120 rnA max. (excluding output load)
Signals:
source
40 rnA max., Open Collector:
kQ pull-ups,
Response:
with 0.1· x 0.1· pin spacing,
row head
pins (incremental only), 14 pins (wi
commutation);
AWG, stranded
PVC; Shield: aluminum/polyester loil
tinned, copper drain wire (28 AWG, 7/36)
Immunity:
(lor models or applications with
sn3(t
60°
Width:
180° ±36°electrical
Blow)
Requirements:
at
Line Driver: ET7272, sink!
16
rnA sink max.
200 kHz min.
Connector: PCB mounted dual
Cable:
(7136),
Tested to IEC 1000
Bulletin Number:
Revision Level: D
Date: 8/10/99
Manufactured
Gurnee,
Phone: 847.662.2666
Application
2,
3,
or
4 PPR
±5
arc-mins. max.
±6
arc-
01
motor
18°
electrical
Pole: 30°;
mechanical
BO°
± 18° electrical
Pole: 45°;
Incremental:
100 rnA max.
Incremental
w12.0
10
conductors·
insulation - black,
28
piUS
702164-000~·
by:
Danaher Controls
1675 Delany Road
IL 60031-1282
Fax: 847.662.6633
Assistance
Mechanical
Weight:
Connector: 0.8 oz. (23 gm)
Connector w/cover: 1.0 oz. (28 gm)
Cable: 1.3 oz (37 gm)
Cable wlcover: 1.5 oz. (43 gm)
Dimension.:
mm) max. wlcover, 1.50" (38.2 mm) max.
without cover; Height:
(w/cover, excluding connector); Emitter to
Detector Gap:
Material: Base, Housing, & Cover: high
temperature,
Aluminum; Disk:
Finish:
Base & Housing: black; Cover: RAL
7010 (dark grey)
Moment
of
gm-cm')
Hub
Diameters:
mm,
8
Hub
Dla.
mm/-O.ooo
Mating
Shaft
0.85" (22 mm) max. inside cover
Mating
Shaft
(Includes
surface)
Mating
Shaft
mm/-O.38
from mounting
Mounting:
Iillister
B.C., or (2) #2-56
screw on 1.28" (32.5 mm) B.C.;
mm) true position to shaft. Shaft: split hub
wlcollar clamp, #2·56 hex socket cap screw
(5164"
hex wrench included)
Electrical/Mechanical
±15° mechanical
Acceleration:
Velocity:
EnvIronmental
Operating
Storage
Temperature:
Shock:
50
Vibration:
Humidity:
Relative
Enclo'
'Rating:
(Ie
1.800.234.8731
typo
typo
Outside Diameter: 1.60· (40.7
0.070" (1.8 mm) min.
glass1illed polymer; Hub:
0.030" thick glass
Inertia: 3.40 x 1
1/8", 114",318",3116",6 mm,
10 mm nominal
Tolerance:
head cap screw on 1.812" (46 mm)
12,000 RPM max.
2.5 G's
+0.001"1-0.000' (+0.026
mm)
Length:
0.45" (12 mm) min.;
Runout:
shalt perpendicularity to mounting
Endplay:
mm) nominal
lace)
Base: (2) #4-40 (M2.5)
(M2.0) hex socket cap
Alignment
100,000
Temperature:
G's
lor
11
msec duration
at
5 to 2000 Hz
90% non·condensing
NEMA 1
Is
with cover)
typo
1.27" (32.3 mm) max.
0"in-oz
sec.' (2.4
0.002" (0.05 mm) max.
+0.015"1·0.015" (+0.38
("
+"
indicates away
#1
0.01" (0.254
Range:
rad/sec'
max.
