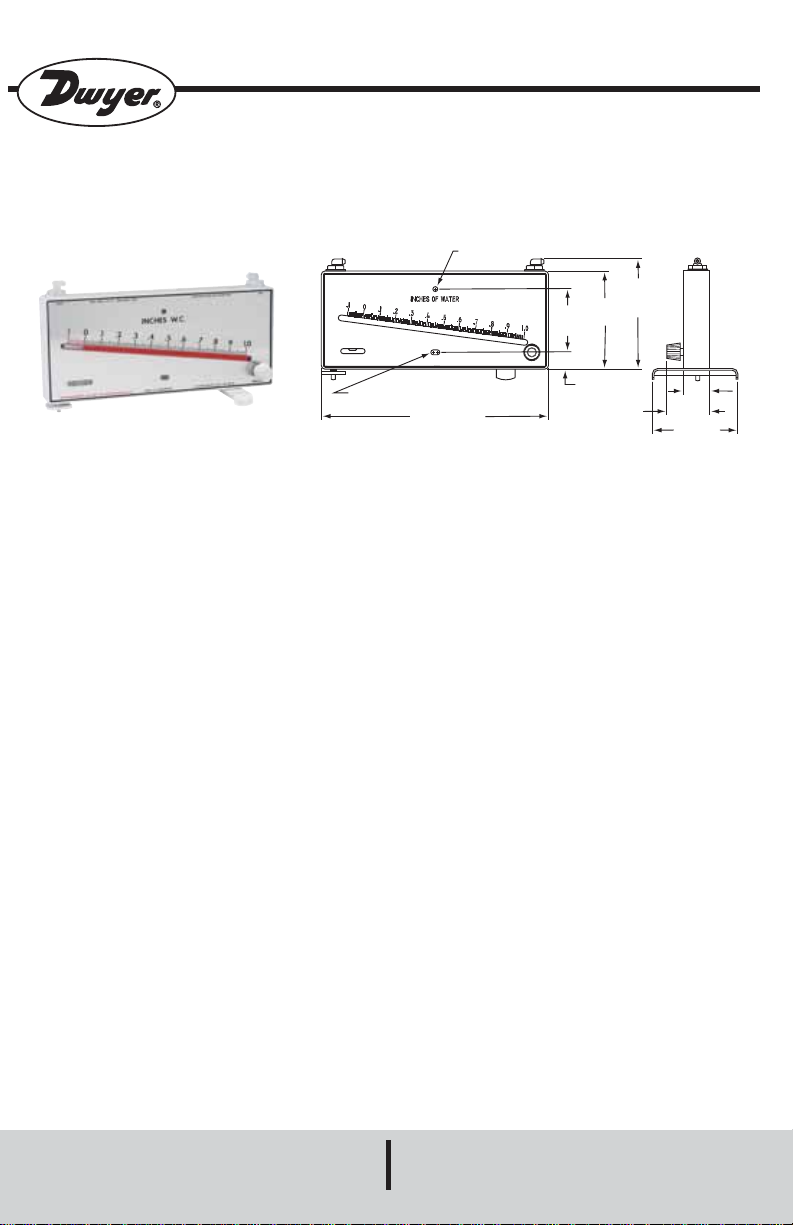
15/64 [5.95] x 13/32 [10.32] MOUNTING SLOT
10-5/8 [269.88]
5-5/16
[134.95]
MAX
4-5/8
[117.48]
2-31/32
[75.41]
25/32
[19.84]
Ø15/64 [5.95] MOUNTING HOLE
1-1/4
[31.75]
2-1/4 [57.15]
MAX
4 [101.60]
MARK II MODEL 40
Bulletin D-59
Mark II - Model 40 Molded Plastic Manometers
Installation and Operating Instructions
Dwyer Mark II - Model 40 Molded
Plastic Manometers are ideally suited
for air velocity and air filter gage applications at minimal cost. These inclined
manometers provide linear calibration
and excellent resolution throughout their
ranges. They are capable of pressure
line spaced 2-31/32˝ apart. Install the
gage with the self-tapping screws provided,
turning the screws down snug but not tight.
Adjust the position of the gage until the bubble is centered in the spirit level. Tighten the
mounting screws, checking to be sure the
instrument remained level, and re-level
as necessary.
measurements above and below
atmospheric, as well as differential pressure measurements.
