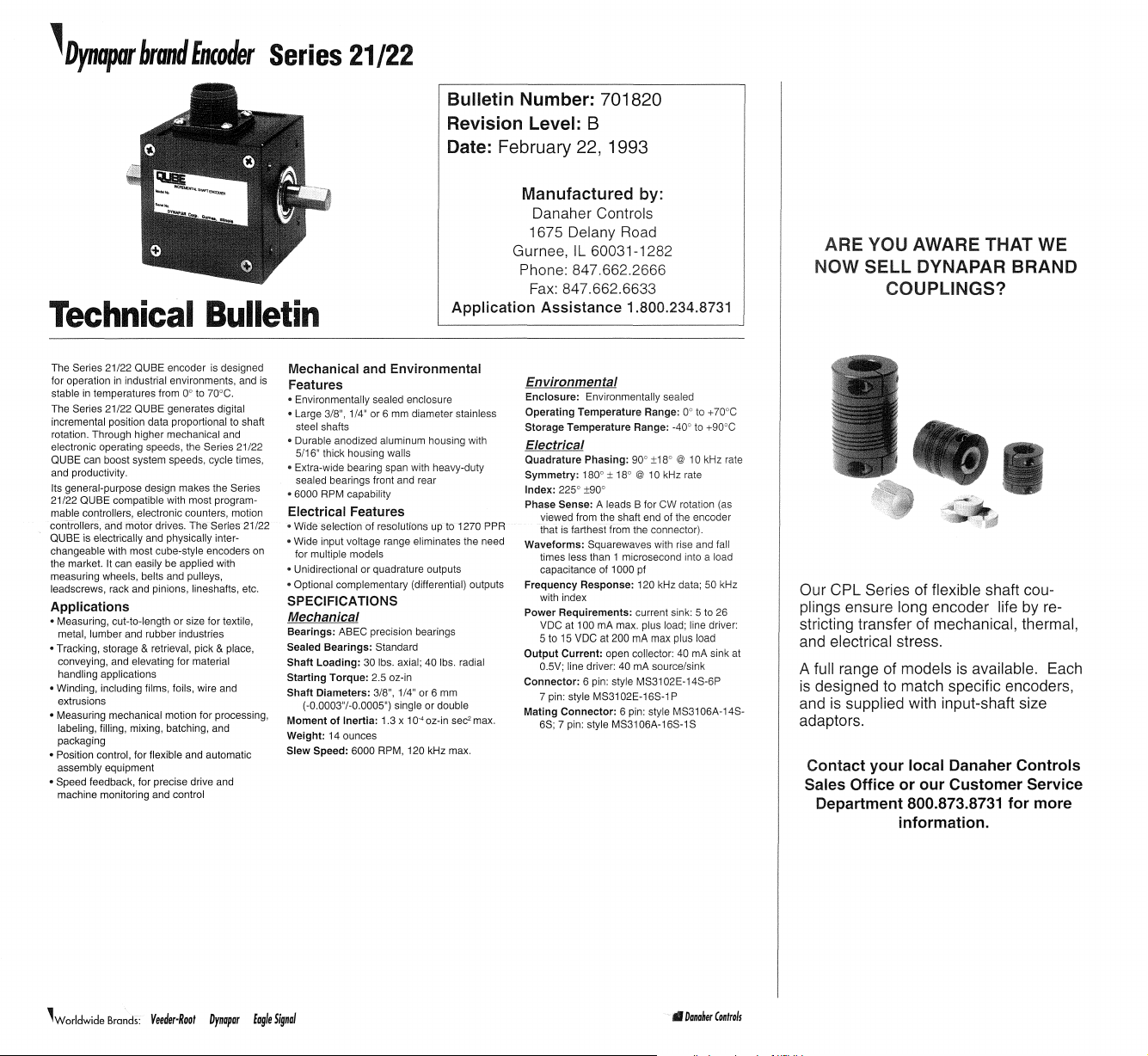
~Dynopor
brand
Encoder
Series
21/22
~
4It-,
o
-~
~
Technical
The Series 21/22 QUBE encoder
for operation
stable
The Series 21/22 QUBE generates digital
incremental position data proportional to shaft
rotation. Through higher mechanical and
electronic operating speeds, the Series 21/22
QUBE can boost system speeds, cycle times,
and productivity.
