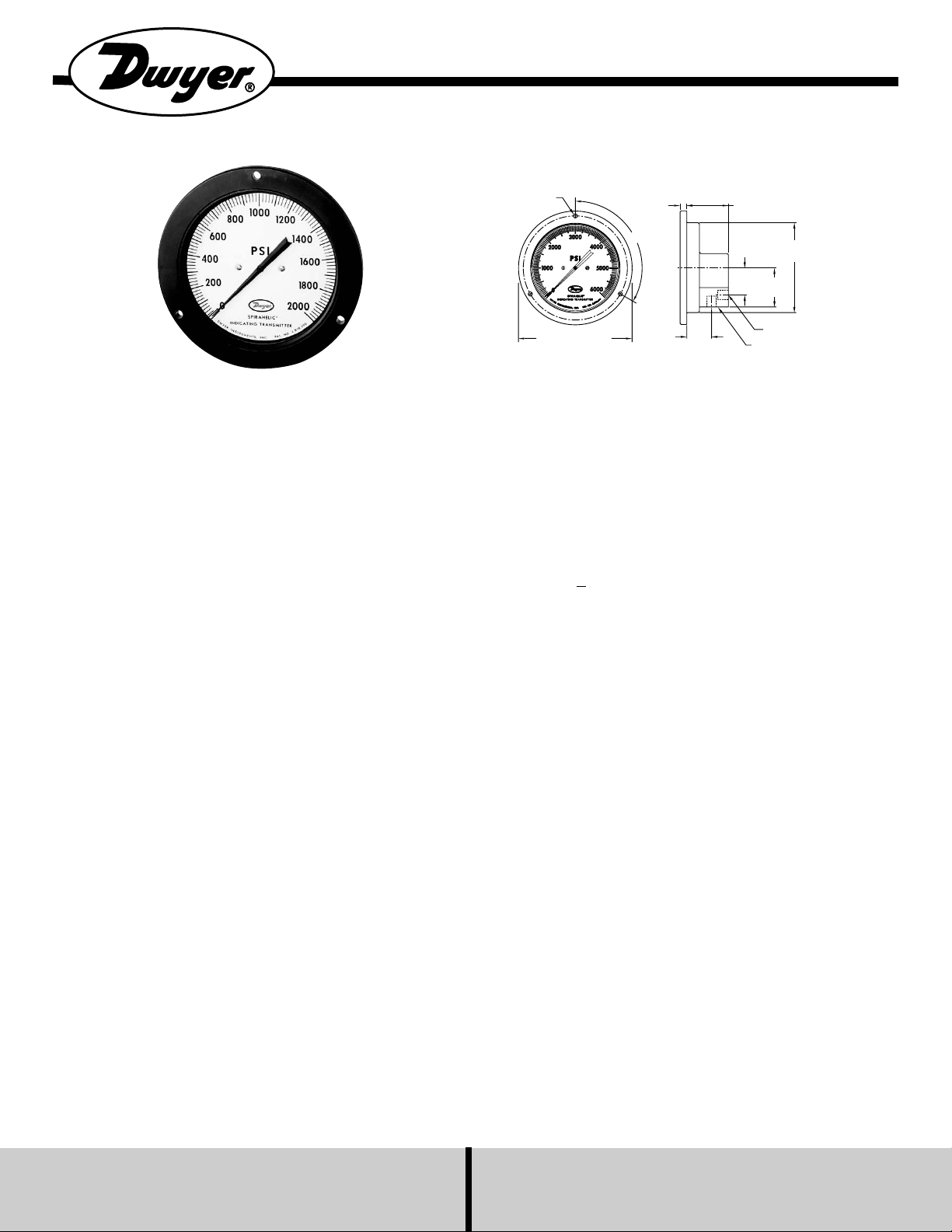
Series 7000 Spirahelic
23/64
[9.13]
120° TYP
Ø5-7/8 [149.23]
(3) Ø7/32 [5.56] MOUNTING
HOLES EQUALLY SPACED ON
A 5-3/8 [136.53] BOLT CIRCLE
2-5/32
[54.76]
1-9/32
[32.54]
1 [25.40] SQUARE
CONNECTION BLOCK
1/4 FEMALE NPT
PRESSURE CONNECTION
TYP 2 PLACES
1-13/32
[35.71]
2-1/32
[51.59]
Ø4-41/64
[117.8]
®
Pressure Indicating Transmitter
Specifications - Installation and Operating Instructions
Bulletin A-33-A
The Dwyer Series 7000 Spirahelic®Pressure
Indicating Transmitter provides local indication on a
large, easy-to-read analog scale while also converting that
pressure into a standard two wire 4-20 mA output signal.