INSTALLATION
Mount the
Stationary Applications:
Mark II manometer on a convenient vertical
surface. The installation should not be
exposed to strong chlorine atmospheres or
solvents such as benzene, acetone, carbon
tetrachloride, etc. The instrument is suitable
for total internal pressures of up to 15 psi
(100 kPa) and ambient temperatures of
150°F (65°C). DO NOT EXCEED THESE
LIMITS. At the mounting location selected,
drill two 9/64˝ diameter holes on a vertical
DWYER INSTRUMENTS, INC.
P.O. BOX 373 Fax: 219/872-9057 e-mail: info@dwyer-inst.com
MICHIGAN CITY, INDIANA 46361,U.S.A
SPECIFICA T IONS
Accuracy
: ±3% of full scale.
Maximum Internal Working Pressure:
15 psi (100 kPa).
Maximum Working Temperature: 150°F
(65°C).
Scale Length: Approx. 8-1/4˝ (21 cm).
Weight: 10 oz (283.49 g).
Accessories: 3/4 oz. gage oil, mounting
screws, 1/8˝ NPT tubing adapters, washers, nuts, red and green pointer flags, (2)
4-1/2 ft.
Phone: 219/879-8000 www.dwyer-inst.com
lengths 3/16˝ I. D. vinyl tubing.

Portable Applications: For portable
use, a molded plastic swing-away foot and
leveling screw are provided. Referring to the
picture on the first page of this bulletin,
secure the swing-away foot to the bottom of
the gage, using the plastic screw in the
tapped hole on the right-hand side. Install
the plastic leveling screw in the tapped hole
on the bottom left side of the manometer. In
use, the swing-away foot is positioned perpendicular to the gage. With the manometer
in operating position, the leveling screw is
adjusted until the bubble is centered in the
spirit level. For storage, the swing-away foot
can be rotated to a position in line with the
gage body.
FILLING
T urn the zero adjust knob fully counter clockwise until it stops; then turn it clockwise
approximately four full turns so as to center
the adjustment to allow room for adjusting
either side of zero. Unscrew the entire low
pressure (right) shut-off connection fitting. A
3/4˝ wrench is required. Also, remove the
cork, disc, and “O” ring. Vent the left connector by turning the elbow 1 - 2 turns
counterclockwise. Slowly fill gage with fluid
provided until fluid rises in the indicating
tube to the vicinity of zero on the scale.
Nearly all the oil provided will be required to
fill the gage. Replace the cork, disc, “O” ring
and the low-pressure shut-off
connection fitting.
OPERATION
The Model 40 manometer is provided with
convenient shut-off tubing connections to
prevent loss of oil when transporting the
gage. To use the gage, turn each barbed
tubing connection counterclockwise 1-2
turns from the closed (fully clockwise) position. Rotate the zero adjustment for an exact
zero reading and the gage is ready for use.
In stationary installations, these steps need
only be performed upon initial installation. In
portable use, each time the gage is used the
connections must be opened, the gage leveled and zeroed; prior to storage, the gage
connections must be closed.
Pressure Connection: Two 4-1/2˝
lengths of plastic tubing are included with
the gage along with two adapters for connection of the tubing to 1/8˝ NPT fittings or
sheet metal ducts. The tubing from the high
pressure pickup should be connected to the
high pressure (left) barbed connection at the
top of the gage. The tubing from the low
pressure pickup should be connected to the
low pressure (right) barbed fitting. Stick-on
red and green arrows are provided to indicate the appropriate range of readings for
the particular application. The 1/8˝ NPT
tubing adapters can be used as static pressure sensors in sheet metal ducts by drilling
a 7/16˝ diameter hole in the duct and
mounting the adapter in the hole, placing
one of the washers on each side of the duct
wall and securing the 1/8˝ NPT nut.
CAUTION
USE .826 SPECIFIC GRAVITY RED
GAGE OIL FOR MODEL #’S 40-1, 40-1AV, 40-250 Pa, 40-250 Pa-AV, and 4025 mm. Use 1.910 SPECIFIC GRAVITY
BLUE GAGE OIL FOR MODEL #’S 412, 41-2-AV, 41-600 PA, 41-60 mm.
TYPICAL APPLICATIONS
Draft Gage: Run iron pipe, 1/8˝ or larg-
er in size, from the source of the draft to a
point within 4-1/2˝ of the manometer.
Provide a means for periodic clean-out to
remove any soot accumulation. Using one
of the lengths of tubing provided, make the
connection from the pipe to the low pressure (right) fitting on the gage.