Its general-purpose design makes the Series
21/22 QUBE compatible with most programmable controllers, electronic counters, motion
con"Iroliers, and motor drives. The Series 21/22
QUBE is electrically and physically interchangeable with most cube-style encoders
the market. It can easily
measuring wheels, belts and pulleys,
leadscrews, rack and pinions, lineshafts, etc.
Applications
o Measuring, cut-to-Iength
metal, lumber and rubber industries
o Tracking, storage & retrieval, pick & place,
conveying, and elevating for material
handling applications
o Winding, including films, foils, wire and
extrusions
o Measuring mechanical motion for processing,
labeling, filling, mixing, batching, and
packaging
o Position control, for flexible and automatic
assembly equipment
o Speed feedback, for precise drive and
machine monitoring and control
in
industrial environments, and
in
temperatures from
0'
be
applied with
or
size for textile,
Iil
Bulletin
is
designed
to 70'C"
on
"~
Mechanical and Environmental
is
Features
o Environmentally sealed enclosure
o Large 3/8", 1/4"
steel shafts
o Durable anodized aluminum housing with
5/16" thick housing walls
o Extra-wide bearing span with heavy-duty
sealed bearings front and rear
o 6000 RPM capability
Electrical Features
o Wide selection
o Wide input voltage range eliminates the need
for multiple models
o Unidirectional
o Optional complementary (differential) outputs
SPECIFICATIONS
Mechanical
Bearings: ABEC precision bearings
Sealed Bearings: Standard
Shaft
Loading:
Starting Torque: 2.5 oz-in
Shaft
Diameters: 3/8", 1/4"
(-0.0003"/-0.0005") single or double
Moment
Weight: 14 ounces
Slew
Speed: 6000 RPM, 120 kHz max.
or
6 mm diameter stainless
of
resolutions up
or
quadrature outputs
30 Ibs. axial; 40 Ibs. radial
of
Inertia: 1.3 x
10"4
or
6 mm
oz-in
Bulletin
Number: 701820
Revision Level: B
Date: February 22, 1993
Manufactured
Danaher Controls
1675 Delany Road
Application
to
1270 PPR
sec'
max.
Gurnee,
Phone: 847.662"2666
IL
60031-1282
Fax:
847.662.6633
Assistance
1.800.234.8731
Environmental
Enclosure:
Operating Temperature Range:
Storage Temperature Range:
Electrical
Quadrature Phasing:
Symmetry:
Index:
Phase Sense: A leads B for CW rotation (as
Waveforms: Squarewaves with rise and fall
Frequency Response: 120 kHz data; 50 kHz
Power
Output
Connector:
Mating
Environmentally sealed
90'
180' ± 18' @ 10kHz
225'
±90'
viewed Irom the shaft end
"that
is farthest from the connector).
times less than 1 microsecond into a load
capacitance of 1000
with index
Requirements: current sink: 5 to 26
VDC at 100 mA max. plus load; line driver:
5 to 15 VDC at 200 mA max plus load
Current: open collector: 40 mA sink at
0.5V; line driver: 40 mA source/sink
6 pin: style MS3102E-148-6P
7 pin: style M831 02E-168-1 P
Connector:
68; 7 pin: style M83106A-168-18
6 pin: style MS3106A-148-
by:
0'
-40'
±18' @ 10kHz
rate
01
the encoder
pi
to
to
+70'C
+90'C
rate
ARE YOU AWARE THAT WE
NOW SELL DYNAPAR BRAND
COUPLINGS?
Our CPL Series of flexible shaft couplings ensure long encoder life by restricting transfer of
and electrical stress.
A full range of models is available. Each
is designed to match specific encoders,
supplied with input-shaft size
and is
adaptors.