Positive pressure of compatible gases or liquids is measured with 1/2% of full scale accuracy. The gage employs a
triple helix Bourdon tube movement with direct drive design
to reduce friction and mass for exceptional responsiveness,
repeatability and accuracy. Because there are no gears,
springs, linkages or other complicated mechanisms, wear is
practically eliminated. The electrical output signal is produced by a piezoresistive pressure sensor mounted on the
pressure block. The pressure block also includes an integral
filter plug to protect the gage interior from dirt and other
particulates. Safety is assured with a solid front case design
and a rear blowout hole.
INSTALLATION
1. Select a location free from excessive vibration where the
temperature limits of 20° to 120°F (-6.7° to 49°C) will not be
exceeded. The mounting surface should be vertical to
SPECIFICATIONS
GAGE SPECIFICATIONS
Service: Compatible gases & liquids
Wetted Materials: Inconel®X-750 Bourdon Tube, Type
316L SS connection.
Housing: Black polycarbonate case and clear acrylic
cover.
Accuracy: Grade 2A (0.5% F.S.).
Stability: + 1% F.S./yr.
Pressure Limit: 150% of full scale. Gage will maintain
its specifications for overpressures up to 150% maximum
range. Normal operation should be between 25% and
75% of full scale.
Temperature Limits: 20 to 120°F (-6.67 to 48.9°C).
Size: 4 -1/2˝ dial face (114.3 mm), Design conforms to
ASME B40.1.
Process Connections: Two 1/4˝ female NPT field selectable back or bottom connection.
Weight: 17.1 oz. (581 g).
match the position in which all standard gages are calibrated. Avoid locations in direct sunlight which may cause
accelerated discoloration of the clear acrylic lens or where
exposure to oil mist or other airborne vapors could likewise
result in lens damage. Make sure that the case relief area on
the rear is not obstructed. This hole is designed to direct
pressure rearward in the event of failure or the Bourdon tube
element. See complete safety recommendations in this bulletin.
2. Cut a 4.94˝ (125 mm) mounting hole and drill (3) 7/32˝
(5.56 mm) bolt holes on a 5.38˝ (137 mm) bolt circle as
shown in drawing above. Attach gage to panel with (3) 3/16˝
bolts of appropriate length.
TRANSMITTER SPECIFICATIONS
Accuracy: 0.5% F.S.
Temperature Limits: 20 to 120°F (-6.67 to 48.9°C).
Thermal Effect: ±0.025% F.S. /°F (0.045% F.S./C°).
Power Requirements: 10-35 VDC (2 wire).
Output Signal: 4-20 mA DC.
Zero & Span Adjustments: Externally accessible
potentiometers.
Loop Resistance: DC, 0-1250 ohms.
Current Consumption: DC, 38 mA max.
Electrical Connections: Screw Terminals.
Mounting Orientation: Vertical.
Agency Approvals: CE.
DWYER INSTRUMENTS, INC.
