
TVFS
R
EMOVAL
C
LEARANCE
G
IN
O
UT
A
B
D
C
C
ONNECTIONS
E
F
Bulletin F-22
Series TVF Total View Industrial Flowmeters
Specifications - Installation and Operating Instructions
A
9
1
.36
5.22
C
B
.81
2
.53
4
D
.68
2
4.00
.71
3
5.70
E
1.35
2.48
F
2.72
3.95
G
3.00
5.00
emale NPT
F
3/4˝
1-1/2˝
Material
T. STL.
S
T. STL.
S
The Series TVF Total View Industrial Flowmeters are
economically priced, tough, simple and accurate meters for
water, oils, coolants, compressed gases and other industrial
applications. The flowmeters have a full-scale accuracy of ±2%
and can be disassembled quickly without the meter being
removed from the pipeline for easy cleaning. The TVFS is
constructed of T-316 stainless steel and features polysulphone
sight tubes. The Series Total View Industrial Flowmeters are
available with standard 3/4˝ and 1-1/2˝ female NPT connections.
The easy to read flowmeters provide 360° rotation of scale on
plastic sight tube models.
SAFETY PRECAUTIONS
Personnel safety should be considered before pressurizing and
operating the system. There are numerous possibilities for error
in system operation and maintenance as well as component
installation. Because human eyes must necessarily come into
close proximity with the flowmeter to read it, it is recommended
that safety shielding be used with the meter along with safety
glasses. The panel mount kit (available for most standard
models) also provides shielding. Another protective measure is
to use a sheet of transparent, high-impact material in a broad
area in front of the meter. If hazardous, toxic, or flammable fluids
are being metered, recommended safeguards should include
methods to protect personnel from splash or rebound. A method
of quick, safe removal of dangerous fluids should also be
included.
SPECIFICATIONS
Service: Compatible gases or liquids.
Wetted Materials: Body: T-316 SS; O-rings: Buna-N; Sight
Tube: Polysulfone.
Temperature Limits: See “Operating Limits” Table.
Pressure Limits: See “Operating Limits” Table.
Accuracy: ±2% FS.
Repeatability: ±1/4% of indicated flow rate.
Process Connections: 3/4˝ and 1-1/2˝ female NPT.
Scale Length: 3.2˝ (8 cm) for 3/4˝ NPT connection, 5.2˝ (13 cm)
for 1-1/2˝ NPT connection.
Weight: 4 lbs (1.8 kg) for 3/4˝, and 12 lbs (5.5 kg) for 1-1/2˝.
RECOMMENDED PIPING: Series TVF Flowmeters generally
have no special straight run or other piping requirements. Inlet
piping should be the same size as the meter connection. Some
effect on meter accuracy may occur at high flow velocities if inlet
piping guidelines are violated. Please refer to the table on the
next page. When installing on different size pipe, use standard
pipe adapters and come into the meter inlet with a nipple 8
diameters long of the same size for greatest accuracy. Control
valves should be mounted on the outlet side of the meter. The
use of a three valve manifold around the meter is suggested (per
Figures 2 & 3) as it allows uninterrupted process flow while the
meter is being cleaned.
DWYER INSTRUMENTS, INC.
P.O. BOX 373 • MICHIGAN CITY, INDIANA 46361, U.S.A. Fax: 219/872-9057 e-mail: info@dwyer-inst.com
Phone: 219/879-8000 www.dwyer-inst.com

MAXIMUM FLOWS (WITHOUT EFFECTING ACCURACY)
TVF FLOWMETER
MAIN
PROCESS
LINE
BY-P ASS
VALVE
FLOW
FIGURE 2: TYPICAL INSTALLATION-
VERTICAL LINE FOR LIQUID, GAS, OR VAPOR
F
SHUT-OFF
VALVES (2)
FIGURE 3: TYPICAL INSTALLATION-
HORIZONTAL LINE FOR LIQUID, GAS, OR VAPOR
SHUT-OFF
VALVES (2)
TVF FLOWMETER
BY-P ASS VALVE
FLOW
MAIN PROCESS LINE
FOR UNDERSIZED PIPES CONNECTED DIRECTLY TO MEM FLOWMETER INLETS
PIPE NPS
1/4
3/8
1/2
3/4
1
-1/4
1
1-1/2
2
2-1/2
3
4
6
DATA
2
(ID)
0.132
0.243
0.387
0.679
1.100
1.904
.592
2
4.272
6.096
9.413
16.209
36.784
MAX. *
GPM LIQ.