Contact
Sales
your
Office
Department
mechanical, thermal,
local Danaher Controls
or
our
Customer Service
800.873.8731
for
more
information.
~Worldwide
Brands:
Veeder·Roof
Dynapor
Eagle
Signal
"
,.
DanaiJfr
Controls
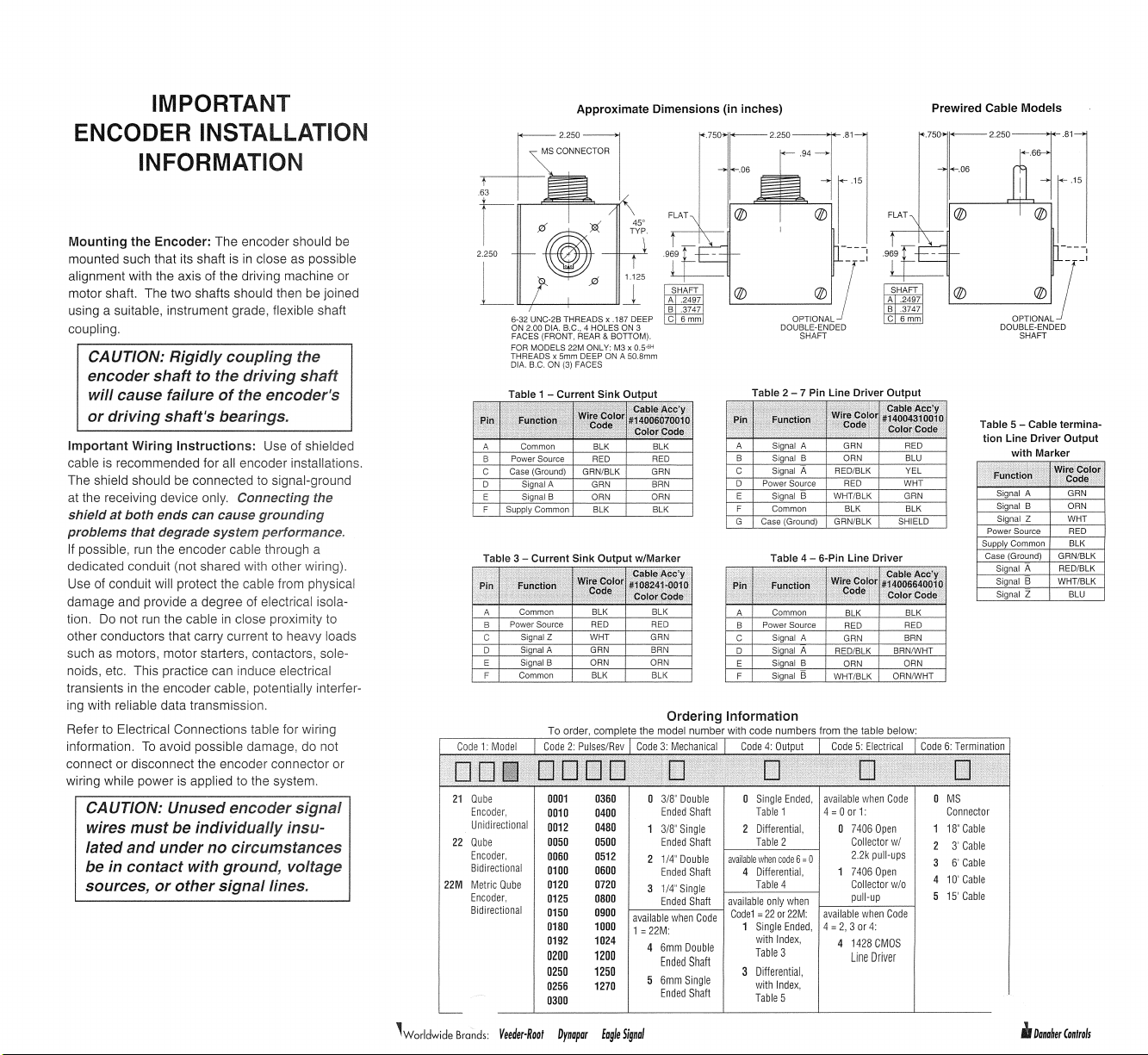
IMPORTANT
ENCODER INSTALLATION
INFORMATION
Approximate Dimensions (in inches)
Prewired Cable Models
Mounting
mounted such that its shaft is
alignment with the axis of the driving machine or
motor shaft. The two shafts should then
using a suitable, instrument grade, flexible shaft
coupling.
the
Encoder:
The encoder should
in
close as possible
be
be
joined
CAUTION: Rigidly coupling the
encoder shaft
will cause failure
or
driving shaft's bearings.