P.O. Box 373 • Michigan City, IN 46361-0373, U.S.A. Fax: 219/872-9057 e-mail: info@dwyer-inst.com
Phone: 219/879-8000 www.dwyer-inst.com
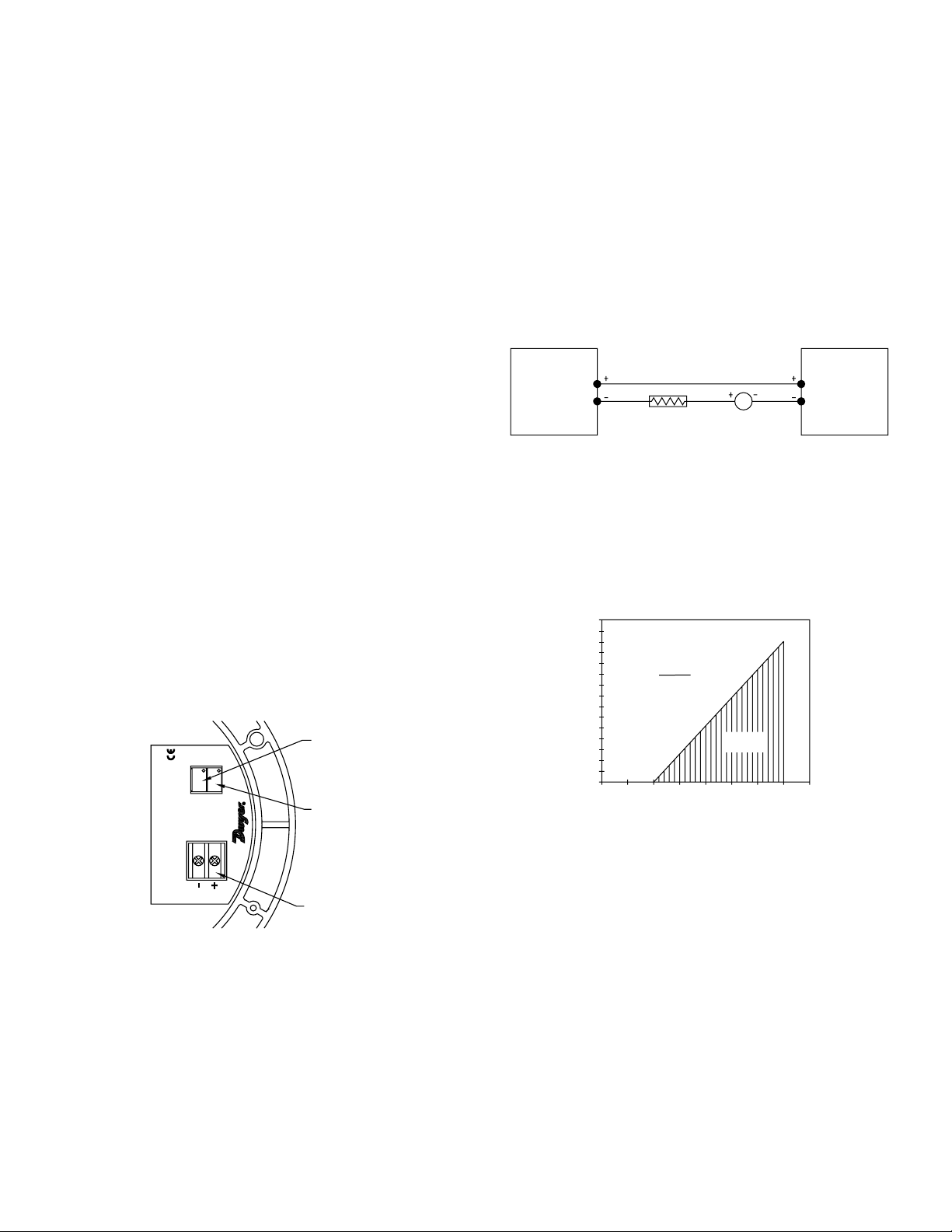
Bulletin A-33-A
MAXIMUM VALUE (1300 OHMS)
1400
1300
1200
1100
1000
900
800
700
600
500
400
300
200
100
50
0
5
10
15 20 25
30 35
40
OPERATING
REGION
RECEIVER RESISTANCE (OHMS)
R L MAX =
Vps-10.0
20mA DC
7000 SERIES
INDICATING
PRESSURE
TRANSMITTER
POWER
SUPPLY
10-35 VDC
mA
RECEIVER
page 2
3. Two 1/4˝ female NPT pressure connections are furnished
to allow a choice of vertical or horizontal piping. The unused
port should be plugged. Use a minimal amount of thread
sealant. Too much could block the internal pressure passage.
CAUTION: When installing fittings or pipe always us a second wrench on the 1˝ pressure block DO NOT allow torque
to be transmitted from block to the gage case.
PNEUMATIC CALIBRATION TESTER
Use a dead weight tester or certified test gage with .125%
or better accuracy. The test gage range should be comparable to the range of the Spirahelic®Pressure Indicating
Transmitter being checked. Connect the lines from the two
instruments to a tee and the third line from the tee to a controllable source of pressure. Apply pressure slowly so pressure equalizes throughout the system. Compare readings, if
gage being tested is found to need calibration, return it,
freight prepaid to the factory.
ELECTRICAL CONNECTIONS
CAUTION: Do not exceed specified supply voltage ratings.
Permanent damage not covered by warranty will result. This
unit is not designed for 120 or 240 volt AC line operation.
Electrical connections to the Series 7000 Spirahelic
Pressure Indicating Transmitter are made at the rear of the
pressure gage. Feed stripped and tinned leads to the terminal block screws shown below, refer to Figure A for locations of the terminal block, span and zero adjustments.