1.72
2.98
4.74
8.31
13.47
23.32
1.74
3
52.29
74.56
115.2
198.4
450.0
MAX. SCFM AIR @ †
ATMOS
0.864
1.59
2.53
4.44
7.20
12.5
7.0
1
28.0
39.9
61.6
106
241
50 PSIG
3.80
7.00
11.1
19.5
31.7
58.8
74.6
23
1
176
271
467
1059
100 PSIG
6.74
12.4
19.8
34.7
56.1
97.2
32
1
218
311
480
827
1878
200 PSIG
12.6
23.2
37.2
64.9
05
1
182
248
408
582
804
1549
3514
* Data per Cameron Hydraulic Data. Based on 5 FPS max. liquid velocity having no effect
on Series TVF Flowmeter accuracy if the inlet pipe is smaller than the meter connections.
† SCFM = 0.445 x (psig + 14.7) x (ID)2. Based on 20 FPS max. air velocity having no effect
on Series TVF Flowmeter accuracy if the inlet pipe is smaller than the meter connections.
OPERATING LIMITS FOR SERIES TVF FLOWMETERS
Maximum Non-Shock Working Pressure, PSIG @ °F (bar @ °C)
BODY SIZE AND
DESCRIPTION
3/4˝ Stainless and
Polysulfone
1-1/2˝ Stainless and
Polysulfone
* Operating limits given are based on water or air. For more severe service, corrosives, and
other media and/or environmental factors, an additional correction factor down-rating these
limits may be required. Limits are based on testing and practical experience. Possible
70ºF
(21ºC)
300
(20.6)
180
(12.4)
extreme application conditions cannot be foreseen. Thus, data is offered only as a guide. It
in no way constitutes a specific recommendation or warranty expressed or implied. The
operating limits should not be exceeded under any circumstances. If there is any doubt