Important
cable is recommended for all encoder installations.
The shield should
at the receiving device only.
shield
problems
If possible, run the encoder cable through a
dedicated conduit (not shared with other wiring).
Use of conduit will protect the cable from physical
damage and provide a degree of electrical isolation.
other conductors that carry current to heavy loads
such as motors, motor starters, contactors, solenoids, etc. This practice can induce electrical
transients
ing with reliable data transmission.
Refer to Electrical Connections table for wiring
information.
connect or disconnect the encoder connector or
wiring while power is applied to the system.
Wiring
at
both
that
Do
not run the cable in close proximity to
in
the encoder cable, potentially interfer-
To
to the driving
of
the encoder's
Instructions:
be
connected to signal-ground
Connecting the
ends can cause
degrade system performance.
avoid possible damage, do not
shaft
Use of shielded
grounding
CAUTION: Unused encoder signal
must
wires
lated
be individually insu-
and
under no circumstances
be in contact with ground, voltage
sources,
or
other
signal
lines.
III
i
6-32 UNC-2B
ON
FACES
FOR
THREADS x 5mm
D[A.
Table 3 - Current Sink Output wIMarker
21
Qube
Encoder,
Unidirectional
22
Qube
Encoder,
Bidirectional
22M
Metric
Qube
Encoder,
Bidirectional
THREADS
2.00
D[A.
B.C., 4 HOLES
(FRONT, REAR & BOTTOM).
MODELS
22M
ONLY: M3 x
DEEP
B.C.
ON
(3)
FACES
0001
0010 0400
0012 0480
0050 0500
0060
0100 0600
0120 0720
0125 0800
0150 0900
0180
0192
0200
0250
0256
0300
1.125
!!~
x .187 DEEP
ON
3
O.5.fiH
ON
A 50.Bmm
0360
0512
available
1000
1 =
1024
1200
1250
1270
~"l~m~i'"
9rE
SHAFT
A .2497
B .3747
CI6mm
o
3/8"
Double
Ended
Shaft
1
3/8"
Single
Ended
Shaft
2
1/4"
Double
Ended
Shaft
3
1/4"
Single
Ended
Shaft
when
Code
22M:
4
6mm
Double
Ended
Shaft
5
6mm
Single
Ended
Shaft
(jJ) (jJ)
OPTIONAL C 6 mm OPT10NAL
DOUBLE·ENDED DOUBLE·ENDED
SHAFT SHAFT
Table 4 - 6-Pin Line Driver
o
Single
Ended,
Table
1 4 = 0
2
Differential,
Table
4
Code1
1
3
2
when
code
Differential,
Table
4
only
when
=220r22M:
Single
Ended,
with
Index,
Table
3
Differential,
with
Index,
Table
5
6 = 0
available
available
19
----
7-[
available
when
or
1:
o
7406
Collectorw/
2.2k
1
7406
Collector
pull·up
available
when
4 =
2, 3 or
4
1428
Line
Open
pull·ups
Open
4:
CMOS
Driver
'If'''~i',,
rE
ASH~:;7
B .3747
Code
w/o
Code
(jJ) (jJ)
Table 5 - Cable termina-
tion Line Driver Output
o
MS
Connector
1
18"
Cable
3'
Cable
2
6'
Cable
3
4
10'
Cable
5
15'
Cable
----I
7-[
with Marker
~Worldwide
Brands:
Veeder-RDIJ/
Oynapor
EagleS~nal
if
Danairer
Con/lois