-40'
to 120"C
_40°
to 85"C
IIP40
dirt-tight
typo
Phillips
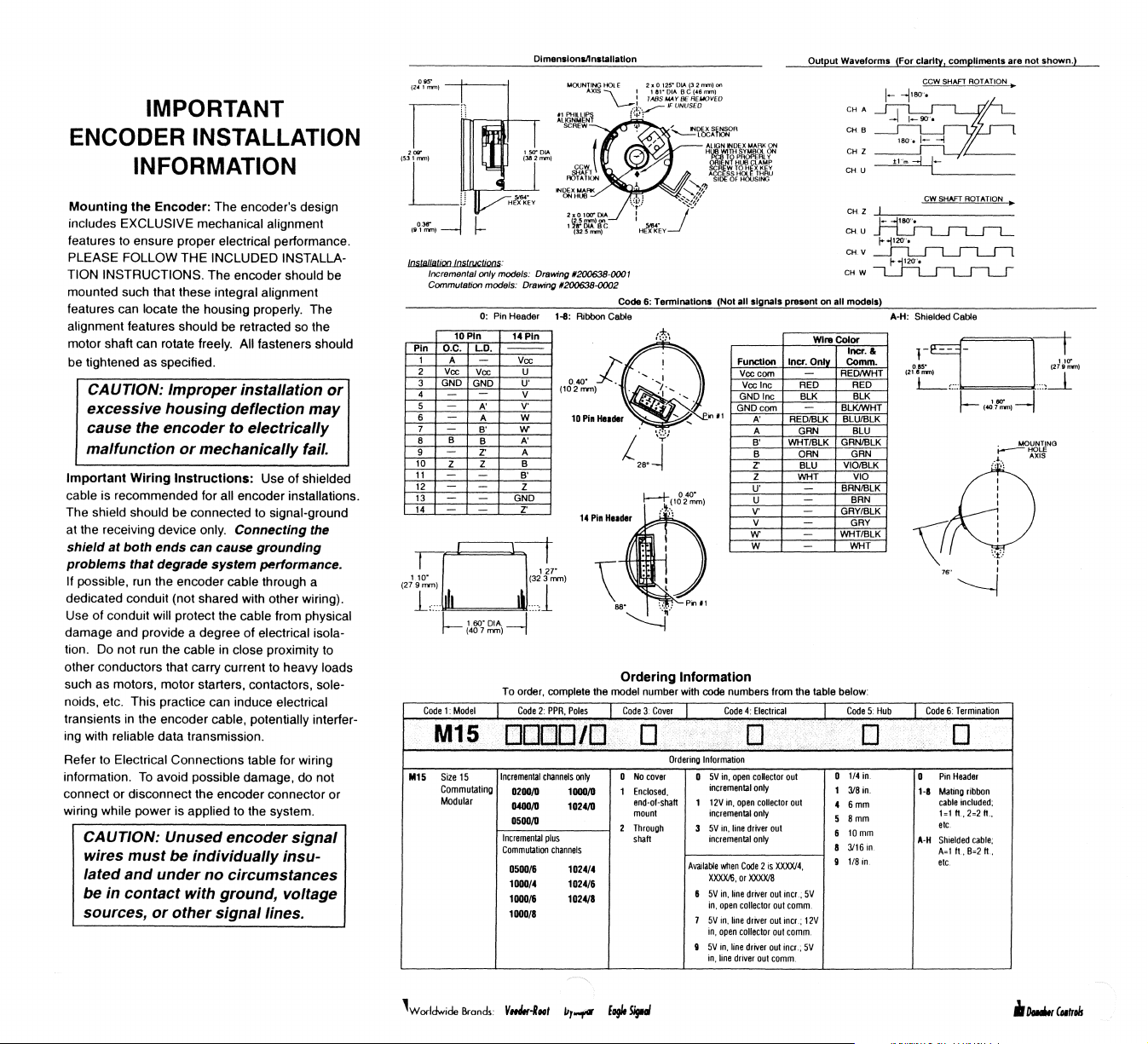
IMPORTANT
ENCODER INSTALLATION
INFORMATION
Mounting
includes
features to ensure proper electrical performance.
PLEASE FOLLOW THE INCLUDED INSTALLATION INSTRUCTIONS.
mounted such that these integral alignment
features can locate the housing properly. The
alignment features should
motor shaft can rotate freely. All fasteners should
be tightened as specified.
Important
cable is recommended for all encoder installations.
The shield should be connected to
at
shield
problems that degrade system pt!rformance.
If possible,
dedicated conduit (not shared with other wiring).
Use of conduit will protect the cable from physical
damage and provide a degree
tion. Do not run the
other conductors that carry current to heavy loads
such
noids, etc. This practice can induce electrical
transients
ing with reliable data transmission.
Refer
information.
connect or disconnect the encoder connector or
wiring while power is applied to the system.
the
Encoder:
The encoder's design
EXCLUSIVE mechanical alignment
The encoder should be
be
CAUTION:
excessive
cause the
housing
encoder
malfunction
Wiring
retracted
Improper
installation
deflection
to electrically
or
mechanically fail.