regarding the safe operating limit for a specific application, please consult the factory prior
to installation and pressurization of the flow device.
80ºF
(26ºC)
300
(20.6)
180
(12.4)
100ºF
(37ºC)
300
(20.6)
180
(12.4)
120ºF
(48ºC)
300
(20.6)
180
(12.4)
140ºF
(60ºC)
300
(20.6)
180
(12.4)
200ºF
(93ºC)
300
(20.6)
180
(12.4)
250ºF
(121ºC)
250
(17.2)
145
(10.0)
300ºF
(148ºC)
115
(7.9)
70
(4.8)
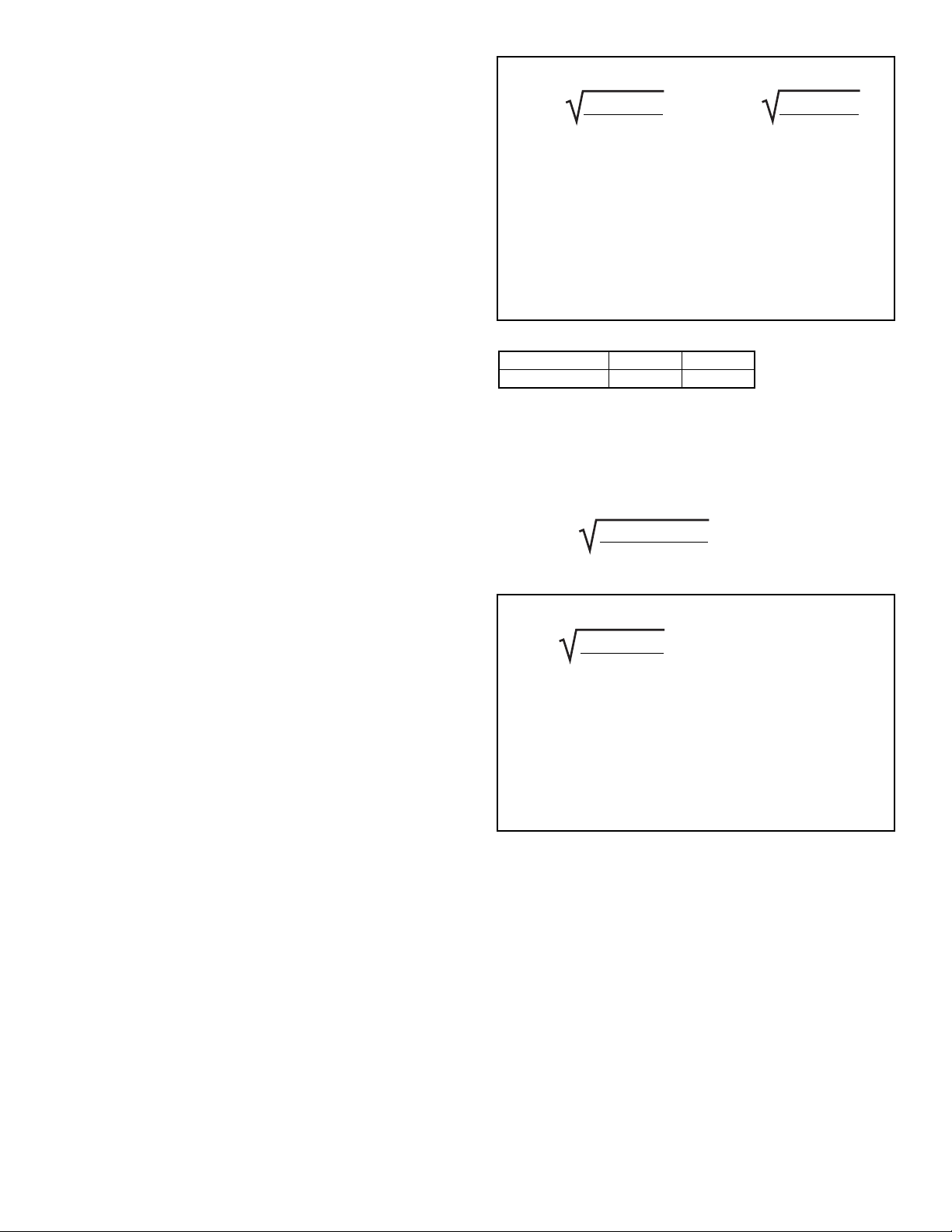
INSTALLATION
PREPARATION: Series TVF flowmeters are ready to install as-
s, although the sight tube may need repositioning so the scale
i
is visible after installation. First, remove the protective caps from
the connection ports. ALSO, REMOVE THE PLASTIC
SHIPPING TUBING ABOVE THE INLET CAP IN THE METER
CORE TUBE! Check that the float moves freely within the core
tube, and that no packing materials are in the meter.
Apply wrenches only on the flats or outer rims of the connection
ports. Avoid over-tightening, and do not use wrenches on other
ortions of the body or sight tube. When solvent cementing in
p
the vicinity of a meter with a polysulfone sight tube, the tube
should be removed until the cement dries and fumes clear.
SURGE CHAMBERS & ACCUMULATORS: Flowmeters are
more accurate and less likely to be damaged when the fluid flow
is smooth. If the meter must be installed on a line where
reciprocating pumps or compressors causing pulsation are
used, surge chambers or accumulators are strongly suggested
to damp the shock wave.