2-Wire Operation - A external power supply delivering 1035 VDC with minimum current capability of 40 mA DC (per
transmitter), must be used to power the control loop. See
Figure B for connection of the power supply, transmitter,
and receiver. The range of the appropriate receiver load
resistance (RL) for the DC power supply voltage available is
expressed by the formula and graph in Figure C. Shielded
two wire cable is recommended for control loop wiring. if
grounding is required use negative side of control loop after
receiver see Figure B.
®
Fig. B
7000
SPIRAHELIC INDICATING TRANSMITTER
MODEL:
RANGE:
SPAN ADJUST
ZERO
SPAN
ZERO ADJUST
TERMINAL BLOCK
PRESSURE RANGING
Each standard Series 7000 Spirahelic
Fig. C
®
Pressure Indicating
Transmitter is factory calibrated to produce a 4 mA output
signal at zero pressure and a 20 mA signal at full scale. Use
Fig. A
the following procedure to check or adjust the output signal
calibration.
1. With the unit connected to its companion receiver and
power supply, an accurate milliammeter should be inserted in
series with the current loop. A controllable pressure source
capable of achieving the necessary full scale pressure
should be connected to the pressure port of the transmitter
and teed to an accurate pressure gage or manometer. The
instrument should be calibrated in the same position in
which it will be used. Vertical mounting is recommended.

The following material is excerpted from a standard
titled Gauges-Pressure Indicating Dial Type-
Elastic Element (ANSI/ASME B40.1-1985) as published by The American Society of Mechanical
Engineers, 345 East 47th St. New York, NY 10017.
This information is furnished to assist the user of Dwyer
®
Spirahelic
for the intended application and conditions.
4 SAFETY
4.1 Scope
mation to guide users, suppliers, and manufacturers
toward minimizing the hazards that could result from
misuse or misapplication of pressure gauges with elastic elements. The user should become familiar with all
sections of this Standard, as all aspects of safety cannot be covered in this Section. Consult the manufacturer or supplier for advice whenever there is uncertainty about the safe application of a pressure gauge.
4.2 General Discussion
ning and careful selection and installation of gauges
into a pressure system. The user should inform the
supplier of all conditions pertinent to the application
and environment so that the supplier can recommend
the most suitable gauge for the application.
pressure gauges has been excellent. Injury to personnel and damage to property have been minimal. In
most instances, the cause of failure has been misuse or
misapplication.
gauges is subjected to high internal stresses, and
applications exist where the possibility of catastrophic
failure is present. Pressure regulators, chemical
(diaphragm) seals, pulsation dampers or snubbers,
syphons, and other similar items, are available for the
use in these potentially hazardous systems. The hazard
potential increases at higher operating pressure.
tially hazardous and must be carefully evaluated:
atoms
flammable mixture or medium
dentally applied
could result in hazardous internal contamination or
where lower pressure gauges could be installed in
higher pressure systems
uids or gases)
media having known or uncertain corrosive effects or
known to be radioactive, random or unique destructive
phenomena can occur. In such cases the user should
always furnish the supplier or manufacturer with information relative to the application and solicit his advice
prior to installation of the gauge.
can cause pressure element failure with very violent
effects, even to the point of completely disintegrating or
melting the pressure gauge. Violent effects are also
produced when failure occurs due to:
heat sources
caused by heat sources such as fires
ed to produce violent effects.
are four basic modes of elastic element failure, as follows.
pressure induced stress generally occurs from the
inside to the outside along a highly stressed edge
radius, appearing as a small crack that propagates
along the edge radius. Such failures are usually more
critical with compressed gas media than with liquid
media.
slowly so case pressure buildup can be averted by providing pressure relief openings in the gauge case.
However, in high pressure elastic elements where the
yield strength approaches the ultimate strength of the
element material, fatigue failure may resemble explosive failure.