Instructions:
so
the
may
Use of shielded
Signal-ground
the receiving device only. Connecting the
at
both
ends can cause
run
the encoder cable through a
cable
as
motors, motor starters, contactors, sole-
in
the encoder cable, potentially interfer-
to
Electrical Connections table for wiring
To
avoid possible damage, do nol
CAUTION: Unused
wires
must
be
individually
lated
and
under
no
be
in
contact
sources,
with ground, voltage
or
other
grounding
of
electrical isola-
in
close proximity
encoder
signal
insu-
circumstances
signa/lines.
or
to
DlmensionsJInstallatJon
lL~~'b~~~
SCREW
/ostaUation Instructions:
Incremental only models: Drawing #200638-0001
Commutation models: Drawing #200638-0002
0:
Pin
Header 1-8: Ribbon Cable
10Pln
Pin
O.C. LD.
1 A
2
Vee
GND
3
4
5 A' V'
6
-
7
B
B
9 Z' A
10
Z
-
11
12
-
13
14
-
n
1,10·
O
(271~1
I
r-
Gode 1 Model
M15
M15
Size
15
Gommutating
Modular
14
Pin
-
Vee
Vee
U
U'
GND
A W
B' W
B
Z
-
- Z
-
-
V
A'
B
B'
GND
Z'
~
127"
(323rrm)
(102
::,1
1_60~
OlA. I
(407
mml
---j
To order, complete the model number with code numbers from the table below:
Gode 2 PPR,
0000/0
Incremental
channels
0200/11
0400/11
0500/11
Incremental
plus
Commutation
channels
0500/6
1000/4 1024/6
1000/6 1024/1
1000/8
Output
Waveforms
MOUNTING
HOl
F 2
)(
AXIS
\...-'
2.0100"
OtA
1~#BrJ:)rC
(32511Wn)
rrvn) .
0'4O"2~':~
10
Pin
Helder
0 125' DlA P 2 ranf
1111"
,
l...a5MAYBEREMOVED
,.l
..
~
[~I)':
Code
6:
Tennlnatlons
.~
.'.,
i 't/I
2B'~
I
.L
A.~'02mm)
• 1:
01,1.
Be
II-
UNUSED
........
" " "
0"'-
on
(46
nrn)
(Not
all
signals
present
on
all
WIre
Color
Functlon
Incr.
Only
Vcccom
Vee
Inc
GND Inc
GNOcom
A'
A
B'
B
Z'
Z
U'
U
V'
V
W
W
REDIBLK
WHT/BlK
REDlWHT
RED
BLK
BlKIWHT
BlU/BlK
GRN
GRNlBLK
ORN GRN
VIOlBlK
BlU
WHT
BRNlBlK
-
-
GRY/BlK
-
WHT/BlK
(For
clarity,
compliments
CCW SHAFT ROT ATION
CH A
~C=
CH, B
CH Z
~L
tim
==I
CH U
CH Z
CH.U
CH V
CH W
models)
Incr.&
Comm.
REO
BlK
BlU
VIO
BRN
GRY
WHT
1-
cw
SHAFT AOT ATION
A·H: Shielded Cable
'CA5'
are
not
shown.)
~
to
. MOUNTINO
76~
Poles
only
1000/11
1024/11
1024/4
Ordering
Gode 3 Gover
0
1
2
Information
I
0
Ordering
Information
No
cover
Enclosed,
end-ol-shan 1 12V
mount
Through
shaft
5V
0
incremental
incremental
5V
3
incremental
Availaille
XXXXIIi,
6
5V
in.
7
5V
in,
5V
9
in,
Gode
.
.......
in,
in,
in,
wilen
in,
open
in,
open
in,
hne
:.
open
open
line
Gode 2 is
or
line
collector
hne
colleclor
line
driver
4:
Electrical
0
coUector
only
collector
only
driver
only
XXXX/8
driver
driver
dnver
out
out
XXXXl4,
out
out
out
out
out
comm
out
out
incr.,
cornm
incr"
comm
incr.,
5V
12V
5V
Gode
0
1/4
in
0
3/8
in.
1
6mm
4
8mm
5
6 10mm
3/16
8
1/8
In
9
5.
Hub I Code
'.'
in
.. '
0
1-8
A-H
6:
Termination
0
Pin
Header
Mating
ribbon
cable
included:
1.1n,2.2n,
etc
Shielded
cable;
A.l
N,8.2N,
etc
~Worldwide
Brands
V"J,r-RHt
~,"'"
Eag/t
SiguI