CORRECTING READINGS FOR NEW LIQUID CONDITIONS
Qa=
Q
s
ps(pf- pa)
pa(pf- ps)
r Q
o
Q
=
a
s
ds(df- da)
da(df- ds)
Where:
Qa= Actual flow, GPM (or same units as scale).
Qs= Meter reading from scale, (scale units).
ps= Specific gravity of calibration liquid related to water in
std.
atmosphere at 70° F. being 1.00.
pa= Specific gravity of metered liquid, same base.
Density of calibration liquid, lbs/ft
ds=
da= Density of metered liquid, lbs/ft
3
.
3
.
pf= Specific gravity of meter float.
df= Density of meter float as per table below.
FLOAT SPECIFIC GRAVITY/DENSITIES
Material
Stainless Steel
pf
8.05
df
501.1
* “Average” for these floats is f = 3.50, df = 217.8.
SIGHT TUBE ROTATION: On visual (the float disk is seen)
indication models with PLASTIC sight tubes, grasp the tube
firmly BY HAND near the body and twist until the scale faces the
desired direction. USE NO TOOLS!
STARTUP
System flow should be started with the by-pass valve open and
meter inlet and outlet valves closed. After the system is
operating, open the meter inlet valve gradually to equalize
internal pressure. Then slowly crack meter outlet valve and wait
for float to stabilize. Finally, slowly open the meter outlet and/or
flow regulating valve all the way and close the system by-pass
valve. AVOID SUDDEN SURGES THAT CAUSE THE METER
FLOAT TO SLAM INTO THE TOP OF THE SIGHT TUBE!
Although not essential, the meter sight tube should be filled to a
level above the float on liquid systems. The snorkel tube
(present in most standard models) allows escape of entrapped
gases except for a small pocket in the upper end which helps
cushion hydraulic shock. To assure proper filling and to flush
any foreign particles from the meter, operate the system at full
flow briefly at startup.
READING FLOW
Read flow directly from the scale as the number nearest the top
edge of the float indicator disk.
COMPENSATING FOR SYSTEM CHANGES
To find the correct flow reading for a system whose fluid
conditions vary from those for which the meter is scaled, use the
conversion data. The most practical method of applying the
formulae is to calculate a conversion factor for the new system
conditions, multiplying the scale reading by that factor. In the
problems, “Qs” has been assigned a value of “1” to determine
the conversion factor. (The factory can provide special scales at
additional cost for other fluids and/or units.)
EXAMPLE: Using a standard stainless seel meter scaled for
water (s = 1.00), what is the conversation factor for an oil with
a specific gravity of 0.85?
Qa= 1.00 x = 1.096
1.00 (8.05 - 0.85)
0.85 (8.05 - 1.00)
CORRECTING READINGS FOR NEW GAS CONDITIONS
Qg= Q
Pgx Tsx ps)
s
Psx Tgx pg)
Where:
Qg= SCFM, corrected to new conditions.
Qs= SCFM read on meter scale.
Pg= Operating pressure, psia (psig + 14.7).
Ps= Pressure stated on scale, psia (psig + 14.7).
Tg= Operating temperature, absolute (°F + 460).
Ts= Temperature stated on scale, absolute (°F + 460).
pg= Specific gravity of metered gas.
ps= Specific gravity stated on scale.
CAUTION: DO NOT OPERATE THE FLOWMETER ON A
SYSTEM EXCEEDING THE OPERATING LIMITS OF THE
UNIT. WHEN CHANGING OPERATING CONDITIONS, MAKE
SURE THAT THE NEW SYSTEM CONDITIONS ARE WITHIN
THE FLOWMETER OPERATING LIMITS, AND ALL WETTED
MATERIALS ARE COMPATIBLE WITH THE FLUID. IF IN
DOUBT, CONSULT THE FACTORY BEFORE OPERATING!!!