gages in properly evaluating their suitability
This Section of the Standard presents certain infor-
4.2.1 Adequate safety results from intelligent plan-
4.2.2 The history of safety with respect to m use of
4.2.3 The pressure sensing element in most
4.2.4 The following systems are considered poten-
(a) compressed gas systems
(b) oxygen systems
(c) systems containing hydrogen or free hydrogen
(d) corrosive fluid systems (gas and liquid)
(e) pressure systems containing any explosive or
(f) steam systems
(g) nonsteady pressure systems
(h) systems where high overpressure could be acci-
(i) systems wherein interchangeability of gauges
(j) systems containing radioactive or toxic fluids (liq-
(k) systems installed in a hazardous environment
4.2.5 When gauges are to be used in contact with
4.2.6 Fire and explosions within a pressure system
(a) hydrogen enbrittlement
(b) contamination of a compressed gas
(c) formation of acetylides
(d) weakening of soft solder joints by steam or other
(e) weakening of soft soldered or silver brazed joints
(f) corrosion
(g) fatigue
(h) mechanical shock
(i) excessive vibration
Failure in a compressed gas system can be expect-
4.2.7 Modes of Elastic Element Failure. There
4.2.7.1 Fatigue Failure. Fatigue failure caused by
Fatigue cracks usually release the media fluid
A restrictor placed in the gauge pressure inlet will
reduce pressure surges and restrict fluid flow into the
partially open Bourdon tube.
4.2.7.2 Overpressure Failure. Overpressure fail-
ure is caused by the application of internal pressure
greater than the rated limits of the elastic element and
can occur when a low pressure gauge is installed in a
high pressure port of system. The effects of overpressure failure, usually more critical in compressed gas
systems than in liquid filled systems, are unpredictable
and may cause parts to be propelled in any direction.
Cases with pressure relief openings will not always
retain expelled parts.
Placing a restrictor in the pressure gauge inlet will
not reduce the immediate effect of failure, but will help
control flow of escaping fluid following rupture and
reduce potential of secondary effects.
It is generally accepted that solid front cases with
pressure relief back will reduce the possibility of parts
being projected forward in the event of failure.
The window alone will not provide adequate protection against internal case pressure buildup, and can
be the most hazardous component.
4.2.7.3 Corrosion Failure. Corrosion failure
occurs when the elastic element has been weakened
through the attack by corrosive chemicals present in
either the media inside or the environment outside it.
Failure may occur as pinhole leakage through the elements walls or early fatigue failure due to stress cracking brought about by chemical deterioration or embrittlement of the material.
A chemical (diaphragm) seal should be considered
for use with pressure media that may have a corrosive
effect on the elastic element.
4.2.7.4 Explosive Failure. Explosive failure is
caused by the release of explosive energy generated
by a chemical reaction such as can result with adiabatic compression of oxygen occurs in the presence of
hydrocarbons. It is generally accepted that there is no
known means of predicting the magnitude or effects of
this type of failure. For this mode of failure, a solid wall
or partition between the elastic element and the window will not necessarily prevent parts being projected
forward.
4.2.8 Pressure Connection. See recommenda-
tions in para. 3.3.4.
4.3 Safety Recommendations.
4.3.1 Operating Pressure. The pressure gauge
selected should have a full scale pressure such that the
operating pressure occurs in the middle half (25 to
75%) of the scale. The full scale pressure of the gauge
selected should be approximately two times the intended operating pressure.
Should it be necessary for the operating pressure to
exceed 75% of full scale, contact the supplier for recommendations.
This does not apply to test, retarded, or suppressed scale gauges.
4.3.2 Use of Gauges Near Zero Pressure. The
use of gauges near zero pressure is not recommended
because the accuracy tolerance may be a large percentage of the applied pressure. If, for example, a
0/100 psi Grade B gauge is used to measure 6 psi, the
accuracy of measurement will be ±50% of the applied
pressure. In addition, the scale of a gauge is often laid
out with takeup, which can result in further inaccuracies when measuring pressures that are a small percentage of the gauge span.
For the same reasons, gauges should not be used
for the purpose of indicating that the pressure in a tank,
autoclave, or other similar unit has been completely
exhausted to atmospheric pressure. Depending on the
accuracy and the span of the gauge and the possibility that takeup is incorporated at the beginning of the
scale, hazardous pressure may remain in the tank even
though the gauge is indicating zero pressure. A venting
device must be used to completely reduce the pressure before unlocking covers, removing fittings, or performing other similar activities.
4.3.3 Compatibility With the Pressure Medium.
The elastic element is generally a thin walled member,
which of necessity operates under high stress conditions and must, therefore, be carefully selected for
compatibility with the pressure medium being measured. None of the common element materials is
impervious to every type of chemical attack. The
potential for corrosive attack is established by many
factors, including the concentration, temperature, and
contamination of the medium. The user should inform
the gauge supplier of the installation conditions so that
the appropriate element materials can be selected.
4.3.4 In addition to the factors discussed above,
the capability of a pressure element is influenced by the
design, materials, and fabrication of the joints between
its parts.
Common methods of joining are soft soldering, silver brazing, and welding. Joints can be affected by
temperature, stress, and corrosive media. Where application questions arise, these factors should be considered and discussed by the user and manufacturer.
4.3.5 Some special applications require that the pressure element assembly have a high degree of leakage
integrity. Special arrangement should be made
between manufacturer and used to assure that the
allowable leakage rate is not exceeded.
4.3.6 Cases
4.3.6.1 Cases, Solid Front. It is generally
accepted that a solid front case per para. 3.3.1 will
reduce the possibility of parts being projected forward
in the event of elastic element assembly failure. An
exception is explosive failure of the elastic element
assembly.
4.3.6.2 Cases, Liquid Filled. It has been gener-
al practice to use glycerine or silicone filling liquids.
However, these fluids may not be suitable for all applications. They should be avoided where strong oxidizing agents including, but not limited to, oxygen, chlorine, nitric acid, and hydrogen peroxide are involved. In
the presence of oxidizing agents, potential hazard can
result from chemical reaction, ignition, or explosion.
Completely fluorinated or chlorinated fluids, or both,
may be more suitable for such applications.
The user shall furnish detailed information relative to
the application of gauges having liquid filled cases and
solicit the advice of the gauge supplier prior to installation.
Consideration should also be given to the instantaneous hydraulic effect that may be created by one of
the modes of failure outlined in para. 4.2.7. The
hydraulic effect due to pressure element failure could
cause the window to be projected forward even when
a case having a solid front is employed.
4.3.7 Restrictor. Placing a restrictor between the
pressure connection and the elastic element will not
reduce the immediate effect of failure, but will help control flow of escaping fluid following rupture and reduce
the potential of secondary effects.
4.3.8 Specific Service Conditions
4.3.8.1 Specific applications for pressure gauges
exist where hazards are known. In many instances,
requirements for design, construction, and use of
gauges for these applications are specified by state or
federal agencies or Underwriters Laboratories, Inc.
Some of these specific service gauges are listed below.
The list is not intended to include all types, and the user
should always advise the supplier of all application
details.
4.3.8.2 Acetylene Gauges. A gauge designed
to indicate acetylene pressure. It shall be constructed
using materials that are compatible with commercially
available acetylene. The gauge may bear the inscrip-
indicate ammonia pressure and to withstand the corrosive effects of ammonia. The gauge may bear the
inscription AMMONIA on the dial. It may also include
the equivalent saturation temperature scale markings
on the dial.
indicate the pressure of corrosive or high viscosity fluids, or both. The primary material(s) in contact with the
pressure medium may be identified on the dial. It may
be equipped with a chemical (diaphragm) seal, pulsation damper, or pressure relief device, or a combination. These devices help to minimize potential damage
to personnel and property in the event of gauge failure.
They may, however, also reduce accuracy of sensitivity,
or both.
indicate oxygen pressure. Cleanliness shall comply with
Level IV (see Section 5). The dial shall be clearly
marked with a universal symbol and/or USE NO OIL in
red color (see para. 6.1.2.1).
4.4 Reuse of Pressure Gauges
moved from one application to another. Should it be
necessary, however, the following must be considered.
quences of incompatibility can range from contamination to explosive failure. For example, moving an oil service gauge to oxygen service can result in explosive
failure.
involve pressure pulsation that has expended most of
the gauge life, resulting in early fatigue in the second
installation.
ment assembly in the first installation may be sufficient
to cause early failure in the second installation.
gauge, all guidelines covered in the Standard relative to
application of gauges should be followed in the same
manner as when a new gauge is selected.
tion ACETYLENE on the dial.
4.3.8.3 Ammonia Gauge. A gauge designed to
4.3.8.4 Chemical Gauge. A gauge designed to
4.3.8.5 Oxygen Gauge. A gauge designed to
It is not recommended that pressure gauges be
4.4.1 Chemical Compatibility. The conse-
4.4.2 Partial Fatigue. The first installation may
4.4.3 Corrosion. Corrosion of the pressure ele-
4.4.4 Other Considerations. When reusing a
©Copyright 2003 Dwyer Instruments, Inc. Printed in U.S.A. 4/03 FR# 17-440819-00 Rev. 1
DWYER INSTRUMENTS, INC.
Phone: 219/879-8000 www.dwyer-inst.com
P.O. Box 373 • Michigan City, IN 46361-0373, U.S.A. Fax: 219/872-9057 e-mail: info@dwyer-inst.com